Selecting Your Ideal Snub Roller Solution
In the intricate world of conveyor systems, every component plays a pivotal role in ensuring smooth, efficient operations. Among these, the snub roller stands out for its critical function in maintaining the system’s heartbeat. Positioned strategically within the conveyor structure, the snub roller is not just another wheel; it is a key player in managing the belt’s tension and alignment. By adjusting the belt’s contact angle with the drive pulley, snub rollers ensure that the belt is tight enough to avoid slippage but not so tight that it causes excessive wear or energy loss. Their role is especially vital in long conveyor systems where the risk of belt misalignment and slackness is higher. Understanding the significance of snub rollers in conveyor systems illuminates the engineering precision behind these seemingly simple mechanisms, highlighting their importance in keeping conveyor belts running smoothly and efficiently.
Snub Rollers and Their Functions
In the realm of conveyor systems, the snub roller plays a pivotal role, often working quietly yet significantly to ensure the system operates smoothly and efficiently. A snub roller, by definition, is a specialized roller designed to increase the amount of traction between the conveyor belt and the drive rollers. This enhancement is not just a matter of efficiency but also of extending the life of the conveyor belt and the system as a whole. Let’s delve deeper into the essential functions of the snub roller and how it integrates with other components of the conveyor system for optimal performance.
Definition and Functions of a Snub Roller
At its core, the snub roller is a crucial component positioned strategically to maintain or increase the arc of contact between the conveyor belt and the drive pulley. This functionality is vital for several reasons, encapsulating the snub roller’s seven primary functions:
- Increasing Traction: The primary function of a snub roller is to enhance the grip between the conveyor belt and the drive rollers, thereby preventing slippage and ensuring efficient transfer of power.
- Reducing Belt Tension: By increasing the arc of contact, snub rollers effectively distribute tension across a broader section of the belt, reducing stress and prolonging the belt’s lifespan.
- Enhancing Belt Alignment: Snub rollers play a part in guiding and aligning the conveyor belt, ensuring it runs smoothly along the conveyor’s path without drifting.
- Supporting Load Distribution: They help in evenly distributing the load across the belt, which is critical for the stable transportation of goods.
- Minimizing Wear and Tear: By preventing slippage and reducing tension, snub rollers contribute to the decreased wear and tear of the belt, leading to reduced maintenance costs and downtime.
- Improving Efficiency: Through their role in enhancing traction and reducing energy loss, snub rollers indirectly contribute to the overall efficiency of the conveyor system.
- Facilitating Speed Adjustments: By modifying the pressure applied by snub rollers, the conveyor system can adapt to varying speeds necessary for different phases of operation or types of materials being transported.
Integration with Conveyor System Components
Snub rollers do not work in isolation; their performance is closely linked with other critical components of the conveyor system, such as idler rollers, deflector pulleys, and take-up pulleys. Here’s how they work together:
- Alongside Idler Rollers: While idler rollers support the conveyor belt’s weight and its load, conveyor belt support rollers, also known as snub rollers, adjust the belt’s tension and alignment, ensuring a smooth and efficient movement. The collaboration between these rollers maintains the conveyor belt’s optimal condition and performance.
- With Deflector Pulleys: Deflector pulleys change the direction of the conveyor belt, and snub rollers assist in this process by ensuring the belt maintains adequate tension and traction during the transition, preventing misalignment and slippage.
- And Take-Up Pulleys: Take-up pulleys adjust the belt’s tension, which is essential for its proper functioning. Snub rollers complement this by increasing the belt’s contact area with the drive pulleys, enhancing traction and allowing the take-up pulleys to work more efficiently in maintaining the correct tension.
The snub roller is more than just an accessory in the conveyor system; it is a linchpin that enhances efficiency, prolongs the lifespan of the system, and ensures the seamless transport of materials. Its symbiotic relationship with idler rollers, deflector pulleys, and take-up pulleys exemplifies the intricate interdependencies within a conveyor system, highlighting the importance of each component’s role in achieving optimal performance.
