Conveyor Belt System with Impact Roller Type
In the intricate world of conveyor systems, rollers play a pivotal role in ensuring the smooth and efficient movement of materials across various industries. Among the diverse array of rollers, the impact roller type stands out for its critical function in absorbing the shock and stress caused by materials as they are loaded onto the conveyor belt. Impact roller types, with shock-absorbing rings, protect conveyor belts from damage, offering durability, abrasion resistance, and noise reduction.These specialized rollers are designed to mitigate the impact at loading points, protecting both the conveyor belt and the system’s structural integrity from potential damage. By effectively dissipating the energy generated by falling objects, impact rollers extend the lifespan of the conveyor system and maintain its operational efficiency. Understanding the importance and functionality of the impact roller type is essential for anyone involved in the design, operation, or maintenance of conveyor systems, as it directly influences the system’s durability and effectiveness in handling materials.
Impact Roller Type:Functions
The impact roller type, often referred to as the buffer roller, plays a crucial role in the protection and longevity of conveyor systems. These specialized rollers are engineered to absorb the kinetic energy of materials as they are dropped onto the conveyor belt, significantly reducing the potential for damage. The primary function of the impact roller type is to act as a buffer between falling materials and both the conveyor belt and the underlying structure, safeguarding them from the wear and tear that can result from direct impact.
Impact rollers are strategically placed at critical points along the conveyor system, most notably at loading zones where materials are transferred onto the belt from a height. These loading points are where the conveyor belt is most vulnerable to damage due to the high velocity and volume of materials being deposited. Without the cushioning effect provided by impact rollers, the repeated impact of falling materials could quickly degrade the belt’s surface, leading to tears, punctures, and premature wear. Additionally, the force of the impact could distort the belt’s alignment or damage the conveyor structure, leading to costly repairs and downtime.
Shock Absorption:
- Impact rollers are constructed with rubber rings or discs that help absorb the shock and energy when heavy or sharp materials fall onto the conveyor belt. This prevents damage to the belt and prolongs its lifespan.
Belt Protection:
- By absorbing impact forces, these rollers prevent tears, punctures, and other types of damage to the conveyor belt. This is particularly important in industries where heavy or abrasive materials are being transported.
Load Distribution:
- Impact rollers help in distributing the load evenly across the conveyor belt. This uniform distribution reduces the stress on specific points of the belt, preventing premature wear and tear.
Noise Reduction:
- The rubber components of impact rollers help in reducing the noise generated when materials are dropped onto the conveyor belt. This contributes to a quieter and safer working environment.
Reduced Maintenance:
- By protecting the conveyor belt and reducing the likelihood of damage, impact rollers help in minimizing maintenance needs and costs. This leads to less downtime and more efficient operation of the conveyor system.
Extended Equipment Life:
- The overall longevity of the conveyor system is enhanced by the use of impact rollers. They protect not just the belt but also other components like idlers, frames, and structures from damage due to impact forces.
Improved Safety:
- A well-maintained conveyor system with impact rollers reduces the risk of accidents caused by belt failure or material spillage, thereby enhancing the safety of the operation.
The design of the impact roller type incorporates features specifically aimed at impact absorption. These rollers typically consist of a series of rubber discs or rings mounted on a steel roller, which allows them to compress under the force of falling materials. This compression acts to dissipate the energy of the impact across the surface of the roller, rather than allowing it to be transferred directly to the conveyor belt or structure. The choice of materials and the design of the roller are critical in ensuring that it can withstand the demands of the application, including the weight, size, and characteristics of the materials being conveyed.
Furthermore, the placement of impact rollers is carefully considered to provide maximum protection where it is most needed. This includes not only the loading points but also any other areas along the conveyor where materials might fall from a height or where the conveyor experiences significant stress. By customizing the placement and density of impact rollers, conveyor system designers can ensure that the system is equipped to handle the specific challenges of any material handling application.
