Aggregate Belt Conveyor Systems Solutions
Aggregate materials, such as sand, gravel, and crushed stone, play a crucial role in the construction and various other industries.Enhance efficiency and cut costs with aggregate belt conveyor systems are designed to transport a diverse range of bulk materials economically. These materials form the foundation of concrete, asphalt, and other essential building products. Efficient transportation of aggregates from one location to another is vital for the success of construction projects. This is where aggregate belt conveyor systems come into play. These systems are designed to move large volumes of aggregate materials swiftly and efficiently, reducing the need for manual labor and minimizing downtime. By integrating aggregate belt conveyor systems into operations, companies can achieve significant improvements in productivity, cost savings, and overall project efficiency.
What Is Aggregate?
Aggregate refers to a broad category of materials used in construction and civil engineering. It generally includes:
- Sand: Fine particles used in concrete, mortar, and asphalt.
- Gravel: Coarse particles that are used as a base material for roads, concrete, and asphalt.
- Crushed Stone: Stones broken into smaller sizes, used in concrete, road bases, and other construction projects.
- Recycled Aggregate: Reprocessed materials from demolished structures, such as crushed concrete or asphalt.
Aggregates are critical in construction because they provide strength, stability, and durability to structures. They are mixed with cement and water to make concrete or asphalt, forming the foundation for roads, buildings, and other infrastructure.
Why Aggregate Belt Conveyor Systems?
Aggregate belt conveyor systems have revolutionized the way aggregate materials are transported, offering numerous advantages over traditional transportation methods. These systems are designed to handle large volumes of materials with ease, providing a reliable and efficient solution for construction and industrial applications. In this section, we will explore the various benefits of using aggregate belt conveyor systems, highlighting their impact on time, cost, and the environment.
Advantages of Aggregate Belt Conveyor Systems Over Traditional Methods
- Efficiency and Speed: Aggregate belt conveyor systems are capable of moving large quantities of materials quickly and efficiently. Unlike traditional methods such as trucks or manual labor, conveyor belts can continuously transport materials over long distances without interruption. This constant flow of materials significantly reduces downtime and increases overall productivity.
- Cost-Effectiveness: Utilizing aggregate belt conveyor systems can lead to substantial cost savings. Traditional methods often involve higher labor costs and fuel expenses. Conveyor systems, on the other hand, require less manual intervention and consume less energy, resulting in lower operational costs. Additionally, they reduce the wear and tear on machinery and vehicles, leading to fewer maintenance expenses.
- Safety: Conveyor systems enhance workplace safety by minimizing the need for manual handling of heavy materials. This reduces the risk of workplace injuries associated with lifting, carrying, and transporting aggregates. Automated systems also eliminate the hazards related to truck traffic and other heavy machinery on site.
- Consistency and Quality Control: Aggregate belt conveyor systems ensure a consistent and controlled flow of materials. This precision helps maintain the quality of the aggregates being transported, as there is less risk of contamination or damage compared to traditional methods. The controlled environment of conveyor systems also allows for better quality control and monitoring.
- Versatility and Adaptability: Conveyor systems can be customized to meet the specific needs of different projects. Whether it’s a stationary setup for a large construction site or a portable system for temporary operations, aggregate belt conveyor systems offer the flexibility to adapt to various requirements. This adaptability makes them suitable for a wide range of applications, from quarries and mining to construction and recycling.
Time, Money, and Environmental Savings
- Time Savings: Aggregate belt conveyor systems significantly reduce the time required to transport materials. Traditional methods like trucks involve loading, transportation, unloading, and potential delays due to traffic or weather conditions. Conveyor systems, however, provide a continuous and uninterrupted flow of materials, drastically cutting down on transportation time and ensuring projects stay on schedule.
- Labor Cost Reduction: With aggregate belt conveyor systems, the need for manual labor is minimized. Automated systems require fewer personnel to operate, leading to a reduction in labor costs. This allows companies to allocate their workforce to other critical tasks, enhancing overall productivity and efficiency.
