Composite Conveyor Rollers: Revolutionizing Material Handling
Conveyor systems play a pivotal role across various industries, from manufacturing and mining to agriculture and beyond, serving as the backbone for material handling and efficient product movement. At the heart of these systems lies the innovative use of composite conveyor rollers, a key advancement that has significantly enhanced the functionality and durability of conveyor systems. Unlike their traditional steel counterparts, composite conveyor rollers offer a lightweight, yet robust alternative that drastically reduces wear and tear on the conveyor belt. Their introduction marks a significant shift towards more sustainable, cost-effective, and efficient operations. The significance of composite conveyor rollers cannot be overstated; they not only improve the operational efficiency of conveyor systems but also contribute to a substantial reduction in maintenance costs and downtime, thereby optimizing the productivity and profitability of industries reliant on these essential systems.
What are Composite Conveyor Rollers?
Composite conveyor rollers represent a groundbreaking advancement in the design and functionality of conveyor systems. These rollers are constructed from a combination of materials, including plastics, reinforced fiberglass, and resins, which are engineered to offer superior strength, durability, and resistance to wear compared to traditional materials. Unlike the conventional steel rollers, which have been the industry standard, composite conveyor rollers provide a lighter, more energy-efficient solution, significantly reducing the operational costs and environmental impact of conveyor systems.
When comparing composite conveyor rollers to traditional steel rollers, several key differences become apparent:
Advantages of using composite materials in conveyor rollers include:
- Reduced Operational Costs: The lightweight nature of composite conveyor rollers means less energy is required to move the conveyor, leading to significant savings in electricity costs.
- Increased Durability: Composite materials are inherently resistant to corrosion, abrasion, and chemicals, extending the life of the rollers and reducing the need for replacements.
- Lower Maintenance Needs: With their superior durability, composite conveyor rollers demand less maintenance, minimizing downtime and maintenance costs.
- Improved Workplace Safety and Noise Reduction: The lighter weight reduces the risk of injuries during manual handling, while the quieter operation contributes to a better working environment.
- Environmental Sustainability: Composite conveyor rollers are often made from recyclable materials and consume less energy, aligning with eco-friendly operational goals.
Composite conveyor rollers offer an innovative solution that surpasses traditional steel rollers in efficiency, durability, and environmental sustainability, making them a preferred choice for modern conveyor systems.
The Advantages of Composite Conveyor Rollers
Composite conveyor rollers offer a multitude of benefits over traditional materials like steel, encompassing enhanced durability, cost-efficiency, environmental sustainability, and safety improvements. These advantages stem from the innovative design and materials used in their construction, which have been tailored to meet the rigorous demands of modern industrial applications.
Enhanced Durability and Performance
The construction and material properties of composite conveyor rollers result in several significant benefits:
- Corrosion Resistance: Composite materials are highly resistant to corrosion from chemicals, moisture, and other corrosive elements, ensuring the rollers maintain their integrity over time.
- Abrasion Resistance: They exhibit excellent abrasion resistance, which reduces wear and extends the life of the rollers, even in harsh operating conditions.
- Reduced Wear on Equipment: The lighter weight of composite rollers leads to less wear and tear on the conveyor belt and other system components, prolonging their lifespan.
- Temperature Resistance: These rollers can withstand extreme temperatures without degrading, making them suitable for use in environments that are too harsh for traditional materials.
- Moisture Resistance: Composite materials do not absorb moisture, preventing swelling or other water-related damage that can occur with wood or metal rollers.
Cost-Efficiency
Composite conveyor rollers also present significant cost advantages:
- Lower Energy Costs: The reduced weight of composite rollers means less energy is required to move the conveyor, leading to lower electricity costs.
- Less Frequent Replacements: Their increased durability means that composite rollers need to be replaced less often than steel rollers, reducing replacement costs.
- Reduced Maintenance Costs: With fewer instances of corrosion and wear, maintenance needs and associated costs are significantly lower.
- Improved System Efficiency: The smooth operation and reduced friction of composite rollers can enhance overall system efficiency, further lowering operational costs.
- Long-Term Savings: While the initial investment in composite conveyor rollers may be higher than traditional rollers, the long-term savings in maintenance, energy, and replacement costs provide a superior return on investment.
