Zero-Impact Roller Conveyor: Efficiency in Fragile Handling
In the vast and intricate world of industrial applications, conveyor systems stand as the backbone of efficient material handling and logistics. These systems are pivotal in ensuring the seamless movement of goods across different stages of production, packaging, and distribution, significantly enhancing productivity and operational efficiency. Amidst the variety of conveyor technologies, zero-impact roller conveyor emerges as a groundbreaking solution specifically designed to address the challenges of handling fragile materials. Unlike traditional conveyors that may subject goods to potential damage through impact and pressure, zero-impact roller conveyors are engineered to gently and securely transport sensitive items, ensuring their integrity from start to finish. This innovative approach not only minimizes product loss but also optimizes the overall handling process, making zero-impact roller conveyors an indispensable tool in industries where the safety of delicate items is paramount.
What is a Zero-Impact Roller Conveyor
In the realm of material handling and logistics, the advent of zero-impact roller conveyors marks a pivotal innovation, designed to revolutionize how products, especially those susceptible to damage, are transported within various industrial settings. This sophisticated conveyor system is distinguished by its unique ability to move items with minimal to no contact, thereby eliminating the risk of damage that can occur with traditional conveyor systems. Below, we delve into the intricacies of what makes zero-impact roller conveyors a game-changer in the industry, exploring both their definition and the underlying principles that enable their exceptional performance.
Definition and Explanation of Zero-Impact Roller Conveyors
Before we explore the defining characteristics and operational principles of zero-impact roller conveyors, it’s essential to understand the context and necessity that led to their development. Traditional conveyor systems, while efficient in the movement of goods across distances, often fall short when it comes to handling fragile or sensitive items. The introduction of zero-impact roller conveyors addresses this gap, offering a solution that combines the efficiency of conveyor transport with the delicacy required for vulnerable products.
- Core Concept: At its core, a zero-impact roller conveyor is designed to transport goods without causing any physical stress or damage, making it ideal for industries where product integrity is critical.
- Targeted Application: These conveyors are particularly beneficial in sectors such as pharmaceuticals, electronics, and food processing, where even minor impacts can result in significant product loss.
- Innovative Design: The design of zero-impact roller conveyors incorporates advanced mechanisms and technologies to ensure smooth and gentle handling of items, regardless of their fragility.
- Operational Efficiency: Despite their gentle handling capabilities, these conveyors do not compromise on operational efficiency, offering fast and reliable transport solutions.
- Customization Capability: They are highly customizable, allowing for adjustments in speed, spacing, and routing to meet specific operational requirements.
- Integration with Automation: Zero-impact roller conveyors seamlessly integrate with automated systems, enhancing precision in material handling and reducing manual intervention.
- Safety and Ergonomics: By minimizing the need for manual handling, these conveyors also contribute to a safer and more ergonomic workplace environment.
- Sustainability Focus: The emphasis on reducing product damage translates to less waste, aligning with sustainability goals of reducing, reusing, and recycling.
- Cost-Effectiveness: Over time, the reduction in product damage and improved efficiency can lead to significant cost savings, offsetting the initial investment in the technology.
The Working Principle Behind Zero-Impact Technology
The operational excellence of zero-impact roller conveyors is not just a result of their innovative design but also the sophisticated technology that powers them. Understanding the working principle behind this technology sheds light on how these conveyors manage to achieve what traditional systems cannot.
- Sophisticated Sensing: Utilizing an array of sensors, zero-impact roller conveyors detect the presence, size, and speed of items, enabling precise control over their movement.
- Intelligent Speed Control: The system’s intelligence extends to dynamically adjusting conveyor speed based on real-time feedback, ensuring optimal spacing between items.
- Adaptive Load Management: Regardless of load diversity, the conveyor can adapt its handling strategy to maintain zero impact on the items.
- Gradual Acceleration and Deceleration: Through controlled acceleration and deceleration, items are moved without the risk of collision or damage.
- Independent Zone Operation: The conveyor is segmented into independently controlled zones, allowing for accumulation without contact.
- Real-Time Adjustments: Continuous monitoring and real-time adjustments ensure the system operates at peak efficiency, adapting to changes in the production environment.
- Energy Optimization: Advanced models can redistribute energy from slowing sections to those requiring acceleration, enhancing overall energy efficiency.
- Scalable Configuration: The modular nature of these conveyors allows for easy expansion or modification, providing flexibility as operational needs evolve.
- Proactive Maintenance Insights: Integration with predictive maintenance technologies enables early detection of potential issues, minimizing downtime and extending equipment lifespan.