Key Components of Snub Rollers
The snub roller, a critical component in the operation of conveyor systems, is comprised of several key parts, each playing a pivotal role in its functionality, durability, and efficiency. Understanding these components not only highlights the complexity of snub rollers but also underscores their significance in the seamless operation of conveyor systems. This discussion will provide an overview of the parts that make up a snub roller, including the materials and construction involved, and delve into the significance of each component.
Components of a Snub Roller
The anatomy of a snub roller is designed for performance and longevity, with each component crafted from materials chosen for their durability and suitability to the roller’s operational environment. The main components include:
- Shell: The outer surface of the snub roller, usually made from steel or heavy-duty polymers, designed to withstand the wear and tear of continuous contact with the conveyor belt. The material choice here is crucial for resisting abrasion and corrosion, ensuring the roller’s longevity.
- Shaft: The central rod that runs through the snub roller, providing structural support. Typically made from high-strength steel, the shaft must bear the weight of the roller and the belt’s tension without bending or breaking.
- Bearings: Positioned at either end of the shaft, bearings reduce friction and allow the roller to spin smoothly. High-quality bearings are essential for minimizing maintenance requirements and extending the life of the roller.
- Seals: These components protect the bearings from dust, debris, and moisture, which can cause premature failure. Effective seals ensure the roller operates efficiently in various environmental conditions.
- End Caps: Attached to the ends of the roller, these caps help to maintain the structural integrity of the roller, protect the bearings and seals, and can also provide mounting points for the roller within the conveyor system.
Significance of Each Component
- Shell: The durability and efficiency of the snub roller hinge on the quality of the shell. A well-constructed shell not only supports the conveyor belt but also reduces the risk of damage and wear, ensuring smoother operations and less frequent replacements.
- Shaft: The shaft’s strength is vital for supporting the snub roller’s weight and the dynamic forces exerted by the conveyor belt. A robust shaft prevents deformations that could affect the roller’s performance and alignment.
- Bearings: The bearings play a critical role in the snub roller’s operational efficiency. High-quality bearings reduce the energy required to rotate the roller, lowering overall energy consumption of the conveyor system. They also decrease the likelihood of operational failures.
- Seals: Effective sealing is crucial for protecting the bearings from environmental contaminants, which can extend the maintenance intervals and operational lifespan of the snub roller. This is especially important in harsh or dusty industrial environments.
- End Caps: By protecting the inner components and providing a secure mounting point, end caps ensure that the snub roller remains fixed in its intended position, contributing to the overall stability and reliability of the conveyor system.
Each component of a snub roller is integral to its overall performance, durability, and efficiency within a conveyor system. From the shell to the end caps, the materials and construction of these components must be carefully considered to ensure the snub roller can withstand the demands of its operational environment. The strategic design and quality of these parts not only ensure the longevity of the snub roller itself but also contribute to the smooth and efficient operation of the entire conveyor system.
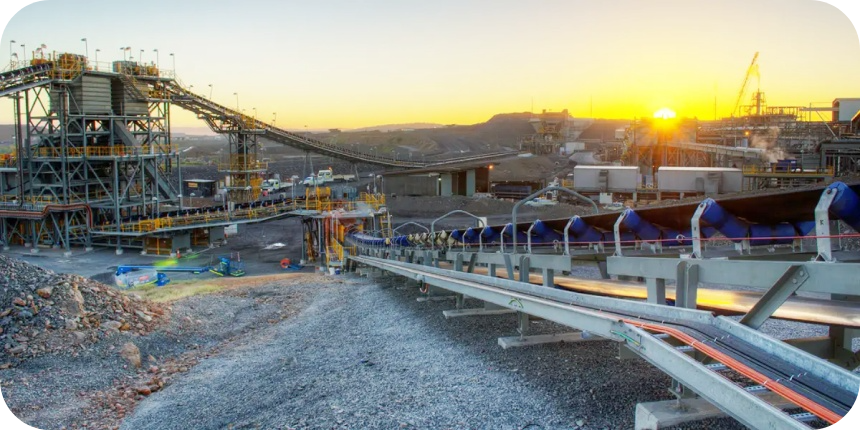
The Interplay between Snub Rollers and Other Conveyor Components
The role of snub rollers within conveyor systems extends beyond their individual functionality, into a dynamic interplay with other critical components like idler rollers, head pulleys, and deflector pulleys. This interplay is essential for maintaining belt tension, preventing slippage, and ensuring the overall efficiency and longevity of the conveyor system. Through the strategic placement and coordination of snub rollers with these components, conveyor systems achieve optimal performance. Let’s explore this synergy in detail, highlighting four examples of configurations that leverage the interaction between snub rollers and other conveyor parts.
