Polymer Rollers: the Smart Choice for Your Conveyor System
Polymer rollers, increasingly recognized for their exceptional qualities, are revolutionizing various industries. From mining and agriculture to recycling and material handling, these innovative components are becoming a staple in conveyor systems worldwide. Their growing popularity is a testament to their ability to meet diverse industrial needs while offering unparalleled efficiency and sustainability.Industries seeking efficient and sustainable solutions find an ideal match in polymer rollers. Their energy-saving, durable, and versatile nature makes them a key asset in modern conveyor systems, enhancing performance while supporting sustainable, cost-effective practices.
Description
Our polymer rollers are designed for durability and performance. Each roller features a machined polymer tube or solid bar mounted on sealed precision bearings. The bearings are safeguarded by non-contact rubber seals and metal end caps, ensuring optimal protection and longevity.
Key benefits:
- Smooth and quiet rotation
- Minimal maintenance
- Long service life
- Withstands vibration, shock loads
- Customizable to application
What is the Polymer Rollers?
Polymer conveyor rollers , a pivotal component in modern conveyor systems, are engineered rollers made primarily from polymer materials. Polymer roller technology centers on using synthetic materials for their strength, durability, and resistance to corrosion, moisture, and chemicals. Their hollow-core design significantly lightens them compared to solid steel rollers, enhancing energy efficiency by requiring less power for conveyor belt movement.
Roller Properties
Polymer rollers are engineered to deliver exceptional performance in conveyor systems. Their unique properties make them a superior choice for a wide range of industrial applications.
Excellent Properties:
- High Impact Strength: These rollers can withstand repeated impacts from materials without cracking or breaking, ensuring durability and longevity.
- Abrasion Resistance: They are highly resistant to wear and tear from abrasive materials such as rocks, ore, and other harsh substances.
- Low Coefficient of Friction: This feature reduces the drive power required and minimizes belt wear, enhancing the efficiency of the conveyor system.
- Noise Reduction: Polymer rollers operate more quietly than steel rollers, contributing to a less noisy work environment.
- Corrosion Resistance: They perform exceptionally well in wet and chemical-laden environments, making them ideal for various industrial settings.
- Electrical Insulation: Being non-conductive, they provide safety around electrical equipment, reducing the risk of electrical hazards.
Experience the reliability and efficiency of our polymer rollers, designed to optimize your conveyor system’s performance.
What is the Advantages of Polymer Rollers?
Unique Features of Polymer Rollers
Polymer rollers, increasingly sought after in various industries, offer a suite of unique features that set them apart from traditional rollers. One of the standout features is their self-cleaning surfaces. This innovative design minimizes the buildup of materials on the roller, which is a common issue with steel rollers, leading to improved conveyor efficiency and reduced maintenance.
Another significant feature is their anti-static properties. This is particularly beneficial in environments where static buildup can be a safety hazard or can interfere with sensitive materials being conveyed. Additionally, polymer rollers are known for their noise reduction capabilities. The material inherently dampens sound, leading to a quieter operation environment, which is a considerable advantage in noise-sensitive areas.
Energy Efficiency and Cost Savings
The reduced weight of polymer clay roller directly translates to lower power consumption. This is because lighter rollers require less energy to rotate, leading to significant energy savings and reduced operational costs. For businesses looking to improve their environmental footprint while also saving on costs, polymer rollers for sale offer an attractive solution.
Polymer conveyor rollers’s Safe
Safety and ease of installation are key benefits of polymer rollers. Polymer conveyor rollers’s lightweight design simplifies and secures handling during installation and maintenance, reducing injury risks and speeding up the process.
Durability and Resistance to Wear and Corrosion
Polymer rollers, made from durable materials like HDPE, offer strong resistance to wear and corrosion, ensuring longevity and fewer replacements, even in harsh conditions, thus reducing long-term costs.
Enhanced Durability with Strengthened Frame Construction
In addition to their material benefits, many polymer conveyor rollers feature a strengthened frame construction. This enhancement further increases their durability, especially under heavy loads or in demanding industrial environments. The combination of high-quality materials and robust construction ensures that these rollers can withstand the rigors of industrial use while maintaining performance and efficiency.
