Maximizing Durability with the Acid Resistant Conveyor Belt
An acid resistant conveyor belt is specially designed to withstand the harsh conditions of acidic environments. These belts are essential in industries where materials handled can cause corrosion or damage to standard conveyor systems. The importance of acid resistant conveyor belts lies in their ability to ensure operational safety and maintain efficiency in the face of corrosive substances. By utilizing materials that resist acid damage, these conveyor belts offer a durable solution for transporting goods in chemical plants, fertilizer production, and other sectors where acidic materials are prevalent. Their robust construction not only protects the conveyor system but also minimizes maintenance costs and downtime, making them a critical component in the smooth operation of many industrial applications.
The Need for the Acid Resistant Conveyor Belt
The Crucial Role in Various Industries
The acid resistant conveyor belt is indispensable in environments where exposure to chemicals is a daily occurrence. These specialized belts are designed to endure the harsh conditions found in chemical factories, fertilizer production, paper mills, mining operations, and the cement industry, among others. In these settings, materials with chemical corrosiveness are frequently handled, necessitating a conveying solution that can withstand such aggressive substances without degrading.
Industrial Applications Benefiting from Acid Resistance
- Chemical Factories: Where the handling of various acids and alkalis is routine, these conveyor belts resist corrosion, ensuring safe and uninterrupted operations.
- Fertilizer Factories: In the production of fertilizers, where chemicals could erode standard belts, acid resistant belts maintain integrity, preventing contamination and equipment damage.
- Paper Mills: The processing of paper often involves chemicals that could compromise the conveyor system; acid resistant belts offer a reliable solution.
- Mining Industry: Exposure to various chemicals used in processing ores necessitates the use of belts that can withstand such environments.
- Cement Industry: The handling of raw materials that may have acidic properties requires conveyance solutions that are not susceptible to chemical damage.
The deployment of acid resistant conveyor belts in these sectors underscores their significance in maintaining operational efficiency and safety, highlighting their role as a critical component of modern industrial operations.
Acid Resistant Conveyor Belt: Common Conveyor Belt Challenges and Acid Resistance
Overview of Conveyor Belt Challenges
Conveyor belts operating in chemical environments face numerous challenges, including rapid deterioration due to acid exposure, loss of material integrity, and increased risk of operational failures. These issues not only lead to frequent maintenance and replacements but also pose significant safety risks.
Acid Resistant Conveyor Belts as a Solution
The acid resistant conveyor belt is engineered to overcome these challenges by offering superior resistance to corrosive substances. Their specialized construction minimizes the common problems associated with chemical exposure, such as:
- Material Degradation: These belts are made from materials that can withstand acidic environments, significantly reducing the rate of wear and tear.
- Operational Failures: By resisting the corrosive effects of chemicals, these belts maintain their structural integrity, ensuring continuous and reliable operations.
The adoption of acid resistant conveyor belts in environments prone to chemical exposure effectively addresses the prevalent issues, enhancing both safety and efficiency in industrial operations.
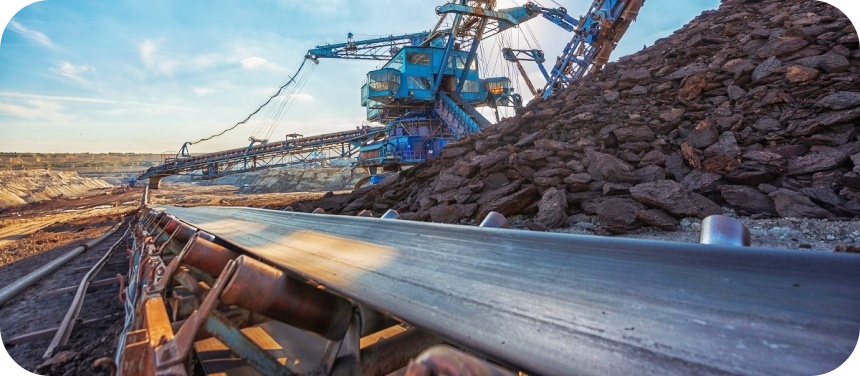
Key Features and Advantages of the Acid Resistant Conveyor Belt
Maximizing Performance with Acid Resistant Technology
The acid resistant conveyor belt stands out in the industrial sector for their unparalleled chemical and corrosion-resistant properties. These belts are engineered to endure the harsh conditions of chemical exposure, making them an indispensable asset in many industrial applications.
