The Ultimate Guide to Rubber Conveyor Belt Material Selection
In the realm of industrial operations, the importance of efficient and reliable material handling systems cannot be overstated. At the heart of these systems, rubber conveyor belts play a pivotal role, bridging the gap between productivity and functionality across various sectors. From mining to manufacturing, the use of rubber conveyor belt material is synonymous with strength, durability, and versatility. This material, chosen for its unparalleled ability to withstand harsh conditions while maintaining flexibility and resistance to wear, is fundamental to the seamless operation of conveyor systems worldwide. As we delve deeper into the nuances of rubber as the material of choice for conveyor belts, it becomes evident that its selection is not merely a matter of preference but a critical decision that impacts the overall efficiency and cost-effectiveness of industrial operations. This introduction serves as a gateway to understanding why rubber conveyor belt material stands out in the vast market of industrial conveyance solutions, highlighting its pivotal role in a myriad of applications.
What is Rubber Conveyor Belt Material
Rubber conveyor belt material stands as a cornerstone in the domain of industrial conveyance systems, attributed to its exceptional properties and versatility. This section delves into the core attributes of rubber as a material for conveyor belts and explores the diversity of types available to meet various operational demands.
Material Properties
The efficacy of rubber conveyor belt material in myriad applications is underpinned by several key properties, making it an ideal choice for conveyor belts:
- Durability: Rubber’s inherent strength and resilience contribute to the longevity of conveyor belts, even under continuous operation.
- Flexibility: This property ensures that the belts can navigate through curves and inclines with ease, without compromising the integrity of the transported materials.
- Resistance to Abrasion: Rubber conveyor belts withstand wear and tear from abrasive materials, maintaining performance over time.
- Impact Resistance: They absorb shocks and impacts from heavy loads, preventing damage to both the belt and the materials being conveyed.
- Chemical Resistance: Rubber belts can resist various chemicals, making them suitable for use in environments exposed to oils, fats, and other substances.
- Temperature Tolerance: They perform across a wide range of temperatures, from the cold conditions of refrigerated environments to the high heat of industrial ovens.
- Customizability: The rubber conveyor belt material can be tailored in terms of thickness, width, and surface texture to meet specific operational requirements, enhancing its utility across industries.
These properties collectively ensure that rubber conveyor belts are a reliable and efficient choice for transporting materials across various distances and conditions, exemplifying their indispensable role in industrial settings.
Types of Rubber Conveyor Belts
The diversity in rubber conveyor belt material types caters to the specific needs of different industries, ranging from general-purpose applications to those requiring specialized properties for extreme conditions. The following table presents an overview of the common types of rubber conveyor belts:
This classification into general-purpose, heavy-duty, and specialty belts underscores the adaptability of rubber conveyor belt material to a broad spectrum of industrial applications. By selecting the appropriate type of belt, businesses can optimize the efficiency, safety, and cost-effectiveness of their material handling operations.
Rubber Conveyor Belt Material
Composition of Rubber Conveyor Belts
Rubber conveyor belts are integral components in a variety of industries, from mining and manufacturing to food processing and logistics. The effectiveness, durability, and longevity of these belts depend significantly on their composition. Understanding the rubber conveyor belt material is essential for selecting the right belt for specific applications and ensuring optimal performance.
Detailed Look at the Materials Used in Rubber Conveyor Belts
The primary material used in rubber conveyor belts is, as the name suggests, rubber. However, the rubber used in these belts is not just any ordinary rubber. It is typically a blend of natural rubber (NR) and synthetic rubber (SR) compounds. This combination is engineered to provide the necessary properties such as flexibility, tensile strength, and resistance to wear and tear.
Natural rubber, derived from the latex of rubber trees, is valued for its excellent elasticity and resilience. It provides the conveyor belts with flexibility, allowing them to bend and flex without cracking or breaking. This is particularly important in applications where the belts must navigate complex paths or handle varying loads.
