Advantages of Using Ceramic Conveyor Belt Lagging
Conveyor belt lagging is crucial for enhancing the efficiency and longevity of conveyor systems. It involves applying a layer of material, typically rubber or ceramic, to the surface of conveyor pulleys. This process increases friction between the belt and pulleys, reducing slippage and wear. Improved traction from conveyor belt lagging ensures smoother operation, reduces maintenance costs, and extends the life of both the belt and pulleys. By preventing belt slippage, lagging also enhances the overall performance and reliability of the conveyor system, making it an essential component in industrial material handling.
How to Use a Conveyor Belt Lagging Calculator
Conveyor belt lagging is essential for enhancing the performance and lifespan of conveyor systems. It involves applying a layer of material, typically rubber or ceramic, to the surface of conveyor pulleys to increase friction and reduce slippage. To ensure the correct application, a conveyor belt lagging calculator can be a valuable tool. This section will guide readers on how to effectively use a conveyor belt lagging calculator to determine the appropriate lagging thickness and materials for their specific needs.
Importance of Conveyor Belt Lagging
Before diving into the use of the calculator, it’s important to understand why conveyor belt lagging is crucial:
- Increased Friction: Lagging increases the friction between the belt and the pulley, preventing slippage and ensuring efficient material transport.
- Reduced Wear: By providing a protective layer, lagging reduces wear and tear on both the belt and the pulley, extending their service life.
- Improved Efficiency: Enhanced grip and reduced slippage lead to smoother operation, higher efficiency, and lower maintenance costs.
Components of a Conveyor Belt Lagging Calculator
A conveyor belt lagging calculator typically includes the following components:
- Pulley Diameter: The diameter of the pulley to be lagged, including and excluding the lagging.
- Belt Width: The width of the conveyor belt, which helps determine the appropriate lagging dimensions.
- Lagging Thickness: The thickness of the lagging material, which can be adjusted based on the calculator’s recommendations.
- Material Type: The type of lagging material to be used (e.g., rubber, ceramic), which affects the performance and durability.
- Operating Conditions: Information about the conveyor’s operating environment, such as temperature, moisture, and load conditions.
Steps to Use a Conveyor Belt Lagging Calculator
- Gather Necessary Information: Before using the calculator, gather all relevant information about your conveyor system. This includes the pulley diameter, belt width, operating conditions, and any specific requirements for the lagging material.
- Input Pulley Diameter: Enter the diameter of the pulley into the calculator. Some calculators may require the diameter without lagging, while others may calculate the final diameter including the lagging. Ensure you provide accurate measurements for precise calculations.
- Enter Belt Width: Input the width of the conveyor belt. This helps the calculator determine the appropriate coverage area for the lagging.
- Select Lagging Thickness: Choose the initial thickness of the lagging material. The calculator will often allow you to adjust this value based on the recommended thickness for your specific application.
- Choose Material Type: Select the type of lagging material you plan to use. Different materials offer varying levels of friction, durability, and resistance to environmental factors. The calculator may provide recommendations based on your operating conditions.
- Input Operating Conditions: Provide details about the conveyor’s operating environment, such as temperature, moisture levels, and load conditions. These factors can influence the performance of the lagging and help the calculator make more accurate recommendations.
- Calculate: Once all information is entered, run the calculation. The calculator will process the data and provide recommendations for the optimal lagging thickness and material type. It may also suggest adjustments to your initial inputs to better suit your application.
- Review Results: Carefully review the calculator’s recommendations. Consider any suggested adjustments to the lagging thickness or material type. Ensure that the recommended specifications meet your operational needs and constraints.
Example of Using a Conveyor Belt Lagging Calculator
Let’s go through a hypothetical example to illustrate the use of a conveyor belt lagging calculator:
- Gather Information: Suppose you have a pulley with a diameter of 800 mm and a conveyor belt width of 1000 mm. The conveyor operates in a dusty environment with a moderate load and occasional exposure to moisture.
