Benefits of Corrugated Sidewall Belt Conveyor Design
Sidewall belt conveyor design is crucial for optimizing material handling processes in various industries. This design involves the integration of corrugated sidewalls and cleats to facilitate the transport of bulk materials at steep angles. The principles of sidewall belt conveyor design focus on enhancing efficiency, preventing spillage, and ensuring the durability of the system. Understanding the importance of sidewall belt conveyor design is essential for engineers and designers to create robust and effective material handling solutions that meet specific industry requirements.
Importance of Sidewall Belt Conveyor Design PDF Resources
The availability of sidewall belt conveyor design PDF resources is invaluable for engineers and designers involved in the creation and optimization of conveyor systems. These resources offer detailed guidelines, technical specifications, and best practices that are essential for designing efficient and reliable sidewall belt conveyors. This section will explore why these PDFs are crucial, highlighting their role in providing comprehensive information, ensuring standardization, and supporting innovation in conveyor design.
1. Comprehensive Information
Sidewall belt conveyor design PDF resources provide comprehensive information on all aspects of the design process. They cover everything from basic principles to advanced techniques, offering a wealth of knowledge that can be applied to various design challenges. These documents typically include detailed descriptions of key components, such as the base belt, corrugated sidewalls, cleats, and support structures, as well as guidelines on selecting appropriate materials and dimensions. By consolidating this information in a single resource, PDFs make it easier for engineers and designers to access the knowledge they need to create effective conveyor systems.
2. Standardization and Consistency
One of the primary benefits of using sidewall belt conveyor design PDF resources is the promotion of standardization and consistency in design practices. These documents often include industry standards and best practices, ensuring that all designs adhere to established guidelines. This standardization helps maintain quality and reliability across different projects and reduces the risk of errors and inconsistencies. By following standardized procedures outlined in the PDFs, engineers and designers can ensure that their conveyor systems meet the necessary performance and safety requirements.
3. Technical Specifications and Calculations
Sidewall belt conveyor design involves numerous technical calculations and specifications, such as determining the appropriate belt speed, tension, and power requirements. Design PDF resources typically include detailed formulas, charts, and examples to assist with these calculations. This information is crucial for ensuring that the conveyor system operates efficiently and effectively under various conditions. By providing clear and accurate technical specifications, PDFs help engineers and designers make informed decisions and optimize their designs for specific applications.
4. Design Examples and Case Studies
Many sidewall belt conveyor design PDF resources include design examples and case studies that illustrate real-world applications of different design principles. These examples provide valuable insights into how various design choices can impact the performance and efficiency of a conveyor system. By studying these case studies, engineers and designers can learn from previous successes and challenges, applying this knowledge to their own projects. This practical information helps bridge the gap between theory and practice, enabling more effective and innovative design solutions.
5. Supporting Innovation
Innovation is essential for advancing the field of sidewall belt conveyor design, and PDF resources play a significant role in supporting this innovation. By providing a comprehensive foundation of knowledge and best practices, these resources enable engineers and designers to experiment with new ideas and approaches. Additionally, many PDFs include information on the latest trends and technologies in conveyor design, helping professionals stay up-to-date with industry advancements. This support for innovation ensures that conveyor systems continue to evolve and improve, meeting the ever-changing needs of various industries.
6. Accessibility and Convenience
One of the key advantages of sidewall belt conveyor design PDF resources is their accessibility and convenience. These documents can be easily downloaded, stored, and shared, making them readily available to engineers and designers at any time. This accessibility ensures that valuable information is always within reach, whether in the office or on-site. Furthermore, the digital format of PDFs allows for easy searching and navigation, enabling users to quickly find the information they need. This convenience saves time and effort, streamlining the design process and improving overall efficiency.
7. Training and Education
Sidewall belt conveyor design PDF resources are also valuable tools for training and education. They serve as comprehensive reference materials for new engineers and designers, providing a solid foundation of knowledge on which to build their skills. Many PDFs include step-by-step belt conveyor design guides and tutorials, making them ideal for self-study and professional development. By incorporating these resources into training programs, companies can ensure that their staff is well-equipped with the knowledge and skills needed to design effective conveyor systems.
8. Ensuring Compliance with Regulations
Compliance with industry regulations and standards is critical in sidewall belt conveyor design. PDF resources often include information on relevant regulations, ensuring that designs meet all necessary legal and safety requirements. This compliance is essential for avoiding penalties and ensuring the safe and reliable operation of conveyor systems. By following the guidelines provided in these PDFs, engineers and designers can ensure that their designs adhere to all applicable standards and regulations.