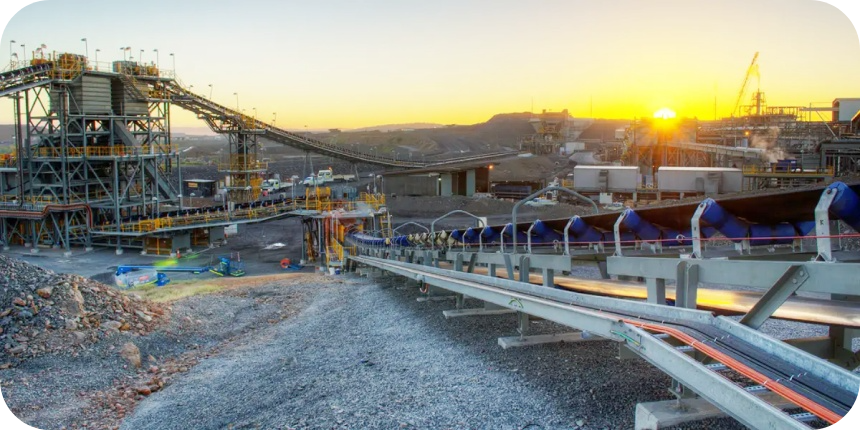
Comparison with traditional steel rollers
Feature/Aspect | Traditional Steel Rollers | Polymer Rollers |
---|---|---|
Weight | Heavier | Lighter |
Energy Efficiency | Require more energy to operate | More energy-efficient |
Corrosion Resistance | Prone to corrosion | Highly resistant to corrosion |
Wear Resistance | Susceptible to wear | Better resistance to wear |
Lifespan | Shorter due to wear and corrosion | Longer due to durable construction |
Suitability in Harsh Conditions | Less suitable in harsh environments | More suitable for harsh environmental conditions |
Diverse Applications of Polymer Rollers
Polymer clay roller, with their advanced features and benefits, have found applications in a wide range of industries. Their versatility makes them suitable for various challenging environments, from heavy-duty industrial settings to delicate material handling.
Gram is various polymer rollers for sale, catering to these diverse applications. Whether it’s for a mining operation requiring heavy-duty rollers or a food processing plant needing hygienic and easy-to-clean components, the range of our polymer rollers meets a wide array of industry demands.
- Mining and Quarrying: Ideal for handling abrasive materials such as rocks and ore, polymer rollers withstand repeated impacts and resist wear, ensuring longevity and reliability in harsh environments.
- Suitability for Challenging Environments: One of the standout features of polymer rollers is their suitability for challenging environments. In industries like mining, agriculture, and marine applications, equipment is often exposed to extreme conditions. Polymer rollers, known for their robustness, can withstand these harsh environments. Their resistance to wear, corrosion, and environmental factors makes them an ideal choice for operations in these sectors.
- Port Material Handling: Ports, known for their harsh and corrosive environments, require equipment that can withstand these challenging conditions. Polymer rollers are increasingly being used in port material handling equipment due to their corrosion resistance and durability. They ensure smooth operations in loading and unloading processes, even in the presence of saltwater and other corrosive elements.
- Food and Beverage Industry: Their corrosion resistance and non-toxic nature make polymer rollers perfect for hygienic applications, ensuring cleanliness and safety in food processing and packaging.
- Pharmaceutical Industry: In environments where cleanliness and chemical resistance are crucial, polymer rollers offer a reliable solution for safe and efficient material handling.
- Manufacturing and Packaging: Polymer rollers contribute to smooth and quiet operation, reducing noise levels and wear on conveyor belts, which is essential in high-speed production lines.
- Electronics Industry: Providing electrical insulation, polymer rollers enhance safety around sensitive electrical equipment, preventing electrical hazards and ensuring smooth operation.
- Automotive Industry: Used in assembly lines and material handling systems, polymer rollers offer durability and low maintenance, making them suitable for the rigorous demands of automotive manufacturing.
- Logistics and Warehousing: Their lightweight yet strong construction allows for efficient handling of various goods, reducing energy consumption and wear on the conveyor systems.
- Textile Industry: Polymer rollers ensure gentle handling of fabrics, preventing damage and maintaining the quality of the materials throughout the production process.
- Printing and Paper Industry: They provide smooth and precise movement of paper and other materials, essential for high-quality printing and finishing processes.
- Mobile Plant and Telescopic Conveyors: In the realm of mobile plants and telescopic conveyors, polymer rollers offer unmatched benefits. Their lightweight nature makes them ideal for mobile equipment, where reducing overall weight is crucial for mobility and energy efficiency. In telescopic conveyors, often used in shipping and logistics, polymer rollers provide the necessary durability and smooth operation, essential for handling materials efficiently and safely.
How to Select Suitable Polymer Clay Roller?
Selecting the right type of polymer roller is crucial for optimizing the efficiency and longevity of your conveyor system.Understanding the unique requirements of different industries and applications is crucial for selecting the most suitable polymer rollers for your specific needs.Here’s a guide to help you make an informed decision:
1. Application Requirements
- Type of Material Being Conveyed: Consider the nature of the materials the roller will handle (e.g., abrasive, corrosive, heavy).