- Energy Efficiency: Conveyor systems are designed to be energy-efficient, consuming less power compared to trucks and other heavy machinery. This reduced energy consumption translates to lower fuel costs and a smaller carbon footprint, contributing to more sustainable operations.
- Reduced Maintenance Costs: The continuous and smooth operation of aggregate belt conveyor systems results in less wear and tear on machinery. Unlike trucks that require regular maintenance and fuel, conveyor systems have fewer moving parts and are less prone to breakdowns. This leads to significant savings in maintenance and repair costs.
- Environmental Impact: Aggregate belt conveyor systems have a positive environmental impact by reducing the reliance on fossil fuels and lowering greenhouse gas emissions. Trucks and other traditional methods contribute to air pollution and increased carbon emissions. In contrast, conveyor systems operate with minimal emissions, promoting a greener and more sustainable approach to material transportation.
Aggregate belt conveyor systems offer numerous advantages over traditional transportation methods, including increased efficiency, cost savings, enhanced safety, consistent quality, and versatility. By reducing transportation time, labor costs, and environmental impact, these systems provide a reliable and sustainable solution for transporting aggregate materials. As industries continue to seek ways to improve productivity and sustainability, aggregate belt conveyor systems stand out as a vital component in achieving these goals.
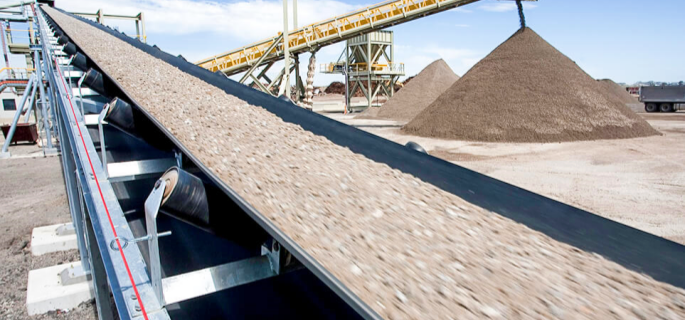
How Do Aggregate Belt Conveyor Work?
Aggregate belt conveyors are used to transport materials like sand, gravel, and crushed stone from one location to another in various construction and mining applications. Here’s how they generally work:
- Material Loading: Aggregates are loaded onto the conveyor system through various means, such as from a hopper, crusher, or loader. The material is placed onto the belt at the loading point.
- Belt Movement: The conveyor belt is powered by a motor-driven pulley system. The belt moves continuously over a series of rollers or idlers, which support and guide the belt along its path.
- Transporting: As the belt moves, it carries the aggregate material from the loading point to the desired destination. The belt’s continuous motion ensures a steady flow of material.
- Discharge: At the end of the conveyor, the aggregate is discharged through a chute or other discharge mechanism. It can be directed into bins, piles, or directly into processing equipment.
- Adjustments and Controls: The conveyor system can be equipped with various controls and sensors to monitor and adjust the speed, direction, and flow of material. This helps ensure efficient operation and prevents overloading or blockages.
- Maintenance: Regular maintenance is required to ensure smooth operation. This includes checking belt tension, replacing worn rollers or belts, and ensuring the system is free from obstructions.
Components of an Aggregate Belt Conveyor System
- Conveyor Belt: The continuous loop that carries the aggregate material.
- Pulleys: Drive and return pulleys that move the belt and control its tension.
- Rollers/Idlers: Support the belt and help reduce friction.
- Hoppers: Feed material onto the conveyor belt.
- Discharge Chutes: Direct the material to its final destination.
- Motors and Gearboxes: Drive the conveyor belt’s movement.
- Control Systems: Manage the operation of the conveyor, including speed and material flow.
Aggregate belt conveyors are favored for their efficiency and ability to handle large volumes of material with minimal labor compared to traditional methods.
Types of Aggregate Belt Conveyor Systems
Aggregate belt conveyor systems come in various types, each designed to cater to specific needs and operational environments. Understanding the different types of conveyor systems can help in selecting the most suitable one for your project. This section explores the key types of aggregate belt conveyor systems, their features, advantages, and applications.
