Conveyor Belt Drum Roller Suits Your System
Conveyor systems are integral to modern material handling, with conveyor belt drum rollers playing a pivotal role in their operation. These rollers are crucial for supporting and moving belts that carry diverse materials across various industries. In the market, you will find an array of conveyor belt drum rollers designed to meet different environmental and operational demands. From lightweight options suitable for small goods to heavy-duty rollers capable of handling large volumes and weights, the variety ensures that every system can achieve optimum efficiency and functionality. This section explores the essential types and functions of conveyor belt drum rollers, highlighting their importance in enhancing conveyor system performance.
What are Conveyor Belt Drum Rollers
Conveyor belt drum rollers are crucial components in the operation of conveyor systems, Large diameter, thick-walled conveyor belt drum rollers serve idler drums, featuring fixed shafts, and machined surfaces for belt protection.facilitating the smooth and efficient movement of materials. These rollers help support and drive the conveyor belt, reducing friction and wear. Let’s delve deeper into their functions and distinctions.
Definition and Primary Functions
A conveyor belt drum roller is a cylindrical component that drives or supports the conveyor belt. These rollers are typically positioned at the ends of the conveyor system, where they provide the necessary tension and traction for the belt’s operation. Here are the nine primary functions of conveyor belt drum rollers:
- Driving the Conveyor Belt: Drum rollers are often motorized to provide the necessary rotational force to move the conveyor belt.
- Supporting the Belt: These rollers help maintain the structural integrity of the belt, ensuring it remains flat and aligned.
- Reducing Belt Slippage: By providing adequate friction, drum rollers help prevent the belt from slipping on the track.
- Adjusting Tension: Conveyor belt drum rollers can be adjusted to increase or decrease the tension on the belt, crucial for efficient operation.
- Guiding the Belt: Properly aligned rollers help guide the conveyor belt, preventing it from drifting sideways.
- Distributing Load Evenly: Rollers ensure that the material load is evenly distributed across the width of the belt.
- Absorbing Shocks: During material loading, drum rollers absorb impacts, protecting the belt and the conveyor framework.
- Facilitating Accumulation: In conveyor belt systems designed for accumulation, drum rollers can be modified to allow the belt to stop and start without affecting the movement of materials.
- Enhancing Longevity: By minimizing wear and tear, well-maintained drum rollers extend the lifespan of the entire conveyor system.

Distinctions Between Crowned and Parallel Drum Rollers
There are primarily two types of drum rollers used in conveyor belts: crowned drum rollers and parallel drum rollers. Each type serves a unique purpose and is suitable for different operational needs.
Crowned Drum Rollers
Crowned drum rollers have a slightly higher diameter in the middle than at the ends. This unique design helps to keep the conveyor belt centered and prevents it from drifting off to the sides. The subtle curvature of the roller’s surface creates varying travel speeds for the belt edges, guiding it back to the center if it begins to move sideways.
Parallel Drum Rollers
In contrast, parallel drum rollers have a uniform diameter across their entire length. This design is suitable for applications where the conveyor belt alignment is controlled externally or where lateral movement is not a concern. Parallel drum rollers provide consistent support across the belt’s width, ensuring stable and uniform motion.
Comparison Table
To further distinguish between these two types of conveyor belt drum rollers, the following table provides a clear comparison of their characteristics:
Understanding the differences between these types of conveyor belt drum rollers is crucial for selecting the right roller for specific conveyor belt applications. By choosing the appropriate type, you can enhance the efficiency and longevity of your conveyor system.