Through a combination of advanced sensing technology, intelligent control systems, and modular design, zero-impact roller conveyors offer a revolutionary approach to material handling, setting a new standard for efficiency, safety, and product integrity in industrial operations.
Key Features and Benefits of Zero-Impact Roller Conveyor
The introduction of zero-impact roller conveyors into the material handling sector has been a game-changer, especially for industries that handle delicate or high-value products. These conveyors are meticulously engineered to eliminate the physical stress traditionally associated with moving goods, thereby ensuring the integrity of each item transported. Below, we explore the distinctive features that define zero-impact roller conveyors and the extensive benefits they bring to operations, highlighting how they revolutionize product handling processes.
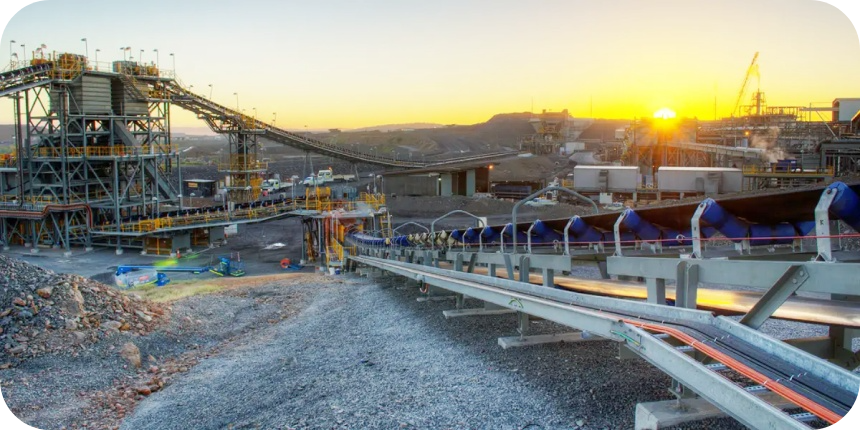
Distinctive Features of Zero-Impact Roller Conveyors
Zero-impact roller conveyors are not just another addition to the conveyor market; they are a sophisticated solution designed with precision and care. Each feature is thoughtfully integrated to address specific challenges in material handling, making these conveyors stand out.
- Precision Control: Central to the design of zero-impact roller conveyors is their precision control capability, allowing for exact handling and placement of items, minimizing the risk of damage.
- Advanced Sensing Technology: These conveyors utilize state-of-the-art sensors to detect items’ proximity, enabling automatic adjustments to maintain safe distances between products.
- Customizable Speed Settings: Flexibility in speed settings ensures that different types of products can be transported at their ideal speeds, enhancing safety and efficiency.
- Modular Design: The modular nature of these conveyors allows for easy expansion or modification, providing businesses with the flexibility to adapt to changing demands.
- Energy-Efficient Operation: Designed with sustainability in mind, zero-impact roller conveyors operate with minimal energy consumption, reducing the environmental footprint of material handling.
- Seamless Integration: These systems are built to integrate effortlessly with existing conveyor setups, enhancing the cohesion and efficiency of material handling operations.
- Automated Load Balancing: The automated load balancing feature ensures even distribution of weight across the conveyor, promoting stability and extending the system’s lifespan.
- Durable Construction: Constructed from high-quality materials, zero-impact roller conveyors are built to last, even under the demands of continuous industrial use.
Comprehensive Benefits of Zero-Impact Roller Conveyors
The adoption of zero-impact roller conveyors brings a multitude of benefits to operations, addressing both immediate and long-term needs for efficient and safe material handling.
- Reduced Product Damage: The primary advantage of these conveyors is their ability to significantly reduce product damage, ensuring that items are delivered in their intended condition.
- Increased Operational Efficiency: By minimizing disruptions due to damaged goods, these conveyors streamline operations, leading to higher overall efficiency.
- Lower Operational Costs: The decrease in product loss and damage directly translates to reduced operational costs and less waste.
- Improved Product Safety: Zero-impact roller conveyors offer a safer transit solution for sensitive and fragile products, protecting them throughout their journey.
- Enhanced Workplace Safety: Automation and precise control reduce manual handling requirements, contributing to a safer work environment.
- Greater Throughput: The efficiency and reliability of these conveyors allow for increased throughput, enabling businesses to handle larger volumes of goods.
- Flexibility and Scalability: The modular design provides the flexibility to scale operations, accommodating growth or changes in production demands.