Synthetic rubber, on the other hand, is manufactured through chemical processes that allow for the creation of rubber with specific properties tailored to different industrial needs. Common types of synthetic rubber used in conveyor belts include butadiene rubber (BR) and styrene-butadiene rubber (SBR). Butadiene rubber is known for its high resistance to abrasion and low temperatures, making it ideal for belts used in harsh environments. Styrene-butadiene rubber, meanwhile, offers a good balance of durability, flexibility, and cost-effectiveness.
In addition to the rubber compounds, other materials are integrated into the conveyor belt to enhance its performance and durability. One of the most critical components is the reinforcement layer, which provides the belt with additional strength and stability.
Explanation of How Fabric Layers and Steel Cables Are Integrated into the Rubber
The reinforcement layers in rubber conveyor belts are typically made from fabric or steel cables, each offering distinct advantages depending on the application requirements.
Fabric Layers:
Fabric layers, also known as carcass or ply, are commonly used in rubber conveyor belts to provide strength and flexibility. These fabric layers are usually made from polyester, nylon, or a combination of both (known as EP fabric). Polyester provides excellent tensile strength and resistance to stretching, while nylon offers high flexibility and shock absorption. The combination of these materials ensures that the conveyor belt can withstand the mechanical stresses of continuous operation.
The fabric layers are embedded within the rubber through a process called vulcanization. During vulcanization, the rubber compounds and fabric layers are subjected to heat and pressure, causing them to bond together. This process not only secures the fabric within the rubber but also enhances the overall durability and performance of the belt. The number of fabric layers, or plies, can vary depending on the belt’s intended use, with more plies providing greater strength for heavy-duty applications.
Steel Cables:
For applications that require even greater strength and durability, steel cables are used as the reinforcement material in rubber conveyor belts. These steel cable belts are known as steel cord belts and are particularly suited for heavy-duty applications such as mining, where the belts must carry large loads over long distances.
Steel cords are embedded within the rubber using a similar vulcanization process. The cords are arranged parallel to each other and are encased in the rubber matrix, providing the belt with exceptional tensile strength and resistance to elongation. This configuration allows the belt to handle high-tension loads without stretching, ensuring efficient and reliable operation even under extreme conditions.
The integration of steel cables into the rubber conveyor belt material enhances its overall strength, stability, and resistance to impact and puncture. This makes steel cord belts ideal for applications where the belt is subjected to heavy loads, sharp materials, and demanding operational environments.
In addition to the primary materials of rubber, fabric, and steel, various additives and treatments are used to further enhance the properties of the conveyor belts. For instance, anti-abrasion and anti-chemical treatments can be applied to the rubber surface to protect the belt from wear and damage caused by abrasive materials or harsh chemicals. Heat-resistant treatments are also available for belts used in high-temperature environments, ensuring the rubber maintains its integrity and performance.
The composition of rubber conveyor belt material is a carefully engineered balance of rubber compounds, reinforcement layers, and specialized treatments. This combination ensures that the conveyor belts provide the necessary strength, flexibility, and durability required for their specific industrial applications. By understanding the materials and processes involved in their manufacture, users can select the right conveyor belts for their needs, ensuring optimal performance and longevity.
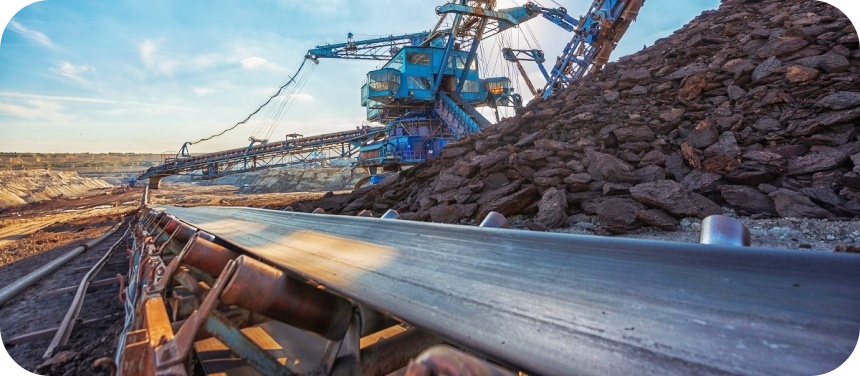
Choosing the Right Rubber Conveyor Belt Material
Selecting the optimal rubber conveyor belt material is pivotal for ensuring operational efficiency, safety, and longevity of the conveyor system. This decision hinges on a thorough understanding of the specific application requirements and the unique properties of rubber materials. Below, we delve into the critical considerations for choosing the right rubber conveyor belt material.
