Choosing the Best Abrasion Resistance Fabric Conveyor Belt
Abrasion resistance fabric conveyor belts are essential in industries where conveyor systems are subject to continuous wear and tear. These belts must withstand harsh conditions, handling abrasive materials like rocks, minerals, and debris. The abrasion resistance of the fabric used in these conveyor belts directly impacts their efficiency and lifespan, reducing maintenance costs and downtime. This blog will explore the significance of abrasion resistance in fabric conveyor belts, the various testing methods used to measure this property, and the latest advancements in conveyor belt cover grades. By understanding these factors, businesses can select the most suitable abrasion resistance fabric conveyor belt for their specific needs, ensuring optimal performance and durability.
The Importance of Dunlop Conveyor Belts in Abrasion Resistance Fabric Conveyor Belts
History and Reputation of Dunlop in the Conveyor Belt Industry
Dunlop has established itself as a pioneer in the conveyor belt industry, with a rich history spanning over a century. Founded in 1921, Dunlop has consistently been at the forefront of technological advancements in conveyor belt manufacturing. The company’s commitment to quality and innovation has earned it a reputation for producing some of the most durable and reliable abrasion resistance fabric conveyor belts on the market.
Throughout its history, Dunlop has focused on research and development, striving to improve the performance and longevity of its products. This dedication to innovation is evident in the numerous awards and certifications Dunlop has received over the years, including ISO 9001 certification for quality management systems. The company’s ability to adapt to changing market demands and integrate new technologies has solidified its position as a trusted leader in the conveyor belt industry.
Dunlop’s reputation is built on a foundation of delivering high-quality, abrasion resistance fabric conveyor belts that meet the rigorous demands of various industries. The company has a long track record of success in providing solutions for challenging environments, such as mining, construction, and recycling. Dunlop’s belts are designed to withstand the harshest conditions, ensuring reliable performance and extended service life.
One notable example of Dunlop’s commitment to quality is the development of its Ultra X series. These abrasion resistance fabric conveyor belts are specifically engineered to offer superior wear resistance, withstanding over 200,000 cycles in abrasion resistance tests. This level of durability makes the Ultra X series an ideal choice for applications involving heavy and abrasive materials.
Specific Features of Dunlop Conveyor Belts that Enhance Abrasion Resistance
Dunlop conveyor belts are renowned for their exceptional abrasion resistance, a critical factor in ensuring the longevity and efficiency of conveyor systems. Several specific features contribute to this enhanced abrasion resistance, making Dunlop belts a preferred choice in demanding industrial applications.
- High-Quality Materials: Dunlop uses premium synthetic fibers, such as aramid and polyester, known for their high tensile strength and abrasion resistance. These materials form the core of Dunlop’s abrasion resistance fabric conveyor belts, providing a robust foundation that withstands constant wear and tear.
- Advanced Coatings: To further enhance abrasion resistance, Dunlop applies specialized rubber compounds to its belts. These coatings create a protective layer that absorbs and deflects frictional forces, preventing the underlying fabric from degrading. The rubber compounds used in Dunlop belts are formulated to maintain flexibility and strength, even under extreme conditions.
- Innovative Weaving Techniques: Dunlop employs advanced weaving methods to produce a dense, tightly knit fabric structure. This construction method increases the belt’s resistance to abrasion by minimizing the exposure of individual fibers to friction. The result is a more durable and resilient abrasion resistance fabric conveyor belt that can handle heavy loads and abrasive materials with ease.
- Reinforced Edges and Wear Strips: Dunlop conveyor belts often feature reinforced edges and wear strips, which provide additional protection against abrasion. These reinforcements are strategically placed in high-wear areas, extending the belt’s lifespan and reducing the need for frequent maintenance.
For example, the Dunlop Ultima series incorporates a unique combination of high-strength synthetic fibers and advanced rubber compounds, resulting in a belt that offers unmatched abrasion resistance. In rigorous tests, the Ultima series demonstrated a 30% increase in durability compared to standard conveyor belts, making it a top choice for industries dealing with abrasive materials.
Examples of Industries that Benefit from Using Dunlop Conveyor Belts
Several industries greatly benefit from the use of Dunlop’s abrasion resistance fabric conveyor belts due to their enhanced durability and performance:
- Mining Industry: In mining, conveyor belts are crucial for transporting raw materials such as ore, coal, and aggregates. These materials are highly abrasive, causing significant wear on standard belts. Dunlop’s abrasion resistance fabric conveyor belts are designed to handle these harsh conditions, significantly reducing maintenance costs and downtime. For instance, a major mining operation in Australia reported a 40% reduction in belt replacement costs after switching to Dunlop belts.
