Streamlining Your Conveyor Belt Installation Procedure
Understanding the conveyor belt installation procedure is crucial for ensuring optimal performance and longevity of the system. This guide provides a detailed overview of the necessary steps and considerations for installing conveyor belts, highlighting essential resources and best practices. By following the conveyor belt installation procedure, you can minimize downtime, prevent potential issues, and ensure a seamless setup process. This comprehensive guide will walk you through various aspects, from sourcing the right installation companies and downloading essential PDFs to creating maintenance checklists and method statements. Proper adherence to the conveyor belt installation procedure is key to achieving a reliable and efficient conveyor system that meets your operational needs.
Conveyor Belt Installation Procedure: Essential PDF Downloads
Importance of Reference Materials
The conveyor belt installation procedure is a meticulous process that requires precise planning and execution. Having a detailed installation PDF guide is crucial for several reasons. First, it ensures that all steps are clearly outlined and easy to follow, reducing the risk of errors. For example, companies like Flexco and Continental provide comprehensive PDF guides that include step-by-step instructions, safety protocols, and troubleshooting tips.
A detailed PDF guide helps standardize the installation process, ensuring consistency across different teams and locations. This is particularly important for large-scale operations where multiple installations might be happening simultaneously. Accessing these documents is straightforward. Most manufacturers, such as Flexco and Fenner Dunlop, offer free downloads of their installation guides directly from their websites. These documents are typically found in the support or resources section of the site.
To utilize these documents effectively, it is essential to ensure that all team members involved in the installation are familiar with the content. Conducting a pre-installation meeting to review the guide can help align the team and clarify any potential issues. Additionally, having a printed or digital copy of the PDF guide on-site allows for quick reference during the installation process, ensuring adherence to the conveyor belt installation procedure.
Recommended Download Sources
When searching for reliable sources of conveyor belt installation procedure PDFs, it is important to choose trusted websites and manufacturers known for their expertise in the field. Flexco, for instance, offers a wealth of resources on their website, including detailed installation guides for various types of conveyor belts. Similarly, Continental’s website provides comprehensive PDF downloads that cover everything from basic installation steps to advanced troubleshooting.
Another reputable source is the Dunlop Conveyor Belting website, which offers detailed installation guides tailored to their specific products. These guides are invaluable for ensuring that the installation procedure is followed correctly and that any unique product specifications are addressed. The Sparks Belting website also provides a range of downloadable resources, including installation and maintenance guides that are designed to help users achieve optimal performance from their conveyor systems.
When downloading an installation guide, it is important to look for key sections that will provide the most benefit. These typically include an overview of the installation procedure, safety instructions, step-by-step installation steps, and maintenance recommendations. Additionally, troubleshooting sections can be particularly helpful for addressing any issues that arise during the installation process.
Utilizing the PDF in the Installation Process
Integrating the conveyor belt installation procedure PDF guide with on-site installation steps is critical for a smooth and efficient setup. The first step is to ensure that all team members have access to the guide. This can be done by distributing digital copies via email or project management software. For those who prefer a physical reference, printing copies of the guide and providing them to the installation team can be beneficial.
During the installation process, the PDF guide should be used as a constant reference. For example, when installing a conveyor belt at a manufacturing facility, the team should follow the steps outlined in the guide to ensure that each phase of the installation is completed correctly. This includes everything from preparing the site and securing the necessary tools to installing the belt and performing initial tests.
One practical example is the use of support and diverting rollers during the belt pulling phase, as recommended by companies like Sempertrans. By referring to the PDF guide, installers can ensure that these components are positioned correctly, reducing the risk of belt misalignment and subsequent operational issues. Another critical aspect covered in most guides is the proper tensioning of the belt. By following the specific tensioning procedures outlined in the PDF, installers can avoid common issues such as slippage and excessive wear.
Ensuring that all team members have access to the conveyor belt installation procedure PDF, whether in digital or printed form, helps maintain consistency and quality throughout the installation process. This approach not only enhances the efficiency of the installation but also contributes to the long-term reliability and performance of the conveyor system.
