Design Process of Aluminium Guide Roller
In the realm of industrial applications, guide rollers play a pivotal role in ensuring the smooth and efficient movement of materials along a designated path. These components are critical in a variety of settings, from manufacturing lines to conveyor systems, where precise guidance and support of materials are necessary for operational success. Among the materials chosen for these rollers, aluminium stands out as a preferred option. The choice of aluminium guide roller is driven by their exceptional combination of strength, lightness, and resistance to corrosion, making them an ideal choice for a wide range of industrial applications. Their lightweight nature not only facilitates easier installation and handling but also reduces the overall load on the machinery, enhancing longevity and reducing maintenance needs.
What Is Aluminium Guide Roller
Aluminium guide roller offer smooth operation, lightweight design, and high performance, ideal for efficient industrial applications. Aluminium guide rollers are integral components in various industrial machinery and conveyor systems, designed to guide, support, and manage the movement of materials through a process. These rollers are crafted from aluminium, a material known for its lightweight, strength, and corrosion resistance. Here are seven key points that define the purpose and advantages of aluminium guide rollers:
- Lightweight: Aluminium guide rollers are significantly lighter than their counterparts made from materials like steel. This reduces the overall weight of the machinery, leading to lower energy consumption and easier handling during installation and maintenance.
- Corrosion Resistance: Aluminium naturally forms a protective oxide coating, making these rollers resistant to corrosion. This is particularly beneficial in environments where moisture or chemicals are present.
- Strength-to-Weight Ratio: Despite their lightness, aluminium guide rollers boast a high strength-to-weight ratio, ensuring durability and the ability to handle substantial loads without deformation.
- Thermal Conductivity: Aluminium’s excellent thermal conductivity helps in dissipating heat generated by the friction between the roller and the material, thus reducing thermal expansion and maintaining roller integrity.
- Recyclability: Aluminium guide rollers are environmentally friendly, as aluminium can be recycled multiple times without losing its properties, reducing the carbon footprint of manufacturing processes.
- Cost-Effectiveness: While the initial cost might be higher than some materials, the durability, low maintenance, and energy efficiency of aluminium guide rollers offer long-term savings.
- Customizability: The versatility of aluminium allows for a wide range of surface treatments and modifications, such as anodizing or coating, to meet specific application requirements, including improved grip or wear resistance.
Comparison with Other Materials
To highlight the advantages of aluminium guide rollers, a comparison with rollers made from other materials is presented in the table below:
This comparison underscores the unique advantages of aluminium guide rollers, making them a superior choice for a wide range of industrial applications where performance, durability, and efficiency are paramount. The lightweight nature of an aluminium guide roller, combined with its corrosion resistance and strength, positions it as an ideal solution for enhancing the operational efficiency of machinery while minimizing maintenance and energy costs.
Key Features of Aluminium Guide Roller
Aluminium guide rollers are essential components in the seamless operation of various industrial systems, offering a blend of functionality and efficiency. Here are nine key features that highlight the unique attributes and advantages of aluminium guide rollers:
- Lightweight Yet Durable: The core advantage of an aluminium guide roller lies in its exceptional lightweight nature combined with remarkable durability. Aluminium’s inherent strength allows these rollers to withstand significant operational stresses without succumbing to wear or deformation, ensuring long-term reliability in demanding industrial environments.
- High Corrosion Resistance: Aluminium naturally forms a protective oxide layer when exposed to the atmosphere, providing an inherent resistance to corrosion. This feature makes aluminium guide rollers particularly suitable for use in environments where moisture or corrosive substances are present, extending their lifespan and reducing maintenance requirements.
- Customization Options: The versatility of aluminium allows for extensive customization of guide rollers to meet specific industrial needs. Whether it’s the diameter, length, surface finish, or the inclusion of features like grooves or coatings, aluminium guide rollers can be tailored to the precise specifications of any application, enhancing performance and compatibility.
- Environmental Benefits: Aluminium is a highly sustainable material, with the ability to be recycled repeatedly without loss of quality. The use of aluminium guide rollers contributes to a lower environmental impact, as recycling aluminium consumes only a fraction of the energy required to produce primary aluminium, thereby reducing the carbon footprint of manufacturing processes.
- Superior Thermal Conductivity: Aluminium’s excellent thermal conductivity helps in efficiently dissipating heat generated during operation. This property minimizes thermal expansion and contraction of the rollers, maintaining dimensional stability and performance under varying temperatures.
- Cost-Effectiveness Over Time: While the initial investment in aluminium guide rollers may be higher compared to some alternatives, their durability, low maintenance requirements, and energy efficiency translate into significant cost savings over the lifespan of the equipment.
- Ease of Installation and Maintenance: The lightweight nature of aluminium guide rollers simplifies installation and maintenance procedures. Their reduced weight lowers the risk of injury during handling and allows for quicker and more cost-effective maintenance and replacement processes.
- Smooth Operation: Aluminium guide rollers ensure a smooth and consistent operation, contributing to the quality of the end product. Their balanced and precise construction reduces vibration and noise, enhancing the overall efficiency of the machinery.
