Innovative Designs in Mild Steel Conveyor Roller Technology
Conveyor rollers, essential components in the seamless operation of material handling systems, play a pivotal role in industrial settings by facilitating the efficient transport of goods across various stages of production and distribution. Among the myriad of materials employed in the manufacture of these rollers, mild steel stands out for its remarkable combination of durability, cost-effectiveness, and adaptability, making it an ideal choice for a wide range of industrial applications. The use of mild steel conveyor rollers is particularly notable for their ability to withstand considerable wear and tear while maintaining their structural integrity over time. This introduction to mild steel as the preferred material for conveyor rollers underscores its significance in ensuring the smooth and uninterrupted flow of operations in warehouses, manufacturing plants, and distribution centers, highlighting its critical role in the backbone of modern industrial operations.
The Basics of Mild Steel Conveyor Rollers
Mild steel, known for its excellent blend of strength and flexibility, emerges as a frontrunner in the selection of materials for conveyor rollers. The fundamental allure of a mild steel conveyor roller lies in its inherent properties—primarily its impressive durability and malleability, which enable it to withstand the rigorous demands of continuous industrial use. Unlike its counterparts, mild steel provides a cost-effective solution without compromising on quality or performance, making mild steel conveyor rollers a go-to choice for businesses looking to optimize their operations.
When compared to materials like stainless steel and PVC, mild steel stands out for several reasons. Stainless steel, while resistant to corrosion and aesthetically pleasing, often comes with a higher price tag, making mild steel a more budget-friendly option without significantly sacrificing performance. On the other hand, PVC rollers offer the advantage of being lightweight and corrosion-resistant but lack the strength and durability needed for heavy-duty applications, where mild steel shines.
Material | Durability | Cost | Weight | Corrosion Resistance |
---|---|---|---|---|
Mild Steel | High | Low to moderate | Moderate | Moderate |
Stainless Steel | Very High | High | Low to moderate | Very High |
PVC | Low to Moderate | Low | Very Low | High |
This comparative analysis underscores why mild steel conveyor rollers are favored for a vast array of industrial scenarios. Their ability to deliver a balanced combination of resilience, affordability, and performance adaptability makes them an indispensable component in the material handling sector.
Advantages of Mild Steel Conveyor Roller
The superiority of mild steel conveyor rollers is evident through their extensive application in various industrial settings, driven by their unmatched durability, cost-effectiveness, and manufacturing flexibility. Each of these attributes plays a critical role in why mild steel is frequently chosen over alternative materials for conveyor rollers.
Durability and Robustness for Heavy-Duty Applications
Mild steel conveyor rollers exhibit exceptional durability and robustness, making them suitable for heavy-duty applications. These include:
- Mining Operations: Mild steel rollers can withstand the abrasive materials and heavy loads typical in mining conveyance systems.
- Agricultural Processing: They endure the harsh conditions and exposure to various organic materials in the agricultural sector.
- Automotive Assembly Lines: Mild steel rollers support the weight and movement of automotive parts and assemblies without faltering.
- Recycling Facilities: They resist the wear and tear from handling recycled materials of varying sizes and weights.
- Construction Material Handling: Mild steel rollers are capable of transporting heavy construction materials like cement, steel beams, and bricks efficiently.
Cost-effectiveness and Accessibility
Mild steel conveyor rollers are a cost-effective solution due to the relative abundance and lower price of mild steel. This affordability does not compromise their performance, making them a preferred option for companies aiming to reduce operational costs without sacrificing quality. Additionally, the widespread availability of mild steel facilitates quicker production times and easier access to replacements or custom orders.
Flexibility in Manufacturing for Various Industrial Needs
The manufacturing flexibility of mild steel conveyor rollers allows them to be tailored to a wide range of industrial needs, including:
- Custom Lengths and Diameters: Rollers can be fabricated to specific sizes to fit unique conveyor systems.
- Specialized Coatings: Depending on the application, rollers can be coated with materials to enhance corrosion resistance, friction, or material flow.
- Variable Load Capacities: Mild steel rollers can be designed to handle varying load capacities, from lightweight packages to heavy machinery parts.
- Integrated Features: Features like grooves for belt drives or specialized end caps can be incorporated to meet the specific requirements of different conveyor systems.