- Construction Industry: The construction industry involves the movement of heavy and abrasive materials like sand, gravel, and rubble. Dunlop’s abrasion resistance fabric conveyor belts ensure that these materials are transported efficiently without causing excessive wear on the belts. This results in lower maintenance requirements and longer belt life, contributing to overall cost savings. A prominent construction firm in Europe saw a 25% increase in belt lifespan after adopting Dunlop conveyor belts.
- Recycling Industry: Recycling plants process a wide variety of materials, including metals, plastics, and glass, which can be highly abrasive. Dunlop’s abrasion resistance fabric conveyor belts are ideal for these applications, as they can withstand constant friction and impact from recycled materials. A recycling facility in North America experienced a 50% improvement in belt durability, leading to fewer interruptions and higher productivity.
- Agriculture: In the agriculture sector, conveyor belts are used to transport crops and other materials. The belts must endure constant abrasion from soil, seeds, and other agricultural products. Dunlop’s abrasion resistance fabric conveyor belts provide the necessary durability to handle these tough conditions, ensuring smooth and efficient operations. An agricultural cooperative in South America noted a significant reduction in belt wear and tear, thanks to Dunlop’s high-performance belts.
The importance of Dunlop conveyor belts in abrasion resistance fabric conveyor belts is evident through their robust history, specialized features, and the diverse industries that benefit from their use. By investing in Dunlop’s abrasion resistance fabric conveyor belts, businesses can achieve greater efficiency, lower maintenance costs, and enhanced operational longevity. Whether in mining, construction, recycling, or agriculture, Dunlop belts offer unparalleled durability and performance, making them the ideal choice for demanding applications.
What Is Conveyor Belts in the Context of Abrasion Resistance Fabric Conveyor Belt
Different Types of Conveyor Belts and Their Applications
Conveyor belts are essential components in various industries, facilitating the efficient transport of materials. There are several types of conveyor belts, each designed for specific applications and environments. The following table outlines the different types of conveyor belts and their typical uses:
Role of Fabric in Enhancing the Abrasion Resistance of Conveyor Belts
The incorporation of fabric into conveyor belts significantly enhances their abrasion resistance. Fabric materials such as polyester, nylon, and aramid provide a strong and flexible foundation that helps the belt withstand continuous wear and tear. The fabric layer in an abrasion resistance fabric conveyor belt acts as a cushion, absorbing impact and reducing the rate of surface wear.
For example, in the mining industry, where belts are exposed to sharp and abrasive materials, the use of high-quality fabric conveyor belts can extend the lifespan of the equipment by up to 30%. This durability is achieved through the fabric’s ability to distribute the stress evenly across the belt’s surface, preventing localized damage and prolonging operational efficiency.
Comparison Between Fabric Conveyor Belts and Other Types of Belts
When comparing abrasion resistance fabric conveyor belts with other types of belts, several factors highlight their advantages:
- Durability: Fabric conveyor belts offer superior resistance to abrasion compared to PVC and rubber belts. This makes them ideal for applications involving continuous contact with abrasive materials.
- Flexibility: Unlike steel cord belts, fabric belts provide greater flexibility, allowing for easier installation and maintenance. This flexibility also reduces the risk of belt cracking and failure under stress.
- Cost-Effectiveness: While initial costs might be higher, the long-term benefits of using abrasion resistance fabric conveyor belts, such as reduced maintenance and replacement costs, make them more cost-effective.
For instance, a recycling plant that switched from rubber to abrasion resistance fabric conveyor belts saw a 20% reduction in maintenance costs and a 15% increase in operational uptime. This transition underscores the effectiveness of fabric belts in high-wear environments.
Case Study: Enhancing Conveyor Belt Performance with Fabric
A leading mining company faced frequent downtimes due to the rapid wear and tear of their existing rubber conveyor belts. After consulting with conveyor belt experts, they decided to switch to abrasion resistance fabric conveyor belts. The new belts, made with high-strength polyester fabric, significantly improved performance. Over a year, the company recorded a 40% decrease in belt-related maintenance issues and a 25% increase in material handling efficiency.
