Shipping Roller Conveyor: Essential Buyer’s Guide
Shipping roller conveyors play a pivotal role in streamlining operations within the logistics and packaging industries. These systems facilitate the efficient movement of goods by minimizing manual handling, thereby speeding up processing times and reducing labor costs. The functionality of shipping roller conveyors extends beyond mere transport; they also enhance flexibility in warehouse layouts and operations. Key factors that influence the adoption of shipping roller conveyors include operational efficiency, overall cost reduction, and the adaptability they offer to meet varying demand conditions. This versatility makes shipping roller conveyors an indispensable tool in modern supply chain management, helping businesses optimize their delivery and handling processes to stay competitive.
What are Shipping Roller Conveyors
A shipping roller conveyor is a mechanized system designed to transport goods and materials along a predefined path using a series of rollers. These conveyors leverage gravity or motor power to move items, significantly reducing the need for manual labor and enhancing workflow efficiency. In gravity roller conveyors, which are a subset of shipping roller conveyors, the incline of the conveyor uses gravitational force to propel goods forward. This feature is particularly beneficial for shipping operations as it simplifies the movement of bulk items and reduces energy costs. Examples where gravity roller conveyors are advantageous include loading docks, packaging lines, and assembly areas, providing a seamless flow of goods.
Types of Shipping Roller Conveyors
Shipping roller conveyors come in various types to suit different industrial needs. The main types include:
- Gravity Roller Conveyors: These rely on the slope of the conveyor and gravity to move items and are ideal for situations where power is unavailable or unnecessary.
- Heavy-Duty Gravity Roller Conveyors: Built with thicker gauge rollers and stronger frames, these conveyors are designed to handle heavier loads, making them suitable for moving large and heavy products such as machinery or large containers.
- Powered Roller Conveyors: These conveyors use motorized rollers to move goods and are essential in situations requiring the movement of items over long distances or when precise control of the movement is needed.
Additionally, shipping roller conveyors are often customized with different features to meet specific requirements. Examples of such features include:
- Adjustable stands: These allow the height of the conveyor to be modified according to operational needs.
- Portable Roller Conveyors: Easily movable, these conveyors are excellent for flexible usage across various locations within a facility.
- Extendable sections: These sections can be expanded or contracted to fit the space and operational requirements, offering versatility in handling different sized loads.
- Curved sections: Facilitate changes in the direction of goods movement, useful in complex warehouse layouts.
- Accumulation features: These allow goods to accumulate at a particular location on the conveyor, useful for batch processing or staged packaging.
Each type and feature of shipping roller conveyors enhances different aspects of shipping and handling, making them a versatile and indispensable component in modern logistics and distribution centers.
Key Considerations for Choosing Shipping Roller Conveyors
Assessing Needs and Applications
Selecting the right shipping roller conveyor requires a thorough understanding of the specific operational needs of a shipping or packaging facility.
- Volume of Goods: High-volume operations might benefit from automated, powered roller conveyors to handle continuous flow efficiently.
- Type of Goods: Fragile items may require roller conveyors with softer surfaces or those equipped with cushioning rollers to prevent damage.
- Operational Speed: Facilities prioritizing speed might opt for motorized roller conveyors that can move items quickly from point A to B.
- Space Constraints: Compact or flexible environments could make the best use of portable or expandable roller conveyors that adjust to available space.
- Workforce Availability: In areas with limited labor, fully automated shipping roller conveyors reduce the need for manual handling.
Choosing the right type of roller conveyor for the task at hand ensures optimal performance and cost-efficiency.
- Gravity Roller Conveyors are best suited for operations where manual or gravity propulsion is feasible, reducing energy costs.
- Powered Roller Conveyors are essential in automated warehouses where high efficiency and volume are critical.
- Flexible Roller Conveyors are ideal for facilities with fluctuating operational layouts and sporadic needs.
