Underground Mining Conveyor Belt System
In the intricate and demanding world of underground mining, the role of the underground mining conveyor belt cannot be overstated. Serving as the lifeline of the operation, these belts facilitate the efficient and continuous movement of extracted materials from deep within the earth to the surface.Underground mining conveyor belt tested resist ignition, minimize fire spread, and tackle the toughest underground mining challenges. The selection of an appropriate conveyor belt is paramount, as it directly impacts the safety of the workforce, the operational efficiency, and the overall productivity of the mining endeavor. A well-chosen belt ensures the smooth transportation of materials, minimizes downtime due to maintenance or failures, and adheres to stringent safety standards to protect workers in the challenging underground environment. Thus, understanding the specific requirements of an underground mining operation and matching them with the right conveyor belt is a critical decision that influences the success and sustainability of the mining activities.
What is Underground Mining Conveyor Belt
Underground mining conveyor belt is a pivotal component in the infrastructure of underground mining operations, serving a dual purpose of enhancing productivity and ensuring safety. These belts are engineered to transport extracted materials such as coal, minerals, and ores from the mining face to the surface or processing facilities. Specific examples of their use include transporting coal from longwall faces, moving ore from the blast site to the lift shaft, conveying crushed material to processing plants, shuttling materials between different levels or sections of a mine, removing overburden material in block caving operations, and carrying backfill material to underground voids for stabilization.
The environment within which underground mining conveyor belts operate is fraught with challenges that demand unparalleled durability and reliability from these systems. They must withstand abrasive materials that can wear down belt surfaces, extreme temperatures that can affect the belt’s integrity, heavy loads that require robust tensile strength, moisture and water that can lead to corrosion, sharp objects that can cause tears and punctures, and the ever-present risk of fire that necessitates fire-resistant materials. The necessity for belts that can endure such conditions while maintaining operational efficiency is paramount, as any failure can lead to significant downtime, increased operational costs, and potential safety hazards for the mining personnel.
Key Features of Underground Mining Conveyor Belt
The underground mining conveyor belt is not just a transport mechanism but a critical infrastructure component that enhances the safety, efficiency, and environmental sustainability of underground mining operations. Understanding the key features of these belts can provide insight into their indispensable role in the mining industry.
Increased Safety:
Safety is paramount in underground mining, and conveyor belts contribute significantly to ensuring a safe working environment. They comply with rigorous international standards such as MSHA (Mine Safety and Health Administration in the USA), CAN (Canadian Standards Association), and ISO (International Organization for Standardization) to ensure the highest safety levels. Fire resistance is a critical feature, with materials designed to prevent ignition and slow the spread of flames, essential in environments where the risk of fire is a constant threat.
Durability:
The durability of an underground mining conveyor belt is vital for continuous operation under the extreme conditions of underground mines. These belts are designed with reinforced materials that resist abrasion, tears, and punctures from sharp rocks and heavy loads. They can withstand exposure to harsh chemicals, extreme temperatures, and constant wear and tear from carrying materials like coal, ore, and rock debris. The robust construction ensures longevity and minimizes maintenance downtime, crucial for the uninterrupted flow of operations.
Environmental Considerations:
Modern underground mining conveyor belts are engineered with environmental considerations at the forefront. Efforts to reduce the environmental impact include using energy-efficient motors, low-impact materials, and designs that minimize dust generation and noise pollution. These environmentally friendly features contribute to more sustainable mining practices, aligning with global efforts to protect the environment.
High Tensile Strength:
The high tensile strength of these conveyor belts is essential to handle the heavy loads and long distances typical in mining operations. They are capable of transporting large volumes of material such as extracted ores, broken rock, and coal over extensive underground networks without stretching, sagging, or breaking. This strength ensures reliability in moving materials from deep within the mine to the surface or processing areas, a critical aspect of mining logistics.
Variety in Sizes:
The underground mining conveyor belt comes in a variety of sizes to accommodate different mining operations. Widths can range from narrow belts suitable for confined spaces to wide belts capable of carrying large volumes of material. Lengths can vary from short segments connecting different parts of a mine to long belts that reach several kilometers, facilitating the transport of materials across vast underground distances. This variety allows for customized conveyor systems tailored to the specific needs of each mining operation, ensuring optimal efficiency and productivity.