Environmental and Safety Benefits
The use of lighter, more durable materials in composite conveyor rollers offers several environmental and safety advantages:
- Reduced Carbon Footprint: Lower energy consumption directly translates to a smaller carbon footprint for operations utilizing composite rollers.
- Recyclability: Many composite materials can be recycled at the end of their life cycle, reducing waste and promoting sustainability.
- Noise Reduction: The operation of composite rollers is significantly quieter than steel rollers, contributing to a more pleasant and less stressful work environment.
- Safety in Handling: The lighter weight of composite rollers reduces the risk of injuries associated with lifting and handling, improving workplace safety.
- Decreased Environmental Impact: The durability and longer lifespan of composite rollers mean fewer resources are consumed over time, further reducing the environmental impact of conveyor system operations.
Composite conveyor rollers offer a forward-thinking solution that addresses the needs of modern industry, combining performance, cost-efficiency, and environmental sustainability in a way that traditional materials cannot match.
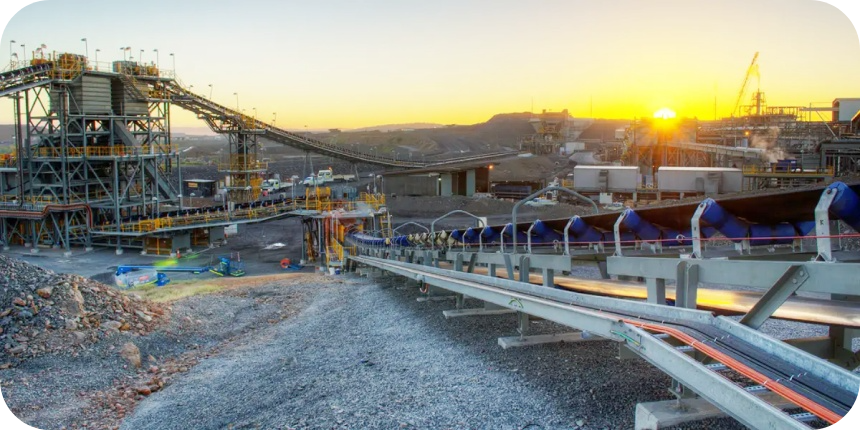
Types of Composite Conveyor Rollers
The market offers a diverse range of composite conveyor rollers, each designed to meet specific operational needs across various industries. Understanding the different types available is crucial for selecting the right composite conveyor roller that aligns with your application’s requirements.
Overview of Composite Conveyor Roller Types
Composite conveyor rollers are categorized based on their construction materials, applications, and the specific challenges they address. Common types include:
- Standard Composite Rollers: These rollers are designed for general use in a wide range of conveyor systems, providing the basic benefits of composite materials, such as reduced weight and increased durability.
- Impact-Resistant Rollers: Engineered for areas where conveyors receive heavy loads, these rollers absorb impact efficiently, protecting the belt and system from damage.
- High-Temperature Rollers: Specifically designed to withstand extreme temperatures, these rollers are ideal for applications in industries like steel manufacturing or baking, where heat resistance is crucial.
- Chemical-Resistant Rollers: These are tailored for use in environments where chemicals or corrosive materials are present, offering superior resistance to chemical damage.
- Food-Grade Rollers: Manufactured with materials safe for food contact, these rollers are used in food processing and pharmaceutical industries, where hygiene and contamination prevention are paramount.
Choosing the Right Composite Conveyor Roller
Selecting the appropriate composite conveyor roller requires consideration of the specific needs of your industry and application.
- Mining and Quarrying: In these industries, impact-resistant composite rollers are essential due to the heavy and abrasive materials being conveyed. Their durability and resistance to wear significantly reduce maintenance needs.
- Steel Manufacturing: High-temperature composite rollers are the best choice for steel manufacturing, where they can withstand the extreme heat without degradation, unlike traditional materials.
- Chemical Processing: For conveyor systems exposed to harsh chemicals, chemical-resistant rollers ensure longevity and prevent material breakdown, maintaining system integrity.
- Food Production: Food-grade composite rollers are crucial in food production lines to meet strict hygiene standards and prevent contamination, ensuring product safety.
- Parcel Handling and Logistics: Standard composite rollers are often sufficient for parcel handling, where their light weight and durability improve efficiency and reduce energy costs.
