Mining Conveyor Belts Selecting and Implementing
What are Mining Conveyor Belts
Mining Conveyor Definition
The mining conveyor meaning becomes evident when one observes its significant role in the mining sector. It refers to an essential system component that streamlines the transfer of materials across a mining site. This system, a conveyor belt by design, efficiently carries diverse materials such as ores and waste between processing or dump areas. By loading these substances onto one end, they are steadily transported to their target locations, reflecting the core function and importance of the mining conveyor within industry operations.
The Significance of Mining Conveyor Belts
The advent of the mining conveyor belt brought about a revolutionary change in the mining industry. The scales of operations increased manifold, and the efficiency of mining processes improved significantly. By reducing the human effort involved in material transportation and minimizing the time taken, these conveyor belts allowed for cost-effective operations. Furthermore, any mining operation, whether small-scale or large-scale, now benefits greatly from the use of the mining conveyor belt, emphasizing its significance.
The Evolution and Technological Advancements of Mining Conveyor Belts
The mining conveyor belt has undergone significant advancements since its inception. From manually operated versions primarily used for moving small amounts of materials over short distances, the mining conveyor belt technology has evolved to automation, which facilitates the transport of substantial quantities of materials over far-reaching distances. Today, such conveyor systems rely on advanced technology to ensure that operations are carried out smoothly, and mishaps are minimized, thus underscoring the ongoing evolution of the mining conveyor belt.
Types of Mining Conveyor Belts Used in Mining
The mining industry relies heavily on conveyor systems to transport mined materials from the depths of the earth to the surface for processing. The proper selection of a mining conveyor belt is vital for the efficiency, safety, and longevity of the equipment. Different mining environments and materials require unique types of conveyor belts. Here we detail the various kinds utilized throughout the mining sector.
Surface vs. Underground Mining Conveyor Belt
When differentiating between surface and underground mining conveyor belts, several critical factors come into play, reflecting the unique challenges and requirements of each mining environment. Here’s a more detailed look at these distinctions:
Surface Mining Conveyor Belts
- Durability Against Elements: Conveyor belts used in surface mining must withstand harsh external weather conditions, including exposure to UV rays, rain, and temperature fluctuations.
- Structural Design: These belts are designed for flexibility and length, capable of covering vast distances across the mining site. The structural integrity needs to support heavy loads, often including large chunks of materials.
- Safety and Accessibility: Given that these belts are more accessible and not confined, the safety requirements, while stringent, differ from underground belts. There’s a focus on operational safety and ease of access for maintenance.
Underground Mining Conveyor Belts
- Fire Resistance: Due to the enclosed spaces and the presence of potentially flammable gases, underground mining conveyor belts are manufactured to be highly fire-resistant, minimizing the risk of ignition.
- Dust Control: These belts are designed to reduce the amount of dust raised during operation, a necessary feature to improve air quality and reduce the risk of respiratory issues among miners.
- Compact and Robust Design: Space is a premium in underground mining. Conveyor belts in these environments are engineered to be compact yet robust, allowing for efficient operation in confined spaces without sacrificing durability or performance.
Conveyor Belt for Mining Industry: Challenges in Surface and Underground Mining
Gram’s conveyor belt for the mining industry is engineered to meet the unique challenges posed by different mining environments. These challenges vary significantly between underground and surface mining operations, each demanding specific features from conveyor belts to ensure efficiency, safety, and durability.
Conveyor Belts in Surface Mining
In surface mining, conveyor belts play a pivotal role in transporting large volumes of materials. The primary challenge here is the handling of bulkier and more abrasive materials compared to underground mining. This requires conveyor belts with high resistance to abrasion and tearing to ensure continuous operation and minimize downtime. The environmental exposure in surface mining also demands that the conveyor belts be resistant to weather elements like sun, rain, and extreme temperatures. The belts must be designed to handle large-scale operations and heavy loads, often over long distances, which puts additional stress on the belt material.
Given the scale of surface mining operations, the efficiency of the conveyor system directly impacts the overall productivity of the mine. This is where the role of mining conveyor belts for sale becomes crucial. The availability of high-quality conveyor belts that can be quickly and easily sourced is essential for maintaining the continuous flow of operations. In conclusion, the conveyor belt’s design and functionality must address the unique challenges of each mining environment, ensuring safety, durability, and efficiency. The ongoing development and availability of specialized Gram mining conveyor belts are key to the success and safety of mining operations worldwide.
