Types of Mining Conveyor Belt: Selection and Implementation Guide
In the realm of mining operations, the significance of conveyor belts cannot be overstated. These pivotal components are the lifeline of the mining industry, facilitating the efficient and continuous transport of materials such as ore, coal, and minerals from extraction points to processing facilities or loading sites. The selection of the appropriate types of mining conveyor belt is crucial, as it directly impacts the operation’s productivity, safety, and cost-effectiveness. Conveyor belts vary widely in design, material, and purpose, each tailored to meet the specific demands of different mining environments and material types. By enhancing efficiency and ensuring the safety of the workforce and the materials transported, conveyor belts play an indispensable role in the mining sector. Their ability to move large volumes of material steadily and reliably over long distances makes them a cornerstone of modern mining operations, underscoring the importance of choosing the right conveyor belt for each mining project.
The Essential Role of Conveyor Belts in Mining
Pivotal Conveyor Belts in Transporting Materials in Mining Operations
Conveyor belts are indispensable in the mining industry, playing a pivotal role in the efficient and effective transportation of materials. The types of mining conveyor belt utilized can significantly impact the operation’s productivity, safety, and cost-efficiency.Here, we delve into the essential roles these conveyor belts play and the diverse materials and environments they are designed for.
- Transporting Materials Over Long Distances: Conveyor belts enable the movement of materials over long distances within mining operations, from the extraction site to processing facilities or loading points, minimizing the need for truck haulage and reducing operational costs.
- Facilitating Continuous Operations: Unlike other modes of transport, conveyor belts allow for continuous operation, essential in mining where downtime can lead to significant financial losses.
- Adapting to Various Terrains: The flexibility of mine conveyor belt systems allows them to be installed over rough and uneven terrain, making them ideal for complex mining landscapes.
- Enhancing Safety: By reducing the need for manual handling and the movement of heavy machinery, conveyor belts help in minimizing workplace accidents and enhancing overall safety.
- Increasing Efficiency: Conveyor belts can move large volumes of material at a consistent rate, ensuring a steady supply of ore to processing plants and thus increasing overall operational efficiency.
- Reducing Environmental Impact: By minimizing ground disturbance and reducing emissions from vehicles, conveyor belts offer a more environmentally friendly alternative to traditional material transport methods.
- Customizable for Specific Needs: The types of mining conveyor belt are designed to meet the specific requirements of various mining operations, with belts available for different materials, temperatures, and environmental conditions.
- Cost-Effective Material Transport: Over time, conveyor belts prove to be a cost-effective solution for transporting materials, thanks to their low maintenance and operational costs compared to other transport methods.
Materials and Environments
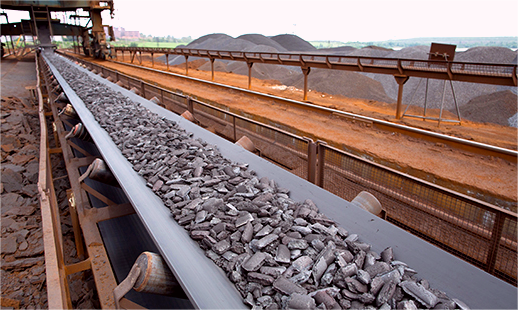
Conveyor belts are designed to handle a wide range of materials and environments, including:
- Abrasive Materials: Such as ores and minerals, which require durable and wear-resistant belts.
- Heavy Materials: Like rocks and coal, necessitating strong belts with high tensile strength.
- Hot Materials: Conveyor belts designed to withstand high temperatures are used for transporting materials like sintered ore or clinker.
- Oily and Greasy Materials: Special oil-resistant belts are utilized to prevent degradation and ensure the materials are transported efficiently.
- Fine and Powdery Materials: Belts with special surface textures or profiles are used to prevent slippage and ensure accurate delivery.
- Hazardous Materials: Non-flammable and anti-static belts are essential for safely transporting materials in potentially explosive environments, such as coal mines.
- Steep Incline Materials: Sidewall and cleated belts are designed to transport materials vertically or at steep inclines, maximizing space and efficiency.
- Wet and Muddy Materials: Waterproof and mud-resistant belts are used in environments where materials come in contact with water, ensuring the integrity of the belt and the safe transport of materials.
