Belt Training Conveyor: Maximizing Efficiency in Material Handling
Belt training conveyor refers to the process of aligning and adjusting a conveyor belt to ensure it runs straight and true along its pathway. Proper belt training in conveyor systems is crucial for maintaining operational efficiency and extending the longevity of the equipment. Without correct belt training, conveyors can suffer from misalignment, leading to increased wear and tear, frequent maintenance, and potential downtime. Common issues include belts running off-track, material build-up, and misaligned pulleys and idlers. Solutions involve regular inspection, precise adjustments, and the use of training idlers and tracking systems to keep the belt properly aligned and functioning smoothly.
Preparing for Belt Training Conveyor
Proper preparation is essential for successful belt training in conveyor systems. This involves understanding the resources available, following precise alignment procedures, and considering the costs associated with training equipment. By thoroughly preparing, you can ensure the longevity and efficiency of your conveyor system.
Belt Training Conveyor PDF Resources
Detailed manuals and guides are indispensable when it comes to belt training conveyor systems. These resources provide step-by-step instructions, technical diagrams, and troubleshooting tips that can significantly simplify the training process. Here are some key reasons why Belt Training Conveyor PDF resources are important:
- Comprehensive Information: PDFs often contain exhaustive details about the belt training conveyor, covering everything from the basic principles to advanced techniques. This comprehensive information ensures that all aspects of the conveyor belt’s operation and maintenance are understood.
- Standard Procedures: Manuals typically outline standard operating procedures that must be followed to achieve optimal results. These procedures ensure consistency in the training process, minimizing errors and reducing the likelihood of operational disruptions.
- Troubleshooting Tips: Belt training conveyor PDF guides often include sections dedicated to troubleshooting common issues. These sections can save time and resources by providing quick solutions to problems such as misalignment or material build-up.
- Visual Aids: Diagrams and images included in PDFs can make complex concepts easier to understand. Visual aids help in identifying parts, understanding their functions, and performing correct adjustments.
- Accessibility: PDFs are easily accessible and can be stored digitally for quick reference. They can be shared across teams, ensuring that everyone involved in the maintenance and operation of the conveyor system is on the same page.
Conveyor Belt Alignment Procedure PDF
Ensuring the conveyor belt is properly aligned is crucial for the efficient functioning of the system. The conveyor belt alignment procedure PDF is a key resource that outlines the necessary steps and checklists for alignment. Here’s a detailed look at why this document is essential and what it typically includes:
- Initial Setup Instructions: The PDF provides detailed instructions on setting up the conveyor belt initially. This includes ensuring the conveyor frame is level and square, which is critical for accurate belt tracking.
- Alignment Checklists: Comprehensive checklists are provided to ensure that all necessary steps are followed during the alignment process. These checklists help in systematically addressing each aspect of the conveyor’s alignment, ensuring nothing is overlooked.
- Step-by-Step Alignment Process: The document breaks down the alignment process into clear, manageable steps. Starting with the head pulley, the process typically involves making incremental adjustments and checking the belt’s position at each stage.
- Tools and Equipment: The PDF lists the tools and equipment required for alignment, ensuring that you have everything needed before starting the process. This can include levels, straight edges, and alignment lasers.
- Safety Precautions: Safety is a priority in any maintenance procedure. The PDF includes safety guidelines to protect personnel during the alignment process. This can involve lockout/tagout procedures and protective gear requirements.
- Final Inspection: Once alignment adjustments are made, the PDF guides you through the final inspection process. This involves running the conveyor to check for proper belt tracking and making any final tweaks as necessary.
Belt Training Conveyor Price
The cost of belt training conveyor systems can vary widely depending on several factors. Understanding these factors can help in budgeting and ensuring that you get the best value for your investment. Here are some considerations that influence the belt training conveyor price:
- System Complexity: The complexity of the conveyor system plays a significant role in determining the cost. More complex systems with advanced features and multiple belts will typically be more expensive to train.
- Materials and Components: The quality and type of materials used in the conveyor system affect the price. High-quality belts, pulleys, and idlers may have a higher upfront cost but can offer better durability and performance.
- Customization Requirements: Customized conveyor systems designed to meet specific operational needs will usually cost more than standard off-the-shelf solutions. Customizations can include specialized belt materials, unique pulley configurations, and tailored training procedures.
