Conveyor Belt Material Properties: Analysis And Selecting
Conveyor belts are essential components in numerous industrial sectors, serving as the backbone for material handling and transportation. They enable efficient movement of goods across different stages of production, packaging, and distribution. This blog post aims to delve into the critical topic of conveyor belt material properties, providing a comprehensive exploration of the various properties and types of materials utilized in constructing conveyor belts. Understanding these properties is vital for selecting the right belt material to ensure operational efficiency and longevity in diverse industrial environments. By examining these elements, we aim to offer valuable insights into optimizing conveyor system performance through informed material selection.
Basics of Conveyor Belt Material Properties
Conveyor belts are critical components in various industrial processes, functioning to transport materials from one point to another efficiently and continuously. These belts are essential in numerous sectors such as mining, manufacturing, and logistics, owing to their ability to enhance productivity and reduce labor costs. Specifically, conveyor belts fulfill ten fundamental roles in industries, including moving goods over long distances, handling bulk material, providing variable speed control, and ensuring the safety of materials transported by minimizing losses and damages.
A crucial aspect of understanding conveyor belts is the knowledge of conveyor belt material properties. The performance and suitability of a conveyor belt for a particular application largely depend on its material composition. Conveyor belts are predominantly made from materials that offer durability, flexibility, and resistance to various environmental factors.
The most common materials used in the manufacturing of conveyor belts include:
- Rubber: Often used for its superior durability and elasticity, rubber conveyor belts are suitable for heavy-duty applications. They are particularly resistant to abrasion and tearing, making them ideal for industries like mining and quarrying.
- Plastic Compounds: These include polyvinyl chloride (PVC) and polyurethane (PU), known for their excellent chemical resistance and hygienic properties, which are crucial in food processing and pharmaceutical industries.
- Fabrics: Materials such as nylon, polyester, and cotton are used to provide structure and support to conveyor belts. Fabrics are chosen for their tensile strength and are often used in layers to enhance load-bearing capacity.
- Steel: Used primarily in heavy industries for its high strength and resistance to heat and sharp objects. Steel conveyor belts are often employed in metalworking or when transporting hot materials.
- Silicone: Known for its high-temperature resistance and non-stick properties, silicone belts are used in food production and processing where temperature control and cleanliness are vital.
- Thermoplastic Polyurethane (TPU): TPU belts are valued for their flexibility, wear resistance, and food-grade safety, making them suitable for a broad range of applications including food, textile, and packaging industries.
Understanding the conveyor belt material properties not only helps in selecting the right belt for specific industrial needs but also enhances the efficiency and longevity of the conveyor system. Each material brings unique benefits and choosing the right one depends on the application’s specific requirements such as load type, environmental conditions, and desired lifespan of the belt.
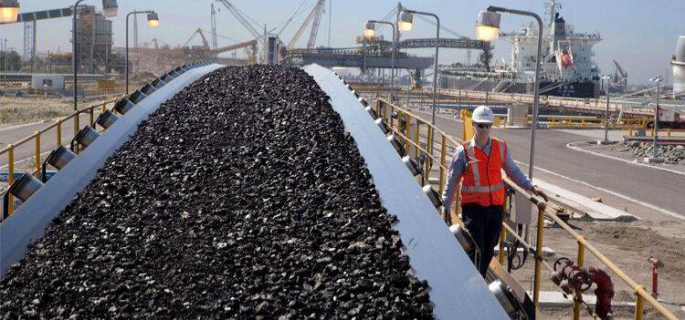
Conveyor Belt Material Properties
Understanding the various types of conveyor belt materials and their unique properties is crucial for selecting the right belt for specific applications. The material properties of conveyor belts determine their performance, durability, and suitability for different environments. Here, we will explore some of the most common types of conveyor belt materials, focusing on their conveyor belt material properties.
