Cost Analysis: Investing in Aluminum Gravity Roller Conveyors
Aluminum gravity roller conveyors stand as a cornerstone in the material handling sector, offering an efficient solution for moving goods across various industries including manufacturing, distribution, and packaging. These conveyors leverage the natural force of gravity to propel items, eliminating the need for an external power source. The use of aluminum as the primary material presents significant advantages. Its lightweight nature facilitates easy installation, reconfiguration, and mobility, making it ideal for dynamic workspaces that frequently adjust to new layouts or processes. Furthermore, aluminum’s inherent durability ensures a long-lasting conveyor solution capable of withstanding the rigors of daily operation while maintaining performance. This combination of efficiency, adaptability, and resilience highlights the pivotal role aluminum gravity roller conveyors play in optimizing workflow and enhancing productivity.
Detailed Insights into Aluminum Gravity Roller Conveyors
Aluminum gravity roller conveyors are essential components in the material handling industry, facilitating the smooth and efficient transport of goods across various distances within manufacturing, warehousing, and distribution centers. This section delves into the key features that make aluminum gravity roller conveyors a preferred choice for businesses seeking to optimize their operations.
Overview of Standard Specifications
The core of an aluminum gravity roller conveyor’s design lies in its standard specifications, which ensure compatibility with a wide range of industrial requirements. The rollers, typically made from high-grade aluminum, vary in diameter. Common sizes range from as small as 1.5 inches to larger diameters exceeding 3.5 inches, designed to accommodate different types of goods and packages. The aluminum construction not only provides a lightweight frame but also offers durability and resistance to corrosion, extending the equipment’s service life even in harsh environments.
Axle details are another critical specification. Axles can be fixed or spring-loaded, influencing the conveyor’s ability to handle loads and its flexibility during assembly and adjustment. Fixed axles offer stability for consistent, heavy loads, while spring-loaded axles allow for quick roller replacement and adjustments, enhancing the conveyor’s adaptability to changing operational needs.
Load capacities of aluminum gravity roller conveyors vary, primarily depending on the roller diameter and the frame construction. These conveyors can typically support weights from a few kilograms per roller to several hundred kilograms, allowing for the transport of a wide range of goods, from lightweight packages to heavy machinery parts.
Flexibility in Lengths and Widths
One of the standout features of aluminum gravity roller conveyors is their flexibility in terms of lengths and widths, making them highly adaptable to different operational layouts and requirements. This adaptability ensures that businesses can customize their conveyor systems to fit specific pathways, workspaces, or processing lines without compromising on efficiency or productivity.
Lengths can be adjusted by adding or removing sections of the conveyor, allowing businesses to extend or shorten their material handling lines as needed. This feature is particularly beneficial for facilities that experience seasonal fluctuations in volume or that are looking to expand their operations.
Widths are also customizable, ensuring that a variety of product sizes can be accommodated. Whether it’s narrow conveyors for small packages or wider systems for bulky items, the versatility in conveyor width helps optimize the flow of goods, reducing bottlenecks and improving overall throughput.
Aluminum gravity roller conveyors stand out for their robust standard specifications and exceptional flexibility. Their lightweight yet durable aluminum construction, combined with customizable lengths and widths, make them an invaluable tool for businesses aiming to streamline their material handling processes. By leveraging these features, companies can enhance their operational efficiency, adaptability, and ultimately, their competitiveness in the marketplace.
Advantages of Aluminum Gravity Roller Conveyors for Businesses
Aluminum gravity roller conveyors offer a range of advantages that can significantly benefit businesses, particularly in dynamic work environments where flexibility, efficiency, and sustainability are key. These conveyors are designed to support a variety of operational needs, from quick setups for temporary applications to enhancing loading and unloading efficiency. Moreover, the choice of aluminum as a material brings with it both ecological and economic benefits that can contribute to a business’s bottom line while also supporting environmental sustainability.
