UHMWPE Conveyor Roller in Conveyor Belt
The UHMW-PE Roller, prominently featuring as a pivotal component in modern conveyor systems, is engineered from ultra-high molecular weight polyethylene. This material endows the uhmwpe conveyor roller with a robust suite of intrinsic properties that set it apart in industrial applications. Notably, its composition contributes to an unparalleled wear resistance that significantly eclipses traditional materials. Tests and practical use have shown that these rollers possess a wear resistance seven times greater than that of steel and thrice that of nylon. Such exceptional durability not only prolongs the lifespan of the rollers themselves but also contributes to the longevity and reduced maintenance requirements of the conveyor systems they are part of. This remarkable wear resistance, when combined with UHMW-PE’s inherent properties, makes these rollers an indispensable asset in enhancing the efficiency and reliability of conveyor operations across various sectors.
UHMWPE Conveyor Roller Product Features
The UHMWPE conveyor roller offers a sophisticated design with numerous operational benefits crafted to enhance productivity and efficiency in industrial applications. These rollers are manufactured using Ultra High Molecular Weight Polyethylene (UHMWPE), which provides a combination of exceptional qualities to meet various industrial demands. Below are the detailed features of the UHMWPE conveyor rollers:
Anti-Friction and Self-Lubricating
UHMWPE conveyor rollers are highly favored for their anti-friction and self-lubricating properties. The surface of these rollers is inherently slick, which significantly reduces the friction between the conveyor belt and the roller itself. This feature not only minimizes the energy consumption during operation but also extends the life of both the rollers and the conveyor belt. The self-lubricating nature of UHMWPE eliminates the need for periodic lubrication, thereby reducing maintenance requirements and downtime.
Impact Resistance
These rollers are designed to withstand severe impacts thanks to the robustness of UHMWPE material. Even in environments where sharp and heavy objects are processed, UHMWPE conveyor rollers maintain their shape and integrity. This impact resistance ensures that the rollers can handle heavy loads and abusive conditions without deforming, cracking, or breaking, which is crucial for maintaining continuous operations in harsh industrial settings.
Noise and Vibration Reduction
The smooth surface of UHMWPE conveyor rollers significantly contributes to noise and vibration reduction. By providing a quieter operation, these rollers are ideal for facilities that prioritize a reduced sound environment, enhancing work comfort and safety. Furthermore, the decreased vibration helps in maintaining the structural integrity of the conveyor system and prolongs the service life of the equipment.
Anti-Adhesion and Anti-Corrosion
UHMWPE is well-known for its anti-adhesion properties, preventing materials from sticking to the roller surface. This is particularly beneficial in industries where adhesive materials are handled, as it ensures a clean operation and reduces cleaning downtime. Additionally, the chemical resistance of UHMWPE makes these rollers highly resistant to corrosive substances, making them suitable for use in chemical processing plants or outdoor applications where they are exposed to harsh weather conditions.
Anti-Aging
The material properties of UHMWPE include excellent resistance to weathering and aging. Unlike other materials that degrade over time due to environmental exposures such as UV light and extreme temperatures, UHMWPE maintains its mechanical properties and appearance. This anti-aging feature of UHMWPE conveyor rollers ensures that they will continue to perform effectively for a long time, providing a reliable solution for long-term applications.
By integrating these features, UHMWPE conveyor rollers not only enhance operational efficiency but also contribute to lower operational costs and improved safety. Their durability, coupled with minimal maintenance requirements, makes them an ideal choice for any business looking to optimize their material handling processes with reliable and high-performance components.
