Basic Self Tracking Conveyor Belt Rules
Conveyor belt systems are integral to a myriad of industries, facilitating the efficient transport of goods across various stages of production and distribution. The effectiveness of these systems hinges significantly on the precision of belt tracking—the ability of the conveyor belt to maintain its intended path. Misalignment can lead to numerous problems, including premature wear, product damage, and increased downtime for adjustments and repairs. Enter the innovative solution to these pervasive challenges: self-tracking conveyor belts. These advanced systems are designed to automatically maintain proper alignment, significantly reducing the need for manual adjustments and the risk of tracking-related issues. By integrating a self-tracking conveyor belt into their operations, businesses can enhance efficiency, minimize maintenance costs, and improve overall productivity, addressing a critical need in conveyor belt technology with a smart, self-regulating solution.
What Are Self-Tracking Conveyor Belts?
Self-tracking conveyor belts represent a significant advancement in conveyor belt technology, designed to autonomously maintain their alignment along the conveyor frame, thereby eliminating the common problem of belt misalignment. Unlike traditional conveyor belts that require manual adjustment and continuous monitoring to stay on track, a self-tracking conveyor belt incorporates unique design features that enable it to automatically correct its path without external intervention.
The basic principle behind a self-tracking conveyor belt lies in its innovative design, which typically includes edges that are shaped or structured in a way that prompts the belt to naturally align itself correctly on the conveyor. This might involve special guiding features, such as tapered edges or rollers, which interact with the conveyor structure to steer the belt back to its central path whenever it begins to drift.
A diagram illustrating how self-tracking conveyor belts work would show the belt’s cross-section and how its design elements interact with the conveyor’s structure. For instance, when the belt starts to move off-center, the unique edge design creates a differential in force across the width of the belt. This differential guides the belt back towards the center of the conveyor path. The belt’s ability to self-correct in real-time significantly reduces wear and tear on the edges, prolongs the belt’s lifespan, and minimizes the risk of product spillage or damage due to misalignment.
The self-tracking conveyor belt is engineered to respond to the dynamic conditions of its operation. By automatically adjusting its trajectory, the self-tracking conveyor belt ensures smooth, efficient, and uninterrupted operation, making it an invaluable asset in settings where operational efficiency and maintenance reduction are paramount. This self-regulating feature not only enhances the reliability of the conveyor system but also contributes to safer working conditions by reducing the need for manual adjustments that could potentially interrupt the conveyor’s operation.
Self Tracking Conveyor Belt Principle
A self-tracking conveyor belt is designed to automatically align and adjust itself to ensure that the belt stays centered and properly aligned on the conveyor system. Here are the fundamental principles behind self-tracking conveyor belts:
- Self-Centering Design: Self-tracking conveyor belts often feature design elements like tapered rollers or specially shaped guide rails that naturally center the belt as it moves. These components help correct any misalignment by guiding the belt back to the center.
- Tracking Rollers: Many self-tracking systems use tracking rollers or idlers positioned along the sides of the conveyor belt. These rollers apply force to the edges of the belt, helping to keep it centered and preventing it from drifting.
- Adjustable Side Guides: Some systems use adjustable side guides that can be fine-tuned to help the belt maintain its alignment. These guides are positioned along the conveyor frame and can be adjusted to correct any deviations.
- Tension Control: Proper belt tension is crucial for tracking. Self-tracking systems often include mechanisms to automatically adjust the belt tension, which helps maintain proper alignment and prevent slipping or wandering.
- Belt Material and Construction: The material and construction of the belt can affect its tracking ability. Certain materials and designs, like those with a specific weave or edge treatment, can enhance self-tracking capabilities.
- Sensors and Feedback Systems: Advanced self-tracking conveyors might use sensors and feedback systems to monitor the belt’s position and make real-time adjustments. These systems can detect when the belt starts to drift and trigger corrective actions.
- Belt Edge Design: The design of the belt edges, such as beveled or crowned edges, can also play a role in self-tracking. These features help the belt move smoothly and stay centered on the rollers or guide rails.
- Regular Maintenance: Even with self-tracking features, regular maintenance is necessary to ensure the system remains effective. This includes checking for wear and tear, ensuring proper tension, and making sure all tracking components are functioning correctly.
Self-tracking conveyors are useful in applications where precise alignment is crucial, and they help reduce the need for manual adjustments and interventions.
