Belt Conveyor Design Guide: Quick Tips and Handbook
Welcome to the Belt Conveyor Design Guide, where we delve into the essentials of belt conveyor systems and their pivotal role in material handling. This guide is crafted to help both newcomers and seasoned professionals understand the fundamental principles of belt conveyor design and their practical applications. Conveyors are integral to various industries, moving everything from bulk materials in mining operations to packages in distribution centers. Our objective is to outline clear, actionable design principles that optimize efficiency, safety, and reliability. Join us as we explore how effective design can transform the functionality and operational success of conveyor systems. This introduction sets the stage for a comprehensive journey through the belt conveyor design guide.
Belt Conveyor Design Guide: Understanding the Basics from Handbooks and Their Relevance
In this section of the Belt Conveyor Design Guide, we explore the foundational concepts laid out in the belt conveyor design handbook pdf. This handbook serves as a critical resource, offering in-depth explanations of the mechanical and structural aspects of conveyor systems. It includes detailed information on design parameters, such as load capacity, belt speed, conveyor belt material properties, and the geometric considerations of conveyor layouts.
Key Concepts from the Handbook
The belt conveyor design handbook pdf systematically breaks down each component of the conveyor system, providing guidelines on how to design for optimal efficiency and durability. Topics covered include selecting the appropriate belt type, calculating the maximum load the conveyor can handle, and choosing suitable drive mechanisms.
Relevance of Foundational Design Principles
Understanding these principles is essential for applying modern technological advances to belt conveyor systems. The principles not only ensure the conveyor’s operational reliability but also enhance safety and reduce maintenance costs. This discussion highlights how traditional design concepts remain relevant, even as new materials and technologies emerge that can significantly improve conveyor performance.
Belt Conveyor Design Guide: Utilizing Calculations for Efficiency in Conveyor Systems
In this critical section of the Belt Conveyor Design Guide, we focus on the practical application of belt conveyor design calculations pdf to enhance the efficiency and functionality of conveyor systems. This guide provides a detailed walkthrough of various calculation methods that are vital for designing an effective mine conveyor belt system.
Detailed Walkthrough of Belt Conveyor Design Calculations
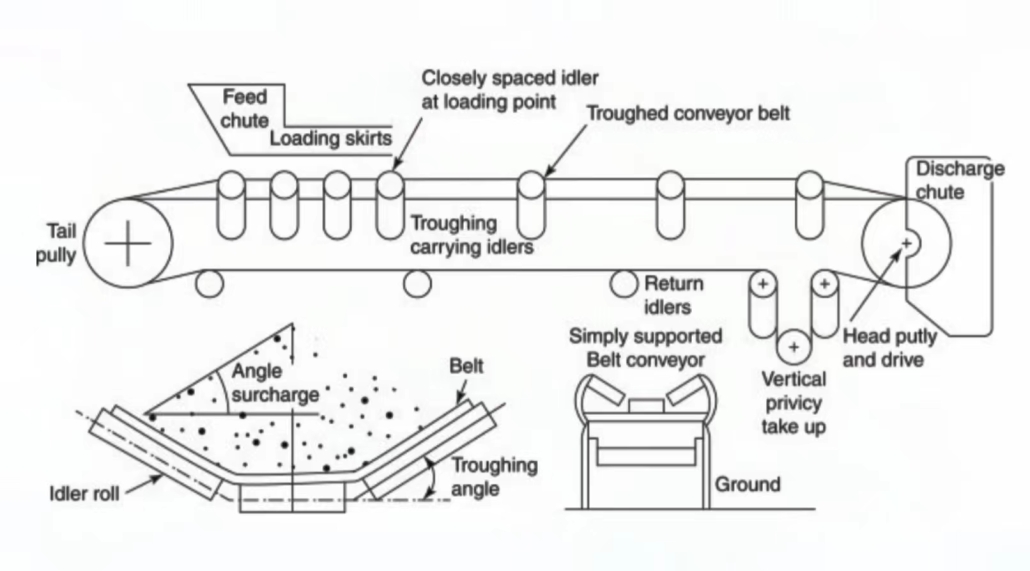
The belt conveyor design calculations pdf includes formulas and methodologies essential for determining the optimal parameters such as belt load, speed, motor power, and tension. These calculations are fundamental in conveyor belt system design that can handle the required capacity while operating efficiently and safely.
