Enhancing Conveyor Reliability with Self Aligning Conveyor Rollers
Conveyor systems are integral to the seamless operation of various industries, efficiently moving materials from one point to another. At the heart of these systems are the rollers, which play a pivotal role in ensuring smooth and continuous movement. However, one of the common challenges faced is belt misalignment, which can lead to significant downtime, increased maintenance costs, and premature wear and tear on the conveyor belt. Enter self aligning conveyor rollers, a revolutionary solution designed to automatically correct any misalignment of the conveyor belt. These specialized rollers detect when the belt begins to drift off-course and gently guide it back to the center, thus preventing the belt from wandering off the edges. By incorporating self aligning conveyor rollers into conveyor systems, industries can not only enhance the efficiency and reliability of their operations but also significantly reduce the risk of operational disruptions caused by belt misalignment.
What is Self-Aligning Idlers
The core concept behind self aligning conveyor rollers is their ability to autonomously correct the alignment of a conveyor belt, ensuring it remains centered during operation. This innovative feature addresses one of the most prevalent challenges in conveyor system management: belt misalignment. Misaligned belts can lead to uneven wear, increased maintenance needs, and potential operational halts, all of which self aligning conveyor rollers aim to mitigate. By incorporating mechanisms that allow for the automatic adjustment of the belt’s position, these rollers play a crucial role in maintaining the efficiency and extending the longevity of conveyor systems.
The Core Concept
Self aligning conveyor rollers are ingeniously designed to detect deviations in the belt’s path and gently steer it back to its proper alignment. This automatic correction process is vital for preventing the belt from slipping off the rollers, reducing the risk of damage to the belt edges, and minimizing material spillage. The functionality of self aligning rollers is pivotal not only in prolonging the life of the conveyor system but also in ensuring operational continuity and efficiency.
Types of Self-Aligning Idlers
Troughed Self-Align Training Idler: These are designed to support the belt in a troughed position, providing better stability and guidance for the belt. They are particularly effective in handling bulk materials, as their shape helps contain the material, reducing spillage and enhancing the efficiency of material transfer.
Troughed Friction Self Align Training Idler: Similar to the troughed self-align idlers but with added friction elements that increase their ability to correct belt misalignment. These idlers are particularly useful in environments where slippage is a concern, as the friction helps maintain the belt’s position even under challenging conditions.
Tapered Self Align Training Idler: These idlers feature tapered rollers that create a slight angle with the belt, guiding it back to the center whenever it starts to drift. The tapered design is particularly effective for conveyor systems that experience frequent changes in loading conditions or directional shifts.
Self Aligning Return Idler: Positioned on the return side of the belt, these idlers correct the alignment of the belt as it makes its way back to the starting point. They are essential for ensuring that the belt is correctly aligned before it is loaded again, reducing the risk of misalignment-related issues on the carrying side.
Impact Idler and Its Application in Absorbing Shock at Loading Points: Impact idlers are designed with a series of cushioned rollers that absorb the shock and impact of material loading. While not self-aligning in the traditional sense, they complement the function of self aligning conveyor rollers by preventing misalignment caused by the sudden weight of loaded materials. Their shock-absorbing capacity reduces the strain on the conveyor system, contributing to the overall longevity and efficiency of the operation.
Together, these various types of self aligning conveyor rollers ensure that the conveyor belt remains centered, regardless of the operational conditions, load size, or material characteristics. This not only minimizes maintenance and operational costs but also maximizes the productivity and lifespan of the conveyor system.
Benefits of Using Self Aligning Conveyor Rollers
The implementation of self aligning conveyor rollers within conveyor systems introduces a plethora of benefits aimed at enhancing operational efficiency, safety, and the overall lifespan of the conveyor system. These specialized rollers are engineered to address and rectify one of the most common and challenging issues in conveyor operation: belt misalignment. Below are detailed insights into the key benefits provided by self aligning conveyor rollers.
