Custom Solutions with V Roller Conveyors for Industries
Conveyors have revolutionized the way industries transport materials and products within their facilities, offering a seamless, efficient flow from one point to another. Among the diverse types of conveyors available, the V roller conveyor stands out for its distinctive design and functionality. Specifically engineered with “V” shaped rollers, this conveyor is adept at handling items that require precise positioning and stability during movement, such as cylindrical products or materials with uneven bases. The unique aspect of V-roller conveyors lies in their ability to minimize product movement and ensure alignment, making them an indispensable tool in various manufacturing and packaging lines. This introduction aims to shed light on the operational mechanics and the significant advantages of incorporating V-roller conveyors into industrial processes, highlighting their versatility and efficiency in material handling.
What is V Roller Conveyor?
A V-roller conveyor is a specialized type of material handling equipment designed to transport cylindrical or spherical products efficiently through production lines or assembly areas. Unlike flat belt conveyors, the v roller conveyor utilizes uniquely shaped rollers configured into a “V” formation. This design cradles the product securely, minimizing surface contact while ensuring stability and precise positioning during transport.
V-Roller Conveyors and Their Design
V-roller conveyors are characterized by their distinctive roller shape, which is pivotal in handling products that are cylindrical—such as pipes, tubes, and rolls of material. Each roller is typically mounted on a fixed axle and spaced at regular intervals, allowing cylindrical items to be supported along two points of contact on each roller, thereby creating a balanced trough. The “V” shape of the guide rollers guides the products forward, preventing them from falling off the sides of the conveyor and providing a controlled pathway.
The construction materials for these conveyors can vary based on the application but generally include heavy-duty metals such as steel or aluminum for industrial environments. For handling delicate surfaces, rollers might be coated with rubber or a plastic composite to reduce abrasion. The design also incorporates adjustable height and speed features, making the v roller conveyor adaptable to different operational requirements and workspaces.
“V” Shaped Rollers and Their Benefits in Handling Cylindrical Products
The “V” shaped rollers in a v roller conveyor offer several advantages when it comes to the handling of cylindrical products:
- Stability: The V-shape provides a natural cradle for round objects, stabilizing them during movement and reducing the risk of rollovers, especially when the conveyor is inclined.
- Reduced Contact Area: With less surface area contact, there is minimized potential for damage to the products’ surfaces, which is particularly advantageous for sensitive materials.
- Improved Alignment: The shape helps to align products perfectly as they move along the conveyor, essential for operations where precision is key, such as in assembly processes or when feeding into machines.
- Increased Load Capacity: By distributing the weight evenly across the rollers, v roller conveyors can handle heavier loads compared to flat belt designs, enhancing productivity with the ability to move bulk quantities.
- Versatility: These conveyors can easily be integrated into complex conveyor systems with curves, inclines, or declines, and are compatible with other conveyor types, allowing for flexible use in logistics hubs and manufacturing facilities.
- Energy Efficiency: The reduced friction from minimal contact reduces the power requirements, which can lead to lower energy costs and a smaller carbon footprint.
- Ease of Maintenance: The simple and robust design of the V-shaped rollers makes maintenance tasks, such as cleaning and roller replacement, more straightforward and less frequent.
The v roller conveyor is an essential tool for industries that handle cylindrical products. Its design not only enhances efficiency and productivity but also offers significant advantages in terms of product safety and quality control, making it a preferred choice in various sectors, including manufacturing, packaging, and distribution.
Key Components of V Roller Conveyors
The functionality and efficiency of a v roller conveyor depend significantly on its design and the specific components it incorporates. Each part plays a critical role in the conveyor’s operation, handling, and overall performance. Below, we explore the key components that make up a v roller conveyor system, detailing their design and practical applications.
V-Shaped Roller Conveyor: Trough Shape Design
The foundational component of any v roller conveyor is the V-shaped roller itself. These rollers are designed with a trough-like profile that securely cradles cylindrical objects, ensuring they are transported safely along the conveyor path without slipping or falling off. The rollers are typically made from durable materials such as steel or aluminum, which can withstand heavy loads and resist wear and tear.
- Design Features: The trough shape of the V-rollers is geometrically optimized to maintain the balance of the cylindrical products. The angle and depth of the “V” are critical parameters that influence the conveyor’s ability to handle different diameters and types of products.
