Innovative Trough Carrier Impact Rollers for Better Conveyance
The trough carrier impact roller serves as a crucial part of heavy-duty industries such as mining, thanks to its vital role in the conveyor belt mechanism. Designed to cradle the belt, it enables the efficient movement of materials while enhancing the productivity of the conveying system. Formidably constructed to endure abrasive and substantial loads, trough carrier impact rollers provide resilience in harsh working environments. Successfully channeling the alignment and durability of conveyor systems, these rollers stand as an essential factor in optimizing bulk material transportation. By preventing spillage and ensuring even load distribution, they not only contribute to operational efficiency but also significantly extend the conveyor belt’s lifespan. Thus, the trough carrier impact roller is an indispensable component in the realm of material handling equipment.
The Crucial Function of Trough Carrier Impact Rollers in the Mining Industry
Trough carrier impact rollers play a significant role in various industries, notably in the mining sector. Their unique design and functionality make them indispensable components of conveyor systems, particularly in challenging and substantial load conditions typical of mining operations.
Utilizing Trough Carrier Impact Rollers in Mining Applications
Trough carrier impact rollers are at the heart of the mining industry’s material handling processes. Their principal function is to support conveyor belts, assisting in the transport of heavy materials across vast distances within a mining facility. They are designed to bear considerable weight, reducing wear and tear on the conveyor belt and ensuring that mining operations run smoothly and efficiently.
The structure of the trough carrier impact roller forms a trough that enables the conveyor belt to carry large amounts of material. This design significantly increases the carrying capacity of the system and ensures that materials are transported securely and safely, minimizing spillage.
How Trough Carrier Impact Rollers Support and Direct Conveyor Belts
A key component of the mining industry, the trough carrier impact roller, not only supports but also properly aligns and guides conveyor belts. They are strategically positioned along the conveyor belt pathway to ensure the belt’s consistent and reliable movement.
Trough carrier impact rollers have a direct influence on the direction of the conveyor belt, maintaining its path and reducing any misalignment. Though seemingly simple, these rollers are engineered precision tools that significantly contribute to the efficiency and reliability of mining operations. By maintaining the path and evenly distributing weight, these rollers help to extend the service life of the conveyor belt, further optimizing mining operations.
Importance of the trough carrier impact roller in the mining industry cannot be overstated. As crucial components ensuring efficient transport and handling of materials, they directly influence mining operations’ productivity and sustainability.
The Robust and Reliable Design of Trough Carrier Impact Rollers
The design of the trough carrier impact roller is a marvel of engineering, providing unmatched robustness and reliability to the conveyor systems they serve, especially within the challenging environments of industries like mining and quarrying. These rollers are specifically designed to ensure the continuous, smooth operation of conveyor belts, even under the most severe conditions, including extreme temperatures, dust, and water exposure.
Key Attributes of Trough Carrier Impact Rollers
The trough carrier impact roller is renowned for its several key attributes that underpin its effectiveness in adverse environments.
Key Attribute | Description |
---|---|
Temperature Resilience | Trough carrier impact rollers are built with materials that thrive in extreme temperatures, ensuring consistent operation from the intense heat of mining sites to the freezing conditions of cold quarries. |
Advanced Sealing Technologies | The rollers feature sophisticated seals that safeguard internal components from dust, water, and contaminants, thereby prolonging their functional lifespan and preserving the conveyor belt's integrity. |
Material and Construction Quality | Utilization of high-grade rubber compounds and durable alloys provides the rollers with the strength needed to handle heavy-duty applications and harsh conditions. |
Optimal Balance and Load Distribution | Precision engineering ensures optimal balance, which aids in even weight distribution across the conveyor belt, minimizing misalignment and reducing wear. |
Trough carrier impact roller embodies a combination of durability, reliability, and efficiency, making it an indispensable component in the seamless operation of material handling systems in adverse conditions. Through its innovative design and the use of cutting-edge materials, it stands as a testament to the advancements in industrial machinery and equipment.