Portable Aggregate Conveyors
Portable aggregate conveyors are designed for flexibility and mobility, making them ideal for temporary or mobile operations. These conveyors are easy to set up and dismantle, allowing them to be moved from one site to another with minimal effort.
- Mobility: Equipped with wheels or tracks, portable conveyors can be easily transported and positioned as needed.
- Quick Setup: These systems are designed for rapid deployment, reducing downtime between project phases.
- Compact Design: Portable conveyors are often compact, making them suitable for sites with limited space.
- Adjustability: Many portable conveyors offer adjustable height and angle settings, allowing for versatile material handling.
- Durability: Built to withstand harsh environments, portable conveyors are made from robust materials that ensure long-lasting performance.
Overland Conveyor Systems for Aggregates
Overland conveyor systems are designed for long-distance transportation of aggregate materials, making them an efficient alternative to traditional hauling methods.
- Cost Efficiency: Overland conveyors reduce the need for multiple transfer points and the associated labor and fuel costs of truck hauling.
- Environmental Benefits: By minimizing the number of trucks on the road, overland conveyors help reduce greenhouse gas emissions and fuel consumption.
- Continuous Operation: These systems provide a continuous flow of materials, improving efficiency and reducing downtime.
- High Capacity: Overland conveyors can transport large volumes of materials over great distances, making them ideal for large-scale projects.
- Reduced Traffic: By reducing truck traffic on site, overland conveyors contribute to a safer and more organized work environment.
Applications of overland conveyor belt systems include mining operations, large construction projects, and any scenario where materials need to be transported over long distances efficiently.
Radial Stacker Conveyors
Radial stacker conveyors are used for bulk material handling, particularly in applications where materials need to be stockpiled efficiently. The functionality, applications, and benefits of radial stacker conveyors include:
- Efficient Stockpiling: Radial stackers can create large stockpiles of materials by rotating around a central pivot point, maximizing storage space.
- Adjustable Discharge Heights: These conveyors can adjust their discharge heights, allowing for precise stacking and minimizing material degradation.
- Versatility: Radial stackers are suitable for various materials, including sand, gravel, and crushed stone.
- Remote Operation: Many radial stackers come with remote control capabilities, enhancing safety and convenience.
- Reduced Material Handling: By creating large, uniform stockpiles, radial stackers reduce the need for additional material handling equipment and labor.
Applications of radial stacker conveyors include aggregate production facilities, mining operations, and any site where efficient stockpiling of bulk materials is required.
Portable Transfer Conveyors
Portable transfer conveyors are designed for mobility and flexibility, making them ideal for applications where materials need to be transferred between different locations quickly. The advantages and use cases of portable transfer conveyors include:
- Flexibility: Portable transfer conveyors can be easily moved to different locations on-site, providing a flexible solution for material transfer needs.
- Ease of Use: These conveyors are simple to operate and require minimal setup time, making them ideal for dynamic work environments.
- Reduced Labor Costs: By automating the transfer of materials, portable conveyors reduce the need for manual labor, leading to cost savings.
- Compact Design: Portable transfer conveyors are typically compact and lightweight, making them easy to transport and maneuver.
- Adaptability: These conveyors can handle a variety of materials, from fine sand to large aggregate pieces, making them versatile for different applications.
Use cases for portable transfer conveyors include short-term projects, construction sites with multiple work areas, and operations that require frequent relocation of equipment.
Aggregate belt conveyor systems offer a range of solutions to meet diverse operational needs. From the mobility of portable aggregate conveyors to the long-distance capabilities of overland systems, the efficient stockpiling of radial stackers, and the flexibility of portable transfer conveyors, each type has distinct advantages that can enhance productivity and efficiency in material handling operations. By understanding these different types, businesses can select the most appropriate conveyor system to optimize their projects and improve overall performance.
