Innovations in 20 Conveyor Roller Technology
Conveyor rollers are essential components in material handling systems, facilitating the smooth and efficient movement of goods in various industries. They are widely used in manufacturing, warehousing, distribution, and shipping applications, where they help streamline operations and improve productivity. The focus of this blog is on the 20 conveyor roller, which is specifically designed for conveyor systems with a frame width of 20 inches. These rollers are crucial for ensuring optimal performance and reliability in systems that require precise and durable components. Understanding the different types, specifications, and applications of 20 conveyor rollers will help you make informed decisions for your material handling needs.
Types of 20 Conveyor Roller
When discussing 20-inch conveyor rollers, it’s essential to understand the specific types available, their applications, and their unique features. Here we’ll explore three primary categories: General Purpose Conveyor Rollers, Corrosion-Resistant Conveyor Rollers, and High-Durability Conveyor Rollers. Each type serves distinct functions in various industrial environments.
General Purpose Conveyor Rollers
General Purpose Conveyor Rollers are the backbone of many conveyor systems. These rollers are versatile and used across various industries for standard operations.
- Common Sizes and Axle Types: Typically, these 20 conveyor rollers come in a range of thicknesses to accommodate different belts and loads. Axles can be either fixed or spring-loaded, providing flexibility in assembly and maintenance.
- Typical Applications and Benefits: They are ideal for handling goods in warehouses, distribution centers, and manufacturing plants where environmental conditions are controlled. Benefits include low cost, ease of installation, and availability in a wide range of materials like steel, aluminum, and plastic, catering to different weight and speed requirements.
Corrosion-Resistant Conveyor Rollers
Designed to withstand harsh environments, Corrosion-Resistant Conveyor Rollers are crucial for industries where exposure to chemicals, moisture, or corrosive elements is a regular occurrence.
- Material and Construction Features: These rollers are typically made from stainless steel or coated with non-corrosive materials such as zinc or a special plastic. The construction avoids any crevices or pits that might harbor corrosive elements.
- Ideal Environments for Use: Ideal for use in food processing, chemical plants, and outdoor locations near the ocean where saltwater exposure is common. These rollers ensure longevity and reliability where standard rollers would fail.
High-Durability Conveyor Rollers
For applications requiring the highest level of durability and load-bearing capacity, High-Durability Conveyor Rollers are engineered to perform under extreme conditions.
- Specifications for Heavy-Duty Operations: These 20 conveyor rollers are built with thick walls and often incorporate reinforced bearings and enhanced axle configurations to withstand heavy impacts and loads.
- Load Capacity and Durability Highlights: High-Durability Rollers are best suited for mining, quarrying, and other heavy industries. They can handle significantly higher loads than standard rollers, with enhanced features that reduce maintenance needs and extend the life cycle of the conveyor system.
Each type of 20-inch conveyor roller is designed to meet specific operational needs, ensuring efficiency and reliability across various industrial applications. By selecting the appropriate type, businesses can optimize their operations and reduce downtime.
Key Specifications and Attributes of 20 Conveyor Roller
When selecting 20 conveyor rollers, it’s important to consider detailed specifications and attributes to ensure optimal performance and longevity. We’ll delve deeper into roller diameter options, axle sizes, material and finish, and load capacity and duty rating, outlining key factors within each category.
Roller Diameter Options
The diameter of the conveyor rollers determines their ability to handle various loads and operate at different speeds.
- Range of Available Diameters: The diameters of 20 conveyor rollers can vary widely, with the larger sizes typically used to support heavier loads and wider conveyor belts.
- Impact on Performance: Larger diameters help distribute the weight of the load more evenly, reducing wear on the conveyor belt and enhancing the system’s overall efficiency.
- Selection Based on Speed: Smaller diameters are better suited for systems that require high-speed operations due to their lower rotational resistance.
- Application-Specific Choices: The choice of diameter often depends on the specific application, with custom diameters available to meet unique industrial requirements.
Axle Sizes
The axle of a conveyor roller is crucial for its installation and operational efficiency.