Snub Rollers’ Interaction with Conveyor Components
- With Idler Rollers: Idler rollers support the conveyor belt’s weight and facilitate its smooth movement. Snub rollers complement this by adjusting the belt’s tension and curvature, enhancing the belt’s contact with drive components. This synergy ensures that the belt moves uniformly without slipping, thereby maintaining efficiency and reducing wear.
- With Head Pulleys: The head pulley drives the conveyor belt forward. Snub rollers positioned near the head pulley increase the contact area between the belt and the pulley, which is crucial for preventing belt slippage, especially under heavy loads or high-speed conditions. This not only enhances the drive efficiency but also distributes the wear more evenly across the belt, prolonging its life.
- With Deflector Pulleys: Deflector pulleys guide the conveyor belt’s direction. Snub rollers, placed strategically around these pulleys, ensure the belt remains tensioned and aligned, facilitating a smooth transition of the belt around corners or angles. This interaction is critical in complex conveyor systems with intricate paths.
Examples of Optimized Configurations
- High-Load Areas: In sections of the conveyor where the belt carries heavy loads, additional snub rollers are placed close to the head pulley to increase traction and prevent slippage. This configuration ensures that the conveyor can handle heavy loads without compromising on speed or efficiency.
- Long Conveyor Systems: For extended conveyor systems, snub rollers are evenly distributed along the length, especially before and after curves or inclines. This setup maintains consistent belt tension throughout the conveyor, preventing sagging or tension spikes that could lead to slippage or accelerated wear.
- Incline/Decline Sections: In sections where the conveyor belt ascends or descends, snub rollers are positioned to ensure that the belt remains in firm contact with the drive pulleys. This arrangement prevents the belt from sliding back under the weight of the load, ensuring smooth and efficient operation in challenging conditions.
- Variable Load Conditions: In conveyor systems that experience varying load conditions, adjustable snub rollers are employed. These can be manually or automatically adjusted to change the belt’s tension in response to the load, ensuring optimal performance under fluctuating conditions.
The strategic interplay between snub rollers and other conveyor components exemplifies the importance of each part working in harmony to achieve the desired operational efficiency and longevity. By understanding and implementing these optimized configurations, engineers and operators can significantly enhance the performance and reliability of their conveyor systems. This synergy not only supports the immediate operational goals but also contributes to the long-term sustainability and cost-effectiveness of material handling operations.
Selecting the Right Snub Roller for Your Conveyor System
Choosing the appropriate snub roller is a critical decision that can significantly impact the efficiency, durability, and maintenance needs of your conveyor system. The right snub roller enhances traction, prevents slippage, and extends the lifespan of both the belt and the entire conveyor system. To ensure you select the most suitable snub roller, consider the following five factors and nine tips that highlight material compatibility and operational requirements.
Factors to Consider
- Conveyor Belt Width: The width of the conveyor belt dictates the required size of the snub roller. A snub roller too small for the belt width won’t provide adequate tension or support, leading to inefficiencies and increased wear.