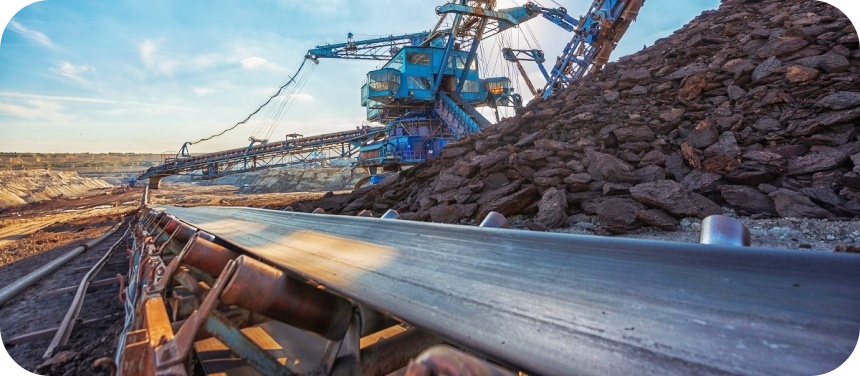
Conveyor Belt Installation Procedure Jobs: Roles and Opportunities
Understanding Job Roles and Responsibilities
The conveyor belt installation procedure involves a variety of key roles, each with specific responsibilities to ensure a successful installation. Primary roles include installation technicians, supervisors, and project managers. Installation technicians are on the frontline, performing the physical installation tasks such as setting up the conveyor structure, aligning and tensioning the belt, and testing the system for proper operation. They must possess a thorough understanding of the conveyor belt installation procedure to ensure every step is executed correctly.
Supervisors oversee the technicians, ensuring that the installation adheres to safety standards and project timelines. They are responsible for troubleshooting any issues that arise and ensuring that all aspects of the installation meet the technical specifications outlined in the conveyor belt installation procedure. Project managers coordinate the overall process, liaising with clients, managing resources, and ensuring that the project stays within budget.
To be effective in these roles, individuals must possess specific skills and qualifications. Technicians should have mechanical aptitude, familiarity with tools and equipment, and a basic understanding of mechanical systems. Certifications from institutions like the National Industrial Belting Association (NIBA) or the International Association of Mechanical Engineers (IAME) can enhance a technician’s qualifications. Supervisors and project managers typically need additional experience and education, often holding degrees in engineering or project management, and certifications like Project Management Professional (PMP) can be beneficial.
Hiring and Training
Hiring skilled individuals for the conveyor belt installation procedure is crucial for the success of the project. Companies like Flexco and Fenner Dunlop prioritize hiring experienced technicians who have a proven track record in similar roles. Best practices for hiring include thorough background checks, skills assessments, and practical tests to ensure candidates have the necessary expertise.
Training is an ongoing process that ensures technicians are up-to-date with the latest installation techniques and safety protocols. Many companies offer in-house training programs tailored to their specific needs. For instance, Continental has a comprehensive training program that includes both classroom instruction and hands-on practice. These programs cover various aspects of the conveyor belt installation procedure, from initial setup to final testing.
Certifications play a vital role in training. Organizations like NIBA offer certification programs that validate a technician’s knowledge and skills. These programs typically cover topics such as belt splicing, tensioning, and alignment, all of which are critical components of the conveyor belt installation procedure. Additionally, companies often encourage continuous education through workshops and seminars to keep their staff abreast of technological advancements and new installation methods.
Job Market and Opportunities
The job market for conveyor belt installation is robust, driven by the continuous demand for efficient material handling systems across various industries. According to the Bureau of Labor Statistics, the employment of industrial machinery mechanics, which includes conveyor belt installers, is projected to grow 5% from 2020 to 2030, reflecting a steady demand for skilled workers in this field.
Companies like Flexco, Continental, and Fenner Dunlop are frequently on the lookout for qualified installation technicians. The mining, manufacturing, and logistics sectors are the largest employers, requiring conveyor systems for their operations. For instance, the expansion of e-commerce has led to a significant increase in warehouse conveyor installations, providing ample job opportunities for skilled technicians.
Career growth in this field is promising. Starting as an installation technician, one can advance to supervisory roles or project management positions. With additional education and experience, professionals can move into specialized roles such as conveyor system designers or consultants. Furthermore, the industry offers competitive salaries, with installation technicians earning an average annual wage of $50,000, while supervisors and project managers can earn significantly higher, depending on their experience and qualifications.
The conveyor belt installation procedure is a vital aspect of ensuring the efficiency and longevity of conveyor systems. By understanding the various roles involved, adhering to best hiring and training practices, and recognizing the job market’s potential, individuals and companies can ensure successful installations and promising career opportunities.
Selecting and Working with Conveyor Belt Installation Companies for Optimal Procedures
Selecting the Right Installation Company
Choosing the right company to handle your conveyor belt installation procedure is crucial for the success of your project. Here are key criteria to consider:
- Experience and Expertise: Look for companies with extensive experience in conveyor belt installation. Companies like Flexco and Fenner Dunlop have decades of experience and a deep understanding of the conveyor belt installation procedure, which ensures they can handle complex installations efficiently. Evaluate their expertise by checking their portfolio and the types of projects they have completed.