- Aesthetic Appeal: Beyond their functional benefits, aluminium guide rollers offer a sleek and professional appearance. The material’s natural luster and the ability to accept various finishes can contribute to the aesthetic appeal of the machinery, reflecting positively on the manufacturing environment.
The key features of aluminium guide rollers, from their lightweight and durable nature to their customization options and environmental benefits, make them an indispensable component in modern industrial applications. Their ability to meet the rigorous demands of various settings while offering sustainability and efficiency underscores the value they bring to operations seeking to optimize performance and reduce operational costs.

Aluminium Guide Roller Specification
To create a detailed specification for an Aluminium Guide Roller, here are the key aspects typically covered:
Material:
- Body Material: High-grade aluminum alloy (e.g., 6061-T6, 6082-T6)
- Coating/Surface Treatment: Anodized or powder-coated for corrosion resistance
Dimensions:
- Outer Diameter: Customizable, typically ranging from 50mm to 300mm
- Inner Diameter (Bore Size): According to the shaft size, typically 10mm to 50mm
- Length (Face Width): Customizable, typically from 100mm to 1000mm
Weight:
- Varies depending on size and application, but aluminum offers a lightweight solution compared to steel
Load Capacity:
- Dependent on size and material, usually capable of handling light to medium loads
- Specific load ratings should be provided based on the application (e.g., 100kg, 200kg)
Surface Finish:
- Roughness: Typically 0.8 µm to 1.6 µm Ra, depending on application requirements
- Type: Smooth or knurled, depending on whether additional traction is required
Bearings:
- Type: Precision ball bearings conveyor roller or needle roller bearings, depending on application
- Sealing: Sealed or shielded bearings for dust and moisture protection
Shaft Compatibility:
- Shaft Material: Steel or stainless steel, with a surface finish compatible with the roller’s bore
- Mounting: Set screws, keyways, or tapered bores, depending on the specific design
Operating Temperature:
- Suitable for temperatures ranging from -20°C to +80°C, depending on bearing selection and lubrication
This specification can be further tailored to fit specific needs or industry applications. Let me know if you need more detailed information on any specific aspect.
Need durable conveyor rollers? Contact us today!
Surface Structure of Aluminium Guide Roller
The surface structure of an Aluminium Guide Roller is crucial for its performance in various industrial applications. Here’s a detailed breakdown of the different types of surface structures that can be applied to Aluminium Guide Rollers:
Smooth Surface:
- Description: A polished or finely machined surface with minimal roughness.
- Applications: Ideal for applications where low friction is required, such as in high-speed conveyors or where the material being conveyed is delicate and needs to avoid damage.
- Surface Roughness (Ra): Typically ranges from 0.4 µm to 0.8 µm.
Knurled Surface:
- Description: A textured surface created by a knurling tool, which forms a pattern of ridges (crosshatch, straight, or diamond pattern).
- Applications: Used in situations where increased traction is needed between the roller and the material it contacts, such as in drive rollers or where slippage must be minimized.
- Knurling Patterns:
- Straight Knurl: Parallel ridges along the roller’s axis.
- Diamond Knurl: Crisscross pattern providing multi-directional grip.
- Cross-Hatch Knurl: Combination of straight and diagonal patterns.
Grooved Surface:
- Description: Machined grooves along the roller’s surface, which can be straight, helical, or in a custom pattern.
- Applications: Common in applications where alignment of the material is critical, such as guiding or steering web materials in processing lines.
- Groove Specifications:
- Depth and Width: Customizable depending on material handling needs.
- Spacing: Uniform or variable, depending on specific alignment requirements.
Coated Surface:
- Description: The roller surface is coated with a material to provide additional properties such as increased wear resistance, reduced friction, or enhanced corrosion protection.
- Types of Coatings:
- Anodized Coating: Provides a hard, wear-resistant surface with good corrosion resistance.
- Teflon (PTFE) Coating: Used for applications requiring low friction and high chemical resistance.
- Rubber or Urethane Coating: Provides a softer surface with high grip, useful in applications where the roller needs to engage materials without damaging them.
Patterned Surface:
- Description: Custom patterns machined or etched onto the surface to meet specific application needs.
- Applications: Often used in specialized material handling applications where the surface pattern is designed to interact uniquely with the material being processed (e.g., embossing or forming).
Matte or Textured Surface:
- Description: A surface that has been bead-blasted, chemically etched, or otherwise treated to create a matte finish.
- Applications: Used to reduce glare or to increase the surface area for better adhesive bonding or coating applications.
Micro-Structured Surface:
- Description: Precision-engineered microstructures on the surface, which can influence material flow, friction characteristics, or fluid dynamics in specific high-tech applications.
- Applications: Advanced industrial processes where precise control over material interaction is required.
Selecting the Appropriate Surface Structure
The choice of surface structure for an Aluminium Guide Roller depends on the specific application requirements, such as the type of material being handled, the need for grip or smoothness, environmental conditions, and the mechanical stresses the roller will face.
