Selecting the Perfect Steel Conveyor Rollers for Industrial Needs
What Are Steel Conveyor Rollers?
Defining Steel Conveyor Rollers
Steel conveyor rollers are pivotal components in material handling systems. Below are their defining elements:
- Material Composition: Constructed from high-grade steel, these rollers offer superior strength and can handle heavier loads compared to other materials.
- Design Purpose: They are designed to rotate on a central axle and facilitate the movement of conveyor belts or materials being conveyed.
- Application Context: Steel conveyor rollers are commonly used in environments that require longevity and toughness, such as mining and heavy manufacturing.
The Significance of Steel Conveyor Rollers in Industry
Understanding the importance of steel conveyor rollers within industrial applications involves recognizing their integral roles:
- Operational Efficiency: They provide an effective way to move products and materials, thereby speeding up production and processing times.
- Durability and Load Capacity: Due to the inherent strength of steel, these rollers can handle extreme weights and harsh conditions without significant wear.
- Minimized Downtime: The robust nature of steel rollers means they don’t need frequent replacement or maintenance, preventing delays in operations.
Steel conveyor rollers are essential for any heavy-duty material handling application, ensuring that systems run smoothly and reliably with minimal interruption. Their design and material selection are specifically geared towards meeting the rigorous demands of industrial processing and manufacturing environments.
Advantages of Steel Conveyor Rollers
Durability and Strength for Heavy Loads
Key Points | Details |
---|---|
Inherent Material Strength | Steel has a high tensile strength, providing the ability to endure heavy loads without bending or breaking. |
Resistance to Wear and Tear | The hardness of steel resists scratching, abrasions, and other forms of wear that can reduce functionality over time. |
High Impact Endurance | Steel rollers can tolerate sudden forceful contacts better than materials of lower density and strength. |
Suitability for Various Industrial and Aggregate Applications
Key Points | Details |
---|---|
Versatile Industrial Use | Due to their robustness, steel rollers are suitable for a multitude of industries, including those with harsh operational conditions. |
Adaptability to Conditions | They perform reliably under varying environmental situations, resisting damage from elements like extreme temperatures or corrosive substances. |
Operational Efficiency Enhancement | With the ability to handle large volumes, steel rollers facilitate the quick and smooth processing of materials, enhancing overall workflow efficiency. |
Longevity and Cost-Effectiveness Over Time
When it comes to longevity and cost-effectiveness, let us break down the benefits point-wise:
Key Points | Details |
---|---|
Extended Operational Life | Steel rollers for conveyors usually have a longer lifespan due to the durability and resistance to environmental challenges. |
Cost Savings in the Long Term | The initial investment is mitigated by reduced maintenance needs and fewer replacements compared to less durable materials. |
Consistent Performance | Their ability to maintain performance levels over time means less downtime and more consistent production flow. |
Less Frequent Maintenance | Steel’s resilience means it generally requires less frequent care, reducing maintenance costs and time. |
The prioritized advantages of steel conveyor rollers can be better appreciated by considering these pointed summaries, clearly demonstrating the long-term benefits and cost savings associated with implementing them in material handling solutions.
Material Comparison: Steel Vs. Plastic Conveyor Rollers
In comparison to other conveyor rollers such as those made from plastic, steel conveyor rollers distinctly stand out. Below is a table showcasing the comparison in key aspects:
Material Features | Steel Conveyor Rollers | Plastic Conveyor Rollers |
---|---|---|
Durability | High (due to steel’s inherent strength) | Lower (plastic may deform under heavy loads) |
Load Capacity | High (can handle demanding weight requirements) | Lower (best suited for lighter loads) |
Longevity | Long (can withstand harsh environments over time) | Shorter (may degrade faster under strenuous conditions) |
Cost-Effectiveness | High (initial cost offset by long operation life) | Lower (frequent replacements can increase costs over time) |
Through these main points, we understand the clear benefits and superior attributes of using steel conveyor rollers, especially when analyzed against alternatives like plastic conveyor rollers. These justification factors are specifically important for businesses looking to enhance efficacy while ensuring longevity and cost-effectiveness in their conveyor systems.
Exploring Different Types of Steel Conveyor Rollers
Steel conveyor rollers are integral to various industries due to the benefits derived from their durability, efficiency, and versatility. Understanding the distinction between the different types of conveyor roller steel can assist businesses in selecting the right roller intended for their specific needs. These types can be primarily categorized into standard steel rollers, heavy-duty conveyor rollers, and specialized steel rollers.