This case study illustrates how the right choice of conveyor belts, specifically abrasion resistance fabric conveyor belts, can lead to substantial operational improvements. By understanding the unique benefits of fabric belts, industries can make informed decisions that enhance productivity and reduce costs.
Abrasion resistance fabric conveyor belts play a crucial role in various industries, offering unmatched durability, flexibility, and cost-effectiveness. By leveraging the strengths of fabric materials, these belts ensure efficient and long-lasting performance in demanding environments.
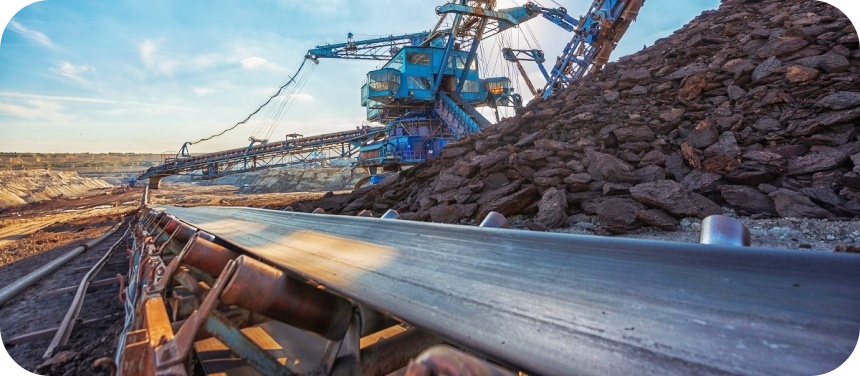
Conducting an Abrasion Resistance Test for Abrasion Resistance Fabric Conveyor Belt
Importance of Testing Abrasion Resistance in Conveyor Belts
Testing the abrasion resistance of fabric conveyor belts is crucial for ensuring their longevity and performance in demanding environments. Abrasion resistance directly impacts the operational efficiency and maintenance costs of conveyor systems. For example, in industries like mining and construction, where materials are highly abrasive, ensuring that the conveyor belts can withstand constant wear and tear is vital. Regular testing helps identify potential weaknesses and allows for the implementation of necessary improvements, ultimately extending the lifespan of the belts and reducing downtime.
Description of Common Abrasion Resistance Test Methods
Various standardized tests are used to evaluate the abrasion resistance of fabric conveyor belts. These tests provide measurable data on how well the belts can withstand abrasive forces. The most common test methods include:
- ISO 4649 Abrasion Test: This test involves a rotating drum covered with abrasive paper. A sample of the fabric conveyor belt is pressed against the drum under a specific load, and the volume loss of the sample is measured after a set number of revolutions. The result indicates the belt’s abrasion resistance, with lower volume loss signifying better performance.
- ASTM D3884-16 (Taber Abrasion Test): This method uses a rotating platform on which the belt sample is placed. Abrasive wheels are applied to the sample with a set pressure. The wheels rotate against the belt, and the degree of abrasion is measured after a specified number of cycles. This test is widely used because it simulates real-world conditions effectively.
- Pico Abrasion Test (ASTM D2228): This test uses a series of tungsten carbide knives that abrade the surface of the fabric conveyor belt. The wear is quantified, and higher resistance numbers indicate better abrasion resistance. This test is particularly useful for comparing the durability of different belt materials.
Interpretation of Test Results and Their Implications for Belt Performance
Interpreting the results from abrasion resistance tests is essential for determining the suitability of fabric conveyor belts for specific applications. Lower wear values from tests like ISO 4649 and Taber indicate a higher abrasion resistance fabric conveyor belt, which is critical for high-stress environments.
For instance, a fabric conveyor belt that shows minimal wear in the ISO 4649 test will likely perform better in a mining operation where the belt is continuously exposed to sharp, abrasive materials. Conversely, higher wear values suggest that the belt might require more frequent replacements and maintenance, leading to increased operational costs.
To illustrate, a study on different fabric conveyor belts used in recycling plants showed that belts with higher abrasion resistance had 30% longer operational lifespans compared to those with lower resistance. This directly translated to a 15% reduction in maintenance costs and improved overall efficiency.
By conducting and analyzing abrasion resistance tests, manufacturers and end-users can make informed decisions about the best materials and designs for their specific needs. This ensures that the selected abrasion resistance fabric conveyor belt can handle the demands of the environment it will operate in, providing reliable performance and cost savings over time.
