High Abrasion Resistant Conveyor Belt test and Archives
Conveyor belts play a pivotal role in a multitude of industries, serving as the backbone for material handling in mining, manufacturing, logistics, and more. These belts are tasked with moving goods and materials over long distances, under varying conditions, which subjects them to significant wear and tear. The key to maximizing their lifespan and ensuring uninterrupted efficiency lies in their resistance to abrasion. An abrasion resistant conveyor belt is specifically designed to withstand the harsh conditions it encounters, including the continuous friction and impact from loading and transporting abrasive materials. This specialized feature not only extends the operational life of the conveyor belt but also significantly enhances the productivity and cost-effectiveness of the industries relying on these essential components. By investing in high-quality, abrasion-resistant belts, businesses can achieve a remarkable improvement in their operational efficiency and reduce the need for frequent replacements, leading to a more sustainable and profitable operation.
What Makes a Conveyor Belt Abrasion Resistant
The durability and longevity of a conveyor belt are crucial for industries that rely on continuous operation and material handling. An abrasion resistant conveyor belt is engineered to withstand the rigorous conditions of transporting materials, especially those that are rough, sharp, or hot, which can significantly wear down standard belts. But what exactly contributes to the abrasion resistance of these specialized belts?
Various Materials and Compounds
To enhance the abrasion resistance of conveyor belts, manufacturers utilize a variety of materials and compounds. One notable example is the UAR (Ultra Abrasion Resistant) compound developed by Bridgestone. This proprietary compound is specifically designed for transporting small but highly abrasive materials, offering an optimal solution for high abrasive operations. Similarly, thermoplastic materials are also used for their excellent wear resistance and ability to maintain performance under varying temperatures and exposure to chemicals.
Fabric Materials

Fabric materials like nylon and polyester play pivotal roles in augmenting the abrasion resistance of conveyor belts. Here are eight key aspects of how these materials contribute:
- Tensile Strength: High tensile strength allows the belt to withstand the forces exerted during loading and operation without stretching or breaking.
- Flexibility: This ensures the belt can navigate around pulleys and through conveyor systems without sustaining damage.
- Impact Resistance: Absorbs the shock and impact of heavy materials falling onto the belt, reducing surface damage.
- Low Elongation: Minimizes stretch under load, maintaining the belt’s shape and integrity over time.
- Chemical Resistance: Protects the belt from degradation due to exposure to oils, greases, and other chemicals.
- Heat Resistance: Allows the belt to operate effectively in high-temperature environments without deteriorating.
- Bonding to Rubber: Both nylon and polyester bond well with rubber coatings, enhancing the overall durability and resistance of the belt.
- Mildew and Rot Resistance: Ensures the belt remains functional in damp or wet conditions, preventing the breakdown of materials.
Incorporating these materials into the construction of an abrasion resistant conveyor belt ensures that it can deliver reliable performance in the toughest industrial environments. By understanding and leveraging the unique properties of these materials, manufacturers can create conveyor belts that meet the specific needs of their applications, providing a balance of strength, flexibility, and resistance to wear.
