Neoprene Idler Rollers: Enhancing Conveyor System Performance
Idler rollers are fundamental components of conveyor systems, serving as the backbone that supports and guides the conveyor belt and the materials it carries. These rollers are pivotal in ensuring the efficient and smooth operation of the conveyor, minimizing downtime and maintenance needs. Among the various materials used to manufacture idler rollers, neoprene stands out for its resilience and versatility. Neoprene idler rollers, made from a synthetic rubber developed by DuPont, offer a unique blend of properties that make them ideal for a wide range of industrial applications. Their durability, resistance to environmental factors, and ability to absorb vibrations contribute significantly to the longevity and reliability of conveyor systems. As such, neoprene idler rollers are not just components; they are critical investments in the productivity and operational efficiency of material handling operations.
What Are Neoprene Idler Rollers?
Neoprene idler rollers are essential components in conveyor systems, designed to support and guide the conveyor belt and the materials being transported. These rollers are crafted from neoprene, a synthetic rubber known for its robustness and adaptability across various industrial environments. The unique properties of neoprene make these rollers highly desirable for applications requiring durability, resistance to chemicals, and the ability to withstand a wide range of temperatures.
Definition and Characteristics of Neoprene Idler Rollers
Neoprene idler rollers are defined by their construction material—neoprene rubber. This material offers several key characteristics that set it apart from other types of rollers:
- Durability: Neoprene’s synthetic composition provides exceptional wear and tear resistance, making these rollers long-lasting.
- Chemical Resistance: They can withstand exposure to oils, solvents, and other chemicals, which is crucial in many industrial settings.
- Temperature Resistance: Neoprene idler rollers perform well in both high and low temperatures, maintaining their integrity and functionality.
- Vibration Dampening: The elasticity of neoprene helps absorb vibrations, protecting the conveyor system and the materials being transported.
- Flexibility: Unlike harder materials, neoprene can flex under load, reducing the risk of damage to the belt or the roller itself.
Comparison with Other Materials
When comparing neoprene idler rollers to those made from materials like ceramic or nylon, several differences become apparent. The table below highlights these differences across various parameters:
Property | Neoprene Rollers | Ceramic Rollers | Nylon Rollers |
---|---|---|---|
Durability | High | Very High | Moderate |
Chemical Resistance | High | Moderate | Low |
Temperature Resistance | Good | Excellent | Good |
Vibration Dampening | Excellent | Poor | Moderate |
Flexibility | High | None | High |
From this comparison, it’s clear that neoprene idler rollers offer a balanced set of properties, making them suitable for a wide range of applications. While ceramic rollers may excel in environments requiring extreme durability and temperature resistance, they lack the flexibility and vibration dampening capabilities of neoprene. Nylon rollers, on the other hand, offer good flexibility and temperature resistance but fall short in terms of durability and chemical resistance. This makes neoprene idler rollers a versatile choice for many industrial conveyor systems, providing a reliable balance between performance and longevity.
Advantages of Neoprene Idler Rollers
Neoprene idler rollers, crafted from the synthetic rubber neoprene, offer a suite of advantages that make them a preferred choice in many conveyor system applications. Their unique material properties provide benefits that are crucial for the efficient and reliable operation of conveyor systems across various industries.
Durability and Resistance to Wear and Tear
One of the primary advantages of neoprene idler rollers is their exceptional durability. Neoprene’s synthetic nature gives it a resilience that is superior to many natural rubbers, allowing these rollers to withstand significant wear and tear over time. This durability is evident in several key areas:
- Long Service Life: Neoprene rollers typically last longer than those made from less durable materials, reducing the need for frequent replacements.
- High Load Bearing Capacity: They can support heavy loads without deforming, ensuring consistent operation and minimal downtime.
- Resistance to Abrasion: Neoprene’s tough surface resists cuts and abrasions, which is essential in environments with rough or sharp materials.
- Weather Resistance: Neoprene idler rollers maintain their integrity in various weather conditions, including exposure to UV light, rain, and extreme temperatures.
- Flexibility: Despite their toughness, neoprene rollers retain enough flexibility to absorb impacts without cracking or breaking.
