Picking the Right Tool to Cut Conveyor Belt Rubber
In industrial settings, the maintenance and repair of conveyor belts are paramount to ensuring operational continuity and safety. The integrity of these belts is often compromised by wear and tear, necessitating precise cuts for both repair and configuration. This introduces the challenge of effectively and safely cutting conveyor belt rubber, a task that requires specific tools designed for this purpose. The evolving technology in this field has led to the development of an array of specialized tool to cut conveyor belt rubber. These tools not only improve the efficiency of the cutting process but also ensure the cuts are clean and precise, reducing the risk of further damage or misalignment during operations.
Why Use Specialized Tool to Cut Conveyor Belt Rubber?
Using the right tool to cut conveyor belt rubber is not just a matter of convenience; it is crucial for safety, precision, and the overall performance of the conveyor system. Improper cutting methods can lead to several safety issues, including jagged edges that pose cutting hazards, potential shrapnel from using inappropriate tools like saws or grinders, the risk of repetitive strain injuries from manual scissors, the danger of slips from using non-specialized sharp tools, and the increased likelihood of accidental cuts to other parts of the belt or machinery. These risks underscore the importance of employing specialized tools designed specifically for cutting conveyor belt rubber.
Furthermore, precision and efficiency are critical when creating finger splices or customizing sizes of conveyor belts. Specialized tools ensure clean cuts that are essential for high-quality splices, maintain the integrity of the belt edges necessary for seamless joins, reduce material waste by minimizing errors, speed up the process to prevent project delays, and ensure uniformity across multiple cuts which is vital for the conveyor’s consistent operation.
Lastly, the longevity and performance of conveyor belts are significantly impacted by the quality of the cuts made during maintenance. Accurate cuts by a specialized tool to cut conveyor belt rubber enhance the belt’s alignment, which reduces wear and tear, prevents belt slippage which can lead to overheating and motor damage, ensures the belt runs smoothly to minimize energy consumption, and extends the overall lifespan of the belt, thereby optimizing operational efficiency and reducing the need for frequent replacements. All these factors play a pivotal role in maintaining an efficient, safe, and cost-effective conveyor system.
Types of Tool to Cut Conveyor Belt Rubber
The selection of the right tool to cut conveyor belt rubber is crucial for efficient, safe, and precise conveyor belt maintenance. The tools available are varied, each designed to meet specific needs within the industry. Here, we explore the types of conveyor belt cutting tools tailored to different situations and requirements.
Universal Tools for Cutting Conveyor Belt Rubber
Universal tools are the go-to choice for versatility, capable of handling a wide range of conveyor belt types and thicknesses. These tools are engineered to cut conveyor belt rubber with precision, regardless of the belt’s specifications. Their adaptability makes them invaluable in facilities that deal with various conveyor systems, ensuring that maintenance crews can perform cuts on multiple types of belts with a single tool, thus optimizing tool inventory and reducing costs.
Heavy Duty Tools for Thick and Multi-Ply Belts
For industrial environments where conveyor belts are thicker and consist of multiple plies, heavy duty tools are essential. These tools are designed with robust torque and durable blades to cut through thick, multi-ply rubber belts efficiently. The high-power output ensures that cuts are clean and accurate, preventing fraying and other damage that could compromise the belt’s integrity. This capability is critical in heavy industries such as mining and quarrying, where conveyor belt failure can lead to significant downtime and safety hazards.
Cordless Conveyor Belt Cutters
Cordless conveyor belt cutters offer unparalleled convenience and mobility, making them perfect for on-site repairs and adjustments. These tools are particularly valuable in situations where access to power is limited or where flexibility is required. Examples of their use include:
- Field Repairs: Quick, on-the-spot repairs in agricultural fields or mining sites where dragging cords could be impractical or unsafe.
- Emergency Situations: Immediate cutting of belts in emergency scenarios to prevent further machinery damage or to quickly replace a section of the belt.
- High-Mobility Sites: Frequent movement between different parts of a large factory or between different conveyor systems can be handled more efficiently without the encumbrance of cords.
- Outdoor Applications: In construction and roadwork scenarios where conveyors are used and power setups are challenging.
- Confined Spaces: Performing cuts in tight spaces where cables could restrict movement or create hazards.
Each type of tool to cut conveyor belt rubber offers specific benefits tailored to various operational needs, highlighting the importance of choosing the right tool for effective conveyor belt maintenance and repair.
Top Picks for Tool to Cut Conveyor Belt Rubber
Selecting the appropriate tool to cut conveyor belt rubber is critical for achieving efficient, safe, and precise maintenance. This section highlights top picks in the industry, each offering unique benefits tailored to different needs and circumstances.