If you have a particular application in mind, I can provide more targeted advice on the best surface structure to use.
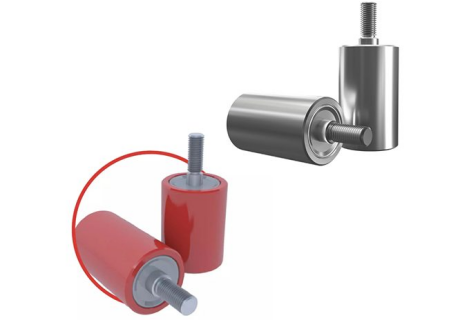
Design of Aluminium Guide Roller
Designing an Aluminium Guide Roller involves considering several factors such as material properties, load capacity, surface structure, and the specific application requirements. Below is a detailed outline of the key design aspects:
Material Selection:
- Aluminium Alloy: The most common alloys used for guide rollers are 6061-T6 or 6082-T6, which offer a good balance of strength, lightweight, and corrosion resistance.
- Coatings: Depending on the environment, additional surface treatments like anodizing or powder coating can be applied to enhance durability and wear resistance.
Core Design:
- Roller Body:
- Outer Diameter (OD): Typically designed based on the load and the material being handled, ranging from 50mm to 300mm.
- Inner Diameter (ID): Bore size is determined by the shaft size, usually ranging from 10mm to 50mm.
- Wall Thickness: Depends on the load capacity and the application’s mechanical requirements; generally, a thicker wall provides higher strength.
- Core Structure:
- Solid Core: For heavy-duty applications requiring high strength.
- Hollow Core: For lighter applications where weight reduction is crucial.
Surface Design:
- Surface Finish:
- Smooth: For applications where low friction is needed.
- Knurled: For increased grip and traction, useful in driving or guiding materials that might slip.
- Grooved: For alignment of belts, ropes, or cables, with grooves that can be straight, spiral, or custom-designed.
- Coated: With rubber or urethane for a softer surface and better grip, or anodized for corrosion resistance.
- Surface Structure:
- Crowned Surface: To aid in self-centering of the material on the roller.
- Textured Surface: For special applications where specific material interaction is required, such as embossing.
Bearing Selection:
- Bearing Type:
- Ball Bearings: Commonly used for low-friction and high-speed applications.
- Needle Bearings: Used for higher load capacities.
- Plain Bearings: Suitable for slower speed, heavy-duty applications.
- Bearing Housing:
- Sealed or Shielded: To protect against dust, moisture, and contaminants.
- Precision Machined: For maintaining alignment and reducing wear over time.
Load Capacity:
- Design Considerations:
- Load Rating: Must be calculated based on the roller’s intended use, factoring in dynamic and static loads.
- Deflection and Stress Analysis: Ensure the roller’s design can withstand the applied loads without excessive deflection or stress, particularly in high-speed or heavy-duty applications.
Mounting and Assembly:
- Shaft Fit:
- Interference Fit: For a secure, non-slip connection between the roller and shaft.
- Keyways or Set Screws: To prevent rotation of the roller relative to the shaft.
- End Caps:
- Material: Often made of plastic or aluminium, designed to protect bearings and the roller’s interior.
- Design: Must allow easy maintenance and replacement of bearings.
Dynamic Balance:
- Balancing: Important for high-speed applications to prevent vibrations that could lead to premature wear or failure. The roller should be dynamically balanced to minimize rotational imbalances.
Environmental Considerations:
- Corrosion Resistance: For outdoor or marine applications, selecting corrosion-resistant materials and coatings is crucial.
- Temperature Resistance: Consideration for the operating temperature range, ensuring materials and bearings are suitable for extreme temperatures if necessary.
Customization:
- Design Modifications: Depending on the specific needs of the application, such as adding flanges for guiding, using perforated designs for weight reduction, or integrating specific surface patterns.
- Modular Design: For easy assembly, disassembly, and maintenance.
Design Process
Conceptual Design:
- Define the application requirements, including load capacity, environmental conditions, and material handling needs.
- Create initial sketches or CAD models to visualize the roller design.
Detailed Design:
- Perform engineering calculations to ensure the roller meets strength, stiffness, and durability requirements.
- Finalize material selection, bearing type, and surface finish based on the application.
Prototyping and Testing:
- Develop a prototype to test the roller’s performance under actual operating conditions.
- Make adjustments based on testing results to optimize the design.
Production:
- Use precision machining techniques to manufacture the rollers, ensuring tight tolerances and high-quality surface finishes.
- Implement quality control processes to ensure each roller meets design specifications.
Installation and Maintenance:
- Provide clear guidelines for installation to ensure proper alignment and functioning.
- Design for easy maintenance, allowing for quick roller bearing replacement or surface re-coating if necessary.
This comprehensive approach ensures that the Aluminium Guide Roller is designed to meet specific application requirements while maintaining durability, efficiency, and reliability.
