Decoding Impact Roller Bearings: An Essential Guide for Beginners
Bearings, in their most fundamental sense, are machine elements that enable parts to rotate or move with minimal friction while supporting a load. This intricate balance of load distribution and reduced friction plays a pivotal role across various operational environments. Whether in automobile engines, home appliances or industrial machinery, bearings harmonize the interplay of moving parts – enhancing efficiency and durability.
Among the galaxy of bearings, one type stands out – the impact roller bearing. As a specific kind of rolling element bearing, impact roller bearings are particularly designed to bear heavy loads and impact forces while reducing friction. They see wide applications where high load capacity and shock resistance are required. Throughout this article, we delve deeper into the world of impact roller bearings, exploring their structure, functions, and significance in various applications.
Unpacking the Impact Roller Bearing
The world of bearings is vast and varied, with the impact roller bearing standing as a testament to engineering precision designed to withstand substantial force while ensuring smooth operation. An impact roller bearing is specifically engineered to manage both radial and axial loads effectively, particularly where impact or shock loads are prevalent. This makes them an invaluable component in heavy machinery, automotive applications, and in industries where durability under high-stress conditions is crucial.
An Impact Roller Bearing is a specialized component designed to handle the dynamic loads and impacts encountered in heavy-duty industrial applications, such as in conveyor systems, crushers, or heavy machinery. These bearings are crucial in environments where conventional bearings might fail due to high shock loads, contamination, or extreme operational conditions.
Highlighting Brands and Focusing on GRAM Impact Roller Bearings
Several brands have distinguished themselves in the manufacturing of high-quality impact roller bearings. Among them, GRAM impact roller bearings stand out for their commitment to durability, performance, and reliability. GRAM has become synonymous with bearings designed to face the challenges of high-impact environments head-on, leveraging advanced materials and innovative designs to minimize wear and tear and maintain operational efficiency under even the most demanding conditions.
By selecting GRAM impact roller bearings, or those from other reputable brands, businesses and technicians ensure they are incorporating components built to last, reducing downtime, and enhancing overall machine performance. With each brand offering its unique advantages, consulting the “Impact Roller Bearing Size Chart” becomes even more critical, ensuring that the chosen bearing not only fits the spatial requirements of the application but also meets or exceeds performance expectations.
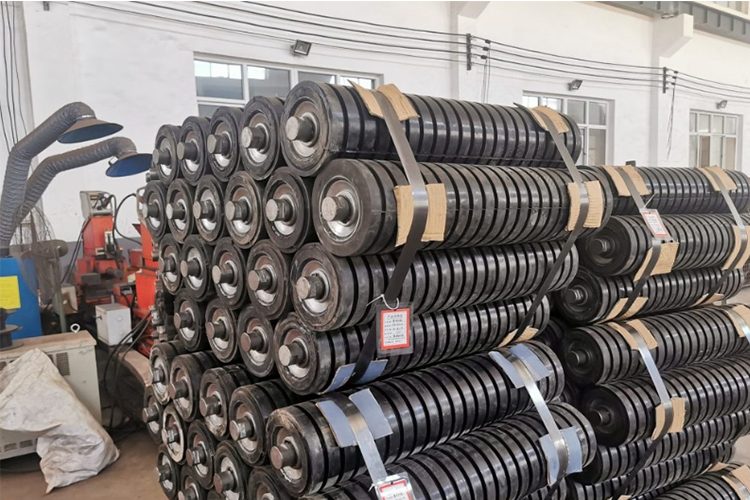
GRAM Impact Roller Bearings
The Sizes of Impact Roller Bearings
To fully understand the versatility and application of impact roller bearings, one must delve into the “Impact Roller Bearing Size Chart” and “Impact Roller Bearing Sizes.” Just as no two applications are exactly alike, impact roller bearings come in a myriad of sizes to accommodate varying load requirements and operational constraints. These size charts provide a comprehensive overview, typically represented in tables, detailing dimensions such as inner diameter, outer diameter, and width, alongside bearing capacities. This categorization ensures engineers and technicians can select the most appropriate bearing size for their specific needs, optimizing performance and extending equipment lifespans.