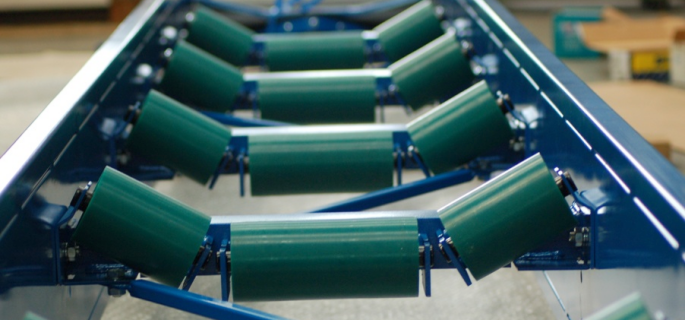
UHMWPE Conveyor Roller Market Reception
Since its introduction to the market, the UHMWPE conveyor roller has consistently received positive acclaim from various sectors of the industry. This reception is a testament to its superior design and the tangible benefits it delivers to operations in manufacturing, distribution, and material handling. Below we explore in detail the market reception of these innovative conveyor rollers:
Customer Feedback
The UHMWPE conveyor roller has been in the market for over two years and during this time, it has garnered overwhelmingly positive feedback from its users. Customers have reported significant improvements in their conveyor operations, highlighting the roller’s effective performance and reliability. The feedback encompasses satisfaction with the roller’s ability to operate smoothly under varying environmental conditions without frequent maintenance. Users have particularly praised the roller’s resistance to wear and abrasion, which significantly cuts down on the need for replacements and thereby reduces the operational costs.
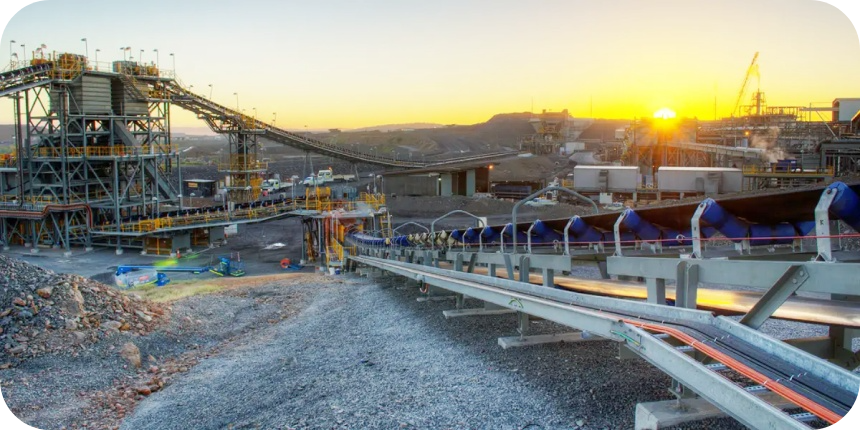
Proven Performance
The performance of the UHMWPE conveyor roller is not just supported by customer testimonials but also by extensive empirical evidence. Rigorous testing and long-term industrial use have consistently demonstrated that these rollers surpass traditional materials in both durability and functionality. Tests have shown that UHMWPE rollers can handle much higher loads and are less likely to deform under pressure, which crucially maintains the integrity of the conveyor belt system.
Further, the material’s low-friction and self-lubricating properties have been proven to reduce energy consumption significantly. This efficiency is not only beneficial in terms of cost but also supports a greener production environment by minimizing operational emissions. The anti-corrosive and anti-adhesive characteristics of the rollers ensure they perform excellently in harsh chemical exposures and sticky material handling applications, respectively.
The UHMWPE conveyor roller stands out in the market not only for its innovative features but also for its proven track record in enhancing conveyor system efficiencies and reducing maintenance hassles. This positive market reception is a clear indicator of its effectiveness and reliability, driving its adoption in more industries seeking to improve their conveyor operations. The combination of customer satisfaction and validated performance metrics strongly advocates for its continued use and integration into sophisticated material handling setups.
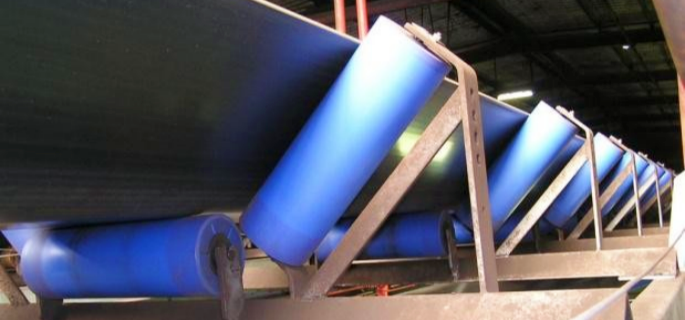
UHMWPE Conveyor Roller Applications
UHMWPE (Ultra High Molecular Weight Polyethylene) conveyor rollers are known for their high durability and excellent wear resistance. They are used in various applications due to their unique properties. Here are some common applications:
1. Mining
- Material Handling: UHMWPE rollers handle abrasive materials like coal, ore, and minerals efficiently, reducing wear and maintenance.