- Common Hex and Round Axle Sizes: Axles are typically available in various sizes, with the most common being hexagonal for added torque resistance and round for ease of installation.
- Axle Selection Based on Use: The selection of an axle size and shape often depends on the load and the environmental conditions of the conveyor system.
- Customization Options: Axles can be customized in terms of length and diameter to fit specific frames or to meet unique operational requirements.
- Material Choices for Axles: Axles are made from materials like steel for strength or aluminum for lighter weight, depending on the needs of the conveyor system.
Material and Finish
The choice of materials and finishes for 20 conveyor rollers affects their durability and suitability for specific environments.
- Material Options: Options include galvanized steel for corrosion resistance, plain steel for cost-effectiveness, and stainless steel for hygienic environments.
- Finish and Coating Options: Finishes can range from natural to powder coatings, which provide extra protection against wear and corrosion.
- Environmental Suitability: Certain materials and finishes are better suited for harsh environments, such as those with high moisture or chemical exposure.
- Compliance with Regulations: Materials and finishes can also be chosen to comply with industry-specific regulations, such as FDA standards for food processing.
Load Capacity and Duty Rating
Load capacity and duty rating are critical factors in selecting the right conveyor roller to ensure safety and efficiency.
- Determining the Right Roller Based on Load Requirements: It’s crucial to select rollers that can handle the maximum expected load without deformation or failure.
- Impact of Load on Roller Lifespan: Continuous operation at or near the roller’s load capacity can shorten its lifespan, so choosing rollers with a higher capacity than currently needed may be beneficial.
- Dynamic vs. Static Load Ratings: Rollers have both dynamic (moving load) and static (stationary load) ratings, and selecting the right type based on usage is essential.
- Custom Load Ratings: For highly specialized applications, custom-designed rollers can be manufactured to handle specific load types and weights.
Each of these aspects plays a vital role in the efficiency, reliability, and durability of 20-inch conveyor rollers, making careful consideration essential when specifying components for a conveyor system.
How to Measure a 20 Conveyor Roller
Accurately measuring a 20 conveyor roller is crucial for ensuring that the roller fits perfectly within the system and operates efficiently. This guide will provide a detailed step-by-step process to help you measure a conveyor roller precisely, followed by an explanation of why these measurements are vital for both compatibility and performance.
Step-by-Step Guide on Measuring Conveyor Rollers
To measure a 20-inch conveyor roller accurately, follow these detailed steps:
- Gather Tools: Ensure you have a measuring tape, a caliper for detailed measurements, and possibly a notebook to record the dimensions.
- Measure the Overall Length: Measure from one end of the roller to the other to determine the overall length, including the shafts.
- Determine the Roller Diameter: Use the caliper to measure the outside diameter of the roller tube itself, which is critical for sizing the belt or roller frame.
- Check the Shaft Diameter: Measure the diameter of the shafts at both ends of the roller, as this affects the bearing and mount compatibility.
- Verify the Face Length: Measure the length of the tube between the two shafts, which is the actual contact surface for the conveyor belt.
- Assess the Wall Thickness: Using a caliper, check the thickness of the roller wall, which can impact the roller’s load capacity.
- Identify Bearing Size: If accessible, measure the inner diameter of the bearing or bearing housing to ensure replacements fit correctly.
- Examine the Spring Retention: If applicable, measure the size and position of any spring-retention mechanisms used in the roller assembly.
- Record Fitting Types: Note the type of fitting or installation method used (e.g., hexagonal, round), as this will influence how the roller is mounted.
Importance of Precise Measurements for Compatibility and Performance
Accurate measurements are not just a technical necessity; they have broad implications for the performance and longevity of conveyor systems.
- Ensures Compatibility: Proper measurements ensure that the roller fits seamlessly into the conveyor system, preventing operational disruptions.
- Enhances Efficiency: Correctly sized rollers reduce the risk of belt slippage, misalignment, and energy wastage, thus optimizing the conveyor’s efficiency.
