Finding the Best Impact Roller for Belt Conveyor Systems
Conveyor systems are vital components in a multitude of industries, from mining to manufacturing, facilitating the seamless transport of goods and materials. Central to these systems’ efficiency is the impact roller for belt conveyor, which plays a crucial role in optimizing conveyor belt performance. These rollers are specifically designed to absorb the shock and impact at loading points, reducing wear and extending the life of the belt. By cushioning and supporting the belt’s load, impact rollers ensure that materials are moved smoothly and efficiently, highlighting their significance in enhancing operational reliability and productivity in conveyor-dependent industries.
What are Impact Roller for Belt Conveyor
Definition and Primary Function of Impact Rollers in Conveyor Systems
Impact rollers, also known as impact idlers, are specialized rollers used in conveyor systems. Their primary purpose is to absorb and reduce the impact force of falling material onto the conveyor belt. The impact roller for belt conveyor is designed to withstand heavy loads and harsh conditions often found in mining, quarrying, and industrial applications.
Construction of Impact Rollers
Impact rollers are constructed differently than standard rollers to provide enhanced durability and shock absorption. They typically feature:
- Rubber Rings: Multiple rubber rings are mounted along the roller, providing cushioning to absorb the impact of falling material.
- Steel Core: A robust steel core supports the rubber rings and ensures the roller can carry heavy loads without deforming.
- Sealed Bearings: Bearings are sealed to prevent dust, moisture, and other contaminants from damaging the roller.
Distinction Between Impact Rollers and Other Types of Conveyor Rollers
Applications of Impact Rollers
Impact rollers are utilized in various industries, including:
- Mining: Where heavy and sharp materials can significantly damage conveyor belts.
- Quarrying: Handling large rocks and debris requires rollers with high shock absorption.
- Cement Plants: Impact rollers protect the belt from damage caused by large, abrasive materials.
- Ports and Terminals: Ideal for handling heavy cargo that drops onto the conveyor belt.
The impact roller for belt conveyor is an essential component in high-impact areas to ensure the longevity and efficiency of conveyor systems. By understanding the difference between impact rollers and other conveyor rollers, industries can optimize their conveyor operations and reduce downtime caused by belt damage.
Types of Impact Roller for Belt Conveyor
When selecting an impact roller for belt conveyor systems, understanding the various types available is crucial. Each type caters to different operational needs, environments, and durability requirements, ensuring that the conveyor system maintains efficiency and longevity.
Used Impact Rollers for Belt Conveyors
Purchasing used impact rollers can be a cost-effective solution for many companies. These rollers, having been in service before, are often sold at a reduced price, making them attractive for budget-conscious operations. The viability of using second-hand impact rollers hinges on their condition and history. The main benefits include reduced initial costs and environmental sustainability by reusing materials. However, it’s essential to conduct thorough inspections and acquire them from reputable sources to avoid compromised performance.
Heavy Duty Impact Rollers for Belt Conveyors
Heavy duty impact rollers are designed to withstand the rigorous conditions of mining, quarrying, and heavy industrial applications. These rollers are built with robust materials and enhanced features such as reinforced frames and specialized bearings. The defining characteristics of heavy-duty impact rollers include their ability to handle high load capacities, resist abrasion, and tolerate extreme weather and environmental conditions. Their design is specifically aimed at reducing downtime and maintenance needs in harsh operational environments.
Best Impact Rollers for Belt Conveyors
Identifying the best impact rollers for belt conveyors involves evaluating several factors, including durability, performance, and the manufacturer’s reputation. The top-tier impact rollers are typically those that offer superior construction materials, such as high-grade rubber and reinforced steel components. These rollers provide optimal performance by efficiently absorbing impact at load points, minimizing belt wear, and maintaining alignment. Additionally, choosing rollers from manufacturers known for quality and innovation ensures reliability and support throughout the roller’s lifespan.
Understanding these types of impact rollers helps in making an informed decision tailored to the specific needs of a conveyor system, enhancing both productivity and operational efficiency.
Components and Design of Impact Roller for Belt Conveyor
The design and components of an impact roller for belt conveyor are pivotal in determining its efficiency and durability. Understanding these elements can help in selecting the right roller for specific applications and ensuring optimal conveyor performance.
Components of an Impact Roller
The primary components of an impact roller include the shell, shaft, bearings, and seals:
- Shell: The outer tube of the roller, typically made from steel or heavy-duty rubber, is designed to absorb the impact of the load dropping onto the belt. The material and thickness of the shell are selected based on the type of materials the conveyor will carry and the overall impact force expected.