The impact roller type serves as an essential component of conveyor systems, offering protection and resilience against the forces of impact. By absorbing the energy of falling materials, these buffer rollers prevent damage to the conveyor belt and structure, thereby enhancing the system’s durability and reducing the need for maintenance and repairs. Their strategic placement and specialized design make them a key factor in the efficient and reliable operation of conveyor systems across various industries.

Understanding the Different Impact Roller Types
When it comes to optimizing the performance and longevity of conveyor systems, selecting the right impact roller type is crucial. Impact rollers play a pivotal role in absorbing the forces exerted by falling materials at loading points, thereby protecting the conveyor belt and the structure from damage. This section delves into the various impact roller types, focusing on their design, material composition, and the importance of choosing the appropriate type for specific conveyor system needs.
Overview of Impact Roller Types
Impact rollers are designed to withstand the high impact of materials being loaded onto the conveyor belt. They are strategically placed at the loading zones of the conveyors where the material drop is significant. The primary function of these rollers is to absorb the impact energy of the falling material, which not only protects the belt from damage but also contributes to the stability of the material being conveyed. Here are some of the most common impact roller types:
Rubber Disc Impact Rollers: This impact roller type features rubber discs mounted on a heavy-duty steel roller. The rubber discs help absorb the impact energy, reducing wear and tear on the belt. They are particularly effective in handling coarse materials and are resistant to abrasion and tearing.
Spring-Loaded Impact Rollers: These rollers are equipped with a spring mechanism that allows for compression under heavy loads, providing an additional level of shock absorption. Spring-loaded impact rollers are suitable for extremely heavy or sharp materials that require a higher degree of cushioning.
Slider Bed Impact Rollers: Instead of individual rollers, a slider bed impact roller uses a solid surface that supports the conveyor belt across its width. This type is particularly useful in situations where the impact zone is broad or when dealing with fine, abrasive materials that could get caught between traditional rollers.
Polyurethane-Coated Impact Rollers: These rollers are coated with a layer of polyurethane, offering excellent resistance to wear, abrasion, and chemicals. Polyurethane-coated impact rollers are ideal for environments where the conveyor system is exposed to harsh chemicals or extreme temperatures.
Adjustable Impact Rollers: Adjustable impact rollers offer the ability to change the roller angle to match the load direction, optimizing the impact absorption and distribution across the roller surface. This flexibility is beneficial in applications where the loading conditions vary significantly.
Importance of Selecting the Correct Impact Roller Type
The selection of the appropriate impact roller type is critical for ensuring the efficiency, durability, and cost-effectiveness of a conveyor system. Factors to consider when choosing an impact roller include the type and size of the material being conveyed, the height from which the material is dropped, environmental conditions (such as exposure to chemicals or extreme temperatures), and the desired lifespan of the conveyor system.
Using the wrong type of impact roller can lead to increased maintenance costs, premature belt wear, and potential system downtime. Therefore, it is essential to assess the specific needs of your conveyor system and consult with experts if necessary to select the most suitable impact roller type.
What is the different impact roller types and their applications is fundamental in protecting conveyor systems from the damaging effects of high-impact forces. By carefully selecting the right impact roller type, businesses can enhance the performance and longevity of their conveyor systems, ultimately leading to improved operational efficiency and reduced maintenance costs.
Optimize your operations with high-quality conveyor belts. Inquire today!
Application of Impact Roller
Impact rollers, also known as impact idlers, find applications in various industries where conveyor belts are used to transport materials with substantial impact forces. Here are some specific applications of impact rollers:
1. Mining Industry
- Material Handling:
- Impact rollers are used in the loading areas where heavy rocks, ores, and minerals are dropped onto conveyor belts. These rollers absorb the shock and protect the belt from damage.
2. Quarrying Industry
- Aggregate Transport:
- In quarries, impact rollers are essential in areas where large aggregates or crushed stone are loaded onto conveyor belts. They prevent damage to the belt and ensure smooth operation.
3. Construction Industry
- Bulk Material Conveyance:
- During construction projects, impact rollers are used to transport heavy materials such as concrete, asphalt, and construction debris, ensuring the belt’s longevity.