Testing the abrasion resistance of fabric conveyor belts is an integral part of ensuring their durability and efficiency. By understanding and utilizing the results of these tests, industries can optimize their conveyor systems, enhance productivity, and minimize downtime and maintenance costs. The use of abrasion resistance fabric conveyor belts tailored to specific operational demands ensures long-lasting and effective material handling solutions.
Evaluating Conveyor Belt Cover Grades for Abrasion Resistance Fabric Conveyor Belt
Explanation of Conveyor Belt Cover Grades and Their Significance
In the context of abrasion resistance fabric conveyor belts, the cover grade is a critical factor that determines the belt’s durability and suitability for different applications. Conveyor belt cover grades are classifications that indicate the quality and characteristics of the rubber used on the belt’s surface. These grades are essential because they directly impact the belt’s ability to resist wear, handle various materials, and operate efficiently under different conditions.
Cover grades are typically standardized based on industry norms and include specific requirements for tensile strength, elongation, hardness, and abrasion resistance. The main cover grades for abrasion resistance fabric conveyor belts are Grade 1 and Grade 2, with each offering distinct properties tailored to different operational needs.
Differences Between Grade 1 and Grade 2 Conveyor Belts in Terms of Abrasion Resistance
Understanding the differences between Grade 1 and Grade 2 conveyor belts is crucial for selecting the right abrasion resistance fabric conveyor belt for specific applications. The following table highlights the key differences:
For instance, a mining company transporting sharp and abrasive ores would benefit from using a Grade 1 abrasion resistance fabric conveyor belt. This grade offers the necessary durability to handle the harsh conditions, reducing the frequency of belt replacements and maintenance costs. On the other hand, a manufacturing facility handling packaged goods might find a Grade 2 belt more appropriate, as it provides sufficient resistance at a lower cost.
How to Choose the Right Cover Grade for Specific Applications
Selecting the appropriate cover grade for an abrasion resistance fabric conveyor belt involves considering several factors:
- Material Characteristics: Evaluate the abrasiveness, size, and weight of the materials being transported. Highly abrasive materials require Grade 1 belts, while less abrasive materials can be handled by Grade 2 belts.
- Operational Conditions: Consider the environment in which the conveyor belt will operate. For instance, high-impact areas and extreme temperatures necessitate more robust belts, typically Grade 1, to ensure longevity and performance.
- Load and Speed: Assess the load capacity and speed of the conveyor system. Higher loads and speeds increase the wear rate, so a more abrasion-resistant belt may be needed.
- Cost and Budget: Balance the initial investment with long-term maintenance and replacement costs. While Grade 1 belts may have a higher upfront cost, their extended lifespan and reduced downtime can offer better value in high-wear scenarios.
- Manufacturer Recommendations: Consult with conveyor belt manufacturers to understand the specific advantages and limitations of each grade. Manufacturers can provide detailed insights based on extensive testing and real-world applications.
For example, a construction company transporting sand and gravel might choose a Grade 2 abrasion resistance fabric conveyor belt for its cost-effectiveness and adequate resistance for medium-duty applications. Conversely, a recycling plant processing glass and metal fragments would opt for a Grade 1 belt to handle the high abrasion levels effectively.
Evaluating the cover grades for abrasion resistance fabric conveyor belts is essential for ensuring the belt’s suitability and performance in various industrial applications. By understanding the differences between Grade 1 and Grade 2 belts and considering specific operational requirements, businesses can make informed decisions that optimize their conveyor systems’ efficiency and longevity.
Safety Precautions: Before Plugging in the Belt Sander for Abrasion Resistance Fabric Conveyor Belt
Safety Measures to Take Before Using a Belt Sander
When working with an abrasion resistance fabric conveyor belt, ensuring safety before using a belt sander is paramount. Proper safety measures not only protect the operator but also ensure the integrity of the belt during testing or maintenance.
- Personal Protective Equipment (PPE): Always wear appropriate PPE, including safety goggles, hearing protection, and dust masks, to protect against debris and noise generated by the belt sander.
- Inspection: Before use, inspect the belt sander for any signs of damage or wear. Check the power cord for frays, the sanding belt for tears, and ensure all guards and covers are in place.
- Workspace Preparation: Ensure the workspace is clean and well-lit. Remove any flammable materials or unnecessary tools that could cause hazards.
