Conveyor Idler Alignment: Troubleshooting Misalignment Issues
Proper conveyor idler alignment is crucial for the efficient operation of conveyor systems. This process ensures that the conveyor belt runs smoothly and remains centered, preventing misalignment that can lead to significant wear and tear, increased maintenance costs, and potential safety hazards. Conveyor idlers are essential components that support the conveyor belt and its load, helping to distribute the weight evenly and maintain the belt’s alignment. By understanding and implementing correct conveyor idler alignment, businesses can enhance the longevity of their conveyor systems, reduce downtime, and improve overall productivity. This blog post will explore the key aspects and benefits of proper conveyor idler alignment.
Importance of Conveyor Idler Alignment
Conveyor idler alignment is a critical aspect of maintaining the efficiency, cost-effectiveness, and safety of conveyor systems. Proper alignment ensures that the conveyor belt runs smoothly and remains centered, which has numerous benefits for the overall operation of the system. This section will delve into the specific advantages of proper conveyor idler alignment, including enhanced efficiency, cost reduction, and improved safety.
Enhanced Efficiency
Proper conveyor idler alignment significantly enhances the efficiency of a conveyor system. When idlers are correctly aligned, the conveyor belt is kept on track, minimizing the risk of it wandering or becoming misaligned. This alignment reduces friction and wear on the belt and other components, allowing the system to operate smoothly and with less resistance. The direct benefits of enhanced efficiency through proper conveyor idler alignment include:
- Optimized Belt Tracking: Correctly aligned idlers ensure that the conveyor belt tracks properly, reducing the likelihood of belt drift. This not only extends the life of the belt but also ensures that the material being conveyed is transported accurately and efficiently.
- Reduced Energy Consumption: When the conveyor belt runs smoothly without unnecessary friction or resistance, the system requires less energy to operate. This reduction in energy consumption leads to lower operational costs and a smaller environmental footprint.
- Increased Throughput: Efficient belt tracking and reduced downtime due to misalignment issues allow the conveyor system to handle more material in less time. This increase in throughput can significantly boost productivity and overall operational efficiency.
Cost Reduction
Proper conveyor idler alignment is also a cost-effective measure that can lead to substantial savings in maintenance and operational expenses. The alignment of idlers plays a crucial role in extending the lifespan of conveyor components and reducing the frequency of repairs and replacements. Key points on cost reduction through proper conveyor idler alignment include:
- Extended Component Lifespan: Misaligned idlers can cause uneven wear and tear on the conveyor belt and other components, leading to premature failure. Proper alignment ensures that the belt and idlers wear evenly, thereby extending their usable life and reducing the need for frequent replacements.
- Lower Maintenance Costs: Regularly aligned idlers reduce the risk of unexpected breakdowns and the associated downtime. By minimizing the incidence of malfunctions, maintenance schedules can be better planned and managed, leading to lower maintenance costs and more predictable operational budgets.
- Reduced Downtime: Conveyor systems with properly aligned idlers experience fewer interruptions due to belt misalignment issues. This reduction in downtime translates directly into increased production time and, consequently, higher revenue.
Safety
Safety is paramount in any industrial setting, and proper conveyor idler alignment contributes significantly to maintaining a safe working environment. Misaligned belts can pose serious safety hazards, including the risk of belt slippage, material spillage, and even catastrophic system failures. Ensuring proper conveyor idler alignment enhances safety in several ways:
- Prevention of Belt Misalignment: Misaligned belts can lead to various safety issues, such as belt slippage, which can cause material to spill and create hazardous conditions. Proper alignment helps prevent these issues, ensuring the belt remains on track and operates smoothly.
- Reduction of Fire Hazards: Excessive friction caused by misaligned idlers can generate heat, which in turn increases the risk of fires, especially in environments where flammable materials are present. Proper alignment reduces friction and minimizes the risk of overheating and fire hazards.
- Improved Operational Safety: A conveyor system with properly aligned idlers operates more predictably and reliably, reducing the likelihood of unexpected failures that could endanger workers. This reliability contributes to a safer working environment and enhances overall operational safety.