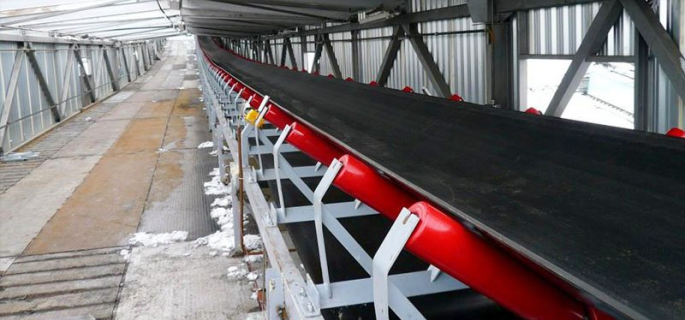
The Importance of Proper Conveyor Belt Tracking
Proper conveyor belt tracking theory is crucial for the smooth operation and longevity of conveyor systems. Misalignment, even by a small margin, can lead to significant problems, affecting the overall productivity and safety of a facility. The integration of a self-tracking conveyor belt system addresses these challenges head-on, providing a self-correcting mechanism that ensures the belt remains aligned, thus mitigating common tracking issues.
Common Conveyor Belt Tracking Problems
- Edge Wear: Misaligned belts frequently rub against conveyor components, leading to premature wear and tear on the edges.
- Material Spillage: A belt that doesn’t track properly can cause material to spill off the sides, leading to waste and the need for additional cleanup.
- Belt Slippage: Improper tracking can cause the belt to slip on the drive pulleys, reducing efficiency and potentially damaging the belt.
- Structural Damage: Continuous misalignment can exert undue stress on the conveyor structure itself, leading to deformation or failure of components.
- Increased Energy Consumption: Misaligned belts require more energy to move, increasing operational costs.
- Decreased Lifespan of the Belt: Constant misalignment and the resulting wear and tear significantly reduce the operational lifespan of a conveyor belt.
- Safety Hazards: Misaligned belts can lead to hazardous working conditions, including the risk of accidents from falling materials or damaged components.
- Operational Downtime: Correcting misalignment issues often requires halting production, leading to downtime and lost productivity.
Consequences of Improper Belt Tracking
The consequences of not maintaining proper belt tracking are manifold, impacting not just the operational efficiency but also the financial bottom line of operations. Here’s how a self-tracking conveyor belt can mitigate these issues:
- Reduced Maintenance Costs: By automatically maintaining proper alignment, self-tracking conveyor belts eliminate the frequent adjustments and repairs associated with traditional belts, thereby reducing maintenance costs.
- Enhanced Operational Efficiency: Self-tracking conveyor belts ensure that materials are transported smoothly and consistently, without the interruptions caused by misalignments, thus maintaining high operational efficiency.
- Protection of Conveyor Belt System: The self-correcting feature of self-tracking conveyor belts minimizes the risk of damage to the belt and conveyor structure, prolonging the system’s overall lifespan.
- Safety Improvements: By reducing the risk of material spillage and component failure, self-tracking conveyor belts contribute to a safer working environment.
- Energy Savings: Properly aligned belts require less energy to operate, leading to significant energy savings over time.
- Increased Productivity: With reduced downtime for maintenance and adjustments, self-tracking conveyor belts support continuous, uninterrupted operation, thereby increasing productivity.
- Longer Belt Lifespan: The reduced wear and tear on self-tracking conveyor belts extend their operational life, offering long-term cost savings.
- Operational Reliability: The reliability of conveyor operations improves significantly with the use of self-tracking conveyor belts, as they ensure consistent material handling without the need for constant monitoring and adjustment.
The importance of proper conveyor belt tracking cannot be overstated, with self-tracking conveyor belts offering an effective solution to a wide range of common problems. By ensuring automatic and continuous alignment, self-tracking conveyor belts not only enhance efficiency and safety but also contribute to significant cost savings and operational reliability.
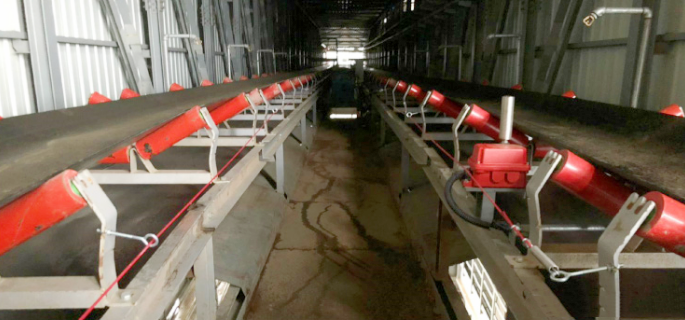
Boost your efficiency with our top conveyor belts.