By understanding the types of composite conveyor rollers available and considering the specific requirements of your industry, you can make an informed decision that enhances the performance and efficiency of your conveyor system.
Used and New Composite Conveyor Rollers for Sale
Finding the right composite conveyor rollers for your system, whether new or used, can significantly impact your operation’s efficiency, cost, and sustainability. Here’s guidance on where to look for these rollers and tips to ensure you purchase high-quality used products.
Where to Find Composite Conveyor Rollers for Sale
Composite conveyor rollers are available from a variety of sources:
- Manufacturer Websites: Many manufacturers of composite conveyor rollers have detailed catalogs of their products online, offering both new and sometimes used options.
- Industrial Supply Companies: These companies stock a wide range of conveyor system components, including new composite rollers.
- Online Marketplaces: Websites like eBay, Alibaba, and industry-specific marketplaces can be good sources for finding both new and used composite conveyor rollers.
- Local Dealers and Distributors: They often have both new and used options and can provide valuable advice and support.
- Auctions and Liquidation Sales: Companies going out of business or upgrading their systems may auction off their used equipment, including composite conveyor rollers.
Tips for Purchasing Used Composite Conveyor Rollers Without Sacrificing Quality
Purchasing used composite conveyor rollers can offer significant cost savings, but it’s important to ensure you’re not compromising on quality.
- Inspect for Damage: Look for signs of wear, cracks, or any damage that could affect the roller’s performance. Photos can be misleading, so inspect the product in person if possible.
- Verify Specifications: Make sure the rollers meet the specific requirements for your conveyor system, including size, load capacity, and material compatibility.
- Ask About History: Inquire about the age of the rollers, previous usage conditions, and reasons for selling. Rollers used in harsh conditions may have less life left than those from more forgiving environments.
- Check for Warranties or Guarantees: Some sellers offer warranties or guarantees on used equipment. These can provide additional assurance regarding the quality and lifespan of the rollers.
- Consider Refurbished Options: Refurbished rollers are used rollers that have been repaired or restored to a like-new condition. They can offer a good balance between cost and reliability.
By carefully selecting your source and performing due diligence on the condition and specifications of the used composite conveyor rollers, you can ensure that your investment adds value to your conveyor system without compromising on quality or performance.
How Composite Conveyor Rollers are Made
The manufacturing process of composite conveyor rollers is intricate and innovative, utilizing advanced materials and technologies to produce rollers that are not only durable but also efficient. Understanding this process and the science behind the materials provides insight into why these rollers offer such superior performance compared to traditional options.
Manufacturing Process
The creation of composite conveyor rollers involves several key steps:
- Material Selection: The process begins with the selection of composite materials, typically including high-grade polymers, reinforced fiberglass, and sometimes, recycled materials. These materials are chosen for their strength, flexibility, and resistance to environmental factors.
- Design and Engineering: Advanced computer-aided design (CAD) software is used to model the rollers precisely. This stage is crucial for ensuring the roller’s structural integrity and performance characteristics meet specific operational requirements.
- Fabrication of the Core: The core of the roller, often made from fiberglass-reinforced resin, is created using techniques like pultrusion or filament winding. These methods ensure the core has high tensile strength and is resistant to bending and wear.
- Layering and Curing: The outer layers, which may include additional reinforcement materials, are applied over the core. The roller is then cured in a controlled environment, which involves heating it to harden and set the composite materials. This process is critical for achieving the desired durability and resistance properties.
- Finishing Touches: Once cured, the rollers undergo machining to achieve the precise dimensions required for specific conveyor systems. Additional treatments, such as the application of UV-protective coatings or anti-static properties, can also be applied depending on the application needs.
- Quality Control: Rigorous testing for strength, durability, and performance is conducted to ensure each roller meets the high standards expected of composite materials. This may include load-bearing tests, wear simulations, and exposure to various environmental conditions.
The Science Behind the Durability and Efficiency
The superior durability and efficiency of composite conveyor rollers are rooted in the materials’ science and the manufacturing process. Composite materials are engineered to withstand harsh environmental conditions, including extreme temperatures, corrosive substances, and physical impacts. The combination of polymers and reinforced fibers provides a high strength-to-weight ratio, meaning these rollers can bear significant loads while being lightweight, which reduces the energy required to operate the conveyor system.
