Conveyor Roller Balls: Essentials for Efficient Material Handling
Conveyor roller balls, also known as ball transfer units, are innovative devices designed to facilitate the smooth and precise transfer of goods across industrial environments. Comprising a large ball seated on a bed of smaller balls enclosed in a casing, these units allow for load movement in any direction with minimal effort. The simplicity and efficiency of conveyor roller balls make them indispensable in assembly lines, packaging facilities, and material handling tasks where traditional fixed-path conveyors are less effective. They are particularly valuable in sectors such as automotive, aerospace, and manufacturing, where versatility in movement and spatial efficiency are crucial. By enabling the repositioning of heavy loads quickly and safely, conveyor roller balls enhance workflow and productivity, reflecting their importance in modern industrial operations.
What are Conveyor Roller Balls
Conveyor roller balls, also recognized as ball transfer units, play a pivotal role in the field of material handling, offering unparalleled flexibility and efficiency. These units are specially designed to facilitate the easy and swift movement of goods in various directions, which traditional conveyor systems may not support. This section delves into the fundamentals of conveyor roller balls, exploring their design, mechanics, and the types available for different industrial applications.
Definition and Mechanics
Conveyor roller balls consist of a large spherical ball supported by smaller balls inside a housing, allowing the top ball to rotate smoothly in any direction. The design ensures that items can glide over the ball surface with minimal friction and resistance, which is critical for applications requiring precision and ease of movement. The mechanics behind these units involve two key components:
- Spherical Top Ball: Acts as the main contact point for moving objects, capable of 360-degree rotation and offering versatility in direction.
- Support Balls: Positioned precisely to create a uniform plane that supports the large ball, enabling consistent performance under load.
The arrangement of these balls within the unit allows for load distribution over a wide area, reducing the chance of indentation on the transported item while maintaining stability and alignment during movement.
Types of Conveyor Roller Balls
To cater to different operational demands, conveyor roller balls are available in various designs and load capacities. Here’s a detailed look at the common types:
Type | Description | Typical Use |
---|---|---|
Heavy Duty Conveyor Roller Balls | Designed to withstand high loads; robust construction. | Used in industries like automotive for moving large parts. |
Mini Ball Transfer Bearings | Compact and precise; suitable for light tasks. | Ideal for electronics manufacturing and delicate assemblies. |
Ball Transfer Conveyor Strips | Extended strips fitted with multiple units for linear motion. | Perfect for packaging lines and sorting centers. |
Each type of conveyor roller ball is engineered to meet specific operational needs, whether it’s handling heavy machinery parts or ensuring the precise assembly of sensitive components. Heavy duty conveyor roller balls are typically made from materials like steel or stainless steel, offering durability and resistance to wear and environmental factors. Mini ball transfer bearings, while smaller in size, provide the same multi-directional functionality but are more suited for light loads and delicate movements. Lastly, ball transfer conveyor strips are utilized to create a stable and consistent pathway for goods to move over longer distances within manufacturing plants and distribution hubs.
Understanding the different types of conveyor roller balls and their specific applications helps in selecting the right unit that best fits the operational requirements and enhances the efficiency of material handling systems. This knowledge is essential for businesses looking to optimize their production or distribution setups with effective conveyor solutions.
Applications of Ball Transfer Units
Industrial Uses
Conveyor roller balls find extensive applications across various industries, offering efficient and versatile material transport solutions:
- Manufacturing and Assembly Lines: In manufacturing and assembly operations, conveyor roller balls are used to facilitate the movement of materials, components, and finished products along production lines. They enable smooth and precise transfer of items between workstations, reducing manual handling and streamlining workflows.
- Automotive Industry: In the automotive sector, conveyor roller balls are utilized for transporting vehicle components, parts, and assemblies during assembly processes. They support efficient material flow and assembly operations, ensuring timely completion of vehicles with high levels of precision and quality.
- Food Processing and Packaging: In the food processing and packaging industry, conveyor roller balls are employed for handling packaged foods, beverages, and perishable goods. They facilitate gentle and hygienic transportation of products along conveyor lines, minimizing product damage and contamination risks.