- Improves Load Handling: Accurate dimensions help in selecting rollers that can handle the intended load without deforming.
- Reduces Wear and Tear: Properly fitted rollers distribute loads evenly, minimizing wear on both the rollers and the conveyor belt.
- Facilitates Smooth Operation: A well-measured roller promotes smoother operation, reducing vibrations and noise, which can also extend the life of other components.
- Prevents System Downtime: By reducing the likelihood of mechanical failures, precise measurements help avoid costly downtime and repairs.
- Aids in Proper Maintenance: Knowing the exact dimensions of each component helps in maintaining or replacing parts before they fail.
- Supports System Upgrades: Accurate measurements are essential when upgrading parts or expanding a system to ensure new components integrate without issues.
Understanding how to accurately measure a 20 conveyor roller and recognizing the importance of these measurements can greatly impact the functionality and maintenance efficiency of a conveyor system.
Applications and Use Cases of 20 Conveyor Roller
Understanding the various applications and use cases of 20 conveyor rollers highlights their versatility and efficiency across different industrial sectors. Here, we explore how these rollers are particularly beneficial in warehouse and distribution centers, manufacturing and assembly lines, and shipping and receiving departments.
Warehouse and Distribution Centers
In warehouse and distribution environments, 20-inch conveyor rollers play a crucial role in streamlining operations and increasing efficiency.
- Optimizing Material Handling: These rollers are instrumental in moving large volumes of goods quickly and with minimal effort, facilitating faster order processing and turnaround.
- Enhancing Safety: By automating material transport, 20 conveyor rollers reduce the need for manual handling, which decreases the risk of injuries and improves workplace safety.
- Improving Space Utilization: The use of conveyor systems allows for more effective use of space in warehouses, as goods can be transported over, under, and around obstacles, maximizing the use of vertical and horizontal space.
- Scalability and Flexibility: Conveyor systems equipped with 20-inch rollers can be easily expanded or reconfigured as storage and distribution needs change, providing flexibility to adapt to business growth or seasonal fluctuations.
Manufacturing and Assembly Lines
20-inch conveyor rollers are integral to the smooth operation of manufacturing and assembly lines, improving both efficiency and product quality.
- Streamlining Production Processes: These rollers facilitate the smooth movement of parts and products between different stages of production, reducing delays and increasing throughput.
- Reducing Damage and Waste: The gentle handling of goods on these rollers minimizes the risk of damage during movement, thereby reducing waste and improving the quality of the finished product.
- Enhancing Precision: In assembly lines, precise movement and positioning of products are crucial; 20 conveyor roller ensures consistent and accurate positioning, which is essential for automated assembly processes.
- Customization for Specific Needs: Conveyor rollers can be tailored to specific manufacturing requirements, such as resistance to heat, chemicals, or other environmental conditions, ensuring their effectiveness in a wide range of industrial applications.
Shipping and Receiving Departments
In shipping and receiving departments, 20 conveyor rollers are vital for managing the inflow and outflow of goods efficiently and effectively.
- Facilitating Quick Loading and Unloading: These rollers accelerate the process of loading and unloading goods to and from delivery vehicles, reducing wait times and increasing operational efficiency.
- Improving Tracking and Sorting: Conveyor systems can be integrated with sensors and tracking systems that help in sorting and tracking goods as they move through the shipping and receiving areas, ensuring accuracy in order fulfillment.
- Reducing Bottlenecks: Efficient movement of goods on conveyor rollers helps in preventing bottlenecks during peak operation times, which is crucial for maintaining a smooth flow of goods.
- Enhancing Adaptability: The flexibility of these conveyor systems allows them to adapt to various types of cargo, supporting a diverse range of products and packaging sizes without the need for extensive reconfiguration.
The use of 20 conveyor rollers across these key areas not only maximizes operational efficiency but also supports a high level of adaptability and safety, making them a valuable component in modern industrial operations.
Buying Guide for 20 Conveyor Roller
Selecting the right 20 conveyor rollers involves careful consideration of several factors, including whether to buy new or used, where to purchase, and cost considerations. This guide provides detailed advice to help businesses make informed purchasing decisions.