The sizes of Impact Roller Bearings can vary significantly depending on their specific application and the requirements of the machinery or equipment in which they are used. Here’s an overview of how these sizes are typically categorized:
1. Bore Diameter (d):
- The bore diameter refers to the internal diameter of the bearing, which is the hole through which the shaft or axle passes.
- Standard Sizes: Bore diameters can range from small sizes like 20 mm (0.79 inches) for light-duty applications to several hundred millimeters (up to 500 mm or more, approximately 20 inches) for heavy-duty industrial applications.
2. Outer Diameter (D):
- The outer diameter is the external diameter of the bearing, which fits into the housing or casing.
- Standard Sizes: Outer diameters can range from 40 mm (1.57 inches) to over 1,000 mm (39.37 inches), depending on the application.
3. Width (B):
- The width of the bearing refers to the thickness of the bearing, measured from one side to the other.
- Standard Sizes: Bearing widths can range from 12 mm (0.47 inches) to over 300 mm (11.81 inches).
4. Rolling Element Size:
- The size and number of rolling elements (cylindrical rollers in the case of impact roller bearings) also vary depending on the bearing’s load capacity.
- Dimensions: Roller diameters can range from a few millimeters to several centimeters, with the length of the rollers varying accordingly.
5. Load Rating:
- Impact Roller Bearings are designed to handle heavy loads. Their load rating is determined by their size, material, and design.
- Dynamic Load Rating (C): Can range from several kN (kilo-Newtons) for smaller bearings to thousands of kN for larger bearings.
- Static Load Rating (Co): This also varies widely, often exceeding the dynamic load rating, especially in heavy-duty applications.
6. Custom Sizes:
- Many impact roller bearings are custom-made to fit specific industrial machinery. These custom bearings can have non-standard dimensions to meet particular needs.
Examples of Common Sizes:
- Medium Duty: A typical size might be 120 mm (bore) x 180 mm (outer diameter) x 40 mm (width).
- Heavy Duty: Larger bearings might be 320 mm (bore) x 480 mm (outer diameter) x 120 mm (width).
Dimensional Standards:
Impact roller bearings often conform to international standards like ISO (International Organization for Standardization) or DIN (Deutsches Institut für Normung), which define standard sizes and tolerances for bearings. These standards help ensure compatibility and interchangeability of bearings across different manufacturers and applications.
he size of an impact roller bearing is highly variable and depends on the specific demands of the application. The dimensions must be carefully selected to ensure that the bearing can handle the expected loads and operating conditions.
Impact Roller Bearing Size Chart:
Bore Diameter (d) | Outer Diameter (D) | Width (B) | Dynamic Load Rating (C) | Static Load Rating (Co) |
---|---|---|---|---|
20 mm (0.79 in) | 47 mm (1.85 in) | 14 mm (0.55 in) | 15 kN | 7.6 kN |
25 mm (0.98 in) | 52 mm (2.05 in) | 15 mm (0.59 in) | 19.5 kN | 10 kN |
30 mm (1.18 in) | 62 mm (2.44 in) | 16 mm (0.63 in) | 27 kN | 14 kN |
35 mm (1.38 in) | 72 mm (2.83 in) | 17 mm (0.67 in) | 35 kN | 18 kN |
40 mm (1.57 in) | 80 mm (3.15 in) | 18 mm (0.71 in) | 42 kN | 22 kN |
50 mm (1.97 in) | 90 mm (3.54 in) | 20 mm (0.79 in) | 55 kN | 28 kN |
60 mm (2.36 in) | 110 mm (4.33 in) | 22 mm (0.87 in) | 72 kN | 36 kN |
80 mm (3.15 in) | 140 mm (5.51 in) | 26 mm (1.02 in) | 105 kN | 53 kN |
100 mm (3.94 in) | 160 mm (6.30 in) | 30 mm (1.18 in) | 135 kN | 68 kN |
120 mm (4.72 in) | 180 mm (7.09 in) | 34 mm (1.34 in) | 165 kN | 82 kN |
150 mm (5.91 in) | 210 mm (8.27 in) | 36 mm (1.42 in) | 200 kN | 100 kN |
200 mm (7.87 in) | 280 mm (11.02 in) | 38 mm (1.50 in) | 300 kN | 150 kN |
250 mm (9.84 in) | 350 mm (13.78 in) | 42 mm (1.65 in) | 400 kN | 200 kN |
300 mm (11.81 in) | 400 mm (15.75 in) | 46 mm (1.81 in) | 500 kN | 250 kN |
Key Notes:
- Dynamic Load Rating (C): The maximum load the bearing can endure during operation, expressed in kN (kilo-Newtons).