- Warehousing and Distribution: In warehousing and distribution centers, conveyor roller balls play a crucial role in sorting, picking, packing, and shipping operations. They enable fast and efficient movement of goods within the facility, from receiving docks to storage areas and outbound shipping lanes, enhancing order fulfillment and logistics efficiency.
- Logistics and Supply Chain: In logistics and supply chain operations, conveyor roller balls are used for loading and unloading cargo containers, trucks, and trailers. They enable smooth and seamless transfer of goods between transportation vehicles and warehouse facilities, optimizing material flow and throughput.
- Material Handling Equipment: Conveyor roller balls are also integrated into various material handling equipment, such as gravity conveyors, ball transfer tables, and transfer carts, to facilitate efficient movement of materials in warehouses, production facilities, and distribution centers.
Benefits in Material Handling
The use of conveyor roller balls offers several advantages in material handling applications:
- Improved Maneuverability: Conveyor roller balls provide omnidirectional movement, allowing items to be easily maneuvered in any direction on the conveyor surface, enhancing flexibility and adaptability in material handling operations.
- Decreased Wear on Items: The smooth and frictionless surface of conveyor roller balls minimizes wear and damage to transported items, ensuring product integrity and reducing maintenance costs associated with conveyor systems.
- Increased Processing Speed: Conveyor roller balls enable high-speed material transfer and sorting, increasing throughput and productivity in manufacturing, distribution, and logistics operations.
- Versatility: Conveyor roller balls can be used with a wide range of materials, including boxes, packages, and irregularly shaped items, making them suitable for diverse material handling applications in various industries.
- Reduced Labor Requirements: Automated conveyor systems equipped with roller balls reduce the need for manual labor in material handling tasks, improving efficiency and worker safety in industrial environments.
- Space Optimization: Conveyor roller balls allow for compact and space-saving conveyor designs, maximizing floor space utilization in warehouses, production facilities, and distribution centers.
- Easy Installation and Maintenance: Conveyor roller balls are easy to install and require minimal maintenance, contributing to reduced downtime and lower operating costs over the lifespan of the conveyor system.
- Enhanced Safety: Conveyor roller balls feature built-in safety features such as ball retainer caps and seals to prevent contaminants from entering the bearing, ensuring safe and reliable operation in demanding industrial environments.
By leveraging the benefits of conveyor roller balls in material handling applications, industries can optimize workflows, increase efficiency, and achieve operational excellence in their respective fields.
Key Products and Where to Find Conveyor Roller Balls
Popular Models and Their Features
- Heavy Duty Ball Rollers Heavy-duty ball rollers are designed to withstand high loads and rugged operating conditions. These rollers typically feature robust construction with durable materials such as steel or stainless steel, ensuring long-term reliability and performance. They are commonly used in applications requiring the transportation of heavy items or materials, such as automotive assembly lines, manufacturing plants, and distribution centers. Heavy-duty ball rollers come in various sizes and load capacities to accommodate different requirements, providing flexibility and versatility in material handling operations.
- Roller Ball Transfer Bearings Roller ball transfer bearings are precision-engineered components that facilitate smooth and efficient material transfer along conveyor systems. These bearings consist of multiple ball bearings housed within a circular or spherical housing, allowing for omnidirectional movement and rotation. Roller ball transfer bearings are commonly used at transfer points or junctions in conveyor lines to redirect or reposition items with minimal friction and resistance. They help improve conveyor system efficiency by reducing rotational friction and minimizing the risk of product damage during material transfer.
Shopping for Conveyor Roller Balls
When shopping for conveyor roller balls, whether new or used, consider the following tips to ensure quality and reliability:
- Evaluate Load Capacity: Determine the maximum load capacity required for your application and select roller balls that can accommodate the weight of the heaviest items to be transported.
- Check Material and Construction: Inspect the material and construction of the roller balls to ensure they are durable and suitable for your application’s operating conditions.
- Assess Bearing Quality: Examine the quality of the ball bearings within the roller balls, ensuring smooth and frictionless rotation for efficient material handling.