- Shaft: The central rod that connects the roller to the conveyor framework and provides the axis of rotation. Shafts must be robust and often are made of high-strength steel to withstand the forces exerted during operation.
- Bearings: These are critical for smooth operation and are usually sealed to prevent dust and particles from causing wear and tear. Bearings reduce rotational friction and support axial and radial loads.
- Seals: Seals protect the bearings by preventing the ingress of contaminants and retaining lubricants, thereby extending the life of the roller and maintaining its efficiency.
Design Variations
The design variations in impact rollers mainly focus on the troughing angle of the roller frame, which is crucial for the conveyor belt’s performance:
- Troughing Angle: This refers to the angle at which the rollers are set, which forms a trough shape with the conveyor belt. This design helps in maintaining the belt’s alignment and supports the weight of the material being transported more efficiently. Common troughing angles are 20, 30, and 45 degrees, chosen based on the material load and transport conditions.
- Impact Zones: Special design considerations are made for rollers placed at impact zones, where material falls onto the belt. These rollers may have thicker shells or specialized rubber coatings to absorb more impact and reduce the stress on the belt.
Understanding these components and design specifics is essential for optimizing the performance of an impact roller for belt conveyor, ensuring that it can handle the expected loads and operating conditions effectively.
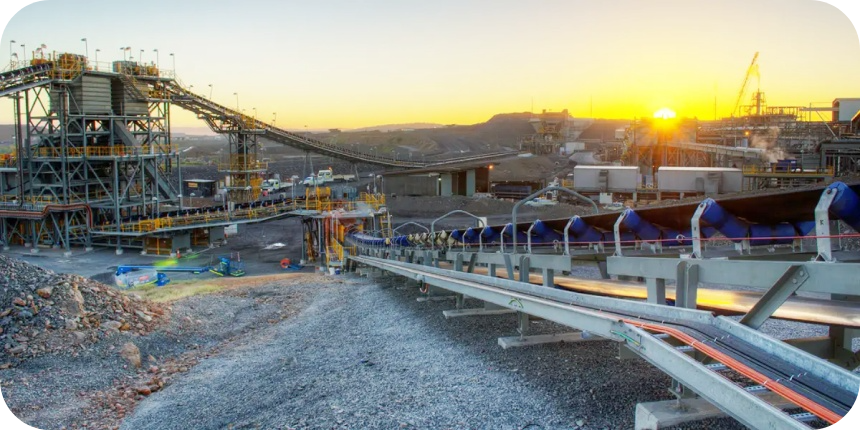
Key Features of Impact Roller for Belt Conveyor
Impact rollers are a critical component of conveyor systems, especially in environments where the belts undergo heavy loading at various points. These rollers are specifically designed to offer enhanced functionality and ensure the longevity of the conveyor system.
Enhanced Load Support and Shock Absorption
One of the most significant features of an impact roller for belt conveyor is its ability to provide enhanced load support and superior shock absorption. This capability is crucial in protecting the conveyor belt from the force of materials dropped from a height, which can cause significant wear and tear. The design of impact rollers typically includes thick, resilient rubber coatings or specially engineered polymers that absorb the kinetic energy of falling materials, thereby reducing the impact on the belt itself and preventing premature damage.
Customization Options
Impact rollers can be customized to meet specific operational needs of various industrial applications. Customization options include:
- Material Choices: Depending on the type of materials the conveyor will carry and the environmental conditions, the rollers can be made from different materials including specialized rubbers, polymers, or even composites.
- Dimensional Adjustments: The diameter and length of the rollers, as well as the type and placement of bearings, can be varied according to the load requirements and conveyor specifications.
- Troughing Angles: Adjustable troughing angles can be designed to fit the specific requirements of the belt’s operational dynamics, ensuring better material retention and reducing spillage.
Technological Innovations
Advancements in the design and manufacturing of impact rollers have led to the integration of several technological innovations:
- Conveyor Roller Seals: These seals are essential for protecting the internal components of the roller, such as bearings, from dust, water, and other contaminants that could reduce the roller’s lifespan. High-quality seals ensure that rollers can operate in various environmental conditions without frequent maintenance.
- Conveyor Idler Rollers: Innovations in idler rollers include the use of high-performance materials that offer reduced friction and wear resistance. These improvements contribute to a longer service life and reduced operational costs.
- Smart Monitoring Systems: Some impact rollers now come equipped with sensors that monitor their condition and performance. This technology allows for predictive maintenance and immediate troubleshooting, which helps in avoiding costly downtimes and enhances overall system efficiency.