Preventing Belt Misalignment and Associated Damages
One of the primary advantages of using self aligning conveyor rollers is their capability to prevent belt misalignment. Misalignment can cause significant damage to the belt edges, lead to material spillage, and even result in the complete halt of conveyor operations. By automatically correcting any deviation in the belt’s path, self aligning rollers ensure that the belt remains centered, thereby minimizing the risk of damage and enhancing the system’s reliability.
Reducing Maintenance Costs and Downtime
Frequent misalignments necessitate regular maintenance and can lead to unexpected downtime, both of which incur significant costs. The proactive alignment corrections made by self aligning conveyor rollers substantially reduce the need for manual adjustments and repairs, thereby lowering maintenance costs. Furthermore, by minimizing the occurrences of belt misalignment, these rollers significantly reduce operational downtime, ensuring a smoother, more consistent flow of materials.
Enhancing the Lifespan of Both the Conveyor Belt and the Rollers
Misalignment not only affects the conveyor belt but can also lead to increased wear and tear on the rollers themselves. Self aligning conveyor rollers are designed to distribute the load evenly and maintain optimal alignment, which reduces uneven wear on both the belt and the rollers. As a result, the lifespan of the conveyor system components is significantly extended, providing a better return on investment.
Improving Material Handling Efficiency by Ensuring Smooth Operation
The smooth and efficient operation of a conveyor system is crucial for maintaining productivity. Self aligning conveyor rollers contribute to this by ensuring that the belt remains properly aligned, thus preventing disruptions caused by spillages or jams. This ensures a consistent flow of materials, improving the overall efficiency of the material handling process. Additionally, by maintaining proper belt alignment, these rollers can help to improve the accuracy of material placement on the belt, further enhancing the system’s efficiency.
The integration of self aligning conveyor rollers into a conveyor system offers substantial benefits, including the prevention of belt misalignment, reduction in maintenance costs and downtime, enhanced lifespan of the system components, and improved operational efficiency. These benefits collectively contribute to a more reliable, cost-effective, and efficient material handling solution.
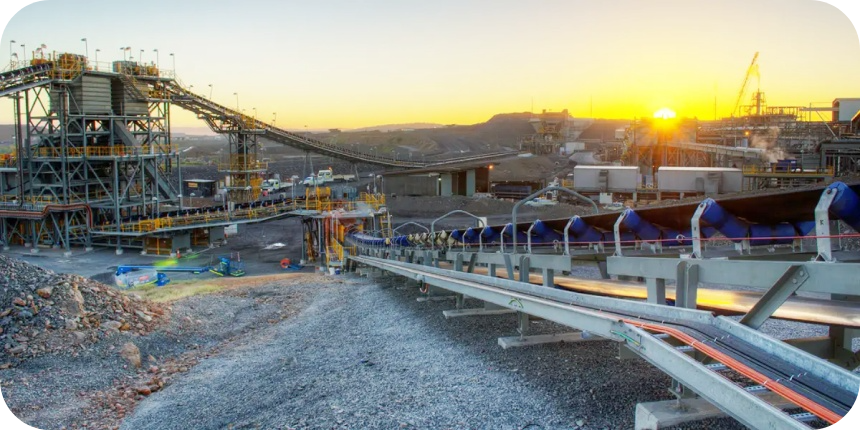
Choosing the Best Self Aligning Conveyor Rollers
Selecting the most suitable self aligning conveyor rollers is crucial for optimizing the efficiency and longevity of your conveyor system. This decision should be informed by a comprehensive understanding of the key features, material options, sizes, specifications, industry applications, and price considerations associated with these specialized rollers.
Key Features to Consider
Material
The material from which self aligning conveyor rollers are made significantly affects their durability, friction levels, and suitability for various environments.
- High-Density Polyethylene (HDPE): HDPE conveyor rollers offer excellent corrosion resistance and are lighter than metal alternatives, reducing the conveyor system’s energy consumption.