Best Abrasion Resistant Conveyor Belt Features
Types of Abrasion Resistant Conveyor Belts
Abrasion resistant conveyor belts are essential in industries where materials cause significant wear and tear. These belts are specifically designed to withstand harsh conditions and extend the lifespan of the conveyor system. Here are some of the most commonly used types:
- Steel Cord Conveyor Belts
Steel cord conveyor belts are reinforced with steel cables, providing exceptional strength and durability. These belts are designed to handle extremely heavy loads and harsh conditions, making them ideal for mining and bulk material handling. The steel cords provide high tensile strength, reducing the risk of elongation and ensuring minimal maintenance over time. - Snake Sandwich Conveyor Belts
Snake sandwich conveyor belts feature two parallel belts that grip materials firmly and move them at steep inclines, even up to 90 degrees. This type of belt is particularly useful in mining and construction industries where materials need to be transported vertically. Their design includes robust, abrasion-resistant materials to handle the high levels of wear encountered in such operations. - Long Belt Conveyor Belts
Long belt conveyors are used for transporting materials over considerable distances, sometimes up to 13.8 km (8.57 miles). These belts can handle both horizontal and vertical curves, making them versatile for various industrial applications. The materials used in long belts are often highly abrasion-resistant to ensure longevity and reliability in transporting heavy and abrasive materials. - Heat Resistant Conveyor Belts
Heat resistant conveyor belts are designed to withstand high temperatures while maintaining their structural integrity. These belts are made from special heat-resistant compounds that prevent the rubber from degrading under extreme heat. They are used in industries such as metal processing and foundries, where materials are often transported at elevated temperatures. - Fire Resistant Conveyor Belts
Fire resistant conveyor belts are essential in environments where fire hazards are present, such as coal mines and power plants. These belts are made from flame-retardant compounds that prevent the belt from igniting and spreading fire. They also offer abrasion resistance, ensuring that they can handle the wear and tear from transported materials while maintaining safety standards.
Characteristics of High Abrasion Conveyor Belts
The quest for the best abrasion resistant conveyor belt is driven by the need for durability and efficiency in industrial operations. These belts are designed to withstand the harsh conditions of transporting abrasive materials, which can quickly wear down lesser quality belts. Understanding the characteristics that define high-quality abrasion-resistant conveyor belts is crucial for selecting the right belt for your application. Here are ten key features to look for:
- High Tensile Strength: Essential for supporting heavy loads without stretching or breaking.
- Superior Abrasion Resistance: The ability to resist wear from rough materials is a hallmark of the best belts.
- Cut and Gouge Resistance: Protection against sharp objects and rough materials that could cut or gouge the belt surface.
- High Impact Resistance: The capacity to absorb the energy of falling materials without damage.
- Low Stretch: Minimal elongation under load, ensuring stable and efficient operation.
- Chemical Resistance: The ability to withstand exposure to oils, fats, and other chemicals.
- Temperature Tolerance: Performance is maintained across a range of temperatures, from very cold to very hot environments.
- Energy Efficiency: Reduced energy consumption due to optimized belt design and materials.
- Long Service Life: A longer lifespan reduces the need for frequent replacements and downtime.
- Ease of Maintenance: Simplified maintenance and repair processes to minimize operational disruptions.
Different Grades of Conveyor Belts and Their Applications
Different grades of conveyor belts are designed to meet the specific demands of various industrial applications. These grades are determined by factors such as the belt’s material composition, thickness, and structural design, each contributing to the belt’s overall performance and suitability for certain tasks. The table below displays common grades and their typical applications:
Selecting the right conveyor belt grade for specific industrial needs is paramount. The wrong choice can lead to increased wear and tear, higher maintenance costs, and potential safety hazards. Factors to consider include the nature of the materials being transported, the environment (e.g., temperature, chemical exposure), and the physical demands (e.g., load size, speed of transport). An abrasion resistant conveyor belt that matches the application’s requirements will ensure optimal performance, safety, and cost-efficiency. This strategic selection process not only extends the life of the belt but also enhances the overall productivity of the operation.
Manufacturers of Abrasion Resistant Conveyor Belts
Leading Manufacturers
In the industrial world, the demand for high-quality high abrasion conveyor belts is met by a select group of manufacturers known for their commitment to durability, innovation, and performance. These manufacturers specialize in producing conveyor belts that are not only resistant to wear and tear but also tailored to meet the specific needs of various industries, from mining and construction to recycling and manufacturing.
Leading manufacturers of high abrasion conveyor belts are recognized for their advanced material science and engineering capabilities. They utilize a range of high-performance materials, including specialized rubber compounds, advanced polymers, and reinforced fabrics, to create belts that withstand the toughest conditions.
