Using the Steel Conveyor Belt Cord Specification PDF
Conveyor belt cord is critical components in the construction of conveyor belts, providing the necessary strength and stability for effective material transport across various industries. These cords are embedded within the belt and serve as the tensile member, ensuring that the belt can withstand the forces exerted during operation. The importance of conveyor belt cords lies in their ability to enhance the performance, reliability, and longevity of conveyor belts, making them essential for applications ranging from mining and construction to manufacturing and logistics.
What is the Heavy Duty Conveyor Belt Cord
Heavy-duty conveyor belt cords are specifically designed for applications that require exceptional strength and durability. These cords are a critical component of conveyor belts used in industries that handle extremely heavy loads and operate under harsh conditions. In this section, we will delve into the construction of heavy-duty conveyor belt cords, their unique properties, and their role in enhancing the performance of conveyor belts.
Construction of Heavy Duty Conveyor Belt Cords
Heavy-duty conveyor belt cords are constructed using high-tensile materials that provide superior strength and durability. The most common materials used in the construction of these cords include:
- Steel Cords: Steel cords are widely used in heavy-duty conveyor belts due to their high tensile strength and resistance to elongation. These cords consist of multiple strands of high-strength steel wires twisted together to form a robust and flexible tensile member. The steel cords are embedded in the rubber matrix of the conveyor belt, providing the necessary reinforcement to handle heavy loads.
- Synthetic Fibers: In some heavy-duty conveyor belts, synthetic fibers such as polyester, aramid, or nylon are used as the tensile members. These fibers offer excellent tensile strength and flexibility, making them suitable for applications that require both strength and adaptability. Synthetic fiber cords are often used in combination with steel cords to enhance the overall performance of the belt.
- Rubber Compounds: The cords are encased in high-quality rubber compounds that protect them from abrasion, impact, and environmental factors. The rubber covers on the top and bottom of the belt provide additional reinforcement and ensure that the cords remain securely embedded within the belt.
Properties of Heavy Duty Conveyor Belt Cords
Heavy-duty conveyor belt cords possess several key properties that make them suitable for demanding applications:
- High Tensile Strength: The primary property of heavy-duty conveyor belt cords is their high tensile strength. This strength allows the belt to carry extremely heavy loads without stretching or breaking, ensuring reliable performance in demanding conditions.
- Low Elongation: Heavy-duty conveyor belt cords are designed to have low elongation, meaning they do not stretch significantly under load. This property ensures that the belt maintains consistent tension and alignment, reducing the risk of slippage and improving overall efficiency.
- Abrasion Resistance: The materials used in the construction of heavy-duty conveyor belt cords are highly resistant to abrasion. This resistance is crucial for applications where the belt is exposed to abrasive materials, such as mining and construction.
- Impact Resistance: Heavy-duty conveyor belt cords can withstand high-impact loads, making them suitable for environments where the belt is subjected to frequent impacts from heavy or sharp materials. This impact resistance prevents damage to the belt and extends its service life.
- Chemical Resistance: In some applications, conveyor belts are exposed to chemicals that can degrade the materials used in their construction. Heavy-duty conveyor belt cords are often treated with chemical-resistant coatings to protect them from such exposure, ensuring long-term performance.
Role of Heavy Duty Conveyor Belt Cords in Enhancing Belt Performance
Heavy-duty conveyor belt cords play a crucial role in enhancing the performance of conveyor belts in several ways:
- Load Capacity: The high conveyor belt tensile strength of heavy-duty conveyor belt cords allows the belts to carry significantly heavier loads compared to standard conveyor belts. This increased load capacity is essential for industries such as mining and construction, where large quantities of materials need to be transported efficiently.
- Longevity: The durability and resistance to wear and tear of heavy-duty conveyor belt cords contribute to the extended service life of the belts. This longevity reduces the frequency of belt replacements and maintenance, resulting in lower operational costs and increased productivity.
- Reliability: Heavy-duty conveyor belt cords provide the necessary strength and stability to ensure reliable performance under demanding conditions. This reliability is critical for industries that require continuous operation and minimal downtime.
- Flexibility: Despite their strength, heavy-duty conveyor belt cords maintain a level of flexibility that allows the belts to navigate curves and inclines within the conveyor system. This flexibility ensures smooth operation and reduces the risk of belt failure.
- Safety: The high strength and durability of heavy-duty conveyor belt cords contribute to the overall safety of the conveyor system. By reducing the risk of belt failure and ensuring consistent performance, these cords help prevent accidents and injuries in industrial settings.