- Training and Installation Services: Professional training and installation services are often necessary to ensure that the belt training conveyor is set up and aligned correctly. These services add to the overall cost but can prevent future issues and reduce maintenance expenses.
- Maintenance and Support: Ongoing maintenance and support costs should be factored into the budget. Regular maintenance is crucial for keeping the conveyor system running smoothly and can involve periodic alignment checks, part replacements, and troubleshooting services.
- Technology and Automation: Advanced tracking systems and automation can increase the price but offer significant benefits in terms of efficiency and reduced manual intervention. These systems use sensors and automatic adjustments to keep the belt aligned, minimizing downtime.
- Training Materials: Investing in comprehensive training materials, such as Belt Training Conveyor PDF resources and alignment procedure documents, can add to the initial cost but are essential for long-term success.
- Supplier Reputation: The reputation and reliability of the supplier also influence the price. Established suppliers with a proven track record may charge more but offer better quality products and services.
By considering these factors, you can make informed decisions about the belt training conveyor price and ensure that your investment leads to efficient and trouble-free operations.
Initial Setup and Testing: Belt Training Conveyor
Setting up and testing a belt training conveyor is a crucial step to ensure smooth and efficient operation. Proper initial setup and thorough testing can prevent common issues such as misalignment, excessive wear, and operational downtime. This section outlines the essential steps for ensuring the conveyor is straight and the importance of conducting an initial test run.
Straight Conveyor Setup
One of the first and most critical steps in the belt training conveyor process is ensuring that the conveyor system is perfectly straight. A misaligned conveyor can lead to significant problems down the line, including belt mistracking, increased wear and tear on the belt and components, and potential safety hazards. Here are detailed steps to ensure a straight conveyor setup:
- Foundation and Frame Alignment: Start by checking the foundation on which the conveyor is mounted. It should be level and stable. Use precision leveling tools to ensure that the frame is perfectly aligned. Any deviation in the foundation can lead to alignment issues that are difficult to correct later.
- Frame Squaring: Ensure that the conveyor frame is square. This means that the frame’s diagonal measurements from corner to corner should be equal. Use a tape measure to check the diagonals and adjust the frame until the measurements are the same. This squaring process is essential for the subsequent steps of aligning the pulleys and rollers.
- Pulley Alignment: Align the head and tail pulleys with the frame. The pulleys should be parallel to each other and perpendicular to the conveyor’s centerline. Use a laser alignment tool or a straight edge to check the alignment. Misaligned pulleys can cause the belt to drift to one side, leading to mistracking.
- Roller Placement: Install the idler rollers along the conveyor’s length. Each roller must be positioned correctly to support the belt evenly. Use a straight edge to ensure that each roller is perpendicular to the conveyor frame. Rollers that are not aligned correctly can create points of uneven tension, causing the belt to run off-track.
- Belt Installation: Once the frame, pulleys, and rollers are aligned, install the conveyor belt. Carefully unroll the belt and place it on the conveyor frame, ensuring that it is centered. Avoid twisting the belt during installation, as this can cause tracking issues. Secure the belt ends with the appropriate fasteners or lacing.
- Tensioning the Belt: Proper belt tension is vital for optimal performance. Over-tensioning can cause premature belt wear, while under-tensioning can lead to slippage and mistracking. Use a tension gauge to measure the tension and adjust it according to the manufacturer’s specifications. Uniform tension across the belt’s width is crucial to prevent drifting.
Initial Test Run
After completing the straight conveyor setup, it is essential to conduct an initial test run. This step ensures that the belt training conveyor system operates correctly and identifies any potential issues before full-scale production begins. Here’s why the initial test run is important and how to conduct it effectively:
- Verification of Setup: The initial test run helps verify that all components are correctly installed and aligned. It confirms that the pulleys, rollers, and belt are working in harmony. Run the conveyor at a slow speed initially, observing the belt’s movement and checking for any signs of misalignment or uneven tension.
- Belt Tracking: During the test run, closely monitor the belt tracking. The belt should run straight and stay centered on the pulleys and rollers. If the belt starts to drift, stop the conveyor and make the necessary adjustments to the rollers and pulleys. This step is crucial for preventing long-term tracking issues that can lead to increased maintenance and operational costs.
- Load Testing: Once the belt tracks correctly without any load, gradually introduce a small load to the conveyor. Observe how the belt handles the load and check for any changes in alignment or tension. This step ensures that the conveyor can handle the operational load without issues.
