Aluminum Guide Rollers: Enhancing Industrial Performance
In the world of mechanical components, the aluminum guide roller stands as a pivotal innovation, revered for its unparalleled blend of durability, efficiency, and lightweight nature. These rollers find themselves at the heart of a multitude of industrial processes, serving as essential components in conveyor systems, manufacturing lines, and even within the compact mechanics of aluminum roller garage doors. The versatility of aluminum guide rollers extends beyond the confines of industrial applications, seamlessly integrating into everyday home use. This integration underscores not just their technical superiority but also their adaptability to a wide range of environmental conditions and operational demands. From guiding heavy machinery with precision to facilitating smooth and silent operations in home appliances, aluminum guide rollers embody a perfect marriage of robustness and precision engineering. Their widespread adoption across various sectors is a testament to their indispensable role in enhancing productivity and operational reliability.
What are Aluminum Guide Rollers
Aluminum guide rollers are an essential component in various industrial, manufacturing, and material handling applications. These specialized rollers are designed to guide materials, products, or machinery parts along a set path within a system, ensuring smooth and efficient operation. The use of aluminum as the primary material for these rollers offers a range of benefits, making them a preferred choice in many sectors.
Definition and Basic Explanation of Aluminum Guide Rollers
An aluminum guide roller is a cylindrical tool crafted from aluminum, designed to assist in the controlled movement and handling of materials through a production line or within a machine. These rollers are typically mounted on a shaft and positioned in strategic locations to direct, support, and manage the flow of materials or products. The key feature of aluminum guide rollers is their construction material – aluminum – which provides a unique set of advantages over rollers made from other materials.
Importance of Aluminum as a Material Choice
The choice of aluminum for guide rollers is not coincidental. This material stands out due to its remarkable properties, which include:
- Lightweight: Aluminum’s low density makes aluminum guide rollers significantly lighter than those made from steel or other metals. This lightness translates to less energy required for the movement of rollers and the materials they guide, leading to energy efficiency improvements in machinery and systems where these rollers are used.
- Durability: Despite its lightweight nature, aluminum boasts a high strength-to-weight ratio, making it durable and capable of withstanding the stresses involved in guiding and transporting materials. This durability ensures a long service life for aluminum guide rollers, reducing the need for frequent replacements and maintenance.
- Resistance to Corrosion: One of the most valued properties of aluminum is its resistance to corrosion. Aluminum naturally forms a protective oxide layer when exposed to the atmosphere, which shields it from rust and corrosion. This feature is particularly beneficial in environments where moisture, chemicals, or other corrosive elements are present, as it maintains the integrity and functionality of the aluminum guide rollers over time.
Aluminum guide rollers are a pivotal component in various industrial settings, offering efficiency, reliability, and durability. The choice of aluminum as a material for these rollers leverages its lightweight nature, strength, and corrosion resistance, providing an optimal solution for guiding and handling materials in numerous applications.
Types and Applications of Aluminum Guide Rollers
Aluminum guide rollers, with their unique properties and versatile applications, play a critical role in various industries and machinery. They are widely appreciated for their lightweight, durability, and resistance to corrosion, which make them indispensable in many settings. Below is an overview of the types and applications of aluminum guide rollers, detailing their usage across different fields.
Each of these types of aluminum guide rollers is designed to meet specific operational needs, utilizing the inherent qualities of aluminum to enhance performance and efficiency. Whether in guiding conveyor belts, extending the life of roller chains, facilitating smooth garage door operation, or providing stable pathways for machinery components, aluminum guide rollers are an essential element in the smooth operation of many systems. Their widespread applications underscore the versatility and reliability of aluminum as a material choice in engineering and design.
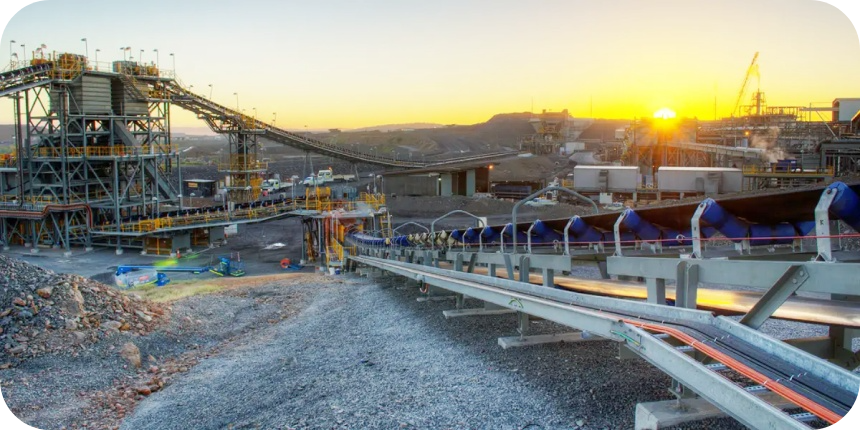
DIY Tips and Techniques for Working with Aluminum Guide Rollers
Working with aluminum, particularly in projects involving aluminum guide rollers, requires a certain level of skill and understanding. Whether you’re a hobbyist looking to undertake a new project or a professional refining your techniques, the following tips and step-by-step guides will help you navigate the process of rolling aluminum sheets and utilizing aluminum guide rollers effectively.