Underground Mining and Conveyor Belt Challenges
In underground mining, conveyor belts face a complex set of challenges. The confined spaces, sharp turns, and steep inclines of underground mines demand highly flexible and durable conveyor systems. In underground mining, safety is crucial, necessitating fire-resistant conveyor belts as a regulatory standard to withstand harsh chemicals, and abrasion, and maintain integrity.
Durability is another crucial factor. The conveyor belts used in underground mining need to be robust enough to handle the constant wear and tear of transporting heavy and abrasive materials. This necessitates the use of high-quality materials and advanced manufacturing techniques, aspects that excellent mining conveyor belt manufacturers such as Gram focus on extensively. Moreover, the maintenance and repair of conveyor belts in underground settings can be challenging due to the limited space and difficult access. This makes the longevity of the belts and the availability of mining conveyor belts for sale for replacements and upgrades an important consideration for mining operations.
Multi-ply, Straight-warp, Steel-cord Belts, Solid Woven Belts and Heat-resistant Belts
The mining belt conveyor, vital for material transport in the industry, relies on its belt type for efficiency and reliability, with mining conveyor belt manufacturers developing various belts for diverse mining needs.
Each type of mining belt conveyor has its unique properties and is engineered to meet specific operational needs. Mining conveyor belt manufacturers such as Gram are key in creating belts that withstand the mining industry’s demands, with the choice depending on the material, transportation distance, and mining conditions. By selecting the appropriate type of conveyor belt, mining operations can achieve optimal efficiency and safety in material handling.
The Role of Shuttle Conveyor Systems
Shuttle conveyor systems are a sophisticated addition to the arsenal of mining conveyor belt options, bringing a unique set of functionalities that enhance flexibility and efficiency in mining operations. Here are some of the key functions and benefits they provide:
- Versatile Material Distribution: One of the primary advantages of shuttle conveyor systems is their ability to move and distribute materials across multiple points. This versatility is crucial for operations requiring the build-up of material piles from different angles and positions.
- Efficient Space Utilization: These systems are designed to optimize space within mining operations. Their ability to move back and forth allows for the effective use of limited space, particularly valuable in constrained environments.
- Enhanced Stockpiling Capabilities: Shuttle conveyors can create layered stockpiles, which is not possible with stationary conveyor systems. This capability enables better control over material segregation and degradation, leading to improved quality management of mined materials.
- Flexibility in Operation: The ability of shuttle conveyor systems to reverse direction and move materials to different locations makes them exceedingly flexible. This flexibility is crucial for dynamically adjusting operations based on immediate requirements and operational challenges.
- Increased Productivity: By facilitating the quick and easy movement of materials without the need for manual handling or multiple conveyor systems, shuttle conveyors significantly increase overall productivity. This efficiency reduces operational costs and time, contributing to a more profitable mining operation.
- Improved Material Blending: Shuttle conveyor systems can blend materials by layering them as they are deposited. This blending capability is essential for operations where material consistency is key to the processing and final product quality.
Shuttle conveyor systems enrich the mining conveyor belt landscape with their dynamic operation and the multitude of functionalities. They address specific challenges in material handling and distribution, offering solutions that traditional conveyor belts cannot. By enhancing flexibility, efficiency, and productivity, shuttle conveyors prove to be invaluable assets in modern mining operations.
Selecting the Right Mining Conveyor Belt
Selecting the right mining conveyor belt is crucial for the efficiency, safety, and cost-effectiveness of mining operations, requiring consideration of several key factors. Additionally, excellent mining conveyor belt suppliers such as Gram are pivotal in providing expertise and options that meet specific mining requirements.
Considering Operational Factors
When selecting a mining conveyor belt, certain operational factors are paramount. Each of these elements plays a strategic role in ensuring that the conveyor belt chosen will meet the needs of the mining operation without fail.
Material Handling Requirements
- Type of Material: The nature of the material being transported—whether fine-grained, sharp-edged, or hot—is critical in determining the type of conveyor belt needed.
- Load Size and Weight: It’s important to consider the average load that the belt will carry. A belt designed for heavy-duty use will have very different specifications than one for lighter loads.
- Transfer Speeds: The desired or required transfer speed of materials can have implications on the type of belt material and motor used.
- Conveyance Distance and Incline: The length of the transport route and whether it includes inclines or declines will influence the belt design and structure.