New vs. Used Conveyor Rollers
When deciding between new and used 20 conveyor rollers, understanding the pros and cons of each option is essential. Below is a table comparing these aspects:
Aspect | New Conveyor Rollers | Used Conveyor Rollers |
---|---|---|
Initial Cost | Higher initial investment | More affordable initially |
Longevity | Longer lifespan, less wear | Shorter lifespan, potential for wear |
Reliability | More reliable, come with warranties | Less reliable, typically no warranty |
Maintenance | Lower maintenance needs initially | Potentially higher maintenance costs |
Availability | May require waiting for manufacture and delivery | Often available immediately |
Customization | Can be customized to specific needs | Limited to what's available in the market |
Environmental Impact | Higher due to production processes | Lower, as reusing equipment reduces waste |
Where to Buy 20-Inch Conveyor Rollers
Finding reliable suppliers and platforms for purchasing 20-inch conveyor rollers is crucial, whether new or used:
- Manufacturer Direct Sales: Buying directly from manufacturers like Hytrol, Interroll, or Precision Pulley & Idler offers customization options and full product warranties.
- Industrial Supply Companies: Companies such as Grainger and McMaster-Carr provide a wide range of conveyor rollers, with extensive catalogs and online purchasing options.
- Online Marketplaces: Platforms like Alibaba or Amazon Business can be good sources for both new and used rollers, offering competitive prices and a broad selection.
- Used Equipment Dealers: Specialized in selling used industrial equipment, these dealers can offer significant savings, with outlets such as Surplus Record or EquipNet.
- Local Distributors and Resellers: They often have deep knowledge of their products and can provide additional services like installation and maintenance.
- Trade Shows and Industrial Expos: These events allow direct interaction with suppliers and hands-on examination of products.
- Refurbished Equipment Suppliers: Companies that refurbish rollers can provide a middle ground between new and used, offering repaired and tested rollers at lower costs.
Cost Considerations
Understanding the factors that affect the price of conveyor rollers can help in budgeting and decision-making:
- Material: Rollers made from high-grade materials like stainless steel are more expensive than those made from plastic or carbon steel.
- Size and Load Capacity: Larger rollers and those capable of handling heavier loads typically cost more.
- Customization: Custom features such as special coatings or adaptations for specific environments can add to the cost.
- Quantity: Purchasing in bulk often results in lower per-unit costs.
- Supplier: Costs can vary significantly between suppliers based on their manufacturing process and materials used.
- Shipping and Handling: The cost of transportation and handling can impact the overall price, especially for heavy items like conveyor rollers.
- Market Conditions: Fluctuations in raw material prices or changes in trade policies can affect prices.
Budgeting Tips for Businesses
Efficient budgeting for conveyor rollers involves several strategies to optimize expenditure:
- Assess Total Cost of Ownership: Include maintenance, repair, and potential downtime costs, not just the purchase price.
- Compare Long-Term Benefits vs. Initial Costs: Investing more initially in higher-quality rollers can save money on future replacements and maintenance.
- Seek Bulk Purchase Discounts: Negotiate with suppliers for discounts on large orders.
- Consider Refurbished Options: Explore cost savings with refurbished rollers that still meet operational requirements.
- Plan for Future Needs: Purchase additional rollers during initial buy to reduce future urgent buying at possibly higher prices.
- Monitor Sales and Discounts: Keep an eye on sales, especially during industrial expos or end-of-year clearances.
- Allocate a Contingency Budget: Set aside funds for unexpected expenses related to roller maintenance or replacement.
- Utilize Financial Planning Tools: Tools like ROI calculators can help visualize the long-term benefits of different types of rollers.
This comprehensive buying guide for 20 conveyor roller equips businesses with the necessary information to make well-informed purchasing decisions, optimizing both performance and cost-effectiveness.