- Sustainability: By optimizing energy use and reducing waste, zero-impact roller conveyors support more sustainable operational practices.
- Long-Term Reliability: The durability and advanced engineering of these conveyors ensure they remain reliable over the long term, offering consistent performance with minimal maintenance.
Zero-impact roller conveyors represent a significant advancement in conveyor technology, offering a blend of innovative features and substantial benefits. These conveyors not only enhance the safety and integrity of transported goods but also contribute to more efficient, sustainable, and cost-effective operations.
Design and Components of Zero-Impact Roller Conveyor
The zero-impact roller conveyor system stands as a hallmark of innovation in the domain of material handling, meticulously engineered to transport goods with the utmost precision and care. This system is a product of advanced engineering, designed to eliminate the physical stresses traditionally associated with conveyor transport, thereby safeguarding the integrity of sensitive and fragile items. Let’s explore the intricate design and the critical components that constitute the zero-impact roller conveyor, each playing a pivotal role in its operation and efficiency.
Sophisticated Design Aspects
At the core of the zero-impact roller conveyor’s design philosophy is the commitment to minimizing the impact on goods during their transport. This objective is achieved through a harmonious blend of advanced engineering principles, innovative materials, and intelligent system integration. The design intricacies of the zero-impact roller conveyor include:
- Precision Engineering: Every aspect of the conveyor, from the rollers to the frame, is engineered for precision, ensuring that goods are transported smoothly and without unnecessary jostling or pressure.
- Material Selection: The choice of materials for both the rollers and the frame is critical. Materials are selected for their durability, friction properties, and ability to absorb vibrations, contributing to the gentle handling of goods.
- Intelligent Control Systems: Integral to the conveyor’s design is an intelligent control system capable of making real-time adjustments based on sensor input, ensuring optimal spacing and speed of goods in transit.
- Ergonomic Considerations: The design also prioritizes operator interaction, ensuring that the system is accessible, safe, and easy to operate, thereby reducing the risk of human error and enhancing safety.
- Modularity and Scalability: A modular design approach allows for easy expansion or reconfiguration of the conveyor system, providing businesses with the flexibility to adapt to changing operational needs.
- Energy Efficiency: Emphasis on energy efficiency is evident in the design of the drive system, which uses advanced motors and control algorithms to minimize power consumption while maintaining performance.
Key Components and Their Functions
Delving deeper into the zero-impact roller conveyor, we find that its exceptional performance is attributed to the synergy of its components:
- Rollers: The rollers are the primary contact point with goods, designed to ensure smooth and stable movement. Special coatings or materials may be used to reduce friction and absorb impact.
- Frame: Serving as the backbone of the conveyor, the frame is robustly constructed to support the weight of the goods and the dynamic forces exerted during operation.
- Drive System: This system powers the movement of the rollers. In zero-impact roller conveyors, it is finely tuned to control the speed and force exerted, ensuring that goods are moved gently.
- Impact Zones: These zones are critical for mitigating the forces goods experience at loading and unloading points. Enhanced cushioning and specialized rollers are employed to absorb and dissipate energy.
Zero-Impact Roller Conveyor Diagram
To visualize the zero-impact roller conveyor’s design and components, consider a diagram that highlights the following points:
- Sensor Integration: Strategically placed sensors along the conveyor detect goods, allowing for adjustments in real-time to maintain optimal conditions.
- Control Panel: Acts as the brain of the operation, processing sensor data to coordinate the conveyor’s movements and settings.
- Variable Speed Rollers: These rollers adapt their speed for the gentle acceleration and deceleration of goods, crucial for reducing impact.
- Cushioned Surfaces: Selected rollers feature cushioned surfaces to further minimize the risk of damage to fragile items.
- Modular Design: The conveyor’s modular sections can operate independently, offering flexibility and efficiency in handling diverse goods.
- Energy-Efficient Motors: These motors power the conveyor, emphasizing the system’s overall energy efficiency and sustainability.
- Automated Load Balancing: This feature ensures goods are evenly distributed, preventing overloading and enhancing stability.
- High-Durability Materials: Components are crafted from materials chosen for their longevity and performance in industrial settings.
- Integrated Safety Features: Emergency stops and barriers are incorporated to ensure the safety of both the goods and the operators.
Through its sophisticated design and integration of advanced components, the zero-impact roller conveyor system redefines the standards for material handling, ensuring that goods are transported safely, efficiently, and without damage.