- Conveyor Speed: High-speed conveyor systems require snub rollers with bearings capable of handling high rotational speeds without overheating or failing. Select a snub roller designed for the speed of your system.
- Type of Materials Being Transported: The weight, abrasiveness, and corrosiveness of the materials being conveyed affect the choice of snub roller. Heavy or abrasive materials necessitate snub rollers with robust construction and durable materials to withstand the increased wear.
- Environmental Conditions: The operating environment, including temperature, humidity, and exposure to chemicals, influences the material selection for snub rollers. For harsh environments, choose snub rollers made from materials that can withstand such conditions without degrading.
- Belt Tension Requirements: The required tension to prevent slippage without causing excessive wear to the belt determines the type and placement of snub rollers. Systems with variable loads might benefit from adjustable snub rollers to maintain optimal tension under different conditions.
Tips on Selecting Snub Rollers
- Material Compatibility: Ensure the snub roller material is compatible with the conveyor belt to prevent chemical reactions or increased wear.
- Bearing Quality: High-quality bearings reduce maintenance needs and enhance the roller’s lifespan. Opt for sealed bearings in dusty or moist environments.
- Adjustability: Adjustable snub rollers allow for changes in tension to accommodate varying loads or environmental conditions, enhancing system flexibility.
- Surface Coating: Consider rollers with surface treatments or coatings for additional protection against wear, corrosion, or material buildup.
- Ease of Maintenance: Select snub rollers that are easy to access and replace, minimizing downtime and maintenance costs.
- Customization Options: For unique conveyor systems, consider custom-designed snub rollers that precisely meet your specifications and requirements.
- Manufacturer Reputation: Choose snub rollers from manufacturers with a proven track record for quality, reliability, and support.
- Energy Efficiency: Some snub rollers are designed to minimize energy consumption through reduced friction and efficient design. These can be particularly beneficial for systems with high operational costs.
- Cost-Effectiveness: While initial cost is an important consideration, factor in the total cost of ownership, including maintenance, replacement, and operational efficiency, to make a cost-effective choice.
Selecting the right snub roller involves a detailed analysis of your conveyor system’s specific needs, taking into account the operational environment, the materials being transported, and the system’s speed and load requirements. By considering these factors and tips, you can choose snub rollers that enhance the performance and longevity of your conveyor system, ensuring smooth, efficient operations and minimizing downtime and maintenance requirements.
Snub Roller Maintenance and Replacement
Proper maintenance and timely replacement of snub rollers are crucial for the longevity and efficiency of conveyor systems. Regular checks and maintenance can prevent breakdowns, reduce downtime, and ensure the continuous, smooth operation of the conveyor belt. Below, find eight guidelines for maintenance and insights into the signs that indicate the need for replacement, along with steps to ensure effective implementation.
Guidelines for Regular Maintenance Checks
- Visual Inspection: Regularly inspect snub rollers for signs of wear, damage, or misalignment. Check for visible cracks, deformations, or any accumulation of material on the rollers.
- Lubrication: Ensure bearings are adequately lubricated according to the manufacturer’s recommendations. Proper lubrication reduces friction, preventing overheating and prolonging the life of the rollers.
- Cleaning: Keep the snub rollers clean of debris, dust, and any material build-up. Accumulated materials can affect the roller’s performance and cause additional wear.
- Alignment Checks: Verify that snub rollers are correctly aligned with the conveyor belt. Misalignment can lead to uneven wear and reduced efficiency.
- Tension Monitoring: Monitor the tension of the conveyor belt, ensuring it’s within the recommended range. Over or under-tensioning can lead to premature wear or slippage.
- Bearing Checks: Listen for unusual noises and check for excessive movement or heat in the bearings, indicating wear or failure.
- Operational Tests: Conduct regular operational tests to ensure the snub rollers and the conveyor system are functioning smoothly and efficiently.
- Record Keeping: Maintain detailed records of inspections, maintenance, and replacements. This history can help identify patterns and predict future maintenance needs.