Material Selection
When it comes to choosing the right rubber conveyor belt material, several application-specific factors must be considered to ensure the belt’s performance and durability:
- Temperature Exposure: Assess whether the belt will operate in extreme temperatures, requiring heat-resistant or cold-resistant rubber.
- Chemical Exposure: Determine if the conveyor belt will come into contact with oils, chemicals, or solvents, necessitating a rubber compound resistant to these substances.
- Abrasion and Wear: Evaluate the level of abrasion the belt will endure to select a material that offers superior wear resistance.
- Load Type and Weight: Consider the weight and nature of the materials to be transported to ensure the belt material can withstand the load without deforming or breaking.
- Conveyor Speed and Distance: Factor in the operational speed and the distance materials will travel, as this can influence the required strength and flexibility of the belt.
- Environmental Conditions: Account for the presence of UV light, ozone, humidity, and other environmental factors that could degrade certain rubber materials.
- Safety Requirements: Identify any fire or explosion risks in the environment to choose a belt material with appropriate fire-resistant properties.
- Regulatory Compliance: Ensure the rubber conveyor belt material complies with industry-specific regulations, especially for food processing or pharmaceutical applications.
- Maintenance and Replacement: Consider the ease of maintenance and the availability of replacement belts, opting for materials that offer a balance between longevity and cost-effectiveness.
- Cost: While not a material property, the cost of the rubber material is an important consideration, balancing initial investment against performance and lifespan.
Conveyor Belt Material Properties
Understanding the physical and chemical properties of rubber materials is crucial for selecting a conveyor belt that meets the demands of specific applications:
- Tensile Strength: The ability of the belt to withstand tension without elongating or breaking.
- Elasticity: The material’s capacity to return to its original shape after being stretched, ensuring flexibility over pulleys and rollers.
- Abrasion Resistance: Resistance to surface wear from rough materials, critical for belts handling abrasive substances.
- Thermal Stability: The ability to maintain properties over a wide temperature range, from extreme cold to high heat environments.
- Chemical Resistance: The capacity to resist degradation when exposed to oils, fats, solvents, and other chemicals.
- Impact Resistance: The ability to absorb shocks and impacts from heavy or sharp objects without sustaining damage.
- Fire Resistance: Important for belts used in environments where there is a risk of fire or explosion.
- Electrical Properties: Some applications may require belts with anti-static properties to prevent the build-up of static electricity.
Specifications and Standards
Rubber conveyor belts must adhere to specific specifications and standards to ensure safety, reliability, and compatibility with various industrial applications:
- Dimensions: Width, thickness, and length specifications to fit the conveyor system.
- Tensile Strength: Minimum required strength to withstand operational loads.
- Elongation at Break: Indicates the elasticity and flexibility of the belt material.
- Abrasion Resistance: Measured to ensure the belt can resist wear over time.
- Thermal Resistance: Specifies the temperature range the belt is designed to operate within.
- Chemical Compatibility: Lists the chemicals the belt material can resist.
- Fire and Safety Standards: Compliance with local and international safety regulations for fire resistance.
- Quality Certifications: ISO and other quality standards that the rubber conveyor belt material must meet, ensuring consistent performance and durability.
By meticulously considering these aspects of rubber conveyor belt material selection, industries can optimize their conveyor systems for performance, safety, and cost-efficiency, thereby enhancing their overall operational effectiveness.
What is Rubber Conveyor Belt Material
Rubber Conveyor Belt: Properties and Benefits
Rubber conveyor belts are widely used across various industries due to their exceptional properties and numerous benefits. The rubber conveyor belt material is designed to meet the rigorous demands of different applications, ensuring efficiency, reliability, and longevity. Understanding the key properties and benefits of rubber as a conveyor belt material is essential for selecting the right belt for specific industrial needs.