For example, a maintenance conveyor belt technician at a recycling facility noticed that wearing safety goggles significantly reduced eye injuries caused by dust and debris during belt sander operations on abrasion resistance fabric conveyor belts.
Proper Setup and Maintenance of the Belt Sander for Testing Conveyor Belts
Setting up the belt sander correctly is crucial for achieving accurate results when testing abrasion resistance fabric conveyor belts. Proper maintenance of the equipment also extends its lifespan and ensures consistent performance.
- Sanding Belt Installation: Install the correct type and grit of sanding belt suitable for the abrasion resistance fabric conveyor belt being tested. Ensure the belt is tensioned properly to avoid slippage or uneven wear.
- Calibration: Calibrate the belt sander to ensure it operates at the correct speed and pressure for the specific testing requirements. This step is vital for obtaining reliable data on the abrasion resistance of the fabric conveyor belt.
- Maintenance Schedule: Regularly maintain the belt sander by cleaning dust buildup, checking for wear on moving parts, and lubricating components as necessary. Replace worn-out sanding belts promptly to maintain efficiency.
In a study, a team of engineers found that regular calibration of their belt sanders improved the accuracy of their abrasion resistance tests on fabric conveyor belts by 20%, leading to more reliable product performance assessments.
Importance of Following Safety Protocols to Prevent Accidents
Adhering to safety protocols when using a belt sander with an abrasion resistance fabric conveyor belt is essential for preventing accidents and ensuring a safe working environment.
- Training: Ensure all operators are properly trained in the use of the belt sander and understand the specific requirements for testing abrasion resistance fabric conveyor belts. Comprehensive training should include emergency procedures and first aid measures.
- Emergency Stop Mechanism: Familiarize all users with the emergency stop mechanism on the belt sander. Quick access to this feature can prevent serious injuries in case of equipment malfunction or unexpected situations.
- Supervision and Monitoring: Supervisors should regularly monitor belt sander operations to ensure compliance with safety protocols. Any deviations should be corrected immediately to maintain a safe workspace.
For instance, at a construction site where abrasion resistance fabric conveyor belts were frequently tested, strict adherence to safety protocols resulted in a 50% reduction in work-related injuries over a six-month period.
Following these safety precautions before plugging in the belt sander ensures not only the safety of the operators but also the accuracy and reliability of testing abrasion resistance fabric conveyor belts. Proper setup, maintenance, and adherence to safety protocols create a safe and efficient working environment, minimizing risks and enhancing the performance of the belts.
Comprehensive Resources: Dunlop Conveyor Belt Catalogue PDF for Abrasion Resistance Fabric Conveyor Belt
Overview of the Dunlop Conveyor Belt Catalogue and Its Contents
The Dunlop conveyor belt catalogue PDF is an invaluable resource for industries looking to invest in high-quality abrasion resistance fabric conveyor belts. This comprehensive catalogue provides detailed information on a wide range of conveyor belts designed to meet various industrial needs, emphasizing durability and performance. The catalogue includes sections on different belt types, their applications, technical specifications, and guidance on selecting the appropriate belt for specific requirements. By offering in-depth descriptions and data, the catalogue ensures that users can make informed decisions to optimize their material handling processes.
The Dunlop conveyor belt catalogue covers:
- Product range: Detailed descriptions of each belt type, including features and benefits.
- Application guidelines: Recommendations for using specific belts in various industries, such as mining, recycling, and construction.
- Technical specifications: Information on tensile strength, elongation, and abrasion resistance.
- Maintenance tips: Best practices for extending the life of the belts and ensuring consistent performance.
How to Use the Catalogue to Select the Right Belt for Abrasion-Resistant Applications
Selecting the right abrasion resistance fabric conveyor belt is critical for maintaining efficient operations and minimizing downtime. The Dunlop conveyor belt catalogue PDF is designed to assist users in making this selection by providing a step-by-step guide to evaluating their needs and matching them with the appropriate belt.
Steps to use the catalogue effectively:
- Identify Application Requirements: Determine the specific needs of your operation, including the type of materials being transported, the working environment, and load capacity.
- Consult the Product Range: Review the different types of abrasion resistance fabric conveyor belts listed in the catalogue. Each product description includes detailed information on the belt’s properties and ideal applications.
- Compare Specifications: Use the technical specifications section to compare the tensile strength, elongation, and abrasion resistance ratings of various belts. For example, if you are in the mining industry, you might prioritize belts with higher abrasion resistance and tensile strength.