Signs Indicating the Need for Snub Roller Replacement
- Excessive Noise: Unusual sounds, such as grinding or squeaking, suggest bearing issues or misalignment.
- Visible Damage: Cracks, significant wear, or deformation on the roller surface or shaft indicate the need for replacement.
- Increased Friction: If the snub roller does not rotate freely or shows signs of dragging, it may be due to bearing failure.
- Misalignment: Persistent misalignment, not corrected by adjustments, may necessitate roller replacement.
- Inefficient Operation: A decrease in conveyor efficiency or an increase in belt slippage despite proper tensioning could be due to worn-out snub rollers.
Steps for Effective Snub Roller Replacement
- Safety First: Before beginning, ensure the conveyor system is powered off and properly locked out to prevent accidental startup.
- Removal of the Old Roller: Carefully remove the damaged or worn snub roller, taking note of its position and orientation for accurate replacement.
- Selection of a Suitable Replacement: Choose a replacement snub roller that matches the specifications of the old one, considering size, material, and load capacity.
- Installation of the New Roller: Install the new roller, ensuring it is properly aligned with the conveyor belt and securely fastened in place.
- Adjustment and Alignment: Adjust the new snub roller for optimal belt tension and alignment, following the manufacturer’s guidelines.
- Operational Testing: After installation, conduct a test run of the conveyor system to ensure the new roller operates smoothly and efficiently.
- Post-Installation Inspection: After the initial run, check the installation and alignment once more to confirm that there are no issues.
- Documentation: Update maintenance records with details of the replacement, including the date, reasons for replacement, and any observations during the process.
Adhering to these maintenance guidelines and recognizing the signs that indicate the need for snub roller replacement are essential for maintaining the operational integrity of conveyor systems. By taking proactive steps towards maintenance and timely replacement, you can ensure that your conveyor system continues to run smoothly, minimizing downtime and prolonging the system’s overall lifespan.
Get in touch with us for detailed specifications and pricing on our Snub Rollers. Submit your inquiry now.
Snub Roller Pricing and Availability
The cost and availability of snub rollers can vary significantly based on several influencing factors. Understanding these factors can help in making informed purchasing decisions, ensuring that you find the right snub roller for your conveyor system at the best possible price. Here we will explore seven key factors that influence snub roller pricing, followed by nine pieces of advice on where to find them for sale and how to maximize the value of your investment.
Factors Influencing Snub Roller Pricing
- Material: The construction material of snub rollers, such as steel, stainless steel, or polymer, significantly affects their price. Materials that offer higher durability or corrosion resistance typically command higher prices.
- Size: Larger snub rollers, which require more material and labor to produce, are generally more expensive than smaller ones. The diameter and length of the roller play a crucial role in determining the cost.
- Manufacturer: The brand and manufacturer’s reputation can influence the pricing. Well-known brands that are recognized for quality and reliability may charge more for their products.
- Design Complexity: Custom-designed snub rollers, which are tailored to specific conveyor system requirements, can be more costly than standard models due to the additional engineering and manufacturing efforts involved.
- Quantity: Purchasing in bulk often allows for discounts. The total number of snub rollers required can impact the per-unit cost, with larger orders typically resulting in lower prices.
- Market Demand: Fluctuations in market demand for snub rollers can affect their price. High demand coupled with limited supply can lead to higher prices.
- Shipping and Handling: The cost of shipping and handling, influenced by the weight of the snub rollers and the distance they need to be transported, can add to the overall cost.
Advice on Finding Snub Rollers for Sale and Maximizing Value
- Compare Suppliers: Research and compare prices from multiple suppliers to find the best deal. Don’t hesitate to negotiate prices, especially for bulk orders.
- Look for Deals: Keep an eye out for discounts, special offers, or clearance sales, which can provide significant savings.
- Consider Refurbished Options: Refurbished snub rollers can offer similar performance to new ones at a lower cost. Ensure they come with a warranty for peace of mind.
