FR Rubber Belt for Fire-Resistant Coal Mining Applications
Fire hazards are a significant concern in many manufacturing environments, making flame-resistant (FR) rubber belts essential for reducing or preventing fire damage to both personnel and equipment. Designed to withstand high heat and flames, FR conveyor belts are specially crafted with flame-retardant compounds and advanced synthetic materials to provide enhanced protection in high-risk areas, such as mining, steel mills, chemical plants, and power stations.
These belts not only resist ignition but also help limit the spread of fire, ensuring that the conveyor system does not become a fire conduit in industrial settings. FR rubber belts are engineered to endure extreme conditions, offering superior durability and performance even in harsh environments. They provide excellent resistance to edge wear, high impact and tear resistance, as well as protection against rot and mildew. With higher breaking strength, improved tracking, and controlled elongation, these belts are capable of handling a wide range of bulk materials efficiently, including at steep angles from 0 to 90 degrees. This makes them ideal for conveyor belt bulk material handling, where strength and reliability are essential to ensure smooth operation and reduce the risk of failure.
Ideal for continuous material transport, FR rubber belts combine safety with durability, making them a reliable solution for industries where fire risks are prevalent. They maintain their performance under elevated temperatures and demanding conditions, ensuring both safe and efficient material handling while protecting valuable assets and personnel.In similar applications, the EP rubber belt also provides exceptional durability and strength, making it a trusted choice for heavy-duty material handling in challenging environments.
Key Features of FR Rubber Belts
- Fire Resistance: Fire resistance is the primary characteristic of FR rubber belts. These belts are specifically designed with materials that resist ignition and limit the spread of flames. The conveyor belt material used in these designs ensures enhanced safety in environments where fire hazards are a concern, providing critical protection for both the equipment and operators. They are manufactured using specialized compounds that incorporate flame-retardant additives. This means that even when exposed to potential ignition sources, FR rubber belts will not catch fire easily. In the event of a fire, these belts help minimize the risk of fire spreading throughout the conveyor system, ensuring the safety of both personnel and equipment in fire-prone environments, such as mines, steel mills, and chemical plants. Fire resistance is typically tested and verified through standardized testing procedures like the ISO 340 and DIN 22131 standards, ensuring that the belt meets the necessary safety requirements.
- Temperature Resistance: FR rubber belts are engineered to withstand high temperatures without degrading or losing their structural integrity. These belts are suitable for applications where the conveyed material exceeds normal temperature ranges, such as in steel manufacturing, cement production, and handling hot materials. Depending on the specific grade of the FR rubber belt, these belts can handle temperature extremes from around 150°C up to 250°C or more, depending on the formulation and intended application. Their temperature resistance prevents the rubber from softening, warping, or becoming brittle when exposed to continuous heat, ensuring the conveyor system operates smoothly even in high-heat environments.
- Durability: One of the key advantages of FR rubber belts is their durability. These belts are built to endure the wear and tear that comes with continuous operation, heavy material loads, and exposure to extreme conditions. The high-quality rubber compounds used in FR belts provide excellent resistance to abrasion, tearing, and wear. This durability ensures that the belts can last for long periods without frequent replacement, reducing downtime and maintenance costs for industrial operations. The toughness of these belts makes them ideal for high-impact environments where the conveyor system might be exposed to rough materials or physical stress.
- Self-Extinguishing Properties: Another significant feature of FR rubber belts is their self-extinguishing properties. In the event of ignition, these belts are designed to extinguish the flames on their own, preventing the fire from spreading further along the conveyor system. This is achieved through the incorporation of fire-retardant additives and a specialized rubber formulation that enables the material to stop burning once the ignition source is removed. While self-extinguishing properties do not make the belts fireproof, they significantly improve safety by limiting the potential for fire escalation, providing more time for fire suppression systems to respond and for personnel to evacuate if necessary.
Applications of FR (Fire Resistant) Rubber Belts
Fire-resistant (FR) rubber belts are specially designed to minimize fire risks in industries that handle flammable materials or operate in high-temperature environments. These belts are critical for ensuring the safety and efficiency of material handling systems in sectors where fire hazards are prevalent. Below are key applications of FR rubber belts across various industries:
Key Applications
Mining Industry
Steel Mills
Coal and Cement Plants
Material Handling in Hazardous Areas
Key Advantages of FR Rubber Belts in These Applications:
FR Rubber Belt Replacement: Essential Guidelines for Safety and Performance
When to Replace FR Rubber Belts:
FR rubber belts are designed to last under extreme conditions, but they do have a limited lifespan, particularly when exposed to high heat and abrasive environments. Here are some key factors to consider when determining whether it’s time to replace your FR rubber belt:
Over time, FR belts can lose their fire-resistant properties due to prolonged exposure to heat, chemicals, or abrasions. If the belt no longer meets the required fire-resistance standards or shows visible signs of damage, it should be replaced immediately.
Regular wear and tear can cause edges to fray or the belt to develop tears, which can compromise its integrity and lead to operational failure. Even small tears or cracks can result in a malfunction, especially in hazardous environments.