Environmental Considerations
- Mining Environment: The difference between an open-pit mine and an underground mine can significantly impact the belt choice, particularly in terms of material and safety features.
- Temperature and Weather Conditions: Belts used in places with extreme temperatures or variable weather conditions may need to be made of special materials that withstand these extremes.
- Safety Regulations: Ensuring compliance with safety regulations for mining operations will involve selecting conveyor belts that have the necessary certifications and fire resistance.
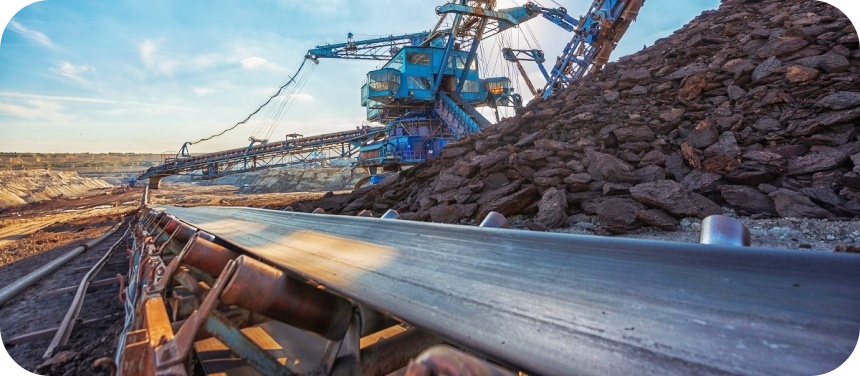
Cost-Effectiveness: New vs. Used Conveyor Belts
Making a cost-effective choice between new and used mining conveyor belts is a balancing act that involves considering the long-term operational costs versus the initial investment.
Pros and Cons of New Mining Conveyor Belts
- Longevity and Reliability: A new conveyor belt is usually associated with longer operational life and less downtime for maintenance.
- Warranty and Support: Manufacturers typically offer support and warranties, which can be valuable for operational stability.
- Latest Technologies: New belts may incorporate advanced technologies for efficiency and safety.
Assessing the Value of Used Mining Conveyor Belts
- Reduced Initial Cost: The most apparent advantage of a used belt is the lower upfront cost, beneficial for constrained budgets.
- Availability: Used belts are often readily available and can be acquired more quickly than ordering a new belt, which may have lead times.
However, when considering a used mining conveyor belt, due diligence is required to assess its condition and suitability for the specific mining environment and operational needs. The decision between new and used should consider not only the immediate cost savings but also the potential long-term benefits and the risk of increased downtime and maintenance expenses.
Mining Conveyor Belt Innovations and Sustainability
The mining industry continues to make significant strides in innovation and sustainability, particularly regarding the mining conveyor belt. This crucial component of mining operations has seen advancements that not only enhance efficiency and safety but also reflect a growing commitment to environmental stewardship. Below, we delve into the latest technological breakthroughs in mining conveyor belts and examine how the industry is addressing sustainability challenges.
Technological Advancements in Mining Conveyor Belts
Recent years have witnessed a surge in technological innovations designed to optimize the performance and reliability of mining conveyor belts. These advancements are a testament to the industry’s commitment to embracing technology for operational excellence.
- Smart Conveyor Belts: Equipped with sensors and IoT (Internet of Things) capabilities, these belts provide real-time data on their health and performance, facilitating predictive maintenance and reducing downtime.
- Energy-Efficient Designs: New materials and designs are being developed to reduce the energy consumption of mining conveyor belts. These include lighter belt materials and low-resistance belt rollers, which significantly decrease the energy needed for belt operation.
- Advanced Material Handling: Innovations in belt materials and coatings have led to belts that minimize spillage and reduce the environmental impact of material transport. This includes the development of belts with higher durability and improved resistance to harsh environmental conditions.
- Safety Enhancements: The integration of safety features such as automatic belt alignment, rip detection sensors, and fire-resistant materials has significantly improved the safety of mining conveyor belt operations.
Efforts Towards Sustainability and Reduced Environmental Impact
The mining industry is increasingly focusing on sustainability, with the mining conveyor belt playing a pivotal role in these efforts. By adopting more environmentally friendly technologies and practices, the industry aims to minimize its environmental footprint while maintaining productivity.
- Reducing Carbon Footprint: The shift towards energy-efficient conveyor belts helps reduce the overall carbon emissions of mining operations. The use of renewable energy sources to power these belts is also becoming more common.