Standard Steel Rollers
Standard steel conveyor rollers are the most commonly used type offering consistent, reliable performance for most commercial and light industrial applications.
Key Features:
- Constructed from robust and sturdy steel, these rollers are designed to resist wear and tear over time, thereby providing long-term operation.
- Standard steel conveyor rollers offer smooth and quiet operation, making them a good choice to enhance the efficiency of material handling processes.
- They usually come with adjustable brackets, allowing easy installation and flexibility to fit in various conveyor systems.
Common Uses: They are widely utilized in sectors such as manufacturing, distribution, and packaging, where they perform tasks like sorting, transferring, and moving products or materials along the production line.
Heavy Duty Steel Conveyor Rollers
For businesses dealing with significant weight capacities and rough operational conditions, heavy-duty steel conveyor rollers come to the rescue.
Characteristics and Benefits:
- These rollers are designed with enhanced bearings and a thicker steel casing, ensuring greater load-bearing capabilities and extreme durability.
- Heavy-duty steel roller conveyors are known for their high resilience and longevity, thereby reducing maintenance costs.
- Despite their robustness, they ensure low noise operations and are resistant to rust and corrosion.
Industry Usage: Industries like mining, construction, and farming, which handle heavy loads and harsh conditions, typically require these heavy-duty rollers.
Specialized Steel Rollers
Specialized steel conveyor rollers, such as tapered, grooved, and sprocket rollers, cater to specific applications and accommodation of unique conveyor system requirements.
Details on Variants:
- Tapered Rollers: Designed for curve conveyors, these can easily handle materials transitioning from one conveyor to another in a different direction.
- Grooved Rollers: Preferred choice for handling sacks, bags or any slippery products. The grooves provide extra grip, preventing slippage during transportation.
- Sprocket Rollers: Often used in chain-driven conveyor systems, these rollers are ideal for managing heavy loads at slower speeds.
Custom Solutions: Customized steel conveyor rollers are an excellent choice for unique conveyor system requirements, providing bespoke solutions to cater to specific operational needs.
By considering these variant types of steel conveyor rollers and their significant features, industries can make well-informed decisions about the best fit for their conveyor systems. This understanding saves both time and financial resources while enhancing the overall operation efficiency.
Choosing the Ideal Steel Conveyor Rollers for Your System
Selecting the most suitable steel conveyor rollers is a decision integral to the efficiency, durability, and success of a conveyor system. These decisions hinge on understanding the specifics of the application, including the types of materials to be conveyed, the environment in which they will operate, and the expected performance. Here, we delve into the important factors like diameter considerations, load capacity, and the price-quality ratio that significantly affect the selection process.
Diameter Considerations
The diameter of steel conveyor rollers is a critical factor to consider, as it directly influences the conveyor system’s performance and longevity.
- Choosing the Right Diameter: The selection between 4-inch, 6-inch, and 1-inch diameter rollers is based on the size of the materials being conveyed and the overall design of the conveyor system. Larger diameter rollers are generally used for heavier loads and larger items, as they offer greater stability and reduced rotation speed, which can prolong the life of the bearing.
- Impact on Performance: The diameter of steel conveyor rollers affects the system’s speed and the minimal size of objects that can be reliably conveyed. For example, smaller diameter rollers are beneficial for high-speed operations and small items, ensuring a smooth transition over the conveyor belt.
Load Capacity
Understanding and choosing the right load capacity for steel conveyor rollers is crucial for maintaining system integrity and efficiency.
- Importance of Appropriate Load Capacity: Rollers selected must match or exceed the maximum weight load they will carry. Utilizing rollers with a capacity less than what is needed can lead to premature failure and downtime.
- Influence on Longevity and Efficiency: Selecting steel conveyor rollers with the correct load capacity ensures the system operates within its design parameters, reducing wear and tear and thereby extending the life of not only the rollers but also the conveyor system itself.
Price and Quality
The price of steel conveyor rollers can be indicative of their quality, but savvy buyers know to look deeper into the value offered.
- Price Influencing Factors: The cost of steel conveyor rollers is often reflective of the materials used, the manufacturing precision, and the load-bearing capacity. Rollers designed for heavy-duty applications, or those crafted with superior-grade steel, often come at a higher price point.
- Balancing Price, Quality, and Value: While the initial price is an important consideration, assessing the long-term value is paramount. High-quality steel conveyor rollers might demand a higher upfront investment but can lead to lower maintenance costs, fewer replacements, and overall better performance over time. Thus, it’s advisable to consider the total ownership cost rather than just the purchase price.
