Sustainable Solutions: Overland Belt Conveyor Systems
Overland belt conveyor systems represent a pivotal advancement in the transportation of bulk materials over long distances. These sophisticated conveyor solutions are engineered to efficiently move vast quantities of materials such as minerals, aggregates, and other bulk commodities, thereby playing a crucial role in the mining and bulk material handling sectors. Their significance cannot be overstated, as they not only enhance operational efficiency but also contribute to substantial cost savings and environmental benefits compared to traditional truck haulage methods. By integrating overland belt conveyor systems into their operations, industries can achieve a seamless, continuous flow of materials, ensuring a steady supply chain and bolstering productivity on a grand scale.
What Are Overland Belt Conveyor Systems?
Overland belt conveyor systems are an integral part of the material handling industry, designed to transport bulk materials over long distances efficiently. These systems consist of a long, continuous belt that rides on a series of rollers or idlers and is powered by pulleys at either end. The belt itself is often made from layers of rubber and fabric or steel cords to provide strength and flexibility, making overland belt conveyor systems capable of handling a wide range of materials, from fine powders to large, abrasive rocks.
The basic concept of overland belt conveyor systems revolves around their ability to move large quantities of material over considerable distances without the need for continuous manual handling or the use of trucks. This not only reduces labor costs but also minimizes the environmental impact by cutting down on fuel consumption and emissions associated with truck transport.
To illustrate the advantages of overland belt conveyor systems over traditional transportation methods, consider the following comparison:
Feature | Overland Belt Conveyor Systems | Traditional Truck Transport |
---|---|---|
Capacity | Can transport thousands of tons per hour | Limited by truck size, typically less than 100 tons per load |
Distance | Efficient over long distances, several kilometers | Cost and efficiency decrease significantly over longer distances |
Environmental Impact | Low emissions, reduced noise, and minimal landscape disruption | High fuel consumption, emissions, and potential road damage |
Operational Cost | Lower energy consumption and maintenance costs over time | High fuel, labor, and maintenance costs |
Continuous Operation | Can operate continuously without interruption | Requires loading and unloading, leading to potential delays |
By integrating overland belt conveyor systems into their operations, industries can achieve significant improvements in efficiency, cost savings, and environmental sustainability compared to relying solely on traditional truck transport methods.
Key Components of Overland Belt Conveyor Systems
Overland belt conveyor systems are complex assemblies made up of several key components that work together to transport materials efficiently over long distances. Understanding these components is essential for anyone involved in the design, operation, or maintenance of these systems. Here’s a closer look at the eight essential components that make up overland belt conveyor systems:
- Conveyor Belt: The heart of overland belt conveyor systems, the conveyor belt is the medium through which materials are transported across the system. It is typically made from layers of rubber, fabric, and steel cords to provide strength, durability, and flexibility.
- Head Pulley: Positioned at the discharge end of the conveyor, the head pulley is powered by an electric motor, which drives the conveyor belt and moves the material along. The head pulley is often coated with a rubber lagging to increase friction and improve belt traction.
- Tail Pulley: Located at the loading end, the tail pulley serves as the turnaround point for the conveyor belt. It can also be adjusted to maintain the proper tension in the belt, ensuring smooth operation.
- Idler Rollers: These support the conveyor belt along its length, providing a smooth surface for the belt to ride on. Idler rollers are strategically placed to support the weight of the belt and the material being transported, preventing sagging and ensuring efficient movement.
- Conveyor Frame: The structure that supports all the components of the conveyor, including the belt, pulleys, and idlers. The conveyor frame is designed to be sturdy and durable, capable of withstanding the weight and forces exerted by the moving belt and the materials it carries.
- Drive System: Comprising motors, gearboxes, and drive belts, the drive system provides the necessary power to the head pulley to move the conveyor belt and transport materials.
- Belt Tensioning System: Essential for maintaining the correct tension in the conveyor belt, the belt tensioning system ensures efficient operation and prevents slippage or excessive wear. This can be achieved through weighted take-up units or screw take-up units.