- Material Options: Depending on the application, the rollers can be coated with materials such as rubber or synthetic polymers to minimize damage to delicate surfaces of the transported goods.
- Applications: This type of roller is ideal for industries where precise and stable movement of cylindrical items is required, such as in the handling of logs, pipes, and large rolls of fabric or paper.
Poly V-Roller Conveyor: Specific Adaptations and Uses
Poly V-roller conveyors are a variation of the standard v roller conveyor, featuring rollers that are connected by a continuous poly V-belt. This design enhances the conveyor’s grip on the product and allows for the transfer of power along the conveyor system, facilitating integrated operations across multiple stages of production.
- Design Benefits: The poly V-belt that links the rollers helps distribute the load evenly, which increases the system’s capacity to handle heavier objects. Additionally, the belt’s presence minimizes slippage and enhances the drive efficiency across the rollers.
- Specific Adaptations: These conveyors are particularly adapted for applications requiring synchronized movement and precise speed control, making them suitable for automated assembly lines.
- Use Cases: They are extensively used in the automotive and packaging industries where products need to be moved in a controlled and precise manner without manual intervention.
V Groove Conveyor Roller: Functionality and Applications
V groove conveyor rollers are designed with a specific “V” shaped groove at the center of the roller, which aligns with similar grooves on the conveyor frame or track. This design ensures that the rollers are self-aligning and that the load is centered automatically.
- Functional Advantages: The V groove in the rollers provides a dual function of guiding the cylindrical products and reducing lateral movement, which significantly enhances the stability of the transport process.
- Material and Design Variations: These rollers can be customized in different sizes and materials, including hardened plastics and high-impact composites, depending on the environmental and load requirements.
- Applications: V groove rollers are commonly used in material handling systems where precise positioning and orientation of the product are critical, such as in material offloading systems and selective assembly lines.
V Belt Conveyor Roller: Integration and Advantages
Integrating V-belts with conveyor rollers creates a highly efficient and robust system known as the V belt conveyor roller system. This setup utilizes the high grip and low slip properties of V-belts to enhance the movement control of products on the conveyor.
- Integration Features: The V-belts are typically looped around the rollers, providing a secure and continuous contact surface, which improves the transmission of motion and power across the conveyor.
- Advantages: The use of V-belts helps in reducing the operational noise and vibration, offering a smoother and more stable product handling. Additionally, V-belts are less prone to stretching and slipping, which improves the overall reliability of the conveyor system.
- Operational Benefits: This type of conveyor is particularly advantageous in applications involving steep inclines or declines, where the risk of product slippage is higher. It is also beneficial in scenarios requiring variable speed operations.
Each component of the v roller conveyor plays an essential role in optimizing the conveyor’s functionality, enhancing the safety and efficiency of product transport. These specialized adaptations allow v roller conveyors to be tailored to meet the specific needs of various industrial applications, thereby broadening their usability and effectiveness in complex manufacturing and processing environments.
Types of V Roller Conveyors
Exploring the various types of v roller conveyors is crucial for industries looking to optimize their conveyor systems to suit specific operational needs. This section categorizes the types of v roller conveyors into used equipment, V-belt driven systems, and pop-up transfer mechanisms, highlighting their features, benefits, and applications, particularly their use in sorting processes.
By understanding these types of v roller conveyors and their specific benefits and applications, businesses can make informed decisions that align with their operational needs and budget constraints, thereby enhancing efficiency and productivity in their conveyor operations.