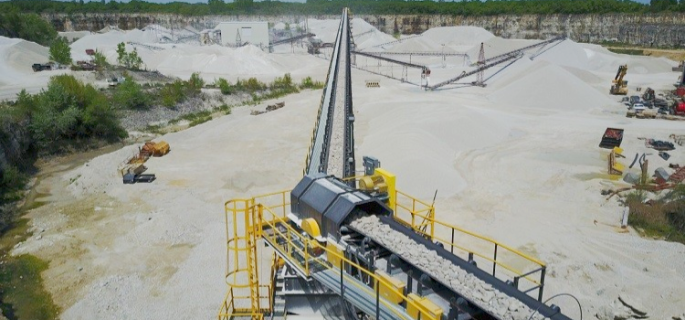
Application of Aggregate Belt Conveyor Systems
Aggregate belt conveyor systems are used in a variety of applications, particularly in construction, mining, and manufacturing industries. Here are some key applications:
Construction Sites
- Concrete Production: Conveyors transport sand, gravel, and crushed stone to mixing plants for concrete production.
- Road Construction: Aggregate conveyors move materials to and from road construction sites, including base layers and surface materials.
Mining Operations
- Material Handling: Conveyors move mined materials such as coal, ore, and aggregate from extraction points to processing facilities or storage areas.
- Stockpiling: Aggregate conveyors help in stockpiling materials efficiently at the mine site or processing plant.
Quarries and Aggregates Production
- Crushing Plants: Conveyors transport raw aggregate to crushers and then move the crushed material to screening or washing units.
- Screening and Sorting: They are used to transport screened and sorted aggregate to different storage bins or directly to customers.
Recycling Facilities
- Recycled Aggregate Processing: Conveyors handle recycled materials, such as crushed concrete or asphalt, and transport them to processing or stockpiling areas.
- Sorting and Separation: They are used to transport and sort recyclable materials into different categories for further processing.
Manufacturing
- Bulk Material Handling: Conveyors move bulk materials used in manufacturing processes, including raw materials and finished products.
- Product Distribution: In manufacturing facilities, conveyors transport products to various stages of production, packaging, and distribution.
Agriculture
- Bulk Grain Handling: Conveyors are used to move bulk grains, such as wheat or corn, from storage bins to processing or packaging areas.
- Seed and Fertilizer Transport: They also handle seeds and fertilizers in agricultural operations.
Ports and Shipping
- Bulk Material Loading/Unloading: Conveyor systems are used to load and unload bulk materials from ships, railcars, or trucks, facilitating efficient transfer to storage or processing facilities.
Waste Management
- Sorting and Transporting Waste: Conveyor systems are used to transport and sort waste materials in recycling centers or waste treatment facilities.
In these applications, aggregate belt conveyor systems provide a reliable, efficient, and cost-effective way to handle and transport materials, minimizing manual labor and improving overall productivity.
Key Considerations When Choosing an Aggregate Belt Conveyor Systems
When selecting an aggregate belt conveyor system, it is essential to consider various factors to ensure the system meets the specific needs of your operation. The right conveyor system can significantly enhance efficiency, reduce costs, and improve overall productivity. This section will discuss the key considerations to keep in mind when choosing an aggregate belt conveyor system, focusing on material characteristics, operational needs, and the importance of customization and design.
Material Characteristics
Understanding the characteristics of the aggregate materials you are working with is crucial when selecting an aggregate belt conveyor system. Different materials have distinct properties that can affect the performance and efficiency of the conveyor system. Key material characteristics to consider include:
- Size and Shape: The size and shape of the aggregate particles can influence the type of belt and the design of the conveyor system. Larger, irregularly shaped particles may require a more robust belt with reinforced edges to prevent spillage and damage.
- Weight and Density: The weight and conveyor belt density of the materials will determine the load capacity of the conveyor system. Heavier materials may necessitate a stronger belt and more powerful drive systems to ensure smooth and efficient transportation.
- Moisture Content: Aggregates with high moisture content can cause slippage and material build-up on the belt, leading to operational inefficiencies. Selecting a conveyor system with appropriate belt materials and cleaning mechanisms can help mitigate these issues.
- Abrasion and Corrosion Resistance: Some aggregates, such as crushed stone and sand, can be highly abrasive, leading to increased wear and tear on the conveyor belt. Choosing belts made from durable materials with high abrasion resistance can extend the lifespan of the system.