Understanding Different Types of Trough Carrier Impact Rollers
The broad category of trough carrier impact rollers holds within a wide variety of purpose-specific designs, including equal troughing rollers, heavy-duty impact rollers, and more. These types are built with specialized features to cater to different industrial requirements and conditions.
Equal Troughing Rollers
Equal troughing rollers represent a classic design of trough carrier impact rollers, featuring a series of rollers of equal length arranged in a troughing configuration. They are designed to support the widest part of the conveyor belt and uniformly distribute the load across the belt’s width. Equal troughing rollers are a popular choice due to their versatility and effective load-carrying capacity, making them suitable for various materials and applications.
Heavy-Duty Impact Rollers
The heavy-duty impact roller is a robust variant of the trough carrier impact roller, specially built for environments where the materials being transported are particularly abrasive or heavy, such as in mining or quarrying. These rollers are fortified with additional padding or rubber lining to absorb the strain of heavy materials. Moreover, they often feature reinforced framing and can bear heavy loads, thus reducing belt wear and prolonging the system’s service life.
Channel Mount Idlers and Garland Idlers
Channel mount idlers are another type of trough carrier impact roller that operate in a slightly different configuration. They are typically mounted on a structured steel channel, which allows for adjustments in the angle and height of the trough. This adaptability makes it easy to fine-tune the system based on specific material handling requirements.
On the other hand, garland idlers consist of several rollers arranged in a ‘garland’ pattern, capable of forming a flexible ‘trough’ in the conveyor belt. This design offers improved belt tracking and material containment while reducing stress and wear on the belt.
While all falling under the umbrella of trough carrier impact rollers, these specific designs each bring unique advantages to conveyor systems, catering to an array of material handling applications across industries.
Material Analysis of Trough Carrier Impact Rollers: The Role of Polyurethane
The use of polyurethane in trough carrier impact rollers has seen a significant uptick due to its superior material properties, which directly contribute to improved functionality and longevity of the rollers. Below is a detailed breakdown of polyurethane’s properties and its benefits to the rollers.
Material Properties of Polyurethane
- Abrasion Resistance: Polyurethane’s excellent abrasion resistance means that trough carrier impact rollers made from this material can endure the harsh scraping and rubbing actions caused by heavy or sharp materials without showing significant wear. This ensures a longer lifespan for the roller itself and less frequent replacements.
- Mechanical Strength: This material boasts a high level of mechanical strength, including tensile, tear, and impact strength. For trough carrier impact rollers, this means the ability to withstand heavy loads and harsh impacts without suffering damage or deformation, maintaining consistent performance.
- Flexibility and Resilience: Polyurethane is uniquely flexible yet resilient. This allows the rollers to absorb shocks and adapt to minor irregularities in loads or belt movements, reducing potential damage to the conveyor belt.
- Temperature Resistance: Whether exposed to extreme heat or freezing conditions, polyurethane maintains its operational integrity. Its performance is stable across a broad temperature range, ensuring reliable roller function in various working environments.
Functional Advantages of Trough Carrier Impact Rollers
- Reduced Maintenance Needs: The durability and resilience of polyurethane significantly lower the need for frequent maintenance and replacements. This translates into cost savings and less operational downtime for businesses that rely on uninterrupted material handling processes.
- Cost-Efficiency: While polyurethane might have a higher initial cost compared to other materials, its longevity and reduced wear on conveyor belts offer long-term financial benefits, making it a cost-efficient choice for trough carrier impact rollers.
- Noise Reduction: The noise-dampening properties of polyurethane contribute to a quieter operation. This is particularly beneficial in enclosed or noise-sensitive environments, improving workplace conditions.
- Customization: The flexibility in the formulation of polyurethane allows manufacturers to tailor the material according to specific needs, like enhanced chemical or moisture resistance, providing an optimized solution for various industrial applications.
By integrating polyurethane into the construction of trough carrier impact rollers, manufacturers can significantly enhance the performance, durability, and overall efficiency of conveyor systems, addressing both immediate and long-term operational needs.