- Adjustment and Fine-Tuning: Use the information gathered during the test run to make any final adjustments. Fine-tune the tension, alignment, and tracking mechanisms to ensure optimal performance. Pay attention to any unusual noises or vibrations, as these can indicate alignment issues or component wear.
- Continuous Monitoring: During the test run, continuously monitor the belt’s performance. Look for signs of wear on the belt edges, check the condition of the rollers and pulleys, and ensure that the belt scraper (if installed) is functioning correctly. Continuous monitoring helps identify minor issues before they become significant problems.
- Documentation and Record Keeping: Document all observations and adjustments made during the test run. Keeping detailed records helps in troubleshooting future issues and ensures that maintenance personnel have a clear understanding of the conveyor’s setup and performance history.
- Operator Training: Ensure that all operators and maintenance personnel are trained on the correct procedures for starting, stopping, and adjusting the conveyor system. Proper training is crucial for preventing operational errors and maintaining the belt training conveyor’s efficiency.
The initial setup and testing of a belt training conveyor are fundamental steps that set the stage for efficient and trouble-free operation. By ensuring that the conveyor is straight and conducting a thorough test run, potential issues can be identified and addressed early, preventing costly downtime and maintenance. Following these detailed steps helps maintain the belt training conveyor’s performance, extending its lifespan and ensuring smooth operations.
Adjustment Process: Belt Training Conveyor
The adjustment process is a critical phase in ensuring that your belt training conveyor operates efficiently and reliably. Proper adjustments help prevent misalignment, reduce wear and tear, and extend the lifespan of your conveyor system. This section provides a detailed guide on adjusting the belt starting from the head pulley, identifying and correcting misalignment, and the role and adjustment of training idlers.
Starting at the Head Pulley
When adjusting a belt training conveyor, it is essential to begin at the head pulley and move backward. This approach ensures that the belt is aligned correctly from the start of its journey, minimizing the risk of misalignment as it travels along the conveyor.
- Initial Inspection: Begin by conducting a thorough inspection of the head pulley. Ensure that the pulley is clean, free of debris, and rotates smoothly. Check for any signs of wear or damage that could affect alignment.
- Pulley Alignment: The head pulley must be perfectly aligned with the conveyor frame. Use a laser alignment tool or a straight edge to check that the head pulley is parallel to the tail pulley and perpendicular to the conveyor’s centerline. Adjust the pulley as needed to achieve proper alignment.
- Belt Tensioning: Proper tensioning at the head pulley is crucial. The belt should be tight enough to prevent slippage but not so tight that it causes excessive wear. Use a tension gauge to measure the tension and adjust according to the manufacturer’s specifications.
- Fine-Tuning Adjustments: After ensuring the pulley is aligned and the belt is properly tensioned, make fine-tuning adjustments. Run the conveyor at a slow speed and observe the belt’s movement. If the belt tends to drift to one side, adjust the head pulley slightly to correct the tracking.
- Consistent Monitoring: Continue to monitor the belt as it moves over the head pulley. Consistent tracking at the head pulley sets the stage for proper alignment throughout the entire conveyor system.
Identifying Misalignment
Early identification of misalignment is vital for maintaining the efficiency of a belt training conveyor. Misalignment can cause excessive wear, reduce efficiency, and lead to operational downtimes. Here’s how to recognize and address misalignment issues:
- Visual Inspection: Regularly inspect the conveyor belt for signs of misalignment. Look for uneven wear patterns on the belt edges, which indicate that the belt is not running straight.
- Tracking Observation: Observe the belt tracking at various points along the conveyor. The belt should remain centered on the pulleys and idlers. If the belt veers to one side, this is a clear sign of misalignment.
- Check Roller Alignment: Misaligned rollers are a common cause of tracking issues. Use a straight edge or laser alignment tool to check that all rollers are parallel and perpendicular to the conveyor frame. Adjust any rollers that are out of alignment.
- Pulley and Idler Inspection: Ensure that all pulleys and idlers are aligned correctly with the conveyor frame. Misaligned pulleys and idlers can cause the belt to run off track. Make necessary adjustments to align them properly.
- Load Distribution: Uneven load distribution can also cause misalignment. Ensure that the load on the conveyor is evenly distributed. Overloading one side of the conveyor can lead to tracking issues.