- Flowability: The flowability of the aggregate materials can impact the design of the conveyor system, including the angle of incline and the type of feeders used. Materials with poor flowability may require additional equipment to ensure consistent and controlled movement.
Operational Needs
Matching the conveyor system to your specific operational requirements is essential for optimizing performance and efficiency. Consider the following operational needs when selecting an aggregate belt conveyor system:
- Loading and Unloading: Determine how the materials will be loaded onto and unloaded from the conveyor system. This will influence the type of feeders, hoppers, and discharge mechanisms needed to ensure smooth and efficient transfer of materials.
- Storage and Handling: Consider the storage requirements for the aggregate materials and how the conveyor system will integrate with storage facilities. This includes evaluating the space available for stockpiling and the need for additional equipment, such as stackers and reclaimers.
- Direct Transfer: For operations requiring direct transfer of materials between different processes or equipment, it is important to select a conveyor system that can seamlessly integrate with other components of the production line. This may involve custom-designed transfer points and chutes to ensure efficient material flow.
- Environmental Conditions: The operating environment can significantly impact the performance and durability of the conveyor system. Consider factors such as temperature, humidity, and exposure to corrosive substances when selecting materials and components for the system.
- Operational Efficiency: Evaluate the overall efficiency of the conveyor system, including energy consumption, maintenance requirements, and ease of operation. An efficient system can reduce operational costs and improve productivity.
Customization and Design
The significance of customization and design cannot be overstated when choosing an aggregate belt conveyor system. Each operation has unique requirements, and a one-size-fits-all approach is rarely effective. Custom-designed systems can address specific project demands and optimize performance. Key aspects of customization and design include:
- Tailored Solutions: Custom-designed conveyor systems can be tailored to meet the exact specifications of your operation, ensuring optimal performance and efficiency. This includes designing the system to accommodate specific material characteristics, operational needs, and site conditions.
- Flexibility and Scalability: A custom-designed system can offer greater flexibility and scalability, allowing you to adapt to changing operational requirements and expand the system as needed. This is particularly important for growing businesses and evolving projects.
- Integration with Existing Equipment: Customization ensures seamless integration with existing equipment and infrastructure, reducing the need for extensive modifications and minimizing disruptions to operations.
- Advanced Technology: Custom-designed systems can incorporate advanced technologies, such as automated controls, monitoring systems, and energy-efficient components, to enhance performance and reduce operational costs.
- Support and Maintenance: Working with a supplier that offers custom design services also provides access to ongoing support and maintenance, ensuring the system continues to operate at peak efficiency.
Choosing the right aggregate belt conveyor system requires careful consideration of material characteristics, operational needs, and the importance of customization and design. By understanding these factors and selecting a system tailored to your specific requirements, you can enhance efficiency, reduce costs, and improve overall productivity in your material handling operations. Aggregate belt conveyor systems are a critical component in many industries, and making an informed decision can significantly impact the success of your projects.
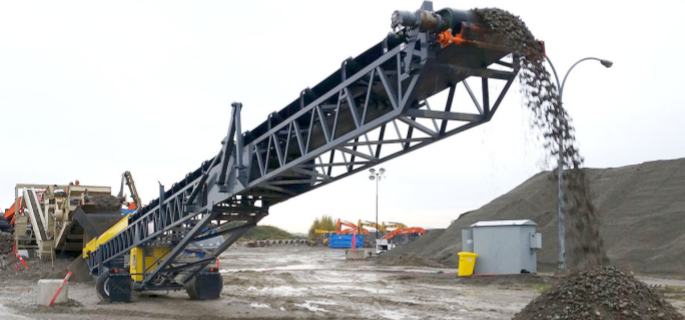
Manufacturers and Suppliers of Aggregate Belt Conveyor Systems
Choosing the right manufacturer and supplier for aggregate conveyor belt is crucial to ensure the efficiency and longevity of your material handling operations. This section provides an overview of notable manufacturers and highlights the key factors to consider when selecting a supplier, including after-sales support, custom design capabilities, and parts availability.