Supporting Dynamic Work Areas and Enhancing Efficiency
In dynamic work areas where the layout and processing needs may change frequently, aluminum gravity roller conveyors provide unparalleled flexibility. Their lightweight design allows for easy reconfiguration, facilitating quick setups for temporary applications or adjustments to existing lines. This adaptability is crucial for businesses that need to respond rapidly to changing market demands or operational requirements.
Moreover, aluminum gravity roller conveyors enhance loading and unloading efficiency. The smooth, frictionless surface of the rollers ensures that goods can be moved with minimal effort, reducing manual labor and speeding up the process. This increase in efficiency can lead to faster turnaround times and higher throughput, enabling businesses to meet their productivity targets more easily.
Ecological Benefits
The use of aluminum gravity roller conveyors also offers several ecological benefits:
- Recyclability: Aluminum is highly recyclable, reducing the need for raw materials and minimizing the environmental impact associated with extraction and processing.
- Lightweight: The lightweight nature of aluminum reduces energy consumption during transportation and operation of the conveyors.
- Durability: Aluminum’s resistance to corrosion extends the life of the conveyors, decreasing the frequency of replacements and the associated environmental footprint.
- Energy Efficiency: The manufacturing process of aluminum is increasingly becoming more energy-efficient, further reducing the ecological impact.
- Minimal Maintenance: Aluminum conveyors require less maintenance, reducing the use of cleaning chemicals and lubricants that can harm the environment.
- Reduced Carbon Footprint: The combination of recyclability, lightweight, and durability contributes to a significantly lower carbon footprint compared to conveyors made from less sustainable materials.
Economic Benefits
The economic benefits of using aluminum gravity roller conveyors are equally compelling:
- Cost-Effectiveness: The initial investment in aluminum conveyors can be offset by their long service life and low maintenance costs.
- Energy Savings: Lower energy consumption during operation can lead to significant cost savings, particularly in large-scale operations.
- Operational Efficiency: The increase in loading and unloading efficiency can reduce labor costs and enhance productivity.
- Flexibility: The ability to quickly reconfigure conveyor layouts can save on restructuring costs, making it easier to adapt to new processes without significant additional investment.
- Resale Value: Aluminum has a high resale value due to its recyclability, providing an additional economic return at the end of the conveyor’s life.
- Reduced Downtime: The durability and ease of maintenance of aluminum conveyors minimize downtime, ensuring continuous operation and productivity.
Aluminum gravity roller conveyors offer businesses a range of advantages that extend beyond their immediate operational benefits. From enhancing efficiency and flexibility in dynamic work areas to providing significant ecological and economic benefits, these conveyors represent a smart investment for businesses looking to optimize their operations while also contributing to environmental sustainability.
Aluminum Gravity Roller Conveyor Pricing
Navigating the pricing of aluminum gravity roller conveyors involves understanding various factors that can influence their cost. This comprehensive guide will delve into six key factors that affect the price of these conveyors, followed by ten practical tips to help businesses budget effectively for new installations or upgrades, ensuring both short-term affordability and long-term savings.
Factors Influencing Pricing
- Design Complexity: The more complex the design of an aluminum gravity roller conveyor, the higher the price. This includes specialized configurations tailored to unique operational needs, such as curved sections, gates, and inclines, which require additional engineering and manufacturing efforts.
- Size Specifications: The dimensions of the conveyor, including length, width, and roller diameter, play a significant role in determining the price. Larger conveyors with wider and larger-diameter rollers require more materials and thus, incur higher costs.
- Material Quality: The grade of aluminum used affects the price. High-grade aluminum alloys that offer enhanced durability and strength for heavy-duty applications tend to be more expensive than standard grades suitable for lighter loads.
- Load Capacity: Conveyors designed to carry heavier loads require robust construction and higher-quality materials, contributing to a higher price point. The engineering required to ensure safety and efficiency under heavy loads adds to the cost.