How Self-Tracking Conveyor Belts Solve Tracking Issues
Self-tracking conveyor belts offer a revolutionary approach to addressing the age-old problem of belt misalignment. Unlike traditional methods that often require manual intervention, these belts are designed with a self-adjusting mechanism that ensures they remain aligned, thus significantly reducing downtime and maintenance costs.
Detailed Explanation of the Self-Adjusting Mechanism
The self-adjusting mechanism of a self-tracking conveyor belt includes several key components and design features that work together to maintain alignment:
- Edge Guides: Some self-tracking belts are designed with built-in edge guides that gently steer the belt back to the center if it begins to drift.
- Tapered Rollers: These rollers are shaped to guide the belt towards the center. As the belt starts to move off-center, it contacts a larger diameter of the roller, which nudges it back to its intended path.
- Unique Belt Design: The belt itself may have a special design, such as a curved or ridged surface, that interacts with the rollers to facilitate self-tracking.
- Differential Tension: The belt can be designed to create differential tension across its width, which naturally corrects any misalignment without external intervention.
- Smart Sensors: In more advanced systems, sensors detect the belt’s position and automatically adjust rollers or other components to correct the belt’s path.
- Automated Adjustment Mechanisms: These mechanisms respond to sensor inputs or the belt’s movement to make real-time adjustments, ensuring continuous alignment.
- Responsive Material: The belt material itself may possess qualities that contribute to self-tracking, such as flexibility that responds to minor shifts in direction or tension.
Comparison with Traditional Conveyor Belt Tracking Methods
Illustrating the Self-Tracking Mechanism in Action
Imagine a conveyor belt that begins to drift to one side. In a traditional system, this would require a stoppage and manual realignment. However, with a self-tracking conveyor belt, the moment the belt begins to drift, its edge design activates. If the belt drifts left, the left edge encounters slightly more resistance, triggering the belt to autonomously adjust back towards the center. This self-correction happens continuously and subtly, ensuring the belt remains aligned without any external input.
This mechanism is not just about preventing misalignment; it’s about creating a system that is inherently stable and self-correcting, reducing wear on the belt and the conveyor system, and improving operational efficiency. The self-tracking conveyor belt represents a significant step forward in conveyor technology, offering a smarter, more reliable, and cost-effective solution to one of the industry’s most persistent challenges.
Basic Conveyor Belt Tracking Rules
Tracking items on a conveyor belt involves several key rules and principles to ensure efficient and accurate operations. Here are some basic rules:
- Spacing: Maintain consistent spacing between items to prevent jamming and ensure smooth operation. The spacing depends on the type of items and conveyor system used.
- Speed: Monitor and adjust the conveyor belt speed based on the type of items being transported and the processing requirements. Different items may require different speeds for optimal handling.
- Alignment: Ensure that items are aligned properly on the belt. Misalignment can cause items to fall off or become jammed.
- Sensors and Cameras: Utilize sensors and cameras for tracking and sorting items. These devices can help detect the presence, position, and orientation of items on the belt.
- Weight Detection: Implement weight sensors if necessary to track the weight of items. This can be crucial for quality control and sorting processes.
- Sorting Mechanisms: Incorporate sorting mechanisms like diverters, pushers, or gates to direct items to different destinations based on their attributes.
- Maintenance: Regularly maintain the conveyor belt system to prevent breakdowns and ensure smooth operation. This includes checking for wear and tear, cleaning, and lubricating parts.
- Safety: Follow safety protocols to protect workers and equipment. This includes using guards, emergency stop buttons, and training employees on safe operation procedures.
- Data Logging: Keep track of data such as item counts, processing times, and errors. This information is useful for analyzing performance and making improvements.
- Integration: Ensure that the conveyor belt system is integrated with other systems, such as inventory management and production control, for seamless operation.