Overview of Notable Manufacturers
Several manufacturers are renowned for their high-quality aggregate belt conveyor systems. These companies have established themselves as leaders in the industry through their innovative designs, reliable performance, and excellent customer service. Here are some notable manufacturers:
- Metso Outotec: Known for its robust and efficient conveyor systems, Metso Outotec offers a wide range of solutions for various aggregate handling needs. Their systems are designed for durability and efficiency, ensuring smooth operations even in the most demanding environments.
- Superior Industries: Superior Industries is a leading manufacturer of aggregate belt conveyor systems, offering a comprehensive range of products, including portable and stationary conveyors, radial stackers, and overland conveyors. Their systems are engineered for maximum efficiency and flexibility.
- Terex Corporation: Terex provides high-quality conveyor systems that are designed to meet the diverse needs of the aggregate industry. Their products are known for their reliability, ease of use, and advanced technology, which helps enhance operational efficiency.
- Masaba Inc.: Specializing in heavy-duty conveyor systems, Masaba Inc. offers a variety of customizable solutions tailored to specific project requirements. Their conveyor systems are built to withstand tough conditions and deliver consistent performance.
- McLanahan Corporation: McLanahan is recognized for its innovative conveyor designs and commitment to quality. Their conveyor belt for aggregate is designed to provide reliable material handling solutions, ensuring efficient and cost-effective operations.
Key Factors in Choosing a Supplier
When selecting a supplier for aggregate belt conveyor systems, it is essential to consider several key factors to ensure you receive the best possible product and support. Here are the critical factors to keep in mind:
After-Sales Support
After-sales support is crucial for maintaining the efficiency and longevity of your conveyor systems. A reliable supplier should offer comprehensive after-sales services, including:
- Technical Support: Access to knowledgeable technicians who can provide assistance with troubleshooting, repairs, and maintenance.
- Training Programs: Supplier-provided training programs to ensure your team is well-versed in operating and maintaining the conveyor systems.
- Warranty and Service Contracts: Suppliers that offer robust warranty and service contracts can provide peace of mind and protect your investment.
Custom Design Capabilities
Custom design capabilities are essential to ensure the conveyor system meets the specific needs of your operation. A supplier with strong customization capabilities can offer:
- Tailored Solutions: Systems designed to match your unique operational requirements, including material characteristics, space constraints, and workflow.
- Engineering Expertise: Access to experienced engineers who can design and implement custom solutions that optimize performance and efficiency.
- Scalability: The ability to scale the system as your operational needs grow or change.
Parts Availability
Availability of replacement parts is critical for minimizing downtime and ensuring the continuous operation of your conveyor systems. A reputable supplier should provide:
- Comprehensive Parts Inventory: A well-stocked inventory of essential parts to reduce lead times and prevent prolonged downtime.
- Quick Delivery: Efficient logistics and distribution networks to ensure rapid delivery of parts when needed.
- Quality Assurance: High-quality replacement parts that meet or exceed the original specifications to maintain system performance and reliability.
Selecting the right manufacturer and supplier for aggregate belt conveyor systems is vital for the success of your material handling operations. By considering factors such as after-sales support, custom design capabilities, and parts availability, you can ensure that your conveyor systems are reliable, efficient, and well-supported. Notable manufacturers like Metso Outotec, Superior Industries, Terex Corporation, Masaba Inc., and McLanahan Corporation offer high-quality products and services that can meet the diverse needs of the aggregate industry. Making an informed choice will help you optimize your operations, reduce costs, and improve overall productivity.
Replacement Parts and Maintenance of Aggregate Belt Conveyor Systems
Proper maintenance and timely replacement of parts are crucial for ensuring the efficiency and longevity of aggregate belt conveyor systems. This section will cover essential replacement parts and provide maintenance tips to keep your conveyor systems running smoothly and efficiently.
