Drive Belt Conveyor System Essentials for Beginners
The drive belt conveyor system has become an indispensable component in modern industrial operations, reflecting both its importance and evolutionary advancements. Originally simple mechanisms, these systems have transformed into complex assemblies crucial for efficient material handling across various sectors. The evolution of the drive belt conveyor system is marked by significant enhancements in durability, efficiency, and adaptability, making them pivotal in the seamless operation of assembly lines, mining operations, and packaging facilities. This introduction underscores the critical role drive belt conveyor systems play, not just in transporting goods, but in optimizing productivity and reducing operational costs within countless industrial applications.
Comprehensive Insights into a Drive Belt Conveyor System
Understanding the definition and basic mechanics of a drive belt conveyor system is essential for optimizing its efficiency and reliability across various industrial applications. At its core, a drive belt conveyor system consists of a series of components that work together to move materials efficiently over distances.
Definition and Mechanics of a Drive Belt Conveyor System
A drive belt conveyor system utilizes a continuous loop of a durable material — typically rubber, PVC, or fabric — which is propelled by pulleys. One or more of these pulleys are powered by a motor, typically electric, which is crucial in driving the conveyor belt. This setup is foundational in industries where large volumes of goods need to be moved from one point to another, making the drive belt conveyor system a backbone of material handling operations.
Components of the System
- Motor: The primary driver, providing the necessary power to move the conveyor belt.
- Drive Pulley: Directly transfers power from the motor, driving the conveyor belt.
- Return Pulley: Allows the belt to loop back and continuously carry materials.
Role of the Conveyor Belt Drive Motor
The conveyor belt drive motor plays a pivotal role in the functioning of a drive belt conveyor system. It not only determines the speed and efficiency with which materials are moved but also influences the system’s overall reliability and performance. The motor’s power output needs to be adequately matched with the system’s demands to ensure efficient operation without overloading or excessive wear.
Importance of Motor Selection
Choosing the right motor involves considering several factors:
- Power Output: Ensuring the motor can handle the load and speed requirements of the conveyor system.
- Energy Efficiency: Optimizing power use to reduce operational costs and environmental impact.
- Durability: Selecting a motor that can withstand the specific environmental conditions of the operation, thus ensuring reliability and longevity.
Essential Components of a Drive Belt Conveyor System
Conveyor Drive Unit
The Conveyor Drive Unit is crucial to the operation of a drive belt conveyor system. It is responsible for the movement of the conveyor belt and, consequently, the materials being transported. The unit primarily consists of three integral parts:
- Motor: This is the powerhouse of the drive unit. The motor’s role is to provide the mechanical energy needed to move the belt. Its specifications, including power output and torque, are critical to matching the demands of the conveyor system, ensuring efficient handling of loads without overstressing the system.
- Gears: Positioned between the motor and the drive pulley, gears help in adjusting the motor’s output to suit the conveyor speed and force requirements. They play a pivotal role in the transmission of power and can significantly influence the system’s operational efficiency and noise levels.
- Belt: The conveyor belt is the component that physically moves the load. Made from materials that can withstand various industrial environments, the belt’s quality directly affects the conveyor system’s efficacy and durability.
Belt Take-Up Units
Belt Take-Up Units are vital for maintaining the necessary tension in the conveyor belt of a drive belt conveyor system. Proper tension is crucial for optimal performance and extended life of the belt and system as a whole.
- Purpose: These units ensure that the conveyor belt operates with sufficient tension, which is essential to prevent slippage on the drive pulley. Consistent belt tension helps in maintaining steady movement of the conveyor, even under varying load conditions.
- Function: Belt take-up units adjust the tension of the conveyor belt by moving the take-up pulley, which in turn affects the belt’s tautness. This adjustment is crucial during the initial installation and periodically throughout the belt’s service life to accommodate stretch, wear, and environmental changes.