- Control System: Modern overland belt conveyor systems are equipped with sophisticated control systems that monitor and regulate the operation of the conveyor. These systems can adjust the speed of the belt, monitor the load, and even stop the conveyor in case of an emergency.
In addition to these components, overland belt conveyor systems can also include special features like Pipe Conveyor Systems. Pipe conveyors are a variation of the traditional belt conveyor where the belt is formed into a circular cross-section, enclosing the conveyed material and protecting it from the environment. This design is particularly useful for transporting materials that need to be protected from contamination or that could pose a hazard if spilled, such as chemicals or minerals.
Understanding these key components and their functions is crucial for the efficient and reliable operation of overland belt conveyor systems. Each component plays a vital role in the system’s overall performance, and their proper maintenance and operation are essential for the long-term success of material transport projects.
Types of Overland Belt Conveyors
Overland belt conveyor systems come in various designs, each tailored to meet specific transportation needs across different terrains and for various materials. Below is a detailed look at the types of overland belt conveyors, highlighting their unique features and applications:
Type | Description | Application |
---|---|---|
Roller Bed Belt Conveyor | Features rollers that provide support to the conveyor belt, reducing friction and making it ideal for longer distances. | Best suited for smooth, flat surfaces where high speed and long distance transportation are required. |
Flat Belt Conveyor | Utilizes a flat belt surface, making it one of the most versatile and commonly used systems for moving items. | Widely used across industries for transporting various items, from small components to large volumes of materials. |
Modular Belt Conveyor | Comprises a series of interlocking plastic modules, making it flexible and suitable for conveying products with complex routes and shapes. | Ideal for applications requiring sharp turns, inclines, or declines within the conveyor path. |
Cleated Belt Conveyor | Equipped with cleats or barriers on the belt surface to prevent slippage of materials, especially on inclines. | Used for inclined paths where materials need to be transported upwards without rollback. |
Curved Belt Conveyor | Designed to navigate around obstacles with ease, featuring belts that can curve around bends. | Suitable for facilities with limited space where conveyor paths need to navigate around existing structures. |
Incline/Decline Belt Conveyor | Specifically designed to manage elevation changes, allowing materials to be moved up or down. | Used in applications where materials need to be transported to different levels within a facility. |
Troughed Belt Conveyor | Features a belt that forms a trough, providing more space and support for bulk materials. | Commonly used in the mining and agricultural sectors for transporting large volumes of bulk materials like coal, grain, or minerals. |
Underground Conveyor Belt Systems | Engineered to operate within underground environments, providing a safe and efficient way to transport materials out of mines. | Essential in mining operations for moving extracted materials from deep underground to the surface. |
Mobile Conveyor Belt Systems | Portable conveyors that can be easily moved and set up for temporary transportation needs. | Useful in construction sites, mining operations, and other scenarios where temporary or flexible transportation solutions are needed. |
Each of these overland belt conveyor systems is designed to address specific challenges in material transportation, offering solutions that enhance efficiency, safety, and productivity in various industrial settings. Whether it’s navigating complex routes with a modular belt conveyor or efficiently moving bulk materials with a troughed belt conveyor, these systems play a crucial role in modern material handling and logistics.