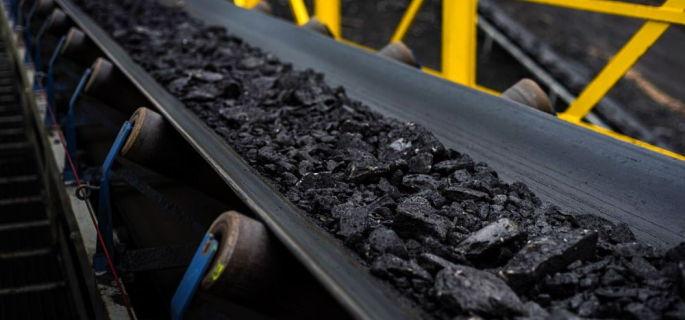
Manufacturers and Parts of Underground Mining Conveyor Belts
Underground mining conveyor belts are critical components in the mining industry, designed to transport raw materials from the mining site to the surface or processing facilities. They are engineered to handle the harsh conditions of underground mining operations, such as dust, moisture, and varying temperatures.
Key Manufacturers of Underground Mining Conveyor Belts
- GRAM manufactures conveyor belts with advanced materials and technology, ensuring high performance and longevity in underground mining environments.
Fenner Dunlop:
- Known for their high-quality conveyor belts, Fenner Dunlop provides a range of products suitable for underground mining applications. Their belts are designed for durability and resistance to wear and tear.
ContiTech (Continental AG):
- A leading supplier of conveyor belts, ContiTech offers belts that are specifically engineered for the demands of underground mining. They focus on safety and efficiency in their designs.
Goodyear:
- Goodyear’s conveyor belts are designed to handle the extreme conditions of underground mining. They provide solutions that enhance productivity and safety.
Phoenix Conveyor Belt Systems:
- Part of Continental AG, Phoenix specializes in producing high-performance conveyor belts for mining and industrial applications, including underground mining.
Parts of Underground Mining Conveyor Belts
Belt:
- The main component, usually made from rubber or synthetic materials, reinforced with layers of fabric or steel cords to provide strength and durability.
Pulleys:
- Essential for driving and guiding the conveyor belt. There are different types of pulleys, such as drive pulleys and tail pulleys, each serving specific functions.
Idlers:
- Support the conveyor belt and the load being transported. Idlers are placed at regular intervals along the conveyor to ensure smooth and efficient operation.
Drive System:
- Comprises motors, reducers, and couplings that provide the necessary power to move the conveyor belt.
Belt Cleaner:
- Installed to remove any material stuck to the belt, ensuring it runs smoothly and efficiently. Primary and secondary cleaners are used for this purpose.
Skirtboard and Sealing Systems:
- Prevent spillage of material and help contain dust within the conveyor system.
Take-up System:
- Maintains the proper tension in the conveyor belt. Gravity take-up systems or screw take-up systems are commonly used in underground mining.
Frame:
- The structural backbone of the conveyor system, supporting all the other components.
Belt Training Components:
- Ensure that the belt runs straight and true on the conveyor structure, preventing misalignment and potential damage.
Safety Devices:
- Include emergency stop switches, pull cords, and sensors to enhance the safety of the conveyor system and protect workers.
Choosing the right manufacturer and parts for your underground mining conveyor belt involves several considerations. Firstly, assess the manufacturer’s reputation in the industry, focusing on their commitment to quality, safety, and innovation. Look for manufacturers with a proven track record in underground mining applications, as they will have a deeper understanding of the unique challenges faced in such environments. Secondly, evaluate the range and quality of parts offered, ensuring they meet or exceed industry standards and are compatible with your conveyor system. Finally, consider the manufacturer’s support services, including technical assistance, warranty, and availability of spare parts, as these factors can significantly impact the operational efficiency and longevity of your conveyor system.