9. Enhancing Collaboration
Collaboration is a key aspect of successful sidewall belt conveyor design, and PDF resources facilitate this collaboration by providing a common reference point for all team members. These documents can be easily shared and reviewed, ensuring that everyone involved in the design process is on the same page. This shared understanding helps streamline communication and decision-making, leading to more cohesive and effective design solutions. By enhancing collaboration, PDF resources contribute to the overall success of conveyor design projects.
The importance of sidewall belt conveyor design PDF resources cannot be overstated. These documents provide comprehensive information, promote standardization, support innovation, and enhance collaboration, making them invaluable tools for engineers and designers. By utilizing these resources, professionals can create efficient, reliable, and compliant conveyor systems that meet the specific needs of their industries. Whether for training, reference, or innovation, sidewall belt conveyor design PDFs are essential for advancing the field of conveyor design and ensuring the success of material handling operations.
Features of Sidewall Belt Conveyor Design
In the modern era of industrial engineering and material handling, the sidewall belt conveyor design has emerged as a revolutionary solution for transporting bulk materials efficiently. This design is especially advantageous in industries requiring the movement of goods over varied elevations and complex paths. To fully appreciate the merits and applications of the sidewall belt conveyor design, it is essential to delve into its features and understand how they influence design decisions.
Flexibility and Adaptability
One of the standout features of sidewall conveyor belts in design is their unparalleled flexibility and adaptability. Unlike traditional conveyor systems, sidewall belts can be designed to navigate sharp inclines and declines, as well as complex curves. This flexibility is achieved through the incorporation of corrugated sidewalls and transverse cleats, which secure the material and prevent spillage. This feature allows for the transportation of materials in a vertical, horizontal, or inclined plane, thereby optimizing the use of space within a facility.
The flexibility of the sidewall belt conveyor design also extends to its ability to handle diverse types of materials. From fine powders to large, bulky items, the design can be customized to meet specific material handling requirements. This adaptability is particularly beneficial in industries such as mining, agriculture, and manufacturing, where the nature of the materials being transported can vary significantly.
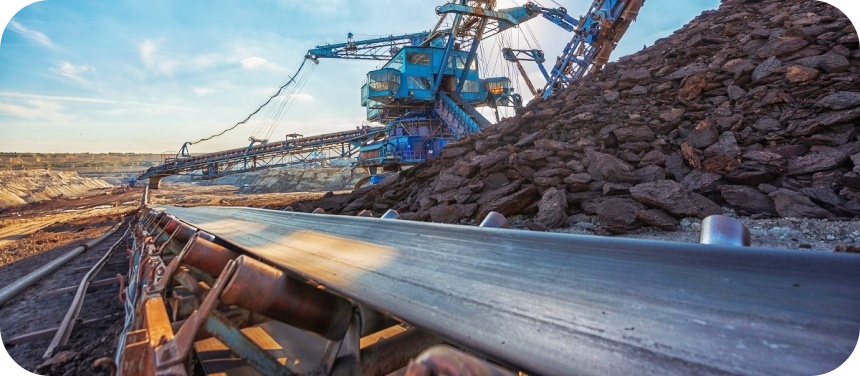
Enhanced Capacity and Efficiency
Another critical feature that influences the sidewall belt conveyor design is its enhanced capacity and efficiency. The unique construction of sidewall belts allows for a significant increase in the load-carrying capacity compared to traditional flat belts. The corrugated sidewalls and cleats not only prevent material spillage but also create pockets that can carry larger volumes of material.
This increased capacity translates directly into higher efficiency, as more material can be transported in a single pass. This is particularly advantageous in high-volume operations, where the ability to move large quantities of material quickly and efficiently is paramount. Additionally, the design reduces the need for multiple conveyor systems, thereby lowering operational costs and simplifying maintenance.
Durability and Longevity
Durability is a cornerstone feature in the design of sidewall conveyor belts. These belts are typically constructed from robust materials such as reinforced rubber or synthetic polymers, which are resistant to wear and tear. The corrugated sidewalls and cleats are also designed to withstand the rigors of continuous operation, including abrasion, impact, and extreme temperatures.
The longevity of sidewall belts is further enhanced by their ability to resist chemical and environmental degradation. In industries such as mining and chemical processing, where exposure to harsh substances is common, the durability of the conveyor belt material is crucial. This resistance to degradation not only extends the lifespan of the conveyor system but also ensures reliable performance over time.
Safety and Environmental Considerations
The sidewall belt conveyor design also prioritizes safety and environmental considerations. The enclosed nature of the conveyor belt, facilitated by the sidewalls and cleats, minimizes the risk of material spillage and dust generation. This is particularly important in industries where dust control is a major concern, such as in food processing or pharmaceuticals.