Types of Rollers in Conveyor Belts
The conveyor belt ecosystem is diverse, with a variety of rollers designed to meet specific operational needs. From handling delicate items with the utmost care to ensuring efficient transport of heavy goods, the choice of roller can significantly impact the conveyor’s performance. Among these, the zero-impact roller conveyor emerges as a standout innovation, designed to eliminate damage to sensitive materials during transport. Let’s explore the various rollers that play critical roles in conveyor belt systems, emphasizing the unique advantages of zero-impact rollers.
Different Types of Rollers Used in Conveyor Belts
Rollers are the backbone of any conveyor system, providing the necessary support and movement to transport goods across facilities. Each type of roller has been developed with specific tasks and environments in mind, from heavy-duty applications to the gentle handling of fragile items.
- Zero-Impact Rollers: Engineered for precision and care, zero-impact rollers ensure that materials are transported without any damage, making them ideal for industries where product integrity is crucial.
- Gravity Rollers: Utilizing the force of gravity, these rollers offer a simple and cost-effective solution for moving goods, particularly effective in downward or inclined pathways.
- Live (Powered) Rollers: Equipped with motors, these rollers provide the force needed for moving heavier loads and offer control over speed and direction, enhancing the conveyor’s versatility.
- Grooved Rollers: Featuring grooves that accommodate drive belts, grooved rollers play a pivotal role in the propulsion of the conveyor belt, ensuring smooth and consistent movement.
- Tapered Rollers: Essential for the smooth navigation of curves and corners, tapered rollers keep materials aligned and prevent them from straying off the conveyor.
- Impact Rollers: Positioned at loading zones, impact rollers absorb the shock of dropping materials, protecting both the conveyor belt and the goods from damage.
- Plastic Rollers: Offering a lightweight and corrosion-resistant option, plastic rollers are suited for environments where moisture or chemical exposure is a concern.
- Stainless Steel Rollers: Renowned for their strength and hygiene, stainless steel rollers are favored in industries requiring cleanliness and durability, such as food processing and pharmaceuticals.
Comparison with Traditional Rollers
When evaluating the performance and suitability of zero-impact rollers in comparison to traditional rollers, several factors come into play. Each type of roller offers distinct advantages, but the choice ultimately depends on the specific requirements of the material handling process.
Feature | Zero-Impact Rollers | Traditional Rollers |
---|---|---|
Impact on Materials | Virtually eliminates damage, safeguarding fragile items. | Potential for damage depending on material and application. |
Application | Best suited for delicate, high-value materials requiring gentle handling. | Wide-ranging, with specific types optimized for various tasks. |
Cost | Higher, reflecting advanced technology and materials. | More variable, with cost-effective options like gravity rollers available. |
Maintenance | May involve sophisticated maintenance due to complex designs. | Generally simpler, though dependent on the type and usage. |
Noise Level | Designed for quiet operation, minimizing workplace noise. | Noise levels vary, with some types generating significant sound. |
Durability | High durability, designed to minimize wear and extend lifespan. | Varies, with some materials and designs offering greater longevity. |
Load Capacity | Engineered to handle specified loads without causing damage. | Load capacity varies widely across different roller types. |
Suitability for Fragile Goods | Specifically designed for fragile goods, ensuring safe transport. | Not all types are suitable for fragile goods without risk of damage. |
This comparison underscores the specialized nature of zero-impact rollers, designed to meet the needs of operations where the safety and integrity of transported items are paramount. By carefully selecting the appropriate type of roller, businesses can optimize their conveyor systems for efficiency, safety, and the preservation of product quality.
Applications of Zero-Impact Roller Conveyor
The advent of the zero-impact roller conveyor has introduced a paradigm shift in how industries approach the transportation and handling of goods. This innovative system, designed to transport items with minimal to no impact, is particularly beneficial in sectors where the integrity of the product is paramount. Below, we explore the diverse industrial applications of zero-impact roller conveyors, highlighting their versatility and the value they bring to various fields.
Industrial Applications Where Zero-Impact Roller Conveyors Are Beneficial
Zero-impact roller conveyors have found their place in a wide array of industries, thanks to their unique ability to preserve the quality and integrity of products during transport. Their application spans sectors that deal with everything from fragile goods to high-speed production lines, demonstrating their adaptability and effectiveness.
- Pharmaceuticals: In an industry where the contamination and damage of products can have serious implications, zero-impact roller conveyors ensure the safe handling of medications, vaccines, and other sensitive items.
- Electronics Manufacturing: The precision and delicacy required in handling electronic components make zero-impact roller conveyor an ideal choice, preventing static build-up and physical damage to components like circuit boards and displays.