Rubber Conveyor Belts
Rubber conveyor belts are highly prized for their durability, flexibility, and resistance to abrasion, making them suitable for a variety of industrial applications. The primary conveyor belt material properties of rubber include excellent tensile strength and elongation capabilities. Common types of rubber used in these belts include styrene-butadiene rubber and natural rubber. These materials allow the belts to withstand harsh conditions, including the presence of oils, fats, and other chemicals.
Fabric Conveyor Belts
Fabric conveyor belts are known for their cost-effectiveness and medium impact resistance, which makes them ideal for general-purpose applications. The key conveyor belt material properties for fabrics include their ability to absorb impact and their operational quietness. Nylon, polyester, and cotton are commonly used in the manufacturing of fabric conveyor belts. These materials provide a good balance between price and performance, particularly in industries where high tensile strength is not the primary requirement.
Metal Conveyor Belts
Metal conveyor belts stand out for their high strength, longevity, and their ability to operate under extreme temperatures. The conveyor belt material properties of metals like stainless steel and carbon steel include high thermal, chemical, and mechanical resistances. These belts are particularly suited for industries requiring sanitary operations, such as food processing, or environments with high or low temperatures.
Plastic Conveyor Belts
Plastic conveyor belts offer advantages such as being lightweight, having corrosion resistance, and requiring easy maintenance. The specific conveyor belt material properties of plastics like PVC and polyurethane include resistance to chemicals, water, and wear. These belts are often used in food production industries because they meet cleanliness and non-toxic standards, in addition to being easy to clean and maintain.
Each type of conveyor belt material offers distinct properties that make them suitable for various industrial applications. Understanding these conveyor belt material properties helps in making informed decisions that enhance efficiency and reduce operational costs.
Reliable conveyor belts to boost your productivity.
How to Choose The Best Material Based on Conveyor Belt Material Properties
Choosing the best material for a conveyor belt involves considering several factors based on the specific application requirements and the properties of various belt materials. Here is a step-by-step guide to help you choose the best conveyor belt material:
Understand the Application Requirements
- Load Type: Consider the weight, size, and type of material being conveyed (e.g., sharp, abrasive, oily).
- Operating Environment: Take into account temperature, humidity, exposure to chemicals, and outdoor/indoor conditions.
- Speed and Length: Determine the speed at which the belt will operate and the length of the conveyor system.
- Incline/Decline: If the conveyor will operate on an incline or decline, it will affect the type of material and surface texture required.
- Hygiene Requirements: For food, pharmaceutical, or other applications requiring cleanliness, specific materials may be required.
Evaluate Material Properties
Different materials have distinct properties that make them suitable for various applications:
Rubber
- Pros: Good impact resistance, flexibility, and durability. Suitable for heavy loads and abrasive materials.
- Cons: Can degrade with exposure to certain chemicals and extreme temperatures.
- Applications: Mining, bulk material handling, heavy-duty applications.
PVC (Polyvinyl Chloride)
- Pros: Lightweight, good resistance to chemicals, and low cost. Suitable for general-purpose conveying.
- Cons: Limited temperature range and not suitable for heavy or abrasive materials.
- Applications: Packaging, light material handling, food processing (with appropriate FDA compliance).
PU (Polyurethane)
- Pros: High resistance to wear and tear, good chemical resistance, flexible, and suitable for food-grade applications.
- Cons: Can be more expensive than PVC and may have lower impact resistance compared to rubber.
- Applications: Food processing, packaging, light to medium material handling.
Metal (Steel, Stainless Steel)
- Pros: Extremely durable, high temperature and chemical resistance, suitable for heavy loads.
- Cons: High cost, heavier, and less flexible than other materials.
- Applications: High-temperature applications, heavy-duty industries, food processing (stainless steel).
Fabric (Cotton, Nylon, Polyester)
- Pros: Lightweight, flexible, and cost-effective. Can be used as reinforcement layers in composite belts.
- Cons: Lower durability compared to rubber and metal, not suitable for very heavy loads.