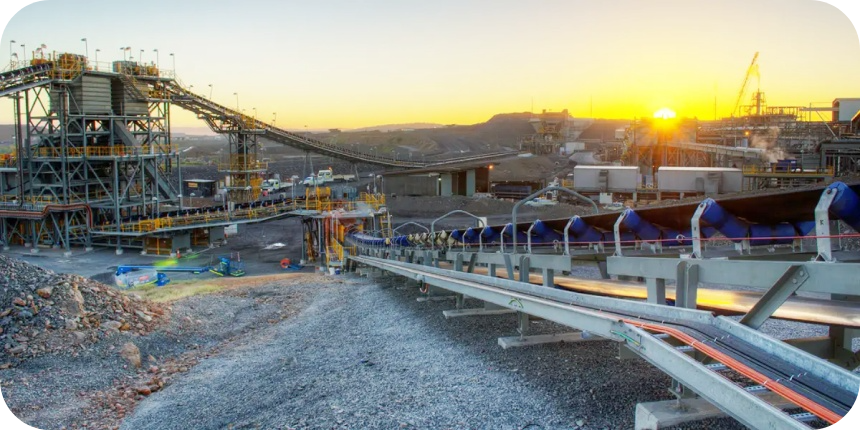
Comparing Roller Conveyors, Including V Roller Conveyor
When selecting a conveyor system, understanding the differences between roller conveyors, including v roller conveyors, and belt conveyors is crucial. These systems differ significantly in terms of design, efficiency, use cases, and overall suitability for specific tasks. This section provides a detailed comparison, focusing on the scenarios where one might be preferred over the other, leveraging a tabular representation for clarity.
Table Overview: Roller Conveyors vs. Belt Conveyors
Detailed Comparison: Roller Conveyor vs. Belt Conveyor
Roller Conveyor (Including V-Roller Conveyor)
- Efficiency: Roller conveyors are highly efficient at transporting items that are consistent in size and shape. The rolling mechanism significantly reduces the friction involved in moving items compared to sliding, which is common in belt conveyors. This makes them suitable for industrial environments where speed and handling large volumes are critical factors.
- Specific Use Cases: They are particularly advantageous for moving heavy and rugged items over long distances. V-roller conveyors excel in handling cylindrical products, ensuring these items are transported securely without the risk of falling off the conveyor.
- Cost-Effectiveness: Roller conveyors are less costly to install and maintain due to their simple and robust design. The absence of a continuous belt and fewer moving parts lowers the frequency and cost of maintenance.
Belt Conveyor
- Versatility: Belt conveyors provide a smooth, continuous surface that can handle a variety of items, including those that are small, irregular in shape, or delicate. This makes them ideal for industries such as food processing, pharmaceuticals, and packaging.
- Energy Considerations: Although belt conveyors are generally more energy-intensive, they offer the flexibility of handling items that roller conveyors cannot, such as loose materials or small, intricate products.
- Operational Benefits: The belt’s continuous movement provides a quiet and smooth operation, which is beneficial in environments where noise reduction is important.
The choice between a roller conveyor (including v roller conveyors) and a belt conveyor depends largely on the specific needs of the operation, including the type of items being transported, the required speed of the system, and cost considerations. Roller conveyors are preferred in industrial settings for their durability and efficiency, especially v roller conveyors for cylindrical objects, while belt conveyors are favored in sectors requiring gentle handling of diverse and delicate products. Understanding these differences and specific scenarios where each is preferred will help in making an informed decision that aligns with operational goals.
Operational Mechanisms of V Roller Conveyors
In any industrial setup, the efficiency of v roller conveyors depends significantly on their operational mechanisms. These systems are engineered to facilitate the easy, reliable transport of goods, particularly cylindrical products, which are otherwise challenging to handle. This section delves into the basic operating principles of roller conveyors and explores specific driving mechanisms that enhance their functionality.
How Do V-Roller Conveyors Work? Basic Principles and Mechanics of Operation
V-roller conveyors are designed to transport items by reducing ground friction, which makes it easier to move heavy or bulky items with less effort and higher efficiency. Here are the foundational principles and mechanics behind their operation:
Basic Principles
- Roller Arrangement: The rollers are typically arranged in a series of “V” shaped troughs, which centralize and stabilize cylindrical objects, preventing them from rolling off the side.
- Gravity or Motorized Drive: Depending on the application, these conveyors can be gravity-fed (inclined to use gravity as the driving force) or motorized (using mechanical systems for propulsion).
- Friction Reduction: The design of the rollers minimizes the surface area in contact with the objects being transported, significantly reducing friction and facilitating smoother movement.
Mechanics of Operation
- Load Distribution: The “V” configuration of the rollers ensures even distribution of weight, which not only aids in stability but also in the reduction of wear and tear on the conveyor components.
- Roller Material: Rollers are often made from materials that enhance durability and reduce friction, such as steel with a rubber coating, which also minimizes potential damage to the items being transported.
Explanation of Driving Mechanisms
To enhance the functionality and reliability of v roller conveyors, different driving mechanisms can be employed. These are designed to fit various industrial applications and requirements for seamless and secure transportation.