How to Roll Sheet Metal Without a Roller
- Using a Makeshift Roller: Utilize a sturdy pipe or another cylindrical tool as a makeshift roller. Secure your aluminum sheet on one end and gently bend it around the pipe, applying even pressure to avoid kinks.
- Manual Bending: For smaller projects, you can manually bend the aluminum sheet over a piece of wood or metal edge. This method requires precision and patience.
- Hammer Forming: This involves laying the aluminum sheet over a form and gently hammering it into shape. Use a leather or rubber mallet to prevent marking the metal.
- Heat Bending: Applying heat to specific areas of the aluminum sheet can make it more malleable. Be cautious with this method, as overheating can weaken the aluminum.
- Cutting and Rejoining: For complex shapes, consider cutting the aluminum sheet into smaller sections, shaping them individually, and then welding or riveting them back together.
- Sandbag and Mallet: For subtle curves, place the aluminum sheet over a sandbag and shape it by gently striking with a mallet. This allows for more control over the curve.
How to Roll Aluminum Sheet and How to Roll Aluminum
- Preparing the Material: Ensure the aluminum sheet is clean and mark your desired measurements clearly.
- Setting Up the Roller: Adjust your roller for the thickness of the aluminum sheet. Ensure it’s secure and stable.
- Feeding the Sheet: Carefully feed the edge of the aluminum sheet into the roller. For manual rollers, ensure even pressure is applied.
- Gradual Curving: Roll the sheet through multiple times, adjusting the roller tighter with each pass to gradually achieve the desired curve.
- Checking Consistency: Regularly check the curve against your template or measurements to ensure consistency.
- Finishing Touches: Once the desired shape is achieved, remove any burrs or sharp edges with a file or sandpaper.
- Safety First: Wear gloves and eye protection to prevent injuries.
- Lubrication: Apply a lubricant to both the aluminum sheet and the roller to reduce friction and the risk of tearing.
- Temperature Control: If the aluminum becomes too hard to work with, gentle heating can increase malleability. Monitor the temperature closely.
- Patience is Key: Take your time and make incremental adjustments, especially when working towards precise specifications.
How to Roll on a Roller
- Safety Checks: Before starting, ensure the roller is in good condition and that all safety guards are in place.
- Material Preparation: Clean the aluminum or material to be rolled. Any debris can affect the rolling process.
- Correct Placement: Feed the material into the roller carefully, starting from the front and ensuring it’s aligned.
- Consistent Pressure: Apply steady and even pressure as you roll the material through, adjusting settings as necessary for thickness.
- Monitor Progress: Continually check the shape and thickness of your material against your project requirements.
- Post-Roll Inspection: After rolling, inspect the material for any imperfections and address them as needed.
Whether you’re rolling aluminum sheets for a custom project or utilizing aluminum guide rollers in a more extensive setup, understanding these techniques and precautions will enhance your DIY projects’ safety, efficiency, and quality.
Customization and Innovation with Aluminum Guide Rollers
The world of aluminum guide rollers is not just limited to off-the-shelf components; it’s a realm where customization and innovation thrive. Aluminum, with its versatility and excellent physical properties, invites a broad spectrum of custom projects and innovative applications. From DIY home projects to cutting-edge industrial uses, aluminum guide rollers can be tailored to meet the exact needs of any endeavor.
Adaptability of Aluminum Rollers and Guides
Aluminum guide rollers are celebrated for their adaptability in various settings, making them a go-to choice for custom projects. Their lightweight nature, combined with strength and corrosion resistance, allows for innovative uses beyond traditional industrial applications. For example, in home DIY projects, aluminum guide rollers can be utilized in creating custom sliding door systems, providing a smooth, effortless glide. In the realm of technology, they can be used in 3D printers and robotics, guiding components with precision.
This adaptability extends to outdoor applications as well, where the corrosion-resistant properties of aluminum are particularly beneficial. From garden tools to custom bike frames, aluminum guide rollers can be designed to fit specific functional and aesthetic requirements, demonstrating their versatility across environments.