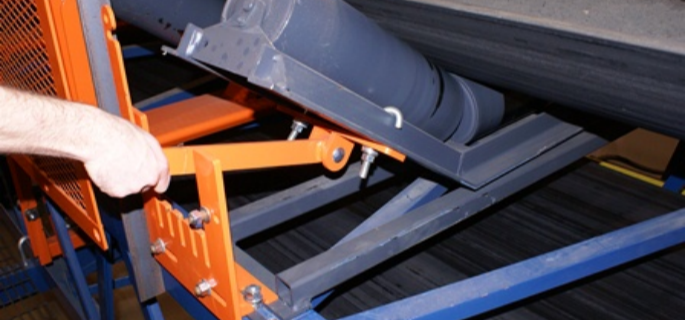
Applications of Self-Tracking Conveyor Belts
Self-tracking conveyor belts have revolutionized various industries by providing a reliable solution to the common problem of belt misalignment. Their unique self-adjusting mechanism not only enhances operational efficiency but also significantly reduces maintenance costs. Below are six specific applications where self-tracking conveyor belts have proven to be particularly beneficial, accompanied by examples of successful implementations.
Agricultural Waste Drying
Application: In the agricultural sector, drying processes for waste products like wood chips and shavings are critical for creating value-added products. These processes require conveyor belts that can handle varying loads and moisture levels without compromising alignment.
Case Study: A leading agricultural processing plant implemented a self-tracking conveyor belt system for their woodchip drying operation. The self-tracking feature ensured consistent alignment despite the heavy, uneven loads, resulting in a 20% increase in throughput efficiency and a significant reduction in downtime for maintenance.
Polymer Extrusion
Application: The polymer extrusion process involves the cooling of extruded polymer tubes before further processing. Traditional belts often lead to tubes sticking together due to close placement and high temperatures.
Case Study: A manufacturer of high-temperature engineering polymers switched to a self-tracking conveyor belt equipped with flighted inserts. This solution mechanically separated the tubes, preventing them from sticking together and increasing the yield by 15% while reducing product waste.
Food Processing
Application: Food processing often involves the transport of products that can easily cause misalignment due to their varying sizes and weights. Conveyor belts in such environments need to be highly reliable and easy to clean.
Case Study: A large bakery installed self-tracking conveyor belts in their dough shaping and cutting line. The belts’ self-aligning properties eliminated the frequent stoppages for manual adjustments, improving production line efficiency by 25% and ensuring consistent product quality.
Packaging and Distribution
Application: Packaging lines and distribution centers require conveyor systems that can adapt to a wide range of package sizes and weights without losing alignment, which could disrupt the sorting and distribution process.
Case Study: An e-commerce fulfillment center adopted self-tracking conveyor belts for their sorting lines. The improved alignment reduced package jams and mis-sorts by 30%, enhancing overall operational efficiency and customer satisfaction.
Mining and Quarrying
Application: The harsh conditions of mining and quarrying operations demand conveyor belts that can withstand heavy loads, abrasive materials, and significant vibrations without misalignment.
Case Study: A quarry implemented self-tracking conveyor belts for transporting crushed stone from the crusher to the storage area. The belts’ durability and self-aligning capabilities led to a 40% reduction in maintenance costs and a 10% increase in material transport efficiency.
Automotive Manufacturing
Application: Automotive assembly lines utilize conveyor belts for the efficient movement of parts and vehicles through various stages of assembly. Precise belt alignment is crucial to maintain the strict timing and sequencing of operations.
Case Study: An automotive manufacturer integrated self-tracking conveyor belts into their assembly line, significantly reducing the incidence of stoppages due to belt misalignment. This change resulted in a smoother production flow and a 5% increase in assembly line speed, directly impacting overall production capacity.
These applications and case studies demonstrate the versatility and effectiveness of self-tracking conveyor belts across a wide range of industries. By solving the persistent issue of belt misalignment, these belts enhance operational efficiency, reduce maintenance costs, and improve product quality and safety.
Choosing the Right Self-Tracking Conveyor Belt
Selecting the right self-tracking conveyor belt is crucial for ensuring optimal performance, efficiency, and longevity of your conveyor system. Various factors must be considered to make an informed decision that meets your specific operational needs. Here are seven key factors to consider when selecting a self-tracking conveyor belt:
Factors to Consider
- Material: The type of material the belt is made from is critical, as it needs to be suitable for the products it will carry and the environment it will operate in. Options range from rubber and PVC to more specialized materials for high temperature or food-grade applications.