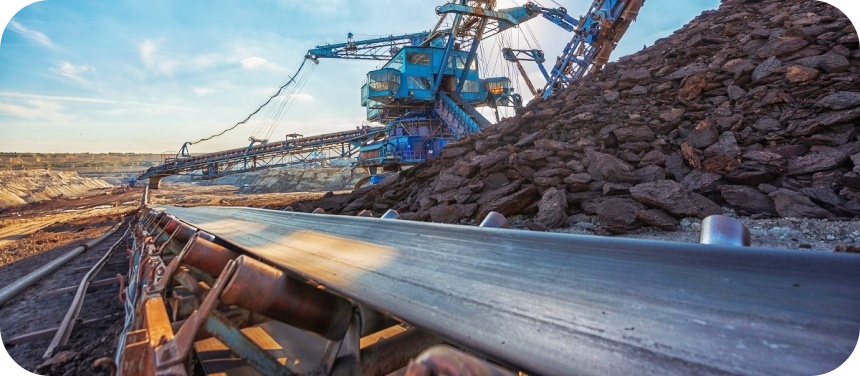
Design and Selection Considerations for Overland Belt Conveyor Systems
Factors Influencing Design
When designing and selecting overland belt conveyor systems, several critical factors must be considered to ensure the system meets the specific needs of the operation while maintaining efficiency, reliability, and cost-effectiveness. Here are ten key factors influencing the design and selection of these systems:
- Motor and Gearbox Selection: The motor provides the necessary power to drive the conveyor belt, and the gearbox ensures the motor’s power is used efficiently. The selection of these components depends on the required speed, torque, and power needed to move the materials.
- Speed of Belt: The belt speed is a crucial factor that affects the capacity of the conveyor and the level of wear on the belt. Higher speeds can increase capacity but may also lead to increased wear and maintenance requirements.
- Tension and Take-up: Proper belt tension is essential for efficient operation. Take-up units allow for adjustments in belt tension due to stretch or changes in environmental conditions, ensuring consistent performance.
- Material to be Conveyed: The type, size, weight, and abrasiveness of the material being transported significantly influence the design of the conveyor system, including the choice of belt material and the design of the loading and discharge points.
- Distance: The length of the conveyor directly impacts the design, particularly in terms of power requirements and structural support needed to span the distance without excessive sagging or stress on the belt.
- Working Environment: Environmental factors such as temperature, humidity, exposure to chemicals, and the presence of dust or water can affect the selection of materials and components used in overland belt conveyor systems.
- Terrain and Route: The topography and layout of the route the conveyor will follow must be considered, as steep inclines, declines, and turns require specific design considerations to maintain efficiency and safety.
- Load Capacity: The system’s design must accommodate the maximum expected load while providing a buffer for peak conditions, ensuring the conveyor can operate effectively under all circumstances.
- Energy Efficiency: Designing for energy efficiency can significantly reduce operational costs. This includes selecting energy-efficient motors, optimizing conveyor speed, and minimizing resistance and friction.
- Safety and Compliance: Safety features and compliance with local, national, and industry-specific regulations and standards must be integrated into the design to protect workers and the environment.
Importance of Choosing the Right Type
The importance of choosing the right type of conveyor for specific applications cannot be overstated. Each type of overland belt conveyor system offers unique advantages and is suited to particular applications:
- Bulk Material Handling: Troughed belt conveyors are often the best choice for large volumes of bulk materials due to their capacity and efficiency.
- Inclined or Declined Routes: Cleated and incline/decline belt conveyors are designed to handle materials on slopes, preventing slippage and ensuring stable transport.
- Complex Routes: Modular belt conveyors can navigate complex routes with ease, making them ideal for facilities with space constraints or the need for multiple turns and elevation changes.
- Enclosed Transport: Pipe conveyor systems provide an enclosed transport solution, protecting materials from environmental elements and minimizing spillage.
- High-Speed Transport: Roller bed belt conveyors are suitable for high-speed transport over long, flat distances, reducing friction and increasing efficiency.
- Portable Applications: Mobile conveyor belt systems offer flexibility and ease of relocation, making them suitable for temporary or shifting operations.
Selecting the appropriate overland belt conveyor system involves a careful analysis of these factors and considerations to ensure optimal performance, reliability, and return on investment.