- Steel: Known for its strength and durability, steel rollers are ideal for heavy-duty applications and environments with high impact or abrasive materials.
- Stainless Steel: These rollers are preferred in food processing, pharmaceuticals, and other industries requiring high levels of hygiene and corrosion resistance.
- Aluminum: Aluminum rollers are lightweight and resistant to corrosion, making them suitable for medium-duty applications and environments with moisture or chemical exposure.
- Composite Materials: Combining the benefits of plastics and metals, composite rollers offer durability, low noise, and reduced weight, making them versatile for various applications.
Sizes and Specifications
The effectiveness of self aligning conveyor rollers is also influenced by their size and design specifications.
- Roller Diameter: The diameter needs to be chosen based on the belt width and material size to ensure proper support and alignment.
- Belt Width Compatibility: Rollers must be compatible with the conveyor belt’s width to provide effective alignment and avoid material spillage.
- CEMA Classes: The Conveyor Equipment Manufacturers Association (CEMA) specifies design standards for rollers. Selecting the correct CEMA class ensures the roller meets the operational demands of your system.
- Load Capacity: It’s essential to choose rollers that can support the maximum load of your conveyor without deformation or failure.
- Bearing Type and Size: Bearings play a crucial role in the roller’s performance and longevity. Selecting the appropriate type and size ensures smooth operation and reduces maintenance needs.
Industry Applications
Self aligning conveyor rollers are designed to meet the needs of various industries, each with its specific requirements.
- Mining: Requires durable and robust rollers that can withstand heavy loads and abrasive materials.
- Steel Mills: Rollers must handle high temperatures and heavy, abrasive materials without compromising performance.
- Cement Plants: Dusty environments demand rollers that can operate reliably in the presence of fine particulates.
- Agriculture: Rollers need to be versatile to handle varying loads and conditions, from grains to bulky produce.
- Packaging: Requires rollers that can ensure precise alignment for delicate handling and efficient packaging processes.
Price Considerations
The price of self aligning conveyor rollers is influenced by several factors.
- Material Quality: Higher-quality materials typically command a higher price due to their durability and performance benefits.
- Manufacturing Complexity: Rollers with specialized designs or features for specific applications may be more costly to produce.
- Brand and Manufacturer: Premium brands or manufacturers with established reputations may offer their products at a premium.
- Order Quantity: Purchasing in bulk often allows for price negotiations, resulting in lower costs per unit.
- Customizations: Customized sizes, materials, or features to meet specific operational requirements can increase the price.
Balancing cost and quality is essential for ensuring long-term savings and operational efficiency. Investing in high-quality self aligning conveyor rollers may involve a higher initial cost but can lead to reduced maintenance expenses, decreased downtime, and longer equipment lifespan, thereby offering better long-term value.
Used vs. New Self Aligning Conveyor Rollers
When it comes to enhancing your conveyor system with self aligning conveyor rollers, one significant decision is whether to invest in new or used rollers. Each option has its merits and drawbacks, influencing the efficiency, cost, and longevity of your system.
Advantages and Disadvantages of Purchasing Used Self-Aligning Conveyor Rollers
Advantages:
- Cost Savings: The most apparent benefit of purchasing used rollers is the potential for cost savings. Used rollers can often be acquired at a fraction of the price of new ones, providing an economical solution for budget-conscious operations.
- Environmental Sustainability: Choosing used rollers contributes to environmental sustainability by recycling and reusing materials, reducing waste, and conserving the resources required to manufacture new rollers.
- Immediate Availability: Used rollers are typically available for immediate delivery, avoiding the lead times associated with manufacturing and shipping new rollers.
- Tested in Real Conditions: Used rollers have been tested in real-world conditions, providing some assurance of their functionality and durability.
- Flexibility in Purchase Quantity: There may be more flexibility in purchasing smaller quantities of used rollers, which is beneficial for replacing specific sections of a conveyor system.