Gram Conveyor:
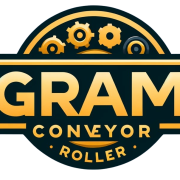
GRAM Conveyor is distinguished by its pioneering Nylon Series, which features high-quality nylon material designed for exceptional performance and durability. Our heavy-duty nylon conveyor rollers are lightweight, corrosion-resistant, and easy to maintain, making them ideal for industries like chemical manufacturing and cleanrooms. GRAM Conveyor’s dedication to innovation and quality ensures our products provide reliable and efficient solutions for various demanding applications, positioning us as a forward-thinking leader in the conveyor system industry.
Bridgestone:
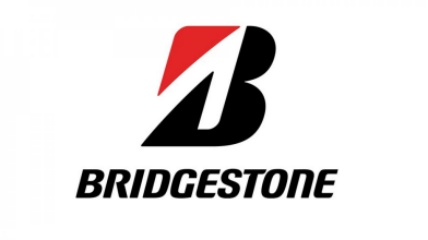
Bridgestone is renowned for its innovative UAR (Ultra Abrasion Resistant) compound, which significantly enhances the durability and lifespan of their conveyor belts. Their commitment to quality and advanced technology positions them as a leader in the industry.
Metso:

Metso, known for their fabric conveyor belts with high tensile strength. Their products are designed to meet the rigorous demands of various industries, ensuring reliability and performance under heavy loads and challenging conditions.
Continental AG:

Continental AG is a global leader in manufacturing conveyor belts and other industrial solutions. Their products are recognized for their durability, efficiency, and cutting-edge technology, making them a trusted name in the industry.
Fenner Dunlop:
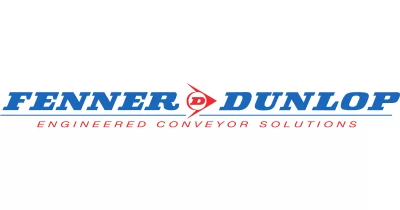
Fenner Dunlop is celebrated for its high-quality conveyor belts, which are engineered to withstand harsh environments and heavy-duty applications. Their innovative solutions and commitment to excellence make them a prominent player in the market.
Yokohama:
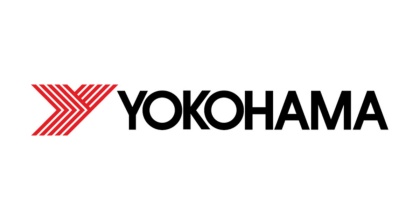
Yokohama is known for its advanced conveyor belt technologies that offer superior performance and reliability. Their focus on innovation and quality ensures that their products meet the highest standards, catering to various industrial needs.
Considerations of These Manufacturers
When selecting a manufacturer for an abrasion resistant conveyor belt, there are several key factors to consider:
- Innovation: Look for manufacturers that invest in research and development to produce belts with the latest technology and materials. This ensures you’re getting a product that meets the highest standards of durability and efficiency.
- Material Quality: The quality of the materials used in the conveyor belt directly impacts its performance and lifespan. Top manufacturers use premium-grade rubber, thermoplastics, and fabrics to enhance abrasion resistance and strength.
- Customization Options: Every industrial application has unique requirements. The best manufacturers offer customization options that allow you to specify the belt’s width, length, thickness, and material composition. This ensures the belt is perfectly suited to your operational needs.
- Technical Support and Service: After-sales support is crucial. Leading manufacturers provide comprehensive technical support, including installation guidance, maintenance tips, and troubleshooting services.
- Reputation and Reliability: A manufacturer’s reputation in the market can be a reliable indicator of the quality and reliability of their abrasion resistant conveyor belts. Look for companies with positive reviews, case studies, and a track record of serving industries similar to yours.
- Certifications and Standards Compliance: Ensure the manufacturer adheres to international quality and safety standards. Certifications such as ISO can be a testament to the manufacturer’s commitment to quality and environmental management.