- Regular Maintenance: Implement a regular maintenance schedule to check for misalignment. Routine inspections can help identify and correct misalignment issues before they lead to significant problems.
Conveyor Belt Training Idlers
Training idlers play a crucial role in maintaining proper belt alignment in a belt training conveyor. These specialized idlers are designed to automatically correct minor misalignments and keep the belt centered. Here’s how they work and how to adjust them:
- Function of Training Idlers: Training idlers are strategically placed along the conveyor to detect and correct belt misalignment. They pivot or tilt slightly to guide the belt back to the center if it starts to drift.
- Placement of Training Idlers: Proper placement of training idlers is essential for effective belt training. Typically, training idlers are installed at key points along the conveyor, such as near the head and tail pulleys, and at intervals along the length of the conveyor. Their placement should be based on the specific design and requirements of the conveyor system.
- Adjusting Training Idlers: When adjusting training idlers, ensure they are correctly positioned and able to pivot freely. The idlers should be set at a slight angle to the belt’s direction of travel. This angle helps guide the belt back to the center if it begins to drift.
- Monitoring Performance: After adjusting the training idlers, run the conveyor and observe the belt’s tracking. The belt should stay centered without frequent adjustments. If the belt continues to drift, recheck the alignment of the training idlers and make further adjustments as necessary.
- Maintenance of Training Idlers: Regular maintenance is crucial for training idlers. Check that they are free of debris and can pivot smoothly. Lubricate moving parts as needed to ensure optimal performance. Replace any worn or damaged idlers promptly to maintain effective belt training.
- Combining with Other Methods: While training idlers are effective, they should be used in combination with other belt training methods. Ensuring proper alignment of pulleys and rollers, maintaining correct belt tension, and evenly distributing the load all contribute to effective belt training.
The adjustment process in a belt training conveyor involves a systematic approach starting from the head pulley, identifying and addressing misalignment, and utilizing training idlers effectively. By following these detailed steps, you can ensure that your conveyor belt operates efficiently, reducing wear and tear and preventing downtime. Regular monitoring and maintenance are key to sustaining optimal performance and extending the lifespan of your conveyor system.
Pulley Shaft Alignment: Belt Training Conveyor
Proper pulley shaft alignment is a critical aspect of maintaining an efficient and well-functioning belt training conveyor. Ensuring that the head and tail pulley shafts are parallel, and making fine adjustments with snub pulleys, can significantly reduce belt tracking issues and extend the lifespan of the conveyor system. This section provides a detailed guide on aligning pulley shafts and adjusting snub pulleys for optimal belt performance.
Parallel Shafts
Achieving parallel alignment of the head and tail pulley shafts is essential for the proper operation of a belt training conveyor. Misaligned shafts can cause the belt to drift, leading to uneven wear, increased maintenance, and potential downtime. Here’s how to ensure that the pulley shafts are parallel:
- Initial Inspection and Preparation: Begin by shutting down the conveyor and locking out all energy sources to ensure safety. Remove any material from the conveyor belt and clean the area around the head and tail pulleys.
- Measuring Parallel Alignment: Use precision tools such as a laser alignment tool, dial indicators, or a straight edge and a measuring tape to check the alignment. Place the measuring tool across the pulley faces at both ends and measure the distance between corresponding points. The measurements should be identical if the shafts are parallel.
- Adjusting the Head Pulley: If the head pulley is out of alignment, loosen the mounting bolts slightly. Use adjustment screws or shims to make small adjustments. Move the pulley until the measurements indicate that it is parallel with the tail pulley. Tighten the bolts securely after making adjustments.
- Adjusting the Tail Pulley: Similarly, check the alignment of the tail pulley. Loosen the mounting bolts and make adjustments using the adjustment screws or shims. Ensure the tail pulley is parallel to the head pulley and tighten the bolts once proper alignment is achieved.
- Checking for Squareness: Besides ensuring parallelism, verify that both pulleys are square to the conveyor frame. Use a carpenter’s square to check that the pulleys are at right angles to the frame. Adjust as necessary to correct any deviations.
- Verification of Alignment: After adjustments, run the conveyor at a slow speed to verify the alignment. Observe the belt tracking and ensure it runs smoothly without drifting. Recheck the alignment if any issues are detected and make further adjustments if necessary.