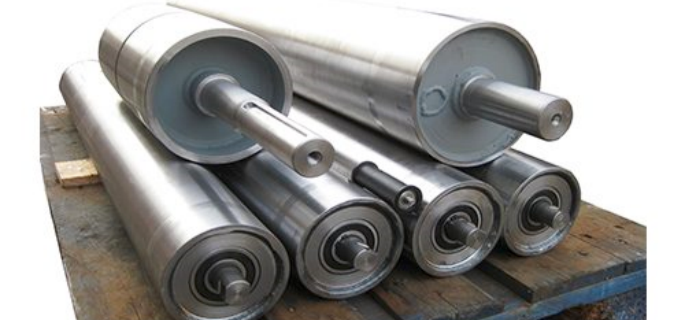
Aluminium Rolling Process
The aluminium rolling process is a critical manufacturing step for producing aluminium guide rollers, a component essential for numerous industrial applications. This process involves transforming aluminium into a specific shape and thickness through mechanical deformation, achieved by passing the metal between rolls. The process is divided into two main types: hot rolling and cold rolling, each affecting the aluminium’s properties in ways that are beneficial for the production of aluminium guide rollers.
Introduction to the Aluminium Sheet Rolling Process
The aluminium sheet rolling process is a cornerstone in the manufacturing of aluminium guide rollers, serving as the bridge between raw aluminium ingots and the precision-engineered rollers used in various industrial applications. This process transforms aluminium from its initial, bulky form into sheets or specific shapes that are the precursors to the final guide rollers. The transformation is achieved through a combination of heat and mechanical pressure, meticulously controlled to yield aluminium of the desired thickness, strength, and surface characteristics. This foundational process not only dictates the physical properties of the aluminium but also its performance in the demanding environments where guide rollers operate.
Detailed Explanation of the Aluminium Rolling Process
The aluminium rolling process is a nuanced and multifaceted procedure that significantly influences the final characteristics of aluminium guide rollers. Here’s a deeper dive into the steps involved and the technicalities that define this manufacturing art:
- Preparation and Heating: The process begins with the preparation of aluminium billets, which are preheated to a specific temperature range. This heating is crucial for hot rolling, as it softens the aluminium, making it pliable and ready for deformation.
- Hot Rolling: The heated aluminium is first subjected to hot rolling, where it passes through a series of rollers at high temperatures. This stage is primarily about reducing the thickness of the aluminium billets to a preliminary gauge and creating a uniform structure.
- Cooling and Cleaning: After hot rolling, the aluminium is cooled, either naturally or through quenching, to bring it down to a manageable temperature for further processing. It’s also cleaned to remove any surface impurities that may affect the quality of the cold rolling process.
- Cold Rolling: This is where the precision work happens. Cold rolling refines the thickness of the aluminium to the exact specifications needed for the guide rollers. It’s performed at or near room temperature, enhancing the metal’s strength and surface finish.
- Intermediate Annealing: Depending on the desired end properties, the aluminium may undergo annealing between cold rolling passes. This heat treatment relieves internal stresses and restores ductility, allowing for further thickness reduction without cracking.
- Final Thickness and Surface Finishing: The aluminium reaches its final thickness through successive cold rolling passes. Surface finishing processes, such as brushing, polishing, or coating, are applied to achieve the desired surface quality.
- Cutting and Shaping: The final step involves cutting and shaping the rolled aluminium into guide rollers. Precision machinery ensures that the rollers meet the exact dimensions required for their specific industrial applications.
How the Rolling Process Affects the Properties of Aluminium Guide Rollers
The aluminium rolling process is not just about altering the dimensions of aluminium; it’s a transformative procedure that significantly enhances the material properties essential for the performance of aluminium guide rollers:
- Enhanced Mechanical Properties: Through work hardening during cold rolling, the aluminium’s yield strength and tensile strength are significantly increased, making the guide rollers more robust and resistant to deformation under load.
- Improved Surface Quality: The rolling process can achieve a superior surface finish, crucial for applications where the roller interacts with other materials. A smooth surface reduces friction and wear, extending the life of both the roller and the materials it contacts.
- Precise Dimensional Tolerances: The controlled environment of the rolling process allows for the achievement of precise dimensional tolerances. This precision is critical for guide rollers, where even minor deviations can lead to significant issues in material handling and processing.
- Optimized Grain Structure: The deformation and recrystallization that occur during rolling optimize the aluminium’s grain structure, enhancing its mechanical properties and making the guide rollers more durable and reliable.
- Customizable Hardness Levels: By adjusting the cold rolling parameters and subsequent heat treatments, manufacturers can tailor the hardness of the aluminium to suit different applications, balancing ductility and strength as needed.
- Corrosion Resistance: The surface treatments applied after rolling can further enhance the aluminium’s natural corrosion resistance, ensuring that the guide rollers can withstand harsh environments without deteriorating.
- Thermal Conductivity Maintenance: Despite the intensive mechanical processing, aluminium retains its high thermal conductivity, a property beneficial for dissipating the heat generated during roller operation.