Roller-to-Roller Chain Drives
- Design: This system involves a chain that connects each roller to adjacent rollers, driven by a central motor. The chain ensures synchronized movement of the rollers, which is crucial for maintaining the orientation and position of cylindrical items.
- Benefits:
- Synchronization: Keeps all rollers turning at the same rate, which is vital for smooth operation.
- Durability: Chains are typically very robust and can handle heavy loads and harsh operating conditions without significant wear.
- Ease of Maintenance: Chain drives are relatively simple to repair and replace, making them ideal for heavy-duty industrial environments.
TKF’s PosiGrip Belt Drive System
- Mechanism: The PosiGrip system utilizes a toothless, high-grip belt that runs underneath the rollers to provide propulsion. The unique feature of this system is that it operates without the need for the belt to physically contact the rollers through gears or teeth, which eliminates the risk of slippage and reduces wear.
- Features:
- Seamless Transportation: The smooth operation of the belt ensures that the items on the conveyor move seamlessly, which is particularly important for delicate or precision-required items.
- Secure Grip: The high-friction surface of the belt grips the rollers securely, maintaining consistent motion even under variable loads.
- Reduced Noise and Wear: With no teeth to engage and disengage, the PosiGrip system operates quietly and with minimal mechanical wear.
- Applications:
- Sensitive Product Handling: Ideal for industries where the products are prone to damage, as the smooth motion reduces impact and vibration.
- High-Speed Operations: The efficient grip and propulsion allow for faster conveyor speeds without compromising the stability of the products.
The operational mechanisms of v roller conveyors, particularly the use of roller-to-roller chain drives and TKF’s PosiGrip belt drive system, significantly enhance their efficiency and reliability. By understanding these mechanisms, industries can better configure their conveyor systems to meet specific operational demands, ensuring optimal performance and longevity of the system. Whether through synchronized chain drives for heavy-duty applications or smooth and secure belt systems for delicate operations, v roller conveyors offer a versatile and efficient solution for modern industrial needs.
Applications and Advantages of V Roller Conveyors
V-roller conveyors are an integral component of modern manufacturing and distribution facilities. Their specialized design allows them to efficiently handle cylindrical products, which can be difficult to transport using other types of conveyors. This section explores the diverse applications of v roller conveyors in various industries and outlines the significant advantages they offer.
Applications of V-Roller Conveyors in Industry
V-roller conveyors are versatile and essential in many industrial operations. Here are eight key applications:
- Logistics and Distribution Centers: For sorting and moving cylindrical packages through sorting centers efficiently.
- Manufacturing Plants: Especially useful in the automotive industry for transporting engines, pipes, and other cylindrical components along the assembly line.
- Construction Material Handling: Used for moving large cylindrical materials such as pipes and tubes, which are common in construction sites.
- Food Processing: In the food industry, these conveyors are used for handling barrels or cylindrical containers that hold ingredients or finished products.
- Pharmaceuticals: Ideal for transporting rolls of labels or cylindrical containers used in drug manufacturing.
- Paper and Printing Industries: Useful for handling large paper rolls, reducing the risk of damage during transport.
- Textile Industry: Conveying fabric rolls efficiently from one process to another without causing fabric warps.
- Rolling Stock Handling: Used in rail and other transportation sectors for moving large cylindrical parts such as wheels or axles.
These applications demonstrate the adaptability of v roller conveyors to different industrial needs, enhancing operational efficiency wherever they are implemented.
Advantages of Using V-Roller Conveyors
V-roller conveyors provide several operational benefits that make them a preferred choice for handling cylindrical products. Below are six advantages of using these conveyors:
- Minimized Product Movement: The V-shaped configuration of the rollers ensures that products remain stable and centered throughout their journey, minimizing lateral movement and potential falls.
- Versatility in Product Sizes: These conveyors can handle a range of product diameters by simply adjusting the spacing and the angle of the rollers, accommodating everything from small tubes to large barrels.
- Increased Safety: By securely cradling products, v roller conveyors reduce the risk of workplace accidents that can occur when products are dislodged from conveyors.
- Enhanced Product Integrity: The gentle handling of the products minimizes damage during transportation, which is critical for quality control in industries like food processing and pharmaceuticals.