- Input Pulley Diameter: Enter 800 mm as the pulley diameter.
- Enter Belt Width: Input 1000 mm as the belt width.
- Select Lagging Thickness: Choose an initial lagging thickness of 10 mm.
- Choose Material Type: Select rubber as the lagging material due to its good friction properties and durability in dusty environments.
- Input Operating Conditions: Provide details about the dusty environment, moderate load, and moisture exposure.
- Calculate: Run the calculation to obtain the recommended lagging specifications.
- Review Results: The calculator recommends a lagging thickness of 12 mm and suggests considering ceramic lagging for enhanced durability in the dusty environment.
Based on the calculator’s recommendations, you may decide to adjust the lagging thickness to 12 mm and explore ceramic lagging options to better meet the demands of your conveyor system.
Benefits of Using a Conveyor Belt Lagging Calculator
- Precision: A lagging calculator provides precise recommendations based on specific measurements and operating conditions, ensuring optimal performance.
- Efficiency: By using a calculator, you can quickly determine the appropriate lagging specifications, saving time and effort in the selection process.
- Cost Savings: Accurate lagging specifications reduce the risk of over- or under-sizing the lagging, leading to cost savings on materials and maintenance.
- Enhanced Performance: Properly sized and selected lagging improves the overall performance and longevity of the conveyor system.
Finding Conveyor Belt Lagging Near Me
Locating reliable suppliers and service providers for conveyor belt lagging in your local area is crucial for ensuring timely and efficient maintenance of your conveyor system. This section will offer tips and resources for finding the best options for conveyor belt lagging near you.
Importance of Local Suppliers
- Quick Response Time: Local suppliers can provide faster service and delivery times, reducing downtime for your conveyor system.
- Support and Maintenance: Local suppliers often offer support services, including installation and maintenance, ensuring your lagging is applied correctly and efficiently.
- Cost Savings: Sourcing lagging materials locally can reduce transportation costs and lead times, contributing to overall cost savings.
Tips for Finding Local Conveyor Belt Lagging Suppliers
- Online Search: Start with a simple online search using keywords such as “conveyor belt lagging near me” or “conveyor belt lagging suppliers in [your location].” This will provide a list of local suppliers and service providers.
- Industry Directories: Use industry-specific directories and websites that list suppliers and service providers in your area. Websites like ThomasNet, Manta, and Yellow Pages can be valuable resources for finding local businesses.
- Manufacturer Websites: Many conveyor belt and lagging manufacturers have dealer locators on their websites. Visit the websites of major manufacturers and use their dealer locator tools to find authorized suppliers near you.
- Trade Associations: Reach out to trade associations related to your industry, such as the Conveyor Equipment Manufacturers Association (CEMA) or the National Industrial Belting Association (NIBA). These associations often have member directories that can help you find reputable suppliers.
- Networking: Leverage your professional network to get recommendations for local suppliers. Colleagues, industry peers, and contractors may have valuable insights and suggestions for reliable lagging suppliers in your area.
- Local Trade Shows and Expos: Attend local trade shows and industrial expos where suppliers and service providers showcase their products. These events provide an opportunity to meet suppliers face-to-face, discuss your needs, and evaluate their offerings.
Evaluating Local Suppliers
Once you have a list of potential suppliers, it’s important to evaluate them to ensure they meet your requirements. Consider the following factors:
- Reputation: Research the reputation of each supplier by reading online reviews, testimonials, and case studies. Look for suppliers with a track record of reliability and quality service.
- Experience: Consider the supplier’s experience in providing conveyor belt lagging solutions. Experienced suppliers are more likely to offer high-quality products and knowledgeable support.
- Product Range: Evaluate the range of lagging materials and products offered by the supplier. Ensure they have the specific type of lagging you need, whether it’s rubber, ceramic, or another material.
- Technical Support: Check if the supplier offers technical support and assistance with selecting the right lagging for your application. Suppliers that provide comprehensive support can help you make informed decisions and ensure proper installation.