- Static Load Rating (Co): The maximum load the bearing can handle when stationary without permanent deformation, also expressed in kN.
Considerations:
- Custom Sizes: Depending on specific industry requirements, custom sizes and load ratings may be available.
- Material and Design: The load ratings can vary based on the material (e.g., steel, ceramic) and the internal design of the bearing.
This size chart provides a general guideline, but the exact specifications should be confirmed with the manufacturer or supplier, particularly for critical applications where precise dimensions and load capacities are essential.
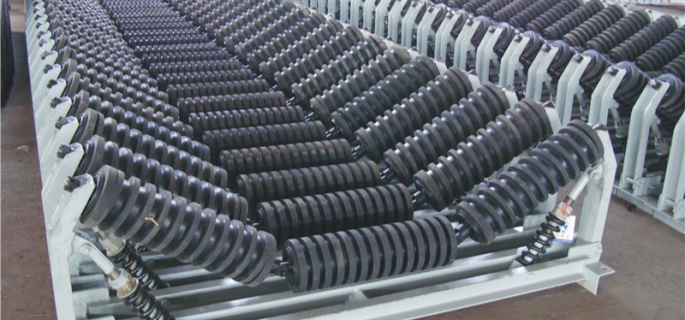
Impact Roller Bearing Products Types
Impact roller bearings are specialized components used in various industrial applications to manage heavy loads, reduce friction, and withstand the high impacts that can occur during operation. Below are some common types of impact roller bearing products:
1. Cylindrical Roller Bearings
- Single-row cylindrical roller bearings: These bearings have a high radial load capacity and are typically used in applications where space is limited.
- Double-row cylindrical roller bearings: These provide higher radial load capacity and are suitable for heavier loads.
- Full-complement cylindrical roller bearings: These have a maximum number of rollers and are used for very high radial loads at low speeds.
2. Spherical Roller Bearings
- Single-row spherical roller bearings: These are designed to handle high radial loads and moderate axial loads in both directions.
- Double-row spherical roller bearings: These can accommodate misalignment and are used in applications with heavy radial and axial loads.
3. Tapered Roller Bearings
- Single-row tapered roller bearings: These are typically used in pairs to handle combined axial and radial loads.
- Double-row tapered roller bearings: Provide higher load capacity and are used in applications like automotive axles.
- Four-row tapered roller bearings: Used in heavy machinery, such as rolling mills, where high radial and axial loads are present.
4. Needle Roller Bearings
- Radial needle roller bearings: Compact and lightweight, these bearings are used in applications with limited space and high radial loads.
- Thrust needle roller bearings: Designed to handle axial loads in one direction while being space-efficient.
5. Thrust Roller Bearings
- Cylindrical thrust roller bearings: Used in applications with high axial loads and low speeds.
- Spherical thrust roller bearings: These bearings can accommodate misalignment and are used in heavy-duty applications where axial loads are significant.
6. Cam Followers
- Standard cam followers: These are designed for applications where there is direct contact with a cam or track.
- Heavy-duty cam followers: These are used in applications where higher loads and impacts are expected.
7. Split Roller Bearings
- Split cylindrical roller bearings: These are designed for easy installation and maintenance, used in applications where bearing replacement is challenging without disassembling the surrounding equipment.
8. Precision Roller Bearings
- High-precision cylindrical roller bearings: Used in machine tools and other high-precision applications where accuracy and rigidity are crucial.
- High-precision tapered roller bearings: Often used in aerospace and other critical applications where precision is key.
9. Sealed Roller Bearings
- Sealed spherical roller bearings: These bearings are protected against contamination and are used in harsh environments.
- Sealed cylindrical roller bearings: Similar to spherical types, but designed for environments where contamination control is crucial.
Each type of impact roller bearing is designed for specific applications and operating conditions. The choice of bearing type depends on factors like load capacity, speed, alignment, space constraints, and environmental conditions.

