Enhancing Accuracy with Conveyor Belt Tracking Roller
Conveyor belt tracking is a pivotal process in ensuring the efficient operation of a conveyor system. The essence of conveyor belt tracking involves aligning and steering the belt to run smoothly along the conveyor’s framework. This prevents the belt from drifting sideways, which can lead to uneven wear, potential damage to the belt, and even system downtime. Utilizing a conveyor belt tracking roller is one of the effective methods to maintain this crucial alignment. The conveyor belt tracking roller adjusts the belt’s position to ensure it stays centered throughout its journey. Emphasizing the alignment of these rollers is essential for minimizing operational disruptions and maintaining high productivity levels in various industries.
What is Conveyor Belt Tracking Roller?
Conveyor belt tracking is the process of ensuring that a conveyor belt aligns correctly and runs straight on the pulleys and the conveyor frame. Maintaining proper conveyor belt tracking theory is essential to increase the lifespan of the belt and minimize wear and tear on the equipment.
Common Issues in Conveyor Belt Tracking
When conveyor belts do not track properly, several issues can arise that affect the efficiency and safety of a conveyor system. Here are eight common issues:
- Belt Slippage: When conveyor belts lose grip and slip off their rollers, it often indicates poor tracking. This slippage can lead to decreased productivity and increased wear on the belt.
- Edge Damage: Improperly tracked belts can rub against the conveyor frame, leading to fraying or cutting of the belt edges.
- Material Spillage: A belt that doesn’t track correctly tends to spill material being conveyed, which can create safety hazards and require additional cleanup.
- Belt Misalignment: This occurs when the belt is not centered on the pulleys and can lead to uneven belt wear and potential breakdowns.
- Increased Energy Consumption: Poor tracking forces the motors to work harder to move the misaligned belt, which consumes more energy.
- Premature Wear of Components: Components such as rollers and bearings may wear unevenly due to improper belt tracking, leading to frequent replacements and downtime.
- Operational Delays: Frequent maintenance and adjustments to re-track the belt can lead to significant operational delays and reduced throughput.
- Unsafe Working Conditions: A misaligned belt can create unsafe conditions for workers near the conveyor, especially when manual intervention is required to adjust or maintain the tracking.
Importance of Conveyor Belt Tracking Rollers
Conveyor belt tracking rollers play a crucial role in maintaining the alignment of the belt. These specialized rollers are designed to ensure that the conveyor belt stays centered throughout its course. Properly adjusted and maintained conveyor belt tracking rollers can significantly reduce the occurrence of the issues listed above and enhance the overall efficiency and safety of the conveyor system. By investing in quality conveyor belt tracking rollers and regular maintenance, companies can achieve smoother operations and lower the total cost of ownership of their conveyor systems.
Types of Conveyor Belt Tracking Roller Systems
Ensuring accurate alignment of a conveyor belt is crucial for the longevity and efficiency of conveyor systems. Various types of conveyor belt tracking systems, including both manual and automatic options, have been developed to maintain consistent belt alignment under different operational conditions. These systems use different methods and technologies to correct misalignment and keep the conveyor belt running smoothly.
Manual Conveyor Belt Tracking
Manual tracking systems rely on the physical adjustment of rollers and the conveyor framework to correct misalignment. This method requires periodic checks and adjustments by maintenance personnel to ensure the belt remains centered. It is a cost-effective solution but can be labor-intensive and less precise compared to automated systems.
Automatic Conveyor Belt Tracking Systems
Automatic systems use conveyor belt tracking sensors and feedback mechanisms to continuously adjust the belt’s position. These systems detect deviations from the centerline and automatically re-align the belt, minimizing the need for manual intervention and improving operational consistency.
Crowned Roller Systems
Crowned rollers are designed with a slight diameter increase towards the center compared to the ends. This design naturally guides the conveyor belt towards the center as it moves. The effectiveness of crowned rollers depends on the proper selection of roller dimensions and material, as well as the belt type and operating conditions.
Functionality of Crowned Rollers
The principle behind crowned rollers is that the belt will tend to move towards the highest diameter part of the roller. As the belt attempts to climb up the slight slope of the crowned roller, gravity and tension bring it back towards the center. This self-aligning feature makes crowned rollers a popular choice in many conveyor applications.