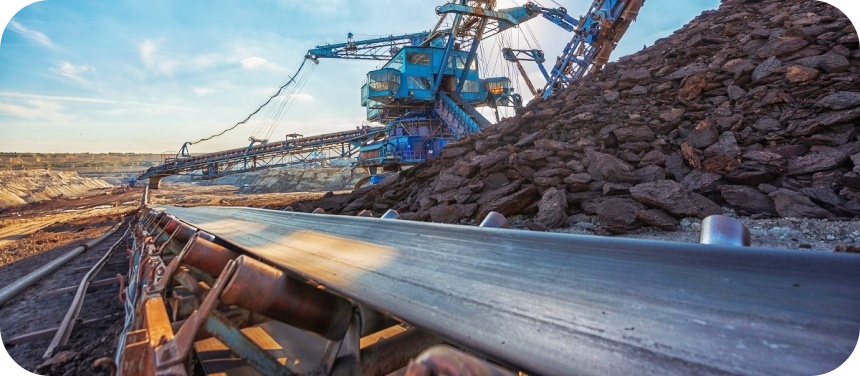
Varieties and Applications of Underground and Overland Drive Belt Conveyor Systems
Underground Conveyor Belt Systems
Underground conveyor belt systems are a specialized category of drive belt conveyor systems, designed specifically to operate efficiently in the challenging environments of underground mining and tunneling. These systems require special design considerations to ensure safety and durability under harsh conditions such as dust, moisture, and limited space.
- Design Considerations: Key design features include robust construction to withstand abrasive materials and potentially corrosive environments. Additionally, the system components, such as motors and belts, are often enclosed to protect them from the surrounding environment and to ensure the safety of the operating personnel.
- Safety Features: Safety is paramount in underground operations. These systems are equipped with numerous safety features like emergency stop mechanisms, fire-resistant materials, and explosion-proof components. Enhanced monitoring and control systems are also integral to detect and manage any operational anomalies promptly.
Overland Conveyors
Overland conveyors are another type of drive belt conveyor system, utilized primarily for moving bulk materials over long distances. These conveyors are critical in industries such as mining, agriculture, and construction where large volumes of materials need to be transported efficiently across vast areas.
- Extensive Material Transportation: Overland conveyors are designed to handle large volumes of materials, which can significantly reduce the number of trucks and heavy vehicles required, leading to a decrease in operational costs and environmental impact.
- Impact on Operational Costs: The implementation of overland conveyors in a drive belt conveyor system can lead to substantial savings in fuel, labor, and maintenance costs. They are also associated with lower emissions compared to traditional truck transport, making them an environmentally friendly option for large-scale operations.
Both underground and overland conveyor systems are integral to the efficient operation of various industries, offering specialized solutions that enhance productivity and safety. Understanding the specific requirements and challenges associated with each type can help in designing a drive belt conveyor system that best fits the needs of the operation.
Drive Belt Conveyor System Innovations from West River Conveyors and Continental Belts
West River Conveyors
West River Conveyors has established itself as a leader in providing custom drive belt conveyor system solutions tailored specifically for the mining and bulk material handling sectors. Their approach focuses on designing systems that meet the unique demands of each operation, ensuring optimal efficiency and safety.
- Custom Solutions: West River Conveyors excels in engineering drive belt conveyor systems that are built to handle the specific challenges of mining environments. These conveyors are designed to manage everything from fine powders to large, abrasive materials, with customization options that include belt width, conveyor path configurations, and materials used in construction to enhance durability and functionality.
- Mining and Bulk Material Handling: Their systems are known for robust construction that withstands the harsh environments of underground and open-pit mines. Features such as dust-proof enclosures for motors and high-load capacity designs ensure that their conveyors perform reliably under the most demanding conditions.
Continental Conveyor Belts
Continental Conveyor Belts are renowned for their innovative materials and technologies that push the boundaries of drive belt conveyor system design. Their products are pivotal in enhancing the efficiency and longevity of conveyor systems across various industries.
- Advanced Materials: Continental’s commitment to innovation is evident in their use of high-tech materials that increase the life span and reduce the maintenance needs of their belts. Materials like thermoplastic polyurethane, which offers exceptional wear resistance and cleanliness, are commonly used in their designs.