- Pricing: Compare pricing from multiple suppliers to ensure you are getting competitive rates. However, be cautious of suppliers with significantly lower prices, as this may indicate lower quality products.
- Warranty and Service: Inquire about warranties and after-sales service. A supplier that stands behind their products with a warranty and offers ongoing support can provide peace of mind and long-term value.
Conveyor Belt Lagging: Step-by-Step Pulley Lagging Procedure PDF
Proper installation and maintenance of conveyor belt lagging are essential for ensuring the efficient operation and longevity of conveyor systems. Pulley lagging is a critical component that enhances the grip between the conveyor belt and the pulley, reducing slippage and improving overall performance. In this section, we will provide a detailed, step-by-step guide for applying pulley lagging. This comprehensive procedure is also available as a downloadable PDF for easy reference.
Conveyor Belt Lagging
Conveyor belt lagging is a layer of material applied to the surface of conveyor pulleys. This material, often made of rubber or ceramic, increases the friction between the belt and the pulley. By enhancing this grip, lagging prevents the belt from slipping, especially under heavy loads or in wet conditions. Effective lagging ensures smooth belt movement, minimizes wear and tear, and reduces maintenance costs.
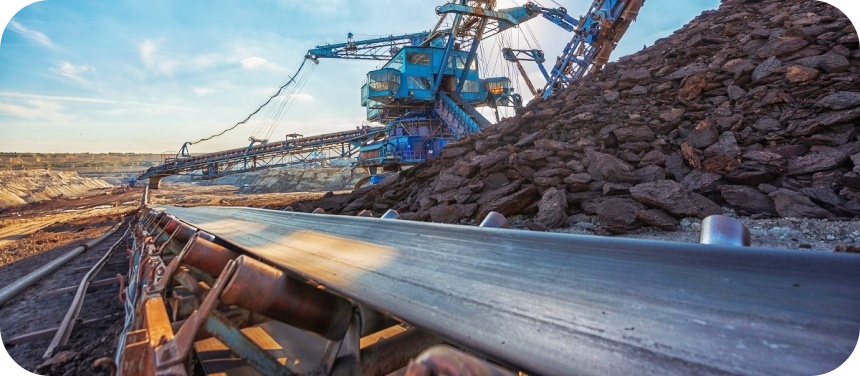
Step-by-Step Pulley Lagging Procedure
- Preparation
- Safety First: Ensure that all safety protocols are in place. Disconnect the power supply to the conveyor system and secure the work area to prevent accidents.
- Clean the Pulley Surface: Thoroughly clean the pulley surface to remove any dirt, oil, or debris. Use a wire brush or a grinder if necessary to achieve a smooth and clean surface.
- Inspect the Pulley: Check the pulley for any signs of damage or wear. If the pulley surface is uneven or damaged, repair or replace it before proceeding with the lagging application.
- Measure and Cut Lagging Material
- Measure the Pulley Dimensions: Accurately measure the circumference and width of the pulley to determine the required size of the lagging material.
- Cut the Lagging Material: Using the measurements, cut the lagging material to the appropriate size. Ensure that the cuts are straight and precise to ensure a proper fit on the pulley surface.
- Apply Adhesive
- Select the Right Adhesive: Choose an adhesive that is compatible with both the pulley surface and the lagging material. Follow the manufacturer’s recommendations for the best results.
- Prepare the Adhesive: Mix the adhesive according to the manufacturer’s instructions. Ensure that the adhesive is mixed thoroughly for optimal bonding strength.
- Apply the Adhesive: Evenly apply a layer of adhesive to both the pulley surface and the back of the lagging material. Use a brush or a roller to spread the adhesive, ensuring full coverage.
- Install the Lagging Material
- Align the Lagging Material: Carefully align the lagging material with the pulley surface. Start at one end and slowly press the lagging onto the pulley, smoothing out any air bubbles or wrinkles as you go.