- Consider Environmental Factors: Take into account environmental factors such as temperature, humidity, and exposure to dust or moisture, and choose roller balls with appropriate sealing and protection features to prevent contamination and damage.
- Verify Compatibility: Ensure compatibility with your existing conveyor system components, including conveyor frames, tracks, and mounting brackets, to facilitate seamless integration and operation.
- Review Manufacturer Reputation: Research the reputation and track record of the manufacturer or supplier, opting for reputable brands known for producing high-quality conveyor roller balls.
- Inspect Used Units Thoroughly: If purchasing used conveyor roller balls, thoroughly inspect them for signs of wear, damage, or deterioration, and test their functionality before making a purchase.
- Request Warranty and Support: Inquire about warranty coverage and after-sales support options from the manufacturer or supplier to address any potential issues or concerns after purchase.
- Seek Recommendations: Seek recommendations from industry experts, colleagues, or trusted sources to identify reliable suppliers or brands of conveyor roller balls.
- Compare Prices and Features: Compare prices and features of different conveyor roller ball models to find the best value for your investment, considering factors such as load capacity, bearing quality, and durability.
- Consider Customization Options: Explore customization options offered by manufacturers to tailor conveyor roller balls to your specific application requirements, such as size, load capacity, and mounting configurations.
- Plan for Maintenance: Develop a maintenance plan for conveyor roller balls to ensure proper lubrication, inspection, and replacement as needed, maximizing their lifespan and performance over time.
By following these tips, businesses can make informed decisions when purchasing conveyor roller balls, whether new or used, and ensure the reliability and efficiency of their material handling systems.
Installation and Maintenance of Conveyor Roller Balls
Setting Up Ball Transfer Tables
Installing ball transfer tables or conveyor strips with conveyor roller balls involves several steps to ensure proper setup and functionality:
- Preparation: Gather all necessary tools and equipment for installation, including mounting brackets, fasteners, and alignment tools.
- Positioning: Determine the location and orientation of the ball transfer table within your conveyor system layout, ensuring proper alignment with adjoining conveyor sections or workstations.
- Mounting: Secure the ball transfer table to the conveyor frame or support structure using mounting brackets or fasteners, ensuring it is level and securely attached to prevent movement during operation.
- Alignment: Adjust the position and alignment of individual ball transfer units within the table to ensure smooth and consistent movement of items across the surface. Verify that the ball transfer units are evenly spaced and aligned to prevent jams or uneven loading.
- Testing: Test the ball transfer table to ensure all roller balls are functioning correctly and moving smoothly. Verify that items can be easily transferred across the surface without sticking or binding, and make any necessary adjustments to optimize performance.
Maintenance Tips
To prolong the life of conveyor roller balls and ensure optimal performance, follow these routine maintenance practices:
- Regular Cleaning: Clean the surface of the ball transfer table regularly to remove dirt, debris, and other contaminants that can impair the movement of roller balls. Use a mild detergent solution and a soft brush or cloth to clean the surface thoroughly.
- Lubrication: Apply lubricant to the roller balls and bearings periodically to reduce friction and prevent wear. Use a lubricant recommended by the manufacturer and apply it according to the specified intervals to maintain smooth operation.
- Inspect Bearings: Check the condition of the bearings in the roller balls regularly for signs of wear, damage, or corrosion. Replace any worn or damaged bearings promptly to prevent further deterioration and ensure smooth rotation.
- Tighten Fasteners: Inspect mounting brackets, fasteners, and other hardware regularly to ensure they are tight and secure. Tighten any loose fasteners or connections to prevent movement or instability in the ball transfer table.
- Check Alignment: Verify the alignment of the ball transfer units within the table periodically to ensure they are evenly spaced and aligned. Adjust any misaligned units to prevent uneven loading and premature wear on roller balls.
- Monitor Load Capacity: Avoid overloading the ball transfer table beyond its rated capacity, as this can lead to excessive wear and damage to roller balls and bearings. Monitor the load capacity of the table and distribute loads evenly to prevent overloading.