By focusing on these criteria, you can select a manufacturer that not only provides an abrasion resistant conveyor belt that meets your specific needs but also supports your goals for operational efficiency, safety, and longevity. The right partnership with a manufacturer can significantly impact the success of your operations, reducing downtime and maintenance costs while improving overall productivity.
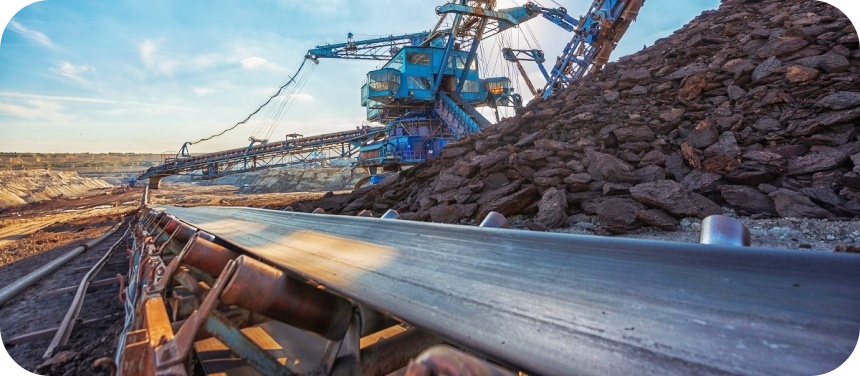
Cost Considerations for Abrasion Resistant Conveyor Belt
Factors Affecting Cost
When investing in an abrasion resistant conveyor belt, understanding the factors that influence its cost is crucial. These belts are designed to offer superior durability and performance in harsh industrial environments, but their advanced features and materials can also affect their price. Here are eight key factors that influence the cost of abrasion-resistant conveyor belts:
- Material Quality: High-quality materials such as UAR compounds, thermoplastics, and reinforced fabrics like nylon and polyester are more expensive but essential for abrasion resistance.
- Manufacturing Process: Advanced manufacturing techniques that enhance the belt’s durability and resistance can also increase production costs.
- Belt Dimensions: Larger and thicker belts require more material and labor to produce, leading to higher costs.
- Customization: Customized belts designed to meet specific operational requirements can be more costly than standard options.
- Innovative Features: Belts with additional features such as heat resistance, chemical resistance, and reinforced edges have higher production costs.
- Brand and Manufacturer: Belts from reputable manufacturers known for their quality and reliability may come at a premium price.
- Market Demand: High demand for specific types of abrasion-resistant belts can drive up prices due to supply and demand dynamics.
- Shipping and Handling: The cost of transporting and handling heavy and bulky conveyor belts can also contribute to the overall cost.
Long-term Benefits of Investing
Despite these cost factors, investing in high-quality abrasion-resistant conveyor belts offers several long-term benefits that can justify the initial expenditure:
- Extended Lifespan: These belts are less likely to suffer from wear and tear, reducing the frequency of replacements.
- Reduced Maintenance Costs: Durable materials and construction minimize the need for frequent repairs and maintenance.
- Increased Operational Efficiency: High-quality belts are less likely to break down, ensuring continuous operation and productivity.
- Improved Safety: Superior materials and design reduce the risk of belt failure, enhancing workplace safety.
- Lower Total Cost of Ownership: Although the initial cost may be higher, the extended lifespan and reduced maintenance needs lead to lower expenses over the belt’s life.
- Enhanced Product Quality: Consistent operation without unexpected downtime or material spillage ensures the quality of the processed or transported products.
- Environmental Benefits: Longer-lasting belts contribute to sustainability by reducing waste and the need for frequent replacements.
- Competitive Advantage: Reliable and efficient operation can improve your company’s competitiveness in the market.
Considering these factors and benefits, the decision to invest in an abrasion resistant conveyor belt should be based on a comprehensive analysis of both immediate costs and long-term returns. By prioritizing quality and suitability for specific industrial applications, businesses can achieve significant savings and operational advantages in the long run.