- Additional Features: Features such as adjustable stands, side guides, and brake rollers for controlling the speed of conveyed items can add to the cost. Each additional feature designed to enhance functionality or safety contributes to the overall price.
- Customization: Customized solutions tailored to specific business needs, such as specific roller coatings for grip or corrosion resistance, significantly influence the final price. Customization can include anything from specific paint colors to match a company’s branding to unique axle configurations.
Budgeting Tips for New Installations or Upgrades
- Assess Operational Needs: Clearly define your operational requirements to avoid overspending on unnecessary features or underestimating your needs, which could lead to costly future upgrades.
- Consider Long-Term Savings: Invest in higher-quality materials and designs that offer long-term durability and reduced maintenance costs, rather than opting for the cheapest initial option.
- Seek Expert Advice: Consulting with manufacturers or specialists can provide insights into the most cost-effective solutions tailored to your specific requirements.
- Compare Quotes: Obtain and compare quotes from multiple suppliers to ensure competitive pricing while taking note of the included features and warranties.
- Evaluate Total Cost of Ownership: Consider not only the purchase price but also installation costs, maintenance expenses, and potential savings from increased efficiency.
- Plan for Scalability: Choose designs that can be easily expanded or modified to accommodate future growth, potentially saving on significant overhaul costs later.
- Opt for Modular Designs: Modular systems can offer flexibility and cost savings by allowing for easy adjustments and expansions without a complete system overhaul.
- Incorporate Energy Efficiency: Selecting conveyors designed for energy efficiency can lead to substantial savings in operational costs over time.
- Utilize Financing Options: Explore financing or leasing options that can make the initial investment more manageable, allowing for immediate operational improvements without a large upfront expense.
- Consider the Resale Value: Factoring in the potential resale value of aluminum conveyors, given their durability and demand, can offset some of the initial costs.
Understanding the factors that influence the pricing of aluminum gravity roller conveyors and employing strategic budgeting tips can help businesses make informed decisions. By balancing initial costs with long-term value, companies can ensure they invest in conveyor systems that enhance operational efficiency, adaptability, and sustainability.
Finding Aluminum Gravity Roller Conveyors for Sale
When in the market for aluminum gravity roller conveyors, whether new or used, knowing where to look and what to consider can significantly streamline the purchasing process. Here are eight pieces of advice on sourcing these conveyors, along with insights into locating reliable sellers and manufacturers, and key considerations for purchasing used gravity roller conveyor for sale.
Sourcing New and Used Aluminum Gravity Roller Conveyors
- Research Manufacturers: Start with a comprehensive research phase to identify manufacturers that specialize in aluminum gravity roller conveyors. Look for companies with strong reputations for quality and customer service.
- Compare New vs. Used: New conveyors come with the latest technology and warranties but at a higher cost. Used conveyors can offer considerable savings, but it’s important to carefully assess their condition and suitability for your needs.
- Attend Trade Shows: Industry trade shows are excellent places to meet manufacturers and suppliers, see the conveyors in action, and negotiate deals.
- Online Marketplaces: Websites specializing in industrial equipment can be valuable resources for comparing options, finding used equipment, and reading reviews.
- Check Referrals: Ask for referrals from businesses in similar industries. Personal recommendations can lead you to reliable suppliers and insightful feedback on specific models or brands.
- Consider Customization Services: Some manufacturers offer customization options for new conveyors. If your operation requires specific features, this could be a decisive factor.
- Evaluate Warranty and Support: For new conveyors, understand the warranty and after-sales support. For used options, inquire about any remaining warranty or support services from the seller.
- Inspect Used Conveyors Thoroughly: If considering used conveyors, inspect them carefully for wear and tear, corrosion, and operational integrity. Consider hiring an expert if you’re not familiar with the technical aspects.
Locating Reliable Sellers and Manufacturers
- Industry Directories: Utilize industry directories and business networks to find manufacturers and suppliers with good ratings and verified customer feedback.