In addition to reducing environmental impact, the design also enhances worker safety by minimizing the potential for material spillage and associated hazards. The stability provided by the sidewalls and cleats ensures that materials remain securely in place during transport, reducing the risk of accidents and injuries.
Versatility in Design and Application
The versatility of the sidewall belt conveyor design is another feature that greatly influences its adoption across various industries. The design can be tailored to meet specific operational requirements, including the angle of incline, belt width, and cleat height. This customization ensures that the conveyor system can handle the specific characteristics of the material being transported, whether it is fine granules or large, irregularly shaped items.
Moreover, the modular nature of the design allows for easy integration into existing systems. Sidewall belts can be retrofitted into existing conveyor setups, providing a cost-effective solution for upgrading material handling capabilities. This versatility makes sidewall belt conveyors an attractive option for industries looking to enhance their material handling efficiency without significant capital investment.
Maintenance and Cost-Effectiveness
Maintenance considerations are also a key feature in the sidewall belt conveyor design. The robust construction and high-quality materials used in the belts reduce the frequency of maintenance requirements. When maintenance is needed, the modular design allows for quick and easy replacement of components such as sidewalls and cleats, minimizing downtime and associated costs.
The cost-effectiveness of sidewall belt conveyors is further enhanced by their energy efficiency. The ability to transport materials over varied elevations and complex paths in a single pass reduces the need for multiple conveyors and associated energy consumption. This not only lowers operational costs but also contributes to the sustainability goals of the organization.
The features of sidewall conveyor belts in design offer numerous advantages that make them a preferred choice in various industrial applications. The flexibility and adaptability of the design allow for efficient material handling over complex paths and varied elevations. Enhanced capacity and efficiency ensure that large volumes of material can be transported quickly and reliably. The durability and longevity of the belts, combined with safety and environmental considerations, provide a robust and reliable solution for material handling needs.
The versatility of the sidewall belt conveyor design allows for customization to meet specific operational requirements, while the modular nature of the system facilitates easy integration and maintenance. The cost-effectiveness of the design, both in terms of operational efficiency and energy consumption, further underscores its value in industrial applications.
As industries continue to seek innovative solutions for material handling, the sidewall belt conveyor design stands out as a versatile, efficient, and reliable option that meets the diverse needs of modern operations.
Benefits of Using Corrugated Sidewall Belt Conveyor Design
Corrugated sidewall conveyor belts are integral to many modern material handling systems, providing numerous benefits that enhance the efficiency and functionality of sidewall belt conveyor design. These benefits stem from the unique structure and capabilities of corrugated sidewall belts, which allow for the transport of materials at steep angles and over complex paths. This section provides an in-depth overview of the advantages of incorporating corrugated sidewall conveyor belts in design projects.
1. Enhanced Material Handling Capabilities
One of the primary benefits of using a corrugated sidewall conveyor belt in sidewall belt conveyor design is its enhanced material handling capabilities. The corrugated sidewalls and integrated cleats enable the conveyor to transport materials at steep inclines, often up to 90 degrees. This capability allows for more efficient use of vertical space and minimizes the footprint of the conveyor system. It is particularly beneficial in environments with limited floor space or where vertical material transport is essential.
2. Prevention of Material Spillage
The design of corrugated sidewall conveyor belts helps prevent material spillage, which is a common issue in traditional conveyor systems. The corrugated sidewalls act as barriers that contain the material on the belt, while the cleats provide additional support to hold the material in place during transport. This containment reduces waste and keeps the work environment clean, which is especially important when handling hazardous or valuable materials. Preventing spillage also minimizes downtime caused by cleanup and maintenance, thereby improving overall productivity.
3. Increased Load Carrying Capacity
Corrugated sidewall conveyor belts significantly increase the load-carrying capacity of a conveyor system. The sidewalls and cleats create pockets that can carry larger volumes of material compared to flat belts. This increased capacity allows for more efficient transport of bulk materials, reducing the number of trips required and lowering operational costs. In sidewall belt conveyor design, this benefit translates to higher throughput and improved efficiency, making it ideal for industries that handle large quantities of materials, such as mining, agriculture, and manufacturing.
4. Versatility in Material Types
Another advantage of using corrugated sidewall conveyor belts is their versatility in handling a wide range of material types. Whether dealing with fine powders, granules, or large, irregularly shaped items, these belts can accommodate various materials without compromising performance. This versatility makes them suitable for diverse applications across different industries, enhancing the adaptability of the conveyor system. In sidewall belt conveyor design, incorporating corrugated sidewall belts ensures that the system can handle different material types with ease, providing a flexible and robust solution.