- Material Recycling and Reuse: There is a growing emphasis on recycling used conveyor belts and repurposing them for other applications. This approach not only reduces waste but also conserves resources by extending the life of the materials used.
- Eco-Friendly Material Choices: Research and development efforts are increasingly focused on finding sustainable materials for belt construction. These include recycled materials and those with a lower ecological footprint during their production and disposal.
- Minimizing Landscape Disruption: Innovations in conveyor belt design and routing are aimed at reducing the physical footprint of mining operations, preserving the natural landscape, and reducing habitat disruption.
Through these technological advancements and a commitment to sustainability, the mining industry is making considerable progress in optimizing the operation and environmental impact of mining conveyor belts. This dual focus not only improves operational efficiency and safety but also aligns mining practices with broader environmental and sustainability goals.
Where Can I Buy Mining Conveyor Belt: Pricing and Purchasing Tips
A major component of planning any mining operation is sourcing the right equipment, including the crucial mining conveyor belt. However, buying a mining conveyor belt isn’t as straightforward as picking the first option you come across. Aspects like pricing and supplier reliability need careful consideration. Herein, we cover the different factors that influence the price of a mining conveyor belt and offer expert tips on how to reliably source a durable and efficient conveyor belt system.
Deciphering Mining Conveyor Belt Pricing Factors
When shopping for a mining conveyor belt, it’s important to understand that various factors contribute to the pricing. These include:
- Type of Material: The materials used to construct the belt affect its cost. For instance, heavy-duty rubber belts will likely cost more than lightweight synthetic options.
- Size and Length: Naturally, the larger and longer the belt, the higher the cost. Length and width directly influence the amount of material used and, consequently, the price.
- Customizations and Add-Ons: Additional features, such as rip detection sensors, integrated scale systems, or specific coatings to protect the belt, will influence its overall cost.
- Manufacturer Reputation: Established manufacturers with a history of high-quality products often price their conveyor belts higher than lesser-known providers. However, the price bump is often justified by the enhanced product quality and support services.
- Production Costs: Factors such as labor and acquisition costs for raw materials can also affect prices.
Tips for Sourcing Reliable and Durable Mining Conveyor Belts
When you’re in the market for a new mining conveyor belt, reliability and durability should be top considerations. To help you navigate the purchasing journey, here are some tips:
- Research Different Suppliers: Don’t limit yourself to the first vendor you find. Instead, compare several suppliers to understand what they offer and at what price.
- Verify Supplier Reputation: Look at supplier reputation, including customer reviews and industry recognitions. This will help you gauge the quality of their products and services.
- Assess After-Sales Support: Post-purchase support is critical, particularly if you’re buying a sophisticated conveyor system. Assess what type of maintenance and repair services are offered.
- Consider Customization Options: If your operation has unique needs, look for suppliers who offer customization options on their mining conveyor belts.
- Negotiate Pricing: Don’t be shy to negotiate pricing with suppliers. You might be surprised at the discounts or additional services you can get with a bit of negotiation.
Buying the perfect mining conveyor belt is not just about the upfront cost. Considering factors like durability, reliability, and after-sales service can save you a lot of time and hassle down the line. Remember also that a higher-priced belt could save you money in the long term, thanks to reduced maintenance costs and longer service life.
Compliance and Safety in Mining Conveyor Belt Operations
When it comes to mining operations, safety is paramount. It becomes an even more pressing concern in the context of mining conveyor belt operations. Conveyor belts present a slew of hazards if not properly designed, installed, and maintained. This article will outline the importance of selecting mining conveyor belts that comply with safety standards for underground mining and will delve into the crucial role of fireproofing and anti-static features in minimizing risks.
Importance of Selecting Compliant Mining Conveyor Belts
Adherence to safety standards when choosing a mining conveyor belt for underground operations plays a crucial role in the overall safety and efficacy of mining processes. Key points of consideration include:
- Regulatory Compliance: Specific standards regulate mining conveyor belts, particularly in underground operations. Mining operations must ensure that their conveyor belts meet these regulations to maintain safety and operational integrity.
- Material Resilience: Underground mining conditions can be harsh and unpredictable. Thus, the mining conveyor belt needs to withstand these conditions while retaining its operational efficiency. This resilience further underscores the need for compliant material selection.
- Operational Safety Features: Compliant belts often incorporate safety features, such as sensors to detect rip and tear or misalignment. These features are crucial in minimizing incidents and ensuring safe operation.