The types of mining conveyor belt play a crucial role in the mining industry, tailored to meet the demands of transporting a variety of materials across diverse environments. Their ability to improve efficiency, safety, and cost-effectiveness in material transport makes them an essential component of modern mining operations.
Types of Mining Conveyor Belts
In the realm of mining, the conveyor belt system plays a pivotal role in transporting materials efficiently across various parts of the mining operation. Among these systems, the types of mining conveyor belts utilized can vary significantly, each designed to meet specific operational needs and environmental challenges. This section will delve into the diverse types of mining conveyor belts, highlighting their unique features, applications, and the advantages they offer in different mining scenarios.
Each of these types of mining conveyor belts has been developed with specific mining environments and challenges in mind, ensuring that operations can select the most suitable option to enhance efficiency, safety, and the overall productivity of the mining process.
Considerations for Selecting the Right Types of Mining Conveyor Belt
Selecting the appropriate types of mining conveyor belt is critical for optimizing efficiency, safety, and cost-effectiveness in mining operations. The choice of conveyor belt affects the operation’s productivity and longevity, making it essential to consider various factors to select the most suitable one. This section will explore key considerations that should guide the selection process of the right types of mining conveyor belt.
Factors Influencing the Selection of Mining Conveyor Belts
- Tensile Strength: The belt’s ability to withstand tension without elongating or breaking is crucial, especially in high-load situations.
- Abrasion Resistance: A belt’s resistance to wear and tear from rough materials ensures longevity and reduces maintenance costs.
- Environmental Conditions: Temperature, humidity, exposure to chemicals, and the presence of water can significantly affect a belt’s performance.
- Material Characteristics: The type of materials being transported (e.g., sharp, hot, or corrosive) dictates the belt material and design needed.
- Conveyor Belt Speed: The speed at which the belt moves affects how materials are transported and can influence the choice of belt material and design.
- Load Capacity: The maximum load the belt must carry without experiencing failure or excessive wear.
- Conveyor Length and Incline: Longer and more inclined conveyors require belts with higher strength and durability.
- Belt Size and Width: Proper sizing ensures efficient material handling and prevents spillage and overflow.
- Maintenance and Repair: Ease of maintenance and repairability are important considerations, especially in remote or harsh environments.
- Cost: While upfront cost is a factor, the total cost of ownership, including maintenance, downtime, and replacement, should also be considered.
Significance of Selecting the Appropriate Belt Size and Material
- Efficiency: The right belt size and material ensure that the conveyor system operates at optimal efficiency, minimizing energy consumption and operational costs.
- Safety: The correct type of belt reduces the risk of accidents and ensures compliance with safety regulations, particularly in hazardous environments.
- Durability: Choosing a belt material suited to the operational environment and material characteristics can significantly extend the lifespan of the conveyor belt.
- Adaptability: The ability of a belt to adapt to varying operational demands without significant degradation is essential for maintaining productivity.
- Reduced Downtime: A well-chosen conveyor belt minimizes downtime caused by repairs, maintenance, and belt replacement, thereby enhancing operational continuity.
- Environmental Impact: Selecting an environmentally friendly conveyor belt, when possible, can help mining operations reduce their ecological footprint.
The selection of the right types of mining conveyor belt involves a comprehensive analysis of operational requirements, environmental conditions, and material characteristics. By carefully considering these factors, mining operations can ensure the efficiency, safety, and longevity of their conveyor belt systems, ultimately leading to increased productivity and reduced costs.
Types of Mining Conveyor Belt: Key Manufacturers and Products

In the realm of mining, conveyor belts are indispensable for transporting materials across various distances and terrains. The types of mining conveyor belt systems utilized can significantly impact efficiency, safety, and the overall cost of mining operations. This section delves into seven leading manufacturers in the mining conveyor belt industry, highlighting their flagship products and innovations that cater to different types of mining conveyor belt needs.
GRAM Conveyor
GRAM Conveyor is an emerging leader in the conveyor belt industry, known for its innovative and durable products. Their GRAM Nylon Series stands out for its high-quality nylon material, which is lightweight, corrosion-resistant, and designed for easy maintenance. This series is particularly suitable for heavy-duty applications in industries such as chemical manufacturing and cleanrooms, highlighting GRAM’s commitment to providing customized solutions that meet the specific demands of the mining sector.