- Compliance with Safety Regulations: Many industrial safety standards and regulations require that conveyor systems be maintained in good working order, including ensuring proper idler alignment. Adhering to these regulations not only keeps workers safe but also helps avoid legal liabilities and potential fines.
The importance of conveyor idler alignment cannot be overstated. It is a fundamental aspect of conveyor system maintenance that enhances efficiency, reduces costs, and significantly improves safety. By ensuring that idlers are properly aligned, businesses can optimize their conveyor operations, extend the lifespan of their equipment, and maintain a safe working environment. Regular inspections and maintenance of conveyor idlers are essential practices that should be integrated into the routine upkeep of any conveyor system to reap these substantial benefits. Proper conveyor idler alignment is not just a technical requirement but a critical factor in achieving operational excellence and sustainability in industrial operations.
Tools and Equipment for Conveyor Idler Alignment
Achieving precise conveyor idler alignment is essential for the smooth operation and longevity of a conveyor system. Proper alignment not only enhances efficiency but also reduces maintenance costs and improves safety. To ensure accurate alignment, specific tools and equipment are required. This section will detail the essential tools used in conveyor idler alignment, including the surveyor’s transit, carpenter’s level, and other additional tools like chalk lines, tape measures, plumb bobs, and rigid steel.
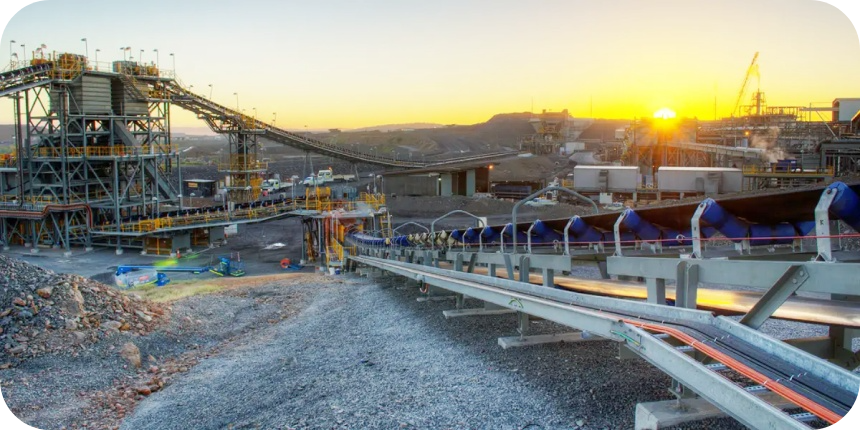
Surveyor’s Transit
A surveyor’s transit is an indispensable tool for achieving accurate conveyor idler alignment. This instrument, used by surveyors to measure horizontal and vertical angles, ensures that the conveyor idlers are aligned precisely.
- Usage for Accurate Alignment: The surveyor’s transit helps establish straight and level lines, which are crucial for aligning the idlers correctly. By setting up the transit at strategic points along the conveyor, technicians can sight along the length of the conveyor to ensure that the idlers are positioned in a straight line.
- Setting Up the Transit: Proper setup of the surveyor’s transit involves placing it on a stable, level surface. The instrument must be calibrated and leveled using its built-in leveling screws and bubble levels. Once set up, the transit can be rotated to sight along the conveyor path.
- Marking Reference Points: Using the transit, technicians can mark reference points along the conveyor frame. These points serve as guides for placing and adjusting the idlers. Ensuring that these reference points are accurate is critical for maintaining the alignment of the entire system.
Carpenter’s Level
A carpenter’s level is another essential tool for ensuring that conveyor idlers are aligned correctly. This simple yet effective tool helps in verifying that the idlers and other components are perfectly level.
- Ensuring Level Alignment: The carpenter’s level is used to check that the idlers are not tilted or uneven. By placing the level on the idler frames, technicians can adjust the idlers until they are perfectly horizontal.
- Checking Multiple Axes: For comprehensive alignment, it’s important to check the level in multiple directions – both along the length and width of the conveyor. This ensures that the idlers are not only level from end to end but also from side to side.