When choosing steel conveyor rollers, taking these detailed considerations into account will ensure that the selected rollers meet the demands of your application, providing a balance between initial investment and long-term operational benefits. Remember, selecting the right rollers is not just about prices; it’s about ensuring your conveyor system runs efficiently, safely, and economically over its lifetime.
Best Steel for Rollers: Considerations for Different Applications
Selecting the most suitable steel for rollers involves careful consideration of factors such as load capacity, environmental conditions, and the specific application area. Different types of steel are better suited to various roller applications. Here are insights into the best steel types for different roller applications:
Carbon Steel
- Ideal for general industrial applications.
- Good strength and durability.
- Economical choice.
- Suitable for medium loads and typical working environments.
Alloy Steel
- Enhanced performance due to alloying elements like chromium, nickel, and molybdenum.
- Suitable for applications requiring higher strength and corrosion resistance.
- Used in offshore equipment or high-temperature environments.
Stainless Steel
- Known for its corrosion resistance.
- Appropriate for rollers exposed to moisture or corrosive environments, e.g., food processing equipment or chemical plants.
- Suitable for outdoor applications due to its resistance to rust.
Heat-Treated Steel
- Subjected to heat treatment to increase hardness and strength.
- Ideal for applications demanding exceptional wear resistance, such as grinding mills and mining equipment.
Chrome Steel
- Excellent for manufacturing bearings and high-speed rollers.
- Features smooth surface finish and wear resistance.
- Suitable for applications involving high-speed rotation.
When choosing steel for rollers, it is crucial to factor in specific application conditions such as temperature, humidity, exposure to chemicals, and operating speeds. The optimal choice depends on the combined impact of these factors.
Effective Steel Conveyor Roller Maintenance and Replacement Strategies
The upkeep of steel conveyor rollers is critical to the smooth operation of conveyor systems. Regular and proper maintenance can significantly extend the life and performance of these rollers while reducing the risk of unexpected system failure. Likewise, recognizing when to replace steel conveyor rollers is equally important to maintain efficiency and prevent extensive downtimes. Below are essential maintenance tips and replacement pointers that ensure that the steel conveyor rollers remain in top-notch condition.
Maintenance Tips for Steel Conveyor Rollers
Proactive maintenance of steel conveyor rollers includes a set of routine procedures designed to keep the system running efficiently and to preemptively address issues that could lead to breakdowns.
Routine Maintenance Procedures:
- Cleaning steel rollers to remove dirt, debris, and buildup that can cause drag and increase the wear on the system.
- Lubricating bearings and checking seals regularly, as poorly lubricated components can result in increased friction and potential failures.
- Ensuring proper alignment of the rollers to prevent uneven wear and tear and to make sure the conveyor belt runs smoothly.
Significance of Regular Inspections:
- Implementing a scheduled inspection routine is crucial for early detection of potential issues, such as minor damages or wear, before they evolve into major problems.
- Regular checks on load capacity, roller spin, and the accumulation of residues will help in maintaining the optimal functionality of the steel conveyor rollers and can substantially prevent downtimes.
Replacing Steel Conveyor Rollers
Recognizing the signs of wear and tear and understanding the proper method of replacement will ensure minimal interruption to operations and the longevity of the conveyor system.
Signs Indicating Replacement:
- Visible damage on the roller surface such as dents, cracks, or corrosion can be clear indicators that it’s time to replace steel conveyor rollers.
- A consistent and unusual noise or vibrations coming from the rollers is often symptomatic of underlying issues like bearing failure.
- A decrease in performance, such as the conveyor system struggling to move smoothly or at the usual speed, may suggest that some rollers need replacement.
Efficiency in Replacement:
- Preparing the correct tools and having replacement rollers readily available can significantly reduce the time required for the operation.
Training maintenance personnel on the specific procedures for roller removal and installation to ensure that replacements are done swiftly and correctly. - Establishing a replacement log to keep track of maintenance history, thus, predicting future replacement needs and scheduling downtime in a controlled and strategic manner.
Understanding the critical role of steel conveyor rollers within material handling processes underscores the importance of adept maintenance and timely replacement. By adhering to regular inspection and maintenance schedules and being vigilant for signs of wear, businesses can ensure the continued reliability and efficiency of their conveyor systems.
Preventing Failures
Proper maintenance practices are essential to prevent failures and extend the lifespan of steel rollers. Here are some common reasons why steel rollers may fail and how to prevent these failures:
- Lack of Lubrication: Inadequate lubrication is a top cause of roller failure, ensure proper lubrication as per manufacturer’s guidelines for rollers with bearings. Regularly inspect and replenish lubricants as needed.