Key Properties That Make Rubber an Ideal Material for Conveyor Belts
Rubber, both natural and synthetic, possesses several inherent properties that make it an ideal material for manufacturing conveyor belts. These properties include elasticity, tensile strength, abrasion resistance, and temperature stability.
Elasticity:
One of the most significant properties of rubber is its elasticity. Elasticity allows rubber conveyor belts to flex and bend without breaking, which is crucial for navigating the various contours and curves of a conveyor system. This property also helps in absorbing shock loads, reducing the risk of damage to the belt and the materials being transported.
Tensile Strength:
Rubber conveyor belt material is known for its high tensile strength, which enables it to withstand heavy loads and high-tension conditions. Tensile strength is particularly important in applications where the belt is subjected to significant stress and strain. The incorporation of reinforcement materials such as fabric or steel cords further enhances the tensile strength of rubber conveyor belts, making them suitable for heavy-duty applications.
Abrasion Resistance:
Conveyor belts often encounter abrasive materials that can wear down the surface over time. Rubber has excellent abrasion-resistant properties, which means it can withstand the wear and tear caused by friction and abrasive materials. This property ensures that rubber conveyor belts maintain their integrity and performance even in harsh operating environments.
Temperature Stability:
Rubber conveyor belts are designed to perform reliably across a wide range of temperatures. Whether in freezing conditions or high-heat environments, rubber maintains its flexibility and strength. Specific rubber compounds can be formulated to enhance heat resistance or cold tolerance, ensuring the belt performs optimally in various temperature extremes.
Chemical Resistance:
In industries where the conveyor belts are exposed to chemicals, oils, and other corrosive substances, rubber provides excellent resistance. The chemical-resistant properties of rubber ensure that the belts do not degrade or lose their structural integrity when exposed to harsh chemicals. This is particularly important in industries such as chemical processing, food production, and mining.
Benefits Such as Durability, Flexibility, and Resistance to Various Environmental Factors
The properties of rubber conveyor belt material translate into several tangible benefits, making these belts a preferred choice for many industrial applications. The key benefits include durability, flexibility, and resistance to various environmental factors.
Durability:
Durability is one of the primary reasons why rubber is chosen as the material for conveyor belts. The combination of elasticity, tensile strength, and abrasion resistance ensures that rubber conveyor belts can withstand prolonged use without significant wear or failure. This durability reduces the frequency of belt replacements and maintenance, leading to lower operational costs and increased productivity.
Flexibility:
The flexibility of rubber conveyor belts is crucial for their operation in complex conveyor systems. Flexible belts can easily navigate through curves, inclines, and declines, ensuring smooth and continuous material flow. This flexibility also allows for easier installation and adjustments, making rubber conveyor belts suitable for a wide range of conveyor configurations.
Resistance to Environmental Factors:
Rubber conveyor belts are designed to resist various environmental factors that can affect their performance. These factors include extreme temperatures, moisture, chemicals, and UV radiation.
Temperature Resistance:
As mentioned earlier, rubber conveyor belts can perform effectively in both high and low temperatures. This temperature resistance ensures that the belts remain functional and reliable, regardless of the operating environment. For instance, heat-resistant rubber belts are used in industries such as foundries and glass manufacturing, where high temperatures are prevalent.
Moisture Resistance:
Rubber’s inherent resistance to moisture makes it ideal for use in wet or humid environments. This property prevents the belt from absorbing water, which can lead to swelling, degradation, and loss of strength. Industries such as food processing and agriculture benefit from the moisture-resistant properties of rubber conveyor belts.
Chemical Resistance:
The ability of rubber to resist chemicals and oils ensures that the conveyor belts can operate in environments where exposure to corrosive substances is common. This resistance protects the belts from chemical damage, extending their lifespan and maintaining their performance. Industries such as chemical processing, oil and gas, and mining often require conveyor belts with high chemical resistance.
UV Radiation Resistance:
Rubber conveyor belts are also resistant to UV radiation, which can cause degradation and brittleness in some materials. This resistance is particularly important for outdoor conveyor systems that are exposed to sunlight. UV-resistant rubber belts ensure long-term durability and reliability in such applications.