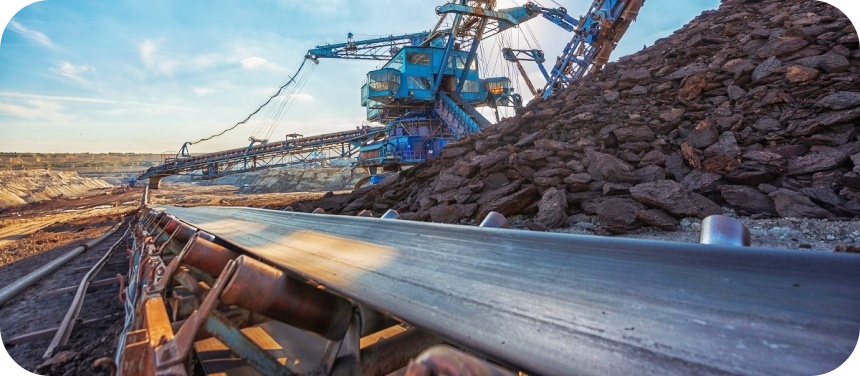
Suitability and Limitations
While crowned rollers are effective for many applications, they have limitations, especially when handling very wide belts or belts carrying heavy loads. In such cases, the forces exerted by the belt might overcome the self-aligning properties of the rollers, leading to potential misalignment. Additionally, these systems may not be suitable for very thin or delicate belts that could be damaged by the constant shifting on the roller surface.
V-Guided Belt Systems
V-guided belt systems incorporate a continuous v-shaped guide attached to the underside of the conveyor belt that runs through a similarly shaped groove in the rollers. This design ensures that the belt is always aligned with the rollers, providing a very reliable tracking solution.
Mechanism of V-Guided Systems
The V-guide increases the stability of the belt’s path by fitting snugly into the corresponding groove in the roller. This interlocking mechanism prevents lateral movements of the belt, ensuring it remains perfectly centered, irrespective of load distribution or operational speeds.
Benefits of Using V-Guided Systems
V-guided systems are particularly beneficial in applications where precise belt tracking is critical, such as in packaging or assembly operations where misalignment could cause product mishandling or damage. These systems are also advantageous in environments where debris might accumulate on the rollers, as the v-guide can help keep the belt clear of obstructions.
Each type of conveyor belt tracking system, including the use of a conveyor belt tracking roller, offers unique benefits and is suited to specific operational needs. The choice between manual adjustments, crowned rollers, V-guided systems, or advanced automatic tracking should be based on the specific requirements of the conveyor application, taking into account factors such as belt size, load conditions, and environmental factors.
Common Conveyor Belt Tracking Roller Problems and Solutions
Proper conveyor belt tracking is crucial for the smooth operation of a conveyor system. Misalignments and other tracking issues can lead to decreased efficiency, increased maintenance costs, and safety hazards. Understanding common problems and knowing how to address them effectively is key to maintaining a reliable conveyor belt system.
Typical Conveyor Belt Tracking Problems
- Belt Tracks to One Side: One of the most frequent issues is the belt consistently tracking towards one side of the conveyor at certain points along the path. This can be caused by a number of factors including improper installation, worn or improperly adjusted tracking rollers, or accumulation of debris.
- Belt Misalignment: This issue involves the belt not being square with the frame of the conveyor, which can result from uneven loading, worn parts, or thermal expansion.
- Over-tensioning: Excessive tension on the conveyor belt can lead to various problems including belt stretch, component wear, and motor overload.
- Under-tensioning: Insufficient tension can cause the belt to slip on the drive rollers, leading to poor tracking and inefficiency.
- Worn Out Rollers: Worn or seized rollers can create uneven pulling on the belt, causing it to track poorly.
- Material Build-Up: Accumulation of material on rollers or pulleys can offset the balance of the belt, leading to misalignment.
- Improperly Installed Load Stations: If load stations are not correctly aligned with the conveyor frame, it can force the belt off track.
- Structural Issues: Any deformities in the frame of the conveyor can lead to chronic tracking problems.
Step-by-Step Guide to Adjusting Conveyor Belt Tracking
Adjusting the tracking of a conveyor belt involves several steps that require careful attention to detail. Here is an 8-step guide to help ensure your conveyor belt tracks straight:
- Inspect the Conveyor: Examine the entire length of the conveyor structure for signs of damage or wear that could affect tracking.
- Check for Material Build-Up: Clean any debris or material build-up from the rollers and pulleys to ensure they rotate freely.
- Verify Roller Alignment: Ensure all rollers are properly aligned and parallel to each other and the belt. Misaligned rollers are a common cause of tracking issues.
- Adjust the Tension: Conveyor belts need the correct tension to function properly. Check the manufacturer’s specifications and adjust as needed.
- Realign the Belt: Use conveyor belt tracking rollers to gently guide the belt back to the center. These rollers can be adjusted to apply slight pressure to steer the belt into the correct position.
- Test the Adjustments: Run the belt at a low speed to observe the effect of your adjustments. Watch for the belt returning to the center and running smoothly over the rollers.