- Ease of Maintenance: Conveyor belts that comply with industry standards are often easier to maintain, primarily because their construction facilitates regular inspection and upkeep routines.
Fireproofing and Anti-Static Features: Essential Safety Measures
Fireproofing and anti-static features represent essential safety measures in mining conveyor belt specifications. These two characteristics can significantly minimize various risks associated with mining operations.
- Fireproofing: In mining environments, especially in coal mines, the risk of fire is a constant threat. Fire-resistant mining conveyor belts can withstand high temperatures and slow the spread of fire, giving workers more time for fire control measures.
- Anti-static Features: Static build-up is a common occurrence on conveyor belts. In a mining environment, this could lead to sparks, potentially causing an explosion in the presence of flammable gases. Anti-static conveyor belts are designed to dissipate static charges, thus reducing this risk.
- Protection of Workers and Equipment: Fireproofing and anti-static features provide an extra layer of protection for both workers and equipment, reducing the risk of accidents and costly equipment damage.
When selecting a mining conveyor belt, adherence to safety and compliance standards is non-negotiable. Vital features like fire resistance and anti-static properties should be present in every mining conveyor belt used in harsh and potentially dangerous environments like underground mines. By prioritizing these elements, mining operations can ensure the safety of workers and the longevity of equipment, ultimately promoting operational efficiency.
Ensuring Maintenance and Durability of Conveyor Belt for the Mining Industry
Maintaining and ensuring the durability of a mining industry conveyor belt is crucial for the smooth operation of a mining conveyor belt system, especially given the significant wear and tear in harsh mining environments. Additionally, the role of mining conveyor belt manufacturers in providing durable and high-quality belts is crucial in ensuring the longevity of these systems.
Maintenance Guide for Mining Conveyor Belt System
- Regular Inspections: Routine inspections are the first step in maintaining the health of a mining conveyor belt system. These inspections should include checking for wear and tear, damage to the belt, misalignment, and any other signs of trouble. Early detection of potential issues can prevent costly repairs and downtime.
- Cleaning Protocols: Keeping the conveyor belt clean is essential to prevent material build-up that can lead to belt misalignment or damage. Regular cleaning schedules should be established based on the type of material being transported and the operating conditions.
- Lubrication and Tension Adjustment: Proper lubrication of the conveyor system’s moving parts is necessary to reduce friction and wear. Additionally, maintaining the correct belt tension ensures efficient operation and prolongs the belt’s life.
- Belt Repair and Replacement: In case of damage, timely repair or replacement of the belt is crucial. Prolonging the use of a damaged belt can lead to more severe issues in the conveyor system. Mining conveyor belt manufacturers often provide repair services or recommendations for maintaining their products.
- Training for Maintenance Staff: Ensuring that the maintenance staff is well-trained and knowledgeable about the specific mining conveyor belt system in use is vital. Maintenance staff must know best practices and signs of issues while ensuring conveyor belt durability in mining involves regular inspections, proper upkeep, and using quality belts suited for mining demands. Collaboration with experienced mining conveyor belt manufacturers like Gram is the key to achieving a conveyor belt system that operates efficiently and withstands the test of time in harsh mining environments.
CONTACT US
Let us help you find a better solution!
FAQs about Mining Conveyor Belt
What type of conveyor belt is used in mining?
In mining, heavy-duty conveyor belts designed to withstand harsh environments and transport large volumes of materials are essential. The most commonly used types are steel cord conveyor belts and fabric-reinforced conveyor belts. Steel cord belts offer high tensile strength and durability, making them ideal for transporting heavy loads over long distances. Fabric-reinforced belts, typically made from polyester or nylon fabrics, are flexible and resistant to impact and abrasion. These belts are essential for moving bulk materials such as ore, coal, and aggregate efficiently and safely within the mining industry.
How to choose a mining conveyor belt?
Choosing a mining conveyor belt requires considering several critical factors. First, evaluate the type and volume of material to be transported, as well as the distance and incline of the conveyor path. The belt’s strength and durability must match the demands of the mining environment. Consider the belt’s resistance to wear, impact, and abrasion, which are common in mining operations. Additionally, select a belt with appropriate fire resistance, especially if used in underground mining. Environmental conditions, such as temperature and moisture levels, should also influence your choice. Consulting with manufacturers for tailored solutions ensures optimal performance and longevity.
What is the most common conveyor belt system?