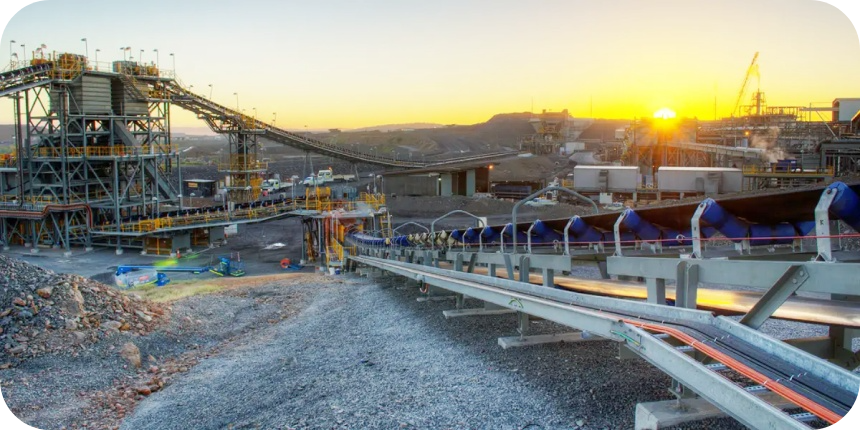
Features of Conveyor Belt Drum Rollers
Engineering and Design Enhancements
The engineering behind conveyor belt drum rollers involves precise design considerations to enhance their functionality and durability. One key feature is the availability of machined shaft ends, which provide robust connections and minimize wear and tear. Additionally, manufacturers offer customizations in tube diameters, adapting to specific conveyor needs. Whether it’s adjusting the diameter for a small-scale operation or increasing it for heavy-duty applications, these modifications ensure that the rollers can handle the required loads efficiently.
Bearing Types and Advantages
In the realm of conveyor belt drum rollers, the choice of bearings plays a significant role in the system’s overall performance. Many rollers feature sealed cartridge bearings, which are preferred for their ability to protect against dust, dirt, and other contaminants. This type of bearing is crucial for maintaining the longevity and efficiency of the roller, reducing maintenance needs and downtime. Sealed bearings are particularly beneficial in environments where fine particles and debris are prevalent, ensuring that the conveyor system remains operational under varying conditions.
The features and specifications of conveyor belt drum rollers are designed to meet diverse industrial needs, enhancing the reliability and efficiency of conveyor systems worldwide. Each component, from the tube dimensions to the types of bearings used, is selected with precision to ensure that every conveyor belt drum roller offers the best possible performance in its specific application.
Specifications of Conveyor Belt Drum Rollers
Detailed Specifications
Conveyor belt drum rollers are designed to support the seamless operation of conveyor belts, and their specifications are crucial for optimal performance. These rollers come in various tube sizes and spindle options to accommodate different operational needs. For instance, standard tube dimensions include diameters such as 114.3mm with a thickness of 6.3mm, 168.33mm with a thickness of 8mm, and 219.1mm with a thickness of 8.8mm. Available spindle options can range from ø25mm to ø40mm, allowing for a tailored approach to different weight capacities and operational speeds.
When specifying conveyor belt drum rollers, it’s essential to consider various parameters to ensure they meet operational requirements. Below are typical specifications and considerations for conveyor belt drum rollers:
Drum Shell
- Material: Common materials include mild steel, stainless steel, and aluminum. The choice depends on the environment and load conditions.
- Diameter: Usually ranges from 200 mm to 1200 mm or more, depending on the application.
- Length: Matches the width of the conveyor belt, typically ranging from 300 mm to 2400 mm or more.
- Surface Finish: Options include smooth, knurled, or coated with rubber lagging for increased grip.
End Discs
- Material: Typically the same as the drum shell, usually steel.
- Thickness: Varies based on drum diameter and load conditions, commonly between 10 mm to 30 mm.
Shaft
- Material: High-strength alloy steel is common to handle high loads and reduce deflection.
- Diameter: Usually ranges from 40 mm to 200 mm, depending on the load.
- Length: Extends beyond the drum to accommodate bearing housings and coupling mechanisms.
Bearings
- Type: Ball bearings or roller bearings are commonly used.
- Load Capacity: Must match the expected load of the conveyor system. Bearings are rated by dynamic and static load capacities.
Lagging
- Material: Rubber, ceramic, or a combination, depending on the required friction and wear resistance.
- Thickness: Typically ranges from 6 mm to 25 mm.
- Pattern: Options include plain, diamond, or herringbone patterns to enhance traction and belt tracking.
Mounting and Alignment
- Mounting: Flanged, foot-mounted, or shaft-mounted designs.
- Alignment: Precision-machined for proper alignment to prevent belt slippage and uneven wear.