Snub Pulley Adjustments
Snub pulleys are auxiliary pulleys located near the head and tail pulleys. They help increase the belt’s wrap angle around the drive pulley, providing better traction and more effective belt control. Adjusting the snub pulleys is a fine-tuning process that helps ensure straight belt running and proper tracking.
- Understanding Snub Pulley Function: Snub pulleys guide the belt and maintain tension. They should be positioned to maximize the belt’s contact with the drive pulley without causing excessive tension that could damage the belt.
- Initial Snub Pulley Positioning: Start with the snub pulleys in their default positions as specified by the conveyor manufacturer. These positions are designed to provide a baseline for optimal belt performance.
- Fine-Tuning Snub Pulley Alignment: If the belt is not tracking properly, small adjustments to the snub pulleys can help correct this. Loosen the adjustment bolts on the snub pulley bracket. Move the pulley slightly forward or backward to alter the belt’s contact angle with the drive pulley. Tighten the bolts once the desired position is achieved.
- Observing Belt Tracking: Run the conveyor at a slow speed and observe the belt tracking. The belt should stay centered on the pulleys and idlers. If the belt still tends to drift, make additional small adjustments to the snub pulleys until the belt runs straight.
- Balancing Tension: Ensure that the adjustments to the snub pulleys do not create uneven tension across the belt. Uneven tension can cause additional wear and tracking problems. Use a tension gauge to measure and balance the tension across the belt’s width.
- Final Adjustments and Testing: After adjusting the snub pulleys, conduct a final test run with the conveyor fully loaded. Monitor the belt tracking and performance under load. Make any final adjustments as needed to ensure that the belt runs smoothly and stays centered.
- Regular Maintenance Checks: Include snub pulley adjustments in your regular maintenance schedule. Periodic checks and adjustments can help maintain optimal belt alignment and prevent tracking issues from developing.
Pulley shaft alignment and snub pulley adjustments are fundamental aspects of maintaining a belt training conveyor. By ensuring that the head and tail pulley shafts are parallel and making precise adjustments to the snub pulleys, you can achieve straight belt running and optimal conveyor performance. Regular inspection, alignment, and maintenance are key to preventing misalignment issues, reducing wear and tear, and extending the conveyor system’s lifespan. Following these detailed steps will help maintain a well-aligned and efficiently operating belt training conveyor, ensuring smooth and reliable material handling operations.
Belt Tracking and Alignment: Belt Training Conveyor
Effective belt tracking and alignment are essential for the optimal performance of a belt training conveyor. Proper tracking ensures the belt runs straight, reducing wear and tear, minimizing maintenance needs, and preventing operational downtime. This section delves into conveyor belt tracking systems, practical tips for achieving straight belt movement, and the crucial role of return rollers in maintaining alignment.
Conveyor Belt Tracking Systems
Conveyor belt tracking systems are designed to monitor and adjust the belt’s position to ensure it stays aligned. These systems offer several benefits that enhance the efficiency and longevity of a belt training conveyor.
- Automated Monitoring: Tracking systems continuously monitor the belt’s position, detecting any deviations from the centerline. This automated process reduces the need for manual inspections and allows for immediate corrections.
- Enhanced Accuracy: Advanced tracking systems use sensors and actuators to make precise adjustments. This ensures the belt remains properly aligned, even with varying loads and speeds.
- Reduced Wear and Tear: By maintaining proper alignment, tracking systems minimize the lateral forces that cause belt edges to wear unevenly. This extends the life of the belt and reduces the frequency of replacements.
- Improved Safety: Misaligned belts can cause spillage, jams, and other hazards. Tracking systems help prevent these issues, creating a safer working environment.
- Energy Efficiency: Properly aligned belts run more smoothly, reducing the energy required to drive the conveyor. This results in lower operating costs and increased energy efficiency.
- Minimal Downtime: Automatic tracking adjustments prevent belt misalignment from escalating into more severe issues that could cause downtime. This ensures continuous, reliable operation.
How to Get a Conveyor Belt to Run Straight
Achieving straight belt movement is a key aspect of maintaining a belt training conveyor. Here are nine practical tips to help ensure your conveyor belt runs straight:
- Proper Installation: Ensure the belt is installed correctly from the start. Misalignment during installation can lead to persistent tracking issues.
- Check Belt Tension: Uneven or improper tension can cause the belt to drift. Use a tension gauge to ensure the belt is evenly tensioned across its width.