- Contaminants and Debris: Dust, dirt, and foreign particles can accumulate on roller surfaces and within bearings, leading to increased friction and wear. Implement a cleaning schedule to remove contaminants and maintain a clean working environment.
- Misalignment: Misalignment of rollers can cause uneven wear and increased stress on the rollers, resulting in premature failure. Regularly check for proper alignment and make necessary adjustments to ensure that rollers are in line with each other.
- Overloading: Exceeding the load capacity of steel rollers can lead to deformation, bearing damage, and roller failure. Always adhere to load capacity guidelines and avoid overloading rollers.
- Corrosion: For steel rollers used in corrosive environments, corrosion can compromise their integrity. Select appropriate corrosion-resistant coatings or stainless steel rollers for such applications.
- Improper Installation: Incorrect installation can cause stress concentrations or uneven loading on rollers. Follow the manufacturer’s installation guidelines carefully, ensuring that rollers are mounted securely and aligned correctly.
Troubleshooting Tips
When issues with steel rollers arise, it’s essential to troubleshoot and address the problem promptly. Here are some basic troubleshooting tips for common issues encountered with steel rollers:
- Excessive Noise: If rollers are producing unusual noise during operation, it may indicate bearing problems or misalignment. Inspect the bearings for damage and ensure proper alignment.
- Uneven Wear: Uneven wear patterns on roller surfaces can result from misalignment, overloading, or inadequate lubrication. Correct the underlying issue and replace any heavily worn rollers.
- Sticking or Jamming: If rollers become stuck or jammed, check for debris or contaminants on the roller surfaces or in the bearings. Clean and lubricate the rollers as needed.
- Vibration: Excessive vibration may indicate misalignment, unbalanced loads, or roller damage. Inspect for misalignment and uneven loading, and replace any damaged rollers.
- Bearing Issues: If you suspect bearing problems, such as overheating or increased friction, inspect the bearings for wear or damage and replace them if necessary. Ensure proper lubrication.
- Roller Damage: In the event of physical damage to a roller, such as dents or bends, replace the damaged roller to maintain smooth operation and prevent further issues.
- Excessive Heat: Overheating of rollers can indicate issues with load distribution, friction, or inadequate lubrication. Investigate the root cause and address it to prevent roller damage.
- Abrasion and Wear: Regularly monitor the condition of roller surfaces for signs of abrasion and wear. Replace rollers that have reached the end of their service life.
Regular inspections, maintenance routines, and prompt resolution of issues are key to ensuring the reliable and efficient operation of steel rollers. By addressing these common failure causes and following troubleshooting guidelines, you can minimize downtime and extend the lifespan of your steel rollers.
Identifying the Ideal Steel Conveyor Roller Manufacturer and Supplier
Choosing the right manufacturer and supplier for steel conveyor rollers is paramount to ensuring the efficiency, reliability, and longevity of your conveyor system. This decision can impact not only the upfront cost but also the long-term maintenance, downtime, and operational efficiency. Below, we outline key considerations when selecting steel conveyor roller manufacturers, provide an overview of top manufacturers, and offer guidance on the purchasing process.
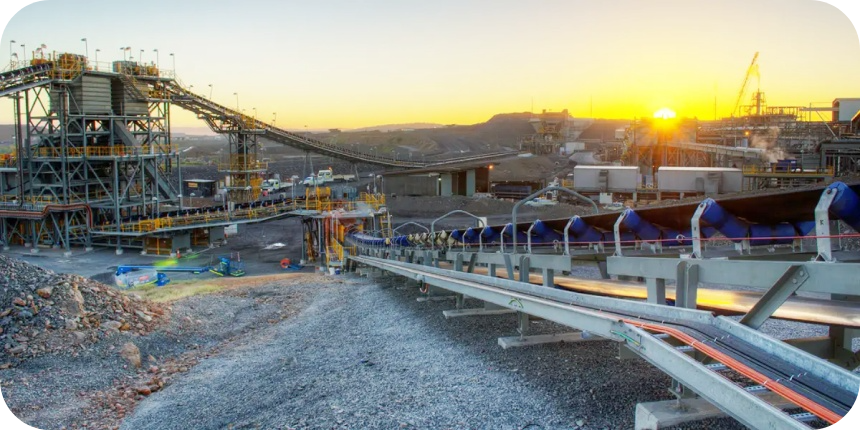
Steel Conveyor Roller Manufacturers
Selecting a reputable manufacturer involves evaluating a range of criteria to ensure you receive high-quality products that meet your specific needs.