- Secure the Lagging: Use a roller or a similar tool to press the lagging firmly against the pulley surface. Apply consistent pressure to ensure a strong bond between the lagging and the pulley.
- Trim Excess Material: If necessary, trim any excess lagging material to ensure a neat and professional finish. Use a sharp utility knife for precise cutting.
- Curing and Finishing
- Allow for Curing: Let the adhesive cure according to the manufacturer’s instructions. This step is crucial for achieving maximum bonding strength.
- Inspect the Installation: After curing, inspect the lagging installation for any loose edges or gaps. Make any necessary adjustments or repairs to ensure a secure and even application.
- Reassemble the Conveyor System: Once the lagging is properly installed and cured, reassemble the conveyor system. Ensure that all components are securely in place before restoring power to the system.
- Maintenance Tips
- Regular Inspections: Periodically inspect the pulley lagging for signs of wear, damage, or detachment. Address any issues promptly to maintain optimal performance.
- Clean the Lagging: Keep the lagging surface clean to prevent buildup of materials that could reduce friction and cause slippage.
- Monitor Performance: Continuously monitor the performance of the conveyor system. If slippage or other issues occur, investigate the condition of the pulley lagging and take corrective action as needed.
Proper application of conveyor belt lagging is crucial for maintaining the efficiency and reliability of conveyor systems. By following this step-by-step guide, you can ensure that the lagging is installed correctly, providing optimal grip and reducing slippage. Regular maintenance and inspection of the pulley lagging will further enhance the performance and longevity of your conveyor system.
Conveyor Belt Lagging: What is Pulley Lagging and Its Importance
Pulley lagging is an essential component of conveyor systems that plays a critical role in enhancing the performance and longevity of conveyor belts. By improving the friction between the belt and the pulley, lagging reduces slippage, wear, and maintenance costs. In this section, we will explain what pulley lagging is, its purpose in conveyor systems, and the benefits it offers in terms of performance and longevity.
Pulley lagging is a layer of material applied to the surface of conveyor pulleys. This material, which can be made from rubber, ceramic, or other composite materials, provides additional grip between the conveyor belt and the pulley. The enhanced friction ensures that the belt moves smoothly and efficiently, even under challenging conditions such as heavy loads, high speeds, or wet environments.
Types of Pulley Lagging
- Rubber Lagging
- Plain Rubber Lagging: This type of lagging is made from high-quality rubber and is used for general-purpose applications. It provides a good balance of grip and durability.
- Diamond-Patterned Rubber Lagging: The diamond pattern on the rubber surface enhances traction and reduces slippage. This type of lagging is ideal for high-tension applications and environments with high moisture levels.
- Ceramic Lagging
- Full Ceramic Lagging: Composed entirely of ceramic tiles, this lagging offers exceptional wear resistance and durability. It is suitable for heavy-duty applications where the conveyor system is exposed to abrasive materials.
- Rubber-Ceramic Composite Lagging: This type combines rubber and ceramic materials, providing both flexibility and high resistance to wear. It is used in applications that require both durability and adaptability.
- Fabric-Reinforced Lagging
- Textile Lagging: This lagging incorporates fabric layers to reinforce the rubber, enhancing its strength and longevity. It is used in applications where additional reinforcement is needed to handle high loads and stress.
Purpose of Pulley Lagging
- Increase Friction
The primary purpose of pulley lagging is to increase the friction between the conveyor belt and the pulley. This increased friction prevents the belt from slipping, ensuring smooth and efficient movement of materials. By reducing slippage, lagging helps maintain the correct belt tension and alignment, which is crucial for the optimal operation of the conveyor system.
- Protect the Pulley
Lagging acts as a protective layer for the pulley surface, shielding it from wear and damage caused by constant contact with the conveyor belt. This protection extends the lifespan of the pulley, reducing the frequency of replacements and maintenance.