ContiTech AG
ContiTech AG, a subsidiary of Continental AG, is renowned for its comprehensive range of rubber and plastics technology-based products. In the mining sector, ContiTech specializes in the development of high-strength conveyor belts designed for heavy-duty operations. Their flagship product, the Stahlcord® series, exemplifies the types of mining conveyor belt systems designed for maximum conveying capacity and durability, suitable for transporting massive loads over long distances with minimal maintenance.
Bridgestone Corporation
Bridgestone, a global leader in tires and rubber products, extends its expertise to high-performance mining conveyor belts. Their Ultra Tuff™ belt series stands out for its exceptional resistance to abrasion, making it ideal for the harsh conditions of underground and open-pit mining environments. These belts exemplify the innovation in types of mining conveyor belt materials aimed at prolonging operational life and reducing downtime.
Fenner Dunlop
Fenner Dunlop specializes in the production of conveyor belts for the mining industry, with a focus on safety and reliability. Their Fire Boss® belt is designed to meet the stringent fire safety standards required in mining operations, providing peace of mind in environments where fire hazards are a constant concern. This product highlights the importance of safety innovations in the types of mining conveyor belt designs.
Phoenix Conveyor Belt Systems GmbH
Phoenix Conveyor Belt Systems GmbH is known for its technologically advanced conveyor belt solutions. Their Phoenocord® St 7500 is one of the strongest belt types in the world, designed for use in surface and underground mining operations where large distances and high loads are involved. This belt demonstrates the advancements in types of mining conveyor belt technologies aimed at enhancing load-carrying capacity and operational efficiency.
Yokohama Rubber Co., Ltd.
Yokohama Rubber Co., Ltd. offers a range of high-quality conveyor belts that include energy-saving and eco-friendly options. Their flagship product, the ENERGY STAR® Conveyor Belt, is designed to reduce energy consumption in the conveyor system, a crucial factor in large-scale mining operations. This innovation reflects the growing emphasis on sustainability in the types of mining conveyor belt systems.
WCCO Belting
WCCO Belting is a leading manufacturer of custom rubber belting for various mining applications. Their TerraTech™ series is engineered for the unique demands of the mining industry, offering durability and flexibility in challenging conditions. This product line showcases the company’s commitment to developing specialized types of mining conveyor belt solutions that address the specific needs of the mining sector.
Each of these manufacturers plays a pivotal role in advancing conveyor belt technology, offering solutions that enhance the efficiency, safety, and sustainability of mining operations worldwide. Their flagship products and innovations in the types of mining conveyor belt systems continue to set industry standards and drive progress in mining conveyor technology.
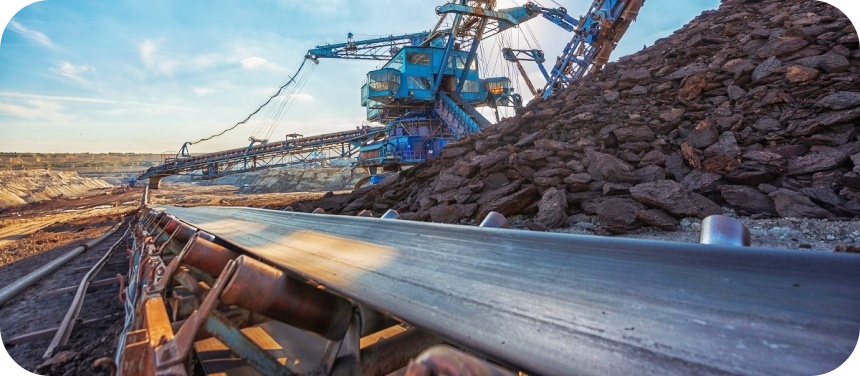
Mining Belt Conveyor
Design and Structure
Mining belt conveyors are engineered to handle the rigors of transporting heavy and abrasive materials over long distances. The design and construction of these conveyors are critical to their efficiency and durability.
- Framework: The conveyor structure typically consists of a series of metal frames or trusses that support the entire system. These frames are designed to withstand heavy loads and are usually made from robust materials like steel to provide stability and durability.
- Belt: The conveyor belt itself is a continuous loop made from materials such as rubber, fabric, or metal, depending on the specific application. For mining, belts are often reinforced with steel cords or synthetic fibers to enhance their strength and resistance to wear and tear.
- Pulleys: Key components at both ends of the conveyor. The head pulley drives the belt, while the tail pulley maintains tension. Pulleys may have specialized surfaces to improve grip and reduce slippage.