- Bulk Purchases: If possible, coordinate with other needs within your operation or with other businesses to make a bulk purchase and take advantage of volume discounts.
- Assess Total Cost of Ownership: Beyond the initial purchase price, consider the lifespan, maintenance needs, and efficiency of the snub rollers to assess their total cost of ownership.
- Online Marketplaces: Explore online industrial supply marketplaces, which often feature competitive prices and a wide range of options.
- Direct from Manufacturers: Buying directly from manufacturers can sometimes offer the best prices, as it eliminates the middleman.
- Check Delivery Costs: Compare delivery costs between suppliers, as high shipping fees can negate any savings made on the purchase price.
- Quality Over Price: While it’s important to find a good deal, prioritize quality and compatibility with your system to avoid future costs related to inefficiency, maintenance, or early replacement.
By considering these factors and following this advice, you can make a more informed decision when purchasing snub rollers, ensuring you get the best possible value and performance for your conveyor system.
FAQs about Snub Roller
A snub roller is an integral component of conveyor systems, designed to provide increased traction between the conveyor belt and the drive pulleys. This small, yet crucial roller is positioned close to the drive pulleys to adjust the angle of contact or “wrap” of the belt on the pulleys. The main purpose of the snub roller is to enhance the performance of the conveyor belt system by maintaining proper tension and alignment of the belt. Its role is critical in preventing belt slippage, especially under heavy loads or high-speed operations. Constructed from durable materials, snub rollers can withstand the wear and tear of continuous operation, playing a vital part in the longevity and efficiency of the conveyor system.
The snub pulley, often confused with the snub roller, serves a similar function in conveyor systems. It is strategically placed to improve the friction between the belt and the main drive pulley, ensuring a firm grip and preventing slippage. The snub pulley works by increasing the arc of contact between the belt and the drive pulley, which enhances the belt’s ability to transmit power without losing traction. Typically found in systems where enhanced traction is required, such as inclined or long conveyors, the snub pulley is vital for maintaining belt tension and extending the operational life of the conveyor system by evenly distributing the stress along the belt.
Idler rollers are found ubiquitously on conveyor systems and perform the crucial function of providing support to the conveyor belt and the materials being transported. These cylindrical rollers are strategically placed along the length of the conveyor framework and help to maintain the integrity and shape of the belt. By doing so, idler rollers facilitate the smooth and consistent movement of the belt, reduce its wear, and distribute the load evenly. They come in various designs tailored to different applications, such as carrying rollers that support the belt’s load, return rollers that support the belt on its return section, and impact rollers that absorb the shock of falling materials.
The rollers on a conveyor are typically cylindrical components that support, guide, and shape the conveyor belt as it moves materials from one location to another. These rollers are essential for the functioning of the conveyor system and are categorized based on their function. The main types include drive rollers, which power the conveyor belt, idler rollers, which support the belt along its path, snub rollers, which adjust the belt’s tension and angle of contact with drive pulleys, and return rollers, which support the belt on its return pass. Each type of roller is designed to ensure the conveyor operates efficiently and effectively, with minimal maintenance and downtime.
Last Updated on July 25, 2024 by Jordan Smith
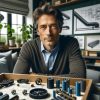
Jordan Smith, a seasoned professional with over 20 years of experience in the conveyor system industry. Jordan’s expertise lies in providing comprehensive solutions for conveyor rollers, belts, and accessories, catering to a wide range of industrial needs. From initial design and configuration to installation and meticulous troubleshooting, Jordan is adept at handling all aspects of conveyor system management. Whether you’re looking to upgrade your production line with efficient conveyor belts, require custom conveyor rollers for specific operations, or need expert advice on selecting the right conveyor accessories for your facility, Jordan is your reliable consultant. For any inquiries or assistance with conveyor system optimization, Jordan is available to share his wealth of knowledge and experience. Feel free to reach out at any time for professional guidance on all matters related to conveyor rollers, belts, and accessories.