- Applications: Light material handling, textile industry, reinforcement layers.
Consider the Surface Texture and Finish
- Smooth Surface: Suitable for gentle handling of products and easy cleaning.
- Rough or Textured Surface: Provides better grip for inclined/declined conveyors or for conveying slippery materials.
- Cleats or Flights: Used for incline/decline applications to prevent material from sliding back.
Check Compliance and Standards
- Food Grade: Ensure the material complies with FDA or other relevant food safety standards for food processing applications.
- Flame Retardant: For applications with fire safety requirements, choose materials that are flame retardant.
- Anti-Static: In environments where static electricity is a concern, choose anti-static materials.
Consult with Suppliers and Experts
- Supplier Recommendations: Work with reputable suppliers who can provide detailed information about the material properties and suitability for your specific application.
- Expert Consultation: Consulting with industry experts or engineers can help in making an informed decision based on the technical requirements and operating conditions.
Test and Validate
- Pilot Testing: If possible, conduct pilot tests with the selected material to validate its performance under actual operating conditions.
- Feedback and Adjustment: Gather feedback from operators and make necessary adjustments to ensure optimal performance and longevity.
By carefully evaluating these factors and material properties, you can select the best conveyor belt material that meets your specific operational needs and enhances the efficiency and durability of your conveyor system.
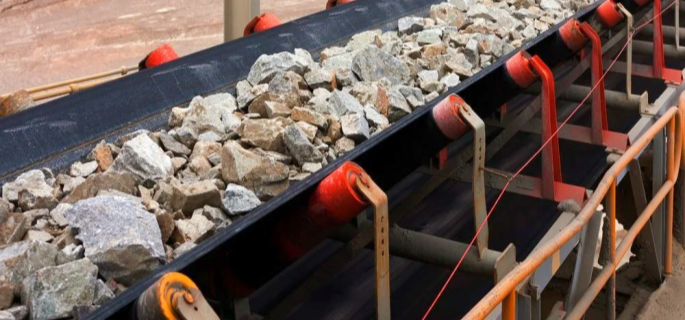
Conveyor Belt Material Properties and Their Impact
In the realm of conveyor belt systems, the conveyor belt material properties play a pivotal role in determining the efficiency, functionality, and durability of the system. Each material contributes distinct characteristics that can significantly affect the overall performance of the conveyor belt. Understanding these properties is essential for selecting the right conveyor belt material for specific industrial applications.
Here, we explore how different materials impact the performance of conveyor belts through a detailed examination of eight key properties:
- Tensile Strength: This is the maximum stress that a material can withstand while being stretched or pulled before breaking. High tensile strength is crucial for materials used in heavy-duty applications where the belts are under constant stress from carrying heavy loads.
- Thermal Resistance: Materials with high thermal resistance can operate effectively in environments with extreme temperatures without degrading. This property is essential for belts used in industries like metalworking or baking, where high temperatures are a norm.
- Chemical Resistance: Conveyor belts must resist corrosion and degradation in environments where chemicals are present. Materials like PVC and polyurethane are valued for their resistance to acids, alkalis, and other aggressive substances.
- Abrasion Resistance: This refers to a material’s ability to withstand mechanical wear and tear. Abrasion-resistant materials are vital for extending the lifespan of conveyor belts used in bulk material handling or mining.
- Flexibility: The ability of a belt to flex without breaking is crucial for systems that involve turns or varying elevations. Materials that offer good flexibility, such as rubber and certain plastics, are preferred for these applications.
- Electrical Conductivity: In environments where static electricity could pose a hazard, materials that can dissipate electrical charge are crucial. For instance, belts in explosive atmospheres or in the electronics manufacturing industry often need to be antistatic.
- Elasticity: Elasticity allows a belt to return to its original shape after being stretched. This property helps maintain tension and stability in the conveyor system, essential for precise and consistent material handling.