Applying Belt Conveyor Design Calculation Examples
To illustrate how these calculations are applied in real-world scenarios, this section includes examples and case studies. Each example demonstrates how to tailor specific conveyor requirements using the formulas provided in the handbook. For instance, calculating the required motor power for a given load and conveyor length helps in selecting the right motor, ensuring that the system is not underpowered or wastefully overpowered.
Belt Conveyor Design Guide: Parts and Assembly for Optimal Functionality
In this crucial section of the Belt Conveyor Design Guide, we offer a comprehensive breakdown of the components involved in conveyor systems, utilizing the belt conveyor parts pdf as a key reference. Understanding each part is vital for efficient assembly, routine maintenance, and effective troubleshooting.
Comprehensive Breakdown of Conveyor Parts
The belt conveyor parts pdf details every component that makes up a conveyor system. This includes the belts themselves, motors, rollers, idlers, frames, and electrical systems. Each part is described in terms of its function, specifications, and integration within the system. This detailed breakdown helps designers and engineers visualize how these parts work together to form a cohesive unit.
Importance of Knowing Each Part
Knowledge of each component is essential not only for the assembly process but also for maintaining the conveyor over its operational life. Familiarity with the parts allows for quicker identification of problems and more efficient troubleshooting when issues arise. This understanding is crucial for minimizing downtime and ensuring the conveyor operates at optimal efficiency. Regular maintenance checks, guided by a deep understanding of each component’s role and requirements, can prevent small issues from becoming major disruptions.
Belt Conveyor Design Guide: Selection and Specification for Optimal Performance
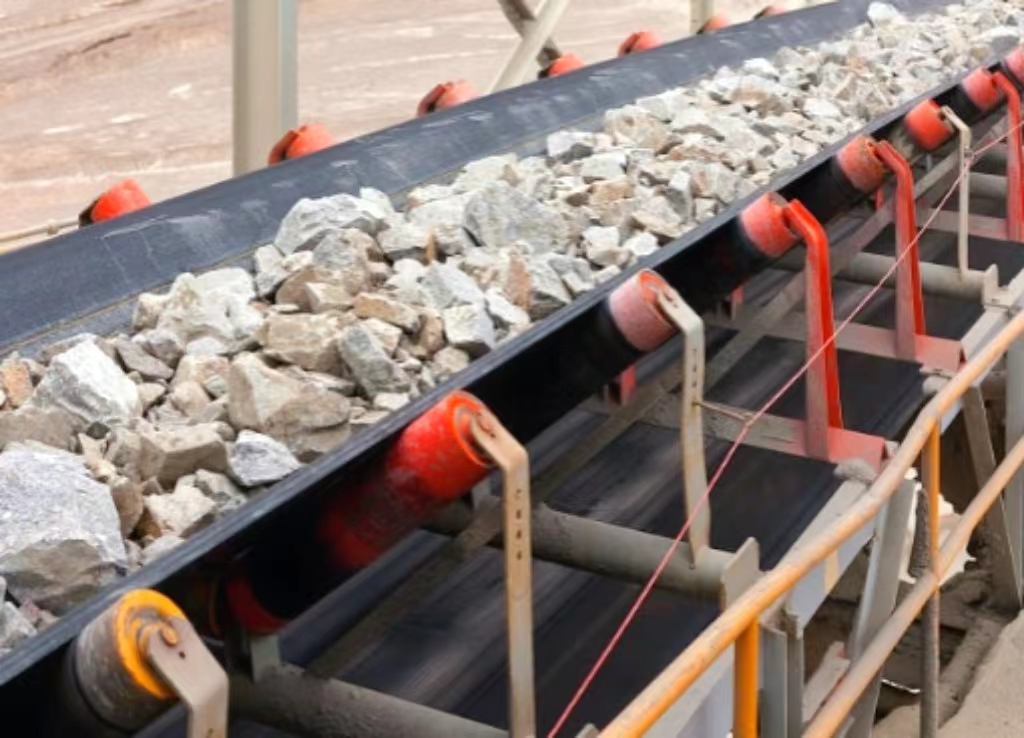
In this essential section of the Belt Conveyor Design Guide, we delve into the process of selecting the right conveyor belt for various applications, guided by the conveyor belt selection guide. Choosing the appropriate belt type is critical for ensuring the efficiency, safety, and longevity of the conveyor system.