- Environment: Assess the working conditions, such as exposure to chemicals, moisture, temperature extremes, and the presence of electrical equipment.
2. Material Properties
- Impact Strength: Choose rollers with high impact strength for applications involving heavy or abrasive materials.
- Abrasion Resistance: Essential for handling materials like rocks, ore, or other rough substances.
- Corrosion Resistance: Important for environments with moisture or chemicals.
- Electrical Insulation: Necessary for applications near electrical equipment to prevent hazards.
3. Roller Specifications
- Size and Dimensions: Ensure the roller’s dimensions (length, diameter) fit the conveyor system and the application requirements.
- Bearing Type: Select precision bearings that can handle the load and rotational speed required.
- Load Capacity: Determine the maximum load the roller will need to support.
- Surface Finish: Consider the finish of the roller’s surface based on the material being conveyed to avoid damage or sticking.
4. Performance Characteristics
- Low Coefficient of Friction: Reduces drive power and minimizes belt wear, enhancing efficiency.
- Noise Reduction: Opt for rollers designed to operate quietly, especially in noise-sensitive environments.
- Vibration and Shock Resistance: Choose rollers that can withstand high levels of vibration and shock loads without compromising performance.
5. Customization Options
In the market for polymer rollers, you’ll encounter diverse variants tailored to specific needs, varying in size, shape, material, and bearing types. Common types include impact rollers for shock absorption at loading points and guide rollers for belt alignment. Many suppliers also customize dimensions and materials to fit your conveyor system precisely.
- Tailored Designs: Look for manufacturers who offer customization to meet specific needs, such as unique dimensions, materials, or additional protective coatings.
- Compatibility: Ensure the roller is compatible with your existing equipment and any other components in your conveyor system.
6. Manufacturer and Quality Assurance
- Reputation and Experience: Select rollers from reputable manufacturers with a track record of quality and reliability.
- Warranty and Support: Consider the warranty offered and the availability of customer support and after-sales service.
7. Cost Considerations
- Budget: Balance between cost and quality, ensuring you get the best value for your investment.
- Long-Term Savings: Factor in the long-term savings from reduced maintenance, longer service life, and improved efficiency.
Selecting the right polymer roller involves understanding your specific application needs, the properties of the materials being handled, and the performance characteristics required. By considering these factors, you can choose a polymer roller that will provide reliable, efficient, and long-lasting performance for your conveyor system.
How Do Polymer Rollers Work?
Polymer rollers are integral components in conveyor systems and various industrial applications, offering numerous advantages over traditional metal rollers. Here’s a detailed look at how they work and the principles behind their operation:
Basic Structure
- Polymer Tube or Solid Bar: The core body of the roller is made from a high-strength polymer, which can either be a machined tube or a solid bar. This material provides durability and reduces overall weight.
- Sealed Precision Bearings: These bearings are housed within the ends of the roller and allow for smooth rotation. They are typically sealed to protect against dust, moisture, and other contaminants, ensuring long-lasting performance.
- Non-Contact Rubber Seals and Metal End Caps: The rubber seals prevent debris from entering the bearing area, while the metal end caps provide additional protection and structural integrity.
Working Mechanism
- Rotation and Load Distribution: The rollers rotate around their central axis, supported by precision bearings. As materials are conveyed over the rollers, their weight is evenly distributed across the surface, minimizing wear and tear on the belt and reducing the power needed to move the conveyor.
- Low Friction Operation: Polymer rollers have a low coefficient of friction, which means less resistance against the conveyor belt. This reduces the drive power required, minimizes energy consumption, and extends the lifespan of the belt.
- Impact and Abrasion Resistance: The high impact strength and abrasion-resistant properties of the polymer material allow the rollers to handle heavy and abrasive loads without damage, maintaining smooth operation even in demanding environments.
- Noise Reduction: Unlike metal rollers, polymer rollers operate quietly, which is beneficial in noise-sensitive environments. This noise reduction is due to the inherent properties of the polymer material, which dampens vibrations and sound.
- Corrosion Resistance: Polymer rollers are resistant to corrosion, making them ideal for use in wet or chemically aggressive environments. This ensures longevity and reduces maintenance needs, as they do not rust or degrade like metal rollers.
- Electrical Insulation: The non-conductive nature of the polymer material provides electrical insulation, which is crucial in applications near electrical equipment, reducing the risk of electrical hazards.
Polymer rollers work by rotating smoothly around their central axis, supported by precision bearings, to facilitate the efficient movement of materials along conveyor systems. Their low friction, impact resistance, noise reduction, corrosion resistance, and electrical insulation make them an excellent choice for enhancing the performance and longevity of industrial conveyor systems. By distributing loads evenly and reducing the power required to move the conveyor belt, polymer rollers contribute to a more efficient and cost-effective operation.