- Technology in Conveyor Belt Construction: Continental has pioneered technologies such as sensor-equipped belts that monitor wear and tear in real time, enabling predictive maintenance. This not only prevents unexpected downtime but also ensures that the conveyor system operates at peak efficiency.
Both West River Conveyors and Continental Conveyor Belts continue to lead the way in developing advanced drive belt conveyor systems that meet the evolving needs of industries worldwide. Their focus on customization and innovative material use significantly enhances the operational capabilities of conveyor systems, making them more efficient, safer, and more adaptable to various environmental conditions.
Guidelines for Installing and Maintaining a Drive Belt Conveyor System
Installation of Drive Belt Conveyor Systems
Proper installation is crucial for the efficient and safe operation of a drive belt conveyor system. This process involves several critical steps that must be meticulously planned and executed:
- Site Preparation: Before installation, ensure that the site is prepared with adequate space and the necessary infrastructure to support the conveyor system. This includes leveling the ground and preparing foundations for heavy components.
- Assembly of Components: Follow the manufacturer’s guidelines to assemble the various parts of the conveyor system, such as the frame, drive units, belts, and electrical controls. It is vital to ensure that all components are aligned and secured correctly to prevent any operational issues.
- Testing: Before full-scale operation, conduct extensive testing to verify that all components of the drive belt conveyor system work harmoniously. This includes checking the motor, drive mechanisms, belt alignment, and control systems to ensure they function as intended.
Maintenance of Drive Belt Conveyor Systems
Regular maintenance is key to extending the life and efficiency of a drive belt conveyor system. It involves several best practices:
- Regular Inspections: Schedule regular inspections to identify any signs of wear or damage early. Check critical components such as the belt, motors, bearings, and electrical systems. This proactive approach helps in addressing potential issues before they lead to significant downtime.
- Preventive Maintenance: Implement a preventive maintenance program that includes tasks such as lubricating moving parts, tightening loose components, and replacing worn parts. This program should be based on the manufacturer’s recommendations and adjusted based on the specific operating conditions of the conveyor system.
- Record Keeping: Maintain detailed records of inspections, maintenance activities, and any repairs carried out on the drive belt conveyor system. This documentation helps in tracking the system’s performance and planning future maintenance activities more effectively.
Ensuring optimal functionality of a drive belt conveyor system requires diligent installation and ongoing maintenance. By adhering to these best practices, companies can achieve maximum efficiency and longevity from their conveyor systems, ultimately reducing operational costs and improving productivity.
Drive Belt Conveyor System Case Studies: Enhancing Productivity Across Industries
Successful Implementations of Drive Belt Conveyor Systems
Numerous industries have witnessed significant operational improvements through the implementation of drive belt conveyor systems. These case studies highlight the versatility and efficiency of these systems in real-world settings.
- Mining Industry: In a large-scale gold mining operation, the introduction of a custom-designed drive belt conveyor system resulted in a 30% increase in material transport efficiency. The system was specifically engineered to handle the rugged terrain and the high volume of materials, reducing the reliance on truck haulage and lowering operational costs significantly.
- Agriculture: A farming cooperative implemented a drive belt conveyor system to streamline the processing of grains from harvest to storage. This system reduced grain handling times by 40% and minimized losses due to spillage, significantly boosting the cooperative’s overall productivity.
- Manufacturing: An automotive parts manufacturer integrated several drive belt conveyor systems within their assembly lines. This strategic integration allowed for a smoother flow of components between different stages of assembly, reducing cycle times and increasing the plant’s output by 25%.
Impact on Productivity and Efficiency
The adoption of drive belt conveyor systems has a profound impact on productivity and efficiency within various sectors:
- Enhanced Operational Speed: Drive belt conveyor systems facilitate faster movement of materials compared to manual handling or other mechanical means. This speed enhancement is critical in high-demand scenarios, such as in manufacturing and mining, where time savings translate directly into cost reductions.