Guidance from the Conveyor Belt Selection Guide
The conveyor belt selection guide provides detailed information on the types of conveyor belts available and their best uses. This guide helps designers choose the right belt based on the specific needs of their project, considering factors such as the nature of the materials being transported, the speed of the conveyor, and the required durability of the belt.
Factors Influencing Belt Selection
Several key factors must be considered when selecting a conveyor belt:
- Material Characteristics: The types of conveyor belt material can greatly influence the choice of belt material based on the materials the belt will carry. For example, abrasive materials require a belt with high wear resistance, while sticky materials might need belts with specific surface properties to prevent material buildup.
- Load Specifications: The weight and volume of the load the conveyor will handle also dictate the type of belt needed. Heavier loads require belts with greater strength and durability to prevent premature wear and failure.
- Environmental Conditions: The environment in which the conveyor will operate affects belt selection. Extreme temperatures, exposure to chemicals, or the presence of water and humidity are all factors that can influence the material and type of belt chosen to ensure operational reliability and longevity.
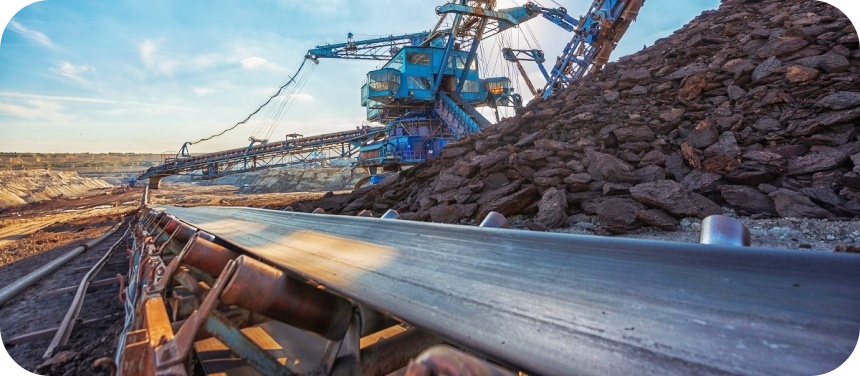
Belt Conveyor Design Guide: Advanced Design Techniques for Optimal Layout and Efficiency
This section of the Belt Conveyor Design Guide explores advanced design techniques that can significantly enhance the efficiency and functionality of conveyor systems. Utilizing resources like the design of belt conveyor pdf, this part provides insight into sophisticated layout planning and optimization strategies that go beyond basic conveyor setups.
Exploring Advanced Layout and Optimization Strategies
The “design of belt conveyor pdf” serves as a crucial resource in understanding how to implement advanced design techniques that optimize material flow and reduce operational costs. This document covers a range of topics from maximizing space utilization to enhancing the speed and reliability of conveyor operations. It includes detailed diagrams and specifications for complex configurations, helping designers create more efficient and effective systems.
Benefits of Innovative Conveyor Designs
One of the innovative designs covered in this section is the cleated belt conveyor design pdf, which provides guidelines on incorporating cleats into belt conveyors. Cleated belts are particularly beneficial for:
- Inclined Transport: Preventing slippage of materials when moving them vertically or at steep inclines.
- Material Segregation: Keeping different materials separate or ensuring precise positioning during transport, which is crucial for batching operations.
- Increased Capacity: Allowing conveyors to carry more material at higher incline angles without compromising speed or safety.
These innovative design elements, when correctly implemented, can greatly enhance the conveyor’s ability to handle diverse operational demands efficiently. By exploring these advanced techniques within the Belt Conveyor Design Guide designers and engineers are equipped with the knowledge to push the boundaries of traditional conveyor design, resulting in systems that are not only more capable but also more cost-effective and adaptable to future advancements in technology.
Belt Conveyor Design Guide: Calculations and Practical Applications for Enhanced Efficiency and Safety
In this vital section of the Belt Conveyor Design Guide, we take a deep dive into conveyor belt calculation techniques and their real-world applications. This part of the guide emphasizes the importance of precision in conveyor design and how calculations play a critical role in enhancing both efficiency and safety.