Environmental Considerations
- Temperature Range: Materials and designs that can withstand the operational temperature range, often from -20°C to +70°C or higher for special applications.
- Corrosion Resistance: Stainless steel or coated materials for corrosive environments.
Example Specifications
GRAM Steel Conveyor Rollers
- Diameter: 300 mm to 1200 mm
- Length: Up to 2400 mm
- Material: Steel with optional rubber lagging
- Bearings: High-capacity ball or roller bearings
- Surface: Smooth or patterned rubber lagging
GRAM Ceramic Conveyor Rollers
- Diameter: 250 mm to 1000 mm
- Length: Matches conveyor width, up to 2200 mm
- Material: Mild steel or stainless steel with optional ceramic lagging
- Bearings: Sealed for life, suitable for high-load applications
- Coating: Various options including diamond, herringbone patterns
GRAM Heavy-duty Conveyor Rollers
- Diameter: 320 mm to 800 mm
- Length: Up to 2000 mm
- Material: High-strength steel
- Bearings: Heavy-duty roller bearings
- Lagging: Rubber or ceramic, up to 20 mm thick
These specifications provide a comprehensive overview of the considerations and parameters involved in selecting and designing conveyor belt drum rollers for mining and industrial applications.

Design of Conveyor Belt Drum Roller
The design of a conveyor belt drum roller involves several key components and considerations to ensure efficient and reliable operation. Here’s an overview of the design process:
Key Components of a Conveyor Belt Drum Roller
Drum Shell:
- Material: Typically made from steel or aluminum for strength and durability.
- Diameter: Determined based on the belt width and the load requirements.
- Surface Finish: Can be smooth or coated with rubber to increase traction and reduce belt slippage.
End Discs:
- Material: Usually steel, welded to the drum shell.
- Function: Provide structural support and house the bearing assemblies.
Shaft:
- Material: High-strength steel to support the load and reduce deflection.
- Design: Precision-machined to fit into the bearing assemblies and to accommodate the coupling for motorized rollers.
Bearings:
- Type: Typically anti-friction bearings (ball or roller bearings).
- Mounting: Can be mounted internally or externally on the end discs.
Lagging:
- Material: Rubber or ceramic coating on the drum surface.
- Purpose: Increases friction between the drum and the conveyor belt, improving traction and reducing slippage.
Design Considerations
Load Requirements:
- Static and Dynamic Loads: Ensure the drum can handle both the weight of the conveyor belt and the materials being transported.
Belt Speed:
- Operational Speed: The drum design must accommodate the operational speed of the conveyor belt, considering factors like centrifugal force.
Environmental Conditions:
- Temperature and Moisture: Materials and coatings must be chosen to withstand the operational environment, including temperature extremes and exposure to moisture or chemicals.
Alignment and Balance:
- Precision Manufacturing: Ensures the drum is properly balanced to avoid vibration and uneven wear on the belt.
Maintenance and Accessibility:
- Ease of Maintenance: Design should allow easy access for maintenance and replacement of bearings and other components.
Design Process
Requirement Analysis:
- Gather data on the operational requirements, including load, speed, and environmental conditions.
Material Selection:
- Choose appropriate materials for the drum shell, shaft, and bearings based on the operational requirements.
CAD Modelling:
- Create a detailed 3D model of the drum roller, including all components and their interactions.
Finite Element Analysis (FEA):
- Conduct stress analysis to ensure the design can withstand operational loads without failure.
Prototyping and Testing:
- Build a prototype and conduct real-world testing to validate the design and make any necessary adjustments.
Production:
- Once validated, proceed with the production of the drum rollers, ensuring quality control at each step.
Example Sources
- Fenner Dunlop: A leading manufacturer providing detailed specifications and design considerations for conveyor drum rollers.
- ContiTech: Offers insights into material selection and design optimization for conveyor components.
- CEMA (Conveyor Equipment Manufacturers Association): Provides standards and best practices for conveyor design, including drum rollers.
By considering these components and design principles, you can ensure the efficient and reliable operation of conveyor belt drum rollers in mining and other industrial applications.