- Certifications and Compliance: Ensure the company complies with industry standards and holds relevant certifications. For example, ISO 9001 certification indicates that the company adheres to quality management standards, which is essential for ensuring the reliability of the conveyor belt installation procedure.
- Customer Reviews and Testimonials: Evaluating customer reviews and testimonials can provide insights into the company’s reliability and quality of service. Websites like Trustpilot and Google Reviews can be helpful for finding unbiased feedback. Positive reviews about the company’s adherence to the conveyor belt installation procedure can be a good indicator of their reliability.
- Technical Support and After-Sales Service: A good installation company should offer comprehensive technical support and after-sales service. This includes providing maintenance services, troubleshooting, and regular check-ups to ensure the conveyor system remains in optimal condition.
Top Installation Companies
Several leading companies specialize in the conveyor belt installation procedure, offering a range of services and specializations:
- Flexco: Known for their comprehensive approach to conveyor belt installation, Flexco provides everything from initial consultation to post-installation support. They offer specialized services in belt splicing, pulley lagging, and system audits to ensure optimal performance.
- Fenner Dunlop: This company specializes in heavy-duty conveyor belt systems used in mining and industrial applications. Their services include on-site installation, emergency repairs, and routine maintenance, all adhering to strict safety and quality standards.
- Continental: Continental offers a wide range of services, including custom conveyor belt design, installation, and maintenance. They are known for their innovative solutions and use of advanced technology to ensure the conveyor belt installation procedure is carried out efficiently.
- Sparks Belting: Sparks Belting provides tailored solutions for various industries, including food processing, logistics, and manufacturing. Their services include installation, preventive maintenance, and emergency repair services, ensuring minimal downtime.
Working with Installation Companies
Effective communication and project management are critical when working with a company to handle your conveyor belt installation procedure:
- Clear Communication: Establish clear lines of communication from the start. Ensure that all stakeholders are informed about the project’s scope, timeline, and expectations. Regular updates and meetings can help keep everyone on the same page and address any issues promptly.
- Project Management Tools: Utilize project management tools such as Asana or Trello to track progress and manage tasks. These tools can help coordinate between different teams and ensure that the conveyor belt installation procedure is completed on time.
- Detailed Contracts and Agreements: Make sure all terms and conditions are clearly outlined in the contract. This should include the scope of work, payment terms, deadlines, and any warranties or guarantees related to the conveyor belt installation procedure.
- Site Preparation and Safety: Work closely with the installation company to prepare the site. This includes ensuring that all necessary permits are obtained, safety protocols are followed, and any potential hazards are addressed before the installation begins.
- Post-Installation Support: Ensure that the company provides post-installation support, including training for your staff on operating and maintaining the conveyor system. This support is crucial for addressing any issues that arise after installation and ensuring the system operates smoothly.
Working with a professional and experienced installation company ensures that the conveyor belt installation procedure is carried out efficiently and effectively. By selecting the right company, you can minimize downtime, ensure safety, and achieve optimal performance for your conveyor system.
Comprehensive Belt Conveyor Maintenance Manual for an Effective Conveyor Belt Installation Procedure
Importance of a Maintenance Manual
A maintenance manual is an indispensable tool in the conveyor belt installation procedure, serving as a detailed guide to ensure the long-term functionality and efficiency of the conveyor system. It plays a crucial role in outlining the regular maintenance tasks, troubleshooting procedures, and safety protocols necessary for maintaining the system’s optimal performance. For example, companies like Flexco and Fenner Dunlop emphasize the importance of a maintenance manual as part of their comprehensive conveyor belt installation procedure.
Key sections of a comprehensive belt conveyor maintenance manual typically include:
- Introduction and Overview: Provides an introduction to the conveyor system, its components, and the importance of maintenance.
- Safety Guidelines: Detailed safety protocols to be followed during maintenance to prevent accidents and injuries.
- Routine Maintenance Schedule: A timetable for regular inspections and maintenance tasks, such as checking belt tension, alignment, and wear.
- Troubleshooting Guide: Step-by-step procedures for diagnosing and fixing common issues that may arise during the conveyor belt installation procedure.
- Parts List and Specifications: Detailed information about the components of the conveyor system, including part numbers and specifications for easy identification and replacement.
Creating a Custom Maintenance Manual
Developing a tailored maintenance manual for your conveyor system involves several key steps to ensure it addresses the specific needs and conditions of your operation. Here’s how to create an effective manual:
- Assess the System Requirements: Begin by thoroughly assessing your conveyor system’s design, components, and operational environment. Companies like Continental and Sparks Belting often conduct detailed system audits to gather this information, which forms the foundation of a custom maintenance manual.