Conveyor belt cords are essential components that provide the strength, durability, and flexibility required for efficient material handling across various industries. Heavy-duty conveyor belt cords, in particular, are designed to handle extremely heavy loads and operate under harsh conditions, making them ideal for applications in mining, construction, manufacturing, and logistics. Understanding the construction, properties, and role of these cords can help businesses select the right conveyor belts for their specific needs, ensuring reliable performance and long-term efficiency.
Conveyor Belt Cord: Navigating the Steel Cord Conveyor Belt Specification PDF
The Steel Cord Conveyor Belt Specification PDF is an essential resource for understanding the detailed construction, performance, and technical parameters of steel cord conveyor belts. This document provides comprehensive information that helps in selecting the right conveyor belt cord for specific industrial applications. In this section, we will explore how to effectively navigate the Steel Cord Conveyor Belt Specification PDF to find the necessary details about belt construction, performance metrics, and technical specifications.
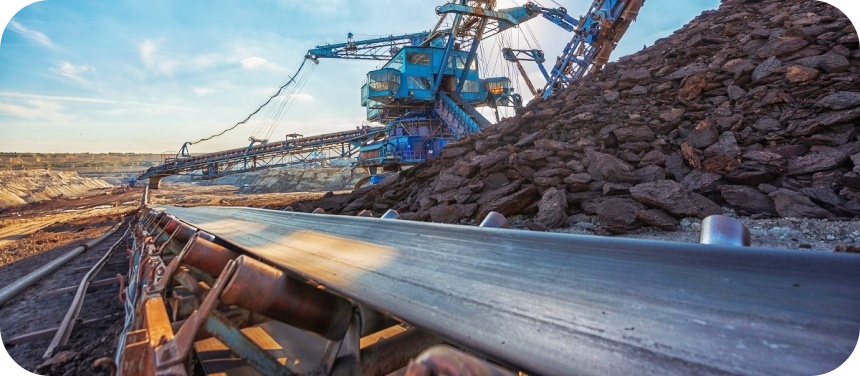
Layout of the Specification PDF
- Introduction and Overview: The initial sections of the specification PDF typically provide an introduction to the document, outlining its purpose and scope. This section often includes an overview of steel cord conveyor belts, their applications, and the advantages they offer over other types of belts. Familiarizing yourself with this section helps set the context for the detailed specifications that follow.
- Technical Specifications: The core of the specification PDF contains detailed technical specifications of steel cord conveyor belts. This section is usually divided into several subsections, each focusing on a specific aspect of the belt’s construction and performance. Key subsections to pay attention to include:
- Belt Construction: This subsection provides information about the materials and construction techniques used in manufacturing the conveyor belt cord. Details such as the type of steel cords used, their arrangement within the belt, and the rubber compounds used for the covers are typically included.
- Tensile Strength: Here, you will find specifications related to the tensile strength of the steel cords and the overall belt. This includes nominal tensile strength, working tension, and elongation at break. Understanding these parameters is crucial for selecting a belt that can handle the required load without stretching or breaking.
- Abrasion and Impact Resistance: This subsection outlines the belt’s resistance to wear and tear, as well as its ability to withstand impacts. Specifications such as abrasion resistance (measured in cubic millimeters) and impact resistance provide insights into the belt’s durability and suitability for harsh operating conditions.
- Fire and Chemical Resistance: For applications involving exposure to high temperatures or chemicals, this subsection provides critical information about the belt’s resistance to fire and chemical degradation. Compliance with safety standards such as ISO 340 and EN 12882 is often highlighted.
- Dimensional Specifications: Detailed information about the belt’s dimensions, including width, length, cover thickness, and overall carcass thickness, is provided in this subsection. These dimensions are essential for ensuring the belt fits the specific conveyor system.
- Performance Metrics: This section of the PDF typically includes performance metrics that indicate how the belt performs under various operating conditions. Key metrics to look for include:
- Load Capacity: The maximum load the belt can carry, expressed in terms of weight per unit length, is provided. This metric helps in determining whether the belt can handle the expected load in your application.
- Speed Rating: The maximum operating speed of the belt, usually measured in meters per second (m/s), is specified. Ensuring the belt can operate at the required speed without compromising performance is crucial for efficient material handling.
- Flexibility: Information about the belt’s flexibility, including its minimum pulley diameter and ability to navigate curves and inclines, is provided. This metric helps in assessing the belt’s suitability for complex conveyor layouts.
