Measuring Success: Conveyor Belt Density Explained
Conveyor belts play a pivotal role in a myriad of industries, streamlining operations in sectors as diverse as mining, agriculture, pharmaceuticals, and food processing. These belts are the lifelines of production lines, ensuring the seamless flow of materials and products across stages of manufacturing and distribution. Amidst various factors that contribute to the optimal functionality of conveyor belts, conveyor belt density stands out for its critical importance. This parameter not only dictates the strength and durability of the conveyor belt but also influences its ability to handle different weights and types of materials. Understanding the significance of conveyor belt density is essential for industry professionals to make informed decisions regarding belt selection, maintenance, and overall system efficiency, ensuring that the chosen conveyor belt meets the specific demands of their operational environment.
What Is Conveyor Belt Density
“Conveyor belt density” is a crucial parameter that significantly impacts the functionality and longevity of conveyor systems. It refers to the mass of the conveyor belt material per unit volume and is typically measured in kilograms per cubic meter (kg/m³). This density is determined by the type of conveyor belt material used in the belt’s construction, such as rubber, fabric, or metal, and the specific composition of these materials.
The role of “Conveyor belt rubber density” is particularly significant as it directly influences the belt’s strength and durability. A higher density usually implies a more robust and durable belt capable of handling heavy loads and resisting wear and tear over time. However, it’s essential to balance density with flexibility, as a very dense belt might be less adaptable to certain conveyor configurations or environmental conditions.
Density also plays a pivotal role in how a conveyor belt performs under different environmental conditions. For instance, belts with a higher density are generally more resistant to impacts, abrasions, and cuts, making them suitable for industries where sharp or heavy materials are transported. Conversely, in cold environments, a belt with lower density might perform better as it can retain more flexibility and resist cracking.
Understanding conveyor belt density is vital for selecting the right belt for specific applications, ensuring that the conveyor system operates efficiently, safely, and cost-effectively. It allows engineers and operators to predict how a belt will behave under various loads and environmental conditions, ensuring the longevity and reliability of the conveyor system.
Conveyor Belt Specifications Standards and Conveyor Belt Density

When it comes to ensuring the optimal performance and safety of conveyor systems, adhering to established “conveyor belt specifications standards” is paramount. These standards provide a framework for the design, testing, and application of conveyor belts, ensuring that they meet the required criteria for safety, efficiency, and compatibility across various industries.
One critical aspect covered by these standards is conveyor belt density. This specification is crucial as it directly impacts the belt’s strength, durability, and overall performance. The density of a conveyor belt is determined by its material composition and construction, which in turn influences its ability to handle different loads and operate under varying environmental conditions.
International standards such as ISO 14890 for general-purpose conveyor belts and ISO 15236 for steel cord conveyor belts outline specific requirements for physical, mechanical, and chemical properties of conveyor belt materials. These standards ensure that belts are capable of performing in the demanding conditions they are subjected to, from heavy industrial loads to extreme weather conditions.
Adhering to these specifications standards, including those related to “density of conveyor belt,” is essential for several reasons:
- Safety: Ensuring that conveyor belts meet international standards minimizes the risk of accidents and injuries in the workplace.
- Efficiency: Standard-compliant belts are designed to optimize performance, reducing downtime and maintenance requirements.
- Compatibility: Following established standards ensures that conveyor belts can be seamlessly integrated into existing systems, regardless of the manufacturer or design.
Understanding and adhering to “conveyor belt specifications standards,” particularly those related to “density of conveyor belt,” is crucial for the safe, efficient, and effective operation of conveyor systems. These standards provide a benchmark for quality and performance, ensuring that conveyor belts meet the rigorous demands of various industrial applications.
Calculating Conveyor Belt Weight and What Is Conveyor Belt Density
The process of calculating conveyor belt weight is integral to the design, selection, and performance optimization of conveyor systems. The weight of a conveyor belt is determined by its volume and the conveyor belt density of the materials used in its construction. The formula for calculating the weight of a conveyor belt is essentially the product of its volume and density: Weight = Volume x Density.
To simplify this calculation, industry professionals often use a “conveyor belt weight calculator,” a tool that automates the process by considering the belt’s dimensions (length, width, and thickness) and the density of the material. The density is a critical factor here, as it varies based on the type of material (rubber, fabric, steel, etc.) and the specific composition of the conveyor belt.