- Involve Experts and Technicians: Collaborate with experienced technicians and industry experts to develop the manual. Their hands-on experience and technical knowledge are invaluable for creating accurate and practical maintenance procedures. For instance, involving a certified technician from NIBA (National Industrial Belting Association) can ensure the maintenance guidelines are up-to-date and in line with industry standards.
- Document Detailed Procedures: Clearly document each maintenance task with step-by-step instructions, including the tools required and estimated time for completion. Use diagrams and photographs to illustrate complex procedures. For example, detailing the exact steps for checking and adjusting belt tension as part of the conveyor belt installation procedure can help prevent common issues such as slippage and excessive wear.
- Include Preventive Maintenance Tips: Incorporate preventive maintenance tips to help extend the lifespan of the conveyor system. This could include recommendations for proper storage of spare parts, guidelines for regular cleaning, and best practices for operating the conveyor under varying loads and conditions.
- Review and Update Regularly: Ensure the maintenance manual is a living document that gets reviewed and updated regularly based on feedback from maintenance personnel and changes in system configuration or operating conditions.
Utilizing the Maintenance Manual
Integrating the maintenance manual into daily operations is essential for maximizing the benefits of the conveyor belt installation procedure. Here’s how to effectively utilize the manual:
- Incorporate into Daily Routines: Make the maintenance manual a core part of your daily operations. Ensure that all maintenance personnel have easy access to the manual, whether in digital form via tablets or printed copies placed at strategic locations within the facility. For example, Flexco recommends placing the manual in the maintenance room and near critical control points of the conveyor system.
- Conduct Regular Training Sessions: Train your staff on the use and importance of the maintenance manual. Regular training sessions can help familiarize new employees with the manual and refresh the knowledge of existing staff. Using real-life scenarios and practical demonstrations can enhance understanding and retention. For instance, conducting a workshop on the conveyor belt installation procedure, including how to use the maintenance manual for troubleshooting, can significantly improve overall system reliability.
- Monitor Compliance and Effectiveness: Establish a system to monitor compliance with the maintenance manual and evaluate its effectiveness. Regular audits and feedback sessions can help identify areas for improvement. Companies like Continental often use maintenance checklists and logs to track completed tasks and identify recurring issues, ensuring continuous improvement of the conveyor belt installation procedure.
- Leverage Technology: Utilize technology to enhance the effectiveness of the maintenance manual. For example, implementing a computerized maintenance management system (CMMS) can help automate scheduling, track maintenance history, and provide real-time updates on the status of maintenance tasks. This integration can streamline the conveyor belt installation procedure and ensure that all maintenance activities are documented and easily accessible.
By creating and utilizing a comprehensive maintenance manual, companies can ensure that their conveyor belt installation procedure not only meets initial setup requirements but also sustains long-term operational efficiency. This proactive approach to maintenance helps prevent costly downtimes, extend the lifespan of the conveyor system, and maintain a safe working environment.
Creating an Effective Conveyor Belt Installation Procedure Maintenance Checklist
Developing a Maintenance Checklist
An effective conveyor belt maintenance checklist is an essential component of the conveyor belt installation procedure, ensuring that the system operates smoothly and efficiently over its lifespan. Developing this checklist involves identifying key components and establishing a regular maintenance schedule.
- Key Components of an Effective Checklist: A comprehensive maintenance checklist should cover all critical aspects of the conveyor belt system. This includes:
- Visual Inspections: Regularly checking for signs of wear, damage, and misalignment.
- Belt Tension and Tracking: Ensuring the belt is properly tensioned and aligned to prevent slippage and uneven wear.
- Rollers and Pulleys: Inspecting rollers and pulleys for wear, alignment, and lubrication needs.
- Drive Mechanisms: Checking motors, reducers, and other drive components for proper operation and maintenance.
- Safety Devices: Verifying that all safety guards and emergency stop mechanisms are functioning correctly.
- Frequency and Scheduling of Maintenance Tasks: The frequency of maintenance tasks should be determined based on the conveyor belt’s usage, environment, and manufacturer recommendations. For example, Flexco recommends daily visual inspections and monthly detailed inspections for most conveyor systems. Establishing a maintenance calendar can help ensure that all tasks are completed on time and nothing is overlooked. For high-use systems, consider more frequent inspections to catch issues before they lead to significant downtime.
Common Maintenance Tasks
Routine maintenance is critical to the conveyor belt installation procedure, helping to prevent unexpected breakdowns and prolong the system’s life.