Benefits of High-Quality Conveyor Belt Drum Roller
High-quality conveyor belt drum rollers significantly enhance the efficiency and safety of conveyor systems. Their design and construction are pivotal in ensuring that conveyor systems operate smoothly under various industrial conditions. Here, we explore the impacts of these components and how specific features like crowned or parallel outer diameters contribute to system performance.
Impact on Efficiency and Safety
Investing in high-quality conveyor belt drum rollers can lead to numerous benefits that impact both the efficiency and safety of conveyor systems. Below are eight key impacts:
- Reduced Downtime: High-quality drum rollers are less prone to failures, thus reducing downtime needed for maintenance and repairs.
- Increased Efficiency: Better quality rollers provide smoother operations, minimizing the energy consumed by the conveyor system and enhancing throughput.
- Longer Lifespan: These rollers are typically made from more durable materials, which withstand wear and tear better, extending the lifespan of both the rollers and the conveyor belt.
- Enhanced Safety: Quality drum rollers are designed to adhere strictly to safety standards, reducing the risk of accidents due to mechanical failures.
- Lower Maintenance Costs: With fewer breakdowns and less wear, the maintenance costs over the life of the conveyor system are significantly reduced.
- Improved Load Handling: High-quality rollers ensure consistent and stable movement, which is crucial for transporting sensitive or heavy loads without causing damage.
- Noise Reduction: Better designed and constructed rollers operate more quietly, which is essential for maintaining a more comfortable working environment.
- Decreased Belt Misalignment: Precision-engineered drum rollers maintain better belt alignment, thereby preventing costly belt damage and material spillage.
Features Aiding in Belt Tracking and Stability
The choice between crowned and parallel drum rollers plays a significant role in belt tracking and the overall stability of a conveyor system:
Crowned Drum Rollers:
- Self-Aligning Capability: The unique design of crowned rollers, featuring a higher center diameter, naturally guides the conveyor belt towards the center, ensuring better tracking and reducing the risk of belt slippage off the roller.
- Optimal for Varying Loads: This type is particularly beneficial in applications where the load on the conveyor varies, as the crown helps maintain belt alignment under changing conditions.
Parallel Drum Rollers:
- Uniform Surface Contact: Parallel rollers provide a consistent contact surface along the belt’s width, which is critical for handling heavy, uniform loads.
- Stable Operation: The uniform diameter across these rollers ensures that the belt does not wobble or sway, which is vital for maintaining stability and preventing material spillage.
The integration of these features into a conveyor belt drum roller design ensures optimal performance and longevity of the conveyor system. Whether your operation requires the flexibility of crowned rollers or the stability of parallel rollers, selecting high-quality components is key to enhancing productivity and safety in industrial settings.

Purchasing Conveyor Belt Drum Rollers
When it comes to optimizing the performance of conveyor systems, selecting the right conveyor belt drum rollers is crucial. The choice of drum rollers affects everything from the system’s efficiency and maintenance requirements to its longevity and safety. Below are essential tips and factors to consider when purchasing conveyor belt drum rollers, along with insights into supplier options and customization.
Tips on Choosing the Right Conveyor Belt Drum Roller
Selecting the appropriate conveyor belt drum roller for various industrial applications involves understanding the specific needs of your system. Here are twelve tips to guide you in making the right choice:
- Understand the Load Requirements: Consider the weight and type of materials the conveyor will carry. Heavier loads might require more robust drum rollers.
- Know Your Belt Type: The material and design of your conveyor belt determine the compatibility with certain drum rollers.
- Consider the Operating Environment: Environmental factors such as exposure to chemicals, temperature extremes, and moisture can dictate the material choice for the rollers.
- Assess Speed Requirements: The speed of the conveyor belt can influence the type of roller needed, as high-speed applications may require specialized bearings.
- Determine Roller Diameter: The diameter of the rollers must be compatible with the conveyor setup to ensure proper belt support and minimize wear.
- Select Roller Material: Steel, aluminum, and plastic rollers offer different benefits and limitations; choose based on durability, weight, and cost considerations.
- Evaluate Bearing Type: Bearings play a critical role in the lifespan and efficiency of drum rollers. Options include sealed and regreasable bearings.