The weight per meter of the conveyor belt is a crucial metric that impacts both the selection and performance of conveyor belts. A heavier belt, implied by higher conveyor belt density, may offer more durability and strength, suitable for heavy-duty applications. However, it also requires more power to operate and may put additional stress on the conveyor system’s structure and components.
A lighter belt may be more energy-efficient and easier to install and maintain but might not be suitable for transporting heavy or abrasive materials. Therefore, understanding the relationship between density of conveyor belt and the resulting weight per meter is essential for selecting a belt that meets the specific needs of an application while ensuring operational efficiency and longevity.
Practical Guide to Conveyor Belt Selection: Focusing on Conveyor Belt Density
When selecting a conveyor belt for your system, it’s crucial to consider various factors that impact its performance and suitability for your specific needs. Here, we delve into five key considerations, emphasizing the critical role of conveyor belt density:

Material Handling Requirements: The nature of the materials being transported is the foremost consideration. Assess the weight, abrasiveness, size, and shape of the materials, as these characteristics dictate the required density of conveyor belt for durability and efficiency. Heavier and more abrasive materials necessitate belts with higher density to withstand wear and tear.
Application and Usage: The intended use of the conveyor system significantly influences belt selection. Different applications, from heavy industrial use to delicate food processing, demand specific belt properties. Conveyor belt density plays a pivotal role in determining the belt’s ability to meet these application-specific requirements.
Environmental Influences: The operating environment can greatly affect conveyor belt performance. Factors such as temperature extremes, chemical exposure, and moisture levels must be considered. A suitable conveyor belt density ensures the belt material maintains its integrity and functionality under these environmental conditions.
System Design Considerations: The physical layout and design of the conveyor system, including length, inclines, and curves, require belts that can accommodate such configurations without compromising performance. The conveyor belt density must align with the system’s design to ensure the belt can handle the associated stresses and strains.
Operational Demands: Operational aspects such as desired speed, load capacity, and maintenance protocols influence belt selection. The density of conveyor belt should support these operational demands, ensuring the belt can sustain the expected load and speed while being durable and manageable in terms of maintenance.
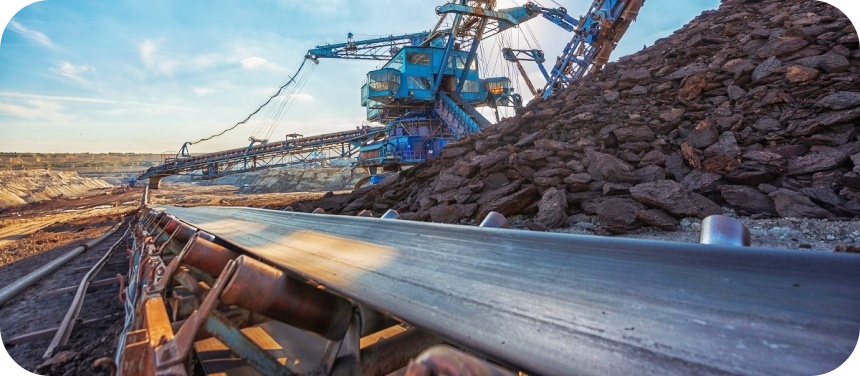
To make informed decisions based on conveyor belt density and other specifications, consider employing the following methods:
- Technical Data Sheets: Manufacturers provide data sheets detailing the specifications of different conveyor belts, including their density. Review these sheets to understand how a belt’s density correlates with its strength, flexibility, and durability.
- Consultation with Experts: Engage with conveyor belt specialists or manufacturers who can offer insights into how density of conveyor belt affects performance in various applications and environments.
- Performance Testing: Where possible, evaluate the performance of different conveyor belts in a controlled environment to observe firsthand how conveyor belt density influences their efficiency and durability.
- Case Studies and References: Look into case studies or seek references from businesses with similar conveyor system requirements. Their experiences can provide valuable insights into the practical implications of density of conveyor belt.
By thoroughly considering these factors and employing methodical approaches to assess conveyor belt density and other critical specifications, you can select a conveyor belt that best suits your specific needs, ensuring optimal performance and longevity of your conveyor system.