5. Customizable Design Options
Corrugated sidewall conveyor belts offer extensive customization options, allowing designers to tailor the belts to specific application requirements. The height of the sidewalls, the type and spacing of the cleats, and the belt material can all be customized to optimize performance for particular tasks. This customization ensures that the conveyor system is perfectly suited to the intended application, enhancing efficiency and reliability. In sidewall belt conveyor design, the ability to customize these belts provides significant advantages, allowing for precise adjustments to meet the unique needs of each project.
6. Improved Safety and Maintenance
Safety is a critical consideration in sidewall belt conveyor design, and corrugated sidewall conveyor belts contribute to safer operation. By containing materials and preventing spillage, these belts reduce the risk of accidents caused by loose materials on the floor. Additionally, the robust design of corrugated sidewall belts requires less maintenance compared to traditional belts, as they are less prone to wear and tear. This durability extends the lifespan of the conveyor system and reduces the frequency and cost of maintenance activities, contributing to a safer and more cost-effective operation.
7. Efficient Use of Space
The ability to transport materials at steep angles allows corrugated sidewall conveyor belts to make efficient use of available space. This efficiency is particularly advantageous in facilities where space is at a premium. By minimizing the footprint of the conveyor system and maximizing vertical space utilization, these belts enable more compact and efficient plant layouts. In sidewall belt conveyor design, incorporating corrugated sidewall belts can lead to significant space savings, allowing for more streamlined and effective facility designs.
8. Compatibility with Existing Systems
Corrugated sidewall conveyor belts are designed to be compatible with existing conveyor systems, making them an easy upgrade option for enhancing material handling capabilities. This compatibility means that businesses can integrate these belts into their current setups without significant modifications, reducing the time and cost associated with upgrading. In sidewall belt conveyor design, the seamless integration of corrugated sidewall belts ensures that the system can be easily enhanced to meet evolving operational needs.
9. Energy Efficiency
The design of corrugated sidewall conveyor belts contributes to energy efficiency in material handling operations. By reducing the need for additional conveyors or equipment to handle steep inclines, these belts minimize energy consumption. Additionally, the efficient transport of materials at higher capacities reduces the overall energy required for operation. In sidewall belt conveyor design, incorporating corrugated sidewall belts can lead to significant energy savings, contributing to more sustainable and cost-effective operations.
The benefits of using corrugated sidewall conveyor belts in sidewall belt conveyor design are numerous and impactful. These belts enhance material handling capabilities, prevent spillage, increase load carrying capacity, and offer versatility in handling different materials. Their customizable design options, improved safety, efficient space use, compatibility with existing systems, and energy efficiency make them an invaluable component in modern conveyor systems. By incorporating corrugated sidewall belts into their designs, engineers and designers can create more efficient, reliable, and cost-effective material handling solutions that meet the diverse needs of various industries.
Role of Cleated Conveyor Belt in Sidewall Belt Conveyor Design
Cleated conveyor belts play a crucial role in the effectiveness and efficiency of sidewall belt conveyor design. These belts feature raised sections, or cleats, that are perpendicular to the belt’s surface, providing additional support and grip for the materials being transported. This section examines how cleated conveyor belts are integrated into sidewall belt conveyor design and the advantages they offer in various applications.
1. Enhanced Material Stability
One of the primary roles of cleated conveyor belts in sidewall belt conveyor design is to enhance material stability during transport. The cleats create compartments that hold the material in place, preventing it from sliding or rolling back, especially on steep inclines. This stability is essential for ensuring the smooth and efficient transport of materials, reducing the risk of spillage and loss. In sidewall belt conveyor design, incorporating cleated belts helps maintain consistent material flow and minimizes interruptions in the handling process.
2. Increased Load Capacity
Cleated conveyor belts significantly increase the load capacity of a conveyor system. The cleats provide additional surface area and support, allowing the belt to carry larger volumes of material without compromising stability. This increased capacity is particularly beneficial in applications that involve transporting bulk materials over long distances or at high speeds. In sidewall belt conveyor design, using cleated belts enhances the system’s ability to handle larger loads, improving overall efficiency and productivity.
3. Versatility in Material Handling
Cleated conveyor belts offer versatility in handling a wide range of materials, from fine powders to large, irregularly shaped items. The design and spacing of the cleats can be customized to accommodate different material types and sizes, ensuring optimal performance for specific applications. This versatility makes cleated belts suitable for various industries, including agriculture, mining, and manufacturing. In sidewall belt conveyor design, incorporating cleated belts ensures that the system can adapt to different material handling requirements, providing a flexible and robust solution.