- Heavy-Duty Roller Conveyors fit well in industrial environments handling heavy or bulky items.
- Accumulating Conveyors are chosen for operations requiring staging or batching of products before further processing.
Price Considerations
The cost of shipping roller conveyors can vary widely based on several factors. These include the type of conveyor, materials used, length and width of the conveyor, and whether it is custom-fitted for specific tasks. To find the best deals on shipping roller conveyors, consider these five tips:
- Compare Prices: Shop around with multiple suppliers to find competitive pricing on models that fit your needs.
- Consider Used Equipment: Purchasing used shipping roller conveyors can offer significant savings. Ensure they are in good condition and suitable for your operation’s requirements.
- Bulk Purchases: Sometimes, buying in bulk can lead to discounts. If you foresee expanding or need multiple units, this could be a cost-effective option.
- Negotiate with Suppliers: Don’t hesitate to negotiate pricing, especially when ordering customized solutions or multiple units.
- Lease or Rent: For short-term needs or budget constraints, consider leasing or renting shipping roller conveyors instead of purchasing outright.
These considerations will guide you in making an informed decision when choosing shipping roller conveyors, ensuring that you receive the best value for your investment while adequately addressing your logistical needs.
Manufacturers and Sources for Shipping Roller Conveyors
Choosing the right manufacturer for your shipping roller conveyor is crucial for ensuring reliability, durability, and efficiency in your logistics operations. Here are insights into selecting a reputable manufacturer, along with examples of criteria to consider:
Leading Shipping Roller Conveyor Manufacturers
Several manufacturers are well-known for their quality and innovation in producing shipping roller conveyors. While specific names cannot be endorsed here, leading companies in this field are typically characterized by their extensive experience, wide range of products, and a strong focus on technological advancements. These manufacturers often invest heavily in research and development to offer more efficient, durable, and adaptable conveyor solutions, catering to a diverse range of industries from e-commerce and automotive to food processing and pharmaceuticals.
Advice on Selecting a Manufacturer
- Reliability: Look for manufacturers with a proven track record. Check their history, years in business, and past client testimonials. A reliable manufacturer should consistently deliver quality products and honor their commitments, such as warranty terms and delivery deadlines.
- Product Range: Assess whether the manufacturer offers a variety of conveyor types that could match your specific needs. A broad product range suggests the manufacturer can provide tailored solutions whether you need gravity roller conveyors, motorized conveyors, or specialized configurations like curved or spiral conveyors.
- Customer Service: Excellent customer service is crucial. This includes pre-sale consultations to understand your needs, responsive support for any issues during and after installation, and available maintenance services. Good customer service ensures you can count on prompt assistance whenever needed.
- Technical Support: A manufacturer that offers comprehensive technical support can be invaluable, especially when integrating complex logistic systems. This includes assistance with system design, installation, troubleshooting, and upgrades.
- Innovative Capabilities: Opt for manufacturers that are leaders in innovation. Those who continually evolve their product offerings to incorporate the latest technologies, such as automated control systems or advanced materials for higher durability and efficiency, will provide you with more advanced and future-proof solutions.
Selecting the right manufacturer for your shipping roller conveyor not only influences the efficiency and effectiveness of your operations but also impacts long-term maintenance costs and scalability. Take the time to evaluate each manufacturer’s strengths in relation to your specific requirements to ensure a successful investment.
Parts and Maintenance of Shipping Roller Conveyors
Maintaining a shipping roller conveyor is critical to ensure it operates efficiently and lasts as long as possible. Understanding the common parts and how to maintain them can significantly impact the productivity and uptime of your conveyor systems.
Common Parts of Shipping Roller Conveyors and Their Functions
Shipping roller conveyors consist of several key components, each crucial for the system’s proper function:
- Rollers: These are the main parts that carry the load. They need to be durable and designed to handle the specific weights and types of materials transported.
- Frame: This supports the rollers and must be robust enough to withstand the load and the stress of continuous operation.