Case Studies: The Impact of Conveyor Belt Density on System Efficiency and Safety
The significance of density of conveyor belt in determining the efficiency and safety of conveyor systems is best illustrated through real-world applications across various industries. Here, we explore a few case studies that highlight the critical role of conveyor belt density and specifications:
Mining Industry Case Study: XYZ Mining Co.

Challenge: XYZ Mining Co. faced frequent belt failures, leading to costly downtime and safety hazards due to the heavy and abrasive nature of the materials being transported.
Solution: After a thorough analysis, it was determined that the density of the conveyor belt was not suitable for the heavy load and abrasive conditions. XYZ Mining Co. switched to a conveyor belt with higher density and enhanced abrasion-resistant properties supplied by HeavyDuty Belts Inc.
Outcome: The new belt with higher conveyor belt density led to a significant reduction in failures, increased operational efficiency, and improved safety, showcasing the importance of selecting a belt with the right density for heavy-duty applications.
Food Processing Industry Case Study: FreshFoods Processing Inc.
Challenge: FreshFoods Processing Inc. struggled with maintaining hygiene standards due to the porous nature of their conveyor belts, which led to contamination risks.
Solution: The plant opted for a conveyor belt with a higher conveyor belt density made from non-porous materials, specifically designed for food applications, provided by CleanBelt Technologies, to prevent contamination.
Outcome: The higher conveyor belt density belt improved cleanliness, reduced contamination risks, and complied with food safety regulations, highlighting the role of belt density in maintaining hygiene standards in the food industry.
Packaging Industry Case Study: PackMaster Ltd.
Challenge: PackMaster Ltd. experienced inefficiencies due to the conveyor belt’s inability to handle varying weights of packages, leading to frequent jams and slowdowns.
Solution: Analysis revealed that the conveyor belt density was too low to provide the necessary flexibility and strength for the range of package weights. PackMaster Ltd. selected a belt with a more suitable density from FlexiConveyor Systems to accommodate the diverse load requirements.
Outcome: The new belt with an optimized conveyor belt density enhanced the system’s adaptability to different package weights, improving throughput and reducing downtime, underscoring the importance of density in versatile applications.
Automotive Manufacturing Case Study: AutoPrecision GmbH
Challenge: AutoPrecision GmbH faced issues with conveyor belt wear and tear, affecting the precision placement of parts and overall assembly efficiency.
Solution: The underlying issue was identified as the inadequate density of the conveyor belt for the high-precision, high-stress environment of automotive assembly. AutoPrecision GmbH implemented a higher density belt designed for durability and precision from AutoBelt Solutions.
Outcome: The upgrade to a conveyor belt with higher conveyor belt density resulted in improved durability, reduced maintenance, and enhanced assembly precision, demonstrating the impact of belt density on performance in precision-demanding environments.
These case studies across diverse industries underscore the pivotal role of density of conveyor belt in ensuring the efficiency, safety, and reliability of conveyor systems. They highlight the necessity of carefully considering conveyor belt specifications, particularly density, to meet the unique demands of different applications and environments.
Practical Applications and Design Considerations for Conveyor Belt Density
Material Handling Requirements
Understanding the specific material handling requirements is crucial when selecting the appropriate conveyor belt density. Different materials have unique characteristics that directly impact the performance and durability of the conveyor belt. Here are several factors to consider:
Material Characteristics:
- Weight: Heavier materials require belts with higher density to support the increased load without excessive sagging or stretching. A belt with inadequate density can fail prematurely under heavy loads.
- Size and Shape: Bulkier and irregularly shaped materials can exert uneven pressure on the belt. Choosing a belt with the appropriate density ensures that it can handle the impact and abrasion from such materials.
- Abrasiveness: Materials with abrasive properties, such as minerals or metals, can wear down the belt surface quickly. A higher density belt typically offers better resistance to abrasion, extending the lifespan of the belt.
- Moisture Content: Wet or sticky materials can add significant weight and cause additional stress on the belt. Conveyor belts with a higher density are better equipped to handle these conditions without excessive wear or slippage.
Assessing these characteristics helps in selecting a conveyor belt density that matches the specific needs of the material being transported, ensuring efficient and reliable operation.