These key features make the impact roller for belt conveyor an indispensable part of modern conveyor systems, particularly in industries where bulk materials handling is a routine but critical task. By understanding and utilizing these features, industries can significantly improve the efficiency and reliability of their conveyor systems.
Installation and Maintenance of Impact Roller for Belt Conveyor
Installation Guidelines for the Impact Roller for Belt Conveyor
Proper installation is crucial for ensuring the impact roller for belt conveyor operates effectively and provides maximum shock absorption. Here are ten essential guidelines:
- Identify Impact Zones: Determine where heavy material loading occurs and designate these zones for impact roller installation.
- Check Belt Alignment: Ensure the conveyor belt is properly aligned to prevent uneven wear on the impact rollers.
- Clear Debris: Remove any debris or obstacles from the conveyor frame before installing the impact rollers.
- Install Support Frames: Use sturdy frames to support the impact rollers, ensuring they are secure and properly aligned.
- Positioning: Install impact rollers directly under the conveyor belt’s loading points, spaced appropriately based on the material weight and belt speed.
- Ensure Roller Spacing: The spacing between each impact roller should be consistent and in accordance with the conveyor design specifications.
- Secure Fasteners: Tighten all fasteners and bolts securely to prevent loosening during operation.
- Align with Standard Rollers: Ensure the impact rollers are aligned with standard rollers to create a smooth belt transition.
- Check Belt Tension: Verify that the conveyor belt is adequately tensioned to reduce the risk of slippage over the impact rollers.
- Test Run: Conduct a test run of the conveyor system, checking for any unusual noises or misalignment that could indicate installation errors.
Maintenance Tips for the Impact Roller for Belt Conveyor
Regular maintenance is vital to ensure the longevity and efficiency of the impact roller for belt conveyor. Here are twelve essential maintenance tips:
- Visual Inspection: Regularly inspect the impact rollers for signs of wear, damage, or misalignment.
- Rubber Ring Wear: Check the rubber rings for cracks, wear, or dislodgement. Replace any damaged rings immediately.
- Bearing Checks: Ensure that the roller bearings are functioning correctly and replace them if they show signs of failure.
- Lubrication: Lubricate bearings periodically to prevent friction and prolong their lifespan.
- Alignment Verification: Verify the alignment of impact rollers with the conveyor belt to prevent uneven wear.
- Fastener Tightness: Check all fasteners regularly to ensure they are tight and secure.
- Belt Cleaning: Ensure the conveyor belt is clean and free from debris that could damage the impact rollers.
- Vibration Monitoring: Monitor the conveyor for excessive vibrations, which could indicate issues with the impact rollers.
- Temperature Monitoring: Be alert for overheating, as high temperatures could signal bearing problems or overloading.
- Load Distribution: Ensure that the material load is evenly distributed across the impact rollers to prevent premature wear.
- Replacement Schedule: Establish a replacement schedule for impact rollers based on the conveyor system’s load and operating conditions.
- Document Maintenance: Keep detailed records of maintenance activities, including inspections, repairs, and replacements, to track performance trends.
By following these guidelines and tips, the impact roller for belt conveyor will maintain its efficiency and effectiveness, contributing to the conveyor system’s smooth and uninterrupted operation. Proper installation and consistent maintenance are critical to minimizing downtime and reducing the risk of damage to the conveyor belt and other components.
Product Showcase: Rulmeca Rollers
Overview of Rulmeca’s Impact Rollers
Rulmeca, a global leader in conveyor components, offers an extensive range of impact rollers specifically designed to protect conveyor belts in high-impact zones. The impact roller for belt conveyor systems featured in Rulmeca’s catalog are engineered to deliver superior performance and durability. These rollers are built to absorb heavy material impacts, ensuring smooth belt operation and reducing maintenance costs.
Rulmeca’s impact rollers are known for their quality construction and advanced design, providing efficient shock absorption, thereby minimizing damage to conveyor belts.
Key Features of Rulmeca Impact Rollers
- Robust Construction: A sturdy steel core provides structural integrity and supports the heavy loads experienced in impact zones.
- Specialized Rubber Rings: High-grade rubber rings ensure exceptional shock absorption and cushioning to protect the conveyor belt.
- Sealed Bearings: The bearings are fully sealed to prevent the ingress of dust, moisture, and other contaminants, ensuring longevity.
- Interchangeable Parts: Rubber rings and other components are easily replaceable, reducing downtime during maintenance.