- Adjustments: If the level indicates that an idler is not properly aligned, adjustments can be made by tightening or loosening bolts and repositioning the idler until the bubble in the level’s vial is centered.
Additional Tools
In addition to the surveyor’s transit and carpenter’s level, several other tools are crucial for precise conveyor idler alignment. These include a chalk line, tape measure, plumb bob, and rigid steel.
- Chalk Line: A chalk line is used to create straight reference lines on the conveyor frame. This tool consists of a string coated with chalk powder that can be stretched and snapped to leave a visible line. These lines serve as guides for placing the idlers accurately along the conveyor’s length.
- Tape Measure: A tape measure is essential for taking precise measurements of distances and ensuring that idlers are spaced correctly. It helps in verifying that the idlers are positioned at equal intervals and that the overall layout of the conveyor system is correct.
- Plumb Bob: A plumb bob is a weight suspended from a string, used to establish a vertical reference line. This tool is particularly useful for ensuring that the idlers are aligned vertically, preventing any tilt that could cause belt misalignment.
- Rigid Steel (2 x 2 Box Tubing or Angle Iron): Rigid steel pieces, such as 2 x 2 box tubing or angle iron, are used as straight edges to verify the alignment of the idlers. By placing these steel pieces along the idlers, technicians can visually and physically check for any deviations from the straight line.
Using the Tools in Combination
The combination of these tools ensures comprehensive and accurate conveyor idler alignment. Here’s how they work together:
- Initial Setup: Start with the surveyor’s transit to establish straight reference lines along the conveyor’s path. Mark these lines clearly using the chalk line.
- Measuring and Marking: Use the tape measure to verify distances and intervals between idlers, ensuring consistent spacing. Mark these positions accurately on the conveyor frame.
- Leveling: Use the carpenter’s level to check each idler’s alignment. Adjust as necessary to ensure each idler is perfectly horizontal.
- Vertical Alignment: Use the plumb bob to verify that idlers are vertically aligned. Adjust to correct any tilt.
- Verification: Place rigid steel pieces along the idlers to ensure they form a straight line without any deviations. Make final adjustments as needed.
Proper conveyor idler alignment is essential for the optimal performance and longevity of conveyor systems. Using the right tools, including the surveyor’s transit, carpenter’s level, and additional tools like chalk lines, tape measures, plumb bobs, and rigid steel, technicians can achieve precise alignment. This meticulous process enhances efficiency, reduces maintenance costs, and improves safety, ultimately contributing to the reliable operation of conveyor systems. By investing in the right tools and following a systematic alignment procedure, businesses can ensure their conveyor systems run smoothly and efficiently.
Types of Conveyor Idlers
Proper conveyor idler alignment is essential for the efficient operation and longevity of a conveyor system. Understanding the different types of conveyor idlers and their roles within the system is crucial for achieving precise alignment. This section will explore the various types of conveyor idlers, including carrying idlers, return idlers, self-aligning idlers, and impact idlers, detailing their functions and importance in maintaining optimal conveyor performance.
Carrying Idlers
Carrying idlers are integral components of a conveyor system, responsible for supporting the conveyor belt and the load it carries. Their primary function is to provide a stable and even surface for the belt, ensuring that the material being transported remains secure and moves smoothly along the conveyor.
- Function and Placement: Carrying idlers are positioned along the length of the conveyor, spaced at regular intervals to support the belt and load. They are typically arranged in sets of three or more rollers, forming a trough shape that cradles the belt. This troughing effect helps to center the material and prevent spillage.
- Load Distribution: By evenly distributing the weight of the load, carrying idlers reduce the stress on the belt and the conveyor frame. This even distribution is crucial for maintaining the integrity of the conveyor system and preventing premature wear and tear.
- Belt Tracking: Proper alignment of carrying idlers is vital for maintaining belt tracking. Misaligned carrying idlers can cause the belt to drift off-center, leading to potential damage and operational inefficiencies. Ensuring correct conveyor idler alignment helps to keep the belt on track and enhances overall system performance.
Return Idlers
Return idlers play a crucial role in supporting the empty belt on its return journey to the loading point. They help maintain belt alignment and prevent sagging, which can lead to operational issues and increased wear.