- Check for Customization Options: Some applications may require custom-sized or -shaped rollers, so it’s important to check if suppliers offer customization.
- Consider Manufacturer Reputation: Choose suppliers known for quality and reliability.
- Inquire About Maintenance Needs: Understand the maintenance that will be required to keep the rollers in optimal condition.
- Look for Safety Features: Features that enhance safety, such as noise-reduction designs, are important.
- Factor in Cost Efficiency: Evaluate the total cost of ownership, including initial costs, maintenance expenses, and potential downtime.
Get durable conveyor rollers for reliable performance.
Conveyor Roller Suppliers and Custom Options
When purchasing conveyor belt drum rollers, you will encounter a range of suppliers offering various products and services. Here are six notable suppliers in the industry:
- Interroll: Known for high-quality, durable rollers suitable for various applications.
- Precision Pulley & Idler: Offers a wide range of custom and standard rollers.
- Rexnord: Provides a comprehensive line of conveyor components, including specialized drum rollers.
- Fenner Drives: Known for innovative material handling solutions.
- Martin Sprocket & Gear: Offers custom fabrication of rollers to meet specific industrial needs.
- Conveyor Components Co.: Specializes in a broad spectrum of conveyor accessories and rollers.
Many of these suppliers offer custom conveyor rollers, enabling you to tailor components specifically to your system’s requirements and operational challenges.
Key Factors to Consider When Purchasing
When deciding on the right conveyor belt drum rollers, here are ten key factors to keep in mind:
- Price: Ensure the cost aligns with your budget and reflects the quality and longevity expected.
- Durability: Choose rollers that can withstand your operating conditions to reduce replacements.
- Compatibility: Rollers must be compatible with existing conveyor systems to ensure efficient operation.
- Material: The construction material impacts the roller’s suitability for different environments and loads.
- Load Capacity: Match the roller’s load capacity with the demands of your system.
- Speed Capability: Verify that the rollers can handle the operational speed of your conveyor.
- Ease of Installation: Consider how easy it is to install the rollers, which can affect downtime and labor costs.
- Maintenance Requirements: Look for rollers that are easy to maintain and have accessible replacement parts.
- Supplier Reliability: Choose suppliers with good service records and availability of parts.
- Warranty and Support: Check for warranties and customer support services to protect your investment.
By carefully considering these factors, you can ensure that you select the best conveyor belt drum rollers for your industrial needs, enhancing system performance and reliability.

Additional Components and Accessories for Conveyor Belt Drum Rollers
Overview of Related Conveyor Parts
Alongside the critical conveyor belt drum rollers, various other components are essential for the assembly and maintenance of a complete conveyor system. These include roller conveyor parts, which comprise assemblies like brackets, frames, and guide rails that support the rollers. Additionally, dyno rollers, which are specifically designed for dynamic and heavy-duty applications, play a vital role in industries requiring high-speed and high-load capacities. Industrial rollers also form an integral part of the system, tailored for specific tasks ranging from lightweight material handling to processing heavy items, ensuring versatility across different sectors.
Availability of Spare Parts and Aftermarket Services
Maintaining the efficiency of conveyor systems often hinges on the timely replacement and availability of spare parts. For conveyor belt drum rollers and associated components, the market offers a wide range of aftermarket services and spare parts. Suppliers and manufacturers provide everything from individual roller parts to comprehensive upgrade kits, allowing for system enhancements and prolonged service life. The availability of these parts ensures that businesses can minimize downtime, maintain productivity, and extend the lifespan of their equipment. Aftermarket services also include expert consultations, maintenance, and repair services, ensuring that each component of the conveyor system, such as conveyor belt drum rollers, performs optimally and reliably. These services are crucial for businesses looking to maintain continuity, efficiency, and safety in their operations.
Where to Buy and What to Expect in Terms of Cost
When planning to purchase conveyor belt drum rollers, it’s crucial to know where to look and what to expect regarding costs. Understanding these aspects can help streamline the purchasing process and ensure you get the best value for your investment.