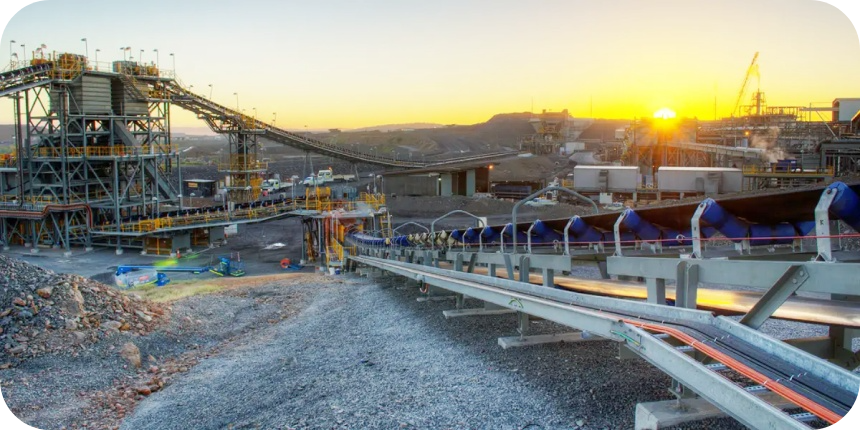
Standard Pipe Diameters and Material Thickness of Trough Carrier Impact Rollers
The construction of trough carrier impact rollers is a disciplined process that involves careful selection of pipe diameters and material thicknesses. This ensures the rollers can perform effectively under the stresses of conveying materials across various distances and environments. The choice of these dimensions directly affects the roller’s durability, capacity, and overall system performance.
Different Standard Pipe Diameters
Standard pipe diameters for trough carrier impact rollers vary, allowing for application-specific adaptations. These diameters are essential in determining the roller’s capacity to handle the load and its compatibility with different conveyor belt widths. Common diameters include, but are not limited to:
- 20mm: Used in light-duty applications where the conveying material is relatively light and the conveyor belt is narrow.
- 89mm to 159mm: The most common range for medium to heavy-duty applications, suitable for a wide range of belt widths and material weights.
- Over 159mm: Used in very heavy-duty applications, capable of supporting large loads over wide conveyor belts.
Each diameter class serves a specific segment of operations, from light agricultural conveying to heavy mining processes, ensuring there’s an efficient match between the roller and the operational demands.
Steel Tube Classes and Thicknesses
Trough carrier impact rollers are typically manufactured from various classes of steel tube, each differing in thickness and, thereby, in strength and durability. These classes are selected based on the environmental challenges and load demands the roller will face. Key considerations include:
- Class A: The lightest class, suitable for low-impact and lighter load applications. These might have a wall thickness around 3mm, offering a balance between weight and performance.
- Class B and C: Represent mid-range classes, with thicknesses varying from 4mm to 6mm. These are designed for general-purpose use, providing a good compromise between durability and cost-efficiency.
- Class D and beyond: Designed for the heaviest and most abrasive applications, with wall thicknesses exceeding 6mm. These tubes provide maximum durability and impact resistance, suitable for mining and quarrying operations.
By understanding the intricacies of pipe diameters and material thicknesses in steel tubes, manufacturers can optimize the lifespan and efficiency of trough carrier impact rollers. The selection process for these dimensions is crucial, as it directly influences the operational consistency, maintenance frequency, and ultimately, the productivity of the conveying system.
The Industry Significance of Trough Carrier Impact Rollers
Trough carrier impact rollers play a defining role in the mining industry. These dependable components of conveyor systems influence company sustainability and market positioning in multiple ways. Their effectiveness in maintaining the smooth running of day-to-day operations contributes to a company’s competitive advantage, economic efficiency, and environmental responsibility.
Impact on Company Sustainability and Market Position
- Operational Efficiency: With the right trough carrier impact rollers, companies can ensure an optimal material handling process, reducing potential system failures and downtime. Lower downtime results in higher productivity, directly impacting the company’s profitability and market position.