Benefits of Overland Belt Conveyor Systems
Overland belt conveyor systems offer a multitude of advantages that make them a preferred choice for bulk material handling across various industries. These systems are not only efficient and cost-effective but also contribute significantly to environmental conservation and enhance safety standards. Here’s a detailed look at the benefits of overland belt conveyor systems:
Efficiency and Cost-effectiveness
One of the primary benefits of overland belt conveyor systems is their ability to transport materials over long distances efficiently. Unlike truck transport, which requires multiple trips and significant manpower, a single overland conveyor can move thousands of tons of material per hour continuously, without interruption. This continuous flow of materials leads to substantial savings in time and operational costs, making overland conveyors an economically viable solution for many industries.
Moreover, overland belt conveyor systems have lower energy consumption compared to other modes of transport. The reduced friction between the belt and the idlers allows for smoother operation, which, in turn, lowers energy requirements and operational costs. The ability to transport large volumes of material with minimal energy use translates into significant cost savings over the lifespan of the conveyor.
Environmental Benefits
Overland belt conveyor systems offer notable environmental benefits, making them an eco-friendly alternative to traditional transport methods. These systems produce zero emissions during operation, as they do not rely on fossil fuels like trucks do. This reduction in emissions is crucial in the fight against air pollution and climate change.
Additionally, overland conveyors minimize noise pollution and dust generation, which are common issues associated with truck transport. The enclosed design of many overland conveyor systems helps contain dust and reduce its release into the environment, contributing to cleaner air and a healthier ecosystem. The lower noise levels also make overland conveyors more suitable for operations close to residential areas, where noise pollution can be a significant concern.
Safety Improvements
Safety is a paramount concern in any industrial operation, and overland belt conveyor systems offer several safety advantages over traditional transport methods. The risk of accidents associated with vehicle collisions and overturning is eliminated with conveyor systems. Moreover, the automated nature of overland conveyors reduces the need for human intervention, thereby minimizing the risk of workplace injuries associated with manual handling of materials.
Overland belt conveyor systems are also equipped with various safety features, including emergency stop systems, pull cord switches, and belt misalignment sensors, which further enhance the safety of operations. These features ensure that any potential issues can be quickly addressed, reducing the risk of accidents and ensuring the safety of personnel.
Overland belt conveyor systems stand out as an efficient, cost-effective, and environmentally friendly solution for transporting materials over long distances. Their ability to reduce emissions, noise, and dust, coupled with significant safety improvements, makes them an ideal choice for industries looking to optimize their bulk material handling processes while minimizing their environmental footprint and enhancing safety standards.
Applications in Industries for Overland Belt Conveyor Systems
Overland belt conveyor systems have found extensive applications across a wide range of industries due to their efficiency, reliability, and capacity to move large volumes of material over long distances. Here’s how various sectors leverage these systems to enhance their operations:
Bulk Handling: Mining, Quarrying, Agriculture
In the mining and quarrying sectors, overland belt conveyor systems are indispensable for transporting extracted materials such as ores, minerals, and aggregates from the mining site to processing facilities or storage areas. These systems are designed to withstand harsh operating conditions, including abrasive materials and rugged terrain, ensuring continuous and efficient material flow. Similarly, in agriculture, overland conveyors are used to transport grains, fertilizers, and other bulk agricultural products, significantly improving the efficiency of farm operations and storage management.
Automotive: Assembly Lines and Parts Transport
The automotive industry relies on overland belt conveyor systems to streamline assembly lines and parts transport within manufacturing facilities. These systems facilitate the smooth and continuous movement of vehicle components from one assembly station to the next, ensuring a seamless production process. The precision and reliability of overland conveyors make them ideal for handling delicate parts and maintaining the pace of production.
Transport and Courier: Package Handling
Overland belt conveyor systems play a crucial role in the transport and courier industry, particularly in sorting centers and distribution hubs. They are used to efficiently move packages of various sizes and weights, sorting them based on destination or other criteria. This automation significantly reduces manual handling, speeds up processing times, and increases the overall efficiency of package distribution networks.
Food Handling: Processing and Packaging Lines
In the food processing industry, overland belt conveyor systems are used to transport raw materials, finished products, and packaged goods along processing and packaging lines. These systems are designed to meet stringent hygiene standards, with materials and surfaces that are easy to clean and maintain. Overland conveyors ensure the gentle handling of food products, minimizing damage and preserving quality from production to packaging.