- Adaptability to Environments: Rollers can be modified for use in extreme temperatures, wet conditions, or areas with high levels of contaminants.
The advantages of mild steel conveyor rollers stem from their robust construction capable of enduring demanding applications, their cost-effective nature that does not compromise on quality or availability, and their flexible manufacturing that caters to a vast array of industrial requirements. These benefits collectively make mild steel rollers an indispensable component in the efficiency and reliability of material handling systems across sectors.
Types of Mild Steel Conveyor Rollers
The versatility of mild steel as a material for conveyor rollers is showcased through the variety of types available, each designed to meet specific industrial needs. The classification of mild steel conveyor rollers into heavy-duty, industrial, and grooved types allows for a more targeted approach in handling materials across diverse operational environments.
Heavy Duty Conveyor Rollers
Heavy-duty mild steel conveyor rollers are engineered to thrive in demanding environments where they must bear heavy loads and withstand rigorous operational conditions. These rollers are essential in industries such as mining, bulk material handling, and heavy manufacturing, where the conveyor systems are under constant stress. The robust construction of these rollers ensures longevity and reliability, minimizing downtime and maintenance requirements. Features may include thicker walls, reinforced bearings, and larger diameters to accommodate the increased load capacities and to ensure smooth operations under challenging conditions.
Industrial Conveyor Rollers
Industrial mild steel conveyor rollers are the backbone of standard conveyor systems found in warehouses, packaging facilities, and assembly lines. Tailored for general industrial applications, these rollers are designed with a focus on versatility and efficiency. They can handle a wide range of materials and products, from boxes and pallets to automotive parts and electronic goods. The adaptability of industrial conveyor rollers makes them a fundamental component in the optimization of material handling processes, enhancing productivity and operational flow.
Grooved Conveyor Rollers
Grooved mild steel conveyor rollers are specialized components designed to facilitate specific movement and control within conveyor systems. The grooves can be customized to match the drive belts or to guide the materials being transported, ensuring precise alignment and directional stability. These rollers are particularly useful in applications requiring the sorting, orientation, or controlled movement of items, such as in postal sorting facilities, packaging lines, and manufacturing plants where precision is key. The addition of grooves adds a level of functionality that supports complex system designs and material handling requirements.
The diversity among mild steel conveyor rollers—spanning heavy-duty, industrial, and grooved types—underscores the material’s adaptability and suitability for a broad spectrum of applications. By selecting the appropriate type of mild steel conveyor roller, businesses can significantly enhance their operational efficiency, reduce maintenance costs, and improve the reliability of their conveyor systems.
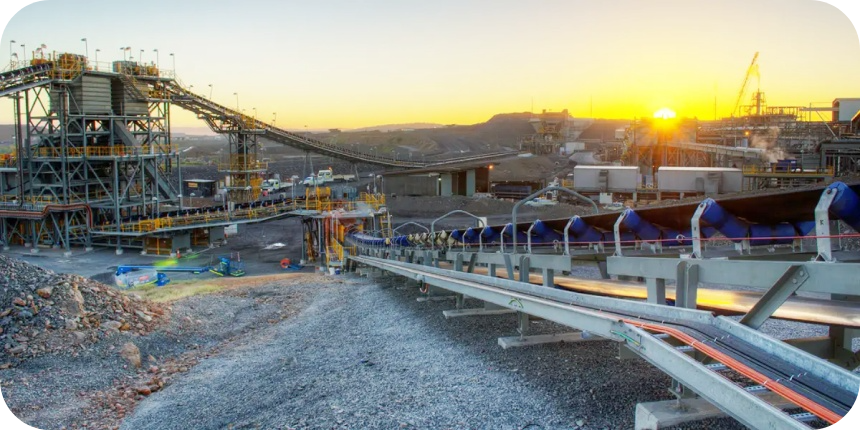
Omni Metalcraft and Mild Steel Conveyor Roller
Omni Metalcraft stands as a beacon in the manufacturing of conveyor components, with its mild steel conveyor rollers being particularly renowned for their quality and durability. As a leading manufacturer, Omni Metalcraft has cemented its reputation through a consistent demonstration of innovation, reliability, and customer-focused solutions in the realm of material handling and conveyor systems.