Guidance on Where to Find Conveyor Belt Drum Rollers for Sale
There are several avenues where you can find conveyor belt drum rollers for sale, each offering different benefits depending on your needs:
- Manufacturer Direct Sales: Buying directly from manufacturers is often the best way to ensure you’re getting the exact specifications you need for your conveyor system.
- Industrial Supply Companies: Companies such as Grainger and McMaster-Carr offer a wide range of conveyor components, including drum rollers.
- Specialized Conveyor Suppliers: Focused on conveyor systems, these suppliers offer expert advice and a wide range of products tailored to material handling needs.
- Online Marketplaces: Platforms like Alibaba and Amazon Business can be good sources for both standard and custom rollers.
- Local Distributors: Working with local distributors can provide the advantage of faster delivery times and lower shipping costs.
- Trade Shows and Expos: These events provide opportunities to directly interact with manufacturers and view products firsthand before purchasing.
- Used and Surplus Equipment Sellers: For companies on a budget, purchasing used or surplus drum rollers can reduce costs significantly.
- Engineering Firms: These firms often have connections with multiple manufacturers and can assist in procuring the right type of drum rollers.
- E-commerce Platforms: Websites dedicated to industrial parts often have extensive catalogues and competitive pricing.
Overview of Pricing Ranges and Factors Influencing the Cost
The cost of conveyor belt drum rollers can vary widely based on several factors:
- Material: Rollers made from high-grade materials like reinforced steel or specialized plastics tend to be more expensive but offer better performance and durability.
- Size and Complexity: Larger and more complex rollers, such as those with integrated sensors or motorized systems, will naturally cost more.
- Quantity: Purchasing in bulk often allows for discounts.
- Customization: Custom specifications for non-standard conveyor systems will increase the cost.
- Supplier: Costs can vary depending on the supplier’s pricing strategy, brand, and the quality of the components they offer.
Prices for standard conveyor belt drum rollers can range from as little as $15 to $20 each for simple designs, to over $200 or more for high-end or specialized models.
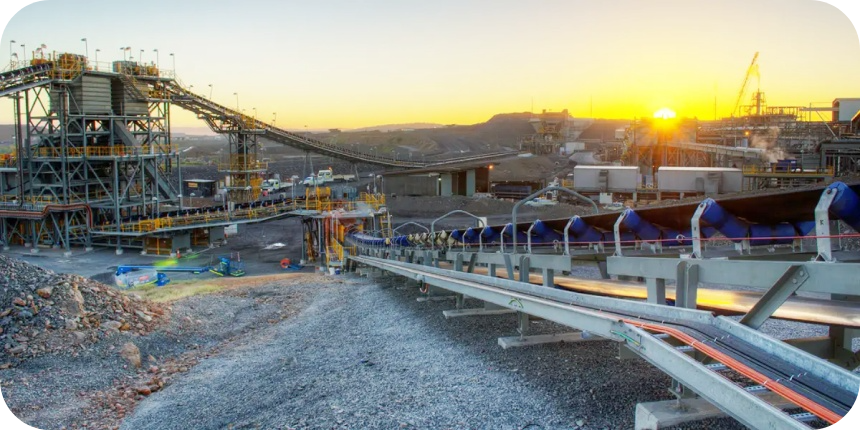
Popular Suppliers and E-commerce Platforms
When it comes to reliable suppliers and platforms for purchasing conveyor belt drum rollers, here are seven popular options:
- Interroll: Renowned for their high-quality rollers and wide range of conveyor components.
- Rexnord: Offers durable drum rollers designed for various industrial applications.
- Precision Pulley & Idler: Specializes in providing precisely engineered rollers.
- McMaster-Carr: Known for its extensive inventory and quick delivery.
- Grainger: A reliable source for a broad array of industrial supplies, including conveyor components.
- Amazon Business: Useful for finding a wide range of products with reviews and competitive pricing.
- Alibaba: Ideal for bulk purchases and custom products, especially for buyers looking to source directly from manufacturers.
By exploring these options, you can find high-quality conveyor belt drum rollers that meet the specific needs of your conveyor system, all while staying within your budget.