Spherical Impact Roller Bearing
A Spherical Impact Roller Bearing is a type of bearing specifically designed to accommodate high radial loads and misalignment in heavy-duty applications. These bearings are particularly well-suited for environments where shock loads, vibration, and misalignment are common, such as in mining, construction, and heavy machinery.
Key Features of Spherical Impact Roller Bearings
Spherical Outer Ring:
- The outer ring of these bearings has a spherical shape, which allows the bearing to adjust to misalignment between the shaft and the housing. This self-aligning feature is crucial in applications where perfect alignment cannot be guaranteed.
Impact-Resistant Design:
- These bearings are engineered to handle heavy impact loads. The design often includes robust rolling elements and a reinforced cage that can withstand sudden and severe load spikes.
Cylindrical or Barrel Rollers:
- The rolling elements in spherical impact roller bearings are typically cylindrical or barrel-shaped, allowing them to distribute loads evenly across the bearing. This design helps in managing high radial and axial loads.
Dual Rows of Rollers:
- Spherical impact roller bearings often have two rows of rollers, which increases their load-carrying capacity and provides greater stability under heavy loads.
Heavy-Duty Materials:
- These bearings are made from high-strength steel or other durable materials to resist wear and fatigue, even under the most demanding conditions.
Sealing and Lubrication:
- Spherical impact roller bearings typically come with robust seals to keep out contaminants like dirt and moisture. They also require proper lubrication to maintain performance and longevity.
Applications
- Mining Equipment:
- Used in crushers, conveyors, and other heavy-duty mining machinery that experiences constant vibration and high impact loads.
- Construction Machinery:
- Applied in bulldozers, excavators, and cranes where misalignment and shock loads are common.
- Material Handling:
- Ideal for conveyor systems that transport heavy materials and experience significant load variations and misalignment.
- Wind Turbines:
- Used in the main shafts of wind turbines, where they must handle both high loads and misalignment caused by wind forces.
Advantages
- Self-Aligning Capability:
- The spherical design allows the bearing to compensate for misalignment, which can be caused by shaft deflection or mounting errors.
- High Load Capacity:
- With their dual rows of rollers and robust design, these bearings can support substantial radial and axial loads.
- Durability:
- Designed to withstand harsh conditions, including high impact, heavy loads, and the presence of contaminants.
Sizes and Specifications
- Bore Diameters:
- Typically range from 20 mm (0.79 inches) to over 500 mm (19.69 inches).
- Outer Diameters:
- Range from 40 mm (1.57 inches) to more than 1,000 mm (39.37 inches).
- Width:
- Can vary depending on the specific application, with typical widths ranging from 12 mm (0.47 inches) to over 300 mm (11.81 inches).
- Load Ratings:
- Dynamic load ratings can range from a few kN for smaller bearings to thousands of kN for larger ones, depending on the design and application.
Spherical Impact Roller Bearings are indispensable in applications requiring robust performance under high load conditions, especially where misalignment is a concern. They offer a combination of durability, flexibility, and load-handling capabilities, making them ideal for the most challenging industrial environments.
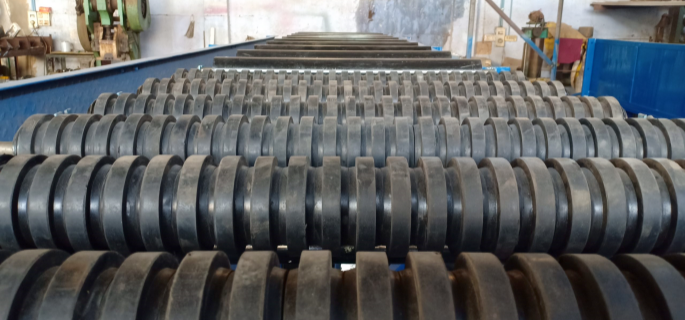
What are Bearing Damage Types and Roller Bearing Wear Patterns in Impact Roller Bearings
Recognizing the various forms of damage that can afflict impact roller bearings is crucial for maintaining their operational integrity. Over their service life, these bearings may encounter several types of damage, which can compromise their efficiency and, ultimately, the machinery they serve.