- Align Pulleys and Rollers: Misaligned pulleys and rollers are common causes of tracking problems. Use precision tools to check and adjust their alignment.
- Cleanliness: Debris and buildup on the belt or rollers can affect tracking. Regularly clean the conveyor to prevent foreign material from interfering with belt alignment.
- Use Training Idlers: Training idlers help correct minor misalignments by guiding the belt back to the center. Ensure they are properly adjusted and maintained.
- Even Load Distribution: Uneven loading can cause the belt to drift. Distribute the load evenly across the belt to maintain proper tracking.
- Regular Inspections: Conduct regular inspections to identify and correct any tracking issues early. This proactive approach helps prevent more severe problems.
- Install Belt Scrapers: Belt scrapers remove material buildup from the belt, which can cause misalignment. Ensure scrapers are properly installed and maintained.
- Professional Assistance: If persistent tracking issues occur, consider consulting a professional. They can provide expert advice and solutions tailored to your specific conveyor system.
Conveyor Belt Tracking Return Rollers
Return rollers play a crucial role in maintaining belt alignment in a belt training conveyor. Positioned on the return side of the belt, these rollers help guide the belt back to the correct path, ensuring consistent tracking.
- Function of Return Rollers: Return rollers support the belt on its return path, helping to keep it aligned. They are strategically placed to ensure the belt remains centered as it travels back to the head pulley.
- Self-Aligning Return Rollers: These specialized rollers can pivot slightly to correct minor misalignments. They automatically adjust the belt’s position, reducing the need for manual interventions.
- Installation and Positioning: Proper installation of return rollers is critical. They should be positioned perpendicular to the conveyor frame and aligned with the belt’s centerline. Incorrect placement can exacerbate tracking issues.
- Maintenance of Return Rollers: Regular maintenance ensures return rollers function correctly. Inspect them for wear, debris buildup, and alignment issues. Replace worn or damaged rollers promptly.
- Adjusting Return Rollers: Fine-tuning the position of return rollers can help correct tracking issues. Make small adjustments and observe the belt’s movement to achieve the desired alignment.
- Balancing Return Rollers: Ensure that the pressure on the belt is evenly distributed across all return rollers. Uneven pressure can cause the belt to drift to one side.
- Integration with Tracking Systems: Combine return rollers with automated tracking systems for optimal performance. The tracking system can monitor the belt’s position and adjust the return rollers as needed to maintain alignment.
Maintaining proper belt tracking and alignment is vital for the efficient operation of a belt training conveyor. Conveyor belt tracking systems, practical tips for straight belt movement, and the effective use of return rollers all contribute to achieving and maintaining proper alignment. By implementing these strategies and regularly monitoring and adjusting your conveyor system, you can ensure reliable performance, reduce maintenance needs, and extend the life of your conveyor belt.
Troubleshooting and Maintenance: Belt Training Conveyor
Proper maintenance and troubleshooting are essential for ensuring the efficient operation of a belt training conveyor. This section explores common tracking issues, the impact of material build-up, and the importance of tail roller adjustments for maintaining proper alignment.
Conveyor Belt Tracking Troubleshooting
Despite proper installation and maintenance, belt tracking issues can still arise. Here are six common tracking issues and how to resolve them:
- Off-Center Loading: Uneven loading can cause the belt to drift. Ensure that the load is evenly distributed across the belt to prevent tracking problems.
- Misaligned Pulleys or Rollers: Misalignment of pulleys or rollers can cause the belt to track off-center. Use precision tools to check and adjust the alignment as needed.
- Belt Tension: Incorrect belt tension can lead to tracking issues. Use a tension gauge to ensure the belt is properly tensioned across its width.
- Build-Up on Pulleys or Rollers: Debris or material build-up on pulleys or rollers can interfere with belt tracking. Regularly clean the pulleys and rollers to prevent build-up.
- Belt Damage: Worn or damaged belts can cause tracking problems. Inspect the belt regularly for signs of wear and replace it if necessary.
- Improper Tracking Systems: If your conveyor is equipped with a tracking system, ensure it is functioning correctly. Adjust or repair the system as needed to maintain proper belt alignment.
Material Build-Up Issues
Material build-up on the belt or conveyor components can also contribute to tracking problems. Here are ten common issues caused by material build-up and solutions to address them:
- Belt Damage: Build-up of material can cause the belt to wear unevenly or become damaged. Use belt scrapers to remove material and prevent damage.