Deep Dive into Conveyor Belt Calculation Techniques
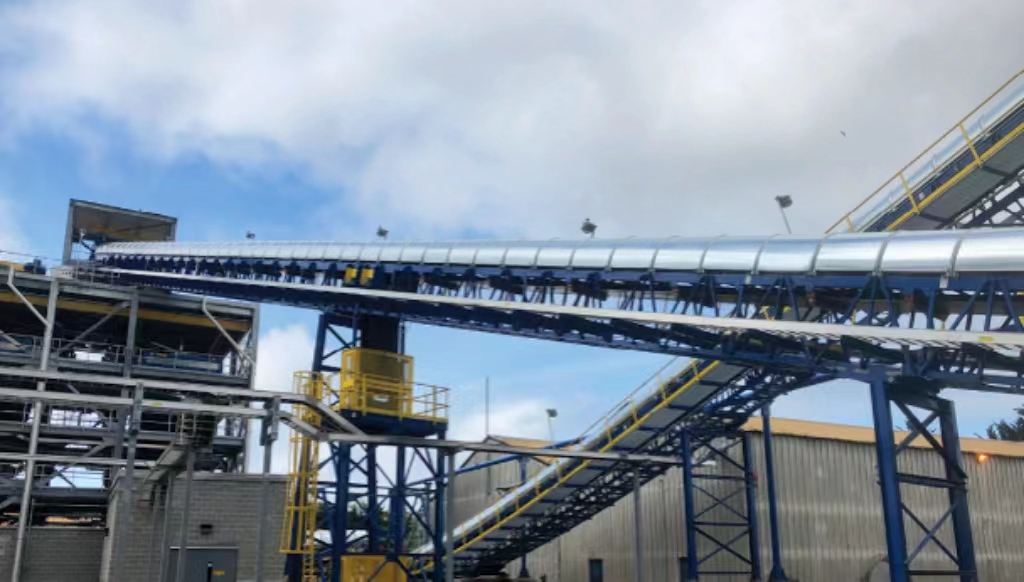
The focus here is on detailed conveyor belt calculation methods as outlined in various engineering resources. These calculations help determine everything from belt speed and load capacity to power requirements and tension management. Understanding these aspects is crucial for designing conveyors that are not only efficient but also robust and reliable under different operational conditions.
Practical Applications of Conveyor Belt Calculations
- Efficiency Impact: Precise calculations ensure that the conveyor system operates at optimal efficiency. For example, correctly calculating the motor power and belt tension can reduce energy consumption and increase the lifespan of the conveyor.
- Safety Enhancements: Accurate calculations are vital for safety. They help in designing systems that can handle the expected load without risk of overloading, which can lead to equipment failure and possible accidents. Calculations also assist in ensuring that all safety measures, like emergency stops and guardrails, are appropriately integrated.
Examples Demonstrating the Impact of Calculations
To illustrate, we discuss case studies where precise conveyor belt calculations have significantly improved operational efficiency and safety:
Case Study 1: Improving Efficiency at ABC Manufacturing
ABC Manufacturing, a leading producer of consumer electronics, faced issues with their conveyor belt system that resulted in frequent wear and tear and bottlenecks in production. The company aimed to enhance throughput and reduce maintenance costs.
Challenges:
- Frequent wear and tear on the belt.
- Bottlenecks in production leading to decreased efficiency.
- High maintenance costs and downtime.
Solution:
ABC Manufacturing implemented calculated changes to the conveyor belt speed. By using a comprehensive belt conveyor design guide, the engineering team adjusted the belt speed to an optimal level that reduced friction and wear on the belt. They also synchronized the conveyor speed with the production line to maintain a smooth flow of materials.
Outcome:
The changes led to a significant improvement in the system’s efficiency. Wear and tear on the belt were reduced, leading to lower maintenance costs and less downtime. Most notably, the throughput increased by 20%, allowing ABC Manufacturing to meet higher production demands and improve overall productivity.
Case Study 2: Enhancing Capacity at XYZ Mining
XYZ Mining, a prominent mining company, needed to upgrade their conveyor system to handle an increasing volume of extracted material. The existing system struggled with the higher loads, leading to frequent breakdowns and safety concerns.
Challenges:
- Handling higher volumes of heavy materials.
- Ensuring the safety of operations under increased loads.
- Reducing the frequency of system breakdowns.