Delving into Bearing Damage Types
Bearing damage can manifest in multiple ways, and each type of damage tells a story about the conditions to which the impact roller bearing has been exposed. Common bearing damage types include:
- Abrasive Wear: Caused by foreign particles or debris, resulting in the scratching and grooving of bearing surfaces.
- Adhesive Wear: Occurring when sliding surfaces bond at a microscopic level under extreme pressure or insufficient lubrication, causing material transfer and increased friction.
- Corrosion and Erosion: Resulting from exposure to corrosive agents, leading to pitting and weakening of impact roller bearing surfaces.
Studies on Roller Bearing Wear Patterns
Wear patterns on impact roller bearings reveal the history of the loads and conditions they’ve endured. A systematic examination of wear patterns such as spalling, brinelling, and scoring can help identify potential causes of failure. Patterns differ based on whether the primary movements are radial or axial, and the variability of operational factors like speed and temperature.
- Spalling: Indicates material fatigue, where surface stresses exceed the endurance limit of the material.
- Brinelling: Shows as indentations on the bearing raceways, usually from excessive load or impact.
- Scoring: Characterised by heavy wear lines, often due to lubrication failure or debris contamination.
Case Examples: Damage and Wear in Impact Roller Bearings
In the context of large-scale industrial operations, where machinery is pushed to its limits, damage and wear take on tangible forms. Impact roller bearings in wind turbines, for instance, may exhibit wear patterns that suggest alignment issues or inconsistent loading. Similarly, bearings within mining equipment might show signs of abrasive wear due to the harsh working environment. Variations in bearing sizes affect the distribution of loads and thus influence the type of damage observed. By studying real-life examples and understanding these patterns, engineers can better predict bearing life spans, prescribe necessary maintenance, and implement design improvements to mitigate future damage to impact roller bearings.
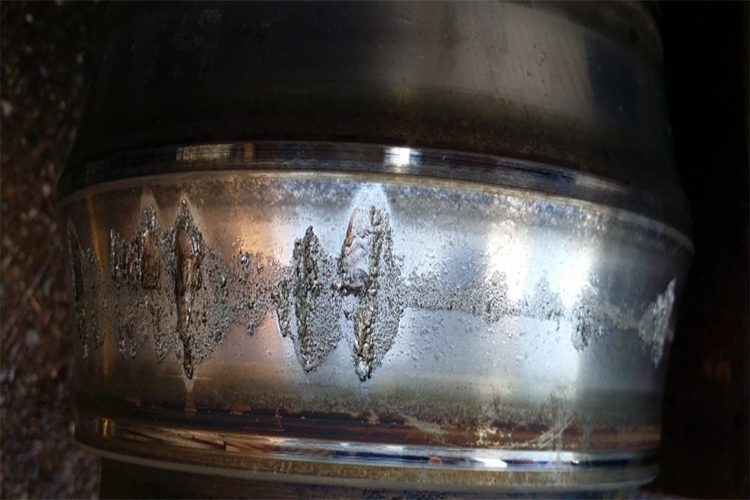
Damage in Impact Roller Bearings
Uncovering Bearing Failure Analysis in Impact Roller Bearings
Bearing failure analysis is an essential post-mortem process conducted when an impact roller bearing fails before its expected service life. This analysis not only uncovers the root causes of failure but also provides actionable insights to prevent future recurrences.
Demystifying the Content of Bearing Failure Analysis
In the context of bearing failure analysis, the goal is to methodically break down the sequence of events leading to an impact roller bearing’s malfunction. The process starts with visual inspections, studying wear patterns, and extends to more intricate methods like scanning electron microscopy and material analysis. This comprehensive investigation includes examinations of lubrication properties, load conditions, environmental factors, and maintenance records to form a full picture of the operational landscape at the time of failure.
Exploring Ball Bearing Failure Analysis in Relation to Impact Roller Bearings
Ball bearing failure analysis shares common grounds with that of impact roller bearings, albeit with some differences due to varying design and application contexts. The analysis often points to issues such as improper handling during installation, insufficient lubrication, or misalignment as culprits for failure. This extended discussion sheds light on subtle nuances unique to ball bearings, such as raceway deformations or ball fracture, which may also be applicable in diagnosing and understanding the distress in impact roller bearings.