Rubber Conveyor Belt Manufacturers and Suppliers
The industry of rubber conveyor belt material is vast and varied, with manufacturers and suppliers around the globe striving to meet the diverse needs of various sectors. These key players in the market differentiate themselves through their product offerings, commitment to innovation, and the level of customer service they provide. Understanding what sets these manufacturers apart can help businesses make informed decisions when selecting the right rubber conveyor belt material for their specific requirements.
Key Manufacturers
The landscape of manufacturers specializing in rubber conveyor belt material is marked by a blend of well-established companies and innovative newcomers. Each brings its own strengths to the table, from extensive product ranges designed to suit every conceivable application, to cutting-edge technologies that push the boundaries of what conveyor belts can achieve. Here’s a closer look at what distinguishes these key manufacturers:
- Extensive Product Range: Leading manufacturers boast an expansive selection of rubber conveyor belts, ensuring a fit for every application, whether it’s in mining, agriculture, manufacturing, or logistics. This range includes everything from general-purpose belts to highly specialized ones, such as heat-resistant, oil-resistant, and fire-retardant belts.
- Innovation: At the forefront of the industry are those manufacturers who invest heavily in research and development to produce the next generation of rubber conveyor belt materials. These innovations may include new rubber compounds that offer improved durability and environmental resistance, belts designed for ultra-high efficiency, or smart conveyor belts embedded with sensors and IoT technology for real-time monitoring and diagnostics.
- Customer Service: Exceptional customer service sets apart the leaders in the rubber conveyor belt material market. This encompasses not only responsive sales and support teams but also comprehensive services such as on-site consultations, custom belt design, installation assistance, and after-sales support. The best manufacturers understand that their relationship with clients extends far beyond the initial purchase, offering ongoing advice and technical support to ensure their conveyor systems operate smoothly.
- Global Presence: Manufacturers with a global footprint are able to serve customers around the world more effectively, ensuring fast delivery times, local support, and the ability to meet a wide range of international standards and regulations. This global network also facilitates a broader understanding of industry trends and requirements, enabling these manufacturers to stay ahead of the curve.
- Sustainability: An increasing number of manufacturers are focusing on sustainability, recognizing the importance of environmentally responsible practices within the industry. This includes the development of rubber conveyor belt materials that are more eco-friendly, both in terms of the raw materials used and the manufacturing processes employed, as well as recycling programs for used belts.
By prioritizing these areas, the key manufacturers of rubber conveyor belt material are not just supplying products; they are providing comprehensive solutions that support the operational success of their clients across a broad spectrum of industries. Their commitment to quality, innovation, and customer service ensures that businesses have access to the best possible conveyor belt solutions, tailored to meet their unique challenges and objectives.
Supplier Selection
Choosing the right supplier for rubber conveyor belt material is critical to the success of your operations. Here are 12 tips to guide you in making an informed decision:
- Quality Assurance: Ensure the supplier has stringent quality control measures in place, with certifications to back them up.
- Material Variety: Look for suppliers offering a wide range of materials to suit different industrial applications.
- Customization Options: The ability to customize products to specific dimensions and properties is crucial for meeting unique operational requirements.
- Technical Support: A supplier should offer comprehensive technical support, from selection to maintenance advice.
- Cost-Effectiveness: Compare pricing, but also consider the long-term value in terms of durability and maintenance needs.
- Lead Times: Shorter lead times can be crucial for maintaining operational efficiency and reducing downtime.
- Reputation: Research the supplier’s reputation in the industry, through reviews, testimonials, and case studies.
- Innovation: Suppliers who invest in research and development can offer the latest in rubber conveyor belt technology.
- Regulatory Compliance: Verify that the supplier’s products comply with all relevant safety and environmental regulations.
- After-Sales Service: Look for suppliers who provide excellent after-sales service, including returns, repairs, and replacements.
- Global Reach: For businesses operating internationally, a supplier with a global distribution network is essential.
- Environmental Practices: Consider the supplier’s commitment to sustainability and eco-friendly manufacturing processes.