Power Generation: Coal and Biomass Transport
Overland belt conveyor systems are critical in the power generation industry for transporting coal and biomass from storage facilities to combustion units. These systems enable power plants to maintain a consistent supply of fuel, ensuring uninterrupted power generation. The capacity to move large volumes of material efficiently makes overland conveyors an essential component of the energy supply chain.
Civil and Construction: Material Handling on Large Project Sites
In the civil and construction sector, overland belt conveyor systems are utilized for material handling on large project sites, such as dams, highways, and urban development projects. They transport construction materials like sand, gravel, and cement over considerable distances, from storage areas to construction sites, facilitating faster and more efficient building processes.
Across these diverse industries, overland belt conveyor systems prove to be invaluable assets, enhancing productivity, reducing operational costs, and contributing to safer and more sustainable operations. Their versatility and adaptability to different materials and environments underscore their importance in modern industrial and commercial activities.
Choosing the Right Manufacturer and System for Overland Belt Conveyor Systems
Selecting the appropriate manufacturer and overland belt conveyor system is crucial for ensuring operational efficiency, reliability, and longevity of the system. Here are key points to consider:
Importance of Selecting Reputable Belt Conveyor Manufacturers
- Experience and Expertise: Established manufacturers with a proven track record in designing and implementing overland belt conveyor systems can provide invaluable insights and solutions tailored to specific industry needs.
- Quality Assurance: Reputable manufacturers adhere to stringent quality standards, ensuring that the components and systems are durable and reliable.
- Innovative Solutions: Leading manufacturers invest in research and development, offering innovative solutions that enhance efficiency and sustainability.
- Comprehensive Support: From initial consultation to after-sales services, reputable manufacturers offer comprehensive support, ensuring smooth operation and maintenance.
- Customization Capabilities: The ability to customize conveyor systems according to specific project requirements is essential for optimal performance.
- Safety Standards: Adherence to international safety standards is crucial to protect workers and the environment.
- Sustainability Practices: Manufacturers committed to sustainability can help reduce the environmental impact of conveyor operations.
- Global Reach: Manufacturers with a global presence can provide support and services across different regions, ensuring consistency in quality and service.
Considerations for Purchasing Overland Conveyor Systems for Sale
- Project Requirements: Understand the specific requirements of your project, including material type, volume, and transport distance.
- System Design: Evaluate the design capabilities of the system, ensuring it meets the project’s needs and industry standards.
- Cost-Efficiency: Consider the total cost of ownership, including initial costs, maintenance, and operational expenses.
- Energy Consumption: Assess the energy efficiency of the system, as this can significantly impact operational costs.
- Maintenance Needs: Understand the maintenance requirements and the availability of spare parts and support.
- Scalability: Ensure the system can be scaled or modified to meet future requirements.
- Technology Integration: Evaluate the system’s ability to integrate with existing operations and technology platforms.
- Environmental Impact: Consider the environmental footprint of the system, including emissions, noise, and dust control.
- Warranty and Service Agreements: Review warranty terms and service agreements to ensure comprehensive coverage and support.
- Testimonials and References: Seek testimonials and references from other clients to gauge the manufacturer’s reliability and the system’s performance.
Customization and Scalability
Customization and scalability are critical factors in selecting overland belt conveyor systems. A system tailored to the specific needs of a project can significantly enhance efficiency and productivity. It’s essential to choose a manufacturer that can provide bespoke solutions, adapting the system’s design, capacity, and technology to meet evolving project requirements. Scalability ensures that the system can accommodate future expansions, changes in material handling needs, or technological advancements, providing a long-term solution that grows with your operation.
In summary, choosing the right manufacturer and overland belt conveyor system involves thorough research and consideration of various factors. By prioritizing experience, quality, innovation, and customization, businesses can invest in a conveyor system that delivers optimal performance, safety, and value over its lifespan.