- Width: The width of the belt should match the size of the products being transported and the capacity requirements of the system. Ensure the belt width is compatible with your conveyor’s design and operational needs.
- Application Requirements: Consider the specific demands of your application, including temperature range, chemical exposure, and the need for features like anti-static properties.
- Load Capacity: Evaluate the maximum load the belt must support. A self-tracking conveyor belt must be capable of handling your operation’s peak load without compromising its tracking capabilities.
- Speed: The operational speed of the conveyor belt should align with your production requirements. Ensure the belt can maintain effective tracking at your desired speed.
- Environment: Factors such as exposure to water, oils, chemicals, and extreme temperatures can affect the performance of a conveyor belt. Choose a belt designed to withstand your operational environment.
- Maintenance and Durability: Consider the maintenance requirements and durability of the belt. A self-tracking conveyor belt should offer low maintenance needs and a long service life to maximize your investment.
Overview of Manufacturers
- Intralox: Known for their innovative modular plastic belting solutions, Intralox offers self-tracking conveyor belts that excel in food processing applications, providing easy cleaning and maintenance.
- Habasit: Habasit’s range of fabric-based conveyor belts includes self-tracking options designed for versatility and durability, making them suitable for a wide range of industrial applications.
- Ammeraal Beltech: Specializing in synthetic belts, Ammeraal Beltech offers self-tracking belts that are highly customizable for specific application needs, including high-temperature and food-grade environments.
- Forbo Siegling: Forbo Siegling stands out for their comprehensive range of conveyor and processing belts, including self-tracking designs that offer reliability and efficiency for logistics and packaging applications.
- Wire Belt Company: Wire Belt Company offers metal conveyor belts with self-tracking capabilities, ideal for applications requiring high strength, temperature resistance, and hygiene, such as in the baking and food processing industries.
When choosing a self-tracking conveyor belt, it’s essential to consider these factors and review the offerings of various manufacturers to find a solution that best fits your specific needs. Each manufacturer has unique strengths and specialties, so selecting a provider that aligns with your operational requirements and offers reliable support and service is crucial for ensuring the success of your conveyor system.
Self Tracking Conveyor Belt’s Installation and Maintenance
The successful operation of a self-tracking conveyor belt system not only depends on its innovative design but also on proper installation and diligent maintenance practices. Ensuring that these belts are correctly installed and maintained is crucial for maximizing their efficiency and longevity. Here, we provide comprehensive guidelines for the installation and maintenance of self-tracking conveyor belts, along with insights into the conveyor belt alignment procedure as it relates to these advanced systems.
Guidelines for Installing Self-Tracking Conveyor Belts
- Assess Conveyor Frame Alignment: Before installation, ensure the conveyor frame is level and square. An improperly aligned frame can hinder the self-tracking feature of the belt.
- Install According to Manufacturer’s Instructions: Follow the specific guidelines provided by the manufacturer, as installation procedures may vary slightly depending on the belt design.
- Ensure Proper Tensioning: A correctly tensioned belt is essential for the self-tracking feature to function. Too much or too little tension can lead to tracking issues.
- Check Pulley and Roller Alignment: Pulleys and rollers should be perfectly aligned with the conveyor frame to support the belt’s self-tracking mechanism effectively.
- Initial Testing: Run the conveyor belt empty for several cycles to allow the self-tracking mechanism to adjust and settle. Observe and make minor adjustments as needed.
Tips for Maintaining Self-Tracking Conveyor Belts
- Regular Inspections: Conduct regular inspections to identify and rectify any potential issues before they escalate, focusing on belt wear, pulley alignment, and tension.
- Cleanliness is Key: Keep the belt and conveyor components clean to prevent debris from interfering with the belt’s tracking.
- Monitor Belt Tension: Periodically check the belt tension to ensure it remains within the manufacturer’s recommended range.
- Check for Wear and Damage: Inspect the belt for signs of wear or damage, particularly along the edges where the self-tracking features are often located.
- Lubricate Moving Parts: Proper lubrication of rollers, pulleys, and other moving parts can reduce friction and wear, supporting the belt’s self-tracking mechanism.
- Avoid Overloading: Consistently overloading the conveyor can stress the self-tracking mechanism and lead to premature wear.
- Update Training Procedures: Ensure that maintenance staff are trained on the specific requirements for maintaining self-tracking conveyor belts.
- Use Genuine Parts for Repairs: When repairs are necessary, use genuine parts from the belt manufacturer to maintain the integrity of the self-tracking features.