- Motor (for powered conveyors): Provides the necessary power to drive the rollers and move the goods along the conveyor.
- Bearings: These help reduce friction between the rollers and the frame, ensuring smooth roller movement.
- Control System (for automated conveyors): Manages the operation speed and direction of the conveyor, crucial for synchronizing with other automated processes in the facility.
Tips on Maintaining Your Shipping Roller Conveyor
Regular maintenance is essential to prevent breakdowns and extend the life of your shipping roller conveyor. Here are five maintenance tips:
- Regular Inspections: Conduct routine inspections to identify wear and tear on rollers, bearings, and other mechanical parts. Early detection of issues like misalignment or damage can prevent more serious problems and costly downtimes.
- Lubrication: Proper lubrication of bearings and other moving parts is crucial. This reduces friction, prevents overheating, and prolongs the lifespan of these components. Use the recommended type of lubricant and follow the manufacturer’s guidelines for application intervals.
- Cleaning: Keep the conveyor clean from dust, debris, and spills. Buildup can hinder roller movement and attract pests or cause corrosion, particularly in critical areas like bearings and motor housings.
- Checking Belt Tension and Alignment (if applicable): For roller conveyors that use belts or chains, regularly check and adjust the tension and alignment. Incorrect tension or misalignment can lead to inefficient operation and increased wear.
- Replacement of Worn Parts: Replace worn or damaged parts promptly to avoid affecting the conveyor’s efficiency and the potential risk of damaging other components. Keeping spare parts on hand can minimize downtime during repairs.
By following these maintenance tips, you can ensure that your shipping roller conveyor remains in optimal working condition, providing reliable service and maintaining efficiency in your logistical operations.
Buying Guide for Shipping Roller Conveyors
When you are in the market for a shipping roller conveyor, deciding between new and used options and knowing where to look can significantly influence your purchasing decision.
New vs. Used Shipping Roller Conveyors
Pros of Buying New:
- Latest Technology: New shipping roller conveyors often incorporate the latest technology, offering improved efficiency, better integration with other systems, and advanced features like adjustable speeds and automated controls.
- Warranty: New equipment typically comes with a manufacturer’s warranty, providing protection against early failures and defects.
- Customization: When buying new, you can have the conveyor customized to specific requirements of your operation, ensuring optimal performance.
- Longer Lifespan: A new shipping roller conveyor will generally have a longer operational life compared to a used one, potentially providing better long-term value.
- Less Maintenance: New conveyors are less likely to require maintenance in the near term, reducing downtime and maintenance costs.
Cons of Buying Used:
- Unknown History: Used conveyors come with a history that might include unknown wear and tear, potentially leading to unexpected breakdowns.
- Shorter Lifespan: A used conveyor has already been in use, which can significantly decrease its remaining operational lifespan.
- Limited Customization: What you see is typically what you get with used equipment; there is little room for modifications or upgrades.
- Maintenance Costs: While initial costs might be lower, used conveyors may require more frequent repairs and maintenance.
- No Warranty: Used equipment seldom comes with a warranty, which means you will bear the full cost of any repairs or replacements.
Considerations for Quality and Durability in Used Equipment:
When considering used shipping roller conveyors, it’s crucial to:
- Inspect the Equipment Thoroughly: Check for signs of wear and damage, especially on rollers, belts, and motor parts.
- Ask for Operational History: Understanding how the equipment was used and maintained can give insights into potential future issues.
- Test Before Purchasing: If possible, see the conveyor in operation to ensure it works smoothly and meets your needs.
- Check for Availability of Replacement Parts: Ensure that you can easily source parts for maintenance or repair.
- Seek Professional Advice: Have a knowledgeable technician assess the conveyor’s condition before making a purchase.
Finding Shipping Roller Conveyors for Sale
To locate the right shipping roller conveyor for your needs, consider these avenues:
- Industry Marketplaces: Websites that specialize in industrial equipment often list both new and used conveyors from various sellers, providing a wide selection of options.