Improve efficiency with our reliable conveyor belt products.
Maintenance and Optimization of Overland Belt Conveyor Systems
Ensuring the longevity and efficiency of overland belt conveyor systems requires a comprehensive approach to maintenance and optimization. Regular, proactive maintenance not only extends the lifespan of the conveyor system but also maintains its efficiency and reliability, minimizing downtime and operational disruptions. Here’s a closer look at the key aspects of maintenance and optimization for these systems:
Regular Maintenance for Longevity and Efficiency
- Scheduled Inspections: Conduct regular inspections of the entire conveyor system, including the belt, pulleys, idlers, and drive units, to identify and address potential issues before they lead to significant problems.
- Belt Maintenance: Monitor the conveyor belt for signs of wear, damage, or misalignment. Promptly repair or replace damaged sections of the belt to prevent further deterioration and potential system failures.
- Lubrication: Ensure that all moving parts, particularly rollers and pulleys, are adequately lubricated to reduce friction and wear, enhancing the system’s longevity.
- Cleaning: Regularly clean the conveyor system to prevent the buildup of debris and materials that can interfere with its operation and lead to premature wear.
- Tension Adjustment: Maintain the correct tension on the conveyor belt to ensure optimal performance and prevent slippage or excessive wear.
- Component Replacement: Replace worn or damaged components, such as idlers and pulleys, as part of routine maintenance to maintain the system’s integrity and functionality.
Design Optimization for Improved Performance
- System Assessment: Conduct a thorough assessment of the conveyor system’s performance, identifying areas where improvements can be made to enhance efficiency and reduce operational costs.
- Energy Efficiency: Evaluate the energy consumption of the conveyor system and implement measures to reduce energy usage, such as optimizing belt speed, upgrading to energy-efficient motors, and minimizing resistance and friction.
- Capacity Enhancement: Consider modifications to increase the system’s capacity, such as upgrading the belt, enhancing the drive system, or optimizing the loading and discharge points, to accommodate increased material handling requirements.
- Technological Upgrades: Incorporate advanced technologies, such as automated monitoring and control systems, to improve the precision and reliability of the conveyor system, enabling real-time adjustments and predictive maintenance.
- Safety Enhancements: Implement additional safety features and protocols to protect workers and the environment, including emergency stop systems, guarding, and dust control measures.
- Training and Education: Provide ongoing training and education for personnel involved in the operation and maintenance of overland belt conveyor systems to ensure they are equipped with the knowledge and skills required to maintain and optimize the system effectively.
By prioritizing regular maintenance and continually seeking opportunities for design optimization, operators of overland belt conveyor systems can achieve improved performance, reduced operational costs, and enhanced safety, ensuring these systems continue to provide reliable and efficient material transport solutions for years to come.
FAQs about Overland Belt Conveyor Systems
Conveyors are essential components in various industries for material handling, and they come in numerous types to suit different applications. However, three of the most prevalent types include roller conveyors, belt conveyors, and modular belt conveyors.
Roller Conveyors: These systems consist of rollers mounted in a frame, where objects can glide along the rollers. They are ideal for moving items with a rigid bottom surface. Roller conveyors can be powered, where the rollers are driven by belts or chains, or non-powered, where items are moved manually or by gravity.
Belt Conveyors: Belt conveyors feature a continuous loop of a flexible material, typically a reinforced belt, driven by pulleys. They are one of the most versatile conveyor types, capable of transporting a wide range of materials, from small components to large volumes of bulk material. Belt conveyors can be designed to handle various loads and can operate over long distances.
Modular Belt Conveyors: These conveyors use a belt made up of individual, interlocked pieces, often made of hard plastic. Modular belt conveyors are highly flexible and can navigate curves and inclines, making them suitable for complex conveyor layouts. They are particularly useful in food processing industries due to their ease of cleaning and maintenance.