4. Improved Incline and Decline Handling
Cleated conveyor belts are particularly effective in handling materials on steep inclines and declines. The cleats provide the necessary grip to prevent materials from sliding back, ensuring smooth and controlled transport. This capability is crucial for applications that require vertical or near-vertical movement of materials. In sidewall belt conveyor design, cleated belts enable the creation of systems that can efficiently move materials across different elevations, optimizing space and improving operational efficiency.
5. Customizable Cleat Designs
The design of the cleats on a conveyor belt can be customized to meet specific application needs. Different cleat shapes, such as T-cleats, L-cleats, and I-cleats, offer varying degrees of support and grip, allowing designers to select the most appropriate type for their requirements. The height, spacing, and angle of the cleats can also be adjusted to optimize material handling performance. In sidewall belt conveyor design, the ability to customize cleat designs provides significant advantages, enabling tailored solutions that enhance efficiency and reliability.
6. Enhanced Durability and Maintenance
Cleated conveyor belts are designed to withstand the rigors of heavy-duty material handling. The cleats are typically made from durable materials that resist wear and tear, ensuring a long service life. Additionally, the cleats’ robust design reduces the likelihood of damage and minimizes maintenance requirements. This durability is essential for maintaining continuous operation and reducing downtime. In sidewall belt conveyor design, using cleated belts ensures that the system remains reliable and efficient over time, minimizing maintenance costs and operational disruptions.
7. Efficient Space Utilization
Cleated conveyor belts contribute to efficient space utilization in sidewall belt conveyor design. By enabling the transport of materials at steep angles, these belts reduce the need for extensive horizontal conveyor systems. This vertical transport capability allows for more compact and streamlined facility layouts, maximizing the use of available space. In sidewall belt conveyor design, incorporating cleated belts helps create more efficient and effective material handling systems that make optimal use of limited space.
Sidewall Belt Conveyor Design: Advantages of V-Guide Conveyor Belt in Sidewall Systems
In the realm of material handling and conveyor system engineering, the sidewall belt conveyor design has become a pivotal solution for transporting bulk materials efficiently over complex paths and varied elevations. One crucial component that enhances the performance and reliability of sidewall belt conveyor systems is the V-guide conveyor belt. This section will delve into the advantages of using V-guide conveyor belts in sidewall belt conveyor design, highlighting their role in improving tracking, reducing maintenance, and enhancing overall system efficiency.
Improved Belt Tracking
One of the primary advantages of incorporating V-guide conveyor belts into sidewall belt conveyor design is the significant improvement in belt tracking. Belt tracking refers to the ability of the conveyor belt to remain aligned with the conveyor frame during operation. Proper tracking is essential to prevent belt misalignment, which can lead to material spillage, increased wear and tear, and potential system downtime.
The V-guide, which is a continuous, raised strip running along the length of the belt’s underside, fits into a corresponding groove on the conveyor frame or pulley. This guide ensures that the belt remains centered and follows a precise path, reducing the likelihood of misalignment. By maintaining consistent tracking, V-guide conveyor belts help to ensure smooth and uninterrupted operation, which is critical for maintaining high productivity levels in industrial settings.
Enhanced Durability and Longevity
Durability is a key consideration in the sidewall belt conveyor design, particularly in industries where conveyor systems are subjected to harsh operating conditions. V-guide conveyor belts contribute to enhanced durability and longevity by reducing the mechanical stress associated with belt misalignment. When a conveyor belt is misaligned, it can rub against the conveyor frame or other components, leading to premature wear and tear.
The V-guide minimizes this mechanical stress by keeping the belt properly aligned, thereby reducing friction and wear. This not only extends the life of the belt but also lowers the frequency of maintenance and replacement, resulting in cost savings for the operation. Additionally, the V-guide itself is typically constructed from durable materials that can withstand the rigors of continuous operation, further contributing to the overall longevity of the conveyor system.
Increased Operational Efficiency
Operational efficiency is a critical factor in the success of any material handling system. The use of V-guide conveyor belts in sidewall belt conveyor design enhances efficiency by ensuring reliable and consistent belt performance. Proper belt tracking, facilitated by the V-guide, reduces the risk of material spillage and system downtime, both of which can significantly impact productivity.
In applications where precise material handling is required, such as in the food processing or pharmaceutical industries, the V-guide’s ability to maintain accurate belt alignment is particularly beneficial. It ensures that materials are transported in a controlled and efficient manner, minimizing waste and ensuring compliance with industry standards. This level of efficiency is essential for maintaining competitive advantage and meeting production targets.
Reduced Maintenance Requirements
Maintenance is an inevitable aspect of any conveyor system, but the use of V-guide conveyor belts can significantly reduce the frequency and complexity of maintenance tasks. By preventing belt misalignment, the V-guide reduces the wear and tear on the belt and other conveyor components, such as pulleys and rollers. This leads to fewer maintenance interventions and longer intervals between service checks.