- Improve Belt Tracking
Properly installed lagging helps improve belt tracking, ensuring that the conveyor belt stays aligned with the pulleys and other components of the system. Improved tracking reduces the risk of belt misalignment, which can cause excessive wear and operational disruptions.
- Enhance Performance in Challenging Conditions
Pulley lagging enhances the performance of conveyor systems in challenging conditions, such as wet, icy, or muddy environments. The increased grip provided by the lagging ensures that the belt moves efficiently, even when the pulley surface is slippery.
Benefits of Pulley Lagging
- Reduced Slippage
One of the most significant benefits of pulley lagging is the reduction in belt slippage. Slippage can cause material spillage, loss of productivity, and increased wear on the belt and pulley. Lagging provides the necessary traction to keep the belt moving smoothly, minimizing these issues.
- Extended Belt and Pulley Life
By protecting the pulley surface and reducing slippage, lagging extends the life of both the conveyor belt and the pulley. The reduced wear and tear on these components lead to lower maintenance costs and fewer replacements, contributing to overall cost savings.
- Improved Efficiency and Productivity
Conveyor systems with properly installed lagging operate more efficiently and reliably. The reduced slippage and improved belt tracking ensure that materials are transported smoothly and consistently, enhancing productivity and reducing downtime.
- Enhanced Safety
Lagging improves the safety of conveyor systems by reducing the risk of belt slippage and misalignment. These issues can lead to operational disruptions and pose safety hazards to workers. By ensuring smooth and reliable operation, lagging helps create a safer working environment.
- Adaptability to Various Applications
Pulley lagging is available in various materials and designs, making it adaptable to different applications and operating conditions. Whether you need lagging for heavy-duty mining operations or for food processing plants, there is a suitable lagging solution to meet your specific needs.
Pulley lagging is a critical component in conveyor systems, providing numerous benefits in terms of performance, longevity, and safety. By increasing friction between the belt and pulley, protecting the pulley surface, and improving belt tracking, lagging ensures smooth and efficient material handling. Understanding the importance of conveyor belt lagging and implementing proper installation and maintenance practices can significantly enhance the efficiency and reliability of your conveyor system.
Conveyor Belt Lagging: Advantages of Ceramic Pulley Lagging
Conveyor belt lagging is a critical component in the efficient operation of conveyor systems. Among the various types of lagging materials available, ceramic pulley lagging stands out for its unique properties and significant advantages. This section will delve into the benefits of ceramic pulley lagging, its distinctive features, and its applications across different industrial settings.
Unique Properties of Ceramic Pulley Lagging
- High Wear Resistance: Ceramic lagging is renowned for its exceptional resistance to wear and abrasion. The ceramic tiles embedded in the rubber matrix provide a hard, durable surface that can withstand the harshest operating conditions. This makes ceramic lagging ideal for applications involving heavy loads, high speeds, and abrasive materials.
- Enhanced Grip and Friction: The surface of ceramic lagging is designed to enhance grip and friction between the conveyor belt and the pulley. The ceramic tiles often feature a diamond-shaped or button pattern that increases the contact area and improves traction. This enhanced grip minimizes belt slippage, ensuring smooth and efficient material transport.
- Impact Resistance: In addition to its wear resistance, ceramic lagging offers excellent impact resistance. The hardness of the ceramic tiles helps to absorb and distribute the impact forces that occur when heavy or sharp materials are loaded onto the conveyor belt. This property protects both the belt and the pulley from damage.
- Temperature and Chemical Resistance: Ceramic lagging is highly resistant to extreme temperatures and chemical exposure. This makes it suitable for environments where the conveyor system is subjected to high heat, cold, or corrosive substances. The lagging maintains its performance and integrity under these challenging conditions, ensuring reliable operation.
Benefits of Ceramic Pulley Lagging
- Extended Service Life: One of the primary benefits of ceramic pulley lagging is its ability to extend the service life of both the conveyor belt and the pulley. The superior wear and impact resistance of the ceramic tiles reduce the frequency of maintenance and replacements, leading to lower downtime and maintenance costs.