Flexco Belt Cutter
The Flexco belt cutter is renowned for its precision and ease of use, making it a top choice for cutting conveyor belt rubber.
- Precision Cutting: Ensures straight, clean cuts every time, which is crucial for the integrity of the belt and the smooth operation of the conveyor system.
- Ease of Use: Designed for user comfort and efficiency, minimizing physical effort and reducing the risk of operator fatigue.
- Durability: Built to withstand tough industrial environments, ensuring longevity and reducing the need for frequent replacements.
- Safety Features: Comes with built-in safety mechanisms to prevent accidents during operation.
- Quick Setup: Easy to set up and use, which reduces downtime during maintenance procedures.
The Flexco belt cutter is competitively priced, offering good value for money considering its robust construction and reliable performance, typically ranging from mid to high-end in pricing, depending on the model and features.
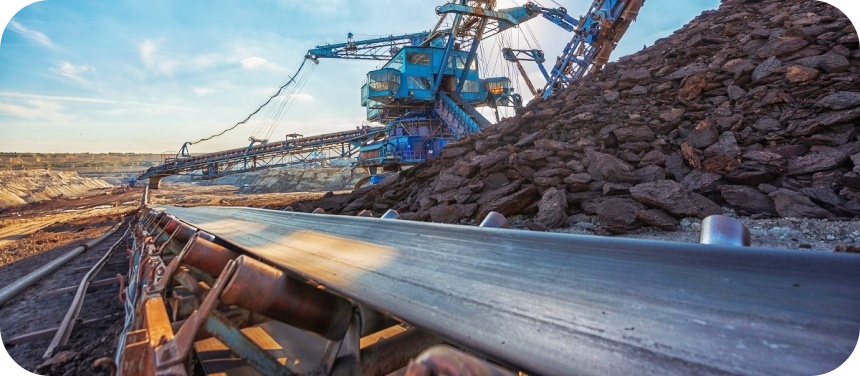
DIY Solutions for Cutting Conveyor Belt Rubber
For smaller operations or less frequent needs, DIY solutions can be both creative and cost-effective. These methods often involve repurposing tools or fabricating custom cutters from available materials. Examples include using heavy-duty shears for thin belts, crafting a cutting edge from a modified wood saw, or adapting automotive tools for occasional cuts. While not as precise or efficient as professional tools, these solutions can suffice in a pinch or for budget-restricted scenarios.
Power Belt Cutters and Conveyor Belt Cutter Machines
For industrial applications demanding high power and volume, power belt cutters and conveyor belt cutter machines are ideal.
- Consistent Cuts: Provides uniform cuts essential for the mass production of conveyor belt components.
- High Efficiency: Capable of handling large volumes of material, significantly reducing the time needed for cutting operations.
- Reduced Labor: Automates the cutting process, minimizing manual labor and associated costs.
- Adaptability: Many models can adjust to different belt thicknesses and materials, offering versatility across various projects.
- Long-Term Investment: Although the initial cost is higher, the robustness and efficiency pay off in the long run.
Comparing Blades: Selecting the Right Conveyor Belt Cutting Blade
Choosing the right cutting blade for different types of rubber is essential for both performance and longevity of the tool. Considerations include:
- Material Compatibility: Selecting a blade material that is suitable for the type of rubber, ensuring clean cuts without damage.
- Blade Thickness: Thicker blades for heavy-duty cutting versus thinner blades for finer, precise cuts.
- Tooth Design: Some blades have teeth configurations designed for specific rubber textures and hardness.
- Heat Resistance: Blades that can withstand the friction-generated heat without losing sharpness or warping.
- Corrosion Resistance: Blades that resist rust and corrosion, particularly important in damp or chemically active environments.
Maintenance and replacement tips to ensure optimal performance include:
- Regular Inspection: Check blades for wear or damage before each use.
- Proper Cleaning: Clean blades after each use to remove any debris or residue.
- Sharpening: Keep blades sharp to maintain cutting efficiency; dull blades can damage the belt and the cutter.
- Proper Storage: Store blades in a dry, safe environment to prevent accidental damage or corrosion.
- Replacement Schedules: Establish and adhere to a blade replacement schedule based on usage frequency and material type to ensure consistent performance.
Each type of tool to cut conveyor belt rubber provides specific advantages depending on the requirements of the task, highlighting the importance of careful selection based on the operational needs of the conveyor system.
Choosing the Right Tool to Cut Conveyor Belt Rubber
Selecting the appropriate tool to cut conveyor belt rubber is essential for achieving optimal results in conveyor belt maintenance and repair. When deciding on the best tool for your needs, there are several critical factors to consider that align with the specific demands of your operations.