Disadvantages:
- Unknown History and Wear: The biggest drawback of used rollers is the uncertainty regarding their history, including exposure to harsh conditions, maintenance practices, and overall wear and tear.
- Reduced Lifespan: Due to their prior use, these rollers may have a reduced operational lifespan, necessitating sooner replacement than new rollers.
- Potential for Higher Maintenance Costs: If the used rollers are near the end of their service life or have been poorly maintained, they may require more frequent repairs or replacements.
- Lack of Warranty: Used rollers often come without a warranty, leaving the buyer to absorb the cost of any failures or malfunctions.
- Compatibility Issues: There is a risk of compatibility issues with existing conveyor system components, which may not be immediately evident.
Tips for Assessing the Condition and Reliability of Used Rollers
- Request Documentation: Ask for any available documentation on the roller’s history, including usage, maintenance records, and previous operating environments to better understand its condition.
- Inspect for Visible Damage: Look for signs of wear and tear, such as cracks, corrosion, or deformities on the roller body and bearings, which could indicate potential failures.
- Check for Smooth Operation: Rotate the roller by hand to ensure it moves smoothly without any grinding noises or resistance, indicating well-functioning bearings.
- Verify Compatibility: Confirm the specifications of the used rollers, such as size, material, and load capacity, to ensure they match the requirements of your conveyor system.
- Consult with a Specialist: If possible, have the rollers inspected by a specialist who can provide an expert opinion on their condition and expected lifespan.
When considering used versus new self aligning conveyor rollers, weigh the initial cost savings against the potential for increased maintenance and shorter lifespan. By carefully assessing the condition and compatibility of used rollers, you can make an informed decision that balances cost, efficiency, and reliability in your conveyor system operations.
Where to Find Self Aligning Conveyor Rollers for Sale
Finding the right source for self aligning conveyor rollers, whether new or used, is crucial for maintaining the efficiency and reliability of your conveyor systems. Below are suggestions on where to find these specialized rollers and the importance of selecting reputable suppliers and manufacturers.
Suggestions for Sourcing Both New and Used Self-Aligning Conveyor Rollers
- Manufacturer Websites: Directly purchasing from manufacturers is one of the best ways to ensure you’re getting new, quality self aligning conveyor rollers. Many manufacturers offer a range of products online, complete with detailed specifications and support.
- Industrial Supply Companies: These companies specialize in providing a wide range of conveyor components, including self aligning conveyor rollers. They often have extensive catalogs and can offer both new and used options.
- Online Marketplaces: Platforms like eBay, Alibaba, and Amazon can be sources for both new and used rollers. They provide access to a global market of sellers, including direct manufacturers and resellers.
- Specialized Conveyor System Dealers: Dealers focusing on conveyor systems and components often have both new and used self aligning rollers. They can provide valuable advice on the best options for your specific needs.
- Auctions and Industrial Surplus Stores: For used rollers, auctions and industrial surplus stores can offer significant deals. These venues often sell off excess inventory from closures or upgrades, providing an opportunity to find quality components at lower prices.
Importance of Choosing Reputable Suppliers and Manufacturers with Certifications
- Guaranteed Quality: Reputable suppliers and manufacturers are more likely to provide high-quality self aligning conveyor rollers that meet industry standards. Certifications like CE and ISO 9001 serve as proof of their commitment to quality and reliability.
- Product Warranty: Certified suppliers often offer warranties on their products, providing peace of mind and protection against defects or premature wear.
- Technical Support: A reputable supplier or manufacturer will offer excellent technical support, assisting with installation, maintenance, and troubleshooting, which is invaluable for ensuring the longevity and efficiency of the rollers.
- Customization Options: Manufacturers with industry certifications usually have the capability to provide customized solutions that can better meet specific operational needs, ensuring optimal compatibility and performance.