When maintenance is required, the design of the V-guide conveyor belt allows for easier identification and correction of issues. The V-guide itself provides a clear visual indicator of belt alignment, enabling maintenance personnel to quickly identify any deviations and make necessary adjustments. This streamlined maintenance process not only saves time but also reduces labor costs and minimizes system downtime.
Enhanced Safety and Environmental Considerations
Safety is a paramount concern in industrial operations, and the use of V-guide conveyor belts in sidewall belt conveyor design contributes to a safer working environment. By ensuring proper belt alignment, the V-guide reduces the risk of material spillage and associated hazards, such as slips and falls. This is particularly important in industries handling hazardous or slippery materials, where spillage can pose significant safety risks.
In addition to improving safety, the V-guide also supports environmental considerations by minimizing material waste. Properly aligned belts reduce the likelihood of spillage, ensuring that materials are transported efficiently and without loss. This not only conserves resources but also reduces the environmental impact of the operation, aligning with sustainability goals and regulatory requirements.
Versatility and Customization
The versatility of V-guide conveyor belts is another advantage that enhances their application in sidewall belt conveyor design. V-guides can be customized to suit specific operational requirements, including the size, shape, and material of the guide. This customization ensures that the V-guide can handle a wide range of materials and operating conditions, making it suitable for diverse industrial applications.
Moreover, the modular nature of V-guide conveyor belts allows for easy integration into existing conveyor systems. This adaptability makes them an attractive option for operations looking to upgrade their material handling capabilities without significant capital investment. The ability to tailor the V-guide to specific needs ensures that the conveyor system operates at optimal efficiency and meets the unique demands of the application.
The advantages of using V-guide conveyor belts in sidewall belt conveyor design are manifold. From improved belt tracking and enhanced durability to increased operational efficiency and reduced maintenance requirements, V-guides play a crucial role in optimizing the performance and reliability of sidewall conveyor systems. By ensuring proper belt alignment, V-guides contribute to a safer working environment, support environmental sustainability, and provide the versatility needed to meet diverse industrial needs.
Submit your request for conveyor belts here, and our team will provide you with the best options and pricing available.
As industries continue to seek innovative solutions for material handling, the incorporation of V-guide conveyor belts into sidewall belt conveyor design stands out as a practical and effective strategy. The benefits of V-guides extend beyond immediate operational improvements, offering long-term advantages that enhance the overall productivity and sustainability of conveyor systems.
Essential Conveyor Belt Tools for Sidewall Belt Conveyor Design
Designing and maintaining sidewall belt conveyor systems requires a comprehensive set of tools to ensure optimal performance, efficiency, and longevity. The sidewall belt conveyor design involves intricate planning and precise implementation, making it essential to utilize the right tools at every stage. This section will provide a detailed overview of the critical conveyor belt tools used in the design and maintenance of sidewall belt conveyors, highlighting their functions and importance.
Design and Planning Tools
- CAD Software
Computer-Aided Design (CAD) software is a fundamental tool in the sidewall belt conveyor design process. CAD software allows engineers to create detailed, accurate models of the conveyor system, including the sidewalls, cleats, and V-guides. These models facilitate precise planning and visualization, enabling designers to identify potential issues and optimize the conveyor layout before physical construction begins.
- Simulation Software
Simulation software is used to model the behavior of the conveyor system under various operating conditions. This tool helps engineers assess the system’s performance, identify bottlenecks, and evaluate the impact of different design choices. By simulating real-world scenarios, designers can make informed decisions that enhance the efficiency and reliability of the sidewall belt conveyor.
- Load Calculation Tools
Load calculation tools are essential for determining the capacity and strength requirements of the conveyor belt. These tools help engineers calculate the maximum load the belt can handle, considering factors such as material weight, belt speed, and incline angle. Accurate load calculations are crucial for ensuring the conveyor system operates safely and efficiently.
Installation and Alignment Tools
- Laser Alignment Systems
Laser alignment systems are used to ensure precise alignment of the conveyor belt and its components. Proper alignment is critical for preventing belt misalignment and ensuring smooth operation. Laser alignment tools provide accurate measurements and visual guides, making it easier to achieve optimal alignment during installation and maintenance.
- Tension Meters
Tension meters measure the tension of the conveyor belt to ensure it is within the recommended range. Proper belt tension is essential for preventing slippage, reducing wear and tear, and maintaining efficient operation. Tension meters provide accurate readings, allowing maintenance personnel to make necessary adjustments and maintain optimal belt performance.