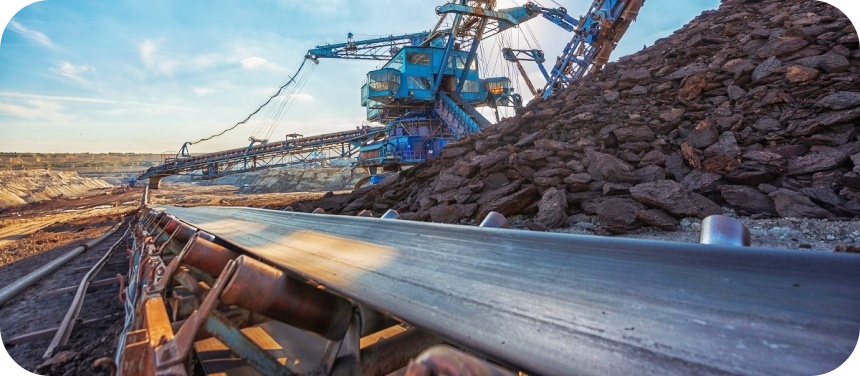
Underground mining conveyor belts are integral to the efficiency and safety of mining operations. With advancements in technology and materials, these belts are becoming more durable and capable of handling the demanding conditions of underground environments. Leading manufacturers continue to innovate, providing robust solutions that enhance productivity and safety in the mining industry.
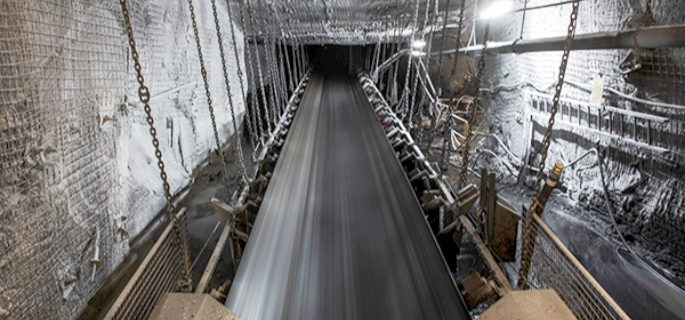
Innovations and Technologies in Underground Mining Conveyor Belts
The realm of underground mining conveyor belts has seen significant advancements in technology, focusing on materials and design improvements to meet the evolving demands of the mining industry. Innovations such as the use of ultra-durable synthetic materials that offer enhanced resistance to wear and tear, the integration of RFID chips for real-time tracking and monitoring of belt conditions, the development of self-extinguishing belt materials to enhance fire safety, the application of reinforced splice designs to ensure belt integrity, the incorporation of sensor-based monitoring systems for predictive maintenance, and the design of energy-efficient conveyor systems to reduce operational costs, all represent the cutting edge in conveyor belt technology.
These technological advancements play a crucial role in enhancing the safety and efficiency of underground mining conveyor belt. For instance, sensor-based monitoring systems enable the early detection of potential issues such as misalignments or wear, allowing for timely maintenance and reducing the risk of costly downtime. Self-extinguishing materials and improved fire-resistant coatings significantly enhance fire safety, protecting both the workforce and the infrastructure. Energy-efficient designs and the use of eco-friendly materials contribute to sustainable mining practices by reducing power consumption and minimizing environmental impact. Advanced splicing techniques and materials ensure robust belt joints, critical for maintaining the integrity of the conveyor system over long distances and under heavy loads. The integration of smart technologies and automation in conveyor systems facilitates optimized material flow and real-time data analysis, leading to improved operational decisions and increased productivity. Lastly, ergonomic and user-friendly control systems enhance the user interface, making it easier for operators to manage and monitor conveyor operations, further contributing to the overall efficiency and safety of mining operations.
Underground mining presents unique challenges that require advanced solutions to ensure safety, efficiency, and productivity. Conveyor belts are integral to the operation, transporting materials seamlessly through complex and often hazardous environments. Innovations in conveyor belt technology have significantly improved their performance, durability, and adaptability in underground mining settings. This article explores the latest advancements and technologies in underground mining conveyor belts.
Looking for detailed information on our conveyor belts? Complete the form and we’ll get back to you with the answers you need.
High-Strength Materials
One of the critical innovations in conveyor belt technology is the use of high-strength materials. Modern conveyor belts are often made from reinforced rubber, steel cord, or synthetic fibers like Kevlar. These materials enhance the belt’s tensile strength, allowing it to carry heavier loads over longer distances without stretching or breaking. This improvement is particularly crucial in underground mining, where the belts must withstand harsh conditions and significant wear and tear.