- Impact Resistance: The ability of a conveyor belt to absorb impact without suffering permanent damage is critical in industries where sharp or heavy objects are routinely dropped onto the belts.
The interplay of these conveyor belt material properties influences not just the choice of material but also the potential applications of the conveyor system. For instance, while rubber belts are suited for mining due to their durability and elasticity, silicone belts are preferable in food processing for their thermal resistance and non-toxic nature. Selecting the correct material based on these properties ensures that the conveyor belt not only meets the demands of its specific industrial environment but also operates with optimal efficiency and longevity.
Conveyor Belt Material Properties Selection and Properties
Selecting the right material for a conveyor belt is a crucial decision that can significantly affect the efficiency, safety, and cost-effectiveness of a material handling system. Understanding conveyor belt material properties is fundamental to making an informed choice that aligns with operational demands and environmental conditions. Here, we discuss seven key factors that should be considered when selecting materials for conveyor belts, and we provide an overview of the conveyor belt formula used to determine the optimal belt type and size.
Factors to Consider in Material Selection
- Type of Environment: The environment in which the conveyor belt will operate dictates the choice of material. Factors such as temperature, exposure to chemicals, moisture levels, and the presence of UV light can influence material degradation and performance.
- Load Type: The weight and nature of the load being transported are critical. Heavy or sharp objects require durable materials like reinforced rubber or steel, whereas lighter loads can be handled by fabrics or plastics.
- Nature of Materials Transported: If the materials being transported are abrasive, corrosive, or particularly bulky, the conveyor belt material must be selected to withstand these characteristics without excessive wear or damage.
- Speed of Conveyor: High-speed conveyor systems require materials that can handle dynamic stresses and have low friction coefficients to reduce energy consumption and wear.
- Maintenance Requirements: Some materials may require more frequent maintenance or have shorter lifespans, affecting operational costs and downtime. Materials like polyurethane are known for low maintenance needs.
- Cost: Budget constraints can influence material choice, though it’s important to consider total lifecycle costs, including maintenance, downtime, and replacement expenses, not just initial purchase costs.
- Compliance and Safety Standards: Materials must comply with industry-specific safety standards, such as food safety for processing industries or flame resistance in hazardous environments.
Conveyor Belt Formula
To calculate the optimal belt type and size based on load and speed, the following formula can be utilized:
B=L×S×K / C
Where:
- B is the belt width,
- L represents the load per unit length (kg/m),
- S is the speed of the belt (m/s),
- K is a constant that factors in the material properties such as tensile strength and bulk density,
- C is a capacity factor that depends on the roll and pitch of the material.
This formula helps in determining the appropriate belt width and material type needed to safely and effectively transport the intended load at the desired speed. By integrating conveyor belt material properties into this formula, designers can optimize conveyor belt systems for both performance and durability.
A thorough understanding of conveyor belt material properties and careful consideration of the above factors are essential to select the best conveyor belt material for a given application. This selection process ensures that the conveyor system will perform efficiently, safely, and economically over its expected lifespan.

Innovations and Advances in Conveyor Belt Material Properties
Technological advancements in conveyor belt materials have led to significant improvements in performance, durability, and sustainability. These innovations are driven by the continuous pursuit of enhancing conveyor belt material properties to meet the evolving needs of various industries. Here, we provide an overview of nine key technological advancements and explore potential future materials and designs that could revolutionize the conveyor belt industry.
Technological Advancements
- Nano-Coatings: Application of nano-coatings on conveyor belts enhances their resistance to abrasion, chemicals, and UV radiation, prolonging their lifespan and reducing maintenance requirements.
- High-Strength Fibers: Incorporation of high-strength fibers such as aramid and carbon into conveyor belt materials improves tensile strength and reduces belt weight, leading to increased load-bearing capacity and energy efficiency.
- Smart Materials: Integration of sensors and actuators into conveyor belt materials enables real-time monitoring of belt condition, temperature, and load distribution, allowing for predictive maintenance and optimized performance.