- Conveyor Belt Skivers
Conveyor belt skivers are used to remove the top cover of the conveyor belt, preparing it for the installation of mechanical fasteners or splices. Skiving ensures a smooth, even surface, which is essential for creating strong, reliable joints. This tool is particularly important in the maintenance and repair of sidewall conveyor belts.
Maintenance and Repair Tools
- Belt Cutters
Belt cutters are used to cut conveyor belts to the required length during installation or repair. These tools provide clean, precise cuts, ensuring that the belt edges are even and reducing the risk of fraying. Belt cutters are available in various sizes and designs to accommodate different belt widths and thicknesses.
- Belt Clamps
Belt clamps are used to hold the conveyor belt in place during maintenance and repair tasks. These clamps provide a secure grip, preventing the belt from moving and ensuring safety while work is being performed. Belt clamps are essential for tasks such as installing splices, repairing damage, or replacing sections of the belt.
- Splicing Tools
Splicing tools are used to join the ends of the conveyor belt, creating a continuous loop. There are several types of splicing methods, including mechanical fasteners, vulcanization, and cold bonding. Each method requires specific tools and techniques to ensure a strong, durable splice. Proper splicing is critical for maintaining the integrity and performance of the conveyor belt.
Monitoring and Diagnostic Tools
- Condition Monitoring Systems
Condition monitoring systems provide real-time data on the health and performance of the conveyor belt. These systems use sensors to track parameters such as belt speed, tension, temperature, and vibration. By continuously monitoring these parameters, maintenance personnel can identify potential issues before they become critical, reducing the risk of unexpected downtime and costly repairs.
- Infrared Thermometers
Infrared thermometers are used to measure the temperature of the conveyor belt and its components. Excessive heat can indicate issues such as friction, misalignment, or overloading. By regularly monitoring temperature, maintenance personnel can identify and address problems early, preventing damage and extending the
life of the conveyor system.
- Ultrasonic Thickness Gauges
Ultrasonic thickness gauges measure the thickness of the conveyor belt and its sidewalls. This tool is essential for monitoring wear and tear, ensuring that the belt remains within safe operating limits. Regular thickness measurements help maintenance personnel plan for timely replacements and prevent unexpected failures.
The successful design and maintenance of sidewall belt conveyor systems depend on the use of a comprehensive set of tools. From design and planning tools like CAD software and simulation programs to installation and alignment tools such as laser alignment systems and tension meters, each tool plays a critical role in ensuring optimal performance and efficiency. Maintenance and repair tools, including belt cutters, clamps, and splicing tools, are essential for keeping the conveyor system in good working order. Monitoring and diagnostic tools like condition monitoring systems, infrared thermometers, and ultrasonic thickness gauges provide valuable data that helps prevent issues and extend the life of the conveyor belt.
By utilizing these essential conveyor belt tools, engineers and maintenance personnel can ensure that sidewall belt conveyor systems operate reliably, efficiently, and safely, meeting the demands of modern industrial applications. The strategic use of these tools in the sidewall belt conveyor design process contributes to the overall success and sustainability of material handling operations.
FAQs about Sidewall Belt Conveyor Design
A sidewall conveyor belt is a specialized type of conveyor belt designed to transport materials at steep angles, even vertically. This type of belt features corrugated sidewalls and transverse cleats that prevent materials from falling off the belt. The corrugated sidewalls create pockets that securely hold the material, while the cleats support and stabilize the load as it moves along the conveyor. Sidewall conveyor belts are commonly used in industries such as mining, construction, agriculture, and recycling, where space is limited and materials need to be transported efficiently over short distances or steep inclines. These belts help maximize space utilization and improve operational efficiency by allowing for the vertical or near-vertical transport of bulk materials.
Designing a belt conveyor involves several key steps to ensure that the system meets the specific requirements of the application. Here are the main steps to consider:
Determine Material Characteristics: Understand the properties of the materials to be conveyed, including bulk density, particle size, moisture content, and flowability. These characteristics influence the design of the conveyor belt and the selection of components.
Define Conveyor Capacity: Calculate the required conveyor capacity, which is the amount of material to be transported per unit of time. This is typically measured in tons per hour (TPH) or cubic meters per hour (m³/h).
Select Belt Width and Speed: Choose the appropriate belt width and speed based on the conveyor capacity and material characteristics. Wider belts can carry larger volumes, while higher speeds increase the material throughput.
Determine Conveyor Length and Elevation: Measure the distance the material needs to be transported and the elevation changes along the route. These factors will influence the conveyor layout and the power requirements.
Select Conveyor Components: Choose suitable conveyor components, including pulleys, idlers, drive units, and tensioning devices. Ensure that these components are compatible with the material characteristics and the overall design of the conveyor.