Technical Specifications and Standards for Abrasion Resistant Conveyor Belt
The performance and durability of an abrasion resistant conveyor belt are not just about the materials used in its construction; they also hinge on adhering to rigorous technical specifications and standards. Among these, the DIN abrasion test procedure stands out as a critical benchmark for assessing the quality and resilience of these belts.
DIN Abrasion Test Procedure

This test is a standard method defined by the Deutsches Institut für Normung (DIN), specifically under the DIN ISO 4649 standard. It measures the abrasion resistance of rubber materials through the loss of mass after rubbing against an abrasive surface under specified conditions. For an abrasion resistant conveyor belt, this test simulates the wear and tear it would endure in an industrial setting. The procedure involves rotating a sample of the conveyor belt material against an abrasive sheet and applying a standard force. The amount of material worn away, measured in cubic millimeters, indicates the material’s abrasion resistance.
Significance of Abrasion Resistance Ratings
The results from the DIN abrasion test are crucial for determining the abrasion resistance rating of a conveyor belt. This rating helps categorize belts into different levels of durability and suitability for various applications. A lower volume of material loss signifies a higher resistance to abrasion, making the conveyor belt ideal for environments where sharp or rough materials are common. These ratings are essential for manufacturers and end-users alike, as they directly relate to the belt’s performance, lifespan, and overall cost-effectiveness in specific operational conditions.
Importance of DIN Abrasion Calculation
The DIN abrasion calculation is integral to selecting the right high abrasion conveyor belt for any application. This calculation, derived from the test results, provides a quantitative measure of the belt’s ability to withstand wear. It allows for a comparative analysis between different belt materials and designs, ensuring that the selected belt meets the operational demands and longevity expectations. For industries where conveyor belts are exposed to severe abrasion, such as mining, construction, and recycling, the DIN abrasion calculation becomes a pivotal factor in the decision-making process.
Incorporating these technical specifications and standards into the selection process of an abrasion resistant conveyor belt ensures that the chosen product not only meets the required performance criteria but also contributes to the efficiency and reliability of the conveyor system. By understanding the significance of the DIN abrasion test procedure, abrasion resistance ratings, and the DIN abrasion calculation, businesses can make informed decisions that optimize their operations and extend the service life of their conveyor belts.
Abrasion Testing and Resistance Rating for Abrasion Resistant Conveyor Belt
Abrasion Testing
Abrasion Testing Methods: Among the various methods used to test the abrasion resistance of conveyor belts, the DIN abrasion test is particularly noteworthy. This standardized test measures the volume of material worn away from the belt surface under a specified set of conditions, providing a quantitative measure of the belt’s resistance to abrasion. The test involves subjecting a sample of the belt material to a rotating abrasive drum under a fixed pressure. The amount of material lost after a certain period or number of rotations is then measured. This method is widely recognized for its reliability in simulating real-world wear and tear on the belts.
Contribution to High-Performance Conveyor Belts: Abrasion resistance tests are crucial in the development of high-performance abrasion resistant conveyor belts. By quantifying the wear resistance of different materials and designs, manufacturers can refine their products to enhance durability. These tests help in identifying the most effective materials and construction techniques to withstand the specific conditions they will encounter in use, such as exposure to sharp objects, heavy loads, and abrasive materials. The insights gained from abrasion testing guide the innovation and improvement of conveyor belts, ensuring they are capable of delivering the best possible performance in their intended applications.
Resistance Rating
Interpreting Abrasion Loss Data: The data obtained from abrasion tests, particularly the volume of material lost, is a key indicator of a conveyor belt’s durability and expected lifespan. A lower abrasion loss signifies a higher resistance to wear, suggesting that the belt will last longer even under harsh conditions. This information is invaluable for end-users, as it helps in making informed decisions when selecting a conveyor belt. By choosing a belt with proven abrasion resistance, businesses can minimize downtime due to belt failures, reduce maintenance and replacement costs, and ensure continuous and efficient operation. Furthermore, interpreting abrasion loss data allows for a more accurate prediction of belt lifespan and efficiency, enabling better planning and budgeting for maintenance and replacements.