- Self-Healing Polymers: Development of self-healing polymers in conveyor belt materials enables them to repair minor damages autonomously, minimizing downtime and extending service life.
- Modular Belts: Modular conveyor belt designs allow for easy customization and quick replacement of damaged sections, improving operational flexibility and reducing maintenance costs.
- Recycled Materials: Utilization of recycled materials in conveyor belt manufacturing reduces environmental impact and promotes sustainability without compromising performance or durability.
- Anti-Microbial Additives: Incorporation of anti-microbial additives in conveyor belt materials inhibits the growth of bacteria and fungi, ensuring hygienic handling of food and pharmaceutical products.
- High-Temperature Resistant Materials: Development of conveyor belt materials capable of withstanding extreme temperatures expands their application range in industries such as steel manufacturing and glass production.
- Lightweight Composite Materials: Adoption of lightweight composite materials in conveyor belts reduces energy consumption, enhances flexibility, and improves overall system efficiency.
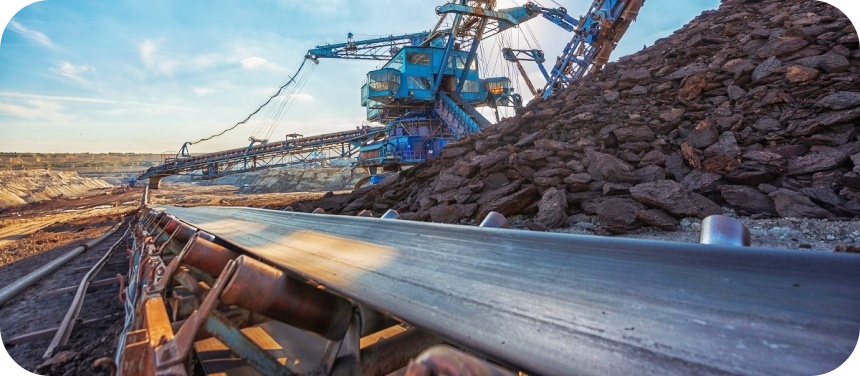
Future Materials and Designs
Looking ahead, several potential innovations could revolutionize the conveyor belt industry:
- Graphene-Enhanced Materials: Integration of graphene, with its exceptional strength and conductivity, could lead to ultra-lightweight and highly durable conveyor belt materials.
- Bio-Degradable Polymers: Development of bio-degradable polymers for conveyor belt manufacturing would address environmental concerns and promote circular economy principles.
- Shape Memory Alloys: Integration of shape memory alloys into conveyor belt materials could enable shape-shifting belts that adapt to changing load conditions and conveyor configurations.
- Nanotechnology Applications: Further exploration of nanotechnology applications in conveyor belt materials could lead to enhanced mechanical properties, self-cleaning surfaces, and advanced functionalities.
- 3D Printing: Advancements in 3D printing technology could facilitate on-demand manufacturing of customized conveyor belt components, reducing lead times and increasing design flexibility.
Ongoing innovations and advances in conveyor belt materials continue to drive improvements in performance, sustainability, and efficiency across industries. By leveraging emerging technologies and exploring novel material compositions, the conveyor belt industry is poised for further transformation, offering enhanced capabilities and addressing evolving customer needs.
Matching Conveyor Belt Material Properties to Application Requirements
Matching conveyor belt material properties to specific application requirements involves a detailed analysis of both the materials’ characteristics and the operational needs of the application. Here’s how you can match conveyor belt material properties to various application requirements:
Application Requirements and Matching Material Properties
1. Heavy Load Handling
- Requirements: High tensile strength, durability, impact resistance.
- Material Properties:
- Rubber: Excellent for heavy loads and impact resistance.
- Steel: Extremely strong and durable for very heavy loads and harsh environments.
- Fabric Reinforced Belts: Added strength from fabric layers like polyester or nylon.