2. Construction
- Heavy Equipment: They are used in conveyors for transporting heavy construction materials like gravel, sand, and cement.
3. Agriculture
- Grain Handling: UHMWPE rollers are ideal for conveyor systems that transport grains and other agricultural products, as they minimize contamination and wear.
4. Recycling
- Sorting and Processing: In recycling plants, UHMWPE rollers handle a variety of materials, including plastics and metals, ensuring smooth operation and longevity.
5. Automotive
- Parts Handling: Used in automotive manufacturing and assembly lines to move parts and components smoothly.
6. Food Processing
- Sanitary Conveyance: UHMWPE rollers are employed in food processing for their resistance to corrosion and ease of cleaning, ensuring hygiene and efficiency.
7. Paper and Pulp
- Paper Transport: They are used in conveyors for transporting paper rolls and pulp, with minimal friction and wear.
8. Industrial Manufacturing
- General Conveyance: UHMWPE rollers are versatile and used in various industrial applications to handle products of different shapes and sizes.
9. Warehousing
- Storage Systems: They are also utilized in warehouse conveyor systems to facilitate the movement of goods and packages.
UHMWPE rollers are valued for their resistance to impact, abrasion, and chemicals, making them suitable for harsh and demanding environments.
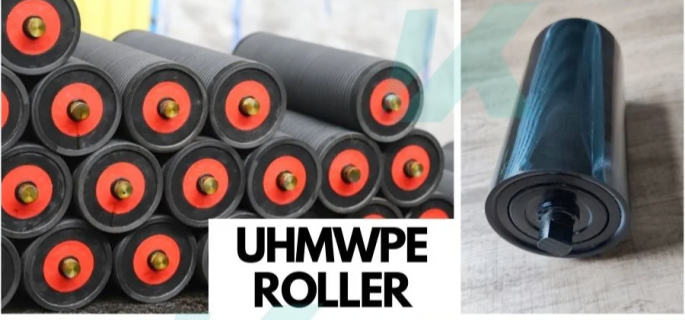
Uses of UHMWPE Conveyor Roller
UHMWPE conveyor rollers are commonly employed in various harsh and demanding environments, which benefit significantly from the unique properties of UHMWPE, such as high impact resistance, anti-corrosion, and minimal friction. Key applications include:
- Metallurgical Mines: In the abrasive and heavy-load conditions of metallurgical mines, UHMWPE rollers offer durability and resistance to wear that metal rollers cannot match.
- Coal Mines: The rollers are used in coal mines to facilitate the smooth and efficient transport of coal, which often involves navigating through tight and uneven spaces.
- Chemical Industries: Given their chemical inertness, these rollers are ideal for moving corrosive materials without degrading over time as traditional materials might.
- Grain Storage Facilities: Their anti-adhesion properties reduce downtime caused by grains sticking to the conveyor, thereby increasing efficiency in material transfer processes.
- Building Material Handling: The robustness of UHMWPE rollers makes them perfect for transporting heavy building materials without the risk of deformation.
- Ports: Handling large quantities of goods often imported or exported in bulk, these rollers can withstand the elements, including salt and moisture, prevalent in maritime climates.
- Salt Fields: UHMWPE’s excellent anti-corrosion properties are crucial in salt fields, where corrosive salt can quickly degrade other materials.
- Electric Power Stations: In the energy sector, reliability and efficiency are paramount; UHMWPE rollers ensure minimal downtime and maintenance.
Industry Adaptability
The physical and chemical properties of the UHMWPE conveyor roller make it particularly useful in environments where traditional metal rollers are less effective. Its durability under physical stress and in chemically aggressive environments means it can perform reliably where other materials would fail. For instance:
- High Impact Applications: The shock-absorbing properties of UHMWPE are ideal for industries involving high-velocity impacts, where brittle materials might crack or shatter.