Customer Testimonials and Success Stories in Polymer Rollers
Customer testimonials play a crucial role in illustrating the real-world benefits and reliability of polymer rollers. These testimonials, coming directly from those who have experienced the advantages first-hand, serve as powerful endorsements. Here, we share some compelling stories from various industries that have witnessed significant improvements after integrating polymer rollers into their systems.
A mining company, previously using traditional steel rollers, faced challenges with frequent breakdowns and maintenance issues due to the harsh working environment. After switching to polymer rollers, they reported a remarkable decrease in downtime. The lightweight nature of the rollers made them easier to handle and install, and their resistance to corrosion and wear significantly extended their lifespan. The company’s maintenance manager stated, “Since we started using polymer rollers, our conveyor system has become more reliable, and our maintenance costs have dropped significantly.”
In the agriculture sector, a large farming equipment manufacturer shared their experience. They replaced their old steel rollers with polymer ones in their grain handling conveyors. The result was a noticeable reduction in power consumption and noise levels. The operations manager noted, “The switch to polymer rollers not only saved us on energy costs but also created a more pleasant working environment for our staff.”
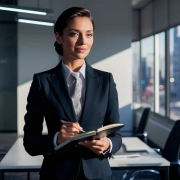
“Our operations require handling extremely abrasive materials, and the wear and tear on our equipment used to be a significant issue. Since switching to polymer rollers, we’ve seen a remarkable improvement. The high impact strength and abrasion resistance of these rollers have drastically reduced our maintenance costs and downtime. They’ve truly proven to be a game-changer for us.”
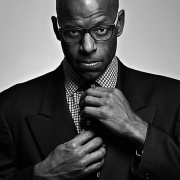
“Working with sensitive electronic components requires rollers that provide electrical insulation and operate without causing static buildup. Polymer rollers have exceeded our expectations in these areas. Their non-conductive nature has improved safety and reduced the risk of damage to our products. These rollers are a vital part of our production process.”
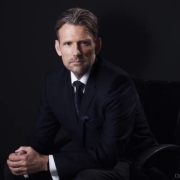
“In the mining sector, dealing with abrasive materials has always been tough on our equipment. Since we started using polymer rollers, we’ve seen a dramatic improvement. The rollers’ high abrasion resistance and impact strength have significantly cut down our maintenance needs and operational downtime. They’ve become an essential part of our conveyor systems, proving to be incredibly reliable and durable under the harsh conditions we face.”
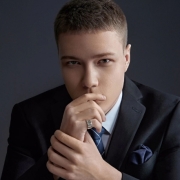
“Our mining operations involve handling extremely rough and abrasive materials, which previously led to frequent roller replacements and high maintenance costs. The switch to polymer rollers has been a game-changer. Their exceptional durability and resistance to wear have greatly reduced both our maintenance workload and downtime. The polymer rollers have proven to be highly effective, helping us maintain smoother and more cost-efficient operations.”
CONTACT US
Let us help you find a better solution!
FAQs about Polymer Rollers
1. What rollers are used in conveyors?
Conveyor systems typically use various types of rollers, including drive rollers, idler rollers, and return rollers. Drive rollers are powered to move the conveyor belt, while idler rollers support and guide the belt. Return rollers ensure the belt returns to the starting point. Additionally, there are specialized rollers like impact rollers, which are used in high-load areas to absorb shock, and tapered rollers for applications requiring angled movement.
2. What are the different types of roller conveyors?
There are several types of roller conveyors, including gravity roller conveyors, which use the force of gravity to move items; powered roller conveyors, which are driven by motors for controlled movement; and accumulation roller conveyors, which allow items to accumulate and sort without jamming. Other types include live roller conveyors with powered rollers and flexible or expandable roller conveyors that can be adjusted to different configurations.
3. How do conveyor rollers work?
Conveyor rollers work by providing a support surface for the conveyor belt and materials being transported. They reduce friction between the belt and the conveyor frame, allowing smooth movement of goods. In a powered roller conveyor, rollers are driven by motors and belts to move materials. In gravity systems, the rollers rely on gravity to propel items along the conveyor. Rollers help maintain the belt’s alignment and can be designed for specific functions like impact absorption or load distribution.
4. What materials are conveyor rollers?
Conveyor rollers are made from various materials depending on their application. Common materials include steel, which offers strength and durability; aluminum, known for its lightweight and resistance to corrosion; and plastic, which is used for its resistance to chemicals and lower friction. Some rollers also have rubber or urethane coatings to enhance grip and reduce noise. The choice of material is based on factors like load capacity, environment, and the type of materials being conveyed.