The abrasion testing and resistance rating of an abrasion resistant conveyor belt are critical factors that determine its suitability for specific industrial applications. These evaluations not only assure the quality and durability of the belt but also contribute to the optimization of operational efficiency and cost-effectiveness. By understanding and utilizing these metrics, businesses can significantly improve their material handling processes, ensuring longevity and reliability in their conveyor systems.
Choosing the Right Abrasion Resistant Conveyor Belt
Selecting the appropriate high abrasion conveyor belt for your operation is a critical decision that impacts not only the efficiency and productivity of your conveyor system but also its overall cost-effectiveness. The right belt can significantly reduce downtime, maintenance costs, and the need for frequent replacements. Here are some guidelines and considerations to help you make an informed choice:
Guidelines on Selecting the Appropriate Conveyor Belt Grade
- Assess the Material Being Transported: Consider the abrasiveness, size, shape, and weight of the materials. Heavier, sharper, and more abrasive materials require belts with higher abrasion resistance.
- Consider the Operating Environment: Temperature, chemicals, and moisture can affect a belt’s performance. Ensure the belt material is suited to withstand your specific environmental conditions.
- Understand Belt Specifications: Pay attention to the belt’s tensile strength, thickness, and elasticity. These factors should align with the demands of your application to ensure optimal performance.
- Evaluate Manufacturer Ratings and Tests: Look for belts that have undergone rigorous testing, such as the DIN abrasion test, and compare their abrasion resistance ratings.
- Consult with Experts: Manufacturers and suppliers can provide valuable advice on the best belt for your application based on their experience and technical knowledge.
- Consider Future Needs: Choose a belt that not only meets your current requirements but also has the flexibility to accommodate future operational changes.
Get a quote for your conveyor belt needs today!
Impacts on the Overall Cost-Effectiveness of Conveyor Systems
- Extended Belt Lifespan: High abrasion resistance means the belt can withstand wear and tear better, leading to a longer service life and fewer replacements.
- Reduced Downtime: A durable abrasion resistant conveyor belt minimizes unexpected breakdowns, keeping your operations running smoothly and reducing costly downtime.
- Lower Maintenance Costs: With less wear and tear, the belt requires less maintenance, saving on labor costs and replacement parts.
- Increased Productivity: A reliable conveyor belt ensures consistent operation, leading to higher productivity and efficiency in material handling.
- Improved Safety: High-quality belts are less likely to fail during operation, reducing the risk of accidents and ensuring a safer workplace.
- Sustainability: By reducing the frequency of belt replacements, you’re also minimizing waste and the environmental impact associated with manufacturing and disposing of conveyor belts.
Choosing the right abrasion resistant conveyor belt is a strategic decision that affects the long-term success of your operations. By carefully considering the specific requirements of your application and the potential impacts on cost-effectiveness, you can select a belt that not only meets your needs but also contributes to the overall efficiency and sustainability of your conveyor system.
FAQs about Abrasion Resistant Conveyor Belt
A conveyor belt designed for abrasive materials is a specialized belt intended for the transportation of materials that are rough, sharp, or otherwise capable of causing wear and tear on standard conveyor belts. These materials include, but are not limited to, sand, gravel, crushed stones, and certain types of ores. Conveyor belts for abrasive materials are constructed using high-durability materials and advanced technologies to withstand the harsh conditions they encounter. They feature high abrasion resistance, ensuring longevity and reliability in environments where standard belts would quickly fail. The design considerations for these belts focus on material composition, thickness, reinforcement, and surface texture to combat the abrasive effects of the materials being transported, thereby reducing maintenance needs and operational downtime.
The three main types of conveyor belts used in various industries are flat belts, modular belts, and cleated belts.
Flat Belts: These are the most common type of conveyor belts, known for their simplicity and versatility. Made from materials like rubber, nylon, and polyester, flat belts are used in applications ranging from material handling to packaging. They are particularly favored for their high efficiency and the ability to transport goods over long distances.