- Aesthetic Improvements: Beyond functional benefits, the rolling process can also impart an aesthetically pleasing finish to the aluminium guide roller, contributing to the visual appeal of the machinery they are part of.
- Environmental Impact: The efficiency of the rolling process and the recyclability of aluminium contribute to the environmental sustainability of manufacturing aluminium guide roller, aligning with global efforts towards greener manufacturing practices.
Understanding these aspects of the aluminium rolling process illuminates how it is not merely a step in manufacturing but a critical determinant of the performance, durability, and application suitability of aluminium guide roller.
Types of Aluminium Guide Roller
Aluminium guide rollers are crucial for numerous industrial applications, offering precision and reliability. These rollers come in various types, each designed to meet specific operational needs. Understanding the differences between Dead Shaft and Live Shaft aluminium guide roller, as well as the impact of specialized finishes and treatments, is essential for selecting the right roller for your application.
Classification of Aluminium Guide Rollers
- Plain Aluminium Guide Roller:
- Description: A simple cylindrical roller with a smooth surface, designed for general guiding applications.
- Applications: Commonly used in conveyor systems, packaging machines, and other material handling equipment where a smooth guiding surface is sufficient.
- Knurled Aluminium Guide Roller:
- Description: Features a textured surface created by knurling, which can be straight, diagonal, or diamond-shaped.
- Applications: Used where additional grip is needed to prevent slippage of materials, often in drive rollers or tensioning systems.
- Grooved Aluminium Guide Roller:
- Description: Machined with grooves along the roller’s surface, which can be straight, spiral, or custom-designed.
- Applications: Ideal for guiding and aligning belts, cables, or other materials that need precise positioning as they move through a system.
- Crowned Aluminium Guide Roller:
- Description: The roller has a slightly convex shape (crowned) along its length, with a larger diameter in the center than at the ends.
- Applications: Helps in keeping belts or other materials centered on the roller, reducing the chances of misalignment in conveyor systems or processing lines.
- Tapered Aluminium Guide Roller:
- Description: The diameter of the roller gradually decreases from one end to the other.
- Applications: Commonly used in conveyor systems where materials need to be guided or centered, especially in curved sections of a conveyor.
- Rubber-Coated Aluminium Guide Roller:
- Description: Aluminium roller with a rubber or urethane coating applied to the surface.
- Applications: Provides additional grip and cushioning, suitable for handling delicate materials or where additional traction is needed, such as in paper processing or textile industries.
- Perforated Aluminium Guide Roller:
- Description: Contains holes or perforations across the surface of the roller.
- Applications: Used in applications where ventilation is required, such as in drying processes, or where the roller needs to be lightweight.
- Anodized Aluminium Guide Roller:
- Description: Aluminium roller treated with an anodizing process to increase surface hardness and corrosion resistance.
- Applications: Suitable for use in harsh environments where corrosion resistance and durability are important, such as in outdoor or marine applications.
- Web Handling Aluminium Guide Roller:
- Description: Specialized rollers designed for web handling, often featuring specific surface treatments or designs that prevent marking or wrinkling of delicate web materials.
- Applications: Used in industries like printing, textile manufacturing, or plastic film production, where the smooth handling of continuous web materials is critical.
- Flanged Aluminium Guide Roller:
- Description: Has one or more flanges on either side of the roller to keep materials on track.
- Applications: Ideal for guiding narrow belts, ropes, or cables and preventing them from slipping off the roller during operation.
- Precision Aluminium Guide Roller:
- Description: Manufactured with high precision and tight tolerances, often featuring high-quality bearings for smooth operation.
- Applications: Used in applications requiring high accuracy and low friction, such as in high-speed processing lines or sensitive material handling systems.
- Idle Aluminium Guide Roller:
- Description: A passive roller that is not driven but guides or supports materials as they move through a system.
- Applications: Commonly used as support or transition points in conveyor systems part, packaging lines, or processing machines.
Dead Shaft vs. Live Shaft Aluminium Rollers Comparison
Here’s a comparison chart to illustrate the key differences between Dead Shaft and Live Shaft Aluminium Rollers:
Specialized Finishes and Treatments for Enhanced Performance
Expanding on the specialized finishes and treatments for aluminium guide rollers, here are additional options that enhance their performance in specific applications:
- Teflon® Coating: This non-stick coating reduces friction and prevents materials from adhering to the roller surface. It’s ideal for use in environments where sticky or adhesive materials are processed.
- Laser Engraving: Laser engraving can be used to create precise, micro-fine patterns on the surface of aluminium guide rollers. This technique is useful for applications requiring enhanced material grip without the use of adhesives.
- Ceramic Coating: Offering extreme hardness and thermal resistance, ceramic coatings protect rollers from wear, corrosion, and high temperatures. This finish is particularly beneficial in the printing industry, where rollers are exposed to aggressive inks and cleaning solvents.
- Electroless Nickel Plating: This treatment enhances corrosion resistance and hardness, making the roller surface smoother and less prone to wear. It’s suitable for applications in corrosive environments or where roller longevity is critical.