- Belt Slippage: Material build-up can reduce the friction between the belt and the pulleys, leading to slippage. Clean the belt and pulleys regularly to prevent slippage.
- Roller Damage: Material build-up can also damage rollers, causing them to wear prematurely. Clean the rollers regularly to prevent damage.
- Tracking Issues: Material build-up can interfere with the belt tracking, causing it to drift off-center. Use belt scrapers to remove material and maintain proper tracking.
- Increased Maintenance Costs: Material build-up can increase maintenance costs due to more frequent repairs and replacements. Regular cleaning and maintenance can help reduce these costs.
- Safety Hazards: Build-up of material can create safety hazards, such as tripping or slipping. Keep the conveyor clean and free of debris to reduce the risk of accidents.
- Reduced Efficiency: Material build-up can reduce the efficiency of the conveyor system, leading to slower operation and decreased throughput. Regular cleaning and maintenance can help maintain efficiency.
- Material Contamination: Build-up of foreign material can contaminate the product being conveyed. Use belt scrapers to remove material and prevent contamination.
- Environmental Impact: Material build-up can have environmental impacts, such as contamination of nearby water sources. Proper maintenance and cleaning can help reduce these impacts.
- Legal Compliance: Failure to maintain a clean and safe conveyor system can lead to legal issues. Regular maintenance and cleaning can help ensure compliance with regulations.
Tail Roller Conveyor Adjustments
Tail roller adjustments are crucial for maintaining proper belt tracking, especially at the end of the conveyor where the belt returns. Here are seven important considerations for tail roller adjustments:
- Alignment: Ensure that the tail roller is aligned with the direction of the belt. Misalignment can cause tracking issues.
- Positioning: Position the tail roller at the correct height to maintain proper tension in the belt. Incorrect positioning can lead to tracking problems.
- Bearing Maintenance: Regularly inspect and lubricate the bearings in the tail roller to ensure smooth operation.
- Material Build-Up: Keep the tail roller clean and free of material build-up to prevent tracking issues.
- Adjustment Mechanism: Familiarize yourself with the adjustment mechanism of the tail roller and how to make proper adjustments.
- Regular Inspections: Conduct regular inspections of the tail roller to check for wear or damage. Replace the roller if necessary.
- Consultation: If you are unsure about how to adjust the tail roller, consult the conveyor manufacturer or a professional technician for guidance.
Troubleshooting and maintenance are vital aspects of ensuring the efficient and reliable operation of a belt training conveyor. By addressing common tracking issues, preventing material build-up, and making proper tail roller adjustments, you can maintain proper belt alignment and extend the lifespan of your conveyor system. Regular inspections, cleaning, and maintenance are key to preventing tracking problems and ensuring smooth operation.
Signs of Proper Belt Training: Belt Training Conveyor
Proper belt training is crucial for the efficient and reliable operation of a conveyor system. Recognizing the signs of proper belt training can help ensure that your conveyor is running smoothly and prevent potential issues. This section explores visual and operational indicators of proper belt training, as well as the long-term benefits associated with it.
Visual and Operational Indicators
- Centered Belt: A properly trained conveyor belt will run centered on the pulleys and rollers. It should not drift to one side or the other.
- Even Wear: Properly trained belts exhibit even wear across the width of the belt. Uneven wear patterns can indicate tracking issues.
- Minimal Spillage: Properly trained belts minimize material spillage along the conveyor path. Any spillage should be minimal and easily manageable.
- Smooth Operation: A well-trained belt runs smoothly without excessive noise or vibration. Any unusual sounds or vibrations can indicate tracking problems.
- Consistent Speed: Properly trained belts maintain a consistent speed throughout their operation. Variations in speed can indicate tracking issues or other problems.
- Minimal Belt Damage: Proper belt training reduces the risk of damage to the belt edges or surface. Any signs of damage should be investigated and addressed promptly.
- Aligned Components: All components of the conveyor system, including pulleys, rollers, and idlers, should be aligned properly with the belt. Misaligned components can lead to tracking issues.
- Proper Tension: The belt should be properly tensioned to prevent slippage and ensure smooth operation. Over-tensioning can cause premature wear, while under-tensioning can lead to tracking problems.
Long-Term Benefits
Proper belt training offers several long-term benefits that contribute to the efficient operation of a conveyor system:
- Reduced Wear: Properly trained belts experience less wear and tear, leading to longer belt life and reduced maintenance costs.