Solution:
XYZ Mining’s engineering team conducted precise load calculations using the belt conveyor design guide. They designed a new conveyor belt system capable of handling the increased load without compromising safety. The system included reinforced belts and upgraded motors to manage the higher volumes of material.
Outcome:
The new conveyor system allowed XYZ Mining to increase their material handling capacity by 15%. The enhanced load management reduced the risk of breakdowns and ensured safer operations. This upgrade not only boosted productivity but also improved the overall safety of the mining operations.
Additional Considerations
In this section of our belt conveyor design guide, we explore crucial additional considerations that ensure the longevity, safety, and efficiency of conveyor systems. Proper maintenance, safety protocols, and adaptation to environmental and operational conditions are essential elements that must be addressed in the design phase.
Maintenance and Safety
Designing for Ease of Maintenance and Safety
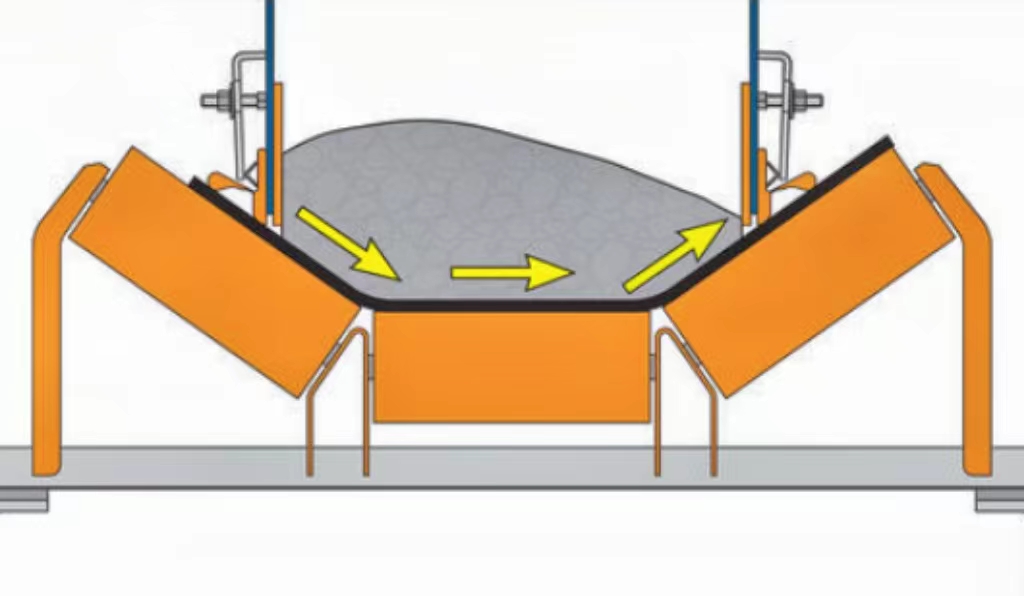
A well-designed belt conveyor system should prioritize ease of maintenance to minimize downtime and extend the equipment’s lifespan. Regular maintenance is vital for the smooth operation of conveyor systems, and designing with maintenance in mind can significantly enhance overall efficiency.
1. Accessibility:
Ensure that all critical components, such as motors, belts, pulleys, and rollers, are easily accessible. This accessibility allows for quick inspections, repairs, and replacements, reducing downtime and maintenance costs.
2. Modular Design:
Incorporating a modular design allows for individual sections of the conveyor to be removed and serviced without dismantling the entire system. This approach not only simplifies maintenance but also facilitates upgrades and expansions.
3. Standardization:
Use standardized components wherever possible. Standard parts are easier to source, replace, and maintain, ensuring that the system remains operational with minimal interruptions.
4. Automated Monitoring:
Integrate automated monitoring systems that provide real-time data on the conveyor’s performance. These systems can detect issues such as belt slippage, misalignment, and wear, enabling proactive maintenance before problems escalate.
5. Maintenance Schedule:
Develop and adhere to a regular maintenance schedule. Routine inspections, lubrication, and component checks can prevent minor issues from becoming major failures.
Importance of Incorporating Safety Features and Regular Inspections
Safety is a paramount concern in any belt conveyor design guide. A safe conveyor system protects workers from accidents and injuries, ensuring a secure working environment.
1. Emergency Stops:
Install emergency stop buttons at strategic locations along the conveyor system. These buttons should be easily accessible and clearly marked to allow for immediate shutdown in case of an emergency.