- Application Guidelines: This section offers practical guidelines for selecting and using steel cord conveyor belts in various industrial applications. It may include recommendations for specific industries, such as mining, construction, and manufacturing, as well as tips for optimizing belt performance and longevity.
- Maintenance and Troubleshooting: The final sections of the specification PDF often provide maintenance tips and troubleshooting advice. This information is invaluable for ensuring the belt’s long-term performance and addressing common issues that may arise during operation.
Steps to Navigate the Specification PDF
- Identify Key Requirements: Before diving into the specification PDF, identify the key requirements for your application. Consider factors such as load capacity, operating speed, environmental conditions, and specific industry standards. Having a clear understanding of your needs will help you focus on the relevant sections of the document.
- Use the Table of Contents: Most specification PDFs include a table of contents that allows you to quickly locate specific sections. Use this feature to navigate directly to the areas that are most relevant to your application.
- Review Technical Specifications: Carefully review the technical specifications section, paying close attention to the details about belt construction, tensile strength, abrasion resistance, and other critical parameters. Compare these specifications to your application’s requirements to ensure the belt meets your needs.
- Evaluate Performance Metrics: Assess the performance metrics provided in the PDF to determine how the belt will perform under your specific operating conditions. Consider factors such as load capacity, speed rating, and flexibility to ensure the belt can handle the expected demands.
- Consider Application Guidelines: Take advantage of the application guidelines section to gain insights into best practices for selecting and using steel cord conveyor belts. Follow the recommendations provided to optimize the belt’s performance and longevity.
- Refer to Maintenance Tips: Regular maintenance is essential for the long-term performance of steel cord conveyor belts. Refer to the maintenance tips and troubleshooting advice provided in the PDF to develop a proactive maintenance plan and address any issues that may arise.
Conveyor Belt Cord: Factors Influencing Steel Cord Conveyor Belt Price
The price of steel cord conveyor belts can vary significantly based on several factors. Understanding these factors is crucial for budgeting and selecting the right belt for your needs. In this section, we will discuss the various elements that affect the pricing of steel cord conveyor belts, including materials, manufacturing processes, and market demand.
Materials
- Steel Cords: The quality and grade of the steel cords used in the conveyor belt are primary determinants of its price. High-tensile steel cords, which offer superior strength and durability, are more expensive than lower-grade steel options. The number and arrangement of steel cords within the belt also impact the cost, with more cords typically leading to higher prices.
- Rubber Compounds: The type and quality of rubber used in the conveyor belt’s construction significantly influence its price. Rubber compounds with enhanced properties, such as increased abrasion resistance, heat resistance, and flexibility, tend to be more costly. The thickness of the rubber covers on the top and bottom of the belt also affects the price, with thicker covers providing greater protection and longevity.
- Additional Materials: Other materials, such as adhesion agents and anti-corrosive coatings, may be used to enhance the performance and lifespan of the steel cord conveyor belt. These additional materials can add to the overall cost but are often necessary for specific applications that require extra durability and protection.
Manufacturing Processes
- Production Techniques: The manufacturing process for steel cord conveyor belts is complex and requires advanced techniques to ensure the proper embedding of steel cords within the rubber matrix. Techniques such as hot vulcanization and cold bonding are used to achieve the desired properties of the conveyor belt. The precision and expertise required for these processes contribute to the overall cost.
- Quality Control: Ensuring the quality and consistency of steel cord conveyor belts involves rigorous testing and inspection throughout the manufacturing process. Quality control measures, such as X-ray inspection of steel cord alignment and tensile strength testing, are essential to maintain high standards. These quality assurance steps add to the production costs but are crucial for delivering reliable and safe conveyor belts.
- Customization: Customizing steel cord conveyor belts to meet specific application requirements can also influence the price. Customizations may include varying the belt width, length, cover thickness, and the number of plies. Tailoring the belt to fit unique operational needs often involves additional design and production steps, resulting in higher costs.
Market Demand
- Industry Demand: The demand for steel cord conveyor belts can vary across different industries, such as mining, construction, and manufacturing. High demand in specific sectors can drive up prices due to increased competition for available products. Conversely, periods of low demand may result in more competitive pricing as manufacturers seek to attract buyers.
- Economic Conditions: Economic factors, such as inflation, currency exchange rates, and raw material costs, can impact the pricing of steel cord conveyor belts. Fluctuations in the global economy can lead to changes in production costs and market prices, influencing the overall cost of conveyor belts.