- Make Incremental Changes: If the belt still tracks to one side, make small incremental adjustments to the conveyor belt tracking rollers, testing after each adjustment.
- Regular Maintenance: Establish a routine maintenance schedule to regularly check belt tension, alignment, and general condition to prevent future tracking issues.
By following these steps and using conveyor belt tracking rollers effectively, you can maintain optimal performance and extend the life of your conveyor system. Regular maintenance and timely adjustments are crucial to avoiding downtime and ensuring safe operation.
Conveyor Belt Tracking Roller: Advanced Belt Tracking Technologies
The advancement of technology has significantly enhanced the capabilities of conveyor belt tracking systems. Modern setups are increasingly incorporating sophisticated engineering and technology to ensure that conveyor belts operate with maximum efficiency and minimal downtime. These advancements not only enhance productivity but also reduce the manual labor involved in maintaining optimal conveyor belt alignment.
Automatic Conveyor Belt Tracking Systems
Automatic conveyor belt tracking systems represent a major leap in conveyor technology. These systems use sensors, actuators, and control algorithms to monitor and adjust the belt’s position in real time. By continuously detecting the belt’s alignment, these systems can immediately correct any deviations, thus preventing the belt from drifting off course. This proactive approach to belt tracking reduces wear and tear on the belt and other conveyor components, extending the lifespan of the entire system.
Integration of Advanced Sensors
The core of an automatic conveyor belt tracking roller system lies in its use of advanced sensors. These can include infrared, ultrasonic, and optical sensors that detect the edge of the belt and its position relative to the conveyor frame. The data from these sensors is processed by a central control unit that adjusts the rollers automatically to maintain the belt’s correct path.
Use of Precision Actuators
Alongside sensors, precision actuators play a crucial role. These devices make the fine adjustments needed to the rollers, ensuring that the belt remains centered. The actuators can be based on various technologies, including hydraulic, pneumatic, or electric systems, each chosen based on the specific requirements and scale of the conveyor system.
Enhanced Efficiency through Technology Integration
Integrating these technologies into conveyor belt tracking roller systems has led to significant improvements in efficiency. Conveyors can now operate at higher speeds and with greater loads without the risk of misalignment. Moreover, the ability to maintain precise control over the belt’s position reduces the frequency and severity of maintenance shutdowns.
Smart Conveyor Systems
The next frontier in conveyor belt tracking technology is the development of smart conveyor systems that integrate IoT (Internet of Things) capabilities. These systems can predict potential issues before they occur, schedule preventive maintenance, and even adapt to changing operational conditions automatically. By gathering and analyzing data over time, smart conveyors can optimize their own performance and reduce operational costs.
Advanced belt tracking technologies, particularly those involving automatic conveyor belt tracking roller systems, represent a significant investment in the future of industrial operations. These technologies not only improve the immediate functionality of conveyor systems but also contribute to long-term sustainability and efficiency. As these technologies continue to evolve, they will play a crucial role in the automation and optimization of industrial processes worldwide.
Preventive Maintenance and Troubleshooting for Conveyor Belt Tracking Roller
Ensuring the longevity and efficiency of a conveyor system involves regular preventive maintenance, particularly focusing on conveyor belt tracking rollers and related components. Implementing a consistent maintenance routine can significantly reduce the occurrence of belt tracking issues and the need for troubleshooting.
Preventive Maintenance Tips
Here are 12 tips on regular maintenance practices to prevent belt tracking issues:
- Regular Inspections: Conduct thorough inspections of the conveyor system at regular intervals to check for signs of wear or damage.
- Cleanliness: Keep the conveyor belt and all related components, including rollers and pulleys, free of debris and material build-up that can affect tracking.
- Lubrication: Regularly lubricate all moving parts, but ensure no excess lubricant is present which could collect debris.
- Check Belt Tension: Routinely check and adjust the belt tension to the manufacturer’s recommended levels to prevent slippage and misalignment.
- Align Conveyor Belt Tracking Rollers: Ensure that the conveyor belt tracking rollers are well-aligned and functioning correctly. Adjust them if necessary to maintain proper belt tracking.
- Replace Worn Parts: Promptly replace worn or damaged rollers, bearings, and other parts to prevent misalignment and tracking issues.
- Monitor Load Distribution: Ensure that the load is evenly distributed across the width of the belt during operation to avoid uneven force on the belt and rollers.
- Check Belt Edges: Regularly inspect the edges of the belt for signs of fraying or damage, as these can indicate tracking issues.
- Record and Analyze: Keep records of maintenance and adjustments to help diagnose recurring problems and improve maintenance practices.
- Train Personnel: Train operational personnel on the proper handling and troubleshooting of the conveyor belt and its components.