High-temperature environments can degrade the surface of FR belts, causing them to become brittle, cracked, or brittle. This can lead to a loss of performance and an increased risk of failure during operation.
Signs that a Belt Needs Replacement:
Recognizing the early warning signs of belt degradation is crucial for preventing costly downtime and ensuring operational safety:
If the FR rubber belt exhibits continuous burning or sparking during operation, it’s a clear sign that the belt’s fire-resistant properties have been compromised. These symptoms indicate that the belt can no longer contain or suppress flames in the event of a fire, which could escalate into a major safety hazard.
FR rubber belts are designed to be both strong and flexible to handle dynamic stress. If the belt becomes stiff, loses its tensile strength, or shows signs of cracking when flexed, it’s no longer safe to use. A decrease in flexibility can lead to reduced performance in applications where the belt needs to adapt to movement or curves.
In high-heat environments, continuous friction between the belt and other components can cause accelerated wear. If the belt is showing signs of excessive abrasion, especially in high-heat zones, it may no longer offer the same level of protection or performance, warranting a replacement.
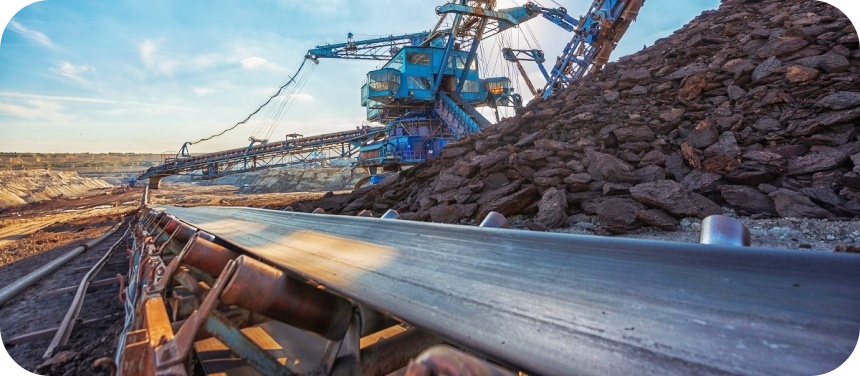
How to Replace an FR Rubber Belt:
When replacing an FR rubber belt, careful attention to detail is required to ensure that the new belt provides the same level of safety and performance as the previous one. Here’s a step-by-step guide to replacing an FR rubber belt:
Before selecting a replacement belt, measure the dimensions of the existing belt (e.g., width, length, thickness) to ensure compatibility with the conveyor system. It’s essential to check the specifications, such as the required fire-resistance rating and temperature tolerance, to match the original belt’s performance.
Select an FR rubber belt that matches or exceeds the specifications of the original. Consider factors such as the required temperature resistance, fire resistance (e.g., T1, T2, or T3 ratings as per IS 1891 Part II), and load-bearing capacity. Always choose a belt designed for the specific application, ensuring that it meets the necessary industrial standards for performance and safety.
Proper installation is key to maintaining the belt’s fire resistance and overall operational safety. Make sure the belt is properly aligned, tensioned, and securely mounted to avoid slippage or premature wear. Follow the manufacturer’s guidelines for installation and ensure that all components (e.g., pulleys, rollers) are in good condition and functioning correctly to prevent additional stress on the new belt.
After replacing the FR rubber belt, it’s important to monitor its performance during the initial operational phase. Conduct regular inspections for signs of wear, heat exposure, or other issues. Keeping a detailed maintenance record will help track the belt’s performance and ensure timely replacement in the future.
FR Rubber Belt Price: Key Factors and Where to Buy
Factors Affecting FR Rubber Belt Price
The cost of FR (Fire-Resistant) rubber belts varies significantly depending on several key factors. Understanding these factors can help you make an informed decision when purchasing FR rubber belts for industrial applications.
Material Quality:
- Higher Quality Materials: FR rubber belts made from premium, heat-resistant materials, such as high-grade synthetic rubber or specialized fire-retardant compounds, tend to be more expensive. The use of advanced materials ensures better performance in extreme conditions, such as higher heat resistance, durability, and fire protection.
- Standard vs. Premium Materials: Standard FR belts may use more common rubber blends that provide sufficient fire resistance for lighter applications, while premium-grade belts are engineered to withstand extreme temperatures and hazardous conditions, contributing to their higher cost. The conveyor belt engineering behind these premium-grade belts ensures they are designed to perform in the most challenging environments, offering enhanced durability and safety.
Belt Size:
- Standard Sizes vs. Custom Sizes: The size of the belt is a significant price determinant. Standard sizes (e.g., 500mm, 1000mm width belts) are typically less expensive. However, if you require custom-sized belts—such as extra-wide, extra-long, or belts with specialized dimensions for particular applications—the price will increase due to the customization process and additional material costs.
- Length and Width: Longer and wider belts require more raw material, which directly increases the cost. Custom sizes also require more precise manufacturing and additional testing to ensure proper fit and performance.
Fire Resistance Rating:
- Temperature Resistance Levels: FR rubber belts are classified based on their fire resistance and temperature tolerance. For example, belts with lower temperature resistance (e.g., up to 120°C) will typically be cheaper than those rated for higher temperatures (e.g., up to 200°C or more). Belts rated for higher temperatures, such as those used in steel mills or power plants, require specialized materials that increase production costs.