Chemical, Oil, and Ozone Resistance
Although neoprene idler rollers may not offer the highest level of chemical resistance when compared to some modern compounds, their ability to resist a broad range of chemicals, oils, and ozone is noteworthy. This resistance is crucial in environments where exposure to such elements is common, providing several advantages:
- Protection Against Chemicals: Neoprene rollers can withstand exposure to mild acids, alkalis, and other industrial chemicals without deteriorating.
- Oil and Grease Resistance: They are less likely to degrade in the presence of oils and greases, maintaining their performance in machinery and automotive applications.
- Ozone and Weathering Resistance: Neoprene’s stability in the presence of ozone prevents cracking and aging, extending the life of the rollers.
- Versatility in Processing Environments: Suitable for use in chemical processing plants, refineries, and other settings where chemical exposure is a concern.
- Maintenance of Physical Properties: Despite exposure to harsh elements, neoprene rollers maintain their physical properties, ensuring consistent performance.
Versatility Across Various Industrial Applications
The versatility of neoprene idler rollers is a significant advantage, allowing them to be used in a wide range of industrial applications. This versatility is demonstrated in their suitability for various environments and operational requirements:
- Material Handling and Logistics: Ideal for conveyor systems in warehouses, distribution centers, and logistics companies, where durability and reliability are paramount.
- Manufacturing and Production Lines: Neoprene rollers can be used in the manufacturing of food and beverages, pharmaceuticals, and electronics, where they may come into contact with chemicals and oils.
- Mining and Heavy Industry: Their durability and resistance to wear make them suitable for the harsh conditions of mining and quarrying operations.
- Agriculture and Farming Equipment: Neoprene rollers are used in agricultural machinery, where they are exposed to outdoor conditions and various chemicals.
- Automotive and Aerospace: In the production and maintenance of vehicles and aircraft, where oil resistance and the ability to withstand a range of temperatures are crucial.
The advantages of neoprene idler rollers—combining durability, chemical resistance, and versatility—make them an excellent choice for a wide array of industrial applications, ensuring efficient and reliable operation of conveyor systems.
Key Features of Neoprene Idler Rollers
Neoprene idler rollers are distinguished by their unique features, which stem from the inherent properties of neoprene. These features contribute to the rollers’ effectiveness and reliability in various applications, making them a preferred choice for many industries.
Neoprene Roller Wheels: Design and Benefits
Neoprene roller wheels are designed with a focus on durability, flexibility, and resistance to environmental factors. The benefits of these design choices include:
- Enhanced Durability: The robust nature of neoprene extends the life of the roller wheels, reducing the need for frequent replacements.
- Improved Traction: The surface texture of neoprene provides better grip and traction, ensuring smooth operation.
- Vibration Dampening: Neoprene’s elasticity helps absorb vibrations, protecting the conveyor system and the materials being transported.
- Chemical Resistance: These wheels can withstand exposure to various chemicals, making them suitable for use in chemical processing environments.
- Weather Resistance: Neoprene’s ability to resist degradation from UV light, ozone, and extreme temperatures makes these wheels ideal for outdoor or variable temperature applications.
Neoprene Drive Roller: Functionality and Advantages
Neoprene drive rollers are critical components in conveying systems, offering specific functionalities and advantages:
- Efficient Power Transmission: The material properties of neoprene ensure efficient transfer of power from the drive system to the conveyor belt.
- Reduced Slippage: The inherent grip of neoprene minimizes slippage between the roller and the belt, enhancing operational efficiency.
- Load Distribution: Neoprene drive rollers evenly distribute the load across the belt, preventing wear and extending the system’s lifespan.
- Operational Quietness: The sound-dampening qualities of neoprene contribute to quieter operation, a significant advantage in noise-sensitive environments.
- Maintenance Ease: The resilience and durability of neoprene drive rollers result in lower maintenance requirements and costs.
Rubber Drive Rollers vs. Neoprene Rollers: A Comparative Analysis
Feature | Rubber Drive Rollers | Neoprene Rollers |
---|---|---|
Durability | Moderate | High |
Chemical Resistance | Low to Moderate | High |
Temperature Resistance | Moderate | High |
Vibration Dampening | Moderate | High |
Cost | Variable | Generally Higher |
Neoprene rollers offer superior durability, chemical and temperature resistance, and vibration dampening compared to standard rubber drive rollers, albeit at a potentially higher cost. This makes them a more suitable option for demanding industrial environments.