- Routine Inspections and Adjustments: Regular inspections should focus on detecting any anomalies that could affect the system’s performance. This includes checking for belt tension and tracking, inspecting rollers and pulleys for smooth operation, and ensuring drive mechanisms are free of debris and properly lubricated. A case study from Fenner Dunlop shows that regular inspections can reduce unscheduled downtime by up to 30%.
- Identifying and Addressing Common Wear and Tear Issues: Common issues include belt misalignment, which can lead to uneven wear and potential system failure. Regularly inspecting the alignment and making necessary adjustments is crucial. Additionally, monitoring for wear on rollers and pulleys can prevent more significant problems. For instance, Continental’s maintenance guidelines recommend replacing any rollers showing signs of excessive wear to avoid damaging the belt and other components.
Benefits of a Maintenance Checklist
Implementing a structured maintenance checklist as part of the conveyor belt installation procedure offers numerous benefits, significantly impacting the system’s overall performance and reliability.
- Enhancing System Longevity and Performance: A well-maintained conveyor system operates more efficiently and has a longer lifespan. Regular maintenance helps identify and resolve issues before they escalate, ensuring that the system runs smoothly and reliably. According to Sparks Belting, systems with regular maintenance schedules can last up to 50% longer than those without.
- Preventing Costly Downtime and Repairs: Unplanned downtime can be extremely costly, not only in terms of repair expenses but also in lost productivity. A proactive maintenance approach helps prevent such scenarios. By adhering to a detailed maintenance checklist, companies can avoid the high costs associated with emergency repairs and operational interruptions. Data from Flexco indicates that preventative maintenance can reduce downtime by 25% and maintenance costs by 15%.
An effective maintenance checklist is integral to the conveyor belt installation procedure, ensuring that the system remains functional, safe, and efficient. By developing a detailed checklist, performing regular maintenance tasks, and understanding the benefits, companies can maximize their investment in conveyor belt systems and maintain optimal operational efficiency.
Detailed Belt Conveyor Parts and Functions PDF for an Effective Conveyor Belt Installation Procedure
Understanding Conveyor Belt Parts
An in-depth understanding of the essential parts of a conveyor belt system is crucial for the successful execution of the conveyor belt installation procedure. Each part plays a vital role in the overall functionality and efficiency of the conveyor system.
Overview of Essential Conveyor Belt Parts and Their Functions
Key components of a conveyor belt system include:
- Conveyor Belt: The primary moving surface that carries materials from one point to another. Made from materials like rubber, PVC, or metal, its selection depends on the application.
- Idlers and Rollers: These are cylindrical components that support the conveyor belt and help it to move smoothly. They reduce friction and wear on the belt.
- Pulleys: These are essential for driving and redirecting the belt. The drive pulley is connected to a motor and moves the belt, while the tail pulley guides the belt back to the drive pulley.
- Motor and Drive Mechanism: The motor powers the conveyor system, while the drive mechanism transmits this power to the drive pulley, facilitating belt movement.
- Frame and Structure: This provides the framework to which all other components are attached, ensuring stability and alignment.
- Belt Cleaners: These components help in removing material stuck to the belt, preventing build-up and ensuring efficient operation.
- Safety Guards and Emergency Stops: These are critical for ensuring the safety of personnel operating the conveyor system.
- Importance of Each Part in the Installation Procedure: Each part must be correctly installed and aligned to ensure the conveyor system operates efficiently. For example, if the idlers and rollers are not properly aligned, it can cause the belt to track improperly, leading to excessive wear and potential system failure. Proper installation of safety guards and emergency stops is also crucial to comply with safety regulations and protect workers.
Accessing Parts and Functions PDF
For a thorough understanding and reference during the conveyor belt installation procedure, accessing detailed parts and functions PDFs from reliable sources is essential.
- Recommended Sources for Downloading Detailed Parts and Functions PDFs: Trusted companies like Flexco, Continental, and Fenner Dunlop provide comprehensive PDFs detailing the parts and functions of their conveyor systems. These documents are typically available for download on their websites under sections like ‘Resources’ or ‘Support’. For instance, Flexco offers an extensive library of technical documents that include detailed descriptions and diagrams of their conveyor components.
- Key Information to Look for in These Documents: When downloading parts and functions PDFs, look for detailed diagrams and descriptions of each component, installation guidelines, maintenance recommendations, and troubleshooting tips. These documents should also include specifications such as dimensions, materials, and part numbers, which are crucial for ordering replacements and ensuring compatibility during the conveyor belt installation procedure.
Using Parts and Functions PDF in Installation
Incorporating the information from the parts and functions PDF during the conveyor belt installation procedure is vital for ensuring accuracy and efficiency.
