30 Roller Conveyor: Essential Features and Benefits
Roller conveyors are indispensable in industrial and warehousing environments, playing a critical role in the streamlined movement of goods across various stages of production and distribution. Among these systems, the 30 roller conveyor stands out due to its adaptability and efficiency in handling materials of different sizes and weights. This type of conveyor is highly valued for its ability to facilitate the easy transport of items, whether for assembly lines, sorting operations, or packaging areas. It is recognized for its robust design and ability to improve operational flow, thereby enhancing productivity and reducing labor costs. This introduction sets the stage for a deeper exploration into the specific features and benefits of the 30 roller conveyor, highlighting its pivotal role in modern material handling solutions.
Overview of the 30 Roller Conveyor
The 30 roller conveyor is an integral component of modern material handling systems found in a variety of industrial and commercial settings. Its design is tailored to enhance efficiency and reliability in moving goods across numerous environments. Below, we will explore both the distinctive characteristics of the 30 roller conveyor that make it so effective, as well as the diverse settings where its impact is most beneficial.
Key Features of the 30 Roller Conveyor:
The 30″ roller conveyor is engineered with specific features that optimize performance and durability. These features are designed to meet the diverse needs of industries, ensuring both versatility and high-capacity handling.
- Diameter of Rollers: Each roller measures 1.9 inches in diameter, providing the perfect balance between size and functionality, allowing for smooth movement of various package sizes.
- Materials Used: Constructed from 16 gauge galvanized steel, the rollers offer outstanding resistance to wear and corrosion, making them ideal for harsh industrial environments.
- Length and Width Options: Available in lengths of 5 and 10 feet, and widths ranging from 12 to 36 inches, these conveyors can be tailored to fit specific spatial requirements and operational demands.
- Load Capacity: Designed to handle loads up to 266 pounds per roller, this system can support substantial weights, essential for industries dealing with heavy goods.
- Bearings: Features crimped and pre-lubricated bearings that enhance smooth operation and reduce the need for frequent maintenance.
- Axle Specifications: Utilizes a 7/16″ hex mild steel axle that reinforces the conveyor’s structural integrity and ensures long-lasting performance.
- Axle Retention: Incorporates a spring retention method at one end of the axle, which simplifies the process of roller adjustment and replacement.
- Coefficient of Friction: With a friction coefficient ranging from .14 to .42, the conveyor facilitates easier and more efficient movement of goods with minimal power usage.
Typical Uses and Effective Environments for the 30 Roller Conveyor:
The 30″ roller conveyor is versatile enough to be effective in a range of environments, from light industrial to heavy-duty applications. Its design caters to the needs of different sectors, enhancing workflow and productivity.
- Shipping Departments: Streamlines the process of moving packages to dispatch areas, optimizing the flow from packaging to shipment.
- Assembly Areas: Enables efficient movement of parts and assemblies across production lines, reducing downtime and increasing assembly speed.
- Sorting Operations: Crucial in facilities that require precise and rapid sorting of products into different categories, improving overall sorting accuracy.
- Packaging Areas: Assists in transporting goods swiftly from the packaging machinery to the storage or dispatch areas, minimizing handling time.
- Distribution Centers: Facilitates faster and more organized handling of products, crucial for maintaining efficiency in inventory and distribution processes.
- Temporary Setups: Easily configured for temporary or seasonal operations, providing flexibility and easy scalability in response to varying operational demands.
- Load Transfer Stations: Offers a seamless transfer of heavy and bulky items between different sections of a facility, enhancing material flow without manual intervention.
- Repair and Maintenance Workshops: Useful in transporting equipment or components smoothly across maintenance areas, aiding in efficient repair processes.
This detailed examination of the 30″ roller conveyor’s features and applications illustrates its critical role in modern industry, highlighting its adaptability and capacity to significantly enhance operational efficiency.
Advantages of Using a 30 Roller Conveyor
The 30 roller conveyor system is a popular choice for many industries due to its robust design and versatile functionality. This system not only enhances operational efficiency but also offers significant advantages over other types of conveyor systems. Here, we explore nine key benefits of using a 30″ roller conveyor in various settings.