4. Cement Industry
- Raw Material Transport:
- In cement plants, impact rollers are installed at the points where raw materials like limestone and clay are loaded onto conveyors. This reduces wear and tear on the belts.
5. Steel Industry
- Slag and Scrap Handling:
- Impact rollers are used in the steel industry to handle slag, scrap metal, and other heavy materials, preventing damage to conveyor systems.
6. Power Generation
- Coal Handling:
- In power plants, especially those using coal, impact rollers are used in the coal handling areas to protect belts from the impact of coal being loaded onto the conveyor system.
7. Recycling Industry
- Waste Management:
- Impact rollers are applied in recycling plants to handle heavy and abrasive materials such as scrap metal, glass, and construction debris, enhancing the durability of the conveyor belts.
8. Ports and Terminals
- Bulk Material Loading and Unloading:
- In ports and terminals, impact rollers are used in bulk material handling systems to manage the impact forces when loading and unloading ships with materials like grain, coal, and ores.
9. Agricultural Industry
- Grain Handling:
- In agricultural settings, impact rollers are used to handle bulk grains and other agricultural products, ensuring the conveyor systems operate smoothly and efficiently.
Benefits in Application
- Enhanced Durability:
- By absorbing the impact of heavy materials, impact rollers extend the lifespan of conveyor belts and reduce maintenance costs.
- Operational Efficiency:
- Reducing belt damage and downtime ensures continuous and efficient operation of the conveyor system.
- Safety Improvement:
- Preventing belt failures and material spillage reduces the risk of accidents, contributing to a safer work environment.
- Cost Savings:
- Lower maintenance and replacement costs, combined with reduced downtime, lead to significant cost savings over time.
In summary, impact rollers are crucial components in various industries, providing essential protection to conveyor systems, enhancing operational efficiency, and contributing to overall cost savings and safety improvements.

Impact Roller Type: Heavy Duty Impact Roller
The heavy-duty impact roller type is specifically engineered to withstand the extreme conditions encountered in high-impact areas such as mining, quarries, and other harsh environments. These environments demand equipment that can endure the rigors of heavy, abrasive materials falling from significant heights, often under extreme temperatures and dusty conditions. The heavy-duty impact roller is designed with these challenges in mind, offering unparalleled durability and protection for conveyor systems in the most demanding applications.
Constructed from robust materials, heavy-duty impact rollers feature a core of reinforced steel designed to resist bending and deformation. The outer layer typically consists of thick, high-quality rubber or a composite material that can absorb shock without deteriorating. This combination of strength and flexibility allows the rollers to dissipate the energy of falling materials effectively, minimizing the impact transmitted to the conveyor belt and its support structure. The resilience of these materials ensures that the rollers maintain their integrity and functionality over time, even in the face of abrasive materials and corrosive elements.
One of the key features that make the heavy-duty impact roller type suitable for such applications is its enhanced sealing system. These rollers are equipped with superior seals that prevent the ingress of dust, water, and other contaminants, which could otherwise lead to premature bearing failure. This sealing capability is crucial in environments where dust and moisture are prevalent, ensuring the longevity of the roller’s internal components.
Moreover, the design of heavy-duty impact rollers often includes a larger diameter and a wider surface area compared to standard rollers. This design choice increases the contact area with the conveyor belt, spreading the load more evenly and further reducing the concentration of stress at any single point. As a result, the conveyor belt experiences less wear and tear, extending its service life and reducing maintenance requirements.
In addition to their robust construction, heavy-duty impact rollers are also designed for ease of maintenance. Features such as easy-access bearing housings and replaceable rings or sleeves allow for quick repairs and replacements without the need to dismantle the entire roller assembly. This design consideration minimizes downtime and ensures that the conveyor system can quickly return to full operational capacity.
The heavy-duty impact roller type is an essential component for conveyor systems operating in environments where high-impact forces are a constant challenge. Through their durable construction, specialized materials, and thoughtful design features, these rollers provide the necessary protection to extend the lifespan of conveyor systems, ensuring reliable operation in the most demanding conditions.