FAQs about Conveyor Belt Drum Roller
The type of roller you use for a conveyor belt largely depends on the application and function of the conveyor. Generally, there are two main categories of rollers used in conveyor belt systems:
Drive Rollers: These are powered rollers connected to the conveyor’s motor. They are responsible for moving the belt and the material on it efficiently along the conveyor system. Drive rollers often have a rubber coating to increase friction between the roller and the belt, ensuring the belt moves smoothly and consistently.
Idler Rollers: These rollers are not powered and function to support the conveyor belt and the materials being transported. They help maintain the belt’s tension and guide it as it loops around the conveyor system. Idler rollers come in various designs, including flat, troughed, and impact types, each serving a specific purpose in aiding the conveyance of different materials.
Both drive and idler rollers are critical to the functionality of a conveyor belt system, ensuring the efficient and effective movement of goods.
To maintain the proper alignment and tracking of a conveyor belt, Crowned Rollers are often used. Crowned rollers have a slight increase in diameter from the ends of the roller to the center. This design naturally guides the conveyor belt to center itself over the crown by utilizing the belt’s tendency to move towards the highest point of the roller. For applications requiring precise belt tracking, V-Guided Rollers are used in conjunction with V-guided belts, where a V-shaped guide grove is incorporated within the roller to mate with a corresponding V-shape on the belt, ensuring consistent tracking along the conveyor path.
A Roller Conveyor is a type of conveyor system that uses a series of rollers mounted in a frame to move products and materials along a path. Roller conveyors are versatile and can be powered (driven) or unpowered (gravity). They handle a wide range of materials, from boxes and pallets to individual components and packaged goods. The choice between powered and gravity roller conveyors depends on the specific needs of the operation, such as the weight of items being moved and the required speed of conveyance. Roller conveyors are prized for their simplicity, efficiency, and ability to handle items of various sizes and shapes.
A Belt Over Roller Conveyor combines features of both belt and roller conveyor systems by placing a belt material over a series of rollers. This setup allows for the smooth, efficient transport of items while benefiting from the added support and control provided by underlying rollers. The rollers underneath can either be powered to drive the belt or serve as idler rollers to support the belt and its load. This type of conveyor is particularly useful for items that require stable support during transport, such as small or delicate goods, and can be customized with different belt materials to suit various applications. Belt over roller conveyors are favored for their capacity to handle a wide range of product types and weights efficiently.
The rollers on a conveyor belt are typically referred to as idlers or idler rollers. These components are essential for supporting both the conveyor belt and the material being transported. There are several types of idlers, each serving a specific function: carrying idlers support the loaded belt, return idlers support the empty belt on its return journey, impact idlers absorb the impact at loading points to protect the belt, self-aligning idlers correct the belt’s alignment to prevent tracking issues, and guide rollers maintain proper belt tracking. Together, these idlers ensure the smooth and efficient operation of conveyor systems, essential in various industries like mining and manufacturing.
A conveyor drum, also known as a conveyor pulley, is a cylindrical component essential for driving and supporting the conveyor belt in a conveyor system. There are two main types: drive drums and tail drums. The drive drum, located at the discharge end, is connected to a motor that moves the belt, while the tail drum, at the loading end, supports and redirects the belt. Key components include the shell (often steel or aluminum, sometimes coated for better traction), end discs, shaft, and bearings. Properly designed conveyor drums enhance system efficiency, reduce operational costs, and extend the conveyor’s lifespan.
Last Updated on June 26, 2024 by Jordan Smith
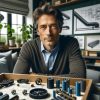
Jordan Smith, a seasoned professional with over 20 years of experience in the conveyor system industry. Jordan’s expertise lies in providing comprehensive solutions for conveyor rollers, belts, and accessories, catering to a wide range of industrial needs. From initial design and configuration to installation and meticulous troubleshooting, Jordan is adept at handling all aspects of conveyor system management. Whether you’re looking to upgrade your production line with efficient conveyor belts, require custom conveyor rollers for specific operations, or need expert advice on selecting the right conveyor accessories for your facility, Jordan is your reliable consultant. For any inquiries or assistance with conveyor system optimization, Jordan is available to share his wealth of knowledge and experience. Feel free to reach out at any time for professional guidance on all matters related to conveyor rollers, belts, and accessories.