- Cost-Effectiveness: The 30 roller conveyor is economically advantageous, offering a cost-effective solution due to its minimal need for manual labor and reduced operational costs, making it ideal for both large-scale industries and smaller operations.
- Versatility: This type of conveyor can be easily installed and reconfigured for both permanent and temporary setups, allowing it to adapt to changing business needs and different operational layouts.
- Supports Heavier Loads: Unlike skatewheel conveyors, the 30 roller conveyor is designed to handle heavier loads, making it suitable for industries that transport large volumes of goods or heavier items.
- Low Maintenance: The durability of the materials, especially the steel rollers, ensures that the conveyor system requires less maintenance, reducing both downtime and long-term costs associated with wear and tear.
- Increased Productivity: With the ability to move items quickly and efficiently, the 30 roller conveyor significantly boosts productivity, enabling faster processing and throughput in operations like manufacturing and distribution.
- Ease of Integration: The modular design of the 30 roller conveyor allows it to be easily integrated with other conveyor systems and production line equipment, creating a seamless flow of operations.
- Improved Worker Safety: By automating the movement of goods, the 30 roller conveyor reduces the need for manual handling, thereby decreasing the risk of injuries and improving overall workplace safety.
- Enhanced System Longevity: The use of high-quality materials and robust construction extend the lifespan of the 30 roller conveyor, ensuring that it can withstand the rigors of daily use without significant degradation.
- Energy Efficiency: The 30 roller conveyor operates with minimal energy consumption compared to motorized conveyor systems, making it an environmentally friendly option that also reduces energy costs.
These advantages make the 30 roller conveyor a reliable, efficient, and economical choice for businesses looking to optimize their material handling processes, proving its worth in diverse industrial scenarios.
Specifications and Customization Options for the 30 Roller Conveyor
The 30 roller conveyor is designed to be highly adaptable, meeting the specific needs of various industries through a range of specifications and customization options. This section details the versatility of the 30″ roller conveyor in terms of its dimensions, materials, and the availability of additional components to enhance its functionality.
Detailed Dimensions of the 30 Roller Conveyor
The 30 roller conveyor is engineered to accommodate a diverse range of industrial applications by offering extensive customization in terms of its dimensions. These variations are designed to fit specific operational requirements and spatial configurations, ensuring efficient use of available space and optimal handling of various types of loads.
- Lengths: The conveyors are typically available in standard segments of 5 feet and 10 feet, which can be linked to form longer sections. This modular approach allows for easy expansion or reconfiguration according to the operational changes. Custom lengths can also be manufactured to meet specific requirements, ensuring that no space constraints hinder the setup.
- Widths: The standard widths for the 30 roller conveyor include 12″, 15″, 18″, 24″, 30″, and 36″. These sizes ensure that there is a suitable option for different types of goods, from small packages to larger boxed items. Wider options are also available, accommodating larger objects and providing greater flexibility in handling bulkier items without sacrificing stability.
- Roller Centers: The spacing between rollers, or roller centers, is a critical dimension that influences the conveyor’s ability to transport goods smoothly. Typical settings include 1-1/2″, 3″, 4-1/2″, and 6″. Adjusting the roller centers is essential for accommodating different sizes of products, as closer spacing provides better support for smaller, more fragile items, while wider spacing is sufficient for larger, sturdier goods. Custom spacing is also possible, tailored to the unique demands of the operation.
- Adjustability: The height and angle of the conveyor can often be adjusted, which is crucial for aligning with other equipment and optimizing the ergonomic handling of goods. This feature allows facilities to modify the conveyor setup to meet specific operational needs or to accommodate changes in production processes.
- Modularity: The design of the 30 roller conveyor often emphasizes modularity, enabling not just extensive lengths through additional sections but also the integration of curves, junctions, and gates. This adaptability makes it easier for businesses to expand or alter their conveyor systems as their production scales up or shifts direction.