- Food and Beverage: Ensuring the integrity of packaging and preventing the bruising of food items, these conveyors are used extensively in the food processing industry, from packaging lines to sorting and distribution.
- Glass and Ceramics: For materials that are inherently fragile, such as glassware and ceramic products, zero-impact roller conveyors provide the gentle handling needed to minimize breakage and waste.
- Automotive Parts: The conveyor system is adept at handling automotive components, from small, delicate parts like sensors and airbags to larger, more robust items, ensuring they reach the assembly line undamaged.
- E-commerce Fulfillment Centers: With the rise of online shopping, fulfillment centers require efficient, damage-free handling of a wide variety of products. Zero-impact roller conveyors facilitate the rapid and safe movement of goods, from electronics to household items.
- Aerospace Components: The aerospace industry benefits from the precise and careful handling of components that are often large, expensive, and structurally integral, ensuring they are transported without stress or damage.
Examples from Industries
The versatility of zero-impact roller conveyor is further demonstrated by the specific applications within these industries, showcasing their ability to meet diverse material handling needs.
- Assembly Lines: Enhancing efficiency while protecting the product integrity during assembly processes.
- Quality Control Stations: Transporting items between inspection points without affecting their condition, ensuring accurate quality assessments.
- Packaging Operations: Handling packaged goods with care, preventing damage to packaging materials and contents.
- Sorting Systems: Used in automated sorting systems to gently divert items to different destinations without causing damage.
- Loading and Unloading Areas: Minimizing impact at critical points of loading and unloading, especially for goods transferred between different transport modes.
- Temperature-Controlled Environments: Ideal for use in refrigerated or heated areas, where product integrity may be temperature-sensitive.
- Clean Rooms: Suitable for environments that require contamination-free conditions, such as semiconductor manufacturing and food processing areas.
- High-Volume Distribution Centers: Facilitating the rapid movement of goods in high-volume settings, ensuring timely and damage-free delivery to retailers and consumers.
The application of zero-impact roller conveyors across these industries and processes highlights their critical role in modern manufacturing and distribution networks. By providing a solution that combines efficiency with the gentle handling of products, zero-impact roller conveyors have become an indispensable tool in achieving operational excellence and customer satisfaction.
How to Select a Zero-Impact Roller Conveyor
Choosing the right zero-impact roller conveyor for your application involves a detailed assessment of your operational needs and the specific characteristics of the materials you intend to transport. The zero-impact roller conveyor, with its innovative design to minimize damage during transport, is an excellent choice for industries where the integrity of the product is critical. Below are nine essential factors to consider when selecting a zero-impact roller conveyor to ensure it meets your operational requirements effectively.
Factors to Consider
- Load Capacity: The first and foremost consideration is the weight of the products the conveyor will carry. Zero-impact roller conveyors are designed to handle specific weight ranges without compromising the zero-impact feature, ensuring that products are transported safely without damage.
- Material Type: The type of materials or products being transported can significantly influence your choice. Zero-impact roller conveyors are particularly beneficial for fragile, delicate, or high-value items that require gentle handling to prevent damage.
- Conveyor Length and Width: The dimensions of the conveyor are crucial to accommodate the size of your products and the available space in your facility. It’s essential to choose a conveyor that fits your spatial constraints while providing enough surface area to transport your goods efficiently.
- Operational Speed: Consider the speed at which you need to move your products. Zero-impact roller conveyors can be customized to operate at varying speeds, ensuring that your products are transported at an optimal pace without causing damage.
- Environmental Conditions: The environment in which the conveyor will operate can affect its performance. Factors such as temperature, humidity, and exposure to chemicals should be considered to select a conveyor that can withstand your specific environmental conditions.
- Integration with Existing Systems: If you’re integrating the zero-impact roller conveyor into an existing material handling system, it’s vital to ensure compatibility. Consider how the new conveyor will connect with your current setup to maintain a seamless operation.
- Customization Options: Look for customization options that can tailor the conveyor to your specific needs. This can include adjustable speeds, reversible operation, or special features like cooling fans or heating elements for temperature-sensitive products.
- Safety Features: Safety is paramount in any industrial setting. Ensure that the zero-impact roller conveyor comes equipped with necessary safety features such as emergency stops, guards, and safety labels to protect your workers and products.
- Maintenance and Support: Finally, consider the maintenance requirements and the level of support available from the manufacturer. A zero-impact roller conveyor with low maintenance needs and robust manufacturer support ensures long-term reliability and efficiency.