- Corrosive Environments: Traditional metal rollers often corrode over time when exposed to harsh chemicals or salty conditions, whereas UHMWPE rollers maintain their integrity.
- Areas Requiring Sanitation: The non-porous nature of UHMWPE makes these rollers easier to clean and disinfect, which is particularly important in food processing and pharmaceutical industries.
- Extreme Temperature Zones: Whether exposed to intense cold or heat, UHMWPE remains stable and functional, unlike many conventional materials that can suffer from thermal expansion or become brittle in cold.
The UHMWPE conveyor roller’s robustness, combined with its low maintenance needs and long lifespan, makes it a superior choice for a multitude of sectors aiming to cut operational costs and increase efficiency. These properties not only extend the operational life of the conveyor systems but also enhance safety and reliability, crucial factors in industrial operations. Thus, UHMWPE rollers are increasingly becoming the preferred option in diverse applications across various industries..
Advantages of UHMWPE Conveyor Roller Over Traditional Options
The UHMWPE conveyor roller presents significant improvements over traditional metal rollers, setting a new standard in the materials handling industry. These rollers leverage the advanced properties of Ultra High Molecular Weight Polyethylene (UHMWPE) to enhance operational efficiencies and reduce costs. Below, we detail the specific advantages that UHMWPE conveyor rollers have over their metal counterparts:
Superior to Metal Rollers
UHMWPE conveyor rollers offer comprehensive benefits that extend beyond the capabilities of traditional metal rollers:
- Improved Transportation Capacity: UHMWPE rollers facilitate a higher throughput due to their lower weight compared to metal. This reduction in weight improves the speed and volume of material that can be handled, enhancing the overall efficiency of transportation systems within industrial operations.
- Enhanced Belt Protection: The smooth and non-abrasive surface of UHMWPE rollers minimizes contact damage to conveyor belts. Unlike metal rollers, which can cause significant wear and tear due to their rougher surfaces and susceptibility to rust, UHMWPE rollers ensure that the belts endure less stress, thereby extending their service life and reducing the frequency and costs of belt replacements.
- Reduced Repair Needs: The durability and resilience of UHMWPE to mechanical shocks and environmental factors mean that these rollers seldom fail or need replacements. This substantial reduction in repair and maintenance requirements not only lowers downtime but also minimizes maintenance costs, contributing to more predictable and controlled operational budgets.
- Energy Efficiency: One of the standout features of UHMWPE rollers is their ability to reduce energy consumption. The inherent low friction coefficient of UHMWPE allows for smoother operations with less energy required to overcome resistance, which is a significant improvement over metal rollers. This smoother operation not only saves energy but also reduces the generation of heat and wear on the system, promoting a longer operational lifespan and further energy efficiencies.
Cost-Effectiveness and Environmental Impact
In addition to direct operational advantages, UHMWPE conveyor rollers also offer cost-effectiveness and positive environmental impacts:
- Lifecycle Costs: The long service life and reduced maintenance requirements of UHMWPE rollers decrease the total lifecycle costs compared to metal rollers. Over time, the savings in replacements and repairs can significantly offset the initial investment in UHMWPE rollers.
- Sustainability: UHMWPE is a more environmentally friendly option than metals, which often require energy-intensive processes that produce significant CO2 emissions. The production of UHMWPE rollers involves less energy and generates lower emissions, supporting industrial efforts towards sustainability.
- Recyclability: Unlike some metals which can degrade in quality upon recycling, UHMWPE can be recycled several times without significant loss of quality, further enhancing its environmental profile.
Durability and Longevity
- Wear Resistance: UHMWPE rollers have superior wear resistance compared to traditional materials, reducing the frequency of replacements.
- Impact Resistance: They can withstand high-impact loads without cracking or breaking, enhancing their longevity.
Low Friction and Noise
- Reduced Friction: UHMWPE rollers have a low coefficient of friction, leading to smoother conveyor operation and reduced energy consumption.