Essential Replacement Parts for Aggregate Belt Conveyor Systems
- Belts: The belt is the core component of any conveyor system. Over time, belts can wear out due to abrasion, tension, and exposure to harsh materials. Regular inspection and replacement of worn belts are essential to prevent system downtime and ensure efficient material transport. Look for signs of fraying, cracks, or significant wear and replace the belt when necessary.
- Rollers: Rollers support the belt and help in the smooth movement of materials. They are subject to wear and tear and can become misaligned or damaged over time. Regularly inspect rollers for signs of wear, noise, or misalignment. Replace any damaged or worn-out rollers to maintain efficient operation and prevent damage to the belt.
- Bearings: Bearings play a vital role in the smooth functioning of rollers and other moving parts. They can wear out due to friction and lack of lubrication. Regularly check bearings for signs of wear, noise, or overheating. Lubricate them as needed and replace any that are worn or damaged to ensure smooth and efficient operation.
- Pulleys: Pulleys are critical for maintaining belt tension and guiding the belt through the system. Worn or damaged pulleys can cause belt misalignment and reduce system efficiency. Regularly inspect pulleys for wear, alignment, and proper tension. Replace pulleys that show significant wear or damage to maintain system performance.
- Drive Units: The drive unit powers the conveyor system and includes components such as motors, gearboxes, and couplings. Regular inspection and maintenance of the drive unit are essential to prevent breakdowns. Check for signs of wear, noise, and overheating. Ensure that all components are properly lubricated and replace any that are showing signs of failure.
Maintenance Tips to Ensure Longevity and Continuous Operation Efficiency
- Regular Inspections: Conduct regular inspections of all components of the aggregate belt conveyor systems. Look for signs of wear, damage, or misalignment. Address any issues promptly to prevent further damage and maintain system efficiency. Develop a checklist to ensure all parts are inspected regularly.
- Proper Lubrication: Lubrication is essential for reducing friction and wear on moving parts. Ensure that all bearings, rollers, and drive components are properly lubricated according to the manufacturer’s recommendations. Regular lubrication can extend the life of these components and prevent unexpected breakdowns.
- Tension and Alignment: Proper belt tension and alignment are crucial for efficient operation. Regularly check the tension and alignment of the belt to ensure it runs smoothly and does not drift off track. Adjust the tension and alignment as needed to prevent premature wear and damage to the belt and other components.
- Cleanliness: Keeping the conveyor system clean is important for preventing material build-up and reducing wear on components. Regularly clean the belt, rollers, and other parts to remove any debris or build-up. This can prevent blockages, reduce wear, and improve overall system efficiency.
- Training and Documentation: Ensure that all personnel involved in the operation and maintenance of the conveyor system are properly trained. Provide them with detailed documentation and guidelines for maintenance procedures. Regular training and clear documentation can help prevent mistakes and ensure that maintenance tasks are performed correctly.
Maintaining aggregate belt conveyor systems involves regular inspection and timely replacement of essential parts such as belts, rollers, bearings, pulleys, and drive units. By following these maintenance tips—conducting regular inspections, ensuring proper lubrication, maintaining correct tension and alignment, keeping the system clean, and providing proper training and documentation—you can ensure the longevity and continuous operation efficiency of your conveyor systems. Proper maintenance not only extends the life of the equipment but also enhances productivity, reduces downtime, and lowers operational costs. Implementing a robust maintenance program is key to maximizing the benefits of your aggregate belt conveyor systems and ensuring their reliable performance in the long term.
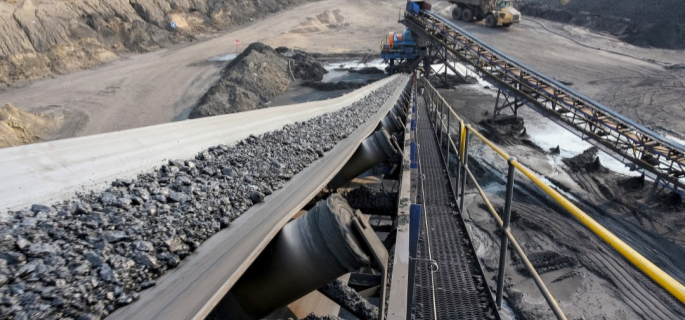
FAQs About Aggregate Belt Conveyor Systems
An aggregate conveyor is a type of material handling equipment used to transport bulk aggregates such as sand, gravel, crushed stone, and other building materials. These conveyors are essential in various industries, including construction, mining, and material production, where large volumes of aggregates need to be moved efficiently and quickly. Aggregate conveyors typically consist of a belt, pulley system, and motor, and are designed to handle heavy loads and operate continuously over long periods. They help streamline processes, reduce manual labor, and improve productivity by providing a consistent and reliable means of transporting materials from one location to another.