2. Guarding:
Implement guarding around all moving parts, such as belts, pulleys, and rollers, to prevent accidental contact. Guards should be designed to be easily removable for maintenance while ensuring adequate protection during operation.
3. Warning Systems:
Incorporate visual and auditory warning systems to alert workers of potential hazards. These systems can include warning lights, alarms, and signage to indicate when the conveyor is in operation or when maintenance is being performed.
4. Regular Inspections:
Conduct regular safety inspections to identify and rectify potential hazards. Inspections should include checking for worn components, loose guards, and ensuring that emergency stops and warning systems are functioning correctly.
5. Training:
Provide comprehensive training for all personnel who operate or maintain the conveyor system. Training should cover safe operating procedures, emergency response, and proper maintenance techniques.
Environmental and Operational Conditions
Adapting Design for Specific Environmental Conditions
Conveyor systems operate in diverse environments, each presenting unique challenges. Adapting the design to specific environmental conditions is crucial for the system’s reliability and durability.
1. Temperature:
Extreme temperatures can affect the performance and lifespan of conveyor components. For high-temperature environments, select heat-resistant belts and materials. In cold environments, choose components that remain flexible and operational at low temperatures.
2. Humidity and Moisture:
High humidity and moisture levels can lead to corrosion and belt slippage. Use corrosion-resistant materials, such as stainless steel, and incorporate drainage systems to manage moisture. For environments with frequent washdowns, like food processing, design conveyors with easy-to-clean surfaces and materials.
3. Chemical Exposure:
In environments where the conveyor is exposed to chemicals, select materials that are resistant to corrosion and chemical degradation. Ensure that all components, including belts and rollers, can withstand the specific chemicals they will encounter.
Considerations for Different Operational Settings
Different operational settings, such as indoor versus outdoor environments, require tailored design considerations to ensure optimal performance.
1. Indoor Settings:
Indoor conveyor systems typically face fewer environmental challenges but must still be designed for efficiency and safety. Consider factors such as space constraints, floor load capacity, and integration with existing equipment.
2. Outdoor Settings:
Outdoor conveyors must withstand weather conditions such as rain, snow, and wind. Use weatherproof components and protective covers to shield the system from the elements. Additionally, consider the impact of UV radiation on belts and other components.
3. Dust and Debris:
In dusty environments, such as mining or agriculture, design conveyors with dust control measures. This can include dust covers, extraction systems, and choosing components that minimize dust accumulation.
4. Noise Levels:
In settings where noise levels must be controlled, select low-noise components and incorporate sound-dampening measures. This is particularly important in indoor environments where noise can impact worker comfort and productivity.
By incorporating these additional considerations into the belt conveyor design guide, you can ensure that your conveyor system is not only efficient and reliable but also safe and adaptable to various environmental and operational conditions. This comprehensive approach to design will help you create a conveyor system that meets all your specific needs and stands the test of time.
Reach out today for custom conveyor belt solutions.
FAQs about Belt Conveyor Design Guide
Designing a belt conveyor involves several key steps to ensure the system is efficient, effective, and safe. Begin by understanding the application for which the conveyor is intended, including the type of materials it will move, their weight, and the necessary speed of transport. From here, decide on the layout of the conveyor system, including whether it will need to run straight, curve, incline, or decline.
Selecting the appropriate belt material is critical; factors include the belt’s durability, resistance to elements, and suitability for the materials it will carry. Choose a motor and drive system that can adequately power the belt under full load without excessive strain. Components like pulleys, idlers, and rollers must be chosen based on their ability to support and guide the belt effectively.
Finally, design the conveyor with safety and maintenance in mind. This includes installing safety guards, emergency stop systems, and easy access for maintenance. The design process should always adhere to industry standards and any applicable regulations to ensure operational safety and reliability.
The criteria for conveyor design revolve around several key factors that ensure the conveyor performs efficiently, safely, and sustainably. These include:
Load Capacity – The conveyor must be able to handle the maximum expected load without failure.
Throughput – The design must meet or exceed the required rate of material transfer.
Operation Efficiency – Includes considerations for power use and mechanical efficiency.
Material Characteristics – The conveyor design must accommodate the specific properties of the material, such as abrasiveness, corrosiveness, size, and overall weight.