Selecting a zero-impact roller conveyor involves a comprehensive evaluation of these factors to find a system that meets your specific material handling needs. By carefully considering each of these aspects, you can ensure that your zero-impact roller conveyor enhances your operational efficiency, protects your products, and integrates seamlessly into your existing processes.
Installation and Maintenance of Zero-Impact Roller Conveyor
Implementing a zero-impact roller conveyor into your operational environment is a strategic move towards enhancing efficiency and safeguarding product integrity. The installation and subsequent maintenance of these conveyors are critical to ensuring they deliver the expected performance and longevity. Below, we delve into the essential steps and practices that underpin the successful deployment and upkeep of a zero-impact roller conveyor system.
Installation Procedures for Zero-Impact Roller Conveyors
The installation of a zero-impact roller conveyor is a meticulous process that requires careful planning and execution. Following a structured approach ensures the system is set up efficiently and ready to operate at its best.
- Pre-Installation Planning: Assess the installation site to ensure adequate space and compatibility with existing systems. Planning includes layout considerations and identifying any potential obstacles.
- Unpacking and Inspection: Upon arrival, unpack the conveyor components carefully and inspect for any damage that may have occurred during transport.
- Assembly of Components: Follow the manufacturer’s instructions to assemble the conveyor. This often starts with the frame, followed by the installation of rollers and the drive system.
- Alignment and Leveling: Proper alignment and leveling of the conveyor are crucial to ensure smooth operation. Use precision tools to check alignment and make necessary adjustments.
- Electrical and Control System Setup: Install and connect the electrical components, including motors and control systems. Ensure all wiring complies with local codes and safety standards.
- Testing without Load: Conduct a comprehensive test of the conveyor without load to verify that all components are functioning correctly and the conveyor operates smoothly.
- Load Testing: After successful no-load testing, perform load testing with actual products to ensure the conveyor can handle the intended weight and volume without issues.
- Safety Checks: Finally, perform thorough safety checks, including verifying emergency stops and guards are in place and functional.
Tips for Maintaining Zero-Impact Roller Conveyors
Regular maintenance is key to extending the life of your zero-impact roller conveyor and ensuring it continues to operate efficiently. Here are ten tips to help you maintain your conveyor system:
- Regular Inspections: Conduct routine inspections to identify any wear and tear or potential issues before they escalate.
- Lubrication: Keep moving parts, especially rollers and bearings, well-lubricated to reduce friction and prevent wear.
- Cleaning: Regularly clean the conveyor to remove debris and dust that could hinder operation or damage the products.
- Alignment Checks: Periodically check the alignment of the conveyor and adjust as necessary to prevent uneven wear.
- Belt Tension: Maintain proper belt tension to ensure efficient operation and prevent slippage or stretching.
- Electrical System Maintenance: Regularly inspect electrical components for signs of wear or damage and ensure connections are secure.
- Software Updates: If your conveyor uses software for operation, ensure it is kept up to date with the latest versions and patches.
- Training for Operators: Ensure operators are properly trained on the correct use and emergency procedures to prevent misuse and accidents.
- Replacement Parts: Keep critical spare parts on hand to minimize downtime in the event of a failure.
- Professional Audits: Consider scheduling periodic audits by the manufacturer or a professional service to ensure your conveyor is in optimal condition.
Zero-Impact Roller Conveyor Manual
The manufacturer’s manual for your zero-impact roller conveyor is an invaluable resource for both installation and maintenance. It provides:
- Specific Assembly Instructions: Detailed steps tailored to your particular model.
- Parts List: A comprehensive list of components for inventory and replacement purposes.
- Alignment Guidelines: Precise instructions for aligning the conveyor to ensure optimal performance.
- Lubrication Specifications: Recommendations for lubricants and lubrication intervals.
- Cleaning Procedures: Guidelines on how to clean your conveyor without damaging sensitive components.
- Troubleshooting Tips: Solutions to common issues that may arise during operation.
- Safety Information: Important safety precautions to protect operators and products.
- Warranty Details: Information on what is covered under warranty and how to make a claim.
- Contact Information: How to contact support for assistance with issues beyond the scope of the manual.
Adhering to the guidelines provided in the zero-impact roller conveyor manual ensures that your conveyor is installed correctly and maintained in a manner that promotes longevity and reliability. Always consult the manual for the most accurate and specific information regarding your conveyor system.