Selecting the right supplier for rubber conveyor belt material is a strategic decision that impacts every aspect of your operation’s efficiency, safety, and profitability. By considering these factors, businesses can establish a productive partnership with their rubber conveyor belt supplier, ensuring a steady supply of high-quality materials tailored to their specific needs.
Cost Considerations for Rubber Conveyor Belt Material
When planning to invest in rubber conveyor belt material, understanding the various factors that influence the price and weighing the pros and cons of new versus used materials are essential steps. This approach ensures that you get the best value for your investment while meeting your specific operational requirements.
Pricing Factors
The cost of rubber conveyor belt material is not uniform; it varies significantly based on several key factors. Recognizing these can help in making informed purchasing decisions:
- Material Thickness: Thicker belts, offering more durability and longevity, typically command higher prices.
- Belt Size: Larger belts, both in terms of length and width, require more material to manufacture, leading to higher costs.
- Special Features: Belts with specialized properties, such as heat resistance, oil resistance, or flame retardancy, often come at a premium due to the additional processing and materials required.
- Quality of Rubber: High-grade rubber materials with superior wear and tear resistance are more expensive but offer better performance and longevity.
- Customization: Customized belts designed to meet specific operational requirements can increase the price due to the additional design and manufacturing effort.
- Market Demand and Availability: The price of rubber conveyor belt material can also be influenced by market dynamics, including demand, availability of raw materials, and economic conditions.
Understanding these factors provides a clearer picture of how rubber conveyor belt material prices are determined and helps in budgeting for procurement.
Used Conveyor Belt Rubber
Purchasing used conveyor belt rubber can be an attractive option for many businesses, offering several benefits but also presenting potential drawbacks:
Benefits:
- Cost Savings: The most apparent advantage is the significant reduction in cost compared to purchasing new materials.
- Environmental Impact: Reusing conveyor belt material contributes to environmental sustainability by reducing waste.
- Immediate Availability: Used belts are often available for immediate delivery, eliminating manufacturing wait times.
- Proven Performance: Used belts have a track record of performance in real-world conditions.
- Flexibility in Quantity: It may be easier to purchase small quantities of used material for minor projects or repairs.
- Test Materials: An economical way to test different materials and configurations before committing to a new purchase.
- Unique Applications: Used belts can be ideal for non-standard applications where the highest quality is not necessary.
Drawbacks:
- Wear and Tear: The condition of used belts may vary, and they may not offer the same lifespan as new materials.
- Limited Selection: Specific sizes, types, and qualities of belts might be hard to find in the used market.
- Lack of Warranty: Used belts typically come without the warranties or guarantees offered with new products.
- Potential for Hidden Damage: There may be internal damage not immediately apparent, affecting performance.
- Maintenance Costs: Increased maintenance or more frequent replacements may offset initial cost savings.
- Safety Concerns: Worn or damaged belts could pose safety risks in certain applications.
- Environmental Regulations: There may be restrictions on the reuse of certain materials in some jurisdictions.
Considering the benefits and drawbacks of used rubber conveyor belt material is crucial for businesses aiming to balance cost savings with operational efficiency and safety. Making an informed choice involves assessing the specific needs of your operation, potential cost implications over the belt’s lifetime, and any safety or regulatory concerns.
Applications of Rubber Conveyor Belts
The versatility and durability of rubber conveyor belt material make it an ideal choice for a wide range of industrial applications. Rubber conveyor belts are found in numerous industries, including mining, manufacturing, and logistics, due to their ability to withstand harsh conditions, heavy loads, and continuous use. This section will explore common industries and applications where rubber conveyor belts are used, providing specific examples of their implementation.
Common Industries and Applications Where Rubber Conveyor Belts Are Used
Rubber conveyor belts are a critical component in many industries, providing efficient and reliable material handling solutions. Here are some of the most common industries that utilize rubber conveyor belts:
Mining
In the mining industry, rubber conveyor belts are indispensable for transporting extracted materials such as ores, coal, and aggregates. The robust nature of rubber belts makes them suitable for the demanding conditions of mining operations, where they must endure heavy loads, sharp materials, and continuous use.