Standard Impact Roller Type
In the realm of conveyor system components, the standard impact roller stands out as a fundamental element designed to enhance the durability and efficiency of conveyor belts. This section provides an in-depth look at the standard impact roller type, focusing on its design, material composition, and its pivotal role in universal conveyor systems.
Overview of Standard Impact Rollers
Standard impact rollers are engineered to absorb the shock and impact of materials as they are loaded onto the conveyor belt, thereby preventing damage to the belt and the conveyor structure. Positioned at the loading points where materials are dropped onto the belt, these rollers are critical in minimizing the force of impact and distributing it evenly across the belt surface. The design of standard impact rollers aims to ensure that conveyor systems can handle a wide range of materials, from fine grains to large, coarse rocks, without compromising the integrity of the conveyor belt.
Materials Used in Standard Impact Rollers
The construction of standard impact rollers typically involves robust materials capable of withstanding significant wear and tear. The core of these rollers is usually made from steel or aluminum, providing the necessary strength and durability. The outer shell is often composed of rubber or a rubber composite, which acts as the primary impact-absorbing material. This rubber coating is specifically formulated to resist abrasion, tearing, and the harsh conditions often encountered in conveyor system environments.
In some cases, polyurethane may be used as an alternative to rubber for the outer layer, offering enhanced resistance to wear, chemicals, and extreme temperatures. The choice between rubber and polyurethane coatings depends on the specific requirements of the application, including the type of materials being conveyed and the environmental conditions of the operation.
Typical Applications of Standard Impact Rollers
Standard impact rollers are versatile components used across a wide range of industries and applications. They are particularly prevalent in sectors such as mining, quarrying, and aggregate processing, where the conveyor systems are subjected to heavy loads and high-impact forces. Additionally, these rollers are commonly found in recycling plants, bulk material handling facilities, and in the construction industry, where they contribute to the efficient and safe transportation of materials.
The universal design of standard impact rollers makes them suitable for a variety of conveyor systems, from flat belt conveyors to troughed belt conveyors. Their ability to absorb impact efficiently not only protects the conveyor belt from premature wear and potential damage but also helps to maintain the alignment and stability of the belt, ensuring smooth and uninterrupted operation.
The standard impact roller type is a critical component in universal conveyor systems, offering robust protection against the damaging effects of material impact. By utilizing durable materials and a design focused on impact absorption, standard impact rollers ensure the longevity and reliability of conveyor systems across multiple industries. Selecting the appropriate impact roller type, based on the specific needs of the application, is essential for optimizing conveyor performance and reducing maintenance requirements.
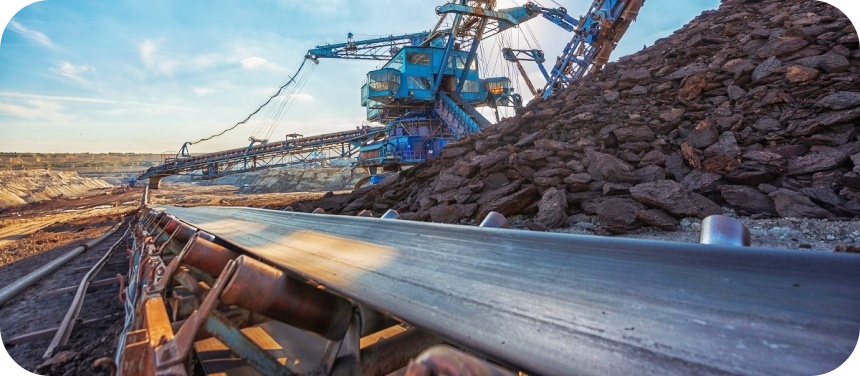
Buffer Roller Types Vs Impact Roller Type
When selecting the appropriate impact roller type for a conveyor system, it’s crucial to understand the differences between the various types available. This comparison table focuses on two primary categories of impact rollers: heavy-duty and standard versions. By examining their material composition, design, application suitability, and durability, we can better appreciate the unique attributes that make each type suited to specific operational environments.