- Compliance with Regulations: Buying from certified suppliers ensures that the products comply with safety and environmental regulations, reducing the risk of legal and operational issues down the line.
Selecting self aligning conveyor rollers from reputable sources with recognized certifications ensures that you receive products that are not only of high quality but also supported by warranties and excellent customer service. This approach helps to minimize downtime, optimize operational efficiency, and secure a better return on investment for your conveyor system components.
Installation and Maintenance of Self Aligning Conveyor Rollers
Ensuring the proper installation and maintenance of self aligning conveyor rollers is crucial for maximizing their benefits in terms of conveyor efficiency and longevity. This section provides an overview of the installation procedures, maintenance tips, and highlights the impact of proper care on the performance and durability of these components.
Installation Procedures for Self-Aligning Idlers
The installation of self aligning conveyor rollers should follow a precise procedure to ensure optimal performance:
- Assessment of Conveyor Alignment: Before installation, assess the conveyor frame and belt alignment to ensure that the system is structurally sound and capable of supporting the self-aligning rollers.
- Selection of Strategic Locations: Install self aligning conveyor rollers at critical points where misalignment is likely to occur, such as loading zones, transitions, and curves.
- Adjustment of Roller Brackets: Ensure that the brackets holding the rollers are adjustable to allow for the precise positioning and alignment of the rollers with the conveyor belt.
- Securing Rollers: Firmly secure the rollers in their brackets to prevent them from shifting during operation. Ensure that all fastenings are tightened to the manufacturer’s specifications.
- Alignment Checks: After installation, check the alignment of the rollers with the belt to ensure they are positioned correctly to guide the belt back to its central path.
Maintenance Tips to Keep Your Self-Aligning Rollers in Top Condition
Regular maintenance of self aligning conveyor rollers is key to their longevity and the overall efficiency of the conveyor system:
- Regular Inspection: Conduct regular inspections of the rollers for signs of wear, damage, or misalignment. Pay special attention to the condition of the bearings and the roller surface.
- Lubrication: Ensure that the rollers and their bearings are adequately lubricated according to the manufacturer’s recommendations to reduce friction and prevent wear.
- Cleaning: Keep the rollers and the surrounding area clean from debris and material buildup, which can interfere with their ability to align the conveyor belt properly.
- Adjustment and Realignment: Periodically check and adjust the positioning and tension of the rollers to ensure they continue to align the belt effectively.
- Replacement of Worn Parts: Replace any parts that show significant wear or damage promptly to prevent further issues or potential failure of the conveyor system.
The Impact of Proper Installation and Maintenance on Roller Longevity and Conveyor Efficiency
Proper installation and diligent maintenance of self aligning conveyor rollers have a profound impact on their longevity and the efficiency of the conveyor system. Correctly installed and well-maintained rollers ensure continuous and effective alignment of the conveyor belt, reducing downtime and maintenance costs. Regular maintenance extends the life of the rollers by preventing premature wear and failure, while also ensuring that the conveyor system operates smoothly and efficiently. This proactive approach to installation and maintenance not only optimizes the performance of self aligning conveyor rollers but also enhances the overall productivity and longevity of the conveyor system.
Reach out for a customized self-aligning-conveyor-rollers solution by sending us an inquiry.
FAQs About Self Aligning Conveyor Rollers
A self-aligning idler is a specialized component utilized within conveyor systems to ensure the conveyor belt remains centered and aligned during operation. These idlers are ingeniously designed to automatically adjust the belt’s path as needed, minimizing the risk of belt misalignment. This misalignment can lead to various operational challenges, including material spillage, increased wear and tear on the conveyor belt, and even complete system shutdowns if left unaddressed. Self-aligning idlers achieve this corrective action through their unique construction, which allows them to pivot or tilt in response to the belt’s movement off-center. By guiding the belt back to its optimal path, self-aligning idlers play a crucial role in maintaining the efficiency, safety, and longevity of the conveyor system. Their use is particularly beneficial in applications where conveyor belts are subject to varying loads, directional changes, or other conditions that may predispose them to misalignment.