Cost and Availability of Zero-Impact Roller Conveyor
The zero-impact roller conveyor is a sophisticated piece of material handling equipment designed to transport goods without causing damage. Its unique capabilities come with considerations regarding cost and availability that are crucial for businesses planning to integrate this technology into their operations. Let’s explore the factors influencing the price range of zero-impact roller conveyors and where they can be acquired.
Price Range and Factors Affecting Cost
The investment in a zero-impact roller conveyor system varies widely, influenced by several key factors. Understanding these can help in budgeting and decision-making processes.
- Size and Length: The dimensions of the conveyor significantly impact the price. Larger and longer systems require more materials and sophisticated support structures, increasing the cost.
- Customization: Custom features tailored to specific operational needs, such as adjustable speeds, special materials for rollers, or integration capabilities with existing systems, can elevate the price.
- Technology and Controls: The advanced technology and control systems that enable the zero-impact functionality, including sensors and software, are critical cost factors.
- Material Quality: High-quality materials used for durability and reliability, such as stainless steel or specialized plastics, can increase the cost.
- Installation Complexity: The complexity of installing the conveyor system, which may require professional services, can add to the overall cost.
- Brand and Manufacturer: Prices can vary between manufacturers based on brand reputation, quality of construction, and after-sales support services.
- Operational Capacity: Conveyors designed to handle heavier loads or operate at higher speeds typically cost more due to the need for reinforced structures and more powerful motors.
- Market Demand: Fluctuations in market demand for zero-impact roller conveyors can influence pricing, with higher demand potentially driving up costs.
- Shipping and Handling: For businesses located far from the manufacturer, shipping and handling fees can significantly affect the total investment required.
Where to Find Zero-Impact Roller Conveyors for Sale
Identifying the right source for purchasing a zero-impact roller conveyor is crucial for getting the best value and support.
- Manufacturer Websites: Directly purchasing from the manufacturer’s website ensures you receive authentic information and support.
- Industrial Equipment Distributors: Distributors specializing in industrial equipment often carry a range of conveyor systems, including zero-impact models.
- Trade Shows: Industrial and manufacturing trade shows are excellent venues to explore different models, compare prices, and meet directly with manufacturers.
- Online Marketplaces: Websites dedicated to industrial equipment sometimes list zero-impact roller conveyors, offering a platform to compare different brands and models.
- Referrals: Recommendations from industry peers or consultants who have experience with zero-impact roller conveyors can lead to trusted suppliers.
- Industry Publications: Magazines and journals focused on manufacturing and logistics often feature advertisements or articles on conveyor systems, including new and innovative models.
- Social Media and Forums: Professional networks and forums can provide insights into where to find reliable zero-impact roller conveyors and share experiences about different suppliers.
- Direct Inquiries: Contacting manufacturers directly for quotes and information can provide detailed insights into options and customization opportunities.
- Used Equipment Dealers: For businesses on a tighter budget, reputable dealers in used industrial equipment may offer zero-impact roller conveyors at a reduced price.
When considering the acquisition of a zero-impact roller conveyor, it’s essential to conduct thorough research and engage with reputable suppliers to ensure you receive a system that meets your operational needs and budget constraints. The right investment in a zero-impact roller conveyor can significantly enhance operational efficiency, product integrity, and overall business performance.
Fill out the form for pricing and details on our Zero-Impact Roller Conveyor.
FAQs about Zero-Impact Roller Conveyor
Conveyor rollers are essential components of conveyor systems, facilitating the smooth movement of materials across various distances. There are several types of conveyor rollers, each designed to meet specific operational needs and applications. The most common types include:
Gravity Rollers: These rollers rely on gravity to move items along the conveyor, making them suitable for lightweight materials and requiring a slight incline to facilitate movement. They are cost-effective and easy to install and maintain.
Powered Rollers: Also known as live rollers, they are driven by motors or chains, allowing for the controlled movement of heavier loads. Powered rollers can adjust speeds and are ideal for automated systems.
Grooved Rollers: Designed with grooves to accommodate drive belts or o-rings, grooved rollers are used to power the conveyor belt or to support and guide it from underneath.
Impact Rollers: Placed in areas where materials are loaded onto the conveyor, impact rollers are designed to absorb the shock and distribute the force, protecting the conveyor belt and materials from damage.
Tapered Rollers: Essential for maintaining the flow of materials around curves, tapered rollers prevent items from veering off the conveyor by ensuring they stay aligned.
Plastic and Stainless Steel Rollers: These rollers offer solutions for environments where corrosion resistance is necessary, such as in food processing or pharmaceutical industries. Plastic rollers are lightweight and quiet, while stainless steel rollers are durable and can handle heavier loads.