This comparison highlights the critical differences between heavy-duty and standard impact roller types, guiding users in selecting the right buffer roller for their specific conveyor system needs. Heavy-duty impact rollers offer enhanced protection and longevity in severe operational environments, while standard impact rollers provide adequate performance for lighter-duty applications. Understanding these distinctions ensures that conveyor systems are equipped with the most appropriate impact rollers, optimizing their efficiency and extending their operational lifespan.

Choosing the Right Impact Roller Type
Selecting the correct impact roller type for a conveyor system is a critical decision that can significantly affect the system’s efficiency, durability, and maintenance requirements. This guide aims to outline the key factors that should be considered when choosing the appropriate impact roller type, emphasizing the importance of belt width, material type, and conveyor speed in the selection process.
Factors to Consider
When selecting an impact roller type, several factors must be taken into account to ensure compatibility with the conveyor system’s requirements and to optimize performance. These factors can be summarized in the following table:
Importance of Belt Width, Material Type, and Conveyor Speed
- Belt Width: The correct impact roller size is essential for providing comprehensive support across the belt’s width, preventing sagging and ensuring uniform impact distribution. An inadequately sized roller can lead to uneven wear and potential damage to the conveyor belt.
- Material Type: The physical characteristics of the conveyed material significantly influence the selection of the impact roller type. For instance, conveying sharp or abrasive materials requires rollers with high resistance to cutting and abrasion, such as those made from specialized rubber compounds or coated with polyurethane.
- Conveyor Speed: The operational speed of the conveyor system dictates the frequency and intensity of impacts experienced by the rollers. High-speed systems may necessitate the use of impact rollers designed for dynamic loads, ensuring that the rollers can absorb and dissipate energy effectively without compromising the system’s integrity.
Selecting the right impact roller type is a multifaceted decision that requires careful consideration of various factors, including belt width, material type, and conveyor speed. By understanding these factors and their implications, conveyor system designers and operators can make informed choices that enhance system performance, extend the lifespan of both the conveyor belt and the rollers, and minimize maintenance requirements.
Installation and Maintenance of Impact Roller
The proper installation and maintenance of the impact roller type are crucial for maximizing the efficiency and extending the lifespan of conveyor systems. This section provides a basic guide on installing buffer rollers, specifically the impact roller type, and offers valuable tips for their maintenance.
Installation Guide for Impact Roller Type
Preparation: Before installation, ensure that you have all the necessary tools and safety equipment. It’s crucial to power down the conveyor system and apply lockout/tagout procedures to prevent accidental startup.
Inspection: Examine the area where the impact rollers will be installed. Check for any signs of wear or damage on the conveyor frame or existing rollers that could affect the new installation.
Removal of Old Rollers: If replacing old rollers, carefully remove them from the conveyor frame. This might require loosening or removing fasteners and brackets that hold the rollers in place.
Positioning the New Rollers: Place the new impact roller type in the designated positions, typically at loading zones or other high-impact areas. Ensure that the rollers are aligned correctly with the conveyor belt‘s path.
Securing the Rollers: Use the provided brackets and fasteners to secure the impact rollers to the conveyor frame. It’s important to follow the manufacturer’s specifications for tightening to ensure the rollers are firmly in place but can rotate freely.
Final Inspection: Once installed, perform a thorough inspection to ensure that all rollers are securely mounted and aligned. Check for any obstructions or issues that could impede the conveyor belt’s movement.
Testing: Carefully remove lockout/tagout protections and power on the conveyor system. Observe the operation of the impact rollers, ensuring they function as intended and absorb impacts effectively.
Maintenance Tips for Impact Roller Type
Regular Inspections: Conduct periodic inspections of the impact rollers to identify any signs of wear, damage, or misalignment. Early detection of issues can prevent more significant problems down the line.