Fairlane Durasoft Rollers: Introduction and Comparison
Fairlane Durasoft rollers are known for their soft, durable urethane coating, which provides excellent traction and noise reduction. When compared to neoprene idler rollers, several differences emerge:
Feature | Fairlane Durasoft Rollers | Neoprene Rollers |
---|---|---|
Material Softness | High | Moderate |
Durability | High | High |
Chemical Resistance | Moderate | High |
Temperature Resistance | Moderate | High |
Cost | Generally Higher | Variable |
While Fairlane Durasoft rollers offer high durability and material softness, making them ideal for applications requiring gentle handling and noise reduction, neoprene rollers provide better chemical and temperature resistance. The choice between the two depends on the specific requirements of the application, including environmental conditions and budget constraints.
Applications of Neoprene Idler Rollers
Neoprene idler rollers find their applications in a broad spectrum of industrial settings, leveraging their unique properties to enhance the efficiency and reliability of conveyor systems and material handling processes. Their versatility makes them suitable for various industries, including manufacturing, packaging, and distribution, among others.
Industrial Applications
The industrial applications of neoprene idler rollers span across several sectors, where their durability, resistance to environmental factors, and ability to absorb vibrations are particularly valued. These applications include:
- Conveyor Systems: Neoprene idler rollers are extensively used in conveyor systems across different industries to support and guide conveyor belts, ensuring smooth and efficient material transport.
- Material Handling: In warehouses and distribution centers, these rollers facilitate the handling of goods by providing a stable and reliable means of moving items from one point to another.
- Bulk Material Processing: Industries involved in the processing of bulk materials, such as mining, agriculture, and recycling, utilize neoprene idler rollers for their ability to withstand heavy loads and abrasive materials.
- Food and Beverage Production: The chemical resistance of neoprene makes these rollers suitable for food and beverage production lines, where they may come into contact with various substances.
- Pharmaceutical Manufacturing: In pharmaceutical manufacturing, the cleanliness and resistance to chemicals of neoprene idler rollers make them ideal for use in environments where hygiene and contamination control are paramount.
Specific Use Cases in Industries
Within these broad industrial applications, neoprene idler rollers serve specific use cases that highlight their adaptability and effectiveness:
- Manufacturing: In automotive manufacturing, neoprene idler rollers are used on assembly lines to move parts and assemblies through different stages of production, benefiting from the rollers’ durability and resistance to oils and chemicals.
- Packaging: Packaging facilities rely on neoprene idler rollers for their conveyor systems, which handle various packaging materials and finished products, taking advantage of the rollers’ smooth operation and flexibility.
- Distribution: Distribution centers use conveyor systems equipped with neoprene idler rollers to sort, move, and organize products for shipping, valuing the rollers’ efficiency and reliability.
- Textile Industry: In textile manufacturing, neoprene idler rollers are used to transport fabrics and materials through dyeing, washing, and finishing processes, where their resistance to chemicals and water is crucial.
- Printing and Publishing: The printing and publishing industry uses neoprene idler rollers in their printing presses and finishing lines, where the rollers’ precision and resistance to deformation ensure high-quality print results.
In each of these use cases, neoprene idler rollers contribute significantly to the operational efficiency, safety, and productivity of the processes they are involved in. Their wide range of applications underscores the versatility and reliability of neoprene as a material for industrial rollers.
Types of Neoprene Rollers
Neoprene idler rollers are a critical component in the design and operation of efficient conveyor systems. Their versatility and durability make them suitable for a wide range of industrial applications. There are several types of neoprene idler rollers, each designed to meet specific operational needs and environmental conditions. These variations enhance the functionality and efficiency of conveyor systems, providing solutions for different industrial challenges.
Plain Neoprene Idler Rollers
Plain neoprene idler rollers are the most fundamental type, primarily used to support and shape the conveyor belt. Their smooth surface ensures that the conveyor belt moves in a consistent and controlled manner, reducing wear and extending the belt’s lifespan. These rollers are particularly valued for their:
- Uniform Surface Contact: Ensuring even distribution of weight and reducing stress points on the conveyor belt.
- Flexibility: Adapting to minor variations in the belt’s path without causing damage or misalignment.
- Durability: Resisting wear from continuous operation and environmental factors like moisture and temperature fluctuations.