Conveyor Belt Alignment Procedure and Self-Tracking Belts
The conveyor belt alignment procedure is simplified with self-tracking conveyor belts. Traditional alignment methods often require manual adjustments to idlers and tracking rollers to correct misalignment. However, self-tracking conveyor belts are designed to automatically adjust their path towards the centerline of the conveyor, reducing the need for manual intervention.
- Initial Alignment: During installation, ensure the conveyor frame, pulleys, and rollers are aligned as this forms the foundation for the self-tracking belt to operate effectively.
- Observe and Adjust: After installation, observe the belt’s operation. Initial minor adjustments may be needed to optimize the self-tracking feature.
- Ongoing Monitoring: While the self-tracking mechanism significantly reduces the need for manual adjustments, regular monitoring ensures the system continues to operate efficiently.
Self-tracking conveyor belts streamline the alignment process, offering a more efficient and low-maintenance solution to conveyor belt tracking issues. By following these installation and maintenance guidelines, businesses can ensure their conveyor systems operate smoothly, maintaining high levels of productivity and operational reliability.
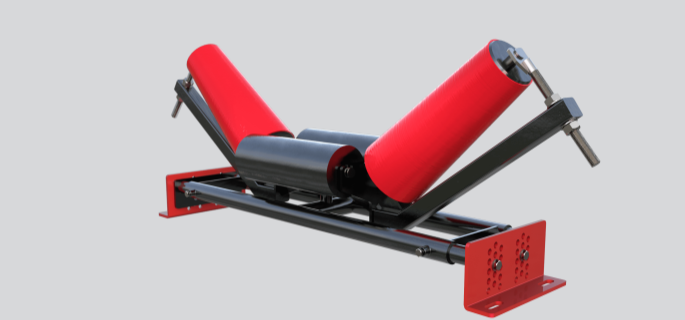
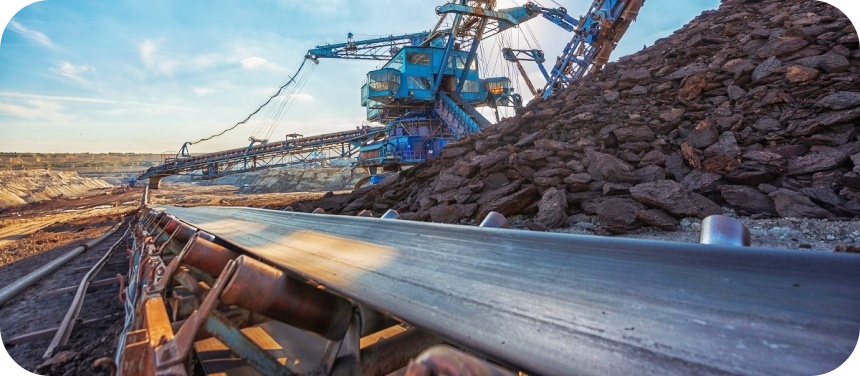
Troubleshooting Common Issues with Self-Tracking Conveyor Belts
Even with the advanced technology behind self-tracking conveyor belts, certain issues can arise during their operation. Understanding how to troubleshoot these problems effectively can help maintain the efficiency and longevity of your conveyor system. Here are ten common issues encountered with self-tracking conveyor belts and how to address them, along with insights on adjusting the belt and the role of tracking rollers.
Common Issues and Troubleshooting Tips
- Belt Drifts to One Side: Check for debris or material buildup on the rollers or pulley that could hinder the belt’s ability to self-track. Clean the affected components thoroughly.
- Excessive Wear on Edges: Inspect for misaligned rollers or pulleys that may cause the belt to rub against the conveyor frame. Adjust the alignment of these components.
- Slipping Belt: Ensure that the belt tension is correctly adjusted. A belt that’s too loose can slip off the drive pulley.
- Belt Not Centering Automatically: Verify that the conveyor frame is level and square. An uneven frame can affect the self-tracking feature.
- Material Spillage: Check the loading zone to ensure materials are being loaded centrally onto the belt. Off-center loading can disrupt the belt’s ability to track properly.
- Increased Energy Consumption: Inspect for bearings in rollers and pulleys that may need lubrication or replacement. Friction from faulty bearings can increase power consumption.
- Noise During Operation: Identify the source of the noise, which could indicate a misaligned roller or a damaged belt section. Replace or adjust as necessary.