- Open-Pit Mining: Rubber belts are used to transport raw materials from the mining site to processing facilities. These belts must be able to handle large volumes of heavy, abrasive materials over long distances.
- Underground Mining: Conveyor belts in underground mines need to be flame-resistant and durable. Rubber belts are designed to meet these safety standards while providing reliable transport in confined spaces.
Manufacturing
The manufacturing industry relies heavily on conveyor systems to streamline production processes. Rubber conveyor belts are used in various stages of manufacturing, from transporting raw materials to moving finished products.
- Automotive Manufacturing: In automotive plants, rubber conveyor belts are used to transport car parts and assemblies along production lines. These belts must be durable and able to withstand the weight and complexity of automotive components.
- Food and Beverage: In food processing plants, rubber conveyor belts are essential for moving raw ingredients, packaging, and finished products. The belts used in these environments need to be food-grade, resistant to oils and chemicals, and easy to clean.
Logistics and Distribution
In the logistics and distribution industry, the efficiency of material handling systems is crucial for the timely delivery of goods. Rubber conveyor belts are used extensively in warehouses, distribution centers, and airports to handle a variety of packages and products.
- Warehousing: Rubber belts are used in automated sorting systems to transport packages to the correct location. These belts must be reliable and capable of handling a wide range of weights and sizes.
- Airports: Baggage handling systems in airports rely on rubber conveyor belts to move luggage from check-in counters to loading areas and from planes to baggage claim areas. The belts need to be durable, safe, and efficient to manage high volumes of luggage.
Examples of How Rubber Belts Are Implemented in Mining, Manufacturing, and Logistics
The use of rubber conveyor belt material can be seen in several specific applications within these industries, highlighting its versatility and effectiveness.
Mining
- Material Transport: In open-pit mining operations, rubber conveyor belts transport bulk materials like iron ore and coal from the extraction site to processing plants. These belts are designed to handle the rough and abrasive nature of mined materials while providing reliable and efficient transport over long distances.
- Processing Plants: Rubber belts are used in crushing and screening plants to move crushed materials to different stages of processing. The belts need to be tough enough to withstand the impact of heavy rocks and the abrasive action of crushed materials.
Manufacturing
- Assembly Lines: In automotive manufacturing, rubber conveyor belts move car bodies and parts along assembly lines. These belts need to provide precise movement and support the weight of large components, ensuring efficient and smooth production processes.
- Food Processing: Rubber belts are used in food processing plants to transport ingredients like grains, fruits, and vegetables through various stages of processing. The belts must be resistant to oils, fats, and cleaning chemicals to maintain hygiene standards and ensure the safe handling of food products.
Logistics and Distribution
- Automated Warehousing Systems: In modern warehouses, rubber conveyor belts are integral to automated storage and retrieval systems (AS/RS). These belts move goods through different zones for sorting, packing, and shipping, ensuring efficient and accurate order fulfillment.
- Baggage Handling: At airports, rubber conveyor belts are used in baggage handling systems to move luggage from check-in to loading areas and from planes to baggage claim. These belts must be durable and capable of handling high volumes of luggage while minimizing the risk of damage to passengers’ belongings.
Learn how our belts can improve your productivity.
FAQs about Rubber Conveyor Belt Material
Rubber conveyor belts are primarily composed of several layers, each serving a specific function to enhance the belt’s performance and durability. The core of these belts is typically made from fabric or steel cord, providing the necessary strength and structural integrity to handle various loads. The fabric used can be made from materials such as polyester, nylon, or cotton, offering different levels of flexibility and tension resistance. The steel cords are used for added strength in heavy-duty applications, where high tensile strength is a must.
The outer layers of rubber conveyor belts are made from a blend of natural and synthetic rubbers. Natural rubber provides excellent flexibility and tensile strength, while synthetic rubbers such as neoprene, nitrile, and styrene-butadiene rubber (SBR) are added for their resistance to abrasions, impacts, chemicals, and temperature variations. This combination ensures the conveyor belt can withstand harsh operational conditions, including exposure to oils, chemicals, and extreme temperatures, while maintaining its elasticity and structural integrity over time. Additives may also be included in the rubber compound to enhance specific properties like fire resistance or static electricity dissipation, making the belts suitable for a wide range of industrial applications.