- Certifications and Standards: Look for sellers and manufacturers that adhere to industry standards and possess relevant certifications, indicating a commitment to quality and reliability.
- Ask for References: Request and follow up on references or case studies from the manufacturer or seller to gauge their reliability and the performance of their conveyors in real-world applications.
What to Look for When Purchasing Used Conveyors Near You
- Proximity: Buying from a local seller can reduce transportation costs and make it easier to inspect the conveyor in person.
- Operational History: Understand the operational history of the conveyor, including any major repairs or modifications.
- Compatibility: Ensure the conveyor’s specifications match your operational needs, including load capacity, size, and roller diameter.
- Spare Parts Availability: Check the availability of spare parts, especially for older models. Difficulty in sourcing parts can lead to increased downtime.
- Safety Standards: Verify that the conveyor meets current safety standards. Older equipment may need modifications to comply with today’s regulations.
By following these guidelines, businesses can make informed decisions when sourcing aluminum gravity roller conveyors, balancing cost considerations with operational needs to find the best solution for their material handling requirements.
Optional Features and Customizations for Aluminum Gravity Roller Conveyors
Aluminum gravity roller conveyors are highly versatile and adaptable to a wide range of industrial applications, thanks to the availability of numerous optional features and customizations. These enhancements not only extend the functionality of the conveyors but also ensure they can be perfectly tailored to meet the specific requirements of different operational environments. Below, we explore several optional variations and features, followed by an examination of their importance in enhancing the conveyor’s utility and adaptation to specific needs.
Optional Variations and Features
- Steel Frames with Aluminum Rollers: Combining steel frames with aluminum rollers offers the best of both worlds— the strength and durability of steel with the lightweight and corrosion-resistant properties of aluminum. This option is ideal for applications requiring robust support without a significant increase in weight.
- Knee Braces: For added stability, especially in longer spans or higher-load situations, knee braces can be installed. These provide additional structural support, preventing sagging and maintaining the conveyor’s integrity over time.
- Mid-Support Holes: Conveyors can be equipped with mid-support holes to allow for easy installation of additional supports where needed. This feature is particularly useful for custom installations or in situations where the conveyor will bear unusually heavy loads.
- Side Rails: Side rails can be added to prevent goods from slipping off the conveyor, enhancing safety and efficiency, especially when moving irregularly shaped items or operating on an incline.
Importance of Optional Features
- Enhanced Durability: Customization options like steel frames can significantly enhance the conveyor’s durability and lifespan, especially in harsh industrial environments.
- Increased Stability: Features like knee braces and mid-support holes offer increased stability, ensuring the conveyor remains aligned and functional under varying load conditions.
- Improved Safety: Adding side rails and other safety features can prevent accidents, ensuring goods are securely transported without risk of falling off.
- Versatility: The ability to customize conveyors with different materials and features allows them to be adapted for a wide range of applications, from lightweight packaging to heavy machinery parts.
- Efficiency: Customizations can improve the efficiency of operations by ensuring the conveyor system is perfectly suited to the task at hand, reducing bottlenecks and enhancing throughput.
- Reduced Maintenance: Selecting features that enhance durability and stability can lead to reduced maintenance needs, lowering long-term operational costs.
- Custom Fit: Optional features allow for a custom fit in any space or for any application, making the most of available space and enhancing operational flow.
- Aesthetic Integration: Customization can also ensure that the conveyor system fits with the aesthetic requirements or branding of a facility, offering a professional appearance alongside functionality.
- Future-Proofing: By choosing features that can adapt to changing operational needs, businesses can future-proof their conveyor systems, ensuring they remain useful and efficient as the business grows and evolves.
Incorporating optional features and customizations into an aluminum gravity roller conveyor setup ensures that businesses can tailor their material handling solutions to meet specific operational needs. This level of customization enhances functionality, safety, and efficiency, providing a competitive edge in any industry.