Design Structural Support: Design the structural support for the conveyor, including the frame and supports. Ensure that the structure can handle the weight of the conveyor and the material being transported.
Consider Safety and Maintenance: Incorporate safety features such as emergency stops, guards, and pull cords. Design the conveyor for easy maintenance, including access points for cleaning and replacing components.
Calculate Power Requirements: Determine the power requirements for the conveyor system, including the motor size and drive unit specifications. Consider factors such as belt tension, friction, and material load.
Designing a conveyor system involves several key criteria to ensure that it meets the operational requirements and performs efficiently. Here are some important criteria to consider:
Material Characteristics: Understand the properties of the material to be conveyed, including its bulk density, particle size, moisture content, abrasiveness, and flowability. These factors influence the choice of conveyor components and the design of the system.
Conveyor Capacity: Determine the required conveyor capacity, which is the amount of material to be transported per unit of time. This is typically measured in tons per hour (TPH) or cubic meters per hour (m³/h).
Belt Width and Speed: Choose the appropriate belt width and speed based on the conveyor capacity and material characteristics. The belt width should be sufficient to handle the material volume, while the speed should ensure efficient material transport without spillage.
Conveyor Length and Elevation: Measure the distance the material needs to be transported and the elevation changes along the route. These factors influence the conveyor layout, the type of conveyor, and the power requirements.
Component Selection: Select suitable conveyor components, including pulleys, idlers, drive units, and tensioning devices. Ensure that these components are compatible with the material characteristics and the overall design of the conveyor.
Structural Support: Design the structural support for the conveyor, including the frame and supports. Ensure that the structure can handle the weight of the conveyor and the material being transported.
Safety Features: Incorporate safety features such as emergency stops, guards, and pull cords. Ensure that the conveyor system complies with relevant safety standards and regulations.
Maintenance Access: Design the conveyor for easy maintenance, including access points for cleaning, inspection, and replacing components. Consider the ease of access to critical parts of the conveyor.
Power Requirements: Calculate the power requirements for the conveyor system, including the motor size and drive unit specifications. Consider factors such as belt tension, friction, and material load.
Environmental Considerations: Consider the environmental conditions in which the conveyor will operate, such as temperature, humidity, and exposure to chemicals or abrasive materials. Choose materials and components that can withstand these conditions.
There are several types of belt conveyors, each designed for specific applications and operational requirements. Here are some common types:
Flat Belt Conveyor: The most widely used type of conveyor belt, flat belt conveyors are used for transporting general materials in a straight line. They are simple in design, cost-effective, and can handle a variety of materials.
Incline/Decline Belt Conveyor: These conveyors have belts that can operate on an incline or decline, allowing materials to be transported to different elevations. They are often used in manufacturing and packaging industries.
Modular Belt Conveyor: Made up of interlocking plastic modules, these conveyors are highly flexible and can be customized to fit various configurations, including curves. They are suitable for food processing and packaging applications.
Cleated Belt Conveyor: Equipped with cleats or ribs, these conveyors are designed to prevent materials from sliding backward on the belt, making them ideal for transporting loose or bulk materials up steep inclines.
Sidewall Belt Conveyor: Featuring corrugated sidewalls and transverse cleats, these conveyors are used for transporting materials at steep angles or even vertically, providing efficient space utilization in confined areas.
Wire Mesh Belt Conveyor: These conveyors use a wire mesh belt to transport materials that require cooling, drying, or drainage. They are commonly used in food processing, baking, and parts washing applications.
Bucket Elevator Conveyor: This type of conveyor uses buckets attached to a belt to transport materials vertically. It is ideal for handling bulk materials like grains, coal, and minerals.
Overland Conveyor: Used for long-distance material transport, overland conveyors are typically used in mining and quarrying operations. They can cover several kilometers and are designed to handle large volumes of material efficiently.
Last Updated on July 22, 2024 by Jordan Smith
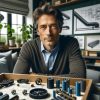
Jordan Smith, a seasoned professional with over 20 years of experience in the conveyor system industry. Jordan’s expertise lies in providing comprehensive solutions for conveyor rollers, belts, and accessories, catering to a wide range of industrial needs. From initial design and configuration to installation and meticulous troubleshooting, Jordan is adept at handling all aspects of conveyor system management. Whether you’re looking to upgrade your production line with efficient conveyor belts, require custom conveyor rollers for specific operations, or need expert advice on selecting the right conveyor accessories for your facility, Jordan is your reliable consultant. For any inquiries or assistance with conveyor system optimization, Jordan is available to share his wealth of knowledge and experience. Feel free to reach out at any time for professional guidance on all matters related to conveyor rollers, belts, and accessories.