- Inspect Surface Condition: Check the surface condition of the ball transfer table regularly for signs of damage, wear, or deformation. Repair or replace any damaged or worn areas to maintain a smooth and level surface for optimal performance.
- Schedule Maintenance: Establish a regular maintenance schedule for the ball transfer table, including cleaning, lubrication, and inspection tasks. Follow the manufacturer’s recommendations for maintenance intervals and procedures to ensure proper care and longevity of conveyor roller balls and components.
By following these maintenance tips, businesses can ensure the reliable operation and longevity of ball transfer tables and conveyor roller balls, minimizing downtime and optimizing material handling efficiency in their operations.
Conveyor Roller Balls’ Manufacturers and Distributors
Leading Suppliers
When it comes to sourcing high-quality conveyor roller balls, several reputable brands and manufacturers specialize in producing reliable and durable ball transfer units:
- Interroll: Interroll is a leading global provider of material handling solutions, offering a wide range of conveyor components, including conveyor roller balls. Known for their innovative designs and superior quality, Interroll’s ball transfer units are widely used in various industries for efficient material transport.
- Omni Metalcraft Corp.: Omni Metalcraft Corp. is a trusted manufacturer of conveyor systems and components, including ball transfer tables and units. Their products are known for their durability, versatility, and precision engineering, making them suitable for a wide range of material handling applications.
- Alwayse Engineering: Alwayse Engineering is a UK-based company specializing in the design and manufacture of ball transfer units since 1939. With a reputation for excellence and reliability, Alwayse Engineering’s products are used in diverse industries worldwide for their smooth and precise material handling capabilities.
- Hudson Bearings: Hudson Bearings is a leading manufacturer of ball transfer units and related products, offering a comprehensive range of sizes and configurations to meet various application requirements. Their ball transfer units are designed for smooth and reliable movement of materials in conveyor systems.
- Richards-Wilcox Conveyor Systems: Richards-Wilcox Conveyor Systems is a trusted name in the material handling industry, providing innovative conveyor solutions and components, including ball transfer units. Their products are known for their durability, performance, and ease of integration into conveyor systems.
- Rexnord: Rexnord is a global leader in providing power transmission and conveyor solutions, offering a wide range of conveyor components, including ball transfer units. Their products are designed to withstand demanding operating conditions and ensure smooth material transfer in conveyor applications.
- Bishop-Wisecarver Group: Bishop-Wisecarver Group is a leading manufacturer of guided motion solutions, including ball transfer units for material handling applications. With a focus on innovation and quality, Bishop-Wisecarver Group’s products are trusted by industries worldwide for their reliability and performance.
- McNichols Conveyor Company: McNichols Conveyor Company specializes in providing conveyor systems and components, including ball transfer units, for a variety of industries. Their products are known for their durability, versatility, and ease of installation, making them a preferred choice for material handling applications.
Where to Find Conveyor Roller Balls
Conveyor roller balls can be found for sale through various channels, including:
- Industrial suppliers and distributors specializing in conveyor components and systems.
- Online marketplaces and e-commerce platforms offering a wide selection of conveyor roller balls from different manufacturers.
- Directly from manufacturers’ websites or authorized dealers, ensuring access to genuine products and comprehensive customer support.
- Local hardware stores or material handling equipment suppliers that stock conveyor components and accessories for industrial applications.
By exploring these sources, businesses can find a variety of conveyor roller balls to suit their specific requirements, whether for new installations, replacements, or upgrades to existing conveyor systems.
FAQs about Conveyor Roller Balls
A ball roller, often associated with conveyor systems, is a spherical unit that facilitates the movement and control of goods across a surface. These rollers are adept at allowing items to glide smoothly in any direction, making them vital components in the manufacturing, packaging, and distribution industries where multidirectional mobility is crucial. Unlike traditional fixed-axis rollers that only permit movement along a straight line or predetermined path, ball rollers incorporate a free-rotating ball housed within a supporting cup or frame, providing unparalleled flexibility in handling and maneuvering goods.