- Improved Efficiency: The enhanced grip and friction provided by ceramic lagging result in more efficient material handling. By preventing belt slippage, the lagging ensures consistent belt speed and alignment, which improves the overall efficiency of the conveyor system. This efficiency translates to higher productivity and reduced energy consumption.
- Reduced Maintenance: Ceramic lagging’s durability and resistance to wear mean that it requires less frequent maintenance compared to other types of lagging. The hard-wearing nature of ceramic tiles minimizes the need for regular inspections and repairs, reducing maintenance costs and operational disruptions.
- Safety: Improved traction and reduced slippage contribute to the safety of the conveyor system. Ceramic lagging helps to prevent belt misalignment and sudden jerks, which can cause material spillage and pose safety hazards. By maintaining smooth and controlled movement, ceramic lagging enhances the overall safety of the conveyor operation.
- Versatility: Ceramic pulley lagging is versatile and can be used in a wide range of industrial applications. It is suitable for various conveyor systems, including those in mining, cement production, power generation, and bulk material handling. Its adaptability makes it a preferred choice for industries with demanding operational requirements.
Applications of Ceramic Pulley Lagging
- Mining Industry: In the mining industry, conveyor systems are exposed to abrasive materials such as ore, coal, and rock. Ceramic pulley lagging provides the necessary wear resistance to handle these tough materials, ensuring reliable operation and prolonged equipment life. It is commonly used in drive pulleys, tail pulleys, and bend pulleys in mining conveyors.
- Cement and Aggregate Industries: Conveyor systems in cement and aggregate production face similar challenges with abrasive materials. Ceramic lagging helps to minimize wear and tear on the pulleys and belts, maintaining efficient material flow and reducing maintenance requirements. It is particularly effective in applications involving clinker, limestone, and other abrasive aggregates.
- Power Generation: In power generation facilities, conveyor systems transport materials such as coal, ash, and biomass. Ceramic pulley lagging enhances the grip and durability of the pulleys, ensuring continuous and efficient material handling. The lagging’s resistance to high temperatures and corrosive environments makes it ideal for these applications.
- Bulk Material Handling: Industries that handle bulk materials, such as grain, fertilizer, and chemicals, benefit from the durability and performance of ceramic pulley lagging. The lagging’s ability to withstand heavy loads and resist chemical exposure ensures reliable operation in bulk material handling applications.
- Recycling and Waste Management: Conveyor systems in recycling and waste management facilities often deal with diverse and abrasive materials. Ceramic lagging provides the necessary durability and grip to handle these materials effectively, reducing the risk of belt slippage and extending the life of the conveyor components.
Conveyor Belt Lagging: Installation Guide for Weld-on Head Pulley Lagging
Installing weld-on head pulley lagging is a crucial step in ensuring the efficient operation and longevity of conveyor systems. This section provides a detailed guide on the installation process for weld-on head pulley lagging, including necessary tools, preparation steps, and best practices.
Tools and Materials Needed
- Weld-on Lagging Strips: Pre-cut strips of lagging material, typically rubber or ceramic, designed for welding onto the pulley surface.
- Welding Equipment: A suitable welding machine and welding rods or wire for attaching the lagging strips to the pulley.
- Measuring Tools: Tape measure, calipers, and a marking pen for accurate measurements and markings.
- Cutting Tools: An angle grinder or cutting torch for trimming the lagging strips to the required size.
- Cleaning Tools: Wire brush, degreaser, and cleaning cloths for preparing the pulley surface.
- Personal Protective Equipment (PPE): Welding helmet, gloves, protective clothing, and safety glasses to ensure safe working conditions.
Preparation Steps
- Safety First: Ensure all safety protocols are in place before starting the installation process. Wear appropriate PPE and make sure the work area is well-ventilated and free of flammable materials.