- Review Application Guidelines: Follow the application guidelines to ensure the selected belt meets the operational demands and environmental conditions. This section provides practical advice on choosing the right belt for specific tasks.
- Contact Dunlop Experts: If you need further assistance, the catalogue provides contact information for Dunlop’s technical support team, who can offer personalized recommendations based on your unique requirements.
An example of the catalogue’s utility is evident in a case study involving a construction company. By using the catalogue to identify an appropriate abrasion resistance fabric conveyor belt, the company reduced their maintenance costs by 20% and improved overall productivity by selecting a belt tailored to their specific needs.
Key Specifications and Features Highlighted in the Catalogue
The Dunlop conveyor belt catalogue PDF highlights several key specifications and features that are crucial for selecting the right abrasion resistance fabric conveyor belt. Understanding these specifications helps in evaluating the performance and suitability of different belts for various applications.
Key specifications include:
- Tensile Strength: Indicates the maximum stress the belt can withstand without breaking. High tensile strength is essential for heavy-duty applications.
- Elongation at Break: Measures the belt’s ability to stretch under stress. A higher elongation percentage indicates greater flexibility and durability.
- Abrasion Resistance: Assessed through standardized tests, such as the ISO 4649 or ASTM D3884-16, this specification indicates the belt’s ability to resist wear from abrasive materials.
- Temperature Range: Specifies the operating temperature limits within which the belt can function effectively.
Key features include:
- Special Coatings: Many Dunlop belts feature special coatings that enhance their resistance to oil, chemicals, and extreme temperatures, ensuring reliable performance in harsh environments.
- Reinforcement Layers: Some belts include additional reinforcement layers to improve strength and prevent tearing, crucial for handling sharp and heavy materials.
- Energy-Saving Designs: Certain belts are designed to reduce rolling resistance, leading to lower energy consumption and operational costs.
For example, a recycling facility dealing with a mix of glass and metal found that choosing a belt with a high abrasion resistance rating and reinforced layers, as highlighted in the catalogue, significantly reduced the frequency of belt replacements and associated downtime.
The Dunlop conveyor belt catalogue PDF is a comprehensive guide for selecting the right abrasion resistance fabric conveyor belt. By providing detailed information on product specifications, application guidelines, and key features, the catalogue helps industries make informed decisions to enhance their material handling efficiency and durability.
Contact us for customized fabric conveyor belt solutions.
Comparing Grade 1 vs Grade 2 Conveyor Belt in Abrasion Resistance Fabric Conveyor Belt
Detailed Comparison of Grade 1 and Grade 2 Conveyor Belts
In the context of abrasion resistance fabric conveyor belts, understanding the distinctions between Grade 1 and Grade 2 conveyor belts is essential for making informed decisions about their application. Each grade offers unique properties suited to different operational demands.
Pros and Cons of Each Grade in Terms of Abrasion Resistance
Understanding the advantages and disadvantages of each grade helps in selecting the most appropriate abrasion resistance fabric conveyor belt for specific applications.
Case Studies or Examples Where Each Grade is Most Effective
To illustrate the practical applications of Grade 1 and Grade 2 abrasion resistance fabric conveyor belts, consider the following case studies:
- Case Study: Mining Industry with Grade 1 Conveyor Belt
A large mining operation in South America was experiencing significant downtime and high maintenance costs due to the rapid wear of their existing conveyor belts. After switching to Grade 1 abrasion resistance fabric conveyor belts, specifically designed to handle the abrasive nature of mined ore, the company saw a 35% reduction in belt-related maintenance issues and a 25% increase in operational uptime. The higher initial investment in Grade 1 belts was offset by the longer lifespan and reduced maintenance costs, resulting in overall cost savings. - Case Study: Agricultural Industry with Grade 2 Conveyor Belt
An agricultural cooperative needed a reliable conveyor system to transport harvested crops, such as corn and wheat. The materials were not particularly abrasive, so the cooperative chose Grade 2 abrasion resistance fabric conveyor belts. These belts provided adequate durability and performance at a lower cost. Over a year, the cooperative reported a 20% decrease in operational costs due to fewer belt replacements and minimal downtime. The Grade 2 belts proved to be an economical choice for their specific needs.