Flame-Resistant Belts
Safety is paramount in underground mining, where the risk of fire is ever-present. Flame-resistant conveyor belts have been developed to reduce the risk of fire spreading. These belts are made from materials that resist ignition and self-extinguish if exposed to flames. This innovation helps protect miners and equipment, ensuring safer working conditions.
Condition Monitoring Systems
Advanced condition monitoring systems have revolutionized conveyor belt maintenance. These systems use sensors and IoT technology to continuously monitor the belt’s health, detecting issues such as wear, misalignment, and temperature changes. Real-time data allows for predictive maintenance, reducing downtime and preventing catastrophic failures. By addressing problems before they escalate, mining operations can maintain higher efficiency and productivity.
Energy-Efficient Drives
Energy consumption is a significant concern in mining operations. New energy-efficient drive systems for conveyor belts have been developed to reduce power usage while maintaining performance. Variable frequency drives (VFDs) and direct drives optimize the belt’s speed and torque, matching the operational demands and minimizing energy waste. These technologies help mining companies lower their energy costs and reduce their environmental footprint.
Automated Control Systems
Automation plays a crucial role in modern underground mining. Conveyor belts equipped with automated control systems can adjust their operation based on real-time data and predefined algorithms. These systems manage belt speed, load distribution, and tension, optimizing performance and reducing the need for manual intervention. Automation enhances safety by reducing human exposure to hazardous environments and improves overall operational efficiency.
Modular Conveyor Systems
Modular conveyor systems offer flexibility and scalability in underground mining operations. These systems consist of interchangeable modules that can be easily assembled, disassembled, and reconfigured to meet changing mining needs. The modular design simplifies maintenance and repair, allowing for quick replacement of damaged sections without extensive downtime. This adaptability is particularly beneficial in dynamic mining environments where operational requirements frequently change.
Improved Belt Cleaning Technologies
Effective belt cleaning is essential to maintain conveyor performance and longevity. Advanced belt cleaning systems use a combination of mechanical scrapers, brushes, and water sprays to remove material buildup and prevent carryback. These technologies reduce the risk of belt damage and ensure efficient material transport. Improved cleaning systems also minimize the need for manual cleaning, enhancing safety and reducing labor costs.
The advancements in underground mining conveyor belt technology have significantly improved the safety, efficiency, and reliability of mining operations. High-strength materials, flame-resistant belts, condition monitoring systems, energy-efficient drives, automated control systems, modular designs, and improved cleaning technologies are just a few of the innovations driving the industry forward. As technology continues to evolve, we can expect further improvements that will enhance the capabilities and performance of underground mining conveyor belts, contributing to safer and more productive mining environments.
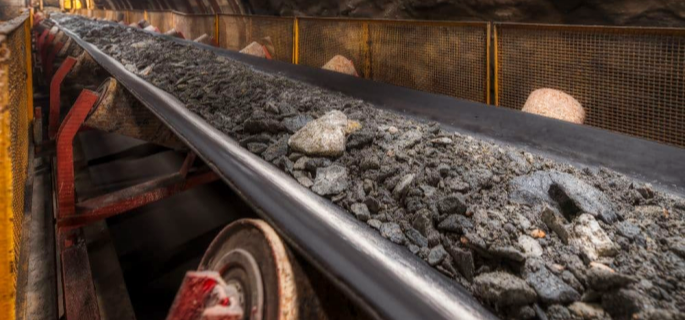
Types of Conveyor Belts Used in Mining with Underground Mining Conveyor Belt Focus
The underground mining conveyor belt landscape is diverse, with various types designed to address the unique challenges of subterranean environments. These belts are pivotal in ensuring the efficient and safe transport of materials within mines.
Multi-ply Belts: Common in underground mining, these belts consist of multiple layers of fabric with rubber interlays, enhancing their durability and load-bearing capacity. Examples include nylon/nylon (NN), polyester/nylon (EP), cotton/nylon (CN), and cotton/cotton (CC) belts, each offering varying degrees of flexibility, strength, and resistance to different environmental conditions.