- Measure and Mark: Measure the circumference and width of the pulley to determine the size and number of lagging strips needed. Use a marking pen to mark the pulley surface where the lagging strips will be welded.
- Clean the Pulley Surface: Thoroughly clean the pulley surface to remove any dirt, grease, rust, or old lagging material. Use a wire brush and degreaser to achieve a clean, smooth surface. This step is crucial for ensuring proper adhesion of the lagging strips.
- Cut Lagging Strips to Size: If the lagging strips are not pre-cut, use an angle grinder or cutting torch to trim them to the required size. Ensure that the strips are slightly shorter than the circumference of the pulley to allow for a small gap between the ends.
Installation Process
- Position the First Strip: Place the first lagging strip on the marked pulley surface, aligning it with the marks. Ensure that the strip is positioned correctly and securely before welding.
- Weld the First Strip: Using the welding equipment, weld the first strip to the pulley. Start by tacking the strip in place at several points along its length to hold it securely. Then, proceed to weld along the entire length of the strip, ensuring continuous and strong welds. Pay attention to the edges and ends of the strip to ensure they are securely welded.
- Repeat for Additional Strips: Continue to position and weld additional lagging strips around the circumference of the pulley. Ensure that each strip is aligned properly and that the ends of adjacent strips are aligned to form a continuous surface. Leave a small gap between the ends of each strip to allow for thermal expansion.
- Inspect the Welds: After welding all the lagging strips, inspect the welds to ensure they are continuous and free of defects. Look for any gaps, weak spots, or areas that may require additional welding. Make any necessary repairs to ensure the lagging is securely attached.
- Clean and Finish: Once the welding is complete, clean the pulley surface to remove any welding residue or debris. Use a wire brush and cleaning cloths to achieve a clean finish. If desired, apply a protective coating to the welded areas to prevent corrosion and enhance the durability of the lagging.
Looking for reliable conveyor belts? Send us your inquiry!
Best Practices for Installation
- Follow Manufacturer Instructions: Always follow the manufacturer’s instructions for the specific type of weld-on lagging being used. This ensures that the installation process is carried out correctly and safely.
- Ensure Proper Alignment: Accurate alignment of the lagging strips is crucial for achieving a smooth and even surface. Misaligned strips can cause uneven wear and reduce the effectiveness of the lagging.
- Use Appropriate Welding Techniques: Use the recommended welding techniques and settings for the type of lagging material and pulley surface. Proper welding ensures strong and durable bonds between the lagging and the pulley.
- Allow for Thermal Expansion: Leave small gaps between the ends of the lagging strips to allow for thermal expansion. This prevents the strips from buckling or becoming dislodged during operation.
- Regular Inspection and Maintenance: Regularly inspect the lagging and pulley for signs of wear or damage. Perform routine maintenance to address any issues and ensure the lagging remains in good condition.
Conveyor belt lagging is essential for enhancing the performance, efficiency, and longevity of conveyor systems. Ceramic pulley lagging offers unique properties and significant advantages, including high wear resistance, enhanced grip, impact resistance, and temperature and chemical resistance. It is widely used in various industries, including mining, cement production, power generation, and bulk material handling.
FAQs about Conveyor Belt Lagging
Rubber lagging refers to the process of applying a layer of rubber material to the surface of conveyor belt pulleys and rollers. This layer is designed to enhance the friction between the belt and the pulley, thereby improving the overall efficiency of the conveyor system. Rubber lagging comes in various types, including plain, diamond, and ceramic lagging, each suited for different applications and operating conditions. Plain rubber lagging provides basic friction enhancement, while diamond-patterned lagging offers increased grip and is often used in more demanding environments. Ceramic lagging incorporates ceramic tiles into the rubber, providing superior wear resistance and grip, especially in harsh or abrasive conditions. The primary purpose of rubber lagging is to prevent slippage between the belt and the pulley, reduce wear and tear, and extend the life of both the conveyor belt and the pulley. Additionally, it helps in noise reduction and energy efficiency, contributing to smoother and more reliable conveyor operation.