- Technological Advancements: Innovations in conveyor belt technology can affect pricing. New materials, improved manufacturing processes, and enhanced performance features can lead to higher initial costs but may offer long-term savings through increased efficiency and reduced maintenance requirements.
Additional Considerations
- Transportation and Logistics: The cost of transporting and delivering steel cord conveyor belts to the installation site can also influence the overall price. Factors such as distance, shipping method, and handling requirements play a role in determining transportation costs.
- Installation and Maintenance: The expenses associated with installing and maintaining steel cord conveyor belts should also be considered. Proper installation ensures optimal performance and longevity, while regular maintenance helps prevent costly repairs and downtime. These costs, though not directly related to the purchase price, are important factors in the total cost of ownership.
- Supplier and Brand Reputation: The reputation and reliability of the conveyor belt supplier can impact pricing. Established brands with a track record of quality and performance may charge premium prices for their products. However, the assurance of receiving a high-quality, reliable steel cord conveyor belt often justifies the higher cost.
The price of a steel cord conveyor belt is influenced by various factors, including the materials used, manufacturing processes, market demand, and additional considerations such as transportation and maintenance. By understanding these factors, businesses can make informed decisions when budgeting for their conveyor belt needs. Investing in a high-quality steel cord conveyor belt may involve higher initial costs, but the benefits
Conveyor Belt Cord: Detailed Overview of Steel Cord Belt Specification
Steel cord conveyor belts are a crucial component in many industrial applications due to their high tensile strength, durability, and ability to handle heavy loads over long distances. The core of these belts, known as the conveyor belt cord, is made of steel, providing superior reinforcement and performance characteristics. This section provides an in-depth look at the specific technical specifications of steel cord belts, focusing on key parameters such as tensile strength, elongation, and cover thickness.
Key Specifications of Steel Cord Belts
- Tensile Strength
The tensile strength of a steel cord belt is one of its most critical specifications. It measures the maximum load the belt can handle before breaking. Tensile strength is typically expressed in Newtons per millimeter (N/mm) of width. Steel cord belts have high tensile strength due to the robust steel cords embedded within the belt, making them ideal for transporting heavy and bulky materials over long distances. For instance, steel cord belts used in mining operations often have tensile strengths ranging from 1000 N/mm to 10000 N/mm, ensuring they can handle the substantial loads typical in such environments.
- Elongation at Break
Elongation at break refers to the extent to which the belt can stretch before breaking. This specification is crucial for determining the flexibility and resilience of the conveyor belt cord. Steel cord belts generally exhibit low elongation, typically less than 0.2% of the belt length, which ensures they maintain their shape and structural integrity even under heavy loads. Low elongation is advantageous because it reduces the need for frequent tension adjustments and ensures consistent performance.
- Cover Thickness
The cover thickness of a steel cord belt protects the internal steel cords from damage and wear. The cover is usually made of rubber or a similar durable material and is available in various thicknesses depending on the application. Typical cover thicknesses range from 4 mm to 10 mm for the top cover and 2 mm to 6 mm for the bottom cover. Thicker covers provide better protection against abrasion, impact, and environmental factors, extending the belt’s lifespan. For example, belts used in highly abrasive environments, such as quarries and mining sites, often have thicker covers to ensure longevity.
- Steel Cord Diameter and Spacing
The diameter and spacing of the steel cords are critical factors influencing the belt’s tensile strength and flexibility. Steel cords typically have diameters ranging from 2.5 mm to 12 mm. The spacing between the cords is designed to ensure even load distribution and to prevent cord separation. Properly spaced cords provide a balance between strength and flexibility, allowing the belt to bend around pulleys while maintaining its load-bearing capacity.
- Adhesion Between Steel Cords and Rubber
The adhesion between the steel cords and the rubber cover is a crucial specification that affects the belt’s durability and performance. Strong adhesion ensures that the steel cords remain securely bonded to the rubber, preventing delamination and maintaining the belt’s structural integrity. Adhesion is typically measured in kilonewtons per meter (kN/m), with higher values indicating stronger bonding.
- Resistance to Abrasion, Impact, and Chemicals
Steel cord belts are designed to withstand various environmental and operational challenges. The resistance to abrasion ensures that the belt can handle rough and abrasive materials without significant wear. Impact resistance protects the belt from damage caused by heavy, falling objects. Chemical resistance ensures that the belt can withstand exposure to harsh chemicals without degrading. These resistance properties are crucial for maintaining the belt’s performance and longevity in demanding industrial applications.