The most common conveyor belt system in industrial applications, including mining, is the belt conveyor system. This system consists of a continuous loop of material, usually rubber or PVC, that is driven by pulleys and supported by rollers. Belt conveyor systems are highly versatile and can transport materials over long distances, across various terrains, and at different angles. They are commonly used for bulk material handling, such as transporting coal, ore, gravel, and sand in mining operations. Their efficiency, reliability, and ability to handle high capacities make them the preferred choice in many heavy-duty industrial settings.
What are conveyor systems for mining?
Conveyor systems for mining are essential for the efficient transport of bulk materials within mining operations. These systems consist of multiple conveyor belts and other components, such as rollers, idlers, and drives, designed to move large quantities of materials like ore, coal, and aggregates. They are used in both surface and underground mining operations to transport materials from the extraction site to processing plants, storage areas, or loading facilities. Mining conveyor systems improve productivity, reduce operational costs, and enhance safety by minimizing the need for manual handling of heavy materials.
What are most conveyor belts made of?
Most conveyor belts are made of a combination of materials that provide the necessary strength, flexibility, and durability required for various industrial applications. The primary materials used are rubber, PVC (polyvinyl chloride), and fabric reinforcements. Rubber is commonly used for its excellent grip, flexibility, and resistance to abrasion and impact. PVC is favored for its durability and resistance to chemicals and moisture. Fabric reinforcements, such as polyester, nylon, or cotton, are embedded within the rubber or PVC layers to enhance tensile strength and stability, ensuring the conveyor belt can handle heavy loads and harsh operating conditions.
What is the coal conveyor belt?
A coal conveyor belt is a specific type of belt conveyor system designed to transport coal from mining sites to processing plants, storage facilities, or loading points. These belts are made of heavy-duty materials, such as rubber or PVC, reinforced with fabric or steel cords to handle the abrasive nature of coal and the heavy loads involved. Coal conveyor belts often include features like fire resistance and anti-static properties to ensure safe operation, particularly in underground mines where the risk of fire and explosions is higher. They are crucial for efficient and continuous coal handling and transport.
How many types of conveyor belts are there?
There are several types of conveyor belts, each designed for specific applications and operating environments. The main types include fabric conveyor belts, which use textile materials like polyester or nylon for reinforcement; steel cord conveyor belts, which incorporate steel cords for high tensile strength and durability; and solid woven conveyor belts, made from a single piece of woven fabric for enhanced robustness. Additionally, there are modular conveyor belts composed of interlocking plastic segments, and specialty belts like flame-resistant, oil-resistant, and high-temperature belts tailored for specific industrial needs.
Which conveyor uses two belts to transfer coal?
The dual-belt conveyor system, often used in mining operations, utilizes two parallel conveyor belts to transfer coal. This system is designed to enhance stability and ensure efficient material handling over long distances and through challenging terrains. The primary belt carries the bulk of the coal, while the secondary belt provides additional support and helps to prevent spillage. This dual-belt setup can handle high volumes of coal and other bulk materials, making it ideal for large-scale mining operations where consistent and reliable transport is critical.
Which metal is used in conveyor belt?
Steel is the primary metal used in conveyor belts, especially in mining and heavy industrial applications. Steel is utilized in various forms within the belt, including steel cords and steel mesh, to provide high tensile strength, durability, and resistance to impact and wear. Steel cord conveyor belts are particularly common in mining due to their ability to handle heavy loads over long distances without stretching. Additionally, stainless steel is often used for specific components, such as rollers and idlers, to provide corrosion resistance and ensure longevity in harsh operating environments.
Which type of belt is most commonly used in mines?
The most commonly used type of belt in mines is the steel cord conveyor belt. These belts are preferred due to their high tensile strength, durability, and ability to handle the heavy loads and harsh conditions typical in mining environments. Steel cord belts consist of a series of steel cables embedded within the belt’s rubber matrix, providing superior resistance to stretching and damage from impact or abrasion. This makes them ideal for transporting large quantities of bulk materials, such as ore, coal, and other mined substances, over long distances and through rugged terrains.
What are the three types of conveyor belts?
The three primary types of conveyor belts are:
Fabric Conveyor Belts: These belts are reinforced with textile materials, such as polyester, nylon, or cotton, providing flexibility and strength for various applications. They are commonly used in general material handling and light-duty operations.
Steel Cord Conveyor Belts: Reinforced with steel cables, these belts offer exceptional tensile strength and durability, making them ideal for heavy-duty applications like mining and bulk material transport.