These points enrich the description of the 30 roller conveyor’s dimensions, emphasizing its adaptability and the ability to tailor the system to specific industrial needs
Customization Options Table for the 30 Roller Conveyor
To further detail the customization options available for the 30 roller conveyor, here is an expanded and enriched table that includes additional features and their potential configurations:
This detailed customization table provides a comprehensive overview of the available options for the 30 roller conveyor, highlighting its adaptability to different industrial environments and specific operational needs.
Availability of Additional Parts and Accessories
The 30 roller conveyor can be enhanced with various parts and accessories to improve its functionality and adaptability:
- Spurs: These are used to divert or merge products onto different tracks, essential for sorting operations and complex conveyor layouts.
- Curves: Available to facilitate changes in direction of the conveyor path, allowing for flexible use within confined spaces.
- Side Guides: These ensure that goods stay aligned on the conveyor, preventing slippage and accidents.
- Leg Supports: Adjustable supports to maintain the conveyor at the optimal height and level, which can be tailored to different environments.
- Guard Rails: Installed along the edges of the conveyor to keep items from falling off, providing additional safety.
- Ball Transfer Tables: These can be integrated into the conveyor system to allow for multidirectional movement of heavy loads.
- Impact Plates: Placed at loading zones to absorb shocks and reduce wear on the conveyor from heavy items.
- Drive Sections: Motorized sections can be added for automated movement, useful in reducing manual handling.
Each of these options ensures that the 30 roller conveyor can be precisely tailored to meet the specific needs of any facility, enhancing both productivity and efficiency.
To Purchase a 30 Roller Conveyor
Choosing and purchasing a 30 roller conveyor involves several key considerations that ensure the equipment meets your specific operational needs while offering the best value for your investment. This section offers detailed guidance on selecting the right 30″ roller conveyor, identifying reliable manufacturers, and comparing pricing effectively.
Guide to Choosing the Right 30 Roller Conveyor: New vs. Used Options
Making a decision between new and used 30 roller conveyors involves weighing various factors, as outlined in the table below:
Finding Reliable Manufacturers and Supplier Criteria
Selecting a reputable manufacturer or supplier for your 30 roller conveyor is crucial. Here are nine key points to consider when evaluating potential vendors:
- Reputation: Look for suppliers with strong industry reputations and positive customer reviews.
- Quality Certifications: Check for relevant certifications (e.g., ISO 9001) that indicate quality manufacturing practices.
- Customer Support: Choose suppliers known for excellent customer service and support.
- Product Range: Ensure they offer a wide range of products and customization options.
- Technical Expertise: Suppliers should have deep knowledge about their products and the ability to provide insights and solutions.
- After-Sales Service: Consider the quality of after-sales support and maintenance services.
- Delivery Timeliness: Evaluate their track record on delivery speed and reliability.
- Financial Stability: Stable suppliers are likely to offer better long-term support and reliability.
- Compliance and Standards: Ensure they comply with industry standards and safety regulations.
Tips on Comparing Prices and Ensuring Best Value
When it comes to investing in a 30 roller conveyor, ensuring you get the best value involves more than just looking at the sticker price. Here are nine tips for effectively comparing prices:
- Total Cost of Ownership: Include maintenance, repair, and operational costs in your calculations, not just the purchase price.
- Compare Features: Align features and capabilities of different models against their costs.
- Bulk Discounts: Ask about discounts for bulk purchases if buying multiple units.
- Warranty Offers: Consider the value of warranty options being offered.
- Financial Options: Look for leasing or financing options that might make a higher-priced option more feasible.
- Trade-In Policies: Some suppliers might offer trade-ins on old equipment for a discount on the new purchase.
- Demonstrations: Request demonstrations to see the equipment in action, which can help assess its true value.
- Negotiate: Don’t hesitate to negotiate on price, especially when dealing with higher-end models or large orders.
- Seasonal Sales: Take advantage of seasonal sales and promotions that may offer significant savings.
Each of these sections provides essential information designed to help make informed decisions when purchasing a 30 roller conveyor, ensuring that you choose a system that meets your needs while providing the best possible return on investment.
Maintenance and Replacement Parts for the 30 Roller Conveyor
Maintaining a 30 roller conveyor and ensuring its components are in optimal condition is crucial for sustaining operational efficiency and prolonging the equipment’s lifespan. This section provides a comprehensive guide on regular maintenance tasks, sourcing replacement parts, and the significance of adhering to manufacturer recommendations.