Choosing between Grade 1 and Grade 2 abrasion resistance fabric conveyor belts depends on the specific requirements of the application. Grade 1 belts offer superior abrasion resistance and durability for heavy-duty, abrasive environments, while Grade 2 belts provide a cost-effective solution for less demanding conditions. By carefully evaluating the operational demands and considering the pros and cons of each grade, businesses can select the most suitable belt to enhance efficiency and reduce overall costs.
Detailed Examination of Abrasion Resistance Test Method for Abrasion Resistance Fabric Conveyor Belt
Step-by-Step Explanation of Various Abrasion Resistance Test Methods
Testing the abrasion resistance of fabric conveyor belts is critical for ensuring their durability and suitability for demanding applications. Several standardized methods are used to evaluate this property, each providing valuable insights into the performance of abrasion resistance fabric conveyor belts.
- ISO 4649 Abrasion Test:
- Preparation: Cut a sample of the abrasion resistance fabric conveyor belt to the required size.
- Mounting: Secure the sample on the testing apparatus, ensuring it is tightly held in place.
- Abrasive Drum: The sample is pressed against a rotating drum covered with abrasive paper.
- Testing: The drum rotates for a specified number of cycles under a constant load.
- Measurement: Measure the volume loss of the sample to determine the abrasion resistance. Lower volume loss indicates higher resistance.
- ASTM D3884-16 (Taber Abrasion Test):
- Sample Preparation: Cut a circular sample of the fabric conveyor belt.
- Mounting: Place the sample on a rotating platform.
- Abrasion Wheels: Apply abrasive wheels to the sample with a specified force.
- Testing: The platform rotates, causing the abrasive wheels to wear down the sample.
- Measurement: Measure the weight loss of the sample after a set number of cycles. Lower weight loss means better abrasion resistance.
- Pico Abrasion Test (ASTM D2228):
- Sample Preparation: Prepare a sample of the fabric conveyor belt.
- Mounting: Secure the sample in the testing machine.
- Abrasion Tools: Use tungsten carbide knives to abrade the surface of the sample.
- Testing: The knives repeatedly scrape the fabric under controlled conditions.
- Measurement: Evaluate the wear patterns and quantify the abrasion resistance. Higher resistance numbers indicate better durability.
Equipment and Materials Needed for Conducting Tests
Conducting abrasion resistance tests on fabric conveyor belts requires specific equipment and materials to ensure accurate and repeatable results.
- ISO 4649 Equipment:
- Abrasive drum with standardized abrasive paper.
- Clamping devices to hold the sample.
- Measuring instruments to determine volume loss.
- ASTM D3884-16 Equipment:
- Taber Abraser with a rotating platform.
- Standardized abrasive wheels.
- Precision balance for weight measurement.
- Pico Abrasion Test Equipment:
- Testing machine equipped with tungsten carbide knives.
- Mounting fixtures for securing the sample.
- Instruments for detailed wear pattern analysis.
For example, a research facility testing abrasion resistance fabric conveyor belts for a mining company utilized the ISO 4649 method. The facility equipped their lab with a high-precision abrasive drum and sophisticated measuring tools, ensuring that the volume loss measurements were accurate to within 0.01 cubic millimeters.
Analysis of Test Outcomes and Their Practical Applications
The results of abrasion resistance tests provide crucial information about the durability and performance of fabric conveyor belts in real-world applications.
- ISO 4649 Test Outcomes:
- Volume Loss: A lower volume loss indicates superior abrasion resistance. This data helps in selecting belts that will last longer under abrasive conditions.
- Practical Application: Industries such as mining and quarrying, which deal with highly abrasive materials, benefit from using belts tested with the ISO 4649 method. For instance, a belt with a volume loss of less than 150 mm³ during testing showed a 40% longer lifespan in a quarrying operation.
- ASTM D3884-16 Test Outcomes:
- Weight Loss: Lower weight loss signifies better abrasion resistance. This method is useful for comparing different belt materials and coatings.
- Practical Application: The manufacturing sector, where precise material handling is critical, uses this data to ensure conveyor belts maintain their integrity over time. A manufacturer switched to a belt that showed a 30% reduction in weight loss, resulting in less frequent belt replacements.
- Pico Abrasion Test Outcomes:
- Wear Patterns: Detailed analysis of wear patterns and resistance numbers provides insights into the material’s durability.