The primary purpose of a lagged pulley is to increase the friction between the conveyor belt and the pulley surface. By doing so, it prevents belt slippage, which is crucial for maintaining efficient and consistent movement of materials along the conveyor system. A lagged pulley also helps to distribute the load more evenly across the belt, reducing the risk of wear and tear on specific areas of the belt and extending its overall lifespan. Moreover, lagged pulleys are instrumental in improving the grip on the belt, especially in wet or dusty environments, ensuring that the conveyor system operates smoothly under various conditions. In addition to enhancing grip and reducing slippage, lagged pulleys also play a significant role in minimizing maintenance requirements. By reducing direct metal-to-belt contact, they help to lower the chances of belt damage and the need for frequent replacements. This not only saves on maintenance costs but also reduces downtime, leading to increased productivity and efficiency in the material handling process.
A lagged roller, similar to a lagged pulley, is a roller within a conveyor system that has been coated with a layer of rubber or another friction-enhancing material. The primary function of a lagged roller is to improve the grip between the roller and the conveyor belt, thereby enhancing the overall efficiency of the conveyor system. Lagged rollers are typically used in areas of the conveyor where slippage is a concern or where additional traction is needed to move materials effectively. These rollers can be found in various parts of the conveyor system, including drive rollers, idler rollers, and tension rollers. The rubber coating on the lagged roller helps to reduce wear and tear on both the roller and the belt, extending their operational life. Additionally, lagged rollers can help to dampen vibrations and noise, contributing to a quieter and smoother running conveyor system. By providing better grip and reducing slippage, lagged rollers play a crucial role in maintaining the reliability and efficiency of conveyor operations, especially in challenging environments.
Applying pulley lagging involves several steps to ensure that the rubber coating is properly adhered to the pulley surface and provides the desired friction enhancement. Here is a general overview of the process:
Preparation: Start by thoroughly cleaning the pulley surface to remove any dirt, grease, or old lagging material. This can be done using a wire brush, solvent, or sandblasting, depending on the condition of the pulley. Ensuring a clean surface is crucial for proper adhesion of the new lagging.
Measurement and Cutting: Measure the circumference and width of the pulley to cut the lagging material to the correct size. It’s important to ensure that the lagging material fits precisely without any gaps or overlaps.
Adhesive Application: Apply a suitable adhesive to both the pulley surface and the back of the lagging material. The type of adhesive used will depend on the specific lagging material and pulley application. Follow the manufacturer’s instructions for the adhesive to ensure proper bonding.
Lagging Application: Carefully wrap the lagging material around the pulley, ensuring it is applied evenly and without any air bubbles. Press the lagging firmly onto the pulley to ensure good contact. For large pulleys, it may be necessary to apply the lagging in sections.
Curing and Finishing: Allow the adhesive to cure according to the manufacturer’s instructions. This may involve letting the pulley sit for a certain period or applying heat to accelerate the curing process. Once cured, trim any excess lagging material and inspect the pulley to ensure the lagging is securely attached.
Last Updated on June 21, 2024 by Jordan Smith
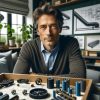
Jordan Smith, a seasoned professional with over 20 years of experience in the conveyor system industry. Jordan’s expertise lies in providing comprehensive solutions for conveyor rollers, belts, and accessories, catering to a wide range of industrial needs. From initial design and configuration to installation and meticulous troubleshooting, Jordan is adept at handling all aspects of conveyor system management. Whether you’re looking to upgrade your production line with efficient conveyor belts, require custom conveyor rollers for specific operations, or need expert advice on selecting the right conveyor accessories for your facility, Jordan is your reliable consultant. For any inquiries or assistance with conveyor system optimization, Jordan is available to share his wealth of knowledge and experience. Feel free to reach out at any time for professional guidance on all matters related to conveyor rollers, belts, and accessories.