Environmental Factors
Environmental factors play a significant role in determining the suitable conveyor belt density. The operational conditions can affect the belt’s performance and durability. Here are key environmental considerations:
Temperature:
- High Temperatures: In environments with high temperatures, such as industrial ovens or furnaces, belts with higher density materials like Polypropylene (PP) or specialized high-temperature polymers are necessary. These materials can withstand high temperatures without degrading.
- Low Temperatures: For cold storage or freezer applications, belts made from materials like Polyethylene (PE), which remain flexible at low temperatures, are ideal. The density of the belt must be sufficient to handle the cold environment without becoming brittle.
Chemical Exposure:
- Corrosive Chemicals: In industries where belts are exposed to chemicals, such as in chemical processing or food processing with aggressive cleaning agents, materials like Polyacetal (POM) are preferred due to their chemical resistance. The density of the belt influences its ability to resist chemical degradation.
- Hygiene Requirements: In food processing or pharmaceutical industries, belts need to be easy to clean and resistant to microbial growth. FDA-approved materials with appropriate density ensure that the belts meet hygiene standards and are durable enough for regular cleaning.
By considering these environmental factors, you can select a conveyor belt density that ensures the belt will perform reliably under the specific conditions it will encounter.
System Design Integration
Ensuring that the chosen conveyor belt density aligns with the overall system design is vital for optimal performance. Here are several aspects to consider:
Load Capacity:
- The conveyor system’s design must account for the maximum load the belt will carry. A belt with the appropriate density will be able to handle the expected loads without excessive stretching or deformation. This is crucial for maintaining the belt’s integrity and preventing system failures.
Belt Tension and Alignment:
- Proper tension and alignment are critical for smooth conveyor operation. A belt with the right density maintains its shape and tension, ensuring that it runs smoothly on the rollers and pulleys. Incorrect belt density can lead to misalignment issues, increased wear, and operational inefficiencies.
Speed and Incline:
- The speed at which the conveyor operates and any inclines in the system affect the choice of belt density. High-speed conveyors require belts that can handle the dynamic stresses involved. Similarly, inclined conveyors need belts with sufficient density to provide the necessary grip and prevent slippage.
System Compatibility:
- The conveyor belt density must be compatible with other system components such as rollers, pulleys, and drive systems. The belt should work seamlessly with these components to ensure efficient power transmission and material handling. Incompatible belt density can lead to increased wear on system components and reduced operational efficiency.
Maintenance and Durability:
- Selecting a conveyor belt with the right density reduces maintenance needs and extends the belt’s lifespan. A properly chosen belt density will withstand the operational stresses, reducing the frequency of replacements and downtime for maintenance.
By integrating the appropriate conveyor belt density into the system design, you ensure that the conveyor operates efficiently, reliably, and safely. This comprehensive approach leads to improved performance, reduced maintenance costs, and enhanced productivity.
Considering material handling requirements, environmental factors, and system design integration is essential when selecting the appropriate conveyor belt density. This ensures that the belt can handle the specific demands of the application, leading to a more efficient, durable, and reliable conveyor system.
Your source for top conveyor belts – contact us now!
FAQs about Conveyor Belt Density
The density of a PVC (Polyvinyl Chloride) conveyor belt refers to the mass of the belt material per unit volume and is a critical factor in determining the belt’s strength, durability, and overall performance. PVC conveyor belts are known for their versatility and durability, making them suitable for a wide range of applications, from food processing to heavy-duty industrial use. The density of PVC material typically ranges from 1.2 to 1.4 grams per cubic centimeter (g/cm³), but this can vary based on the specific composition of the PVC material and any additives used to enhance its properties. The exact density of a PVC conveyor belt can also depend on the manufacturing process and the intended application of the belt. Higher density PVC belts are generally more durable and resistant to wear and tear, making them suitable for more demanding applications.
Calculating the weight of a conveyor belt involves determining the volume of the belt material and multiplying it by the density of the material. The formula for calculating the weight of a conveyor belt is: Weight = Volume x Density. To find the volume, you need to multiply the belt’s length, width, and thickness. Once you have the volume in cubic meters (or another unit of measure), you multiply it by the density of the belt material, which is typically given in kilograms per cubic meter (kg/m³) for rubber or PVC conveyor belts. This calculation provides the total weight of the conveyor belt. It’s important to note that the density of the belt material can vary based on its composition and any specific additives or treatments applied to meet certain operational requirements.