- Integration Ease: V-roller conveyors can be easily integrated into existing conveyor systems, including powered and non-powered setups, making them a flexible option for upgrading current facilities.
- Energy Efficiency: They are designed to use gravity where possible, reducing energy consumption. Even when powered, the efficient design of the rollers and the reduced friction leads to lower power requirements.
The applications and advantages of v roller conveyors highlight their importance and versatility in industrial operations. They are particularly beneficial in industries where cylindrical products are common, offering a safe, efficient, and cost-effective solution for transporting these items. The adaptability to various product sizes and the minimal product movement ensure that v roller conveyors remain a crucial part of modern manufacturing and distribution processes, optimizing throughput and maintaining high standards of product quality.
Customization and Modifications of V Roller Conveyors
V-roller conveyors are highly adaptable and can be customized extensively to meet the specific requirements of various industries. These modifications not only enhance the functionality of the conveyors but also extend their applicability to different environments, including outdoor settings. This section provides an overview of how v roller conveyors can be tailored and offers ten practical tips for customization.
Customizing V-Roller Conveyors for Specific Industrial Needs
Customization of v roller conveyors involves adjusting various aspects of their design and operation to fit the unique needs of specific applications. Here are ten tips for customizing these conveyors:
- Adjustable Roller Spacing: Customize the spacing between the rollers to handle different sizes and types of cylindrical products efficiently.
- Material Choices: Select materials that are suited for the environment in which the conveyor will operate, such as stainless steel for corrosion resistance in wet or outdoor environments.
- Motor Specifications: Choose motors with the right power, speed, and torque specifications to handle the expected load and operational speed.
- Coating Options: Apply specialized coatings to the rollers to prevent sticking or slipping of products, or to withstand harsh chemicals.
- Roller Diameter: Vary the roller diameter to accommodate different product sizes, from small canisters to large barrels.
- Side Guides: Install adjustable side guides to ensure products stay aligned on the conveyor, crucial for automated processes.
- Control Systems: Integrate advanced control systems for precise speed and flow control, which can help synchronize with other parts of a production line.
- Support Frame Modifications: Design the support frames to be adjustable for height or angle to facilitate the gravity-assisted movement of items, or to fit into existing production spaces.
- Weatherproofing: For outdoor use, ensure all components are weatherproofed to handle conditions such as rain, dust, and extreme temperatures.
- Accessory Integration: Add accessories such as sensors for counting or sorting, scales for weighing, and stoppers for batch separation.
Adaptability for Different Environments
V-roller conveyors are not only versatile in their use but also in their adaptability to various environments, including modifications that enable them to function outdoors:
- Outdoor Adaptations:
- Rust and Corrosion Resistance: Use materials like galvanized steel or stainless steel for all metal parts to prevent rust and ensure long-term durability.
- Weather-Resistant Electrical Components: Use sealed and waterproof electrical systems to prevent moisture ingress, which can cause system failures.
- UV Protection: Apply UV-protective coatings to plastic and rubber parts to prevent degradation from prolonged sun exposure.
- Enhanced Drainage Systems: Incorporate drainage systems within the conveyor frame to avoid water accumulation, which can lead to mechanical failures.
- Environmental Considerations:
- Temperature Control: Install systems to handle extreme temperatures, such as heaters or coolers, depending on the geographic location.
- Dust and Debris Shields: Add shields to protect the moving parts from being clogged with dust, sand, or other debris, which is especially important in windy or sandy environments.
- Robust Design Features: Strengthen the design to withstand environmental stresses like heavy winds or seismic activities.
The customization and modification of v roller conveyors are critical in optimizing their performance for specific tasks and environments. By carefully selecting materials, adjusting designs, and integrating necessary accessories, these conveyors can be effectively tailored to meet diverse industrial needs. Whether it’s handling delicate cylindrical products with precision or enduring the harsh conditions of an outdoor installation, customized v roller conveyors offer a reliable and efficient solution for transporting goods.
Submit your specifications for a tailored V Conveyor Roller quote.
FAQs about V Roller Conveyor
Conveyor systems are essential components in material handling and are classified primarily into three types: belt conveyors, roller conveyors, and overhead conveyors.
Belt Conveyors are the most common type, consisting of a continuous belt that stretches between two or more pulleys. They are used to transport parts and materials across a facility or in assembly and packaging lines. Belt conveyors can handle a wide variety of materials, from fine powders to large, bulky items.