Conveyor systems are generally categorized into two main types: mechanical conveyors and pneumatic conveyors.
Mechanical Conveyors: These use physical means to move materials, such as belts, rollers, chains, or screws. Common types of mechanical conveyors include belt conveyors, roller conveyors, and chain conveyors. They are ideal for handling solid materials and are widely used in various industries for their reliability and efficiency.
Pneumatic Conveyors: These systems use air pressure to transport materials through pipelines. They are particularly useful for moving fine, granular, or powdery materials that might be difficult to handle with mechanical systems. Pneumatic conveyors are often used in industries like pharmaceuticals, food processing, and chemical manufacturing for their ability to handle delicate or hazardous materials in a controlled environment.
Belt conveyors come in various types to suit different applications and material handling needs. Some common types include:
Flat Belt Conveyors: These are the most widely used type, featuring a flat belt that moves materials in a straight line. They are versatile and suitable for transporting items of various shapes and sizes.
Incline/Decline Belt Conveyors: These conveyors are designed to move materials up or down an incline. They are commonly used in industries where materials need to be transported between different elevations, such as in packaging and assembly lines.
Modular Belt Conveyors: These use a series of interlocking plastic or metal modules that create a continuous belt. They are highly durable and can handle heavy loads and harsh conditions, making them ideal for food processing and manufacturing.
Cleated Belt Conveyors: These conveyors have raised sections, or cleats, on the belt to prevent materials from sliding back, especially on inclines. They are used for transporting loose or bulk materials like grains, sand, and chemicals.
Curved Belt Conveyors: These are designed to navigate turns and curves, allowing for more flexible and efficient use of space in facilities. They are used in various industries, including warehousing and distribution.
The principle of belt conveyor systems is based on the continuous movement of a belt that transports materials from one point to another. The main components of a belt conveyor system include the belt, pulleys, rollers, and a motor. Here’s how it works:
Belt: The belt is the continuous loop of material that moves the products. It is usually made of durable materials like rubber, fabric, or metal.
Pulleys: There are typically two pulleys at either end of the system. The drive pulley, powered by a motor, pulls the belt, while the idler pulley helps maintain tension and direction.
Rollers: Positioned along the length of the conveyor, rollers support the belt and ensure smooth movement. They reduce friction and wear on the belt.
Motor: The motor powers the drive pulley, causing the belt to move. The motor’s speed and power determine the conveyor’s capacity and efficiency.
The belt conveyor system operates by continuously pulling the belt over the pulleys, moving materials placed on the belt from the loading point to the discharge point. This principle allows for efficient and consistent material transport, reducing manual labor and increasing productivity in various industrial applications.
Last Updated on July 23, 2024 by Jordan Smith
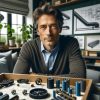
Jordan Smith, a seasoned professional with over 20 years of experience in the conveyor system industry. Jordan’s expertise lies in providing comprehensive solutions for conveyor rollers, belts, and accessories, catering to a wide range of industrial needs. From initial design and configuration to installation and meticulous troubleshooting, Jordan is adept at handling all aspects of conveyor system management. Whether you’re looking to upgrade your production line with efficient conveyor belts, require custom conveyor rollers for specific operations, or need expert advice on selecting the right conveyor accessories for your facility, Jordan is your reliable consultant. For any inquiries or assistance with conveyor system optimization, Jordan is available to share his wealth of knowledge and experience. Feel free to reach out at any time for professional guidance on all matters related to conveyor rollers, belts, and accessories.