FAQs about 20 Conveyor Roller
The standard size of a conveyor roller can vary widely depending on the specific application and industry standards. Generally, conveyor rollers come in a range of diameters and lengths. The most common diameters are between 1.5 inches to 5 inches, but in heavy-duty applications, rollers can be larger, reaching up to 20 inches or more. The length of the roller typically matches the width of the conveyor belt they are designed to support and can vary from a few inches to several feet.
Choosing the right size of conveyor roller is crucial for effective material handling. The roller’s diameter should be suitable for the load it will carry and the speed at which the conveyor will operate. For example, larger diameters are better suited for heavier loads and higher speeds as they reduce the rotation speed and the wear on the bearings. When specifying a conveyor system, it’s important to consult with manufacturers to understand the best roller size options for your specific needs.
The rollers on a conveyor are commonly referred to as “conveyor rollers.” These components are critical for the movement of the conveyor belt or the items being transported on it. Conveyor rollers can be designed to handle various tasks and environments, ranging from lightweight applications, such as transporting small objects in a manufacturing facility, to heavy-duty uses, such as moving large volumes of goods in a warehouse.
There are different types of conveyor rollers, including gravity rollers, driven rollers, impact rollers, and return rollers, each serving distinct functions. For example, gravity rollers move goods through the force of gravity and slight inclinations, while driven rollers are powered by motors or chains to move the conveyor belt. Impact rollers are placed at loading points to absorb shock and reduce damage to the belt from falling items. Return rollers help to support the underside of the belt as it loops back to the beginning of the conveyor system.
Measuring a conveyor roller accurately is essential for ensuring it fits perfectly in the conveyor system and functions as intended. To measure a conveyor roller, you will need tools like a measuring tape or ruler and a caliper for more precise measurements. Here are the steps to measure a conveyor roller:
Overall Length: Measure the length of the roller from one end of the shaft to the other. This is the total length of the roller including the shafts that extend beyond the tube.
Tube Length: Measure the length of the roller tube itself, not including the shafts. This is the part of the roller that actually contacts the conveyor belt.
Diameter: Use a caliper to measure the outside diameter of the roller tube. This dimension is critical as it affects how the roller will interact with the belt and the load.
Shaft Diameter: Measure the diameter of the shaft at each end of the roller, as this affects which bearings and mounting hardware can be used.
Spring Retention: If applicable, note the size and type of any spring retention mechanisms that are part of the roller assembly.
These measurements help in ordering replacements and ensuring compatibility with the conveyor system.
The distance between rollers in a conveyor, often referred to as the roller pitch, is an important design consideration that impacts the conveyor’s ability to transport items smoothly and efficiently. This distance varies based on the size and weight of the items being transported, the type of conveyor, and the specific application.
For light-duty applications, rollers can be spaced further apart, which can be economical as fewer rollers are required. However, for heavier loads or where high stability is necessary, the rollers will be placed closer together to ensure adequate support, preventing the conveyor belt from sagging and ensuring smooth transport of goods.
Typically, the roller pitch can range from as close as 2 inches to as far apart as every 12 inches or more. Engineers and system designers calculate the optimal distance based on load requirements and conveyor speed to ensure performance and durability. For custom applications, consulting with a conveyor specialist or manufacturer is advisable to determine the ideal configuration.
Last Updated on May 17, 2024 by Jordan Smith
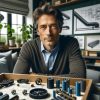
Jordan Smith, a seasoned professional with over 20 years of experience in the conveyor system industry. Jordan’s expertise lies in providing comprehensive solutions for conveyor rollers, belts, and accessories, catering to a wide range of industrial needs. From initial design and configuration to installation and meticulous troubleshooting, Jordan is adept at handling all aspects of conveyor system management. Whether you’re looking to upgrade your production line with efficient conveyor belts, require custom conveyor rollers for specific operations, or need expert advice on selecting the right conveyor accessories for your facility, Jordan is your reliable consultant. For any inquiries or assistance with conveyor system optimization, Jordan is available to share his wealth of knowledge and experience. Feel free to reach out at any time for professional guidance on all matters related to conveyor rollers, belts, and accessories.