- How to Reference the PDF During the Installation Process: Keep the PDF readily accessible during the installation process. This can be done by having printed copies on-site or digital copies accessible via tablets or laptops. Each step of the installation should be cross-referenced with the PDF to ensure that components are installed correctly and align with manufacturer specifications. For example, when installing idlers and rollers, refer to the PDF to verify the correct positioning and alignment, which is crucial for preventing belt misalignment and wear.
- Ensuring Proper Installation and Alignment of All Parts: Follow the step-by-step instructions and diagrams provided in the PDF to ensure each part is installed and aligned correctly. This includes setting the correct tension for the belt, aligning pulleys to prevent belt drift, and installing safety guards according to the guidelines. Regularly consulting the PDF can help prevent common installation errors and ensure the conveyor system operates as intended.
For instance, during a recent installation project at a mining facility, technicians used Continental’s parts and functions PDF to guide the installation process. By following the detailed instructions and diagrams, they were able to complete the installation efficiently, ensuring all components were correctly aligned and secured. This attention to detail helped to prevent operational issues and extend the life of the conveyor system.
Utilizing a detailed belt conveyor parts and functions PDF is an integral part of the conveyor belt installation procedure. It ensures that all components are correctly installed and aligned, helping to achieve a reliable and efficient conveyor system. By understanding the importance of each part, accessing comprehensive documentation, and referencing it during installation, companies can enhance the performance and longevity of their conveyor systems.
Comprehensive Maintenance PDF for an Effective Conveyor Belt Installation Procedure
Comprehensive Maintenance Guides
A detailed maintenance PDF guide is an essential component of the conveyor belt installation procedure, ensuring that all maintenance activities are performed consistently and effectively. The importance of having such a guide cannot be overstated, as it provides a standardized approach to maintaining the conveyor system, which is crucial for its longevity and efficiency.
Importance of Having a Detailed Maintenance PDF Guide: A comprehensive maintenance PDF serves as a centralized reference that outlines all necessary maintenance tasks, schedules, and procedures. For example, companies like Flexco and Continental provide extensive maintenance guides that cover everything from routine inspections to complex repairs. These guides ensure that maintenance personnel are well-informed and equipped to handle any issues that arise, reducing the risk of downtime and costly repairs.
Key Sections to Include in a Maintenance Guide: An effective maintenance PDF should include several key sections:
- Introduction and Safety Guidelines: This section should introduce the maintenance manual and outline all necessary safety protocols.
- Routine Maintenance Schedule: A detailed timetable for regular maintenance activities, such as inspections, lubrication, and component replacements.
- Inspection Procedures: Step-by-step instructions for inspecting various parts of the conveyor system, including belts, pulleys, rollers, and safety devices.
- Troubleshooting and Repair Guidelines: Detailed procedures for diagnosing and fixing common issues that may arise during the conveyor belt installation procedure.
- Parts and Tools List: A comprehensive list of parts and tools required for maintenance tasks, ensuring that maintenance personnel have everything they need.
- Record Keeping and Reporting: Guidelines for documenting maintenance activities and reporting any issues or repairs.
Downloading and Utilizing Maintenance PDFs
Accessing and integrating maintenance PDFs into your routine is crucial for maintaining an effective conveyor belt installation procedure.
Recommended Sources for Maintenance PDF Downloads: Trusted sources for downloading maintenance PDFs include the websites of major conveyor system manufacturers. For example, Flexco, Fenner Dunlop, and Sparks Belting offer detailed maintenance guides on their websites. These guides are typically available in the resources or support sections and are free to download.
Integrating the Guide into Your Maintenance Routine: To make the most of the maintenance PDF, it should be seamlessly integrated into your daily operations. This can be achieved by:
- Distributing the PDF to All Maintenance Personnel: Ensure that all team members have access to the guide, either in digital format on tablets or printed copies.
- Regular Training Sessions: Conduct regular training sessions to familiarize staff with the contents of the guide and the importance of following the procedures outlined in it. For instance, Continental conducts periodic training for their maintenance teams, emphasizing the correct use of their maintenance PDFs.
- Creating a Maintenance Calendar: Use the routine maintenance schedule from the PDF to create a maintenance calendar, ensuring that all tasks are performed on time.
- Documenting Maintenance Activities: Encourage maintenance personnel to document all activities as outlined in the record-keeping section of the PDF. This helps in tracking the system’s health and identifying recurring issues.
Benefits of a Maintenance PDF
Implementing a maintenance PDF as part of the conveyor belt installation procedure offers numerous benefits, enhancing the overall efficiency and reliability of the conveyor system.