- Belt Thickness: The thickness of the conveyor belt dictates the type of cutting tool required. Thicker, multi-ply belts may need robust, heavy-duty cutters to penetrate effectively without damaging the belt.
- Frequency of Use: For industrial settings where conveyor belts are frequently serviced, a durable and fast-operating tool is essential. Conversely, for less frequent use, a simpler and more cost-effective model may suffice.
- Material Type: Different materials require different blade specifications to ensure clean cuts without degrading the belt material. Tools designed for rubber might not be suitable for belts containing metal weaves or other specialized materials.
- Operational Environment: The environment in which the tool will be used also affects the choice. For example, in wet or corrosive environments, tools with corrosion-resistant properties are necessary.
- Budget: Financial constraints play a significant role in the decision-making process. It’s crucial to find a balance between quality and cost, ensuring the tool is not only effective but also provides good value for money.
Beyond the tool itself, aftermarket support is a critical aspect of purchasing decisions. The importance of warranties and customer service cannot be overstated, as they ensure the longevity and effectiveness of the tool to cut conveyor belt rubber. Warranties protect against defects and failures, potentially saving costs on repairs or replacements. Effective customer service provides assistance in setup, usage, maintenance, and troubleshooting, which is invaluable for maximizing tool performance and lifespan. Ensuring that your chosen tool comes with reliable support will help safeguard your investment and enhance your operational efficiency.
Learn more about our high-performance conveyor belt options.
FAQs About Tool to Cut Conveyor Belt Rubber
Cutting a rubber conveyor belt accurately and safely requires specific steps and tools to ensure the cut is clean and does not damage the belt. First, measure and mark the area where the belt is to be cut. Use a straight edge or a chalk line to ensure the line is straight. Secure the belt on a flat surface to prevent it from moving. Choose a tool designed specifically for cutting conveyor belt rubber, such as a power belt cutter or a sharp utility knife designed for heavy-duty materials. When cutting, apply steady and even pressure to make a straight cut through the belt. After cutting, inspect the edges for any irregularities or jagged edges that might need to be trimmed or sanded down for a smooth finish. Safety is crucial, so always wear appropriate protective gear, such as gloves and eye protection, when cutting conveyor belts.
The best tool to cut a conveyor belt depends on the type of belt and the precision required for the cut. For general purposes, a heavy-duty utility knife may suffice for thinner belts. However, for thicker, reinforced belts or for cuts requiring high precision, specialized tools like the Flexco belt cutter or electric power belt cutters are recommended. These tools are designed to handle the robust nature of conveyor belts and can provide clean, straight cuts without fraying the edges of the belt. Such specialized tools often come with features that enhance safety and efficiency, including guides that ensure straight cuts and ergonomic designs that reduce strain on the operator.
Various tools can be used to cut a conveyor belt, depending on the specific needs of the operation and the type of belt material. For small, infrequent cuts, a sharp utility knife or heavy-duty shears might be sufficient. For more frequent or large-scale operations, specialized cutting tools such as power belt cutters, electric shears, or table-top cutting machines are ideal. These tools are specifically designed to handle the dense and tough materials used in conveyor belts and can provide quick, clean, and safe cuts. For highly specialized applications, laser cutting systems may also be used, though these are less common due to their high cost and operational complexity.
Conveyor belts are typically made from rubber compounds that can withstand considerable stress, wear, and environmental exposure. The most common type of rubber used is styrene-butadiene rubber (SBR), known for its good abrasion resistance and cost-effectiveness. For applications requiring higher resistance to oils and chemicals, nitrile rubber (NBR) might be used. Ethylene propylene diene monomer (EPDM) rubber is employed for its superior resistance to weathering, heat, and ozone. Natural rubber is also used for conveyor belts requiring flexibility and high tensile strength. Each type of rubber has specific properties that make it suitable for different industrial environments and applications.
Last Updated on July 16, 2024 by Jordan Smith
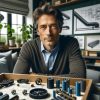
Jordan Smith, a seasoned professional with over 20 years of experience in the conveyor system industry. Jordan’s expertise lies in providing comprehensive solutions for conveyor rollers, belts, and accessories, catering to a wide range of industrial needs. From initial design and configuration to installation and meticulous troubleshooting, Jordan is adept at handling all aspects of conveyor system management. Whether you’re looking to upgrade your production line with efficient conveyor belts, require custom conveyor rollers for specific operations, or need expert advice on selecting the right conveyor accessories for your facility, Jordan is your reliable consultant. For any inquiries or assistance with conveyor system optimization, Jordan is available to share his wealth of knowledge and experience. Feel free to reach out at any time for professional guidance on all matters related to conveyor rollers, belts, and accessories.