Introduction to Omni Metalcraft as a Leading Manufacturer
Omni Metalcraft’s expertise in the industry is exemplified by:
- Advanced Manufacturing Techniques: Utilizing state-of-the-art technology to ensure precision and efficiency in the production of mild steel conveyor rollers.
- Comprehensive Quality Assurance: Each roller undergoes rigorous testing to meet high standards of durability and performance.
- Wide Industry Application: Serving a diverse range of sectors including logistics, automotive, pharmaceutical, and food processing with tailored solutions.
- Eco-Friendly Practices: Commitment to sustainable manufacturing processes that minimize environmental impact.
- Exceptional Customer Service: Providing comprehensive support from selection through to post-installation, ensuring optimal system performance.
Highlighting Features from the Omni Metalcraft Roller Catalog
The Omni Metalcraft roller catalog showcases features that set their mild steel conveyor rollers apart:
- Superior Load Capacity: Designed to handle heavy loads without compromise, ideal for industrial applications.
- Extended Lifespan: Manufactured to resist wear and tear, ensuring long-term reliability and reduced maintenance costs.
- Customizable Dimensions: Offering rollers in various sizes and lengths to fit specific conveyor systems and applications.
- Corrosion Resistance: Coated with protective materials that extend the life of the rollers in harsh environments.
- Precision Bearings: Equipped with high-quality bearings to ensure smooth operation and reduce noise levels.
Discussion on the Custom Solutions and Applications of Omni Rollers
Omni Metalcraft’s commitment to innovation is further demonstrated through their provision of custom solutions tailored to meet unique operational requirements. These include:
- Specialized Coating Options: For applications requiring additional friction or reduced material adhesion.
- Variable Roller Configurations: To accommodate different conveyor layouts and material handling strategies.
- Integrated Sensor Technology: For automated systems that require precise monitoring and control.
- High-Temperature Adaptations: Rollers designed to operate in extreme temperatures without degrading.
- Impact and Shock Resistance: Custom-engineered rollers that can withstand sudden forces, essential for dynamic environments.
Omni Metalcraft’s dedication to quality, combined with their ability to offer custom-engineered solutions, makes their mild steel conveyor rollers a preferred choice for businesses looking to enhance their material handling systems. With a focus on durability, functionality, and customer satisfaction, Omni Metalcraft continually sets the standard for excellence in the conveyor industry.
Selecting the Right Mild Steel Conveyor Roller
Choosing the appropriate mild steel conveyor roller is crucial for optimizing the efficiency and longevity of a conveyor system. The right selection ensures not only the smooth operation of the conveyor but also significant savings in maintenance and replacement costs over time. This decision must be informed by a thorough understanding of the application’s specific requirements and the operating environment.
Factors to Consider
When selecting a mild steel conveyor roller, several key factors need to be taken into account:
- Load: The weight and type of materials the conveyor will carry. Heavy-duty rollers are needed for bulk materials like metals or stones, while lighter loads may only require standard rollers.
- Environment: The conditions under which the conveyor will operate. Environments with high humidity or exposure to chemicals necessitate rollers with protective coatings to prevent corrosion.
- Speed: The operational speed of the conveyor. High-speed applications may require rollers with precision bearings to ensure smooth and efficient operation.
- Roller Diameter: The size of the roller affects the type of material it can convey efficiently. Large-diameter rollers are better suited for heavy or large materials, whereas smaller rollers are ideal for light or small items.
- Application Specifics: Special considerations such as the need for noise reduction in quiet environments, or impact resistance in areas where materials are dropped onto the conveyor, should influence the choice of roller.
Making an Informed Decision with a Conveyor Roller Catalog PDF
Utilizing a conveyor roller catalog PDF is a strategic step towards making an informed decision. These catalogs typically offer:
- Detailed Specifications: Including dimensions, load capacities, and material compositions, allowing for comparison against application requirements.
- Customization Options: Information on available modifications to accommodate unique environmental conditions or operational needs.
- Comparison Charts: Facilitating a side-by-side comparison of different roller models to evaluate which best meets the specific demands of your application.