Superior Chemical and Corrosion-Resistant Properties
- Chemical Resistance: These belts are specifically designed to resist deterioration from various chemicals, including strong acids and alkalis. This resistance ensures that the belt’s integrity is maintained, even in environments with high chemical concentrations.
- Corrosion Resistance: Beyond resisting chemical damage, these belts are also built to withstand corrosion, ensuring longevity and durability in challenging industrial settings.
Five Key Advantages
- Excellent Elasticity and Minimal Elongation: These belts maintain their shape and tension under load, ensuring consistent operation and reducing the risk of misalignment or slippage.
- High Adhesion and Flexibility: The construction of acid resistant belts allows for high adhesion between the belt layers and flexibility, facilitating smooth operation over pulleys and through conveyor systems.
- Durability Against Chemical Damages: The material composition of these belts ensures they can withstand exposure to chemicals without degrading, significantly extending their service life.
- Superior Bonding Properties: The advanced manufacturing techniques used in these belts ensure that the layers bond securely, preventing layer separation even under harsh conditions.
- Resistance to a Wide Range of Chemicals: These belts are not just resistant to acids and alkalis; they can also handle chlorinated compounds and coolant oils, making them versatile for various industrial applications.
The combination of these features and advantages makes acid resistant conveyor belts a critical component in industries where chemical exposure is a routine challenge, ensuring operational continuity and safety.
Standards and Specifications for the Acid Resistant Conveyor Belt
Ensuring Quality and Reliability Through Rigorous Standards
Acid resistant conveyor belts are subject to stringent standards and specifications to ensure they meet the high demands of industrial applications. These standards guarantee that the belts possess the necessary qualities to withstand acidic environments effectively.
Conveyor Belt Standards
- International and Industry-Specific Standards: Acid resistant conveyor belts are manufactured in compliance with international standards such as ISO and DIN, as well as industry-specific standards that dictate performance criteria in chemical exposure scenarios.
- Quality Assurance: These standards ensure that the belts are of high quality, reliable, and capable of performing under the specified conditions without failure.
Datasheet Specifics
- Tensile Strength and Elongation at Break: These specifications indicate the belt’s ability to withstand tension and stretching, crucial for maintaining operational integrity.
- Abrasion, Hardness, and Ozone Deterioration: Measurements of the belt’s resistance to wear, its hardness level, and its ability to resist ozone deterioration are critical for assessing its durability.
- Acid and Alkali Resistance Classes: The classification (A1, A2, A3) provides a clear indication of the belt’s resistance level to different acids (HCL, H2SO4) and alkalis (NaOH), including the density and conditions of exposure.
Meeting or exceeding these standards and specifications is essential for the acid resistant conveyor belt, ensuring they can provide the necessary protection and durability in corrosive environments. This adherence to high standards is what makes these belts a reliable choice for industries facing chemical exposure challenges.
Get the best deals on conveyor belts here.
Choosing the Right Acid Resistant Conveyor Belt
Strategic Selection for Optimal Performance and Durability
Selecting the appropriate acid resistant conveyor belt for specific industrial applications is crucial to ensure operational efficiency, safety, and longevity of the conveyor system. Several factors must be considered to make an informed choice that meets the unique demands of each application.
Factors to Consider
- Chemical Composition of Materials: Understanding the specific chemicals the conveyor belt will be exposed to is essential. This includes the concentration of acids or alkalis and the temperature of the materials, as different belt materials offer varying levels of resistance.
- Operating Environment Conditions: The ambient environment—temperature, humidity, and exposure to other potentially damaging elements—can affect the performance and lifespan of the conveyor belt.
- Load Type and Size: The weight and nature of the materials being conveyed (e.g., sharp, abrasive, or heavy items) can influence the choice of belt material and design to ensure durability and reduce wear.
Importance of Comprehensive Evaluation
- Whole Thickness and Adhesive Strength: Evaluating the belt’s total thickness and the adhesive strength between layers is critical for assessing its ability to withstand the operational load and the corrosive effects of chemicals.
- Resistance Levels: It’s important to match the belt’s resistance levels with the chemicals’ corrosiveness it will encounter. This includes not only acid and alkali resistance but also resistance to other substances that may be present in the environment, such as oils or solvents.
Choosing the right acid resistant conveyor belt involves a thorough assessment of these factors to ensure the belt can perform effectively and last longer under specific operational conditions. This strategic selection process helps in optimizing the conveyor system’s performance and minimizing maintenance and replacement costs.