Cleaning: Keep the impact rollers clean from debris and buildup, which can affect their performance. Use appropriate cleaning methods based on the roller materials and the type of debris.
Lubrication: If the impact roller type features components that require lubrication, such as bearings, ensure they are lubricated according to the manufacturer’s recommendations. Use the correct type of lubricant and apply it in the right amounts.
Replacement of Worn Parts: Replace any worn or damaged parts promptly. This includes the rubber rings or sleeves on the impact rollers, which can wear down over time and reduce the roller’s impact-absorbing capabilities.
Adjustments: Make necessary adjustments to the alignment and tension of the impact rollers to ensure they continue to operate efficiently. Misaligned or improperly tensioned rollers can cause uneven wear and reduce the conveyor system’s effectiveness.
By following these installation and maintenance guidelines, you can ensure that the impact roller type in your conveyor system performs optimally, providing effective impact absorption and contributing to the system’s overall longevity and efficiency.
Boost productivity with our superior conveyor belts. Reach out now!
Exploring Other Roller Types
While the impact roller type is crucial for absorbing the forces at loading points and protecting the conveyor belt, other roller types also play vital roles in ensuring the smooth and efficient operation of conveyor systems. This section provides an overview of additional roller types, including load rollers, return rollers, guide rollers, and idler rollers, highlighting their functions and importance within conveyor systems.
Load Rollers
Load rollers, as the name suggests, are primarily responsible for supporting the weight of the materials being conveyed. Positioned along the carrying side of the conveyor, these rollers are designed to withstand the load’s weight while minimizing friction, allowing for smooth and efficient material transport. The durability and material composition of load rollers are critical, as they directly influence the conveyor system’s ability to handle various loads without compromising speed or energy efficiency.
Return Rollers
Return rollers are located on the underside of the conveyor, supporting the belt as it returns to the starting point after offloading the material. These rollers are essential for maintaining belt tension and alignment, preventing sagging and ensuring that the belt runs smoothly along its path. Return rollers often have a simpler design compared to load rollers, as they do not directly bear the load of the conveyed materials. However, their role in preserving the conveyor belt’s integrity and prolonging its lifespan is equally important.
Guide Rollers
Guide rollers are installed at strategic points along the conveyor frame to ensure that the conveyor belt remains centered and aligned. Misalignment can lead to uneven wear, increased maintenance costs, and potential system failures. Guide rollers gently steer the belt back to its correct path, minimizing the risk of belt damage and material spillage. Their placement and adjustment are crucial for maintaining optimal conveyor performance and reliability.
Idler Rollers
Idler rollers serve a general purpose in conveyor systems, providing additional support to the conveyor belt and materials being transported. These rollers help distribute the weight of the load more evenly, reducing the stress on individual rollers and the conveyor belt. Idler rollers can be customized in various configurations, such as troughing idlers or flat idlers, to match the specific needs of the conveyor system and the nature of the materials being conveyed.
Each roller type within a conveyor system has a specific role that contributes to the system’s overall functionality and efficiency. From supporting heavy loads to ensuring belt alignment and reducing friction, these rollers work together to facilitate the smooth operation of the conveyor. The selection and placement of these rollers are critical decisions that impact the conveyor system’s performance, maintenance requirements, and longevity. Understanding the role and importance of each roller type, including the impact roller type, is essential for designing and operating effective conveyor systems that meet the demands of various material handling applications.
FAQs about Impact Roller Type
Conveyor rollers are essential components of conveyor systems, facilitating the smooth movement of materials along the conveyor belt. There are several types of conveyor rollers, each designed for specific applications and operational requirements. The main types include:
Gravity Rollers: These rollers rely on gravity to move products and are typically used in manual loading or unloading applications. They are cost-effective and suitable for lightweight materials.
Powered Rollers: Powered rollers are driven by motors, making them suitable for automated systems where control over the speed and direction of material movement is required. They can handle heavier loads compared to gravity rollers.