Straight-warp Belts: Designed to withstand sharp objects and high-impact forces, straight-warp belts are essential in areas prone to heavy wear and tear. They are characterized by their unique construction, which includes a single layer of fabric with weft and warp wires that provide exceptional tear resistance and tensile strength.
Steel-cord Belts: These belts feature longitudinal steel cords for reinforcement, making them ideal for long-distance and high-load applications. Steel-cord belts are known for their low elongation, high tensile strength, and excellent durability, making them suitable for deep underground mining operations where reliability is crucial.
Heat-resistant Belts: In mines where high temperatures are a concern, such as those dealing with hot materials or located in warm climates, heat-resistant belts are used. These belts are made from compounds that can withstand elevated temperatures without degrading, ensuring the integrity of the conveyor system.
Factors Influencing Selection: The selection of an underground mining conveyor belt type is influenced by several factors, including the material to be transported, the mining environment, the distance over which the material must be moved, and the mine’s operational requirements. For instance, the abrasive nature of the mined material may necessitate a belt with high wear resistance, while the presence of flammable gases could require the use of fire-resistant belts. The belt’s width, speed, and load capacity must also be matched to the mine’s production needs to ensure efficient and uninterrupted operations.
Understanding these types and their applications helps in selecting the most appropriate underground mining conveyor belt for specific mining tasks, ensuring operational efficiency, safety, and longevity of the conveyor system.
Design and Structure of Underground Mining Conveyor Belts
The design and structure of an underground mining conveyor belt are critical to its performance, operational efficiency, and safety. These belts must be meticulously engineered to withstand the harsh conditions of underground mining while ensuring the continuous and reliable transportation of materials.
Key Considerations in Design and Structure:
- Material Composition: The choice of materials, such as rubber compounds, synthetic fabrics, or steel cords, is crucial for durability and functionality. For instance, rubber belts with fire-resistant properties are essential in coal mines to mitigate fire risks.
- Belt Width and Thickness: These dimensions are selected based on the capacity requirements and the size of the material to be transported. Wider and thicker belts can carry more material, which is vital for high-production mines.
- Tensile Strength: The belt must have sufficient tensile strength to handle the operational loads without stretching or breaking. This is particularly important in long-haul applications where the belt spans extensive distances.
- Reinforcement Features: Features like rip and tear resistance are vital for belts operating in environments with sharp, abrasive materials. Reinforcements such as steel cords or special fabric weaves enhance the belt’s durability.
- Conveyor Structure: The supporting structure, including frames, idlers, and rollers, must be robust to support the belt and the load it carries. The design should also allow for easy maintenance and adjustments.
- Drive and Tensioning Systems: Efficient drive systems are necessary for the smooth operation of the belt, while tensioning mechanisms ensure the belt remains taut and minimizes slippage.
Importance of Conveyor Belt Structure Design:
The design of an underground mining conveyor belt structure is paramount in ensuring operational efficiency and safety. A well-designed belt minimizes the risk of operational failures, such as belt slippage, misalignment, or tears, which can lead to downtime and pose safety hazards. The structure must also accommodate the unique challenges of the underground environment, including limited space, variable terrain, and the need for flexibility in installation and maintenance. Moreover, the design impacts the belt’s lifespan and the overall cost-effectiveness of the conveyor system. By prioritizing the structural integrity and suitability of the conveyor belt design, mining operations can achieve higher productivity, maintain safety standards, and reduce operational costs.
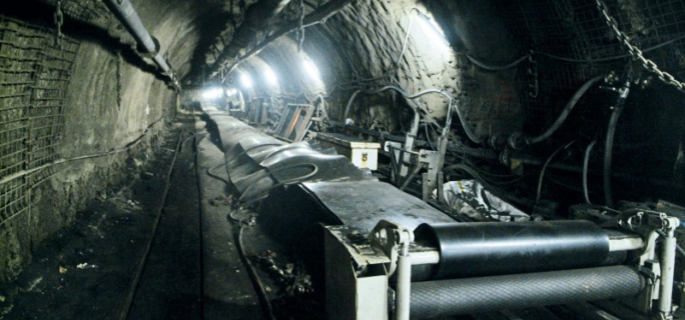
Applications and Case Studies of Underground Mining Conveyor Belts
The underground mining conveyor belt plays a pivotal role in the efficient operation of below-ground mining activities. Its applications span across various mining operations, demonstrating its versatility and critical importance in ensuring productivity and safety.