Roller Conveyors utilize rollers mounted in frames to convey product either by gravity or manually pushing the product along the conveyor. Roller conveyors are suitable for handling solid items such as boxes, trays, or pallets and are highly favored for their simplicity and efficiency.
Overhead Conveyors are mounted on the ceiling and are used to transport items along a prescribed path within a facility. These conveyors can save valuable floor space, making them ideal for handling materials in busy or compact environments. Overhead conveyors are commonly used in industries such as automotive, where parts need to be moved through various processes along the assembly line.
Each type of conveyor is specifically designed to suit different operational needs, considering factors such as the nature of materials, the required speed of transportation, and the environment in which they operate.
Conveyor rollers play a pivotal role in the movement of materials in various industrial settings. They can be broadly classified into several types, each designed to meet specific industrial needs:
Gravity Rollers: These rollers operate without external power and rely on inclined surfaces or manual force to move items. They are economical and simple for use in assembly lines or material handling processes.
Driven Rollers: Powered by belts, chains, or gears, these rollers are used in automated conveyor systems where precise control of item movement is necessary. They are ideal for handling large volumes of goods quickly.
Impact Rollers: Placed at points where material is loaded onto the conveyor, impact rollers absorb the shock and impact of loading operations, thereby reducing damage to the conveyor belt.
Guide Rollers: Used to ensure that the conveyor belts or materials do not run off their tracks. They are critical in maintaining the alignment and efficiency of the conveyor system.
Tapered Rollers: These are specially designed to facilitate turns and curves in conveyor systems. Their tapered shape allows the conveyor to bend while maintaining the orientation and positioning of items on the belt.
Understanding the specific roles and types of rollers can significantly enhance the efficiency and effectiveness of a conveyor system.
A power roller conveyor is a conveyor system that uses powered rollers to move materials along the conveyor path. These rollers are typically driven by belts, chains, or gears that are connected to motors, making them ideal for transporting heavy loads or for applications where automatic control is required.
The main advantage of power roller conveyors is their ability to regulate the speed and direction of the material flow. This control helps in synchronizing multiple processes in an assembly line or in sorting operations. Power roller conveyors are particularly beneficial in facilities that deal with heavy items or require rapid movement of goods across considerable distances.
This type of conveyor is also adaptable to various industrial conditions, often equipped with sensors and monitoring devices that help maintain efficiency and safety standards. Whether integrating into an existing manufacturing line or setting up a new assembly line, power roller conveyors offer a robust and reliable material handling solution.
The primary purpose of a roller conveyor is to transport materials across an area in a smooth and controlled manner. Roller conveyors are versatile systems used in a variety of industrial, commercial, and retail settings, from production lines to shipping departments.
They are particularly valued for their ability to facilitate the movement of goods with minimal effort—whether the operation is gravity-driven or motor-powered. The simplicity of their design allows for easy installation and maintenance, while their efficiency enhances workflow and productivity.
Furthermore, roller conveyors are designed to handle a wide range of materials, including boxes, pallets, trays, and more. They can be customized with different roller sizes, materials, and configurations to accommodate specific needs and load requirements. This adaptability not only improves the handling capacity but also minimizes the risk of damage to the materials being transported, ensuring a smooth, uninterrupted flow of operations.
In summary, roller conveyors optimize the transport and sorting of goods within facilities, contributing significantly to operational efficiency.
Last Updated on July 30, 2024 by Jordan Smith
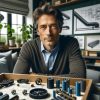
Jordan Smith, a seasoned professional with over 20 years of experience in the conveyor system industry. Jordan’s expertise lies in providing comprehensive solutions for conveyor rollers, belts, and accessories, catering to a wide range of industrial needs. From initial design and configuration to installation and meticulous troubleshooting, Jordan is adept at handling all aspects of conveyor system management. Whether you’re looking to upgrade your production line with efficient conveyor belts, require custom conveyor rollers for specific operations, or need expert advice on selecting the right conveyor accessories for your facility, Jordan is your reliable consultant. For any inquiries or assistance with conveyor system optimization, Jordan is available to share his wealth of knowledge and experience. Feel free to reach out at any time for professional guidance on all matters related to conveyor rollers, belts, and accessories.