- Fire Resistance Standards: Belts that meet higher fire resistance standards (such as ISO 340 or IS 1891 Part II) will also command higher prices, as these standards involve rigorous testing and certification processes.
Custom Features:
- Special Coatings and Treatments: Some FR belts are equipped with additional protective coatings to improve resistance to chemicals, UV rays, abrasion, or ozone. These special coatings enhance the belt’s durability and lifespan but can add to the overall cost.
- Thickness and Durability: Belts that are thicker or designed for heavy-duty applications (such as mining or steel mills) will often come at a premium price. The added thickness provides additional heat resistance and mechanical strength, which is vital for handling heavier loads or more demanding environments.
General Price Range of FR Rubber Belts
The price of FR rubber belts can vary greatly depending on their specifications, but here is a general guide to what you can expect:
For standard industrial applications with lower fire resistance requirements, basic FR belts may start at a lower price range. These are typically suitable for environments with moderate temperatures or less exposure to fire hazards (e.g., small-scale manufacturing or general material handling). Prices may range from $5 to $20 per meter for these belts, depending on the size and quality.
Belts designed for more demanding industrial applications, such as moderate heat-resistant environments (e.g., cement plants, coal handling), will typically fall in the mid-range. Expect prices to range from $20 to $50 per meter, depending on factors like material quality, fire-resistance rating, and size.
High-end FR belts designed for harsh, high-temperature environments such as steel mills, power plants, or mining operations can be significantly more expensive. These belts are often custom-made, with premium materials, specialized coatings, and high-temperature resistance (up to 200°C or more). Prices for these belts can range from $50 to $150 per meter, or even higher for custom sizes or extreme specifications.
Where to Buy FR Rubber Belts
Manufacturers and Suppliers:
Online Retailers:
Local Distributors:
Benefits of FR Rubber Belts: Why They Are Essential for Industrial Applications
FR (Fire-Resistant) rubber belts offer several significant advantages for industries where fire safety and durability are paramount. Below are some of the key benefits that make FR rubber belts a valuable choice for material handling in high-risk environments.
Enhanced Safety
Cost Efficiency
Longevity
Performance Under High-Temperature and Hazardous Conditions
Environmental Protection
FAQs about FR Rubber Belt
What is a FRAS Belt?
An FRAS belt refers to a Fire-Resistant Anti-Static belt, which is designed to prevent the risk of fire and static electricity build-up in industrial applications. These belts are specifically engineered to comply with safety regulations in environments where flammable materials or hazardous substances are present. FRAS belts are commonly used in mining, coal handling, and other high-risk industries. The fire-resistant properties of these belts help prevent the ignition of combustible materials during transport, reducing the risk of fire outbreaks. Anti-static properties ensure that static electricity, which could potentially cause sparks or ignition, is effectively minimized. FRAS belts are manufactured with special materials, such as specific rubber compounds, that undergo testing for both their ability to withstand high temperatures and their anti-static capabilities. They are ideal for use in industries dealing with flammable dust, chemicals, and materials. The primary purpose of FRAS belts is to enhance safety by reducing fire risks while maintaining durability and performance in harsh industrial environments.
What is the Rubber Belt on the Engine?
The rubber belt on an engine is an essential component of the engine’s power transmission system. Typically known as a timing belt or serpentine belt, these rubber belts help drive various engine components, such as the alternator, water pump, air conditioning compressor, and power steering pump. The timing belt ensures that the engine’s camshaft and crankshaft remain synchronized, allowing for proper valve timing and efficient engine performance. The serpentine belt, a more common type in modern engines, is a long, continuous belt that is used to drive multiple accessories with a single belt. It is typically made of high-strength rubber and reinforced with materials such as polyester or fiberglass to withstand high friction, wear, and heat. Over time, these belts can wear down, stretch, or crack, so it’s important to monitor them regularly for signs of damage. If the rubber belt on the engine breaks or malfunctions, it can lead to significant engine failure or performance issues, making timely replacement crucial for maintaining the engine’s reliability.
How Long Do Rubber Belts Last?
The lifespan of a rubber belt depends on various factors, including the type of belt, the environment in which it is used, and the maintenance practices in place. On average, rubber belts in industrial applications last anywhere from 1 to 5 years. Belts used in automotive engines (such as serpentine belts or timing belts) typically need replacement every 60,000 to 100,000 miles, depending on the manufacturer’s recommendations. However, in industrial settings, such as conveyor belts used for material handling, the lifespan can be influenced by the load they carry, the operating temperature, and the presence of abrasive materials. Heat-resistant belts, for example, may last longer in high-temperature environments, while fire-resistant belts are designed to withstand harsher conditions. Regular maintenance, such as monitoring for wear, checking for cracks, and ensuring proper tensioning, can significantly extend the lifespan of rubber belts. Proper lubrication, protection from excessive heat, and timely replacements when wear is evident are essential to maximizing their longevity.
CONTACT US
Let us help you find a better solution!