The material found on the surface of a conveyor belt varies depending on its intended application but generally includes some form of rubber compound. This rubber may be blended with other materials to enhance specific properties. For example, belts used in the food industry might incorporate materials that are FDA approved for contact with food, while belts used in mining or construction might be made from highly durable and abrasion-resistant rubbers.
Moreover, the surface material of a conveyor belt can be engineered to provide certain functionalities such as increased grip, low friction, or resistance to heat and chemicals. This customization is achieved through the addition of textures, patterns, or the incorporation of specialized compounds into the rubber blend, allowing the conveyor belt to be precisely tailored to the needs of each application.
The manufacturing process of rubber conveyor belts involves several key steps, starting with the creation of the belt’s core or carcass, which provides the structural foundation. This core is made by layering and bonding fabric or steel cords together, depending on the belt’s intended use. For fabric belts, layers of woven fabrics like polyester, nylon, or cotton are stacked and bonded. For steel cord belts, longitudinal steel cords are embedded in rubber to form the core.
Next, the rubber compound is prepared by mixing natural and synthetic rubber with various chemicals and additives to achieve the desired properties, such as resistance to abrasion, chemicals, and temperature. This rubber mixture is then applied to the carcass in a process known as calendaring, where the rubber is pressed into thin sheets and layered onto the carcass under heat and pressure to ensure strong adhesion.
After calendaring, the belt undergoes vulcanization—a chemical process that involves heating the rubber to initiate a reaction that cross-links the rubber molecules, resulting in increased strength, elasticity, and resistance to wear. The vulcanization process can be done in a press or through a continuous vulcanization method, depending on the size and type of the belt being produced.
Finally, the finished conveyor belt is inspected for quality and tested to ensure it meets the required specifications and performance standards. Once approved, it’s rolled, packed, and shipped to customers. This manufacturing process allows for the production of rubber conveyor belts that are tailored to meet specific operational needs, providing a reliable and efficient means of material transport across various industries.
The composition of a conveyor belt can vary widely based on its intended use, but most are constructed from a combination of several basic components. At its core, the conveyor belt consists of a carcass that provides the structural strength and shape. This carcass is typically made from layers of fabric or steel cords. Fabric layers can include materials such as polyester, nylon, or cotton, each offering unique properties in terms of flexibility, strength, and cost. Steel cords are used for added strength and are essential in heavy-duty applications where high tensile forces are expected.
The carcass is then covered with rubber layers that protect the belt from environmental conditions, wear, and tear. These rubber layers are made from a mix of natural and synthetic rubber compounds, including neoprene, nitrile, and styrene-butadiene rubber (SBR), chosen for their resistance to abrasions, impacts, chemicals, and temperature fluctuations. The specific composition of the rubber compound is tailored to meet the operational demands of the conveyor belt, with additives included to enhance properties like fire resistance or to reduce static build-up.
In summary, the composition of a conveyor belt is a carefully engineered combination of materials designed to offer the optimal balance of strength, flexibility, and durability required for its specific application. This allows conveyor belts to function reliably under a wide range of conditions, supporting industries worldwide in the efficient and effective transport of materials.
Last Updated on July 12, 2024 by Jordan Smith
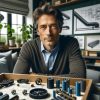
Jordan Smith, a seasoned professional with over 20 years of experience in the conveyor system industry. Jordan’s expertise lies in providing comprehensive solutions for conveyor rollers, belts, and accessories, catering to a wide range of industrial needs. From initial design and configuration to installation and meticulous troubleshooting, Jordan is adept at handling all aspects of conveyor system management. Whether you’re looking to upgrade your production line with efficient conveyor belts, require custom conveyor rollers for specific operations, or need expert advice on selecting the right conveyor accessories for your facility, Jordan is your reliable consultant. For any inquiries or assistance with conveyor system optimization, Jordan is available to share his wealth of knowledge and experience. Feel free to reach out at any time for professional guidance on all matters related to conveyor rollers, belts, and accessories.