- Supporting the Returning Belt: Return idlers are typically positioned beneath the conveyor frame, supporting the belt as it returns from the discharge point to the loading point. They ensure that the belt remains flat and tensioned, preventing it from sagging or folding.
- Reducing Wear: By providing support to the returning belt, return idlers reduce the wear and tear on the belt, prolonging its lifespan. Proper alignment of return idlers is essential to avoid belt misalignment, which can cause excessive wear and potential damage.
- Maintaining Belt Tension: Return idlers help maintain the tension of the returning belt, ensuring smooth and efficient operation. Correct conveyor idler alignment of return idlers ensures that the belt remains taut and reduces the risk of operational disruptions.
Self-Aligning Idlers
Self-aligning idlers are designed to automatically correct any misalignment of the conveyor belt. They are an essential component for maintaining proper conveyor idler alignment and ensuring the smooth operation of the conveyor system.
- Mechanism and Operation: Self-aligning idlers are equipped with a pivoting mechanism that allows them to adjust and realign the belt automatically. When the belt starts to drift off-center, the self-aligning idler pivots to correct the alignment and bring the belt back to its proper position.
- Advantages in Belt Alignment: The primary advantage of self-aligning idlers is their ability to maintain belt alignment without manual intervention. This automatic correction helps to reduce downtime and maintenance costs associated with belt misalignment.
- Enhanced Safety and Efficiency: By preventing belt misalignment, self-aligning idlers enhance the safety and efficiency of the conveyor system. They reduce the risk of spillage and operational disruptions, contributing to a more reliable and productive operation.
Impact Idlers
Impact idlers are designed to absorb the impact of heavy loads being dropped onto the conveyor belt. They are typically installed in areas where the belt is subjected to significant impact, such as loading zones.
- Special Use in Heavy Loading Areas: Impact idlers are positioned at points where heavy or abrasive materials are loaded onto the conveyor belt. They are built to withstand the force of these loads and protect the belt from damage.
- Shock Absorption: The rollers of impact idlers are made from materials that can absorb and dissipate the energy from heavy impacts. This shock absorption prevents the belt from being damaged and reduces the wear on the conveyor components.
- Prolonging Belt Life: By protecting the belt from the damaging effects of heavy loads, impact idlers help to prolong the lifespan of the belt and reduce maintenance costs. Proper conveyor idler alignment of impact idlers ensures that they function effectively and provide optimal protection.
Understanding the different types of conveyor idlers and their roles within a conveyor system is crucial for achieving and maintaining proper conveyor idler alignment. Carrying idlers support the load, return idlers support the empty belt, self-aligning idlers correct misalignments automatically, and impact idlers protect the belt from heavy loads. Each type of idler plays a specific role in ensuring the efficient, cost-effective, and safe operation of the conveyor system. By investing in the right idlers and ensuring their proper alignment, businesses can optimize their conveyor operations, reduce maintenance costs, and enhance the longevity and performance of their conveyor systems.
Step-by-Step Conveyor Idler Alignment Procedure
Achieving precise conveyor idler alignment is essential for ensuring the efficient operation and longevity of a conveyor system. Proper alignment reduces wear and tear, minimizes maintenance costs, and enhances safety. This section outlines a comprehensive step-by-step procedure for aligning conveyor idlers, including preparation, establishing the center line, aligning the idlers, and making final adjustments.
Preparation
Proper preparation is crucial for effective conveyor idler alignment. This phase involves inspecting all components and ensuring the conveyor is clean.
Inspection
- Check for Wear and Damage: Before starting the alignment process, thoroughly inspect all conveyor components, including the belt, idlers, frames, and pulleys. Look for signs of wear, damage, or misalignment that could affect the alignment process.
- Replace Damaged Parts: If any components are found to be damaged or excessively worn, replace them before proceeding with the alignment. Ensuring all parts are in good condition is essential for accurate alignment.
Cleanliness
- Clean the Conveyor: Ensure that the entire conveyor system is clean. Remove any debris, dirt, or material buildup from the belt and idlers. A clean conveyor allows for more accurate measurements and adjustments.