Modular Belts: Constructed from interlocking plastic pieces, modular belts offer a durable solution capable of handling heavy loads and sharp or abrasive materials. They are easy to repair and maintain, as individual links can be replaced without replacing the entire belt. Modular belts are often used in food processing industries due to their ease of cleaning and resistance to corrosion.
Cleated Belts: These belts feature raised sections, or cleats, that help in transporting materials up inclines and preventing slippage of the product. Cleated belts are ideal for applications where materials need to be moved at an angle, such as in bulk material handling or recycling operations.
Grade 1 and Grade 2 conveyor belts are categorized based on their durability and resistance to abrasion, with each grade suitable for different applications and material types.
Grade 1 Conveyor Belts: These are high-quality belts designed for maximum resistance to abrasion and wear. They are typically made from materials that can withstand harsh conditions, including the transport of sharp, heavy, or highly abrasive materials. Grade 1 belts are ideal for critical applications where longevity and durability are paramount.
Grade 2 Conveyor Belts: While still designed to be durable, Grade 2 belts offer a moderate level of abrasion resistance compared to Grade 1. They are suited for handling less abrasive materials like processed agricultural products, light to medium mining operations, and general-purpose industrial applications. Grade 2 belts provide a balance between performance and cost, making them a practical choice for many operations.
The main difference lies in their application suitability, with Grade 1 belts being the choice for more demanding environments and Grade 2 belts serving well in less abrasive conditions.
The best material for a conveyor belt depends on the application it is intended for. Materials commonly used in the manufacture of conveyor belts include rubber, PVC, polyurethane, nylon, and polyester.
Rubber: Offers excellent flexibility and high tensile strength, making it ideal for heavy-duty applications and the transportation of abrasive materials.
PVC: Provides good resistance to chemicals, abrasion, and weather, suitable for various industrial applications, including food processing.
Polyurethane: Known for its exceptional resistance to wear, tear, and chemicals, polyurethane belts are used in applications requiring cleanliness and non-marking properties.
Nylon: Features high strength and abrasion resistance, making it suitable for heavy-load transportation in industries like mining and quarrying.
Polyester: Offers a good balance of cost, durability, and performance, suitable for moderate to heavy applications that require resistance to moisture and chemicals.
Selecting the best material involves considering factors such as the nature of the materials being transported, the operating environment, and specific application requirements.
The most abrasion-resistant rubber is typically polyurethane. Polyurethane rubber is renowned for its exceptional abrasion resistance, making it an ideal choice for applications that involve high wear and tear. Its ability to withstand harsh conditions and abrasive materials significantly enhances the lifespan of products made from this material.
The strongest conveyor belt available is often considered to be the steel cord conveyor belt. Steel cord conveyor belts are reinforced with steel cables, which provide exceptional tensile strength and durability. These belts are designed to handle extremely heavy loads and harsh conditions, making them suitable for demanding industrial applications such as mining, bulk handling, and large-scale material transport. Their robust construction ensures minimal elongation and high impact resistance, contributing to their reputation as the strongest conveyor belts in the industry.
Last Updated on June 21, 2024 by Jordan Smith
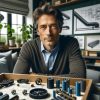
Jordan Smith, a seasoned professional with over 20 years of experience in the conveyor system industry. Jordan’s expertise lies in providing comprehensive solutions for conveyor rollers, belts, and accessories, catering to a wide range of industrial needs. From initial design and configuration to installation and meticulous troubleshooting, Jordan is adept at handling all aspects of conveyor system management. Whether you’re looking to upgrade your production line with efficient conveyor belts, require custom conveyor rollers for specific operations, or need expert advice on selecting the right conveyor accessories for your facility, Jordan is your reliable consultant. For any inquiries or assistance with conveyor system optimization, Jordan is available to share his wealth of knowledge and experience. Feel free to reach out at any time for professional guidance on all matters related to conveyor rollers, belts, and accessories.