Furthermore, the material properties of composites can be tailored during the manufacturing process to meet specific needs, such as increased resistance to abrasion or chemicals. This adaptability ensures that composite conveyor rollers can be optimized for virtually any environment or application, significantly extending their lifespan and reducing the need for frequent replacements.
The manufacturing process and the science behind composite materials together make composite conveyor rollers a highly effective and efficient choice for modern conveyor systems, offering unmatched durability, performance, and cost-efficiency.
Implementing Composite Conveyor Rollers in Your Operations
The decision to upgrade to composite conveyor rollers is a strategic move that can enhance the efficiency, safety, and cost-effectiveness of your operations. Understanding how to assess your needs and implement these advanced rollers is crucial for achieving the desired outcomes.
Identifying Your Needs
Assessing whether composite conveyor rollers are a suitable upgrade involves a detailed analysis of your current conveyor system and operational requirements. Consider the following steps:
- Evaluate Current Performance: Review the performance of your existing rollers, noting issues such as wear rate, maintenance frequency, and failure rates.
- Analyze Operational Environment: Consider the operational environment, including exposure to chemicals, moisture, temperature extremes, and abrasive materials. Composite rollers offer superior resistance in harsh conditions.
- Determine Load Requirements: Assess the weight and type of materials being conveyed. Composite rollers can handle a wide range of loads but are particularly beneficial for heavy or abrasive materials.
- Consider Energy Efficiency Goals: If reducing energy consumption is a priority, the lightweight nature of composite rollers can contribute to lower energy costs.
- Review Safety and Noise Concerns: If workplace safety and noise reduction are important, the lighter weight and quieter operation of composite rollers can be significant advantages.
Installation and Maintenance
Installing composite conveyor rollers and maintaining them for longevity and peak performance involves several key guidelines:
- Follow Manufacturer Instructions: Always adhere to the installation guidelines provided by the manufacturer to ensure optimal performance and avoid voiding warranties.
- Use Appropriate Tools and Techniques: Ensure that installation is performed with the correct tools and techniques to prevent damage to the rollers or the conveyor system.
- Regular Inspections: Conduct regular inspections to identify and address wear or damage early. Look for signs of uneven wear, misalignment, or accumulation of debris.
- Clean Regularly: Keep the rollers and the conveyor belt clean to prevent material build-up that can affect performance and cause unnecessary wear.
- Lubricate as Needed: While composite rollers typically require less lubrication than metal rollers, ensure that any moving parts in the conveyor system are appropriately lubricated according to the manufacturer’s recommendations.
- Adjust for Alignment: Ensure rollers are correctly aligned during installation and check alignment periodically to prevent uneven wear or belt tracking issues.
- Monitor Load Capacity: Avoid exceeding the recommended load capacity for the rollers to prevent premature wear or failure.
Implementing composite conveyor rollers requires a thoughtful approach to both selection and maintenance. By carefully assessing your needs and adhering to best practices for installation and upkeep, you can maximize the benefits of composite conveyor rollers, enhancing your operation’s efficiency, safety, and bottom line.
Case Studies: Success Stories with Composite Conveyor Rollers
The transition to composite conveyor rollers has brought significant operational improvements across various industries. These real-world examples highlight the benefits achieved through the adoption of composite rollers, underscoring their versatility and effectiveness.
Mining Industry
Challenge: A leading mining company faced frequent downtime due to the rapid wear and failure of metal rollers in their harsh, abrasive environment.
Solution: The company upgraded to impact-resistant composite conveyor rollers designed to withstand the abrasive conditions.
Outcome: The switch resulted in a 50% reduction in roller failures and a significant decrease in maintenance costs and downtime, enhancing overall productivity.
Food Processing
Challenge: A food processing plant struggled with sanitation and corrosion issues, impacting their conveyor system’s reliability and cleanliness.
Solution: The plant implemented food-grade composite rollers, which are resistant to corrosion and easy to clean, meeting strict hygiene standards.
Outcome: The new rollers led to improved sanitation levels, reduced maintenance requirements, and increased the longevity of the conveyor system.
Parcel Handling and Logistics
Challenge: A logistics company was looking to improve the efficiency of its conveyor systems in distribution centers to handle increased parcel volumes.
Solution: Lightweight composite rollers were installed to reduce the system’s energy consumption and enhance handling efficiency.
Outcome: The upgrade resulted in a 20% increase in conveyor speed, lower energy costs, and reduced noise levels, significantly improving parcel processing times.