- Installation and Maintenance Guidelines: Helping to anticipate the ease of integration into existing systems and future maintenance needs.
- Contact Information for Expert Advice: Providing an opportunity to consult with manufacturers or suppliers to gain insights or clarification on the best roller selection for your application.
By carefully considering the factors outlined and leveraging the comprehensive information available in a conveyor roller catalog PDF, businesses can ensure they select the right mild steel conveyor roller. This selection process is critical to achieving optimal performance, reliability, and efficiency in conveyor operations, ultimately contributing to the success and profitability of industrial and manufacturing processes.
Price and Availability of Mild Steel Conveyor Rollers
The price and availability of mild steel conveyor rollers are critical considerations for businesses seeking to enhance or maintain their conveyor systems. Understanding these factors can significantly impact the decision-making process, ensuring that operations remain both efficient and cost-effective.
General Pricing Insights
The cost of mild steel conveyor rollers can vary widely based on several factors including size, load capacity, and any custom features required. Generally, standard rollers are more affordably priced, making them a popular choice for businesses looking to balance quality with cost. However, for specialized applications or environments, custom rollers, though more expensive, provide necessary performance enhancements that justify their higher price point.
Tips on Finding the Best Deals
- Bulk Purchases: Buying in bulk often results in lower per-unit costs due to economies of scale. Suppliers may offer significant discounts for large orders.
- Comparative Shopping: Utilize online platforms and catalogs to compare prices from different suppliers. Price variations can be substantial.
- Seasonal Sales and Promotions: Keep an eye on industry suppliers for sales events or promotional offers, which can lead to considerable savings.
- Negotiate with Suppliers: Don’t hesitate to negotiate prices, especially for custom orders or bulk purchases. Suppliers are often willing to adjust pricing to secure a sale.
- Consider Refurbished or Used Rollers: For operations where the highest level of performance is not critical, refurbished or used rollers can provide a cost-effective alternative.
Availability and Lead Times for Custom Orders
The availability of mild steel conveyor rollers generally is good, with many suppliers keeping a ready stock of standard sizes for immediate delivery. However, for custom rollers designed to meet specific operational requirements, lead times can vary significantly. Factors influencing these times include the complexity of the design, the current workload of the manufacturer, and the availability of materials. To mitigate potential delays, it’s advisable to:
- Plan Ahead: Allow sufficient lead time for custom orders by planning your needs well in advance.
- Maintain Open Communication: Regularly communicate with your supplier about your order’s status and any potential delays to adjust your plans accordingly.
- Seek Expedited Options: Some suppliers offer expedited manufacturing services for an additional fee, which can be valuable when rollers are urgently needed.
The pricing dynamics and availability nuances of mild steel conveyor rollers is essential for making informed procurement decisions. By leveraging these insights, businesses can optimize their conveyor system investments, ensuring they achieve the best possible balance of performance, cost, and delivery timing.
Ask About Our Steel Conveyor Rollers Specifications.
Replacing and Maintaining Mild Steel Conveyor Rollers
Ensuring the longevity and optimal performance of a conveyor system involves regular maintenance and timely replacement of its components. Mild steel conveyor rollers, fundamental to the system’s operation, require specific attention to maintain their efficiency and to prevent unnecessary downtime.
Guidelines for Conveyor Roller Replacement
- Regular Inspections: Schedule regular inspections of the conveyor rollers to identify wear and tear or any potential issues that could lead to breakdowns.
- Listen for Noise: Unusual noises such as grinding or squeaking are often the first indicators that a roller may need replacement.
- Monitor Movement: Rollers that stick or do not turn freely can cause conveyor belts to slip or materials to be damaged and should be replaced.
- Check for Visible Damage: Physical damage to rollers, such as dents or cracks, can impair functionality and should prompt immediate replacement.
- Adhere to Manufacturer’s Recommendations: Follow the manufacturer’s guidelines for maintenance and replacement intervals to ensure optimal performance and longevity.
Maintenance Tips to Extend the Lifespan of Mild Steel Rollers
- Lubrication: Regularly lubricate bearings according to the manufacturer’s specifications to ensure smooth operation and to prevent wear.
- Cleanliness: Keep the rollers and conveyor environment clean from dust, debris, and corrosive materials that can damage the roller surface and its components.