2. Abrasive Material Handling
- Requirements: High abrasion resistance, durability.
- Material Properties:
- Rubber: High resistance to wear and tear, suitable for abrasive materials.
- PU (Polyurethane): Good abrasion resistance, suitable for less extreme abrasives.
3. Chemical Resistance
- Requirements: Resistance to oils, chemicals, and solvents.
- Material Properties:
- PVC (Polyvinyl Chloride): Good resistance to a variety of chemicals.
- PU (Polyurethane): Excellent chemical resistance.
- Stainless Steel: Exceptional resistance to corrosive chemicals and high temperatures.
4. Temperature Resistance
- Requirements: Ability to withstand high or low temperatures without degrading.
- Material Properties:
- Steel: Excellent for high-temperature applications.
- Silicone Belts: Suitable for high-temperature food processing.
- PTFE (Polytetrafluoroethylene): High heat resistance and non-stick properties.
- Rubber: Suitable for moderate temperature ranges.
5. Food Processing
- Requirements: Food-grade materials, easy to clean, non-toxic.
- Material Properties:
- PU (Polyurethane): Food-grade, resistant to oils and fats, easy to clean.
- Stainless Steel: Food-grade, hygienic, and durable.
- PVC (Polyvinyl Chloride): Food-grade options available, suitable for general food processing.
6. Incline/Decline Conveying
- Requirements: High friction surface, cleats or textured patterns to prevent slippage.
- Material Properties:
- Rubber: High friction and flexibility, suitable for inclines.
- Cleated Belts: Available in various materials with cleats to handle inclines.
- Textured PVC/PU: Surface textures to enhance grip.
7. Static-Sensitive Environments
- Requirements: Anti-static properties to prevent static buildup.
- Material Properties:
- Anti-Static PVC/PU: Specifically designed to prevent static buildup.
- Conductive Rubber: Contains conductive materials to dissipate static electricity.
8. Lightweight and Flexible Applications
- Requirements: Flexibility, lightweight, ease of handling.
- Material Properties:
- Fabric Belts (Cotton, Nylon, Polyester): Lightweight and flexible, suitable for light loads.
- PVC: Lightweight and flexible, suitable for various general-purpose applications.
Summary of Material Selection Based on Properties
Application Requirement | Best Material(s) | Key Properties |
---|---|---|
Heavy Load Handling | Rubber, Steel, Fabric Reinforced Belts | High tensile strength, impact resistance |
Abrasive Material Handling | Rubber, PU | High abrasion resistance, durability |
Chemical Resistance | PVC, PU, Stainless Steel | Chemical resistance, durability |
Temperature Resistance | Steel, Silicone, PTFE, Rubber | High/low temperature resistance |
Food Processing | PU, Stainless Steel, PVC | Food-grade, easy to clean, non-toxic |
Incline/Decline Conveying | Rubber, Cleated Belts, Textured PVC/PU | High friction, cleats or textures for grip |
Static-Sensitive Environments | Anti-Static PVC/PU, Conductive Rubber | Anti-static properties |
Lightweight and Flexible Applications | Fabric Belts (Cotton, Nylon, Polyester), PVC | Flexibility, lightweight, ease of handling |
Practical Steps for Selection
- Define Requirements: Clearly outline the specific needs of your application.
- Evaluate Options: Compare the material properties against these requirements.
- Consult Suppliers: Seek advice and recommendations from reputable suppliers.
- Test Samples: If possible, test material samples in real operating conditions.
- Make an Informed Decision: Choose the material that best matches your operational needs and budget constraints.
By aligning the conveyor belt material properties with the application requirements, you can ensure optimal performance, longevity, and efficiency in your conveyor system.
Practical Applications and Examples of Conveyor Belt Material Properties
The practical applications of conveyor belts across various industries highlight the critical role of conveyor belt material properties in achieving operational success. Different types of conveyor belts, each tailored with specific material properties, provide unique advantages in handling the diverse requirements of various sectors. Here, we discuss eight real-world applications of conveyor belts and present case studies that underscore how material properties have significantly impacted performance and efficiency.