Each type of conveyor offers unique advantages and is selected based on the specific requirements of the application, including the nature of the materials to be transported, the required speed and efficiency, and the layout of the transportation route.
The most common conveyor belt system is the flat belt conveyor. Flat belt conveyors are widely used across various industries due to their simplicity, efficiency, and versatility. They consist of a flat belt made from materials like rubber, fabric, or plastic, stretched over two or more pulleys. One of the pulleys is typically powered, moving the belt and the material on it with ease.
Flat belt conveyors can transport a wide range of materials, from small, delicate parts to large, bulky items. They can be designed to operate in straight lines, inclines, declines, or even around corners with the addition of curved sections. The simplicity of their design makes them easy to install, operate, and maintain, contributing to their popularity.
Their versatility extends to the customization options available, including adjustable speeds, belt materials tailored to specific applications, and the inclusion of features like guides, cleats, or sidewalls to accommodate various material handling needs. This adaptability makes flat belt conveyors a go-to solution for industries such as manufacturing, packaging, food processing, and logistics.
Horizontal and vertical curves are incorporated into overland belt conveyor designs to navigate the natural topography of the terrain and optimize the conveyor path for efficiency and cost-effectiveness. These curves allow the conveyor to follow the most practical route, avoiding obstacles and minimizing the need for extensive ground preparation or construction work.
Horizontal Curves: These curves enable the conveyor to change direction horizontally, allowing it to skirt around hills, bodies of water, buildings, or other obstacles in its path. By using horizontal curves, the conveyor can maintain a more direct and shorter route, reducing the overall length of the system and, consequently, the initial installation and long-term operational costs.
Vertical Curves: Vertical curves allow the conveyor to navigate changes in elevation, either ascending or descending hills or valleys. This capability is particularly important in mining operations where the conveyor needs to transport materials from deep pits or across varied terrains. Vertical curves help maintain a continuous and efficient flow of materials, eliminating the need for additional material handling equipment or complex loading and unloading stations at different elevations.
Incorporating horizontal and vertical curves into overland belt conveyor systems requires careful engineering to ensure the belt maintains proper tension and alignment, and the materials are securely conveyed without spillage. The use of curves enhances the flexibility and adaptability of overland conveyors, making them an effective solution for complex material transportation challenges.
A conveyor belt system is a mechanical device that transports materials or goods from one location to another using a continuous belt that moves over a series of rollers or a flat surface. The system typically consists of a belt, pulleys (or drums), rollers, and a drive mechanism that powers the belt’s movement.
The conveyor belt serves as the carrying medium, and its movement can be powered by an electric motor or can be gravity-driven in inclined installations. The materials or items to be transported are placed on the belt, which then moves them to their desired destination. Conveyor belt systems are highly versatile and can be customized with various features such as speed controls, direction changes, and inclines or declines to suit specific applications.
Conveyor belt systems are widely used across numerous industries, including manufacturing, packaging, mining, agriculture, and logistics, due to their efficiency in handling a wide range of materials, from small parts to large bulk items. They are favored for their ability to improve productivity, reduce labor costs, and enhance safety by minimizing manual handling of materials.
Last Updated on August 13, 2024 by Jordan Smith
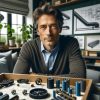
Jordan Smith, a seasoned professional with over 20 years of experience in the conveyor system industry. Jordan’s expertise lies in providing comprehensive solutions for conveyor rollers, belts, and accessories, catering to a wide range of industrial needs. From initial design and configuration to installation and meticulous troubleshooting, Jordan is adept at handling all aspects of conveyor system management. Whether you’re looking to upgrade your production line with efficient conveyor belts, require custom conveyor rollers for specific operations, or need expert advice on selecting the right conveyor accessories for your facility, Jordan is your reliable consultant. For any inquiries or assistance with conveyor system optimization, Jordan is available to share his wealth of knowledge and experience. Feel free to reach out at any time for professional guidance on all matters related to conveyor rollers, belts, and accessories.