- Reduced Tracking Efficiency Over Time: Conduct a comprehensive inspection of the belt and conveyor system for wear and tear. Replace worn parts and adjust tension as needed.
- Belt Tension Issues: Regularly check belt tension and adjust according to the manufacturer’s specifications to ensure optimal performance.
- Accumulation of Debris Underneath the Belt: Keep the conveyor and surrounding area clean to prevent debris from interfering with the self-tracking mechanism.
Adjusting the Belt to Run Straight
The self-tracking feature of these belts typically requires minimal adjustment. However, if the belt needs re-centering, ensure that the conveyor frame is level and that all rollers and pulleys are properly aligned. For minor adjustments, refer to the manufacturer’s guidelines, as some belts may allow for slight tension modifications to enhance the self-tracking capability.
Roles of Conveyor Belt Tracking Rollers
- Supporting the Belt: Tracking rollers provide essential support, helping to distribute the load evenly across the belt.
- Maintaining Alignment: They play a crucial role in guiding the belt back to its central path, especially in the initial stages of operation or after maintenance work.
- Reducing Wear and Tear: By ensuring that the belt remains aligned, tracking rollers help minimize edge wear and extend the belt’s lifespan.
- Enhancing Performance: Properly functioning tracking rollers contribute to the smooth and efficient operation of the conveyor system.
- Preventing Material Spillage: By keeping the belt aligned, tracking rollers help prevent spillage that can occur when the belt drifts.
- Facilitating Automatic Adjustments: In conjunction with the self-tracking feature of the belt, tracking rollers ensure that any minor misalignments are corrected automatically, maintaining optimal performance without manual intervention.
Understanding these common issues and the role of tracking rollers can help ensure that your self-tracking conveyor belt operates efficiently, minimizing downtime and maintaining productivity. Regular inspection and maintenance, aligned with the manufacturer’s guidelines, are key to the long-term success of your conveyor system.
Boost your efficiency with our top conveyor belts.
The Future of Conveyor Belt Technology
The evolution of conveyor belt technology has been marked by significant advancements aimed at enhancing efficiency, safety, and operational effectiveness in various industries. From the early days of manual belt operation and maintenance to the introduction of automated systems, the journey has been transformative. Today, the focus is increasingly on automation, smart systems, and the integration of advanced materials and sensors to create more intelligent, self-regulating conveyor solutions. Among these innovations, self-tracking conveyor belts stand out as a pivotal development, signaling a move towards more autonomous and reliable material handling systems.
Evolution Towards Automation and Smart Systems
The trend towards automation and the use of smart systems in conveyor technology is driven by the need for higher efficiency, reduced downtime, and minimal human intervention. Modern conveyor systems are being equipped with sensors and IoT (Internet of Things) technology to monitor performance in real-time, predict maintenance needs, and even adjust operations dynamically based on the data received. This shift not only improves operational efficiency but also enhances safety by reducing the need for manual adjustments and inspections in potentially hazardous environments.
The Potential for Automatic Conveyor Belt Tracking Systems
Self-tracking conveyor belts represent a significant step towards the realization of fully automatic conveyor belt tracking systems. These belts, equipped with self-adjusting mechanisms, pave the way for conveyor systems that require minimal human intervention to maintain optimal alignment and performance. The potential benefits of such systems are vast, including:
- Increased Efficiency: Automatic adjustments to belt alignment reduce downtime and increase throughput.
- Reduced Maintenance Costs: With less need for manual adjustments and repairs, maintenance costs can be significantly lowered.
- Enhanced Safety: Reducing the need for human interaction with moving parts lowers the risk of accidents and injuries.
- Longer Equipment Lifespan: By ensuring optimal operation and reducing wear and tear, the lifespan of conveyor components can be extended.
Impact on Industry
The adoption of self-tracking conveyor belts and the further development of automatic tracking systems are set to have a profound impact on various industries. In sectors such as mining, manufacturing, logistics, and food processing, where conveyor systems play a critical role, these technologies can lead to substantial productivity gains, cost savings, and safety improvements. As industries continue to embrace automation and smart technologies, conveyor systems will become even more integral to operational success, with self-tracking conveyor belts at the forefront of this evolution.