Rubber-Coated Neoprene Rollers
Rubber-coated neoprene rollers offer enhanced durability and resistance, making them suitable for more demanding environments. The rubber coating provides an additional layer of protection against abrasion, chemicals, and other potentially damaging substances. Key benefits include:
- Increased Lifespan: The rubber coating extends the roller’s service life by protecting the core from direct exposure to harmful elements.
- Improved Grip: Enhancing the traction between the roller and the conveyor belt, which is crucial for maintaining accurate belt movement.
- Noise Reduction: Absorbing operational sounds and vibrations, contributing to a quieter working environment.
Rubber Disc Neoprene Rollers
Rubber disc neoprene rollers are designed with spaced rubber discs along the roller’s length, providing support while also facilitating the separation of carryback (material that sticks to the belt). These rollers are especially useful in applications where cleanliness and material separation are priorities. Their advantages include:
- Effective Cleaning: The gaps between discs help in dislodging and removing debris from the belt.
- Edge Support: Concentrated at the ends of the roller, the discs provide additional support to the belt edges, preventing sagging and misalignment.
- Versatility: Suitable for various materials, including those that are sticky or prone to clumping.
Customizable Options for Specific Industrial Needs
Neoprene idler rollers can be customized to meet the unique requirements of different industries and applications. Customization options may include:
- Diameter and Length: Tailored to fit the specific dimensions of the conveyor system.
- Bearing Types: Selected based on load requirements and operational speeds.
- Surface Texture: Modified to enhance grip or facilitate cleaning, depending on the application.
- Environmental Resistance: Adjustments in the neoprene compound to enhance resistance to chemicals, temperatures, or UV exposure.
These customizable features ensure that neoprene idler rollers can be precisely engineered to address the challenges of any industrial environment, enhancing the efficiency and reliability of conveyor systems across a broad spectrum of applications.
Choosing the Right Neoprene Idler Roller
Selecting the appropriate neoprene idler rollers for your conveyor system is crucial to ensuring optimal performance, longevity, and efficiency. Various factors must be considered to make an informed decision that meets the specific needs of your application. Understanding these factors will help you choose rollers that not only fit your system but also enhance its operation.
Factors to Consider
When selecting neoprene idler rollers, several key factors come into play. Each of these factors can significantly impact the performance and suitability of the roller for your conveyor system:
- Bearing Brand: The brand of bearings used in the rollers can affect their reliability and durability. For example, well-known brands like SKF, Timken, NSK, NTN, and FAG are recognized for their quality and can offer greater assurance of performance and longevity.
- Size: The size of the roller must be compatible with the conveyor belt’s width and the load it carries. Common sizes include diameters of 4 inches for light-duty applications and up to 7 inches or more for heavy-duty applications.
- Diameter: The diameter of the roller impacts the belt’s speed and the system’s overall capacity. Larger diameters are typically used for higher load capacities and longer conveyor lengths. Diameters can range from small (less than 2 inches) for tight spaces and light loads, to large (6 inches or more) for heavy-duty applications.
- Wall Thickness: The thickness of the roller’s wall can influence its strength and ability to withstand heavy loads. Thicker walls provide more durability but may increase the weight and cost of the roller. Common wall thicknesses range from 0.065 inches for light applications to 0.25 inches or more for heavy-duty use.
- Seal Type: The type of seal used in the roller bearings can affect maintenance requirements and protection against contaminants. Options include non-contact seals for low-friction applications, contact seals for high contamination environments, and labyrinth seals for the best balance of protection and low friction.
Customization Options
To meet the specific standards and requirements of different conveyor applications, neoprene idler rollers offer various customization options:
- Material Composition: Adjustments to the neoprene compound can enhance resistance to chemicals, abrasion, or temperature extremes.
- Surface Treatment: Options like grooving, lagging, or coating with other materials can improve traction, reduce wear, and facilitate material handling.
- Bearing Configuration: Custom bearings can be designed for specific load capacities, speeds, or environmental conditions.
- Shaft Configurations: Shafts can be customized in length, diameter, and material to fit the conveyor framework and load requirements precisely.
- Specialty Seals: For environments with extreme dust, moisture, or chemical exposure, specialty seals can be incorporated to protect the roller bearings and extend their service life.
Choosing the right neoprene idler rollers involves a careful consideration of these factors and customization options. By selecting rollers that are tailored to your specific operational needs, you can ensure the longevity, efficiency, and reliability of your conveyor system.