- Idlers and Rollers: Support the belt along its length. Idlers are strategically placed to prevent sagging and ensure smooth movement. They can be flat or trough-shaped to support the belt and the material being transported.
- Drive System: Typically includes electric motors and gearboxes. The drive system must be powerful enough to move the belt and its load over long distances, and it often includes features like variable speed controls to adjust the belt speed as needed.
- Controls and Safety Features: Modern conveyors are equipped with advanced control systems to monitor and manage their operation. Safety features such as emergency stop buttons, guards, and sensors help prevent accidents and ensure safe operation.
Common Uses
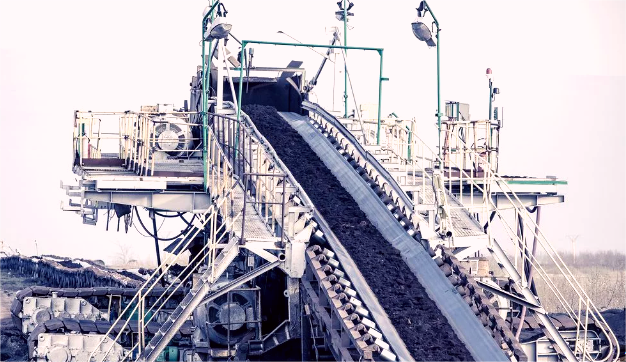
Mining belt conveyors are versatile and essential components in both surface and underground mining operations. Their applications include:
- Surface Mining:
- Overburden Removal: Transporting soil and rock away from mining sites.
- Ore Transport: Moving raw ore from the mining site to processing plants or stockpiles.
- In-Pit Crushing and Conveying (IPCC): A system that reduces the need for truck haulage, lowering operational costs and environmental impact.
- Underground Mining:
- Material Haulage: Conveyors are used to transport extracted materials from deep within mines to the surface.
- Ore Handling: Efficiently moving ore to crushers or processing stations located underground.
- Waste Transport: Disposing of mining waste materials by transporting them to designated areas.
Advantages
Mining belt conveyors offer several key advantages, making them indispensable in mining operations:
- Efficiency: Conveyors provide a continuous and efficient method of transporting materials over long distances. They are more energy-efficient compared to traditional truck haulage, especially for large-scale mining operations.
- Durability: Designed to withstand the harsh conditions of mining environments, including abrasive materials, heavy loads, and extreme weather. High-quality materials and construction techniques ensure long-lasting performance.
- High Capacity: Capable of transporting large quantities of materials at a steady rate. This high throughput is crucial for meeting the demands of modern mining operations.
- Cost-Effectiveness: Reduces the need for fuel and maintenance associated with truck fleets. Over time, conveyors can significantly lower operational costs.
- Safety: Enhances safety by reducing the number of trucks and personnel required to transport materials. Modern conveyors come equipped with safety features to prevent accidents and protect workers.
- Environmental Impact: Lower emissions compared to diesel trucks, contributing to more sustainable mining practices. Conveyors can also help minimize the footprint of mining operations by reducing the need for extensive road networks.
Mining belt conveyors are a backbone of the mining industry, providing a reliable and efficient means of transporting materials. Their design, versatility, and advantages make them a vital component in both surface and underground mining operations.
Conveyor Belt Composition
Materials Used
Conveyor belts used in mining operations are constructed from a variety of materials, each chosen for specific properties that enhance the belt’s performance and durability. The primary materials include:
- Rubber: Natural or synthetic rubber is commonly used for the top and bottom covers of conveyor belts. Rubber provides flexibility, resilience, and resistance to abrasion, impacts, and various chemicals. It also has good temperature resistance, making it suitable for a wide range of mining environments.
- Steel Cords: For belts designed to carry heavy loads over long distances, steel cords are used as reinforcements. These cords provide exceptional tensile strength and durability, making the belts capable of withstanding significant stress without stretching. Steel cord belts are particularly common in high-tension applications like mining.
- Fabric: Different types of fabrics, such as polyester, nylon, or cotton, are used in the conveyor belt carcass. Fabrics provide flexibility and strength, and they can be layered to increase the belt’s overall durability. Polyester and nylon fabrics are preferred for their high tensile strength and resistance to moisture and chemicals.