- Improved Workplace Safety: By automating the transport of heavy or hazardous materials, drive belt conveyor systems reduce the risk of workplace injuries. This improvement in safety not only protects workers but also decreases downtime due to accidents and related investigations.
- Reduced Operational Costs: The efficiency of drive belt conveyor systems significantly lowers energy consumption and manpower requirements. For example, in mining operations, the shift from truck haulage to conveyor systems can cut fuel costs dramatically, while also reducing maintenance expenses associated with vehicle fleets.
These case studies and impacts demonstrate the transformative role that drive belt conveyor systems can play in enhancing productivity and efficiency across a broad range of industries. By understanding and leveraging the capabilities of these systems, organizations can achieve substantial operational improvements, leading to increased competitiveness and sustainability.
Projections on the Evolution and Technological Advancements in Drive Belt Conveyor Systems
Technological Advancements in Drive Belt Conveyor Systems
The future of drive belt conveyor systems is set to be transformed by several technological advancements. These innovations are expected to revolutionize the way materials are handled across various industries, enhancing both efficiency and reliability.
- Automation: Advancements in automation technology are making drive belt conveyor systems smarter and more autonomous. Sensors and programmable logic controllers (PLCs) are increasingly being integrated to enable real-time monitoring and control of the conveyor operations, which enhances the accuracy and speed of material handling.
- Artificial Intelligence (AI): AI is beginning to play a crucial role in optimizing drive belt conveyor system operations. Through predictive analytics, AI can forecast maintenance needs and operational disruptions before they occur. This capability not only prevents downtime but also extends the lifespan of the equipment by ensuring timely maintenance.
- Material Science: Innovations in material science are leading to the development of more durable and efficient conveyor belts. New materials are being designed to withstand harsher conditions, reduce energy consumption, and minimize maintenance needs. These materials include composites that are both lighter and stronger than traditional materials.
Preparing for Integration of Automated and AI-driven Systems
As drive belt conveyor systems evolve, companies must prepare to integrate more sophisticated technologies to stay competitive. Here are some strategies to consider:
- Investment in Skilled Workforce: Training and developing a workforce capable of operating and maintaining advanced conveyor systems is crucial. As systems become more integrated with AI and automation, the skill sets required will change, necessitating ongoing education and training.
- Upgrading Infrastructure: To accommodate advanced technologies, companies may need to upgrade their existing infrastructure. This could involve installing more robust networking capabilities, enhancing power supplies, or redesigning layouts to accommodate new types of conveyor systems.
- Collaboration with Technology Providers: Forming partnerships with technology providers can help companies stay at the forefront of innovation. These collaborations can provide access to the latest technologies and expertise, enabling companies to implement advanced solutions that optimize their conveyor operations.
The future trends in drive belt conveyor systems are shaping up to make these systems more integral than ever to industrial operations. By embracing these advancements and preparing for their integration, companies can ensure that they remain competitive in an increasingly automated and efficient industrial landscape.
Fill out the form for pricing and details on our conveyor belts.
Considerations for Selecting the Optimal Drive Belt Conveyor System for Specific Applications
Factors to Consider When Selecting a Drive Belt Conveyor System
Choosing the right drive belt conveyor system involves a careful assessment of several factors to ensure the selected system meets the specific needs of your operations efficiently and effectively.
- Cost: Evaluate the initial investment against the expected operational and maintenance costs over the system’s lifespan. It’s crucial to balance upfront costs with long-term savings and efficiency gains.
- Environment: The environmental conditions where the conveyor will operate can significantly affect its design and material choice. For instance, systems used in outdoor, dusty, or wet conditions require different specifications to withstand such environments compared to those used indoors.
- Material Type: The type of materials the conveyor will handle must also be considered. Different materials like bulk goods, heavy loads, or hazardous substances require specific types of conveyor systems that can handle them safely and efficiently.
- System Flexibility and Scalability: Consider whether the conveyor system can adapt to future changes or expansions in production. A modular system might offer more flexibility than a custom-built, fixed installation.