By dissecting and learning from past failures, engineers and maintenance teams can enhance the reliability and function of impact roller bearings. Through failure analysis, the industry not only achieves improvements in bearing design but also refines the envelope of best practices in bearing installation, maintenance, and operation.
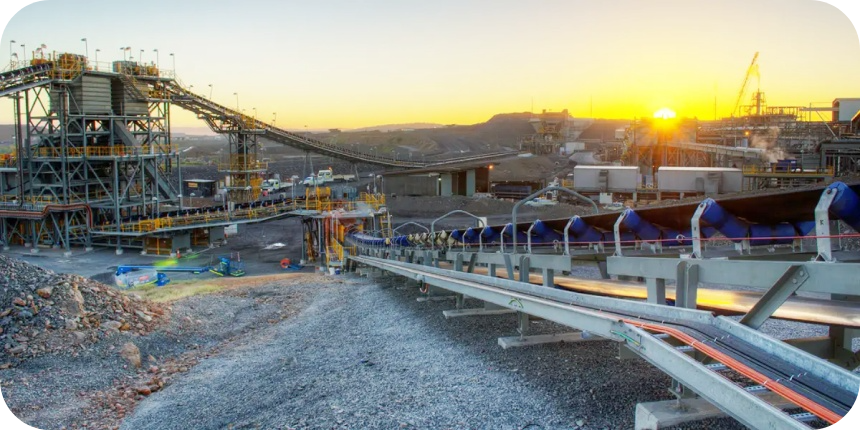
Checking the Cause of Bearing Damage in Impact Roller Bearings
Understanding the causes of bearing damage is pivotal for the maintenance and longevity of impact roller bearings. Bearing failures not only result in operational downtimes but can also lead to severe accidents. By dissecting the causes behind bearing peeling and interpreting bearing failure symptoms, we can preemptively address problems before they escalate into significant issues.
Pinpointing the Causes of Bearing Damage
Bearing damage in impact roller bearings often traces back to a handful of culprits, including mechanical overload, lubrication failure, improper installation, and environmental factors. Bearing peeling, for instance, is a condition where the surface layer of the bearing’s raceways or rolling elements begins to flake off. This condition can result from material fatigue, which is often due to cyclic loading beyond the material’s limit, inadequate lubrication that leads to metal-to-metal contact, or contamination that introduces abrasive particles into the bearing surfaces.
Each of these causes translates into practical operational problems. Mechanical overload, for example, can occur when equipment is improperly loaded or subject to impact forces that exceed the design specifications of the bearing. Inadequate lubrication may stem from using the wrong type of lubricant, insufficient amounts, or degradation of lubricant over time. Improper installation encompasses a range of errors, including using excessive force, misalignment, and using incorrect fitting tools, which can induce premature wear or failure. Environmental factors include exposure to corrosive substances, ingress of dirt or water, and operating in temperatures outside the recommended range for the bearing materials.
Real-Life Examples Illustrating Common Reasons for Damage
Let’s consider a few real-life scenarios to illustrate these reasons:
- Mechanical Overload: A heavy-duty conveyor system transporting mining ore exceeded its operational load, resulting in several impact roller bearings experiencing premature peeling and ultimately failing. The excessive load surpassed the bearings’ dynamic capacity, leading to material fatigue.
- Lubrication Failure: In a paper mill, several impact roller bearings failed due to lubrication failure. The high temperature and humidity environment caused the lubricant to degrade faster than anticipated. The ensuing metal-to-metal contact resulted in significant wear and overheating, contributing to bearing seizure.
- Improper Installation: During maintenance of a wind turbine, several impact roller bearings were replaced. However, improper fitting techniques were used, leading to misalignment. The misaligned bearings experienced uneven load distribution, leading to early signs of peeling and vibration issues.
- Environmental Factors: In a coastal energy plant, impact roller bearings in the turbine system showed signs of corrosion-induced damage. The salty air environment accelerated the corrosion process, compromising the integrity of the bearing materials and leading to premature failure.
By analyzing these causes and real-life examples, maintenance teams and engineers can develop more robust strategies to prevent bearing damage, ensuring the reliability and efficient performance of machinery equipped with impact roller bearings.