- Polyurethane (PU) and Polyvinyl Chloride (PVC): These materials are often used in belts that require excellent wear resistance, low noise, and ease of cleaning. PU and PVC belts are especially common in food processing but can also be used in certain mining applications where these properties are beneficial.
Layer Structure
The typical structure of a mining conveyor belt consists of multiple layers, each serving a specific purpose to enhance the belt’s performance and longevity. The main components of the layer structure include:
- Carcass: The carcass is the core of the conveyor belt, providing structural support and determining its strength and elongation properties. It is typically composed of fabric layers or steel cords. The choice of carcass material depends on the application and the required strength of the belt.
- Top Cover: The top cover is the outermost layer of the conveyor belt that comes into contact with the transported materials. It is made of rubber or other synthetic materials designed to resist wear, impacts, and environmental conditions. The thickness of the top cover can vary depending on the application’s demands.
- Bottom Cover: The bottom cover, similar to the top cover, is made of durable materials like rubber. It provides a protective layer for the carcass and ensures smooth operation over idlers and pulleys. The bottom cover may also be designed to reduce friction and wear against conveyor components.
- Sidewalls and Cleats: Some conveyor belts are equipped with additional features like sidewalls and cleats. Sidewalls are vertical barriers along the edges of the belt, preventing material spillage and enabling the transport of bulk materials at steep angles. Cleats are raised sections on the belt surface that help in moving materials up inclines and maintaining consistent spacing between items.
Special Features
Mining conveyor belts can be customized with special features to meet specific operational requirements and challenges. These features enhance the belt’s functionality and adaptability to different mining conditions. Some of the special features include:
- Cleats: Cleats are raised sections or ribs on the surface of the conveyor belt, which help in moving materials at an incline. They prevent materials from sliding back and ensure consistent spacing between items. Cleats can be made in various shapes and sizes, depending on the application.
- Sidewalls: Sidewalls are vertical barriers attached to the edges of the conveyor belt. They prevent material from spilling over the sides and allow for the transportation of bulk materials at steeper angles. Sidewalls are particularly useful in applications involving loose or granular materials.
- Special Coatings: Conveyor belts can be coated with materials that provide additional properties like heat resistance, oil resistance, flame resistance, and anti-static properties. These coatings enhance the belt’s performance in specific conditions and extend its lifespan.
- Textured Surfaces: Some conveyor belts have textured or patterned surfaces to increase grip and reduce slippage, especially in inclined or declined conveyor systems. These textures can also help in handling materials with irregular shapes or surfaces.
- Impact-Resistant Layers: For applications involving heavy impacts, such as loading from a high drop point, conveyor belts can be reinforced with impact-resistant layers. These layers absorb shocks and protect the carcass and other components from damage.
- Flame-Resistant Materials: In underground mining operations, flame-resistant conveyor belts are crucial for safety. These belts are made from materials that resist ignition and prevent the spread of fire, complying with stringent safety standards.
Understanding the composition of conveyor belts and their special features allows mining operations to select the right belt for their specific needs, ensuring efficiency, durability, and safety in material transport.
Purchasing and Maintenance Tips for Types of Mining Conveyor Belt
Selecting the right types of mining conveyor belt and maintaining them properly are crucial for optimizing the efficiency and longevity of conveyor systems in mining operations. Below are detailed insights on choosing the most suitable conveyor belt and maintaining it to ensure prolonged service life.
Selecting the Right Types of Mining Conveyor Belt
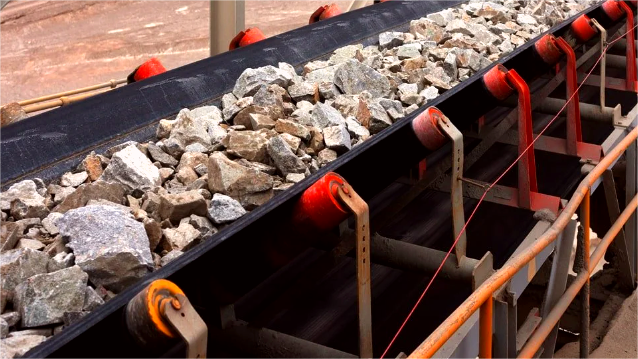
- Assess Material Characteristics: Consider the type of materials the belt will transport. Different materials such as coal, minerals, and ores require specific belt properties like abrasion resistance and conveyor belt tensile strength.