- Alignment Checks: Ensure that the conveyor system is correctly aligned. Misalignment can cause uneven wear and tear on rollers, leading to premature failure.
- Load Distribution: Avoid overloading the conveyor system. Ensure that loads are evenly distributed across the rollers to prevent excessive stress on individual rollers.
- Rust Prevention: Apply protective coatings or treatments to mild steel rollers in environments prone to moisture or chemicals to prevent rust and corrosion.
Implementing these maintenance strategies and adhering to a regular replacement schedule can significantly enhance the efficiency and lifespan of mild steel conveyor rollers. By taking proactive steps to maintain and replace rollers when necessary, businesses can minimize downtime, reduce repair costs, and maintain a high level of productivity in their operations.
FAQs About Mild Steel Conveyor Roller
The selection of rollers for a conveyor belt depends largely on the application, including the weight of materials being transported, the environment in which the conveyor operates, and the speed at which the conveyor must run. Typically, rollers are made from materials such as mild steel, stainless steel, PVC, and even aluminum to meet various operational needs. Mild steel rollers, for instance, are prized for their durability and cost-effectiveness, making them suitable for heavy-duty applications. In environments where corrosion resistance is paramount, stainless steel or PVC rollers might be preferred. The choice of roller is critical for ensuring the smooth and efficient operation of a conveyor system, influencing both its performance and longevity. It’s essential to consider the specific requirements of your conveyor system before making a selection, including factors such as load capacity, environmental conditions, and the nature of the materials being conveyed.
Mild steel is commonly used for manufacturing conveyor rollers due to its excellent balance of strength, flexibility, and cost. This type of steel is capable of handling significant stress and weight, making it ideal for industrial applications where robustness and reliability are paramount. For environments that require a higher degree of corrosion resistance, stainless steel rollers are often employed. Stainless steel offers the added benefits of being able to withstand harsh chemicals and moisture, making it suitable for food processing, pharmaceutical, and outdoor applications. The choice between mild steel and stainless steel rollers hinges on the specific needs of the conveyor system, including budgetary constraints and environmental conditions.
Conveyor rollers can be made from a variety of materials, each chosen for its unique properties and suitability for different applications. Mild steel and stainless steel are among the most common due to their durability and, in the case of stainless steel, corrosion resistance. PVC and other plastics are also used, especially in applications requiring lightweight rollers or those that operate in environments where corrosion resistance is a priority without the need for the strength of steel. In some cases, aluminum rollers are utilized for their lightweight and corrosion-resistant properties, albeit in less demanding applications. The choice of material impacts the conveyor system’s overall performance, maintenance needs, and longevity.
Roller conveyors can be categorized into several types based on their mechanism of operation and the materials they are designed to handle. The primary types include gravity roller conveyors, powered roller conveyors, and grooved roller conveyors. Gravity roller conveyors rely on the force of gravity to move items across the rollers and are best suited for light to medium loads. Powered roller conveyors use motors to move materials, making them ideal for heavy loads and controlled movement over long distances. Grooved roller conveyors have rollers with grooves that are matched with belts or chains to drive the rollers and are used when precise movement or positioning of items is required. Each type of roller conveyor has its unique advantages and is selected based on the specific needs of the application, including the weight of the items being moved, the desired speed of transport, and the level of control required over the movement of items.
Last Updated on July 12, 2024 by Jordan Smith
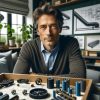
Jordan Smith, a seasoned professional with over 20 years of experience in the conveyor system industry. Jordan’s expertise lies in providing comprehensive solutions for conveyor rollers, belts, and accessories, catering to a wide range of industrial needs. From initial design and configuration to installation and meticulous troubleshooting, Jordan is adept at handling all aspects of conveyor system management. Whether you’re looking to upgrade your production line with efficient conveyor belts, require custom conveyor rollers for specific operations, or need expert advice on selecting the right conveyor accessories for your facility, Jordan is your reliable consultant. For any inquiries or assistance with conveyor system optimization, Jordan is available to share his wealth of knowledge and experience. Feel free to reach out at any time for professional guidance on all matters related to conveyor rollers, belts, and accessories.