Strategies to Prevent Failure in Impact Roller Bearings
The unwelcome scenario of bearing failure can be sidestepped through a combination of robust maintenance practices, adherence to industry-recommended strategies, and new technologies for early detection of bearing damage and wear. In the case of impact roller bearings, a preventive and proactive approach can significantly enhance operational efficiency and extend the service life of the component.
Maintenance Practices to Deter Bearing Damage
Regular and systematic maintenance is the first line of defense against bearing failure. Key practices include timely lubrication with appropriate lubricants, routine visual inspections for signs of wear or damage, maintaining a clean operating environment, and aligning the bearings correctly during installation or replacement.
When it comes to an impact roller bearing, the load and operating conditions should be carefully monitored as these bearings are often used in heavy-duty and high-impact applications. The use of protective seals can also help prevent the ingress of contaminants that can accelerate wear and cause premature bearing failure.
Industry-Recommended Maintenance Strategies for Impact Roller Bearings
Industry professionals advocate for regular inspections and the creation of a proactive maintenance schedule. As part of this strategy, operators should monitor parameters like temperature and vibration with the help of advanced tools and sensors. These metrics can hint at abnormalities, such as an unexpected rise in temperature indicating poor lubrication or abnormal vibrations that could denote misalignments, helping preempt potential failure scenarios. Additionally, adhering to the manufacturer’s guidelines for installation, lubrication, and load limits is a must for maintaining the integrity of impact roller bearings.
Incorporating Early Detection Systems for Bearing Damage and Wear
In the realm of advanced strategies to prevent bearing failures, early detection systems come to the forefront. Technologies like condition monitoring systems (CMS) enable real-time tracking of key performance metrics in impact roller bearings. These systems use a range of sensors to gather data related to vibration, temperature, load, speed and more. Coupled with sophisticated analysis software, these systems can provide early alerts for potential problems such as lubrication issues, alignment errors, or impending mechanical failure, allowing teams to respond promptly before the issue escalates.
Further, technologies like predictive maintenance tools leverage machine learning and artificial intelligence to discern subtle patterns or anomalies in machine operation, providing predictive insights to prevent bearing failure.
Embracing meticulous maintenance practices, following industry-recommended strategies, and adopting early detection systems can tangibly improve the longevity and performance of impact roller bearings, reducing the risk of sudden failure and potentially expensive downtimes.
Fill in your details to get a quote on our Impact Roller Bearings.
FAQs about Impact Roller Bearing
Roller bearings are designed to reduce friction and support loads in various applications. The primary types encompass cylindrical, spherical, tapered, and needle roller bearings, each serving distinct purposes.
Cylindrical Roller Bearings: Characterized by their cylindrical shape, these bearings can handle high radial loads and operate well at high speeds. They are suitable for applications requiring the bearing to support heavy radial loads, such as electric motors and automotive transmissions.
Spherical Roller Bearings: These bearings have barrel-shaped rollers between the inner and outer rings, which are inclined at an angle to the bearing axis. They are especially adept at accommodating misalignment and shaft deflections, making them ideal for applications in sectors like mining and construction where operational conditions can lead to misalignments.
Tapered Roller Bearings: Featuring conical rollers against the inner and outer ring raceways, their design allows them to efficiently support both radial and axial loads. The capacity to handle large loads and the capability to adjust clearance make them a popular choice in automotive, industrial, and construction machinery.
Needle Roller Bearings: With their small cylindrical rollers, needle roller bearings have a high load capacity relative to their size. They are particularly effective in applications where the bearing space is limited. Despite their slender appearance, they are robust, making them suitable for automotive components such as rocker arm pivots and compressors.
Each type brings unique advantages, catering to the specific needs of a wide range of applications by supporting different load capacities, speeds, and alignment requirements.
Roller bearings can be compromised by several factors, which may include excessive loads, inadequate lubrication, contamination, misalignment, and improper handling.
Excessive Loads: Subjecting bearings to loads beyond their designed capacity can cause deformation, increased friction, and ultimately, premature failure.
Inadequate Lubrication: One of the primary reasons for bearing failure, insufficient lubrication leads to increased friction and overheating, accelerating wear and damage.
Contamination: The intrusion of foreign particles, such as dirt, dust, or water, can severely diminish the performance of roller bearings by causing abrasion and corrosive wear.