Real-world Applications:
- Coal Transportation: In coal mines, the underground mining conveyor belt is used extensively to transport coal from the mining face to the surface for processing. This application showcases the belt’s ability to handle bulk materials over long distances.
- Ore Haulage: In metal mines, these conveyor belts transport ore from deep within the mine to processing areas, highlighting their capacity to carry heavy loads and operate in challenging conditions.
- Material Handling in Gold Mines: Conveyor belts in gold mines efficiently move extracted rock and ore to crushing and screening facilities, demonstrating their role in streamlining the gold extraction process.
- Waste Removal: Conveyor belts are also used for removing overburden and waste materials, proving their utility in maintaining the cleanliness and efficiency of mining operations.
- Backfilling Applications: These belts transport backfill material to underground voids, aiding in mine stabilization and showcasing their versatility in material handling.
- Connecting Underground Operations: Conveyor belts link various sections of a mine, facilitating the seamless flow of materials and personnel between different mining areas.
Case Studies:
- Case Study 1: A case study from a large-scale coal mine revealed that implementing an optimized underground mining conveyor belt system led to a 20% increase in coal transportation efficiency. The study highlighted the importance of conveyor design in maximizing throughput and reducing energy consumption.
- Case Study 2: In a precious metal mine, the introduction of a high-strength, fire-resistant conveyor belt resulted in a significant reduction in fire incidents, enhancing worker safety and minimizing production downtime.
- Case Study 3: A copper mine’s case study demonstrated how the integration of sensor-based monitoring systems in conveyor belts led to a 30% reduction in maintenance costs. The sensors provided real-time data on belt health, allowing for predictive maintenance and avoiding unexpected failures.
- Case Study 4: A study in a diamond mine showed that the use of specially designed, wear-resistant conveyor belts extended the belt’s lifespan by 50%, reducing replacement costs and ensuring continuous operation.
- Case Study 5: In an underground salt mine, the implementation of an energy-efficient conveyor belt system led to a 15% reduction in energy consumption, showcasing the environmental and economic benefits of optimized conveyor systems.
These applications and case studies underscore the critical role of the underground mining conveyor belt in enhancing the efficiency, safety, and sustainability of mining operations. They highlight how advancements in conveyor belt technology and design can lead to significant improvements in mining productivity and operational safety.
Maintenance and Safety of Underground Mining Conveyor Belts
The underground mining conveyor belt is a critical component of the mining infrastructure, necessitating stringent maintenance and safety protocols to ensure operational longevity and protect workers and equipment.
Best Practices for Maintenance:
- Regular Inspections: Conducting routine inspections of the underground mining conveyor belt to identify wear, damage, or misalignments early can prevent costly repairs and downtime.
- Scheduled Cleaning: Regular cleaning of the conveyor belt and components helps prevent material buildup that can lead to belt misalignment or operational inefficiencies.
- Lubrication of Moving Parts: Proper lubrication of rollers, pulleys, and other moving parts reduces friction, wear, and the risk of overheating, extending the lifespan of the conveyor system.
- Belt Tension Monitoring: Maintaining optimal belt tension ensures efficient operation and prevents slippage or excessive wear.
- Splice Monitoring and Repair: Regularly checking the splices for signs of wear or damage and conducting timely repairs can prevent belt failures.
- Training for Maintenance Staff: Providing comprehensive training for maintenance personnel on the specific requirements of underground mining conveyor belts ensures that they can effectively identify and address issues.
Safety Protocols and Measures:
- Emergency Stop Systems: Installing easily accessible emergency stop mechanisms along the length of the conveyor belt allows for the immediate shutdown of the system in case of an emergency.
- Guarding of Moving Parts: Implementing guards around moving parts such as pulleys and rollers prevents accidental contact and injuries.
- Fire Prevention and Suppression: Equipping the conveyor system with fire-resistant belts, fire detectors, and suppression systems minimizes the risk of fire, a critical concern in underground mining.