- UV Coating: Applied to protect the roller from ultraviolet light damage, UV coatings are beneficial in outdoor applications or processes involving UV light exposure. This coating helps maintain the integrity of the roller surface over time.
- Diamond Coating: For the ultimate in durability and wear resistance, diamond coatings can be applied to aluminium guide rollers. This option is ideal for extremely abrasive environments where maintaining roller integrity is challenging.
Each of these specialized finishes and treatments adds a layer of functionality to aluminium guide rollers, extending their usability across a wider range of industrial applications. By selecting the appropriate finish or treatment, manufacturers can significantly enhance the performance, durability, and operational efficiency of their guide rollers.
Applications of Aluminium Guide Roller
Aluminium guide rollers are pivotal in a myriad of industrial applications, where their unique properties significantly contribute to the efficiency and reliability of operations. Here are seven critical applications that highlight the essential role of aluminium guide rollers:
- Sorting Facilities and Logistics Centers: In the fast-paced environment of sorting facilities and logistics centers, aluminium guide rollers are indispensable for directing parcels and goods along sorting lines. Their lightweight nature ensures high-speed operation with minimal energy consumption, while their durability withstands the constant, heavy flow of items.
- Machine Guides and Production Plants: Aluminium guide rollers serve as critical components in machine guides within production plants, guiding raw materials through the machinery for processing. Their precision and smooth operation are vital for maintaining the quality and consistency of the production output.
- Elevators, Escalators, and Conveyor Systems: The movement mechanisms of elevators, escalators, and conveyor systems rely heavily on aluminium guide rollers for smooth operation. Their corrosion resistance and strength ensure reliability and safety in these applications, where failure can result in significant downtime or hazards.
- Packaging and Labelling Industries: In the packaging and labelling industries, the precision and smoothness provided by aluminium guide rollers are crucial for the accurate placement of labels and the efficient packaging of products. Their ability to be customized for specific applications allows for enhanced performance tailored to the unique needs of these industries.
- Printing and Paper Processing: Aluminium guide rollers play a significant role in the printing and paper processing industries, where they guide paper through printers and processing machinery. Their smooth surface and thermal conductivity help in preventing paper jams and ensuring high-quality print outputs.
- Textile Manufacturing: In textile manufacturing, aluminium guide rollers are used to guide fabric through machines for weaving, dyeing, and finishing processes. Their lightweight and durable nature minimize fabric distortion and wear on the machinery, ensuring high-quality textile production.
- Food and Beverage Processing: The food and beverage processing industry benefits from the use of aluminium guide rollers in conveyor systems that transport ingredients, packaging materials, and final products. The non-toxic nature of aluminium and its resistance to corrosion make it an ideal choice for applications requiring strict hygiene standards.
Each of these applications benefits from the key features of aluminium guide rollers, such as their lightweight yet durable nature, customization options, and environmental benefits. Whether it’s facilitating the movement of goods in a logistics center, ensuring the precision of machinery in a production plant, or maintaining hygiene standards in food processing, aluminium guide rollers are essential for a wide range of industrial applications. Their versatility and performance underscore their importance in modern industrial operations, making them a preferred choice for companies looking to enhance efficiency and reliability in their processes.
Understanding the nuances of the aluminium rolling process and its impact on the properties of aluminium guide rollers is crucial for selecting the right type of roller for specific industrial applications. This knowledge ensures the optimal performance, durability, and efficiency of the rollers in their respective uses.
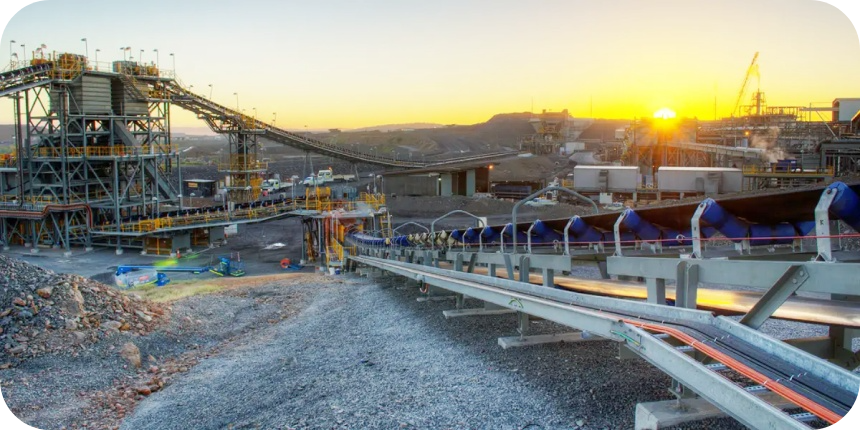
To Choose the Right Aluminium Guide Roller
Selecting the appropriate aluminium guide roller for your application is a critical decision that can significantly impact the efficiency, reliability, and overall performance of your machinery. Here are nine essential factors to consider when choosing an aluminium guide roller, followed by an in-depth look at the importance of dynamic balancing and surface finish.