Modular Conveyor Belts: Made from interlocking plastic segments, these belts are highly versatile, allowing for easy maintenance and customization. They are often used in food processing, packaging, and other industries requiring frequent belt modifications or cleanings.
What is the alternative to conveyor belt?
An alternative to conveyor belts is the pneumatic conveying system. This system uses air pressure or vacuum to transport bulk materials through pipelines, making it ideal for moving fine, granular, or powdered substances over long distances. Pneumatic conveyors are particularly useful in industries where dust control and contamination prevention are critical, such as in food processing, pharmaceuticals, and chemical manufacturing. Another alternative is the screw conveyor, which uses a rotating helical screw blade within a tube to move materials. This method is suitable for handling semi-solid materials, including wood chips, aggregates, and food waste.
What are the grades of conveyor belts?
Conveyor belts are classified into various grades based on their properties and intended use. The main grades include:
Grade M: General-purpose rubber conveyor belts with moderate abrasion resistance, suitable for light to medium-duty applications.
Grade N: Similar to Grade M but with enhanced wear resistance, used in applications where higher abrasion resistance is required.
Grade R: Flame-resistant conveyor belts designed for use in underground mining and other hazardous environments.
Grade T: Heat-resistant conveyor belts capable of withstanding high temperatures, used in industries like foundries, cement plants, and steel mills.
Grade S: Oil-resistant conveyor belts that prevent degradation when exposed to oils and chemicals, ideal for food processing and recycling industries.
What is the most durable type of belt?
The most durable type of conveyor belt is the steel cord conveyor belt. These belts are reinforced with steel cables that provide exceptional tensile strength, resistance to stretching, and durability under heavy loads. Steel cord belts can handle harsh operating conditions, such as high impact, abrasion, and extreme temperatures, making them ideal for mining, bulk material handling, and other heavy-duty industrial applications. Their robust construction ensures a longer lifespan and reliable performance, reducing downtime and maintenance costs in demanding environments.
What type of conveyor is used in coal mining?
In coal mining, the most commonly used type of conveyor is the belt conveyor system. These systems consist of a continuous loop of reinforced rubber or PVC belt, driven by pulleys and supported by rollers. Belt conveyors are designed to transport large quantities of coal efficiently and safely from the mining site to processing plants or storage facilities. They are often equipped with features like flame resistance and anti-static properties to enhance safety, particularly in underground mines where the risk of fire and explosions is higher. Belt conveyors are essential for ensuring continuous and reliable coal transport in mining operations.
What are the different types of conveyor systems?
There are several types of conveyor systems used in various industries, including:
Belt Conveyor Systems: Comprising continuous belts driven by pulleys, they are versatile and commonly used for bulk material handling.
Roller Conveyor Systems: Utilizing rollers to transport items, ideal for handling packages and heavy loads in warehouses and manufacturing.
Pneumatic Conveyor Systems: Using air pressure or vacuum to move bulk materials through pipelines, suitable for fine or granular substances.
Screw Conveyor Systems: Employing a rotating helical screw blade within a tube to move semi-solid materials.
Chain Conveyor Systems: Using chains to move heavy loads, often found in automotive and heavy machinery industries.
Slat Conveyor Systems: Consisting of slats attached to a chain, suitable for handling heavy or bulky items.
Overhead Conveyor Systems: Hanging from an overhead track, these systems transport items above ground level, saving floor space.
How fast does a mining conveyor belt go?
The speed of a mining conveyor belt typically ranges from 0.1 to 10 meters per second, depending on the specific application and requirements. For example, coal conveyors may operate at speeds around 2 to 4 meters per second to efficiently move bulk materials from extraction sites to processing areas. Higher speeds, such as 5 to 6 meters per second, can be used for transporting lighter materials or for long-distance conveyance. The optimal speed is determined by factors like the type of material being transported, the conveyor’s length, and the incline, balancing efficiency and safety in mining operations.
What is the maximum speed of a conveyor belt?
The maximum speed of a conveyor belt can reach up to 15 meters per second (approximately 900 meters per minute), though this is typically found in high-speed bulk material handling systems in mining and other heavy industries. Such high speeds are used to maximize throughput and efficiency when transporting large volumes of materials over long distances. However, operating at these speeds requires robust and well-maintained equipment to handle the increased wear and tear. Safety measures, such as effective guarding and monitoring systems, are also crucial to prevent accidents and ensure smooth operation at high speeds.