- Regular Safety Training: Conducting regular safety training sessions for all workers operating near or with the underground mining conveyor belt ensures they are aware of potential hazards and emergency procedures.
- Conveyor Belt Alignment: Ensuring the conveyor belt is properly aligned reduces the risk of belt damage and potential accidents caused by material spillage.
- Visibility and Signage: Enhancing visibility around the conveyor area with adequate lighting and clear signage helps prevent accidents by making workers aware of the conveyor’s presence and operational status.
Adhering to these maintenance and safety best practices ensures the underground mining conveyor belt operates efficiently and safely, minimizing the risk of downtime and enhancing the overall safety of the mining environment.
FAQs About Underground Mining Conveyor Belt
A conveyor belt in mining is an essential component of a mining conveyor system, which is used to transport bulk materials across distances within a mine. These belts serve as the backbone of material handling systems in various mining operations, including the extraction of coal, metals, and minerals. The primary purpose of a conveyor belt in mining is to improve efficiency and safety by automating the transportation of materials from the mining site to processing facilities or storage areas. This automation reduces the need for manual labor, minimizes transportation time, and lowers the risk of accidents associated with material handling. Conveyor belts in mining are designed to withstand harsh conditions, including abrasive materials, heavy loads, and varying temperatures, ensuring reliable operation in challenging environments.
In mining, several types of conveyor belts are used, each designed for specific applications and material handling requirements. The most common types include:
Multi-ply Belts: Composed of multiple layers of fabric with rubber interlays, these belts are versatile and used for transporting a variety of materials.
Straight-warp Belts: Known for their high impact and tear resistance, making them suitable for heavy-duty applications such as transporting large rocks.
Steel-cord Belts: Characterized by steel cables running the length of the belt, these are used for long-distance and high-load applications, offering superior strength and durability.
Solid Woven Belts: Made from a single, solid woven layer of fabric, these belts are often used in underground mining due to their fire-resistant properties.
Each type of belt is selected based on the specific needs of the mining operation, including the material to be transported, the distance of transportation, and the environmental conditions.
Underground conveyor belts are typically made from durable materials that can withstand the demanding conditions of underground mining environments. The most common materials include:
Rubber: Often reinforced with textiles or steel cords for added strength, rubber conveyor belts are widely used for their flexibility, durability, and resistance to abrasion and impact.
PVC (Polyvinyl Chloride): PVC belts are flame-resistant and suitable for applications where fire safety is a concern, such as in coal mines.
Polyurethane: Known for its resistance to wear, tear, and water, polyurethane belts are used in applications where durability and longevity are critical.
Kevlar®: For extremely challenging conditions, Kevlar-reinforced belts offer high strength, low stretch, and resistance to high temperatures and chemicals.
The choice of material depends on factors such as the type of material being transported, the presence of potentially hazardous conditions, and the need for fire resistance.
The most commonly used type of conveyor belt in mines is the multi-ply rubber belt. This type of belt is favored for its versatility, as it can handle a wide range of materials from fine powders to large, bulky items. Multi-ply rubber belts are constructed from several layers of fabric and rubber, which provide the necessary strength and flexibility for various mining applications. They are particularly valued for their durability, ability to absorb impacts, and resistance to abrasion, making them suitable for both surface and underground mining operations. The adaptability of multi-ply rubber belts to different environmental conditions and their cost-effectiveness also contribute to their widespread use in the mining industry.
Last Updated on July 22, 2024 by Jordan Smith
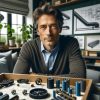
Jordan Smith, a seasoned professional with over 20 years of experience in the conveyor system industry. Jordan’s expertise lies in providing comprehensive solutions for conveyor rollers, belts, and accessories, catering to a wide range of industrial needs. From initial design and configuration to installation and meticulous troubleshooting, Jordan is adept at handling all aspects of conveyor system management. Whether you’re looking to upgrade your production line with efficient conveyor belts, require custom conveyor rollers for specific operations, or need expert advice on selecting the right conveyor accessories for your facility, Jordan is your reliable consultant. For any inquiries or assistance with conveyor system optimization, Jordan is available to share his wealth of knowledge and experience. Feel free to reach out at any time for professional guidance on all matters related to conveyor rollers, belts, and accessories.