Impact Rollers: Positioned at conveyor loading points, impact rollers are designed to absorb the shock and impact from falling materials, protecting the belt and system from damage.
Grooved Rollers: These rollers are designed with grooves that can accommodate round belts for driving the roller. They are often used in lightweight applications or where precise movement control is needed.
Tapered Rollers: Ideal for curves in conveyor systems, tapered rollers ensure materials stay on track around bends. Their shape helps maintain the alignment of the materials being transported.
Each type of conveyor roller serves a unique purpose within a conveyor system, and the selection of the appropriate roller type depends on the specific needs of the application, including the weight of materials, the desired speed of movement, and the environmental conditions of the operation.
Impact rollers are specialized types of conveyor rollers designed to absorb the shock and impact of materials as they are dropped onto the conveyor belt at loading points. These rollers are crucial for preventing damage to the conveyor belt and extending the lifespan of the conveyor system. Impact rollers are characterized by their robust construction, which typically involves a series of rubber discs or rings mounted on a heavy-duty steel roller. The rubber discs help dissipate the energy from falling materials, reducing the force transmitted to the belt and underlying structure. Impact rollers are essential in applications where the conveyor system handles heavy or sharp materials that could cause significant wear and tear. By effectively absorbing the impact, these rollers ensure smoother operation, reduce maintenance costs, and enhance the overall efficiency of the conveyor system.
Idlers are rollers that support the conveyor belt and the materials being transported. Several types of idlers cater to various functions within a conveyor system:
Carrying Idlers: Also known as troughing idlers, these are used on the carrying side of the conveyor belt to support the load being transported. They are typically arranged in a trough shape to hold the belt and materials in place.
Return Idlers: Positioned on the return side of the belt, return idlers support the belt as it loops back to the beginning of the conveyor system. They help maintain the belt’s tension and alignment.
Impact Idlers: Similar to impact rollers, impact idlers are placed at loading zones to absorb the shock of materials falling onto the belt, protecting it from damage.
Self-aligning Idlers: These idlers are designed to automatically adjust the belt’s alignment if it starts to drift off-center. They are crucial for preventing the belt from slipping off the rollers and reducing wear.
Guide Idlers: Guide idlers are used to steer the belt into a particular path and are often employed in curved sections of the conveyor system.
Each type of idler plays a specific role in supporting the conveyor belt and ensuring the efficient and smooth operation of the conveyor system.
The primary difference between carrying idlers and impact idlers lies in their intended purpose and design within a conveyor system.
Carrying Idlers: These idlers are designed to support the weight of the materials being transported along the carrying side of the conveyor belt. They are usually arranged in a trough shape to cradle the belt and its contents, helping to maintain the belt’s shape and alignment. Carrying idlers are essential for the smooth and efficient movement of materials and are used throughout the length of the conveyor system.
Impact Idlers: Impact idlers, on the other hand, are specifically designed to absorb the shock and impact of materials as they fall onto the conveyor belt at loading points. They are constructed with durable materials and often feature rubber discs or rings that cushion the impact, protecting the conveyor belt and the structure of the conveyor system from damage. Impact idlers are critical in applications where the conveyor handles heavy or sharp materials that could cause significant wear to the belt.
Last Updated on July 26, 2024 by Jordan Smith
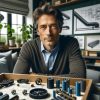
Jordan Smith, a seasoned professional with over 20 years of experience in the conveyor system industry. Jordan’s expertise lies in providing comprehensive solutions for conveyor rollers, belts, and accessories, catering to a wide range of industrial needs. From initial design and configuration to installation and meticulous troubleshooting, Jordan is adept at handling all aspects of conveyor system management. Whether you’re looking to upgrade your production line with efficient conveyor belts, require custom conveyor rollers for specific operations, or need expert advice on selecting the right conveyor accessories for your facility, Jordan is your reliable consultant. For any inquiries or assistance with conveyor system optimization, Jordan is available to share his wealth of knowledge and experience. Feel free to reach out at any time for professional guidance on all matters related to conveyor rollers, belts, and accessories.