- Direct Manufacturers: Purchasing directly from manufacturers can provide access to the latest models and customization options.
- Equipment Auctions: Auctions can be a source of high-quality used conveyors at potentially lower prices.
- Local Suppliers: Checking with local industrial equipment suppliers can offer the advantage of seeing the equipment in person before buying.
- Trade Shows: Industry trade shows often feature the newest technology and provide opportunities to negotiate directly with manufacturers or distributors.
Whether choosing new or used, or sourcing from marketplaces or direct manufacturers, the right preparation and knowledge can lead you to the best shipping roller conveyor for your operational needs.
FAQs About Shipping Roller Conveyor
A roller conveyor is a type of conveyor system used predominantly in material handling and packaging operations to move products or loads across an area. This system utilizes a series of rollers mounted in a frame, which can either be powered or unpowered (gravity-driven). Powered roller conveyors use motors to move the rollers, while gravity roller conveyors rely on a slight downward tilt of the conveyor to allow items to slide across the rollers from one end to the other, utilizing gravity. Roller conveyors are particularly favored for their simplicity, efficiency, and ability to handle a wide range of products, regardless of shape, size, and weight. They are highly adaptable and can be customized with curves, gates, and other features to fit specific operational needs.
The rollers on a conveyor are the cylindrical components that spin and carry goods along the conveyor system. They are a critical part of roller conveyors and are designed to support and move products efficiently. These rollers can vary significantly in size, material, and design based on their intended use. Common materials used for rollers include metal, plastic, and rubber-coated rollers. Metal rollers are durable and ideal for heavy loads, while plastic rollers are lighter and suitable for lighter items. Rubber-coated rollers offer additional grip and cushioning, which helps in transporting delicate items without damage. The choice of roller type directly impacts the conveyor’s effectiveness in different environments and applications.
In packaging operations, several types of conveyors are used, but belt conveyors and roller conveyors are the most common. Roller conveyors are particularly prevalent due to their ability to handle various packages, such as boxes, trays, and pallets, efficiently. They can be easily integrated into packaging lines to facilitate the movement, sorting, and accumulation of products before, during, and after the packaging process. Gravity roller conveyors are often used for simple transfer tasks, whereas powered roller conveyors are utilized for more complex or longer-distance transportation needs within a packaging facility. The choice of conveyor in packaging depends on factors like the speed of operation, the size and weight of packages, and the degree of automation required.
Conveyor rollers come in a wide range of sizes, which can be selected based on the specific requirements of the operation where they are used. The diameter of conveyor rollers typically ranges from as small as 20 millimeters to more than 200 millimeters. The width of the rollers also varies, commonly from a few inches to several feet, depending on the width of the conveyor belt or frame they are meant to fit within. When choosing the size of conveyor rollers, considerations include the type of materials to be conveyed, the load weight, the conveyor speed, and the overall system design. Smaller rollers are generally used for lighter loads and smaller items, while larger rollers are better suited for heavier and bulkier items.
Last Updated on August 1, 2024 by Jordan Smith
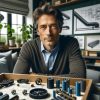
Jordan Smith, a seasoned professional with over 20 years of experience in the conveyor system industry. Jordan’s expertise lies in providing comprehensive solutions for conveyor rollers, belts, and accessories, catering to a wide range of industrial needs. From initial design and configuration to installation and meticulous troubleshooting, Jordan is adept at handling all aspects of conveyor system management. Whether you’re looking to upgrade your production line with efficient conveyor belts, require custom conveyor rollers for specific operations, or need expert advice on selecting the right conveyor accessories for your facility, Jordan is your reliable consultant. For any inquiries or assistance with conveyor system optimization, Jordan is available to share his wealth of knowledge and experience. Feel free to reach out at any time for professional guidance on all matters related to conveyor rollers, belts, and accessories.