Making the Right Purchase Decision for an Aluminum Gravity Roller Conveyor
Selecting the right aluminum gravity roller conveyor for your business involves careful consideration of various factors to ensure the model you choose aligns perfectly with your operational needs. Here are nine strategies to guide you in making an informed purchase decision, along with seven critical questions to ask suppliers or manufacturers.
Strategies for Selecting the Right Model
- Understand Your Requirements: Clearly define the primary use of the conveyor, including the types of materials it will transport, the weight of these materials, and the required speed of movement.
- Analyze Model Strings and Specifications: Pay close attention to model strings that detail the conveyor’s specifications, such as roller diameter, width, frame material, and load capacity. These specifications are crucial for matching the conveyor to your operational needs.
- Consider the Work Environment: The work environment plays a significant role in selecting the right conveyor. Factors such as exposure to chemicals, moisture, or extreme temperatures can influence the choice of materials and design features.
- Assess Flexibility and Scalability: Evaluate the conveyor’s ability to adapt to future changes in your operations, such as expansions or shifts in the types of goods handled.
- Evaluate Load Capacity: Ensure the conveyor’s load capacity aligns with the heaviest items it will need to transport, incorporating a margin for safety and potential future needs.
- Inspect Roller and Frame Material: While aluminum is lightweight and resistant to corrosion, certain applications may benefit from a combination of aluminum rollers with steel frames for added strength.
- Review Optional Features and Customizations: Identify any additional features or customizations that could enhance efficiency, safety, or convenience, such as side rails, adjustable stands, or specific roller types.
- Consider Ease of Maintenance: Look for conveyors designed for easy maintenance, including accessible components and modular designs that allow for quick repairs or replacements.
- Budget Appropriately: Beyond the initial purchase price, consider installation costs, maintenance expenses, and potential operational savings. A higher upfront cost might be justified by lower long-term expenses or increased productivity.
Questions to Ask Suppliers or Manufacturers
- Can the conveyor be customized to fit specific operational needs? Understand the extent of customization available to ensure the system meets all your requirements.
- What is the expected lifespan of the conveyor under normal operation conditions? This helps gauge the long-term value of the investment.
- Are there any known compatibility issues with certain types of goods or environmental conditions? This question can uncover potential limitations of the conveyor system.
- What maintenance is required to keep the conveyor in optimal condition? Regular maintenance requirements can affect operational costs and uptime.
- What warranty and after-sales support are offered? A comprehensive warranty and reliable support can provide peace of mind and protect your investment.
- Can you provide references or case studies from businesses with similar applications? Real-world examples can demonstrate the conveyor’s performance and reliability.
- What are the lead times for delivery and installation? Knowing when the conveyor can be up and running is crucial for planning purposes.
By carefully considering these strategies and asking insightful questions, businesses can ensure they select an aluminum gravity roller conveyor that not only meets their current needs but also accommodates future growth and changes. This approach leads to a more efficient, adaptable, and cost-effective material handling solution.
Last Updated on August 1, 2024 by Jordan Smith
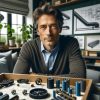
Jordan Smith, a seasoned professional with over 20 years of experience in the conveyor system industry. Jordan’s expertise lies in providing comprehensive solutions for conveyor rollers, belts, and accessories, catering to a wide range of industrial needs. From initial design and configuration to installation and meticulous troubleshooting, Jordan is adept at handling all aspects of conveyor system management. Whether you’re looking to upgrade your production line with efficient conveyor belts, require custom conveyor rollers for specific operations, or need expert advice on selecting the right conveyor accessories for your facility, Jordan is your reliable consultant. For any inquiries or assistance with conveyor system optimization, Jordan is available to share his wealth of knowledge and experience. Feel free to reach out at any time for professional guidance on all matters related to conveyor rollers, belts, and accessories.