Criteria for Selection:
- Quality and Consistency: The manufacturer’s ability to provide high-quality and consistent steel conveyor rollers should be verifiable through certifications, customer feedback, and product warranties.
- Experience and Reputation: Companies with a long-standing presence in the market often have a track record that can be reviewed for reliability, innovation, and customer satisfaction.
- Customization and Support: The capability to offer customized solutions and proactive support services is crucial for addressing unique operational challenges and ensuring system longevity.
Leading Manufacturers Overview:
Manufacturer | Advantages | Disadvantages |
---|---|---|
Interroll Group | – Globally recognized brand – Wide range of high-quality rollers – Strong focus on research and development | – Premium pricing – May be overengineered for simple applications |
Precision Pulley & Idler (PPI) | – Extensive customization options – Excellent customer support – Strong presence in heavy-duty industries | – Higher cost relative to some competitors – Limited global distribution in certain regions |
Rexnord Industries, LLC | – Diverse product lineup catering to different industries – Innovative solutions like digital monitoring – Robust global distribution network | – Complexity in the selection process due to vast product range – Sometimes focuses more on complete systems than on individual components |
Gram Conveyor | Gram Conveyor is a modern and innovative company, that offers cutting-edge solutions, incorporating the latest technology in steel conveyor rollers. | Depending on their manufacturing capabilities and scale, there could be longer lead times for custom orders or large quantities. |
Evaluating the advantages and disadvantages of different steel conveyor roller manufacturers is essential to making an informed decision that aligns with both operational needs and budget constraints.
Buying Guide
The process of purchasing steel conveyor rollers involves several considerations to ensure that you obtain the best value and performance.
Tips for Purchasing:
- Assess the specific needs of your conveyor system, including load capacity, roller size, and material compatibility.
- Request quotes from multiple suppliers to compare pricing, availability, and lead times.
- Prioritize manufacturers and suppliers that offer post-purchase support, including maintenance guides and technical assistance.
Online vs. Offline Purchasing Considerations:
- Online:
- Offers convenience and the ability to quickly compare different suppliers.
- The availability of customer reviews and ratings can provide additional insights.
- Some challenges may include the difficulty in verifying product quality and the potential for longer lead times due to shipping.
- Offline:
- Enables direct inspection of products and immediate purchase of available stock.
- Allows for personal interaction with the supplier, potentially leading to better customization and support services.
- May involve more time to visit suppliers and compare options manually.
Making an informed decision on purchasing steel conveyor rollers requires careful consideration of how and where to buy them. Whether online or offline, understanding your system’s specific needs, along with thorough manufacturer evaluation, is key to finding reliable and efficient steel conveyor rollers.
How Steel Conveyor Rollers Work
The function and operation of steel conveyor rollers are foundational to numerous industries worldwide, facilitating the smooth and efficient movement of goods across various distances and environments. Let’s delve into the mechanism and efficiency of these critical components, shedding light on why they are the backbone of modern material handling and logistics.
Mechanism Explained
Steel conveyor rollers operate on a relatively straightforward but ingenious principle. These cylindrical components are mounted within the frame of a conveyor belt system. As the conveyor belt moves, either manually, by gravity, or powered by motors, the steel conveyor rollers underneath rotate, allowing goods to glide over them with minimal friction.
- Structure: The typical steel conveyor roller consists of a steel tube mounted on a shaft, with bearings at either end to facilitate smooth rotation. The materials and design specifications can vary depending on the application, including factors like load capacity and environmental conditions.
- Operation: In powered conveyor systems, motors drive the belt, causing the steel conveyor rollers to rotate and propel items forward. In gravity-fed systems, the rollers spin as items move down the conveyor’s slight decline.
- Advantages: Steel, as a material, offers durability and strength, making these rollers suitable for heavy loads and industrial environments. The simplicity of the mechanism ensures reliability and low maintenance.
- Load Distribution: The cylindrical shape of a steel roller evenly distributes loads over a larger surface, reducing pressure on conveyed materials and minimizing the risk of damage or deformation.
- Reduced Friction: Steel rollers reduce friction between their surface and materials they contact, providing a smooth, low-friction surface that eases the movement of objects, requiring less force for pushing or pulling.
- Rolling Motion: As a load is applied to the roller, it rotates around its axis. This rolling motion, enabled by the cylindrical shape of the roller, offers a significant advantage over sliding, which would result in much higher friction. The rolling action of the steel roller makes it easier to transport heavy or bulky items.