Collaborating with Manufacturers for Customized Solutions
Working closely with manufacturers like West River Conveyors can significantly enhance the process of selecting and customizing a drive belt conveyor system.
- Define Your Needs: Clearly communicate your operational requirements, challenges, and expectations with the manufacturer. This includes throughput rates, space limitations, and specific operational goals.
- Leverage Expertise: Manufacturers like West River Conveyors bring a wealth of experience and can provide insights into what systems can best meet your needs. They can suggest innovations and adjustments that might not be immediately obvious to someone outside the conveyor industry.
- Customization Options: Explore customization options that can make a standard conveyor system better suited for your specific conditions. Custom tailoring might involve special belt materials for high-temperature environments, unique conveyor layouts to fit within existing spaces, or integrated sensors for monitoring wear and efficiency.
- After-Sales Support: Ensure that the manufacturer provides robust after-sales support. This includes maintenance, parts replacement, and possibly training for your team on the new system’s operation and maintenance.
FAQs about Drive Belt Conveyor System
The drive system of a belt conveyor is the mechanism that propels the conveyor belt, enabling it to transport materials along the assembly line or processing area. This system typically consists of a motor, a drive pulley, and a gearbox. The motor provides the power, converting electrical energy into mechanical motion. The gearbox adjusts the motor’s speed and torque to suit the conveyor’s operational needs. The drive pulley, which is attached to the motor and gearbox via a shaft or directly, transfers this motion to the conveyor belt. Depending on the design and requirements of the conveyor, the drive system can be positioned at either end of the conveyor or even at the center to facilitate specific operational dynamics.
Conveyor belts are driven by a combination of motors and drive pulleys that work together to move the belt. The motor powers the system, while the drive pulley, which is mounted on a shaft connected to the motor, transfers this power onto the belt. In some systems, a gearbox is also included to adjust the speed and torque from the motor. The drive pulley typically has a larger diameter compared to other pulleys in the system to provide greater contact surface with the belt, which increases friction and facilitates better traction. The drive can be direct, where the motor is connected directly to the pulley, or indirect, involving chains or belts linking the motor to the pulley. The choice of drive method depends on the conveyor’s load, speed requirements, and operational environment.
The drive unit of a conveyor is the assembly that includes the motor, drive pulley, and sometimes a gearbox, all of which work together to move the conveyor belt. This unit is crucial for the conveyor’s operation as it dictates the speed and force with which the belt moves. The motor’s specifications, such as power and torque, need to be chosen based on the conveyor’s size, the weight of the materials being transported, and the speed at which the materials need to be moved. The gearbox, if present, modulates the motor’s output to ensure that the conveyor operates within the desired parameters, thereby preventing any mechanical stress or inefficiency in the system.
The drive pulley in a conveyor system serves as the primary point of transfer for the motor’s power to the conveyor belt. It is located at one end of the conveyor and is powered by the motor, either directly or through a gearbox and drive shaft. The drive pulley’s function is to exert the necessary traction on the conveyor belt to initiate and maintain its motion. It is typically coated or treated with materials such as rubber to increase the friction between the pulley and the belt. This treatment ensures that the belt does not slip and provides smooth, consistent movement of the belt across the conveyor system, which is essential for the efficient handling of materials.
Last Updated on August 1, 2024 by Jordan Smith
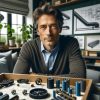
Jordan Smith, a seasoned professional with over 20 years of experience in the conveyor system industry. Jordan’s expertise lies in providing comprehensive solutions for conveyor rollers, belts, and accessories, catering to a wide range of industrial needs. From initial design and configuration to installation and meticulous troubleshooting, Jordan is adept at handling all aspects of conveyor system management. Whether you’re looking to upgrade your production line with efficient conveyor belts, require custom conveyor rollers for specific operations, or need expert advice on selecting the right conveyor accessories for your facility, Jordan is your reliable consultant. For any inquiries or assistance with conveyor system optimization, Jordan is available to share his wealth of knowledge and experience. Feel free to reach out at any time for professional guidance on all matters related to conveyor rollers, belts, and accessories.