- Adjust Skirting: Ensure that skirting is adjusted properly to minimize spillage that can cause belt misalignment.
- Review and Update Maintenance Procedures: Regularly review and update maintenance procedures based on manufacturer updates and operational experience.
Troubleshooting Guide for Common Problems
When problems occur, having a structured approach to troubleshooting can quickly identify and correct issues with minimal impact on operation. Here’s a basic guide:
Belt Drifts to One Side
- Check for debris or material build-up on rollers and pulleys.
- Inspect and adjust the alignment of conveyor belt tracking rollers.
- Ensure that the load is centered as it is placed on the conveyor.
Belt Slippage
- Verify that the belt tension is adequate.
- Check the condition of the drive pulleys for wear or buildup.
- Adjust the drive pulleys and tension if necessary.
Excessive Wear on Belt Edges
- Look for misaligned rollers or pulleys.
- Adjust side guides or conveyor belt tracking rollers to realign the belt.
- Replace any damaged or worn-out rollers.
Increased Noise or Vibration
- Inspect bearings and rollers for wear and lubricate as needed.
- Check for loose components and tighten as required.
- Ensure that the belt and pulleys are clean and free of foreign materials.
Adhering to these preventive maintenance tips and troubleshooting steps can help maintain the performance of conveyor belt systems and reduce the need for costly repairs and downtime. Regular attention to the conveyor belt tracking rollers is particularly crucial in maintaining the overall health of the conveyor system.
Fill out the form below to get in touch with our sales team for Conveyor belt tracking quotes.
FAQs about Conveyor Belt Tracking Roller
To track a conveyor belt, various types of rollers can be used, including the idler rollers and tracking rollers. The most specific are the tracking rollers or guide rollers, which are specially designed to influence the belt’s position on the conveyor. These rollers can be adjusted to tilt slightly in one direction or another, guiding the belt back to the center if it begins to drift. Additionally, some systems use crowned rollers that have a larger diameter in the center than at the ends, creating a natural guiding mechanism as the belt automatically seeks the highest part of the roller. The choice of roller for tracking a conveyor belt depends on the conveyor type, belt width, and the specific handling requirements of the materials being transported.
Tracking a belt on a roller involves adjusting the rollers themselves or the conveyor frame to guide the belt back to its intended path. The basic steps include:
Ensuring that all rollers and the conveyor frame are aligned and level.
Running the belt at low speed to observe the direction of drift.
Adjusting the rollers at the ends of the conveyor—if the belt drifts to one side, the roller on that side is tilted in the direction opposite to the drift, and vice versa.
Making small incremental adjustments and checking the belt’s response after each adjustment.
Continuously monitoring and adjusting until the belt remains centered during operation. This process requires careful attention to detail and patience, as overcorrection can lead to the belt drifting in the opposite direction.
Conveyor belt tracking is the process of maintaining the belt aligned on its correct path during operation to prevent it from drifting or slipping off the rollers. Proper belt tracking ensures that the conveyor system runs smoothly and efficiently, minimizing wear and tear on the belt and extending its lifespan. This process is crucial for avoiding operational disruptions caused by misalignments and can involve various techniques and equipment, depending on the specific system design. Effective tracking helps prevent damage to the belt edges, reduces spillage of materials being transported, and can significantly decrease downtime required for maintenance and repairs.
Conveyor belt rollers, also known as idler rollers, are cylindrical rods that support and move the conveyor belt. They are an essential part of a conveyor system and are designed to support the belt’s weight and the load being transported. The rollers are spaced along the length of the conveyor and can vary in size, material, and design based on the application’s needs. The main types of conveyor belt rollers include drive rollers, which power the belt movement, idler rollers that support the belt along its path, and return rollers that guide the belt on its return trip. Rollers are typically made from metal, plastic, or rubber and must be durable enough to withstand continuous operation under various environmental conditions.
Last Updated on July 31, 2024 by Jordan Smith
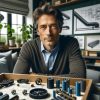
Jordan Smith, a seasoned professional with over 20 years of experience in the conveyor system industry. Jordan’s expertise lies in providing comprehensive solutions for conveyor rollers, belts, and accessories, catering to a wide range of industrial needs. From initial design and configuration to installation and meticulous troubleshooting, Jordan is adept at handling all aspects of conveyor system management. Whether you’re looking to upgrade your production line with efficient conveyor belts, require custom conveyor rollers for specific operations, or need expert advice on selecting the right conveyor accessories for your facility, Jordan is your reliable consultant. For any inquiries or assistance with conveyor system optimization, Jordan is available to share his wealth of knowledge and experience. Feel free to reach out at any time for professional guidance on all matters related to conveyor rollers, belts, and accessories.