- Bearings: Many steel rollers incorporate bearings, such as ball bearings or roller bearings, which further reduce friction and allow for smooth, efficient rotation. Bearings also help maintain the integrity of the roller’s structure over time.
- Alignment and Support: Steel rollers are typically mounted within a framework or system that aligns and supports them properly. This alignment ensures that the rollers work together seamlessly to transport materials without skewing or misalignment issues.
Efficiency in Operation
The efficiency of steel conveyor rollers is not accidental but the result of careful engineering and design, focusing on reducing operational costs and maximizing productivity.
- High Load Capacity: Steel’s inherent strength enables these rollers to support heavier weights without deformation. This capacity for handling heavy loads without compromise ensures that even bulky or large items can be transported efficiently.
- Durability and Longevity: Steel conveyor rollers are highly resistant to wear and tear, thanks to the robustness of the material. This durability means that they require less frequent replacement and can operate in harsh conditions without significant degradation, ensuring continued operational efficiency over time.
- Material Handling: Steel rollers are commonly used in conveyor systems, where they play a crucial role in efficiently moving materials from one point to another. Their low-friction properties make it easier to transport heavy loads, reducing the effort required and increasing productivity.
- Manufacturing Processes: In manufacturing settings, steel rollers are often used in equipment like metal rolling mills and sheet metal forming machines. They ensure precise and consistent material shaping while reducing wear and tear on the machinery.
- Industrial Automation: Steel rollers are key components in automated systems, such as robotic assembly lines and packaging machinery. Their smooth operation contributes to the reliability and speed of these processes.
- Material Processing: Steel rollers are used in various material processing applications, including printing, paper production, and textile manufacturing, where they assist in the precise movement and tensioning of materials.
- Transportation Industry: Steel rollers are used in systems such as roller conveyors at airports and distribution centers, enabling the efficient movement of luggage and packages.
Incorporating steel conveyor rollers into material handling systems offers a blend of mechanical simplicity and advanced efficiency. By understanding these mechanisms and the principles behind their operation, industries can optimize their conveyor systems for better performance, durability, and cost-effectiveness. Whether for small operations or large-scale industrial applications, steel conveyor rollers remain a critical component in the seamless movement of goods across the globe.
CONTACT US
Let us help you find a better solution!
Most Popular Steel Conveyor Roller for Sale in Gram Conveyor
1.5″ Diameter Steel Conveyor Roller – 13.8″ Long for Transporting Such as Foating Fishing Boats, Kayaks, Rafts and so on
- Heavy-Duty Construction
- Easy Disassembly
- Two-Hole Galvanized Bracke
1.5’’ Diameter Steel Conveyor Roller, Easy to Install Industrial Metal
- Large Deal
- Ideally Sized for All Your Needs
- Spring Loaded for Heavy Goods Transport
- Elegant Silver Finish
- Versatile Applications
10″ Long Steel Conveyor Roller 1.5″ Diameter Industrial Use,Easy Install Reliable & Sturdy for Your Conveyor Needs
- Smooth Sliding
- Easy Installation
- Superior Performance
- Durable Affordable Solution
- Enhance Safety
10″BF Length 1.5″ Dia Galvanized Steel Conveyor Roller
- Diameter (Ø) 1.5 inch
- Length 10″ Between Frame (BF)
- Easy maintenance and low downtime with a spring-loaded mechanism for quick installation and disassembly of your roller conveyor system.
10 Inches Long Steel Conveyor Roller, for Conveying All Kinds of Goods and Heavy Objects
- Premium Roller, Is Strong and Durable, And Has a Beautiful Appearance.
- Easy to Disassemble and Install
- Easily Transport Your Own Goods, Save a Lot of Effort.
16″ Long Steel Conveyor Roller 1.5″ Diameter, Industrial Use, Easy Install, Reliable & Sturdy for Your Conveyor Needs
- Effortlessly Glide Bulk Materials, Bulk Products, And Inventory with Ease.
- Easy Installation: Quick and Hassle-Free Installation.
- Roller Capable of Handling up to 100 Lbs
- Ideal for DIY Enthusiasts, Contractors, Woodworking, And Industrial Users.
22” Long Steel Conveyor Roller,1.5” Dia.