Calculating the TPH of a belt conveyor involves determining the volume of material that can be moved per unit of time and converting that volume into tons. The formula to calculate TPH is: TPH = (Belt Speed in m/s) x (Belt Width in meters) x (Material Density in kg/m³) x (Load Cross Section Area in m²) / 1000. The belt speed is how fast the belt moves, typically measured in meters per second. The belt width is the width of the belt in meters. The material density is the weight of the material per cubic meter, and the load cross-section area is the area of the material profile on the belt, which can be estimated based on the material’s surcharge angle and the belt width. This calculation provides an estimate of how many tons of material the conveyor can move per hour, which is crucial for designing and optimizing conveyor systems for specific applications.
The gradient of a conveyor belt, also known as the incline or slope, refers to the angle at which the conveyor belt is set to rise or fall along its path. It is typically measured in degrees or as a percentage. The gradient is a critical design parameter that affects the belt’s ability to transport materials efficiently without spillage or backslide. The maximum gradient a conveyor belt can handle depends on various factors, including the type of material being conveyed, the belt’s design, and the presence of cleats or sidewalls on the belt. For example, flat belts with no cleats may only be able to handle very gentle slopes, typically up to 18-20 degrees, while belts with cleats or profiles can handle steeper inclines, sometimes up to 30 degrees or more. The choice of gradient has significant implications for the conveyor’s design, operational efficiency, and the required power to move the material.
The density of a rubber conveyor belt typically ranges between 1.1 to 1.5 grams per cubic centimeter (g/cm³). This range can vary depending on the specific composition and type of rubber used. Rubber conveyor belts are commonly used in various industries due to their flexibility, durability, and resistance to wear and tear. The exact density can be influenced by factors such as the type of rubber (natural or synthetic), the presence of reinforcing materials, and any additional fillers or additives used in the manufacturing process. Understanding the density of a rubber conveyor belt is crucial for calculating the belt’s weight, which is important for designing and maintaining conveyor systems, ensuring they operate efficiently and safely.
The density of nylon conveyor belts generally falls within the range of 1.14 to 1.25 grams per cubic centimeter (g/cm³). Nylon, known for its high strength-to-weight ratio and excellent wear resistance, is often used in applications requiring robust and lightweight belt solutions. The density of nylon belts can be affected by the specific type of nylon used (such as Nylon 6 or Nylon 6/6) and the presence of reinforcing fibers or additional layers within the belt structure. Nylon belts are favored in industries where durability and reduced weight are critical, such as in the textile, automotive, and logistics sectors. Accurate knowledge of the belt density helps in the precise calculation of load capacities and the design of conveyor systems tailored to specific operational requirements.
The density of a polyurethane (PU) conveyor belt typically ranges from 1.2 to 1.25 grams per cubic centimeter (g/cm³). Polyurethane belts are valued for their excellent abrasion resistance, flexibility, and ability to operate under a wide range of temperatures. These characteristics make PU conveyor belts ideal for applications in the food processing, packaging, and pharmaceutical industries, where hygiene and performance are paramount. The density of PU conveyor belts can vary slightly depending on the specific formulation of the polyurethane used and the inclusion of any reinforcing materials. Understanding the density is essential for determining the belt’s weight, load-carrying capacity, and overall suitability for specific applications, ensuring efficient and reliable operation of the conveyor system.
Last Updated on June 21, 2024 by Jordan Smith
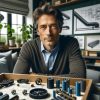
Jordan Smith, a seasoned professional with over 20 years of experience in the conveyor system industry. Jordan’s expertise lies in providing comprehensive solutions for conveyor rollers, belts, and accessories, catering to a wide range of industrial needs. From initial design and configuration to installation and meticulous troubleshooting, Jordan is adept at handling all aspects of conveyor system management. Whether you’re looking to upgrade your production line with efficient conveyor belts, require custom conveyor rollers for specific operations, or need expert advice on selecting the right conveyor accessories for your facility, Jordan is your reliable consultant. For any inquiries or assistance with conveyor system optimization, Jordan is available to share his wealth of knowledge and experience. Feel free to reach out at any time for professional guidance on all matters related to conveyor rollers, belts, and accessories.