The design of ball rollers can vary significantly depending on their application, including factors such as load capacity, material (e.g., steel, nylon), and environment compatibility. Innovations in ball roller technology continue to enhance the efficiency, durability, and range of applications, from simple material transfer solutions to complex, automated assembly and sorting systems. This flexibility and adaptability make ball rollers indispensable to modern material handling and logistics operations.
A ball conveyor is a type of material handling equipment that integrates multiple ball rollers (or ball transfers) into a system designed for moving objects in any direction with minimal effort. Unlike conventional conveyor systems, which typically allow movement in a single linear direction, a ball conveyor enables freer, omnidirectional motion, making it easier to rotate, position, and redirect goods as required. This capability is especially beneficial in workstations, assembly lines, and packing areas where flexibility in movement and positioning of items can significantly boost efficiency and productivity.
Ball conveyors are used in a variety of settings, including airports for baggage handling, manufacturing for movement of parts and assemblies, and retail for stocking and display purposes. The system’s simplicity—coupled with its effectiveness in reducing manual handling, thereby minimizing labor costs and improving safety —makes it a favored choice in numerous industries. By offering versatility in design, from flat surfaces populated with ball units to modular assemblies for specific applications, ball conveyors continue to evolve, addressing the growing and changing needs of material handling and logistics.
Conveyors utilize a range of roller types, each designed to optimize the system for different applications and materials being handled. The choice of roller type significantly impacts the conveyor’s efficiency, durability, and suitability for specific tasks. The most commonly used rollers in conveyors include:
Gravity Rollers: Relying on gravity to move items, these rollers are cost-effective and suited for lightweight goods and applications where manual adjustment is feasible.
Driven Rollers: Powered by motors or belts, driven rollers are essential for automated systems and applications requiring precise speed and direction control.
Grooved Rollers: These are used in conjunction with belts or chains and are mainly found in powered conveyor systems.
Plastic Rollers: Suitable for environments where corrosion resistance is necessary, plastic rollers are lightweight and quiet but have limited load capacity.
Stainless Steel Rollers: Ideal for food processing and pharmaceutical applications due to their corrosion resistance and ease of cleaning.
Tapered Rollers: Utilized in curved sections of conveyor systems, tapered rollers ensure smooth transitions and alignment of items.
Each type of roller offers specific advantages, and the optimal choice depends on factors such as the weight and type of goods being conveyed, environmental conditions, required speed, and desired control level.
A conveyor roller is a cylindrical device that, when assembled with others and mounted in a frame, creates a conveyor system designed to move materials from one location to another. Conveyor rollers can be powered, using internal motors or external drives, or unpowered, relying on gravity or manual force to move items across the surface. The primary purpose of a conveyor roller is to facilitate the easy, safe, and efficient transport of goods, reducing manual handling requirements and optimizing workflow.
Conveyor rollers are made from various materials, including metal, plastic, and rubber, each offering different benefits in terms of load capacity, durability, and application compatibility. These rollers are critical components in numerous industries, including manufacturing, logistics, food processing, and retail, allowing for the streamlined movement of products through production lines, warehouses, and distribution centers.
The design and specification of conveyor rollers depend on several factors, including the system’s intended use, the environment in which it will operate, and the properties of the items it will transport. Innovations in roller technology and materials have greatly expanded their applications, enhancing conveyor system performance and reliability across many sectors.
Last Updated on April 18, 2024 by Jordan Smith
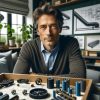
Jordan Smith, a seasoned professional with over 20 years of experience in the conveyor system industry. Jordan’s expertise lies in providing comprehensive solutions for conveyor rollers, belts, and accessories, catering to a wide range of industrial needs. From initial design and configuration to installation and meticulous troubleshooting, Jordan is adept at handling all aspects of conveyor system management. Whether you’re looking to upgrade your production line with efficient conveyor belts, require custom conveyor rollers for specific operations, or need expert advice on selecting the right conveyor accessories for your facility, Jordan is your reliable consultant. For any inquiries or assistance with conveyor system optimization, Jordan is available to share his wealth of knowledge and experience. Feel free to reach out at any time for professional guidance on all matters related to conveyor rollers, belts, and accessories.