- Create Infeed Tables for Woodworking Material Handling Solutions and Other Industrial Applications
- Temperature-Rated for Operation Within -80°f to 200°f (-62°c to 93°c)
36″ Galvanized Steel Conveyor Roller: Premium Conveyor Rollers for Roller Conveyors, Woodworking Stands
- Versatile Loading Solution
- Heavy-Duty Performance
- Precise Bracket Specifications
- Durable Roller Design
- Optimal Length and Durability
Heavy Duty 15″ Galvanized Steel Conveyor Roller Set- 250lb Load Capacity
- Improve Workspace Efficiency
- Durable Galvanized Steel Construction
- Easy Installation with Spring-Loaded Design
- Secure and Stable Bracket
- Reliable 250-Pound Capacity
FAQs about Steel Conveyor Rollers
Why are rollers called rollers?
Rollers are called rollers because they rotate to move, support, or shape materials in industrial processes. The term “roller” stems from their rolling motion, which is essential in heavy industries such as mining, construction, and manufacturing. In these sectors, rollers facilitate the transportation of heavy loads, the compaction of materials, and the formation of products through processes like rolling mills. Their design and function are crucial for efficiency and productivity, providing smooth and controlled movement of raw materials and finished products.
How do l choose the right roller?
Choosing the right roller involves considering factors like load capacity, material compatibility, and operating environment. In heavy industries like mining, it’s essential to select rollers that can withstand high stress, abrasive materials, and harsh conditions. Key criteria include the roller’s diameter, width, and surface material, which should match the specific application requirements. For instance, steel rollers are suitable for heavy loads and abrasive materials, while rubber-coated rollers offer better grip and reduced wear for lighter loads. Consulting with suppliers and understanding the operational demands ensures optimal performance and longevity.
What are the three types of drive rolls?
The three types of drive rolls are pinch rolls, nip rolls, and tension rolls. In heavy industries, these rolls play vital roles in material handling and processing. Pinch rolls apply pressure to control material flow, essential in rolling mills. Nip rolls, often used in pairs, grip materials to ensure smooth feeding and precise alignment. Tension rolls maintain consistent tension in the material, preventing slack and ensuring uniform processing. Each type is designed to meet specific operational needs, enhancing efficiency and product quality in demanding environments like mining and metalworking.
What are the 3 different groove shapes for drive rollers?
The three different groove shapes for drive rollers are V-groove, U-groove, and flat groove. In industrial applications, these groove shapes ensure secure and precise material handling. V-groove rollers provide a strong grip for materials with a matching profile, ideal for guiding and aligning. U-groove rollers offer versatility, accommodating a variety of shapes while maintaining stability. Flat groove rollers are suitable for flat surfaces, ensuring even pressure distribution. Selecting the appropriate groove shape enhances the roller’s performance, reduces slippage, and improves the accuracy of material movement in heavy-duty operations.
What is the difference between track rollers and carrier rollers?
The three different groove shapes for drive rollers are V-groove, U-groove, and flat groove. In industrial applications, these groove shapes ensure secure and precise material handling. V-groove rollers provide a strong grip for materials with a matching profile, ideal for guiding and aligning. U-groove rollers offer versatility, accommodating a variety of shapes while maintaining stability. Flat groove rollers are suitable for flat surfaces, ensuring even pressure distribution. Selecting the appropriate groove shape enhances the roller’s performance, reduces slippage, and improves the accuracy of material movement in heavy-duty operations.
What are the classification of rollers?
Rollers in heavy industries are classified based on their function and application. The primary types include drive rollers, idler rollers, and impact rollers. Drive rollers are powered to move materials along a conveyor system, providing the necessary force for material transport. Idler rollers support the conveyor belt and material load without direct power, ensuring smooth and efficient operation. Impact rollers are designed to absorb shock and reduce wear in areas where heavy or abrasive materials are loaded onto the conveyor. Additionally, specialized rollers like return rollers and guide rollers enhance system stability and alignment in mining and construction applications.
What is the most common type of conveyor?
The most common type of conveyor in heavy industries like mining and construction is the belt conveyor. Belt conveyors are versatile, efficient, and capable of handling a wide range of materials, from bulk solids to individual items. They consist of a continuous belt that moves over rollers and pulleys, driven by an electric motor. Belt conveyors are favored for their ability to transport materials over long distances, at varying inclines, and with minimal maintenance. Their design allows for easy integration into existing systems, making them indispensable for material handling in demanding environments such as mines and quarries.
How are conveyor rollers measured?