Real-World Applications
- Mining Industry: Heavy-duty rubber belts with high tensile strength and abrasion resistance are used to transport ores and minerals over long distances in rugged terrain.
- Food Processing: Conveyor belts made from food-grade materials like PVC and silicone, which offer easy cleaning and resistance to bacterial growth, are essential for maintaining hygiene and preventing contamination.
- Packaging Industry: Lightweight and flexible fabric belts are utilized to handle various packaging operations smoothly and efficiently, adapting to different shapes and sizes of packages.
- Agriculture: Durable and moisture-resistant conveyor belts are used for moving grain and other agricultural products, which require resistance to the outdoor environment and variable weather conditions.
- Pharmaceuticals: Antistatic and chemical-resistant conveyor belts are critical in pharmaceutical manufacturing, where cleanliness and precise handling of sensitive materials are paramount.
- Aerospace: Advanced composite materials are employed in conveyor systems for handling aircraft parts, where strength, lightweight, and resistance to extreme temperatures and chemicals are required.
- Recycling Operations: Rubber belts reinforced with metal or other strong fibers are used in recycling plants to withstand the sharp and heavy recycled materials while preventing belt damage.
- Retail Warehousing: Automated conveyor systems using modular and synthetic belts help in the rapid sorting and distribution of goods in large warehouses, improving logistics and reducing labor costs.
Case Studies
Mining Conveyor Belt Optimization
In a large mining operation, traditional conveyor belts were frequently tearing and suffering from excessive wear due to the abrasive nature of the mined ores. By switching to a belt made from a new rubber compound specifically engineered for high abrasion resistance and incorporating high-strength fibers, the mine significantly reduced downtime and maintenance costs, enhancing overall productivity.
Food Industry Efficiency Improvement
A food processing plant was experiencing issues with bacterial contamination on its standard PVC conveyor belts. The introduction of a new conveyor belt material featuring anti-microbial additives and a smoother surface that is easier to clean led to a marked reduction in contamination incidents and downtime for cleaning, thus improving safety and operational efficiency.
These case studies illustrate how understanding and applying specific conveyor belt material properties can lead to substantial improvements in the performance and efficiency of conveyor systems. As industries continue to evolve and face new challenges, the development and selection of appropriate conveyor belt materials will remain crucial for meeting the increasingly complex and varied demands of modern industrial operations.
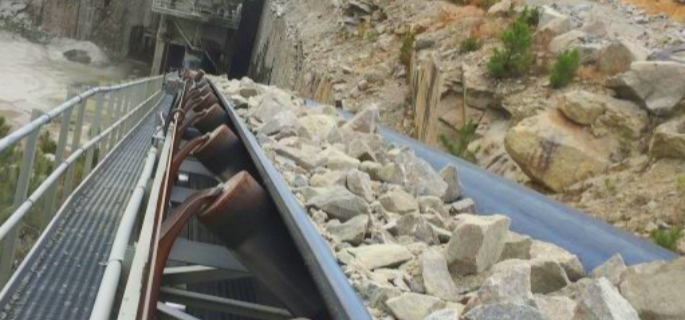
FAQs about Conveyor Belt Material Properties
Conveyor belts are made from a variety of materials, each selected based on the requirements of strength, flexibility, and durability needed for the specific application. Common materials include:
Rubber: Often reinforced with layers of fabric or steel cables, rubber is prized for its flexibility, durability, and ability to handle rough and abrasive materials.
PVC (Polyvinyl Chloride): PVC belts are suitable for food industry applications due to their resistance to oils and chemicals.
Polyurethane: Known for its hygienic qualities, making it ideal for food processing industries. It’s also wear-resistant and capable of handling lighter duties.
Metal: Employed in high-temperature environments or where durability and load capability are critical, such as in mining or quarrying.