Environmental Factors – Conditions such as temperature, humidity, and exposure to chemicals or UV light affect material choice and design specifics.
Safety Requirements – Includes guards, safety switches, and other features to protect operators and maintenance personnel.
Ease of Maintenance – Accessibility for repairs and routine maintenance should be considered to minimize downtime.
Cost-Effectiveness – The design should be economically feasible, balancing upfront costs with long-term operational and maintenance expenses.
To calculate the capacity of a belt conveyor, you need to determine the belt’s speed, width, and the density of the material being conveyed. The basic formula for calculating the conveyor capacity is:
[ \text{Capacity (tons per hour)} = \text{Belt Speed (feet per minute)} \times \text{Belt Width (inches)} \times \text{Material Density (pounds per cubic foot)} \times \text{Conversion Factor} ]
The conversion factor adjusts for the dimensions in the formula, typically 15 for a common setup. The belt speed and width should be determined based on the material flow requirements and the physical constraints of the processing facility. Material density is specific to the goods being moved.
To calculate the roll length of a conveyor belt, you need to know the diameter of the belt’s core, the belt thickness, and the diameter of the rolled belt. The formula to determine the roll length is:
[ \text{Roll Length} = \frac{N(D^2 – d^2)}{4T} ]
Where:
(N) is the number of turns or revolutions the belt makes around the core.
(D) is the outer diameter of the roll.
(d) is the diameter of the core.
(T) is the thickness of the belt.
The result will give you the total length of the belt rolled up. This calculation is crucial for ensuring that you have enough belt material for the system without excess, which can help in cost planning and logistics.
Designing a conveyor belt involves considering several key factors to ensure efficiency, reliability, and longevity. Here are the primary considerations:
Material Type: The type of material being transported greatly influences the design. Factors such as weight, size, abrasiveness, and temperature resistance of the material need to be taken into account. For example, heavy or abrasive materials require more durable belts and stronger motors.
Conveyor Length and Incline: The length and incline of the conveyor affect the motor power and belt tension. Longer conveyors require more powerful motors, and inclined conveyors need additional design considerations to prevent material rollback.
Load Capacity: The maximum load capacity is critical to avoid overloading the conveyor, which can lead to system failures or reduced lifespan. It’s important to calculate the peak load the conveyor will handle and design accordingly.
Belt Speed: The speed at which the conveyor belt operates must match the production requirements. Higher speeds can increase productivity but also require more precise control and maintenance.
Environmental Conditions: The operating environment impacts the choice of materials and components. Factors such as humidity, temperature extremes, chemical exposure, and dust levels must be considered to select suitable materials and prevent premature wear.
Belt Material: Choosing the right belt material is essential for durability and performance. Options include rubber, PVC, polyurethane, and metal, each suited to different applications and environments.
Drive and Idler Pulley Design: Proper design of the drive and idler pulleys ensures efficient power transmission and reduces belt slippage. The diameter and material of these pulleys should be matched to the belt type and application.
Support Structure: The support structure must be robust enough to handle the weight of the belt and the materials being transported. It should also allow for easy maintenance and adjustments.
Safety Features: Incorporating safety features such as emergency stops, guards, and warning systems is crucial to protect workers and prevent accidents.
Maintenance Access: Designing for easy maintenance can reduce downtime and increase the lifespan of the conveyor. Consider features like modular components, easy-to-access parts, and user-friendly maintenance procedures.
By carefully considering these factors, you can design a conveyor belt system that is efficient, reliable, and well-suited to your specific needs.
Last Updated on June 21, 2024 by Jordan Smith
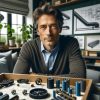
Jordan Smith, a seasoned professional with over 20 years of experience in the conveyor system industry. Jordan’s expertise lies in providing comprehensive solutions for conveyor rollers, belts, and accessories, catering to a wide range of industrial needs. From initial design and configuration to installation and meticulous troubleshooting, Jordan is adept at handling all aspects of conveyor system management. Whether you’re looking to upgrade your production line with efficient conveyor belts, require custom conveyor rollers for specific operations, or need expert advice on selecting the right conveyor accessories for your facility, Jordan is your reliable consultant. For any inquiries or assistance with conveyor system optimization, Jordan is available to share his wealth of knowledge and experience. Feel free to reach out at any time for professional guidance on all matters related to conveyor rollers, belts, and accessories.