Conveyor rollers are measured by their diameter, length, and shaft size, critical for ensuring proper fit and function in heavy-duty applications. The diameter of the roller affects the conveyor’s load capacity and speed, with larger diameters providing higher load capacity. Length is measured from end to end, ensuring it matches the conveyor frame width for proper support and alignment. Shaft size, including diameter and length, is essential for compatibility with the conveyor’s mounting brackets and drive system. Precise measurement of these dimensions ensures optimal performance, reduces wear, and extends the lifespan of the conveyor system in industrial settings.
What is the purpose of rolling steel?
Metal rollers work by rotating to move, shape, or support materials in various industrial processes. In conveyor systems, metal rollers facilitate the movement of materials along the belt, reducing friction and ensuring smooth transport. In rolling mills, metal rollers shape and form metals by applying pressure as the material passes through them. The rollers can be powered or idler, depending on whether they drive the process or support it. Precision engineering and material properties of the rollers are crucial for achieving the desired outcomes, ensuring efficiency, and maintaining product quality in heavy industries.
Why use conveyor rollers?
Conveyor rollers are used to facilitate the smooth and efficient movement of materials along a conveyor system in heavy industries such as mining and construction. They support the conveyor belt and the load it carries, reducing friction and ensuring consistent transport of materials. Conveyor rollers are crucial for maintaining the alignment and stability of the conveyor belt, preventing spillage and minimizing wear and tear. Their use enhances operational efficiency, increases productivity, and reduces maintenance costs by ensuring reliable material handling, even in harsh and abrasive environments.
What is the purpose of the steel roll?
The purpose of the steel roll is to shape and form steel into desired profiles through the rolling process. In heavy industries, steel rolls are essential for producing beams, bars, plates, and other structural components. They are used in rolling mills where heated steel is passed through a series of rolls to achieve specific dimensions and surface finishes. This process improves the mechanical properties of the steel, such as strength and ductility, making it suitable for construction, machinery, and infrastructure projects. Steel rolls ensure uniformity and precision in the final products, meeting industry standards and specifications.
What is the danger you need to consider when using the metal rollers?
When using metal rollers in heavy industries, several dangers must be considered to ensure safety. The primary risks include crushing injuries from the rotating rollers, entanglement in moving parts, and severe cuts from sharp edges. Additionally, there is the danger of flying debris if the rollers are handling abrasive materials. Ensuring proper guarding around the rollers, implementing safety protocols, and providing adequate training for operators are crucial measures to mitigate these risks. Regular maintenance and inspection of the rollers are also essential to prevent mechanical failures that could lead to accidents.
What is the difference between steel and rubber rollers?
Steel and rubber rollers differ significantly in their material properties and applications. Steel rollers are highly durable and capable of withstanding heavy loads and abrasive materials, making them ideal for mining and construction applications. They provide high precision and strength, essential for shaping and transporting heavy materials. Rubber rollers, on the other hand, offer better shock absorption and grip, making them suitable for handling delicate or lightweight materials. Rubber rollers reduce noise and vibration, providing a smoother operation. The choice between steel and rubber rollers depends on the specific requirements of the application, including load capacity, material type, and environmental conditions.
Are nylon rollers better than steel?
Steel and rubber rollers differ significantly in their material properties and applications. Steel rollers are highly durable and capable of withstanding heavy loads and abrasive materials, making them ideal for mining and construction applications. They provide high precision and strength, essential for shaping and transporting heavy materials. Rubber rollers, on the other hand, offer better shock absorption and grip, making them suitable for handling delicate or lightweight materials. Rubber rollers reduce noise and vibration, providing a smoother operation. The choice between steel and rubber rollers depends on the specific requirements of the application, including load capacity, material type, and environmental conditions.
How do metal rollers work?
Metal rollers work by rotating to move, shape, or support materials in various industrial processes. In conveyor systems, metal rollers facilitate the movement of materials along the belt, reducing friction and ensuring smooth transport. In rolling mills, metal rollers shape and form metals by applying pressure as the material passes through them. The rollers can be powered or idler, depending on whether they drive the process or support it. Precision engineering and material properties of the rollers are crucial for achieving the desired outcomes, ensuring efficiency, and maintaining product quality in heavy industries.
What is a metal roller called?
A metal roller is commonly called a roller or a rolling mill roll, depending on its specific function in industrial processes. In conveyor systems, it is simply referred to as a roller or conveyor roller. In rolling mills, where metals are shaped and formed, it is often called a rolling mill roll or simply a roll. These rolls are integral components in processes like hot and cold rolling, where they help transform raw metal into finished products with precise dimensions and improved mechanical properties. The terminology may vary slightly based on the industry and specific application.