Real-World Applications and Conveyor Belt Examples
Demonstrating Versatility and Efficiency in Diverse Industries
The acid resistant conveyor belt has proven their value across various sectors by solving common conveyor belt problems and enhancing operational efficiency. This section highlights real-world applications and examples where these belts have made a significant impact.
Case Studies of Acid Resistant Conveyor Belts in Action
- Chemical Processing Plants: In environments where harsh chemicals are processed or manufactured, acid resistant conveyor belts have successfully prevented corrosion and material degradation, ensuring continuous production lines.
- Mining Operations: Facing acidic minerals and challenging conditions, these conveyor belts have offered durability and reliability, reducing downtime and maintenance costs.
- Fertilizer Production Facilities: Here, the belts withstand the corrosive effects of chemical fertilizers, maintaining the integrity of the conveyor system and preventing contamination.
Solving Industry-Specific Problems
- Enhanced Safety and Reliability: By resisting the corrosive effects of acids and alkalis, these belts ensure safer working conditions and more reliable material handling processes.
- Operational Efficiency: The durability and chemical resistance of these belts minimize the need for frequent replacements and maintenance, leading to improved operational efficiency and reduced operational costs.
These real-world examples underscore the critical role of the acid resistant conveyor belt in addressing industry-specific challenges, showcasing their ability to enhance safety, reliability, and efficiency in environments exposed to harsh chemicals.
FAQs about Acid Resistant Conveyor Belt
The best material for a conveyor belt depends on its intended application, including the type of materials it will carry and the environment in which it will operate. Common materials include:
Rubber: Versatile and durable, suitable for general use and bulk material handling.
PVC: Lightweight and suitable for various industries, including food processing and pharmaceuticals.
Polyurethane (PU): Offers excellent resistance to wear, chemicals, and oils, making it ideal for food processing and pharmaceutical applications.
Nylon: Known for its high strength and abrasion resistance, suitable for heavy-duty applications.
Steel: Used in metal belts for extreme conditions and high-strength applications.
A food grade conveyor belt is designed specifically for applications that require direct contact with food products. These belts are made from materials that meet strict hygiene standards to prevent contamination and ensure food safety. Common characteristics include:
Non-toxic and non-absorbent materials: Such as FDA-approved PVC, PU, and some grades of rubber.
Easy to clean: Surfaces that are smooth and resistant to bacteria growth.
Resistance to oils, fats, and chemicals: To ensure durability in various food processing environments.
Food grade conveyor belts are used in the food industry, including processing, packaging, and pharmaceuticals, to maintain the highest levels of hygiene and safety.
Alternatives to conveyor belts depend on the application and include:
Roller conveyors: Suitable for moving items in a straight line or through changes in elevation or direction.
Chute conveyors: Utilize gravity for the movement of materials from one level to another.
Bucket elevators: Ideal for vertically transporting bulk materials.
Pneumatic conveying systems: Use air pressure or vacuum to transport materials through tubes.
Vibratory conveyors: Employ vibration to move materials along a trough.
Each alternative has its unique advantages and is selected based on the specific needs of the material handling process.
The strongest conveyor belts are typically made from steel or other metal materials, designed for extreme conditions and heavy-duty applications. Steel cord conveyor belts, for example, are known for their high tensile strength, durability, and resistance to tearing and impact. They are used in mining, quarrying, and other heavy industries where high strength and the ability to carry heavy loads are crucial. These belts can handle tensile forces significantly higher than those of fabric-reinforced belts, making them the strongest type of conveyor belt available.
Last Updated on July 4, 2024 by Jordan Smith
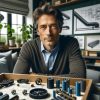
Jordan Smith, a seasoned professional with over 20 years of experience in the conveyor system industry. Jordan’s expertise lies in providing comprehensive solutions for conveyor rollers, belts, and accessories, catering to a wide range of industrial needs. From initial design and configuration to installation and meticulous troubleshooting, Jordan is adept at handling all aspects of conveyor system management. Whether you’re looking to upgrade your production line with efficient conveyor belts, require custom conveyor rollers for specific operations, or need expert advice on selecting the right conveyor accessories for your facility, Jordan is your reliable consultant. For any inquiries or assistance with conveyor system optimization, Jordan is available to share his wealth of knowledge and experience. Feel free to reach out at any time for professional guidance on all matters related to conveyor rollers, belts, and accessories.