- Consider the Mining Environment: Underground, open-pit, and above-ground operations have distinct environmental conditions that influence the choice of conveyor belt.
- Evaluate Load Capacity and Belt Speed: Choose a belt that can handle the anticipated load volume and speed, ensuring efficient and uninterrupted operations.
- Understand Belt Flexibility Requirements: For systems with numerous curves and angles, select a belt that offers the necessary flexibility without compromising on durability.
- Check for Heat and Fire Resistance: Especially in underground mining, belts with fire-resistant properties are crucial for safety.
- Prioritize Wear and Abrasion Resistance: Durable materials that withstand wear and tear reduce the need for frequent replacements.
- Look for Oil, Grease, and Chemical Resistance: In environments where belts may be exposed to such substances, opting for resistant materials can significantly extend the belt’s lifespan.
- Consider Maintenance and Repair Needs: Some belts are designed for easier maintenance and repair, which can be a critical factor in minimizing downtime.
Find durable and efficient conveyor belts. Send us an inquiry!
Maintenance Tips for Mining Conveyor Belts
- Regular Inspections: Conduct routine inspections to identify wear, damage, or misalignment early.
- Cleanliness: Keep the belt and surroundings clean to prevent material buildup that can affect the belt’s operation and lifespan.
- Proper Tensioning: Ensure the belt is correctly tensioned, as both over-tensioning and under-tensioning can lead to issues.
- Monitor Belt Alignment: Misaligned belts can cause uneven wear and potential damage. Regularly check and adjust alignment.
- Lubricate Moving Parts: Proper lubrication of rollers, pulleys, and other moving parts reduces wear and extends the belt’s life.
- Immediate Repairs: Address any identified damages or issues immediately to prevent further deterioration.
- Use Quality Spare Parts: When repairs are needed, use high-quality spare parts that match the belt’s performance requirements.
- Train Personnel: Ensure that operators and maintenance staff are properly trained on the specifics of the conveyor system to prevent mishandling.
- Implement a Preventive Maintenance Program: Establish a schedule for preventive maintenance based on manufacturer recommendations and operational experience.
- Record Keeping: Maintain detailed records of inspections, maintenance, and repairs to track the belt’s condition and predict future maintenance needs.
By carefully selecting the appropriate types of mining conveyor belt for specific operations and adhering to these maintenance tips, mining operations can significantly enhance the efficiency and longevity of their conveyor systems, leading to improved productivity and reduced operational costs.
FAQs about Types of Mining Conveyor Belt
The most commonly used type of belt in mines is the steel cord belt. Steel cord belts are favored for their high strength, durability, and the ability to carry heavy loads over long distances. These belts are constructed with steel cables embedded in rubber, providing a high level of tear resistance and tensile strength. This makes them particularly suited for the harsh conditions of mining environments, where they must withstand abrasion, impacts, and often sharp materials. Additionally, steel cord belts can operate under high tension and are less susceptible to elongation, making them ideal for deep mines and high-capacity applications where reliability and maintenance minimization are critical.
Conveyor systems in mining are used for the transportation of materials across various stages of the mining process, from extraction to processing and eventually to the delivery of the final product. These systems are integral to modern mining operations as they enhance efficiency, reduce labor costs, and minimize the environmental impact associated with traditional truck haulage. Conveyor systems in mining can range from simple belt conveyors used to transport ore to complex systems integrating multiple types of conveyors, feeders, and elevating mechanisms. They are utilized in both surface and underground mining operations for the movement of bulk materials such as coal, ore, and overburden, facilitating a continuous and reliable flow of materials.
The three main types of conveyor systems are belt conveyors, roller conveyors, and chain conveyors.
Belt Conveyors are the most common and versatile type, used for transporting materials over short to long distances, either horizontally or at inclines. They consist of a continuous belt that moves over rollers or a flat surface, carrying materials from one point to another.
Roller Conveyors utilize a series of rollers to move goods. They are best suited for handling solid items or containers and are commonly used for sorting, assembling, and loading processes. Roller conveyors can be powered or gravity-operated, depending on the application’s needs.
Chain Conveyors are designed to transport heavy loads and are typically used in applications where rugged, durable conveyance solutions are required. They consist of a series of short, interconnected links or chains that move over sprockets, ideal for moving bulky or heavy materials that are unsuitable for belt or roller conveyors.