Factors to Consider
- Application Requirements: Understand the specific needs of your application, including the type of material being guided, the speed of operation, and environmental conditions.
- Load Capacity: Evaluate the maximum load the aluminium guide roller will need to support. This includes both the weight of the materials being processed and the dynamic forces exerted during operation.
- Speed of Operation: Consider the operational speed of your system. Higher speeds may require rollers with specialized bearings and dynamic balancing to ensure smooth operation.
- Environmental Conditions: Assess the environmental conditions in which the roller will operate, such as exposure to chemicals, moisture, or extreme temperatures, and choose materials and finishes accordingly.
- Size and Dimensions: The size and dimensions of the roller must be compatible with your machinery and the materials being processed. This includes the roller’s diameter, length, and the shaft size.
- Material Compatibility: Ensure the aluminium and any coatings or treatments are compatible with the materials they will contact to avoid contamination or damage.
- Maintenance Requirements: Consider the ease of maintenance and the availability of replacement parts. Rollers designed for easy maintenance can reduce downtime.
- Customization Options: Look for customization options that can enhance the roller’s performance in your specific application, such as surface treatments, grooves, or custom bearings.
- Cost-Effectiveness: While initial cost is a factor, also consider the roller’s lifespan and maintenance costs. A more expensive roller that offers longer service life and lower maintenance costs may be more cost-effective in the long run.
The Importance of Dynamic Balancing and Surface Finish
Dynamic balancing and surface finish are critical aspects of aluminium guide roller performance, impacting operation in several ways:
- Vibration Reduction: Properly balanced rollers reduce vibration, leading to smoother operation and less wear on the roller and machinery.
- Extended Bearing Life: Dynamic balancing minimizes the load on bearings, extending their life and reducing maintenance requirements.
- Improved Product Quality: A smooth surface finish ensures consistent contact with the material being guided, improving product quality and reducing waste.
- Noise Reduction: Balanced rollers operate more quietly, contributing to a better working environment and meeting noise regulation standards.
- Increased Operational Speeds: Rollers that are dynamically balanced can operate at higher speeds without compromising stability or safety.
- Enhanced Durability: A superior surface finish can protect against corrosion and wear, extending the roller’s lifespan even in harsh conditions.
- Precision Guiding: The accuracy of material guiding is improved with a well-balanced roller, essential for applications requiring high precision.
- Efficiency: Smooth and balanced operation reduces energy consumption, as less force is required to move the roller and the materials it guides.
When choosing an aluminium guide roller, it’s essential to consider a comprehensive range of factors to ensure the roller meets the specific needs of your application. Additionally, paying close attention to the dynamic balancing and surface finish of the roller can significantly enhance its performance, longevity, and the overall efficiency of your operation.
Case Studies: Success with Aluminium Guide Roller
The implementation of aluminium guide rollers across various industries has demonstrated significant benefits, enhancing operational efficiency, product quality, and machinery longevity. Below are highlighted case studies showcasing the successful integration of aluminium guide rollers in different sectors, accompanied by testimonials from businesses that have experienced the advantages firsthand.
Successful Implementations in Various Industries
The adoption of aluminium guide rollers across diverse sectors has marked a significant shift towards more efficient, reliable, and cost-effective production processes. These industries have leveraged the unique properties of aluminium—lightweight, high strength, excellent corrosion resistance, and thermal conductivity—to enhance their operations. The following case studies showcase the broad applicability and success of aluminium guide rollers, illustrating their impact on various fields ranging from printing and textiles to food processing and logistics. Each example highlights the strategic advantage gained through this technological upgrade, underscoring the versatility and effectiveness of aluminium guide rollers in meeting industry-specific challenges.
- Printing Industry: A leading printing company replaced their traditional steel rollers with aluminium guide rollers, resulting in a 30% increase in operational speed due to the lighter weight and reduced inertia of aluminium.
- Textile Manufacturing: By switching to aluminium guide rollers, a textile manufacturer observed a noticeable improvement in fabric handling precision, reducing waste and improving product quality.
- Packaging Industry: A packaging plant reported a 25% reduction in energy consumption after integrating aluminium guide rollers, attributed to the rollers’ lower friction and smoother operation.
- Food Processing: In a food processing facility, the transition to aluminium guide rollers enhanced conveyor system reliability and cleanliness, thanks to aluminium’s natural corrosion resistance and ease of cleaning.
- Automotive Manufacturing: An automotive parts manufacturer noted improved production line efficiency and reduced maintenance downtime after adopting aluminium guide rollers, highlighting the material’s durability and ease of maintenance.
- Pharmaceuticals: A pharmaceutical company praised aluminium guide rollers for their contribution to a cleaner production environment, essential for maintaining high hygiene standards.
- Logistics and Warehousing: A logistics company implemented aluminium guide rollers in their sorting and distribution centers, experiencing improved sorting accuracy and system longevity.
- Paper Industry: The switch to aluminium guide rollers in a paper mill led to enhanced control over paper tension and alignment, crucial for high-quality printing and paper production.