The future of conveyor belt technology is intrinsically linked to the advancement of self-tracking conveyor belts and the development of fully automated tracking systems. These innovations promise to redefine the efficiency, safety, and reliability of material handling across a broad spectrum of industries, marking a new era in conveyor technology.
FAQs about Self-Tracking Conveyor Belt
Conveyor belt tracking is the process of ensuring that a conveyor belt remains aligned and centered during operation. Proper tracking prevents the belt from drifting off to one side, which can lead to several operational issues, such as uneven belt wear, damage to the belt edges, material spillage, and decreased efficiency of the conveyor system. Effective belt tracking is achieved through the precise alignment of conveyor rollers and pulleys and maintaining the correct belt tension. It’s a critical aspect of conveyor belt maintenance that ensures smooth operation, prolongs the lifespan of the belt, and supports the safety and productivity of material handling operations. Conveyor belt tracking is not just about fixing misalignment; it’s about preventing it through proper installation, regular maintenance, and adjustments as needed to accommodate changes in load and operational conditions.
A tracked conveyor refers to a conveyor system that is designed with a mechanism to automatically keep the conveyor belt aligned with the conveyor’s structural frame. This type of conveyor utilizes guide tracks, edges, or other mechanisms to ensure that the belt does not drift sideways during operation. Tracked conveyors are particularly useful in applications where the conveyor path has curves, where the belt is subjected to side-loading, or in environments where maintaining manual alignment would be challenging or labor-intensive. The tracking feature is integral to the conveyor’s design, enhancing reliability, reducing maintenance requirements, and improving operational efficiency. By minimizing belt misalignment, tracked conveyors help prevent material spillage, reduce wear and tear on the belt, and ensure consistent material flow, making them an essential solution in many industrial and manufacturing settings.
An automatic conveyor belt refers to a conveyor system that operates with minimal human intervention, thanks to the integration of automated control systems. These conveyors are equipped with sensors, motors, and control units that enable them to start, stop, regulate speed, adjust direction, and even track the belt’s alignment automatically. Automatic conveyor belts can be programmed to operate according to specific operational schedules, respond to real-time data inputs (such as load size and weight), and adjust their operations dynamically to optimize efficiency and productivity. The automation of conveyor belts not only enhances operational efficiency but also improves safety by reducing the need for direct human interaction with the conveyor during operation. Automatic conveyor belts are widely used in various industries, including manufacturing, packaging, logistics, and material handling, where they contribute to streamlined processes, reduced labor costs, and increased throughput.
Keeping a conveyor belt on track involves several key practices and adjustments to ensure that the belt remains centered and aligned with the conveyor frame. Here are some strategies:
Ensure Proper Installation: The conveyor frame, rollers, and pulleys must be installed level and square to the direction of belt travel. Misalignment of these components can cause the belt to track off-center.
Maintain Correct Belt Tension: Both over-tensioning and under-tensioning can lead to tracking problems. Follow the manufacturer’s recommendations to adjust the tension correctly.
Regularly Inspect and Clean the Conveyor: Debris, material buildup, and wear can affect belt tracking. Regular cleaning and inspection can identify and rectify issues before they lead to misalignment.
Adjust the Rollers and Pulleys: Misaligned rollers and pulleys can steer the belt off its intended path. They should be adjusted to ensure they are perpendicular to the belt’s direction of travel.
Use Self-Tracking Belts: Consider using self-tracking conveyor belts designed with edges or guiding mechanisms that automatically correct any deviation in the belt’s path.
Implement Tracking Devices: For challenging applications, additional tracking devices such as guide rollers or tracking frames can be installed to assist in keeping the belt aligned.
Last Updated on July 23, 2024 by Jordan Smith
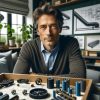
Jordan Smith, a seasoned professional with over 20 years of experience in the conveyor system industry. Jordan’s expertise lies in providing comprehensive solutions for conveyor rollers, belts, and accessories, catering to a wide range of industrial needs. From initial design and configuration to installation and meticulous troubleshooting, Jordan is adept at handling all aspects of conveyor system management. Whether you’re looking to upgrade your production line with efficient conveyor belts, require custom conveyor rollers for specific operations, or need expert advice on selecting the right conveyor accessories for your facility, Jordan is your reliable consultant. For any inquiries or assistance with conveyor system optimization, Jordan is available to share his wealth of knowledge and experience. Feel free to reach out at any time for professional guidance on all matters related to conveyor rollers, belts, and accessories.