Aligning a conveyor involves several steps to ensure that both the conveyor belt and the entire conveyor system are correctly positioned for optimal performance and longevity. First, it’s essential to ensure the conveyor frame is square and level. This can involve adjusting the legs or supports of the conveyor to achieve a level position. Next, check the pulleys and rollers to ensure they are properly aligned to the frame and with each other. Misaligned pulleys can lead to belt tracking issues. The belt tension should also be adjusted to specifications; too much or too little tension can cause alignment problems. For belts that are consistently misaligning, self-aligning idlers can be installed. These specialized idlers automatically guide the belt back to the center if it begins to drift off course. Regular inspections and adjustments are vital to maintaining proper alignment, as wear and tear on components can lead to misalignment over time. Using laser alignment tools or professional conveyor alignment services can also ensure precise alignment, especially for complex systems or after major modifications.
Conveyors utilize various types of rollers, each designed to fulfill specific functional requirements and applications within the conveyor system. The most common types include:
Carrying Rollers: These are the most prevalent, supporting the conveyor belt and the material being transported. They are spaced along the length of the conveyor to prevent the belt from sagging.
Return Rollers: Positioned on the underside of the conveyor, return rollers support the belt on its return path, ensuring it remains tensioned and aligned.
Impact Rollers: Installed at the loading points, impact rollers absorb the shock and force of material falling onto the conveyor, protecting the belt from damage.
Guide Rollers: These are used to guide the belt and keep it aligned, particularly in curved sections of the system.
Self-Aligning Rollers: Designed to automatically correct any misalignment of the conveyor belt, enhancing the system’s efficiency and reducing maintenance needs.
Each type of roller plays a crucial role in the conveyor’s operation, contributing to the system’s efficiency, reliability, and maintenance requirements.
Roller conveyors are versatile systems used to move materials and products in manufacturing, distribution, and packaging environments. They come in various types, each suited to different applications and material handling requirements:
Gravity Roller Conveyors: These rely on gravity to move items across the horizontal or slightly inclined paths. They are ideal for manual sorting, assembly processes, or as a cost-effective means of transporting goods.
Powered Roller Conveyors: Equipped with motors, these conveyors move items along the conveyor path without manual assistance, suitable for heavy loads or high-volume material handling.
Accumulation Conveyors: Designed to allow for the accumulation of products on the conveyor while maintaining a constant flow, these conveyors prevent products from touching, reducing damage during transport.
Flexible Roller Conveyors: These systems can be extended, curved, or bent to fit various spaces and applications, offering versatility in setup and storage.
Live Roller Conveyors: Powered rollers move the product across the conveyor surface. They can be used for heavy loads and are particularly useful in applications requiring product alignment or sorting.
Each type offers specific advantages, from the simplicity and low cost of gravity conveyors to the advanced features of powered and specialized systems, making the choice dependent on the operational needs, budget, and desired level of automation.
Last Updated on August 1, 2024 by Jordan Smith
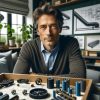
Jordan Smith, a seasoned professional with over 20 years of experience in the conveyor system industry. Jordan’s expertise lies in providing comprehensive solutions for conveyor rollers, belts, and accessories, catering to a wide range of industrial needs. From initial design and configuration to installation and meticulous troubleshooting, Jordan is adept at handling all aspects of conveyor system management. Whether you’re looking to upgrade your production line with efficient conveyor belts, require custom conveyor rollers for specific operations, or need expert advice on selecting the right conveyor accessories for your facility, Jordan is your reliable consultant. For any inquiries or assistance with conveyor system optimization, Jordan is available to share his wealth of knowledge and experience. Feel free to reach out at any time for professional guidance on all matters related to conveyor rollers, belts, and accessories.