Enhance productivity with our conveyor rollers. Contact us now!
Testimonials from Businesses
Hearing directly from businesses that have benefited from integrating aluminium guide roller into their operations offers invaluable insights into the practical advantages of this transition. These testimonials reflect a wide range of positive outcomes, including operational efficiencies, cost savings, product quality improvements, and environmental benefits. The feedback from companies across different industries not only attests to the tangible benefits of aluminium guide roller but also serves as a testament to their role in driving innovation and sustainability in modern manufacturing and processing environments. Below are reflections from businesses that have experienced firsthand the transformative impact of switching to aluminium guide roller, providing a real-world perspective on their value and performance.
- Increased Efficiency: The lighter weight of aluminium guide roller allowed us to increase the speed of our production lines without sacrificing stability or precision.
- Reduced Maintenance Costs: We’ve seen a significant reduction in maintenance needs since switching to aluminium rollers, directly impacting our bottom line positively.
- Enhanced Product Quality: Our product quality has improved markedly. The precise control offered by aluminium guide roller ensures consistent product dimensions and appearance.
- Energy Savings: The energy efficiency gains were unexpected but very welcome. The smoother operation of aluminium rollers reduces our energy consumption noticeably.
- Improved Workplace Safety: The reduced weight of aluminium rollers makes them easier and safer for our staff to handle during maintenance and setup.
- Longevity and Durability: We were initially concerned about the durability of aluminium, but these rollers have outlasted our old steel ones, with less wear and tear.
- Customization Capabilities: Being able to customize the surface finish and design of the aluminium guide rollers for our specific needs has been a game-changer.
- Environmental Impact: As a company committed to sustainability, the recyclability of aluminium guide roller aligns with our environmental goals, reducing our carbon footprint.
These case studies and testimonials underscore the transformative impact of aluminium guide rollers across industries, offering compelling evidence of their advantages in terms of efficiency, quality, and sustainability. The switch to aluminium guide roller not only meets the immediate operational needs of businesses but also contributes to broader environmental and economic goals.
FAQs about Aluminium Guide Roller
Guide rollers play a crucial role in various industrial and manufacturing settings by directing, supporting, and positioning moving materials along a predetermined path. These components are essential for ensuring smooth, efficient, and accurate transportation of materials through different stages of production or processing. The primary function of a guide roller is to maintain the correct alignment and tension of materials, such as sheets, films, cables, or any other continuous substrates, as they move through machinery or equipment.
The effectiveness of guide rollers in preventing material deviation is vital for minimizing waste and ensuring high-quality output. By maintaining proper alignment, guide rollers help avoid issues like wrinkling, tearing, or misalignment that can compromise product quality. Additionally, they contribute to the overall efficiency of the operation by reducing downtime and maintenance needs, as well as extending the lifespan of both the materials being processed and the machinery itself.
Guide rollers are designed to withstand the operational conditions of their specific applications, including high speeds, heavy loads, and environmental factors such as temperature and humidity. They come in various materials, sizes, and configurations, each tailored to meet the unique requirements of different industries, including printing, packaging, textile manufacturing, and more.
A guided roller, often referred to simply as a guide roller, is a specialized roller designed to control the movement and direction of materials as they pass through a machine or assembly line. These rollers are strategically placed to ensure materials follow a specific path, preventing misalignment and facilitating smooth transitions between different stages of a process. Guided rollers are integral to the functionality of conveyor systems, material handling equipment, and various types of machinery that require precise material guidance.
The design of a guided roller can vary widely depending on its intended use. Some are equipped with features like grooves or coatings to enhance grip, while others may be tailored for minimal contact to avoid damage to sensitive materials. The choice of material for the roller itself, such as aluminium, steel, or plastic, is determined by factors including the weight of the materials being guided, the speed of operation, environmental conditions, and the need for specific properties like corrosion resistance or thermal conductivity.
Guided rollers are not only about directing materials but also about enhancing the efficiency and reliability of the production process. They reduce the risk of material jams, ensure consistent product quality, and help maintain a steady flow of materials, contributing to the overall productivity and profitability of operations. Whether in the form of simple idler rollers or more complex motorized units, guided rollers are indispensable components in modern industrial applications.
Last Updated on August 15, 2024 by Jordan Smith
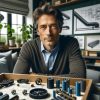
Jordan Smith, a seasoned professional with over 20 years of experience in the conveyor system industry. Jordan’s expertise lies in providing comprehensive solutions for conveyor rollers, belts, and accessories, catering to a wide range of industrial needs. From initial design and configuration to installation and meticulous troubleshooting, Jordan is adept at handling all aspects of conveyor system management. Whether you’re looking to upgrade your production line with efficient conveyor belts, require custom conveyor rollers for specific operations, or need expert advice on selecting the right conveyor accessories for your facility, Jordan is your reliable consultant. For any inquiries or assistance with conveyor system optimization, Jordan is available to share his wealth of knowledge and experience. Feel free to reach out at any time for professional guidance on all matters related to conveyor rollers, belts, and accessories.