Misalignment: Bearings designed to handle specific alignment conditions may suffer from uneven load distribution if misaligned, leading to uneven wear and increased stress on the bearing components.
Improper Handling: Incorrect installation methods, such as using excessive force or inappropriate tools, can harm the bearing’s integrity right from the onset.
It’s paramount to adhere to proper maintenance practices, including regular inspections, correct installation, and ensuring an environment free of contaminants, to extend the life of roller bearings.
When comparing the strength and load-bearing capacities of roller and ball bearings, roller bearings generally come out ahead due to their larger contact area with the races. This design characteristic allows roller bearings to support higher radial loads compared to ball bearings of the same size. Roller bearings are structured to distribute loads across a broader surface area, which translates into higher load capacities and potentially longer service life under heavy-duty conditions.
However, “stronger” can be context-dependent. For applications requiring the accommodation of both radial and axial loads in high-speed environments, ball bearings might be preferred for their ability to handle these conditions with less friction and heat generation. Ultimately, the choice between roller and ball bearings comes down to the specific requirements of the application, including load type, operational speed, precision, and space constraints.
For applications tasked with supporting heavy loads, spherical and tapered roller bearings are commonly utilized due to their design and load distribution capabilities.
Spherical Roller Bearings: Spherical roller bearings are adept at handling heavy radial loads and can accommodate misalignment, a common occurrence in heavy load applications. Their design allows them to manage both radial and axial loads efficiently, making them an excellent choice for applications in harsh environments where shaft deflection or misalignments may occur.
Tapered Roller Bearings: Tapered roller bearings excel in applications that subject bearings to heavy radial and axial loads. Their ability to adjust the clearances and manage a large load capacity across the roller’s conical surface makes them indispensable in heavy machinery, such as construction equipment, mining trucks, and agricultural machinery.
The three main types of roller bearings are:
Cylindrical Roller Bearings: These bearings use cylindrical rollers and are designed to support heavy radial loads with low friction.
Spherical Roller Bearings: These have an inner ring with two raceways and an outer ring with a spherical raceway, allowing for angular misalignment.
Tapered Roller Bearings: These bearings are capable of supporting both radial and axial loads and are commonly used in automotive applications.
The cost to replace a roller bearing can vary widely depending on the type of bearing, the vehicle or machine, and labor costs. Typically, the price range is between $100 to $500 per wheel for automotive bearings, including parts and labor. For industrial applications, the cost can be much higher.
Signs that your roller bearings might be bad include:
Unusual noises like grinding or humming coming from the wheel or machinery.
Vibrations or wobbling in the wheel or shaft.
Excessive play or looseness in the bearing area.
Uneven wear on tires or other connected parts.
Increased friction or heat in the area where the bearing is located.
Roller bearings are most preferred in applications where there is a need to support heavy loads with low friction, such as in automotive wheel hubs, industrial machinery, and heavy-duty conveyor systems.
It is not safe to drive with a bad wheel bearing. A failing wheel bearing can lead to unpredictable wheel behavior, increased risk of accidents, and further damage to the vehicle. It should be replaced as soon as possible.
The life expectancy of a wheel bearing typically ranges from 85,000 to 100,000 miles (137,000 to 160,000 kilometers) under normal driving conditions. However, this can vary depending on driving habits, road conditions, and maintenance practices.
Last Updated on August 9, 2024 by Jordan Smith
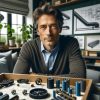
Jordan Smith, a seasoned professional with over 20 years of experience in the conveyor system industry. Jordan’s expertise lies in providing comprehensive solutions for conveyor rollers, belts, and accessories, catering to a wide range of industrial needs. From initial design and configuration to installation and meticulous troubleshooting, Jordan is adept at handling all aspects of conveyor system management. Whether you’re looking to upgrade your production line with efficient conveyor belts, require custom conveyor rollers for specific operations, or need expert advice on selecting the right conveyor accessories for your facility, Jordan is your reliable consultant. For any inquiries or assistance with conveyor system optimization, Jordan is available to share his wealth of knowledge and experience. Feel free to reach out at any time for professional guidance on all matters related to conveyor rollers, belts, and accessories.