- Cost-Effective Maintenance: Trough carrier impact rollers designed for durability and longevity significantly cut down on maintenance and replacement costs. This contributes to better cost management, paving the way for economic sustainability and stronger financial performance in the competitive market.
- Minimizing Environmental Impact: Environmental responsibility is increasingly critical in the mining industry. High-quality trough carrier impact rollers contribute to this by reducing wear and tear on the system, thereby decreasing waste generated from roller replacements. These act as important sustainability indicators, positioning the company as a responsible player in the global market.
- Improved Safety: High-quality trough carrier impact rollers also increase workplace safety by minimizing system failures that can cause accidents. A safe work environment directly influences the company’s reputation and its position as an employer of choice in the industry.
As such, the impact of a well-designed and manufactured trough carrier impact roller on a company’s bottom line and industry standing is profound. This vital component, therefore, deserves careful consideration in any organization’s broader strategic planning and operational efficiency pursuits.
Request a free consultation for your impact roller needs.
FAQs about Trough Carrier Impact Roller
A troughing roller, part of a conveyor system, is designed to support the conveyor belt and the material being transported. These rollers are set at an angle on the frame of the conveyor to form a trough, shaping the belt to contain the material and prevent it from spilling over the edges. The design typically involves a central idler roller with slightly angled ones on either side, creating a cradle-like form. Troughing rollers play a crucial role in maintaining the efficiency and integrity of bulk material handling operations by ensuring stable belt movement and even distribution of load, enhancing the overall material transfer process.
Carrying idlers and impact idlers serve distinct functions within a conveyor system. Carrying idlers, also called troughing idlers, are used throughout the length of the conveyor to support the belt and the material conveyed on it. They reduce friction and help maintain the belt’s shape and tension. Impact idlers, on the other hand, are designed to absorb the shock and impact of the falling material, primarily at the loading point of the conveyor. They have a robust construction and often feature thicker, more resilient materials like rubber or reinforced coatings to withstand the force of heavy or sharp objects dropping onto the conveyor belt, thus preventing damage both to the belt and the rollers themselves.
The size of conveyor idler rollers can vary extensively to suit different applications, belt widths, and load requirements. They typically range from about 20mm in diameter for small, light-duty conveyors, up to 159mm and beyond for heavy-duty applications. The width of these rollers is designed to match the width of the conveyor belts they will be supporting, with common sizes ranging from 400mm to over 2400mm. The width of the roller is crucial as it dictates the total surface area available to support the belt and the transferred material, with wider rollers offering more support for wider belts and greater loads.
An idler roller primarily functions to provide support to conveyor belts and to guide them in a controlled path. These rollers play a vital role in reducing friction between the belt and the conveyor framework, hence enabling smooth and efficient movement of materials. Idler rollers also help to maintain the integrity and shape of the conveyor belt, ensuring that it remains in a centered and optimal position for carrying materials. In various sections of the conveyor system, different types of idler rollers such as impact idlers, carrying idlers, and return idlers are employed, each contributing towards the stability, protection, and efficiency of the belt conveyor operation.
Last Updated on July 5, 2024 by Jordan Smith
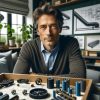
Jordan Smith, a seasoned professional with over 20 years of experience in the conveyor system industry. Jordan’s expertise lies in providing comprehensive solutions for conveyor rollers, belts, and accessories, catering to a wide range of industrial needs. From initial design and configuration to installation and meticulous troubleshooting, Jordan is adept at handling all aspects of conveyor system management. Whether you’re looking to upgrade your production line with efficient conveyor belts, require custom conveyor rollers for specific operations, or need expert advice on selecting the right conveyor accessories for your facility, Jordan is your reliable consultant. For any inquiries or assistance with conveyor system optimization, Jordan is available to share his wealth of knowledge and experience. Feel free to reach out at any time for professional guidance on all matters related to conveyor rollers, belts, and accessories.