Nine Advantages of Rulmeca’s Design and Material Quality
- High Shock Absorption: Rulmeca’s impact rollers effectively absorb shock from falling material, minimizing conveyor belt damage.
- Durability: The rollers are made from high-quality materials to withstand harsh environments and heavy-duty applications.
- Reduced Downtime: Easy-to-replace components enable swift maintenance, reducing conveyor system downtime.
- Long Lifespan: Sealed bearings and durable rubber rings ensure the impact roller for belt conveyor systems have a long service life.
- Efficient Load Distribution: Impact rollers help distribute the load evenly across the belt, preventing uneven wear.
- Noise Reduction: Rubber rings help reduce operational noise, creating a quieter working environment.
- Corrosion Resistance: Anti-corrosive materials and coatings protect the impact rollers in challenging environments like mining or port facilities.
- Customizable Solutions: Rulmeca offers custom impact roller solutions tailored to specific conveyor requirements.
- Global Availability: With a worldwide network, Rulmeca provides easy access to spare parts and technical support, ensuring smooth operations.
Rulmeca’s impact roller for belt conveyor systems exemplify quality and reliability, making them a preferred choice across various industries. The advanced design and robust materials used in these rollers enhance the performance and safety of conveyor belts in high-impact zones, ensuring efficient and uninterrupted material handling.
Request Technical Support for Impact Conveyor Rollers.
Case Studies of Impact Roller for Belt Conveyor
In the world of material handling, the impact roller for belt conveyor plays a critical role in enhancing the longevity and efficiency of conveyor systems. Below, we explore real-world applications and cases that underscore the significance of selecting optimal impact rollers.
Real-World Applications of Impact Rollers
- Mining Operations in Western Australia: BHP Billiton, one of the largest mining companies globally, implemented premium impact rollers for their extensive mining conveyor systems. The introduction of high-quality impact rollers resulted in a remarkable reduction in downtime caused by equipment wear and tear, proving the value of investing in superior components.
- Grain Transportation in the Midwestern United States: Archer Daniels Midland Company (ADM), a leader in agricultural processing, utilized customized impact rollers in their grain conveyor systems. This strategic choice significantly decreased spillage and maintenance requirements, boosting overall operational efficiency.
- Automotive Parts Manufacturer in Germany: Volkswagen AG, renowned for precision and quality, integrated specially designed impact rollers to handle delicate automotive parts. These rollers absorbed shocks during transportation, reducing the incidence of part damage and maintaining the integrity of sensitive components.
- Coal Handling in India: Tata Power installed high-performance impact rollers in their coal handling plants. These rollers were crucial in minimizing the breakdown of conveyor belts due to the abrasive nature of coal, thereby enhancing the durability of the conveyor system.
- Cement Production in Brazil: Votorantim Cimentos, one of Brazil’s largest cement producers, adopted heavy-duty impact rollers to cope with the harsh conditions of cement production. This adaptation not only improved conveyor belt life but also optimized the energy consumption of their conveyance operations.
- Airport Baggage Handling in Dubai: Dubai International Airport equipped their baggage handling systems with advanced impact rollers. This upgrade ensured smoother and quieter operations, leading to faster baggage processing times and improved passenger satisfaction.
Impact of High-Quality Rollers on Conveyor Efficiency and Operational Costs
- Reduction in Maintenance Costs: High-quality impact rollers, such as those produced by Continental AG, are engineered to withstand extreme conditions without frequent replacements. This durability directly translates into lower maintenance costs and less operational downtime.
- Increased Conveyor Belt Life: By effectively absorbing the impact energy of falling materials, impact rollers extend the life of conveyor belts. This is particularly evident in industries like mining and quarrying, where belts are subjected to severe impacts.
- Enhanced Material Handling Efficiency: Properly selected impact rollers improve the alignment and stability of the conveyor belt, leading to more efficient material handling. For instance, Amazon’s distribution centers have reported smoother operations and reduced material spillage with the adoption of state-of-the-art impact rollers.
- Energy Savings: The reduced friction and optimized belt performance afforded by high-quality impact rollers lead to lower energy consumption. This has been demonstrated in the operations of Cemex, where energy efficiency has been a key benefit of their upgraded conveyor system.
- Improved Safety: Enhanced roller quality also contributes to safer working conditions. This is especially important in industries such as chemical processing or where hazardous materials are transported.
- Cost-Benefit Analysis: Investing in high-quality impact rollers often results in a favorable cost-benefit analysis, as demonstrated by FedEx in their logistics hubs. The initial higher investment is offset by the long-term savings in maintenance, energy, and replacement costs.