- Lubricate Moving Parts: Lubricate any moving parts as needed to ensure smooth operation. Proper lubrication can also help identify any issues with the components that might need addressing before alignment.
Establishing Center Line
The center line is a crucial reference point for aligning the idlers. Accurate marking and verification are essential steps in this process.
Marking
- Use a Plumb Bob: Suspend a plumb bob from a fixed point above the conveyor to establish a vertical reference. Mark this point on the floor or conveyor frame as the starting point of the center line.
- Stretch a Chalk Line: Stretch a chalk line from the starting point along the length of the conveyor. Snap the chalk line to create a visible, straight line that will serve as the center reference for aligning the idlers.
Verification
- Double-Check Measurements: Measure the distance from the chalk line to the edges of the conveyor frame at multiple points along its length. Ensure that the center line is equidistant from both sides of the frame to verify its accuracy.
- Adjust as Necessary: If any discrepancies are found, adjust the chalk line accordingly. Accurate measurements are critical for proper conveyor idler alignment.
Aligning Idlers
Aligning the idlers involves positioning carrying, return, and self-aligning idlers correctly relative to the center line. Each type of idler plays a specific role in the alignment process.
Carrying Idlers
- Positioning: Place the carrying idlers along the center line, ensuring they are evenly spaced and parallel to each other. Use the chalk line as a guide to position the idlers accurately.
- Alignment: Align each carrying idler so that its center aligns perfectly with the chalk line. Use a carpenter’s level to ensure that the idlers are level and adjust them as necessary to achieve proper alignment.
- Secure: Once aligned, securely fasten the carrying idlers to the conveyor frame. Recheck the alignment after securing to ensure nothing shifted during the fastening process.
Return Idlers
- Positioning: Position the return idlers beneath the conveyor frame, using the center line as a reference. Ensure they are spaced consistently and aligned with the center line.
- Alignment: Align each return idler with the center line, ensuring that they are level and parallel. Use a carpenter’s level to verify the alignment and make adjustments as needed.
- Secure: Securely fasten the return idlers to the frame and recheck their alignment to confirm they are properly positioned.
Self-Aligning Idlers
- Installation Tips: Install self-aligning idlers at strategic points along the conveyor where belt misalignment is most likely to occur. Follow the manufacturer’s guidelines for installation to ensure optimal performance.
- Adjustments: Ensure that self-aligning idlers are free to pivot and adjust as needed. Their ability to self-correct depends on their freedom to move in response to belt misalignment.
- Check Functionality: After installation, run the conveyor and observe the self-aligning idlers. Ensure they are functioning correctly and making necessary adjustments to maintain belt alignment.
Final Adjustments
After aligning all idlers, make final adjustments to ensure optimal conveyor performance.
Leveling
- Verify Leveling: Use a carpenter’s level to check that all idlers are level and parallel. Adjust any idlers that are not perfectly level to ensure uniform support for the belt.
- Consistent Height: Ensure that all idlers are at a consistent height relative to the conveyor frame. This uniformity helps maintain even belt tension and reduces the risk of misalignment.
Tension Adjustment
- Fine-Tune Belt Tension: Adjust the belt tension to the manufacturer’s specifications. Proper tension is crucial for preventing belt slippage and ensuring smooth operation.
- Check Alignment Under Load: Run the conveyor with a load to verify that the belt remains aligned. Make any necessary adjustments to the idlers or tension to maintain proper alignment.
Proper conveyor idler alignment is essential for the efficient, safe, and cost-effective operation of a conveyor system. By following this step-by-step procedure—preparing the system, establishing a precise center line, aligning the idlers, and making final adjustments—technicians can ensure that the conveyor operates smoothly and reliably. Investing time in accurate alignment not only enhances the system’s performance but also extends the lifespan of the conveyor components, ultimately leading to significant cost savings and improved safety.