- Operating Temperature Range
The operating temperature range indicates the temperatures within which the steel cord belt can function effectively. Steel cord belts are typically designed to operate within a range of -40°C to +80°C. Some specialized belts can withstand even higher temperatures, up to +200°C, for specific applications such as steel mills or chemical plants. Ensuring the belt operates within its specified temperature range prevents premature failure and maintains its performance.
Importance of Steel Cord Belt Specifications
Understanding the detailed specifications of steel cord belts is crucial for selecting the right belt for specific applications. These specifications directly impact the belt’s performance, durability, and suitability for various industrial environments. By carefully considering factors such as tensile strength, elongation, cover thickness, and resistance properties, businesses can ensure they choose a belt that meets their operational requirements and provides reliable, long-term performance.
Conveyor Belt Cord: Steel Cord Belt Joint Techniques
The joint, or splice, is a critical part of any conveyor belt system, particularly for steel cord belts where strength and durability are paramount. Proper splicing ensures the belt’s continuous operation and maintains its tensile strength and performance. This section examines different joint techniques for steel cord belts, including hot vulcanization and mechanical splicing, and their impact on belt performance.
Hot Vulcanization
- Process Overview
Hot vulcanization is a common technique for joining steel cord belts. This process involves applying heat and pressure to the belt ends to create a seamless and durable joint. The ends of the steel cords are carefully prepared and aligned, and a special vulcanizing press is used to bond the rubber cover and steel cords together.
- Advantages
- Strong Bond: Hot vulcanization creates a strong, seamless bond that matches the tensile strength of the rest of the belt, ensuring consistent performance.
- Durability: The joint formed through hot vulcanization is highly durable and resistant to wear and tear, making it suitable for heavy-duty applications.
- Flexibility: The vulcanized joint maintains the flexibility of the belt, allowing it to bend around pulleys and adapt to the conveyor’s configuration without compromising strength.
- Considerations
- Equipment and Expertise: Hot vulcanization requires specialized equipment and skilled technicians, which can increase the initial setup cost and complexity.
- Time-Consuming: The process can be time-consuming, requiring the belt to be taken out of service during splicing, leading to potential downtime.
Mechanical Splicing
- Process Overview
Mechanical splicing involves using mechanical fasteners to join the ends of the steel cord belt. This method is quicker and less complex than hot vulcanization. Various types of fasteners, such as plate fasteners, hinged fasteners, and rivet fasteners, are used to secure the belt ends.
- Advantages
- Speed: Mechanical splicing is significantly faster than hot vulcanization, reducing downtime and allowing the belt to be back in service quickly.
- Simplicity: The process is straightforward and does not require specialized equipment or highly skilled technicians, making it a cost-effective option.
- Flexibility: Mechanical splices can be easily adjusted or replaced if needed, providing flexibility for maintenance and repairs.
- Considerations
- Strength: Mechanical splices may not provide the same level of tensile strength as hot vulcanized joints, potentially reducing the overall strength of the belt.
- Wear and Tear: Mechanical splices are more susceptible to wear and tear, especially in applications involving heavy loads or abrasive materials, which can lead to more frequent maintenance and replacements.
- Flexibility: Mechanical splices can be less flexible than hot vulcanized joints, potentially causing issues with belt alignment and operation over time.
Impact on Belt Performance
- Tensile Strength
The choice of splicing technique significantly impacts the tensile strength of the steel cord belt. Hot vulcanized joints maintain the belt’s original tensile strength, ensuring consistent performance. In contrast, mechanical splices may reduce the belt’s tensile strength, affecting its ability to handle heavy loads.
- Durability and Longevity
Hot vulcanized joints are more durable and resistant to wear and tear, extending the belt’s lifespan and reducing the need for frequent maintenance. Mechanical splices, while easier to install and adjust, may require more frequent inspections and replacements due to their susceptibility to wear and damage.
- Flexibility and Adaptability
Both splicing techniques offer varying degrees of flexibility. Hot vulcanized joints maintain the belt’s flexibility, allowing it to adapt to the conveyor’s configuration without issues. Mechanical splices can be less flexible, potentially causing alignment and operational challenges over time.
- Maintenance and Repair
Mechanical splicing offers the advantage of quick and easy adjustments and repairs, making it suitable for applications where downtime needs to be minimized. Hot vulcanized joints, while more durable, require more time and specialized skills for repairs, which can lead to longer downtimes during maintenance.