- Improved Efficiency: Properly trained belts run more efficiently, reducing energy consumption and operating costs.
- Lower Maintenance Costs: Proper belt training reduces the frequency of maintenance and repairs, resulting in lower overall maintenance costs.
- Increased Productivity: A well-trained conveyor belt leads to smoother operation and fewer interruptions, increasing overall productivity.
- Safer Operation: Properly trained belts are less likely to experience tracking issues, reducing the risk of accidents and injuries.
- Better Product Quality: Proper belt training ensures that materials are conveyed smoothly and without contamination, resulting in higher product quality.
- Compliance: Proper belt training helps ensure that the conveyor system complies with safety and environmental regulations, avoiding potential fines and penalties.
Recognizing the signs of proper belt training is essential for maintaining the efficiency and reliability of a conveyor system. By monitoring visual and operational indicators, you can ensure that your conveyor belt is running smoothly and prevent potential issues. Investing in proper belt training not only improves the performance of your conveyor system but also leads to long-term cost savings and operational benefits.
FAQs about Belt Training Conveyor
Training a conveyor involves adjusting the idlers, pulleys, and loading conditions to ensure the belt runs centrally and smoothly over the conveyance system. Initially, this process begins with ensuring the conveyor frame and structure are correctly aligned. If the frame is misaligned, the conveyor belt will not run straight. Once alignment is secured, the idlers are adjusted. Troughing idlers need to be set so that the belt runs in the center when loaded, and return idlers adjusted to maintain the belt’s central path when it’s unloaded. It’s also crucial to check that the belt tension is correctly set, as an overly tight or loose belt can veer off course. Regular monitoring and maintenance are required to keep the conveyor running efficiently, with retraining necessary if any modifications to the conveyance system are made.
The conveyor belt method refers to a systematic, step-by-step approach to move objects or material from one point to another using a flexible, continuous loop of material—the conveyor belt—driven by pulleys. This method is highly efficient for transporting goods across various distances, slopes, and elevations within a given facility or across multiple locations. The conveyor belt method enables the seamless, continuous movement of items, significantly enhancing productivity and operational efficiency in various industries, including manufacturing, warehousing, and distribution. By utilizing this method, businesses can streamline their operations, reduce manual handling, and potentially lower labor costs and risk of injuries.
A belt conveyor works through the action of a motor-driven pulley system, where one or more pulleys are powered, moving the belt and the material on the belt forward. The powered pulley is called the drive pulley, while the unpowered one is known as the idler pulley. Conveyors operate on the principle of friction between the belt and the pulley, which requires that the belt be tensioned against the pulleys with enough force to move the belt and control the load. The belt itself is often made of several layers of different materials, designed to provide strength, support the load, and resist wear. Various types of belt conveyors are tailored to the nature of the materials they are designed to transport, with adjustments made for factors like belt speed, load capacity, and the physical properties of the items being moved.
A conveyor belt worker is commonly referred to as a conveyor operator or conveyor belt operator. These skilled workers are responsible for the operation and maintenance of the conveyor belt systems used in various industries for the transport of materials and goods. Their duties typically include monitoring conveyor systems to ensure they are functioning correctly, loading and unloading items, conducting regular maintenance and repairs, and adjusting the speed, alignment, and tension of the belts as necessary. Conveyor operators must have a good understanding of the machinery they work with and adhere to safety protocols to prevent accidents and ensure the efficient operation of the conveyor system.
Last Updated on May 23, 2024 by Jordan Smith
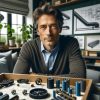
Jordan Smith, a seasoned professional with over 20 years of experience in the conveyor system industry. Jordan’s expertise lies in providing comprehensive solutions for conveyor rollers, belts, and accessories, catering to a wide range of industrial needs. From initial design and configuration to installation and meticulous troubleshooting, Jordan is adept at handling all aspects of conveyor system management. Whether you’re looking to upgrade your production line with efficient conveyor belts, require custom conveyor rollers for specific operations, or need expert advice on selecting the right conveyor accessories for your facility, Jordan is your reliable consultant. For any inquiries or assistance with conveyor system optimization, Jordan is available to share his wealth of knowledge and experience. Feel free to reach out at any time for professional guidance on all matters related to conveyor rollers, belts, and accessories.