Fabric belts: Made with layers of fabrics like polyester, nylon, or natural fibers to provide different levels of stretch and wear resistance.
These materials can be used alone or combined to enhance functional properties like heat resistance and tensile strength.
To manufacture a conveyor belt, you need:
Base belt material: Rubber, plastic (PVC or polyurethane), or metal.
Reinforcement fabric: Fabrics like nylon, polyester, or cotton can be woven into the belt to provide additional strength and resistance to stretching.
Coatings or treatments: Depending on the belt’s usage, various coatings can be applied for properties like resistance to heat, oil, or chemicals. Materials like PVC or Teflon might be used for coatings.
Structural components: For enhanced durability, materials such as steel cables or Kevlar fibers can be incorporated, particularly in belts used for heavy loads or high-stress applications.
The choice and combination of materials depend primarily on the belt’s intended use, the environmental conditions it will face, and the physical demands of the transported materials.
The specification of a conveyor belt includes:
Width and length: Dimensional specifications that suit the application’s load and the conveyor system’s size.
Tensile strength: The maximum load the belt can handle.
Material composition: Identifies the types of materials used and their proportions in the belt’s construction.
Thickness: Depending on the belt type, thickness can affect durability and flexibility.
Top and bottom cover thickness and material: These protect the belt’s core from environmental factors and load-based wear and tear.
Operating environment: Specifications may also define the belt’s suitability for operating temperatures, exposure to chemicals, or food safety standards.
The specifications ensure that a conveyor belt will perform effectively in its designated role within specific operational parameters.
Belt materials vary by the type and function of the belt but typically include:
Rubber: Provides a flexible, durable surface with good grip.
PVC and Polyurethane: These plastics offer excellent resistance to oils, fats, and chemicals, making them suitable for food processing belts.
Fabric: Materials like polyester, nylon, and cotton are used depending on the required strength, flexibility, and cost.
Steel and other metals: Used for their strength and heat resistance, suitable for heavy-duty and high-temperature applications.
Composite materials: Some belts are made from a combination of materials, like a rubber belt with a fabric reinforcement or a metal belt with a rubber coating, to optimize performance attributes.
Choosing the correct material will depend on the belt’s envisioned use, including the types of materials it will carry and the environment it will operate in.
Conveyor belt shafts are typically made from materials that offer high strength, durability, and resistance to wear and tear. Common materials used for conveyor belt shafts include steel and stainless steel. Steel shafts are widely used due to their excellent mechanical properties, including high tensile strength and toughness, making them suitable for heavy-duty applications. Stainless steel shafts are preferred in environments where corrosion resistance is crucial, such as in food processing, pharmaceuticals, and chemical industries. Stainless steel provides excellent resistance to rust and corrosion, ensuring longevity and reliability even in harsh conditions. Additionally, for specialized applications, shafts may be made from materials like aluminum, which offers lightweight properties, or composite materials for specific performance characteristics. The choice of material depends on the specific requirements of the conveyor system, including load capacity, environmental conditions, and maintenance considerations.
Last Updated on July 9, 2024 by Jordan Smith
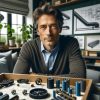
Jordan Smith, a seasoned professional with over 20 years of experience in the conveyor system industry. Jordan’s expertise lies in providing comprehensive solutions for conveyor rollers, belts, and accessories, catering to a wide range of industrial needs. From initial design and configuration to installation and meticulous troubleshooting, Jordan is adept at handling all aspects of conveyor system management. Whether you’re looking to upgrade your production line with efficient conveyor belts, require custom conveyor rollers for specific operations, or need expert advice on selecting the right conveyor accessories for your facility, Jordan is your reliable consultant. For any inquiries or assistance with conveyor system optimization, Jordan is available to share his wealth of knowledge and experience. Feel free to reach out at any time for professional guidance on all matters related to conveyor rollers, belts, and accessories.