- Client Satisfaction and Return on Investment: Companies like DHL have experienced increased client satisfaction due to more reliable and efficient conveyor systems, which in turn has positively impacted their return on investment.
- Innovation and Customization: The continuous innovation in impact roller technology allows for customized solutions that meet specific industrial needs, as seen in the bespoke systems developed for Tesla’s manufacturing lines.
These case studies and points highlight the critical role of impact roller for belt conveyors in enhancing the efficiency and cost-effectiveness of conveyor systems across diverse sectors. By choosing the right rollers, companies can achieve significant improvements in operational performance and cost savings.
FAQs about Impact Roller for Belt Conveyor
In belt conveyor systems, various types of rollers are used to support and guide the conveyor belt and manage the load being transported. The most common types include:
Carrying Rollers: These are the most prevalent type of roller and are strategically placed along the length of the conveyor to support the belt’s weight and the material it carries. They help ensure smooth belt movement.
Return Rollers: Positioned beneath the conveyor belt on its return path, return rollers serve to support the belt when it is not loaded with material, helping to maintain its shape and tension.
Impact Rollers: Specifically designed and located at the loading points, impact rollers are constructed with a series of resilient rubber discs. They absorb the shock and impact of heavy materials being dropped onto the conveyor belt, protecting both the belt and the system from damage.
Each type of roller plays a crucial role in the efficiency and longevity of a belt conveyor system.
Impact rollers are designed specifically for installation at the conveyor belt’s loading points. They serve a dual purpose:
Shock Absorption: They absorb the kinetic energy from materials as they are loaded onto the belt. This is crucial for preventing damage to the conveyor belt, which could be caused by the continuous impact of heavy or sharp materials.
Support and Protection: Beyond absorbing impact, these rollers also provide critical support to the conveyor belt at its most vulnerable points, reducing belt sag and thereby minimizing the risk of damage. Consequently, impact rollers are fundamental components that extend the operational life of the conveyor system.
Impact rollers are essential for transporting heavy or bulky materials, where the constant dropping or direct loading of goods could easily damage a regular conveyor system.
Tracking rollers, also known as guide rollers or aligning rollers, are specialized rollers designed to keep the conveyor belt aligned properly. Misalignment can occur due to various factors such as uneven loading, wear, and tear on the rollers or belt, or an imbalance in the conveyor structure itself. Tracking rollers are strategically positioned along the conveyor framework to gently steer the belt back to its correct path, ensuring smooth operation and reducing wear and risk of damage. These rollers help prevent issues such as belt drift or misalignment, which can lead to decreased conveyor efficiency, belt damage, and potentially dangerous situations. Keeping the belt properly aligned is essential for the safety, efficiency, and longevity of the conveyor system.
Rollers in conveyor systems serve several crucial functions, including:
Support: They provide support to the conveyor belt, helping it to carry the load smoothly and efficiently from one point to another within an industrial or commercial setting.
Movement and Efficiency: By reducing the friction between the belt and the structure, rollers allow for the smooth and efficient movement of goods. This not only facilitates the transportation of materials over long distances but also contributes to lower energy consumption and operational costs.
Protection: Certain types of rollers, like impact rollers, are designed to absorb shock and protect the conveyor belt from damage caused by falling or heavy loads. This extends the lifespan of the conveyor system and reduces maintenance needs.
Conveyor Belt Alignment: Tracking or guide rollers play a vital role in keeping the conveyor belt aligned, preventing slippage or misalignment that could lead to operational disruptions or damage.
In summary, rollers are integral to the functionality, efficiency, and maintenance of conveyor systems, aiding in the seamless transport of various materials across numerous industries.
Last Updated on July 12, 2024 by Jordan Smith
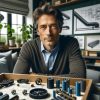
Jordan Smith, a seasoned professional with over 20 years of experience in the conveyor system industry. Jordan’s expertise lies in providing comprehensive solutions for conveyor rollers, belts, and accessories, catering to a wide range of industrial needs. From initial design and configuration to installation and meticulous troubleshooting, Jordan is adept at handling all aspects of conveyor system management. Whether you’re looking to upgrade your production line with efficient conveyor belts, require custom conveyor rollers for specific operations, or need expert advice on selecting the right conveyor accessories for your facility, Jordan is your reliable consultant. For any inquiries or assistance with conveyor system optimization, Jordan is available to share his wealth of knowledge and experience. Feel free to reach out at any time for professional guidance on all matters related to conveyor rollers, belts, and accessories.