Neoprene Idler Rollers Price and Availability
The price and availability of neoprene idler rollers can vary widely based on several factors. Understanding these factors can help you budget for and source the right rollers for your conveyor system needs.
Overview of Pricing Factors
Several key factors influence the price of neoprene idler rollers. Being aware of these can help you navigate your options more effectively:
- Size and Diameter: Larger rollers typically cost more due to the increased amount of material and manufacturing effort required. For instance, rollers designed for heavy-duty applications will be priced higher than those for light-duty tasks.
- Customization: Custom features such as specific bearing types, seal options, or specialized surface treatments can add to the cost. Customized rollers designed to meet unique operational requirements or environmental conditions are often more expensive.
- Quantity: Ordering in bulk can significantly affect the price per unit. Suppliers often offer discounts for large orders, making it cost-effective for large-scale operations or for stocking up on replacements.
- Material Quality: The quality of neoprene and other materials used in the roller construction can impact the price. High-grade materials that offer superior durability and performance features come at a premium.
- Brand and Manufacturer: The reputation and location of the manufacturer can influence the cost. Renowned brands known for their quality and reliability might charge more, but they often provide better warranties and customer support.
Tips on Where to Find and How to Select Neoprene Idler Rollers
Finding and selecting the right neoprene idler rollers for your needs involves considering several sources and criteria:
- Industry Suppliers and Distributors: Start by researching suppliers and distributors specializing in conveyor components. Companies like McMaster-Carr, Grainger, and Applied Industrial Technologies are known for their wide selection and reliable service.
- Manufacturer Direct Purchases: Contacting the manufacturer directly can provide access to the latest products and customization options. This route often allows for negotiating prices, especially for bulk orders.
- Online Marketplaces: Platforms like Alibaba and Amazon Business cater to industrial purchases, offering a range of options from various sellers. These marketplaces can be useful for comparing prices and availability.
- Trade Shows and Expos: Industry-specific trade shows and expos are excellent places to explore new products, meet suppliers, and negotiate deals. They offer the opportunity to see the rollers firsthand and discuss specific needs with experts.
- Referrals and Reviews: Seek recommendations from industry peers and online forums. User reviews and testimonials can provide insights into the reliability and performance of different neoprene idler rollers.
When selecting neoprene idler rollers, consider not only the price but also the quality, warranty, and support offered by the supplier or manufacturer. Ensure the rollers meet your specific requirements for load capacity, environmental resistance, and operational speed to achieve the best value and performance from your investment.
Maintenance and Care for Neoprene Idler Rollers
Proper maintenance and care are crucial for maximizing the lifespan and efficiency of neoprene idler rollers in conveyor systems. By adhering to best practices for maintenance, you can ensure these components continue to perform optimally, reducing downtime and maintenance costs.
Best Practices for Extending the Life of Neoprene Idler Rollers
- Regular Inspection: Schedule regular inspections of neoprene idler rollers to check for wear, damage, or misalignment. Early detection of issues can prevent more significant problems down the line.
- Cleanliness: Keep the rollers and the conveyor belt clean. Accumulation of debris can cause premature wear and tear on the rollers. Use appropriate cleaning agents that will not degrade the neoprene material.
- Lubrication: Ensure that the bearings in the rollers are properly lubricated according to the manufacturer’s recommendations. Adequate lubrication reduces friction, heat, and wear, extending the life of the rollers.
- Alignment Checks: Regularly check and adjust the alignment of the conveyor belt and rollers. Misalignment can cause uneven wear and tear on the rollers and the belt, leading to premature failure.
- Load Distribution: Ensure that the load on the conveyor belt is evenly distributed. Uneven loads can put excessive stress on individual rollers, leading to faster degradation.
Common Maintenance Challenges and Solutions
Maintaining neoprene idler rollers involves overcoming several common challenges. Here are some typical issues and their solutions:
- Buildup of Materials: Materials sticking to the rollers can cause imbalance and wear. Solution: Implement a regular cleaning schedule and consider using scrapers or other cleaning devices designed for conveyor systems.
- Environmental Damage: Exposure to harsh chemicals or extreme temperatures can degrade neoprene. Solution: Use neoprene idler rollers with a protective coating or choose rollers made from materials better suited to the specific environmental conditions.