Each type of roller offers unique advantages, making it crucial to select the appropriate roller type based on the specific requirements of the conveyor system and the materials being transported.
Impact rollers in belt conveyors play a critical role in protecting both the conveyor belt and the materials being transported. Positioned at points where materials are loaded onto the conveyor, such as feed and transfer points, impact rollers are designed to absorb the shock and impact of falling materials. This absorption is achieved through the rollers’ robust construction, often featuring a rubber coating or specially designed structures that dissipate the force of impact.
The primary purpose of impact rollers is to extend the lifespan of the conveyor belt by preventing punctures, tears, or other damage that can occur when materials are dropped onto the conveyor. Additionally, they help to distribute the load evenly across the belt’s width, reducing wear and tear on the belt and the conveyor system as a whole.
Impact rollers are essential in industries where heavy or abrasive materials are handled, such as mining, quarrying, and bulk material handling. By mitigating the force of impact, these rollers ensure smoother operation, reduce maintenance costs, and enhance the overall efficiency of the conveyor system.
While roller conveyors are versatile and widely used in various industries for material handling, they come with certain limitations that may affect their suitability for some applications. These limitations include:
Limited Handling of Irregularly Shaped Items: Roller conveyors are best suited for items with flat bottoms. Irregularly shaped or uneven items may not move smoothly or could become stuck.
Difficulty with Very Small or Large Items: Very small items may fall between rollers, and very large items may require specially designed systems to ensure stability and efficient transport.
Gravity Conveyors Require a Slope: Gravity roller conveyors depend on a slope to facilitate movement, which may not be feasible in all facility layouts.
Powered Conveyors Require Energy: Powered roller conveyors consume electricity, adding to operational costs and requiring access to power sources.
Noise Levels: Particularly in the case of powered roller conveyors, noise generated during operation can be a concern in some environments.
Maintenance Requirements: Regular maintenance is necessary to ensure smooth operation, including lubrication, cleaning, and adjustment of rollers.
Limited Control Over Speed: Especially with gravity conveyors, controlling the speed of items can be challenging without additional mechanisms.
Understanding these limitations is crucial when designing a conveyor system, ensuring that the chosen conveyor type aligns with the specific needs of the operation and the characteristics of the materials being transported.
Unpowered roller conveyors, also known as gravity conveyors, utilize the force of gravity to move items along the conveyor path. This type of conveyor is an efficient and cost-effective solution for transporting goods across short to medium distances within facilities. The applications of unpowered roller conveyors are diverse and include:
Order Picking and Packing: In distribution centers and warehouses, unpowered roller conveyors are commonly used in picking and packing areas to facilitate the movement of goods between different stages of the order fulfillment process.
Assembly Lines: They are used in manufacturing settings to move products between workstations, where assembly or processing occurs. This allows for a smooth flow of components and partially assembled products.
Loading and Unloading: Gravity conveyors are effective for loading and unloading goods from trucks, containers, or other transport vehicles, reducing manual handling and speeding up the process.
Sorting and Inspection: In quality control areas, unpowered roller conveyors allow for the easy inspection and sorting of items, enabling workers to remove defective products or categorize items efficiently.
Retail Backrooms: They facilitate the movement of stock from storage areas to retail floors, making it easier to manage inventory and restock shelves.
The simplicity, low maintenance, and cost-effectiveness of unpowered roller conveyors make them a popular choice in various industries. However, their application is best suited to scenarios where the natural slope of the installation site can be leveraged, and where the items being transported are of a suitable size and weight to move smoothly over the rollers.
Last Updated on August 5, 2024 by Jordan Smith
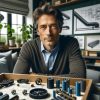
Jordan Smith, a seasoned professional with over 20 years of experience in the conveyor system industry. Jordan’s expertise lies in providing comprehensive solutions for conveyor rollers, belts, and accessories, catering to a wide range of industrial needs. From initial design and configuration to installation and meticulous troubleshooting, Jordan is adept at handling all aspects of conveyor system management. Whether you’re looking to upgrade your production line with efficient conveyor belts, require custom conveyor rollers for specific operations, or need expert advice on selecting the right conveyor accessories for your facility, Jordan is your reliable consultant. For any inquiries or assistance with conveyor system optimization, Jordan is available to share his wealth of knowledge and experience. Feel free to reach out at any time for professional guidance on all matters related to conveyor rollers, belts, and accessories.