In terms of conveyor belt cord, the choice of joint technique for steel cord belts significantly impacts the belt’s performance, durability, and suitability for various industrial applications. Hot vulcanization offers a strong, seamless bond that ensures consistent performance and durability but requires specialized equipment and skilled conveyor belt technicians. Mechanical splicing provides a quicker, simpler, and more flexible solution, though it may not offer the same level of tensile strength and durability as hot vulcanized joints. Understanding the strengths and limitations of each technique allows businesses to choose the most appropriate method for their specific needs, ensuring reliable and efficient operation of their conveyor belt systems.
Get a quote for your Steel Conveyor Belt Cord needs by filling out this form.
FAQs about Conveyor Belt Cord
A conveyor cord is a reinforcement element embedded within a conveyor belt to provide it with additional strength and durability. These cords are typically made from high-strength materials such as steel, polyester, or aramid fibers. The primary function of conveyor cords is to support the belt’s load-carrying capacity and maintain its structural integrity under heavy stress and tension. In steel cord conveyor belts, the steel cords are arranged in parallel and are coated with rubber to bond them to the belt structure, ensuring even load distribution and reducing the risk of belt failure. This reinforcement allows the belt to handle large volumes of material over long distances, making conveyor cords essential for heavy-duty industrial applications such as mining, quarrying, and bulk material handling.
A pull cord is a safety device installed alongside a conveyor belt to provide an emergency stop mechanism. The pull cord runs parallel to the conveyor and is easily accessible to workers. In the event of an emergency, such as a worker being caught in the machinery or a mechanical failure, pulling the cord immediately stops the conveyor belt. This quick access to a stop mechanism helps prevent accidents and injuries by allowing for a rapid response to hazardous situations. Pull cords are part of the conveyor’s safety system and are typically installed at intervals along the length of the conveyor to ensure they are within reach at all times. Regular testing and maintenance of pull cords are essential to ensure their functionality and reliability in emergency situations.
A cable belt conveyor is a type of conveyor system that uses cables as the driving force to move the belt. Unlike traditional conveyor systems that use rollers or drums to drive the belt, a cable belt conveyor employs a pair of wire ropes or cables that run along the entire length of the conveyor. The belt is supported and driven by these cables, which are connected to a series of drive and return pulleys. This design allows the conveyor to cover longer distances and navigate complex routes with greater flexibility. Cable belt conveyors are particularly useful in applications where the terrain is uneven or where there are significant changes in elevation. They are commonly used in the mining industry to transport bulk materials over long distances, providing a cost-effective and efficient solution for material handling.
A conveyor belt system comprises several essential parts that work together to facilitate the efficient transport of materials. The main components include:
Belt: The conveyor belt itself, which is typically made of rubber, PVC, or other durable materials. The belt carries the materials and is the primary surface that moves along the conveyor system.
Pulleys: These are cylindrical devices that help drive and redirect the belt. The drive pulley is connected to the motor and powers the belt, while the tail pulley is located at the opposite end to maintain tension.
Idlers: Idlers are rollers placed along the length of the conveyor to support the belt and maintain its alignment. They help reduce friction and wear, ensuring smooth belt operation.
Drive Unit: The drive unit includes the motor and gearbox that provide the necessary power to move the belt. The motor drives the drive pulley, which in turn moves the belt.
Frame: The frame or structure supports the entire conveyor system, including the belt, pulleys, and idlers. It provides stability and ensures proper alignment of the components.
Take-up Device: This device adjusts the tension of the conveyor belt to compensate for stretching and wear. It ensures that the belt remains tight and properly aligned during operation.
Belt Cleaner: Belt cleaners are installed to remove debris and buildup from the belt’s surface, preventing material carryback and maintaining efficient operation.
Safety Devices: Safety devices, such as pull cords, emergency stops, and safety guards, are installed to protect workers and ensure safe operation of the conveyor system.
Last Updated on August 5, 2024 by Jordan Smith
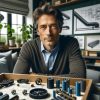
Jordan Smith, a seasoned professional with over 20 years of experience in the conveyor system industry. Jordan’s expertise lies in providing comprehensive solutions for conveyor rollers, belts, and accessories, catering to a wide range of industrial needs. From initial design and configuration to installation and meticulous troubleshooting, Jordan is adept at handling all aspects of conveyor system management. Whether you’re looking to upgrade your production line with efficient conveyor belts, require custom conveyor rollers for specific operations, or need expert advice on selecting the right conveyor accessories for your facility, Jordan is your reliable consultant. For any inquiries or assistance with conveyor system optimization, Jordan is available to share his wealth of knowledge and experience. Feel free to reach out at any time for professional guidance on all matters related to conveyor rollers, belts, and accessories.