- Bearing Failure: Bearings are critical to roller function and can fail due to lack of lubrication or contamination. Solution: Use sealed or shielded bearings where appropriate and maintain a regular lubrication schedule.
- Misalignment: Misaligned rollers can cause the conveyor belt to track incorrectly, leading to wear and potential damage. Solution: Regularly inspect the alignment of rollers and adjust as necessary to ensure proper belt tracking.
- Wear and Tear: Over time, rollers will naturally wear down, potentially affecting the conveyor’s operation. Solution: Schedule regular inspections to identify worn rollers and replace them before they cause system issues.
By addressing these common challenges with proactive maintenance and care strategies, you can significantly extend the operational life of neoprene idler rollers and maintain the efficiency of your conveyor system.
FAQs About Neoprene Idler Rollers
A neoprene roller is a type of roller made from neoprene, which is a synthetic rubber material known for its versatility and resilience. Developed by DuPont in 1931, neoprene is a trade name for the chloroprene elastomer, valued not for excellence in a single property but for a combination of essential properties. Neoprene rollers are known for their average strength in several desirable categories, making them a historic synthetic rubber used extensively across many industries. Despite only having average tolerance to chemical, oil, and ozone resistance, neoprene rollers are widely utilized in industrial applications ranging from conveyor systems to material handling equipment. They are particularly favored for their durability, flexibility, and resistance to wear and tear, making them suitable for environments where they might be exposed to various elements and mechanical stresses.
Idler rollers, or sometimes simply known as conveyor rollers, are cylindrical bars that run along and underneath a conveyor belt. They play a crucial role in supporting the weight and impact of the materials being transported along the belt. Idler rollers aid in the smooth, continuous movement of these materials and can be self-aligning to assist in maintaining the belt’s tracking. Depending on the structure and shape of the conveyor belt, the rollers are usually positioned within a metal frame and are known as idler sets. They are essential components in the efficient operation of conveyor systems, reducing friction and wear on the belt, and helping to prevent belt misalignment and slippage.
Idler roller conveyors are categorized based on their design and the specific application they serve. The main types include:
Troughing Idlers: These are used in bulk material handling conveyors and consist of a central idler roll with a pair of idlers on either side. The angle of these side idlers helps to keep the material centered on the belt.
Impact Idlers: Positioned at loading points, impact idlers are designed to absorb the shock and impact of heavy materials falling onto the conveyor belt, thereby protecting the belt and the structure from damage.
Return Idlers: These support the return side of the belt as it loops back over to the beginning of the conveyor system. They can be flat or slightly curved to assist in belt tracking.
Self-Aligning Idlers: These are used to correct any misalignment of the conveyor belt, ensuring it runs straight. They can be pivoted or mounted on a swivel base to guide the belt back to its correct path.
Guide Rollers: Installed on the sides of conveyor belts in a vertical position, guide rollers help to ensure the belt stays on track, preventing it from drifting sideways.
The standard size of an idler roller can vary widely depending on the application, the width of the conveyor belt, and the load it is designed to support. However, common diameters for idler rollers range from about 3 inches (76 mm) to 6 inches (152 mm), with lengths tailored to match the width of the conveyor belt they are supporting. The spacing between idler rollers is also a critical factor in design and typically ranges from 1 to 1.5 meters (3 to 5 feet), depending on the type of material being conveyed and the load on the belt. Custom sizes are frequently manufactured to meet specific requirements of a conveyor system, including larger diameters and wider widths for heavy-duty applications.
Last Updated on March 21, 2024 by Jordan Smith
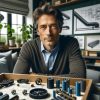
Jordan Smith, a seasoned professional with over 20 years of experience in the conveyor system industry. Jordan’s expertise lies in providing comprehensive solutions for conveyor rollers, belts, and accessories, catering to a wide range of industrial needs. From initial design and configuration to installation and meticulous troubleshooting, Jordan is adept at handling all aspects of conveyor system management. Whether you’re looking to upgrade your production line with efficient conveyor belts, require custom conveyor rollers for specific operations, or need expert advice on selecting the right conveyor accessories for your facility, Jordan is your reliable consultant. For any inquiries or assistance with conveyor system optimization, Jordan is available to share his wealth of knowledge and experience. Feel free to reach out at any time for professional guidance on all matters related to conveyor rollers, belts, and accessories.