Steel Manufacturing
Challenge: A steel mill experienced frequent roller failures due to the extreme heat and heavy loads, leading to costly production stoppages.
Solution: High-temperature composite conveyor rollers, capable of withstanding the mill’s demanding conditions, were introduced.
Outcome: The composite rollers offered enhanced durability and heat resistance, reducing roller replacement frequency by 75% and contributing to smoother, uninterrupted operations.
Chemical Industry
Challenge: A chemical manufacturing facility needed to address the rapid degradation of its conveyor rollers caused by exposure to aggressive chemicals.
Solution: The facility replaced its existing rollers with chemical-resistant composite rollers specifically designed to resist corrosion.
Outcome: This change not only extended the life of the conveyor system but also reduced maintenance interventions and improved the overall safety of the operation.
These case studies illustrate the transformative impact that composite conveyor rollers can have on an operation’s efficiency, safety, and cost-effectiveness. By addressing unique industry challenges with tailored solutions, composite rollers are proving to be a valuable investment for businesses aiming to optimize their conveyor systems.
Learn more about our high-quality conveyor roller solutions.
FAQs About Composite Conveyor Rollers
Conveyors utilize a variety of rollers designed to facilitate the efficient movement of materials or products along the system. The type of roller selected often depends on the application, material being transported, and the environment in which the conveyor operates. Commonly used rollers include steel, plastic, and composite rollers. Steel rollers are durable and ideal for heavy loads and harsh conditions. Plastic rollers are lightweight and suitable for lighter loads and environments where corrosion resistance is important. Composite rollers, made from materials like fiberglass and reinforced polymers, offer a balance between durability and weight, making them ideal for a wide range of applications due to their resistance to corrosion, wear, and environmental conditions. The choice of roller significantly impacts the conveyor’s performance, maintenance needs, and overall efficiency.
Roller conveyors are categorized based on their functionality and the specific needs they serve within various industries. The primary types include gravity roller conveyors, powered roller conveyors, and live roller conveyors. Gravity roller conveyors rely on the force of gravity to move items and are often used for product sorting and assembly lines. Powered roller conveyors utilize motors to move materials, making them suitable for heavier loads and controlled movement. Live roller conveyors combine both gravity and powered rollers, offering versatility for dynamic operations with varying load requirements. Each type has its unique benefits and is selected based on factors such as load weight, speed requirements, and operational efficiency.
The primary purpose of a roller conveyor is to transport materials or products smoothly and efficiently from one point to another within a facility. Roller conveyors are versatile and can be used in a wide range of industries, including manufacturing, packaging, and distribution. They are designed to facilitate the movement of goods, reduce manual handling, improve operational efficiency, and enhance workplace safety. Roller conveyors can handle various items, from small components to large pallets, making them an integral part of production lines, assembly processes, and warehousing operations. Their ability to be customized with different roller types and configurations allows for tailored solutions that meet specific operational needs.
A roller conveyor consists of several key components that work together to move materials efficiently. These include rollers, which are the cylindrical elements that carry the load; the frame, which supports the rollers and provides structure to the system; bearings, which facilitate smooth roller movement; and the drive mechanism, in powered conveyors, which includes motors and belts to move the rollers. Additional components may include guide rails to keep items on track, stops to control product movement, and sensors for automated systems. The design and composition of these components vary based on the conveyor’s type and the specific requirements of the application, ensuring optimal performance and reliability.
Last Updated on July 9, 2024 by Jordan Smith
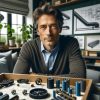
Jordan Smith, a seasoned professional with over 20 years of experience in the conveyor system industry. Jordan’s expertise lies in providing comprehensive solutions for conveyor rollers, belts, and accessories, catering to a wide range of industrial needs. From initial design and configuration to installation and meticulous troubleshooting, Jordan is adept at handling all aspects of conveyor system management. Whether you’re looking to upgrade your production line with efficient conveyor belts, require custom conveyor rollers for specific operations, or need expert advice on selecting the right conveyor accessories for your facility, Jordan is your reliable consultant. For any inquiries or assistance with conveyor system optimization, Jordan is available to share his wealth of knowledge and experience. Feel free to reach out at any time for professional guidance on all matters related to conveyor rollers, belts, and accessories.