What is the best belt for underground mining?
The best belt for underground mining is a flame-resistant steel cord conveyor belt. These belts combine the strength and durability of steel cords with flame-resistant properties, essential for the safety and efficiency of underground operations. Flame-resistant belts are designed to withstand high temperatures and prevent the spread of fire, reducing the risk of catastrophic incidents in confined spaces. Additionally, these belts are resistant to abrasion and impact, ensuring long-term performance and reliability. They also typically feature anti-static properties to minimize the risk of igniting combustible dust present in underground mining environments.
What are mining conveyor belts made of?
Mining conveyor belts are primarily made of durable materials designed to withstand the harsh conditions of mining environments. The most common materials include:
Rubber: Used for its flexibility, grip, and resistance to abrasion and impact.
Steel Cords: Embedded within the rubber matrix to provide high tensile strength and durability, essential for handling heavy loads.
Fabric Reinforcements: Materials like polyester, nylon, or cotton are used in some belts to add flexibility and strength.
Special Coatings: Flame-resistant, oil-resistant, or heat-resistant coatings may be applied depending on the specific requirements of the mining operation. These materials ensure the conveyor belts can handle the demanding conditions and prolonged use typical in mining applications.
How long does a conveyor last?
The lifespan of a conveyor belt in mining operations can vary widely depending on several factors, including the type of material it is made from, the operating conditions, and the level of maintenance. On average, a high-quality conveyor belt in a mining environment can last between 3 to 10 years. Factors such as exposure to abrasive materials, impact damage, and environmental conditions like moisture and temperature extremes can affect longevity. Regular maintenance, such as inspections, repairs, and timely replacements of worn components, can significantly extend the lifespan of a conveyor belt, ensuring continuous and efficient operation.
What is the average speed of an industrial conveyor belt?
The average speed of an industrial conveyor belt typically ranges from 0.5 to 3 meters per second, depending on the application and the industry. In mining and heavy industrial environments, the speed may be adjusted to balance efficiency and safety. For instance, belts used for transporting heavy, bulk materials such as ore or coal might operate at speeds between 1 and 2 meters per second to ensure stable and safe handling. The specific speed chosen will depend on factors such as the type of material, the distance to be covered, and the required throughput of the system.
How long does the great conveyor belt take?
The term “great conveyor belt” often refers to the oceanic conveyor belt, a global system of deep-ocean currents that circulates water around the world’s oceans. This natural conveyor belt is driven by differences in water temperature and salinity and can take approximately 1,000 years to complete a full cycle. The process involves the movement of warm surface waters to the poles, where they cool, sink, and flow back toward the equator as deep, cold currents. This global circulation plays a crucial role in regulating the Earth’s climate and distributing heat and nutrients across the oceans.
What is the longest mining conveyor belt?
The longest mining conveyor belt in the world is the Bou Craa conveyor belt in the Western Sahara, operated by the Phosphate Rock company. This belt stretches over an impressive 98 kilometers (61 miles) from the Bou Craa phosphate mine to the coastal city of El Aaiún. The belt is used to transport mined phosphate rock directly from the extraction site to the shipping port. Designed to handle the harsh desert conditions, the Bou Craa conveyor belt is a marvel of engineering, efficiently moving large volumes of material across significant distances and showcasing the capabilities of modern conveyor systems in the mining industry.
What’s the great conveyor belt?
The “great conveyor belt” refers to the global oceanic conveyor belt, also known as thermohaline circulation. This massive, interconnected system of deep-ocean currents circulates water around the globe, driven by differences in water temperature and salinity. Warm surface waters move toward the poles, where they cool, sink, and become dense, creating deep currents that flow back toward the equator. This process takes approximately 1,000 years to complete a full cycle and plays a critical role in regulating the Earth’s climate. In heavy industries like mining, understanding natural conveyor systems can provide insights into sustainable resource management and environmental impact.
What speed do belt conveyors run at?
Belt conveyors in heavy industrial and mining applications typically run at speeds ranging from 0.1 to 10 meters per second, depending on the specific requirements of the operation. For example, conveyors transporting heavy bulk materials like ore or coal usually operate at speeds between 1 and 4 meters per second to balance efficiency with safety and material handling considerations. High-speed conveyors, reaching up to 15 meters per second, are used for lighter materials or when rapid transportation is essential. The optimal speed for any given conveyor system is determined by factors such as the type of material, distance, incline, and desired throughput.