Common Issues and Troubleshooting of Conveyor Idler Alignment
Proper conveyor idler alignment is crucial for the efficient operation of a conveyor system. However, several common issues can arise that affect alignment. Understanding these issues and knowing how to troubleshoot them is essential for maintaining optimal performance. This section will discuss common misalignment causes, correction techniques, and maintenance tips to ensure conveyor idlers remain properly aligned.
Misalignment Causes
Several factors can contribute to conveyor idler misalignment, including:
- Uneven Loading: Uneven distribution of material on the conveyor belt can cause one side of the belt to experience more tension than the other, leading to misalignment.
- Belt Slippage: If the conveyor belt slips on the idlers, it can lead to misalignment as the belt may not track properly.
- Improper Installation: Incorrect installation of idlers, particularly self-aligning idlers, can lead to misalignment issues.
- Belt Damage: Damage to the conveyor belt, such as cuts or tears, can cause the belt to track improperly and result in misalignment.
- Environmental Factors: Extreme temperatures, humidity, and other environmental factors can affect the alignment of conveyor idlers over time.
Correction Techniques
When misalignment occurs, several techniques can be used to correct the issue:
- Adjusting Idler Position: Check the alignment of each idler along the conveyor and adjust as needed to ensure they are all in line with the center line.
- Tensioning the Belt: Proper belt tension is essential for maintaining alignment. Adjust the tension of the belt according to the manufacturer’s specifications.
- Replacing Damaged Components: If any idlers or other conveyor components are damaged, replace them promptly to prevent further misalignment.
- Cleaning and Lubrication: Ensure that idlers are clean and properly lubricated to reduce friction and prevent sticking, which can lead to misalignment.
Maintenance Tips
To prevent misalignment and ensure proper conveyor idler alignment, follow these maintenance tips:
- Regular Inspections: Conduct regular inspections of the conveyor system to check for signs of misalignment or damage.
- Cleanliness: Keep the conveyor system clean and free of debris to prevent issues with idler movement.
- Lubrication: Properly lubricate idlers and other moving parts to reduce friction and prevent sticking.
- Alignment Checks: Periodically check the alignment of idlers using a straight edge or laser alignment tool to ensure they are properly aligned.
- Training: Provide training to personnel responsible for maintaining the conveyor system to ensure they understand the importance of proper alignment and how to achieve it.
Maintaining proper conveyor idler alignment is essential for the efficient and safe operation of a conveyor system. By identifying common misalignment causes, using correction techniques, and following maintenance tips, operators can prevent issues and ensure that their conveyor systems operate smoothly. Regular inspections, cleanliness, lubrication, and proper alignment checks are key to preventing misalignment and maximizing the lifespan of conveyor components.
Diagrams and Illustrations about Conveyor Idler Alignment
Visual aids such as diagrams and illustrations are invaluable for understanding and implementing proper conveyor idler alignment. They provide a clear, visual representation of the alignment process, making it easier for operators to follow the correct procedures. This section includes an alignment diagram, frame dimensions, and a procedure flowchart to assist with conveyor idler alignment.
Alignment Diagram
An alignment diagram provides a visual guide for aligning conveyor idlers. It illustrates the correct positioning of carrying, return, and self-aligning idlers relative to the center line of the conveyor. The diagram includes measurements and angles to ensure precise alignment. Referencing the alignment diagram during the alignment process can help operators achieve optimal alignment and prevent misalignment issues.
Frame Dimensions
Standard dimensions for idler frames are crucial for ensuring proper alignment. The frame dimensions determine the placement and spacing of idlers along the conveyor. These dimensions are typically specified by the conveyor manufacturer and are based on factors such as belt width, load capacity, and conveyor length. Using the correct frame dimensions ensures that idlers are positioned correctly and aligned with the center line of the conveyor.
Procedure Flowchart
A procedure flowchart provides a step-by-step visual representation of the conveyor idler alignment process. It outlines the sequence of actions required to align carrying, return, and self-aligning idlers, from preparation to final adjustments. The flowchart includes decision points and instructions for each step of the alignment process, making it easy for operators to follow and implement. Following the flowchart helps ensure that all necessary tasks are completed in the correct order, leading to successful conveyor idler alignment.