- Quieter Operation: Their low-friction properties also result in quieter conveyor systems compared to metal rollers.
Corrosion and Chemical Resistance
- Corrosion-Free: Unlike metal rollers, UHMWPE does not corrode, making it ideal for environments exposed to moisture or chemicals.
- Chemical Resistance: It is resistant to a wide range of chemicals, ensuring durability in various industrial applications.
Lightweight
- Reduced Weight: UHMWPE rollers are significantly lighter than metal rollers, which reduces the overall weight of the conveyor system and can lead to cost savings in shipping and installation.
Lower Maintenance Costs
- Self-Lubricating: The material’s low friction properties reduce the need for additional lubrication, leading to lower maintenance requirements.
- Ease of Cleaning: UHMWPE rollers are easy to clean and maintain, making them suitable for environments with stringent hygiene requirements.
Enhanced Load Capacity
- High Load Bearing: UHMWPE rollers can support substantial loads, making them suitable for heavy-duty applications while maintaining performance.
Temperature Tolerance
- Wide Temperature Range: UHMWPE can operate effectively across a broad temperature range, from very low to high temperatures, without losing its properties.
Environmental Impact
- Recyclability: UHMWPE is recyclable, making it a more environmentally friendly option compared to some traditional materials.
Customization
- Versatility: UHMWPE rollers can be easily customized in terms of size, shape, and additional features, allowing for tailored solutions to specific conveyor needs.
The UHMWPE conveyor roller not only surpasses traditional metal rollers in performance and durability but also offers additional benefits in terms of cost savings, energy efficiency, and environmental impact. These advantages make UHMWPE rollers a prudent choice for industries looking to improve their conveyor operations sustainably and economically.
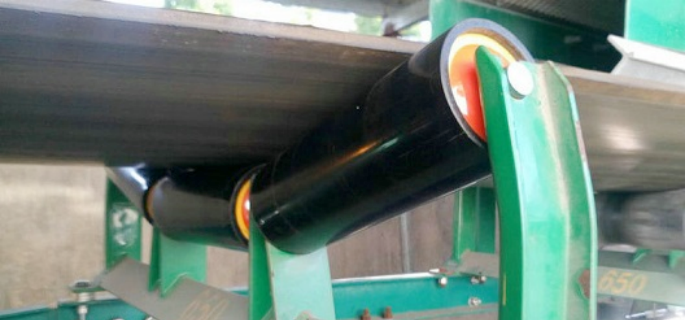
Economic Benefits of UHMWPE Conveyor Roller
The UHMWPE conveyor roller, through its superior material properties and performance efficiencies, offers compelling economic benefits to industries that incorporate it into their operations. These rollers not only enhance the productivity and longevity of conveyor systems but also contribute to substantial cost savings over time. Here we detail the notable economic advantages and the return on investment these rollers provide:
Cost-Effectiveness
The UHMWPE conveyor roller brings about cost-effectiveness through several key economic advantages:
- Reduced Maintenance Costs: Due to the high wear resistance and self-lubricating properties of UHMWPE, these rollers require less frequent replacement and minimal maintenance. This significant reduction in maintenance needs eliminates the frequent downtime and labor costs associated with replacing or repairing less durable rollers.
- Lower Energy Usage: The low friction coefficient of UHMWPE not only improves the operational smoothness of conveyor systems but also reduces the energy required to operate them. This decreased energy demand results in lower electricity costs and contributes to a more environmentally friendly operation.
- Decreased Conveyor Belt Wear: UHMWPE rollers are softer on conveyor belts compared to metal rollers. This softness, combined with their smooth surface, greatly reduces the wear and tear on belts, thereby extending the belts’ lifespan and decreasing the costs and interruptions caused by belt failures.
- Enhanced Productivity: With smoother and faster operations enabled by UHMWPE rollers, production timelines are optimized. This efficiency can lead to higher throughput and potentially increased revenue, making a direct impact on the profitability of operations.
- Longevity: The inherent properties of UHMWPE ensure that these rollers last significantly longer than traditional materials, especially in corrosive or abrasive environments. The extended lifespan of the rollers reduces the need for frequent replacements, thus saving costs related to procurement and installation.