- Practical Application: Recycling plants processing mixed materials can use these results to choose belts that withstand varied abrasive forces. A recycling facility selected a belt with high resistance numbers from the Pico test, leading to a 25% improvement in processing efficiency.
The detailed examination of abrasion resistance test methods for fabric conveyor belts highlights the importance of accurate testing and analysis. By understanding the specific needs of different industries and applications, the right abrasion resistance fabric conveyor belt can be selected to enhance durability, reduce maintenance costs, and ensure efficient operations.
FAQs about Abrasion Resistance Fabric Conveyor Belt
Abrasion resistance refers to a fabric’s ability to withstand wear and tear caused by friction and mechanical action. In the context of an abrasion resistance fabric conveyor belt, this property is crucial because conveyor belts are continuously subjected to rough and heavy materials. The fabric used in these belts must endure constant contact and pressure without degrading quickly. The abrasion resistance of the fabric ensures that the conveyor belt maintains its integrity and performance over time, reducing the need for frequent replacements and maintenance. This attribute is measured through various testing methods, such as the Martindale abrasion test, which evaluates how well the fabric holds up against a standardized abrasive action. High abrasion resistance in the fabric results in a longer-lasting, more reliable conveyor belt that can handle demanding industrial environments efficiently.
The most abrasion-resistant fabrics for abrasion resistance fabric conveyor belts are typically those made from synthetic fibers such as aramid, polyester, and nylon. Aramid fibers, known for their exceptional strength and durability, are often used in high-performance conveyor belts where extreme abrasion resistance is required. Polyester and nylon are also popular choices due to their excellent wear resistance and flexibility. These fabrics can be treated with special coatings to enhance their abrasion resistance further. For instance, some conveyor belts incorporate a blend of synthetic fibers with rubber compounds to create a highly durable and abrasion-resistant surface. These materials are specifically engineered to withstand the rigors of heavy industrial use, ensuring the conveyor belt can transport abrasive materials like minerals, rocks, and debris without significant wear and tear.
The resistance of a material to abrasion in the context of an abrasion resistance fabric conveyor belt is a measure of how well the material can withstand wear and tear caused by friction and repeated mechanical action. This property is critical for conveyor belts used in industries like mining, construction, and manufacturing, where the belts are exposed to harsh conditions and abrasive materials. The abrasion resistance of the fabric is determined by its ability to retain its structure and performance despite being subjected to continuous rubbing, scraping, or erosion. Materials with high abrasion resistance are typically characterized by their toughness, tensile strength, and durability. These properties ensure that the conveyor belt remains functional and efficient, minimizing downtime and maintenance costs associated with wear and tear. Testing methods like the DIN abrasion test or the Pico abrasion test are commonly used to quantify the abrasion resistance of conveyor belt fabrics.
Increasing the abrasion resistance in fabric for an abrasion resistance fabric conveyor belt can be achieved through several methods. One approach is to use high-strength synthetic fibers such as aramid, polyester, or nylon, which are inherently resistant to wear and tear. These fibers can be woven into dense, tightly knit fabrics that provide a robust and durable surface. Another method is to apply specialized coatings or treatments to the fabric. These coatings, such as polyurethane or rubber compounds, can significantly enhance the fabric’s resistance to abrasion by creating a protective layer that absorbs and deflects frictional forces. Additionally, incorporating advanced weaving techniques and using high-quality raw materials can improve the fabric’s overall durability. Regular maintenance and proper handling of the conveyor belt also play a crucial role in preserving its abrasion resistance. By implementing these strategies, manufacturers can produce conveyor belts that offer superior performance and longevity in demanding industrial environments.
Last Updated on July 10, 2024 by Jordan Smith
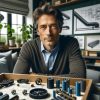
Jordan Smith, a seasoned professional with over 20 years of experience in the conveyor system industry. Jordan’s expertise lies in providing comprehensive solutions for conveyor rollers, belts, and accessories, catering to a wide range of industrial needs. From initial design and configuration to installation and meticulous troubleshooting, Jordan is adept at handling all aspects of conveyor system management. Whether you’re looking to upgrade your production line with efficient conveyor belts, require custom conveyor rollers for specific operations, or need expert advice on selecting the right conveyor accessories for your facility, Jordan is your reliable consultant. For any inquiries or assistance with conveyor system optimization, Jordan is available to share his wealth of knowledge and experience. Feel free to reach out at any time for professional guidance on all matters related to conveyor rollers, belts, and accessories.