- Streamlining Maintenance Processes: A detailed maintenance PDF helps streamline the maintenance process by providing clear, step-by-step instructions for all tasks. This reduces confusion and ensures that all maintenance activities are performed correctly and efficiently. For example, Flexco’s maintenance guides are designed to be user-friendly, helping technicians quickly find the information they need and perform tasks accurately.
- Ensuring Consistency and Thoroughness in Maintenance Tasks: Consistency is key to effective maintenance. A standardized maintenance PDF ensures that all tasks are performed consistently, regardless of who is conducting the maintenance. This thorough approach helps in early detection of potential issues, preventing minor problems from escalating into major failures. According to a study by Fenner Dunlop, consistent use of a maintenance PDF can reduce unexpected downtime by up to 25%.
Using a comprehensive maintenance PDF as part of the conveyor belt installation procedure not only helps in maintaining the system’s efficiency but also extends its lifespan. By ensuring that all maintenance tasks are performed regularly and correctly, companies can prevent costly repairs and downtime, ultimately improving their bottom line. Integrating these guides into daily operations, providing regular training, and maintaining thorough documentation are all key steps in achieving a reliable and effective conveyor system.
Method Statement for a Comprehensive Conveyor Belt Installation Procedure
Importance of a Method Statement
A method statement is a critical document in the conveyor belt installation procedure, providing a detailed description of the work to be done and the method by which it will be completed. This document ensures that all tasks are carried out safely, efficiently, and in compliance with relevant regulations and standards.
- Role of a Method Statement in the Conveyor Belt Installation Procedure: The method statement serves as a guide for the installation team, detailing each step of the conveyor belt installation procedure. It includes information on the equipment and materials to be used, the sequence of tasks, and the safety measures to be implemented. By following a well-prepared method statement, installation teams can minimize risks and ensure that the installation is completed correctly and on time. For example, companies like Flexco and Fenner Dunlop use detailed method statements to streamline their installation processes and ensure high standards of safety and quality.
- Legal and Safety Considerations: The method statement also addresses legal and safety considerations, ensuring compliance with local regulations and industry standards. This includes adherence to Occupational Safety and Health Administration (OSHA) guidelines and other relevant safety protocols. By incorporating these elements into the method statement, companies can protect their workers and avoid legal liabilities. For instance, Continental includes comprehensive safety guidelines in their method statements, which have helped them maintain an excellent safety record in their installation projects.
Developing a Method Statement
Creating an effective method statement involves a thorough understanding of the conveyor belt installation procedure and collaboration with various stakeholders.
Key Components to Include in a Method Statement
An effective method statement should include the following components:
- Scope of Work: A detailed description of the work to be performed, including the specific tasks involved in the conveyor belt installation procedure.
- Materials and Equipment: A list of all materials and equipment needed for the installation, along with their specifications.
- Step-by-Step Instructions: Detailed, step-by-step instructions for each phase of the installation process, from site preparation to final testing and commissioning.
- Risk Assessment: An assessment of potential risks associated with the installation, along with measures to mitigate these risks.
- Safety Procedures: Specific safety procedures to be followed during the installation, including the use of personal protective equipment (PPE) and emergency response plans.
- Quality Control Measures: Procedures for ensuring the quality of the installation, including inspection and testing protocols.
Involving Stakeholders and Experts in the Development Process
Developing a comprehensive method statement requires input from various stakeholders, including project managers, safety officers, and installation technicians. Engaging these experts ensures that all aspects of the conveyor belt installation procedure are covered and that the method statement is practical and effective. For example, involving a certified safety officer from NIBA (National Industrial Belting Association) can help identify potential hazards and develop appropriate safety measures.
Implementing the Method Statement
Ensuring compliance with the method statement during the conveyor belt installation procedure is crucial for a successful installation.
- How to Ensure Compliance with the Method Statement During Installation: To ensure compliance, the method statement should be distributed to all team members involved in the installation. Regular briefings and training sessions can help reinforce the importance of following the method statement and address any questions or concerns. Additionally, assigning a supervisor or project manager to oversee the installation can help ensure that all tasks are performed according to the method statement. For instance, Flexco assigns experienced supervisors to monitor their installations, ensuring strict adherence to the method statement and maintaining high standards of safety and quality.
- Monitoring and Documenting the Installation Process: Continuous monitoring and documentation are essential for maintaining compliance and identifying areas for improvement. This includes regular inspections and audits of the installation process, as well as detailed record-keeping of all activities performed. Using digital tools and software can streamline this process, allowing for real-time tracking and reporting. For example, Fenner Dunlop uses a computerized maintenance management system (CMMS) to monitor their installations, providing real-time data and ensuring that all tasks are documented and analyzed for future reference.