Return on Investment
Investing in UHMWPE conveyor rollers yields a high return on investment (ROI) due to several factors:
- Prolonged Service Life: The durability of UHMWPE means that these rollers do not need to be replaced as often as metal rollers. This longevity not only saves money in terms of direct replacement costs but also in the indirect costs of downtime and reduced disruption to operations.
- Efficiency Gains: The smoother operation of conveyors fitted with UHMWPE rollers leads to lower operational costs. These rollers can handle higher loads and speeds, which translates into more efficient production processes and lower per-unit costs of operation.
- Operational Cost Reductions: The sum total of maintenance savings, enhanced productivity, reduced energy consumption, and extended equipment life all contribute to significant operational cost reductions. These savings make the initial investment in UHMWPE rollers worthwhile, as the cost is offset by the numerous economic benefits realized over the rollers’ operational lifetime.
The economic benefits of UHMWPE conveyor rollers are evident in their cost-effectiveness and strong return on investment. Industries employing these rollers can expect reduced operational costs, enhanced system longevity, and greater overall efficiency, which are critical factors in achieving long-term profitability and competitive advantage. These benefits underscore why UHMWPE conveyor rollers are becoming an increasingly popular choice in various sectors seeking to optimize their conveyor operations economically.
For custom uhmwpe-conveyor-roller solutions, submit your details through this form.
FAQs about UHMWPE Conveyor Roller
UHMW and UHMWPE are actually two different terms for the same material. UHMW is an acronym for Ultra High Molecular Weight, usually referring to a type of polyethylene plastic. On the other hand, UHMWPE stands for Ultra High Molecular Weight Polyethylene. Both terms refer to a highly durable type of plastic known for its high impact strength, low friction properties, and excellent resistance to abrasion and wear. Industries use this material for a variety of applications where durability and resistance to various forms of physical stress are critical.
Conveyor rollers are used in various industries to transport materials and goods from one point to another. These rollers can be made from different materials depending on the specific use case. Steel rollers are commonly used due to their strength and durability. However, UHMWPE rollers are gaining popularity because they offer a lighter, yet equally sturdy, alternative with excellent durability, wear resistance, and low friction properties. These characteristics make UHMWPE rollers well-suited in environments where noise reduction, material protection, and low maintenance are crucial.
Yes, Ultra High Molecular Weight Polyethylene (UHMWPE) is extraordinarily durable. UHMWPE is known for its high impact strength, excellent resistance to wear and abrasion, and low friction properties, which contribute to its durability. It’s considered to be seven times more wear-resistant than steel and three times more wear-resistant than nylon, making it highly sought after in industries that require durable materials, such as mining, transport, and materials handling.
Motor Driven Roller (MDR) technology is commonly used in the conveyor industry, and several manufacturers are specialized in producing these rollers. The specific producer of an MDR Roller can vary depending on geographic location and specific hardware requirements. Some notable manufacturers include Itoh Denki and Interroll, but these are just a couple of examples. Many companies manufacture MDR rollers, each with their specifications and capabilities. To find an accurate answer, it is recommended to consider the specific requirements and conduct a comprehensive market research or consult a specialist in the field.
Last Updated on August 2, 2024 by Jordan Smith
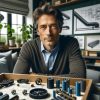
Jordan Smith, a seasoned professional with over 20 years of experience in the conveyor system industry. Jordan’s expertise lies in providing comprehensive solutions for conveyor rollers, belts, and accessories, catering to a wide range of industrial needs. From initial design and configuration to installation and meticulous troubleshooting, Jordan is adept at handling all aspects of conveyor system management. Whether you’re looking to upgrade your production line with efficient conveyor belts, require custom conveyor rollers for specific operations, or need expert advice on selecting the right conveyor accessories for your facility, Jordan is your reliable consultant. For any inquiries or assistance with conveyor system optimization, Jordan is available to share his wealth of knowledge and experience. Feel free to reach out at any time for professional guidance on all matters related to conveyor rollers, belts, and accessories.