The most common conveyor belt system is the flat belt conveyor. Flat belt conveyors are widely used across various industries due to their simplicity, efficiency, and versatility. They consist of a flat belt that moves over pulleys and rollers, transporting materials from one point to another. Flat belt conveyors can handle a wide range of materials, from small, delicate parts to large, bulky goods. They are easily customizable to fit specific operational requirements, such as speed, load capacity, and the inclusion of sidewalls or cleats to prevent spillage. Their widespread application includes assembly lines, packaging, sorting, and material handling tasks in manufacturing, warehousing, and logistics operations.
Mining conveyor belts can be purchased from specialized manufacturers that produce industrial conveyor systems and components. Leading companies in this field include ContiTech AG, Bridgestone Corporation, Fenner Dunlop, Phoenix Conveyor Belt Systems GmbH, Yokohama Rubber Co., Ltd., and WCCO Belting. These manufacturers offer a wide range of conveyor belts designed specifically for mining applications, ensuring high durability, reliability, and performance under demanding conditions. Additionally, many of these companies provide custom-engineered solutions to meet the unique requirements of different mining operations. Buyers can contact these manufacturers directly or through their distributors and sales representatives, who can provide technical advice, support, and after-sales service. It’s also possible to explore online industrial marketplaces and trade shows that focus on mining equipment and technology to find a suitable supplier.
There are several types of conveyor belts, each designed to suit specific applications and environments. Here are the primary types of conveyor belts used in various industries:
Flat Belt Conveyors:
Description: The most common type, flat belt conveyors, are used to transport items across short distances.
Applications: Widely used in manufacturing plants, warehouses, and distribution centers.
Features: Simple design, easy to maintain, suitable for moving small to medium-sized items.
Modular Belt Conveyors:
Description: Made from interlocking plastic pieces, these belts are easy to clean and highly durable.
Applications: Commonly found in food processing, pharmaceutical, and packaging industries.
Features: Hygienic, resistant to corrosion, customizable for specific uses.
Cleated Belt Conveyors:
Description: These belts have raised sections (cleats) that help transport materials at an incline.
Applications: Ideal for moving items up or down steep slopes, such as in mining and agriculture.
Features: Prevents material rollback, improves load carrying capacity.
Inclined/Declined Belt Conveyors:
Description: Designed to move products between different elevations.
Applications: Useful in multi-level warehouses and production facilities.
Features: Can be fitted with cleats or textured surfaces to prevent sliding.
Curved Belt Conveyors:
Description: These belts can navigate corners and turns, optimizing space.
Applications: Suitable for complex layouts in various industries.
Features: Smooth transitions, reduced product handling.
Wire Mesh Belt Conveyors:
Description: Constructed from metal wires, these belts are heat resistant and durable.
Applications: Common in high-temperature applications, such as baking, drying, and cooling.
Features: Good airflow, easy to clean, withstands extreme conditions.
Roller Bed Conveyors:
Description: These belts are supported by rollers, which reduce friction and make it easier to move heavy loads.
Applications: Frequently used in warehousing, packaging, and assembly lines.
Features: Efficient for transporting bulky or heavy items, low maintenance.
Specialty Belts:
Description: Customized belts designed for specific purposes, such as magnetic belts, timing belts, and steel belts.
Applications: Used in specialized industries like mining, automotive, and electronics.
Features: Tailored to meet unique operational requirements, offering specialized functions.
Understanding the different types of conveyor belts and their specific applications can help you select the right belt for your needs, ensuring efficiency and durability in your operations.
Last Updated on June 21, 2024 by Jordan Smith
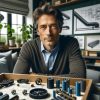
Jordan Smith, a seasoned professional with over 20 years of experience in the conveyor system industry. Jordan’s expertise lies in providing comprehensive solutions for conveyor rollers, belts, and accessories, catering to a wide range of industrial needs. From initial design and configuration to installation and meticulous troubleshooting, Jordan is adept at handling all aspects of conveyor system management. Whether you’re looking to upgrade your production line with efficient conveyor belts, require custom conveyor rollers for specific operations, or need expert advice on selecting the right conveyor accessories for your facility, Jordan is your reliable consultant. For any inquiries or assistance with conveyor system optimization, Jordan is available to share his wealth of knowledge and experience. Feel free to reach out at any time for professional guidance on all matters related to conveyor rollers, belts, and accessories.