Implementing a comprehensive method statement as part of the conveyor belt installation procedure ensures that the installation is carried out safely, efficiently, and in compliance with all relevant regulations. By developing a detailed method statement, involving stakeholders and experts, and ensuring strict compliance during the installation, companies can achieve successful and reliable conveyor system installations.
Fill out the form to get a quote for our durable and reliable conveyor belts.
FAQs about Conveyor Belt Installation Procedure
Installing a belt in a conveyor belt system involves several crucial steps to ensure optimal performance and longevity. First, you need to turn off and lock out all power to the conveyor system. Safety is paramount, so make sure the conveyor is completely shut down. Next, loosen the tension on the belt by adjusting the take-up mechanism. Carefully remove the old belt if necessary, and inspect all conveyor components for any signs of wear or damage. Clean the conveyor thoroughly to remove any debris. Lay the new belt on the conveyor frame, ensuring it is properly aligned. Gradually re-tension the belt, ensuring it is centered and aligned correctly along the conveyor structure. Adjust the tracking and make any necessary fine-tuning adjustments to prevent the belt from drifting during operation. Finally, power up the conveyor and conduct a test run to verify the success of the installation. Ensure that the belt runs smoothly without any issues, completing the final step on how to install a conveyor belt.
Setting up a conveyor belt requires careful planning and precise execution. Begin by reviewing the conveyor system’s specifications and requirements. Ensure that all necessary tools and materials are available, including the conveyor belt, rollers, and tensioning devices. Position the conveyor belt frame in its designated location, ensuring it is level and properly anchored. Install the rollers or idlers along the conveyor frame, following the manufacturer’s guidelines. Attach the conveyor belt to the frame, making sure it is centered and aligned. Gradually tension the belt using the take-up mechanism, ensuring it is not too tight or too loose. Adjust the tracking to prevent any belt misalignment during operation. Conduct a thorough inspection to ensure all components are securely fastened and properly aligned. Once satisfied, power up the conveyor system and perform a test run to verify smooth and efficient belt movement. Make any necessary adjustments to optimize performance and ensure the belt operates without any issues.
Joining conveyor belts is a critical step in ensuring a continuous and efficient conveyor system. The process typically involves two main methods: mechanical splicing and vulcanizing. Mechanical splicing is quicker and involves using metal fasteners or clips to join the belt ends. To start, align the belt ends and mark the splice area. Install the fasteners according to the manufacturer’s instructions, ensuring a secure and tight connection. Vulcanizing, on the other hand, is a more permanent solution that involves heat and pressure to bond the belt ends. This process begins by preparing the belt ends, cutting them to the required length, and skiving them to create a smooth surface. Apply a bonding agent and align the belt ends in a vulcanizing press. The press applies heat and pressure to fuse the belt ends, creating a strong and seamless joint. After cooling, inspect the splice to ensure it is properly bonded and free of defects. Both methods require precision and attention to detail to ensure a reliable and durable splice.
The process of conveyor belts involves several stages, from design and manufacturing to installation and maintenance. Initially, conveyor belts are designed based on the specific needs and requirements of the application. Factors such as load capacity, belt speed, and environmental conditions are considered. The manufacturing process involves selecting appropriate materials, such as rubber, PVC, or metal, and fabricating the belt to the desired dimensions. Once manufactured, the conveyor belt is installed in the conveyor system, following precise procedures to ensure proper alignment and tension. The installation process includes setting up the conveyor frame, installing rollers or idlers, and tensioning the belt. After installation, regular maintenance is essential to ensure optimal performance and longevity. This includes inspecting the belt for wear and damage, adjusting the tension and tracking, and cleaning the conveyor components. Proper maintenance helps prevent downtime and extends the lifespan of the conveyor belt, ensuring efficient and reliable operation in various industrial applications.
Last Updated on August 1, 2024 by Jordan Smith
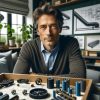
Jordan Smith, a seasoned professional with over 20 years of experience in the conveyor system industry. Jordan’s expertise lies in providing comprehensive solutions for conveyor rollers, belts, and accessories, catering to a wide range of industrial needs. From initial design and configuration to installation and meticulous troubleshooting, Jordan is adept at handling all aspects of conveyor system management. Whether you’re looking to upgrade your production line with efficient conveyor belts, require custom conveyor rollers for specific operations, or need expert advice on selecting the right conveyor accessories for your facility, Jordan is your reliable consultant. For any inquiries or assistance with conveyor system optimization, Jordan is available to share his wealth of knowledge and experience. Feel free to reach out at any time for professional guidance on all matters related to conveyor rollers, belts, and accessories.