Overview of Typical Maintenance Tasks
Regular maintenance of a 30 roller conveyor is essential to prevent breakdowns and minimize wear and tear. Here are more detailed key maintenance tasks:
- Lubrication: Frequent lubrication of bearings and rollers to ensure smooth operation and reduce friction, which can help prevent overheating and extend the life of the moving parts.
- Cleaning: Regular cleaning to remove debris, dust, and any particulate matter that can accumulate on the conveyor and impair its function, potentially leading to jams or degradation of components.
- Inspection: Conducting routine checks for signs of wear or damage on rollers, bearings, and the conveyor frame to identify issues before they lead to a breakdown.
- Adjustment: Tightening and adjusting belts, rollers, and other components to prevent misalignment that can cause uneven wear or operational inefficiencies.
- Belt Tensioning: Ensuring the belt is properly tensioned to avoid slippage and uneven wear, which can affect the conveyor’s performance and lead to premature wear.
- Alignment Checks: Regularly checking and correcting the alignment of the conveyor to ensure efficient operation and prevent damage to the conveyor and the products being transported.
- Electrical Systems Checks: Inspecting motors and controls for proper function and safety compliance, including checking for wire integrity and connection stability.
- Replacement of Worn Parts: Prompt replacement of worn or damaged parts to prevent further damage and maintain efficiency, ensuring that replacements are timely to avoid operational downtime.
- Record Keeping: Maintaining a log of maintenance activities to track the condition and repairs of the conveyor system over time, which helps in predicting potential failures and scheduling preventive maintenance.
Information on Replacement Rollers and Other Parts
When it comes to replacing parts on a 30 roller conveyor, knowing where to find quality components and how to choose the right ones is crucial:
- OEM vs. Aftermarket: Weigh the benefits of original equipment manufacturer (OEM) parts, which are guaranteed to fit and perform as needed, against aftermarket parts, which might be less expensive but vary in quality.
- Compatibility: Ensure that replacement parts are compatible with your specific model of 30 roller conveyor, to avoid malfunctions or inefficiencies due to improper fit.
- Material Quality: Opt for parts made from high-quality materials that offer durability and optimal performance, which can reduce the frequency of replacements.
- Supplier Reputation: Source parts from reputable suppliers known for quality and service to ensure reliability and product support.
- Warranty: Check if the replacement parts come with a warranty, which can provide assurance against defects and offer peace of mind.
- Price Comparison: Compare prices from different suppliers to ensure you are getting a fair deal without compromising on quality.
- Urgency of Replacement: Consider the lead times for receiving parts, especially if the conveyor is critical to your operations, to minimize downtime.
- Bulk Orders: Investigate the possibility of bulk orders if frequent replacements are anticipated; this can reduce costs and ensure availability of parts when needed.
- Technical Support: Ascertain whether suppliers offer technical support for the installation and use of replacement parts, which can be invaluable for ensuring correct installation and operation.
These detailed guidelines aim to assist in maintaining a 30 roller conveyor effectively and ensuring that any necessary replacements are made with the best possible parts, maintaining the system’s efficiency and longevity.
Last Updated on May 22, 2024 by Jordan Smith
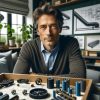
Jordan Smith, a seasoned professional with over 20 years of experience in the conveyor system industry. Jordan’s expertise lies in providing comprehensive solutions for conveyor rollers, belts, and accessories, catering to a wide range of industrial needs. From initial design and configuration to installation and meticulous troubleshooting, Jordan is adept at handling all aspects of conveyor system management. Whether you’re looking to upgrade your production line with efficient conveyor belts, require custom conveyor rollers for specific operations, or need expert advice on selecting the right conveyor accessories for your facility, Jordan is your reliable consultant. For any inquiries or assistance with conveyor system optimization, Jordan is available to share his wealth of knowledge and experience. Feel free to reach out at any time for professional guidance on all matters related to conveyor rollers, belts, and accessories.