Diagrams and illustrations play a crucial role in facilitating proper conveyor idler alignment. They provide a visual representation of the alignment process, making it easier for operators to understand and implement the correct procedures. Alignment diagrams, frame dimensions, and procedure flowcharts are valuable tools for ensuring that idlers are positioned correctly and aligned with the center line of the conveyor. By using these visual aids, operators can achieve optimal conveyor idler alignment, leading to improved conveyor performance and reduced maintenance costs.
Fill out the form to receive a quote for our conveyor rollers.
FAQs about Conveyor Idler Alignment
The placement of self-aligning idlers along the conveyor track can significantly impact the efficiency and reliability of the conveyor system. While the specific spacing can vary depending on the belt width, material load, and the system’s overall design, a general guideline is to install self-aligning idlers at intervals of 30 to 50 feet (9 to 15 meters). This spacing ensures that any belt misalignment is promptly corrected before it can escalate into a more significant issue. It’s essential to conduct a thorough analysis of the conveyor’s operational conditions and requirements to determine the optimal spacing for self-aligning idlers in any given system.
Conveyor alignment involves adjusting the conveyor’s structure and components to ensure everything is correctly positioned and the belt moves smoothly along the intended path. The process typically includes the following steps:
Inspecting the Conveyor Structure: Check for any signs of misalignment, such as uneven wear patterns on the belt or irregularities in the idlers and rollers.
Aligning the Pulleys and Rollers: Use measuring tools to adjust the head and tail pulleys and ensure they are parallel to each other and perpendicular to the conveyor’s centerline.
Adjusting the Idlers: Position the idlers so they are evenly spaced and parallel to each other, making any necessary adjustments to promote uniform belt tension.
Installing and Adjusting Self-Aligning Idlers: Place self-aligning idlers at strategic points along the conveyor to correct any potential misalignments as the belt moves.
Testing and Monitoring: After adjustments, run the conveyor belt and observe its movement, making further refinements as needed to achieve optimal alignment.
Professional guidance or specialized equipment may be necessary for precise alignment, especially for complex or heavily loaded conveyor systems.
A self-aligning idler is a specialized component used in conveyor systems designed to automatically adjust the belt’s position to ensure it is always centered on the conveying track. These idlers are crucial for maintaining the conveyor belt’s proper alignment, reducing wear and tear, and minimizing the likelihood of belt drift or misalignment issues that can lead to operational disruptions. Self-aligning idlers typically consist of a set of rollers with the ability to pivot and steer the belt back to its correct position when it starts to move off-track, ensuring smoother operations and prolonging the belt’s lifespan.
The spacing between conveyor idlers is a critical factor in ensuring the belt’s support and minimizing sag, which can affect the conveyor’s operational efficiency and the lifespan of the belt. The ideal spacing is influenced by several factors, including the belt width, load characteristics, material type, and conveyor speed. Generally, for standard conveyor systems, idlers are spaced between 3 to 5 feet (approximately 0.9 to 1.5 meters) apart in the loading zone where material impact is highest. In contrast, in non-loading areas, the spacing can be extended up to 6 to 8 feet (about 1.8 to 2.4 meters). Achieving the correct idler spacing is paramount for maintaining adequate support for the conveyor belt, reducing wear and tear, and enhancing the system’s overall performance and durability.
Last Updated on August 5, 2024 by Jordan Smith
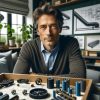
Jordan Smith, a seasoned professional with over 20 years of experience in the conveyor system industry. Jordan’s expertise lies in providing comprehensive solutions for conveyor rollers, belts, and accessories, catering to a wide range of industrial needs. From initial design and configuration to installation and meticulous troubleshooting, Jordan is adept at handling all aspects of conveyor system management. Whether you’re looking to upgrade your production line with efficient conveyor belts, require custom conveyor rollers for specific operations, or need expert advice on selecting the right conveyor accessories for your facility, Jordan is your reliable consultant. For any inquiries or assistance with conveyor system optimization, Jordan is available to share his wealth of knowledge and experience. Feel free to reach out at any time for professional guidance on all matters related to conveyor rollers, belts, and accessories.