Custom-Made Aluminum Rollers and Guides
The possibility of creating custom-made aluminum rollers and guides opens up a new level of precision and efficiency in projects. Customization allows for the exact specifications of a project to be met, including dimensions, load-bearing capacities, and specific environmental resistances. This is particularly important in industrial settings where machinery must meet stringent operational requirements.
Manufacturers and fabricators of aluminum guide rollers often offer bespoke services, working closely with clients to design and produce rollers that fit the unique parameters of their projects. This collaborative process involves detailed planning and prototyping, ensuring that the final product not only meets but exceeds expectations.
For innovative applications, custom aluminum guide rollers can be engineered with unique features, such as integrated sensors for monitoring speed and load, or special coatings to enhance wear resistance or reduce friction. These innovations extend the functionality and longevity of the rollers, making them even more integral to the success of complex systems.
The customization and innovation possible with aluminum guide rollers highlight the material’s significant role in both traditional industries and emerging technologies. Whether for a bespoke piece of machinery, a DIY home project, or an innovative industrial application, the adaptability and potential for customization of aluminum guide rollers offer unparalleled opportunities. As technology advances, the boundaries of what can be achieved with these components are continually expanding, promising even more creative and efficient solutions in the future.
Choosing the Right Aluminum Guide Roller
Selecting the appropriate aluminum guide roller for your project is crucial to ensuring efficiency, longevity, and safety. With various types and designs available, understanding what factors to consider can make the selection process less daunting. Here are seven key factors and nine pieces of advice to help you choose the right aluminum guide roller for your specific needs, whether it be for industrial, commercial, or personal projects.
Factors to Consider
- Size and Diameter: The size of the roller, including its diameter and length, should match the requirements of your system. Consider the space available and the size of materials or products the roller will guide.
- Load Capacity: Evaluate the weight the roller needs to support. Aluminum guide rollers are favored for their strength-to-weight ratio, but it’s essential to select a roller that can handle the load without deformation.
- Environmental Conditions: Assess the environment in which the roller will operate. Factors such as temperature, moisture, and exposure to chemicals can affect the choice of aluminum alloy and protective coatings.
- Speed Requirements: Consider the speed at which the roller will operate. High-speed applications may require rollers with precision bearings and balanced construction to ensure smooth operation.
- Type of Bearing: The choice of bearings is crucial for performance and lifespan. Options include sealed bearings for dust-prone environments or high-precision bearings for applications requiring minimal friction.
- Surface Finish and Coating: The surface treatment of the roller affects its friction, wear resistance, and ability to resist corrosion. Choices range from anodized finishes to specialized coatings for extra protection or reduced friction.
- Compatibility with Existing Systems: Ensure the roller is compatible with the existing setup, including mounting hardware and guide tracks. This compatibility is vital for smooth integration and operation.
Advice on Selection
- Understand Your Application: Clearly define the purpose of the aluminum guide roller in your project. This understanding will guide your selection process, ensuring the roller meets your specific needs.
- Consult with Manufacturers: Manufacturers and suppliers have valuable insights and can offer recommendations based on their experience with similar applications.
- Prioritize Quality Over Cost: While budget constraints are real, investing in a high-quality roller can save money in the long run through reduced maintenance and longer service life.
- Consider Custom Solutions: If off-the-shelf options do not perfectly match your requirements, consider custom-made rollers. Many manufacturers offer this service.
- Research the Alloy Types: Different aluminum alloys offer varying properties. Research the most suitable alloy for your application, considering factors like strength, weight, and corrosion resistance.
- Evaluate the Roller Design: Look for designs that enhance performance, such as those that minimize vibration or are optimized for high-speed operations.
- Check for Certifications: Certifications can indicate quality and adherence to industry standards. Look for products that meet or exceed these standards.
- Plan for Maintenance: Choose rollers that are easy to maintain and come with clear guidelines for prolonging their lifespan.
- Safety First: Ensure the roller and its installation meet all safety requirements, especially in applications where failure could lead to injury or damage.
Choosing the right aluminum guide roller involves careful consideration of your project’s specific requirements. By taking into account the factors and advice outlined above, you can select a roller that offers the best performance, reliability, and value for your application.
Maintenance and Care for Aluminum Guide Rollers
Proper maintenance and care are crucial for ensuring the longevity and optimal performance of aluminum guide rollers. These components are vital in various applications, from industrial machinery to commercial installations. Here are 12 essential tips for maintaining aluminum guide rollers, followed by guidance on regular inspection and cleaning practices.
Maintenance Tips
- Regular Inspection: Schedule regular inspections of the aluminum guide rollers to identify wear, damage, or alignment issues early.
- Clean Regularly: Keep the rollers clean from dust, debris, and other materials that could cause wear or corrosion. Use a soft cloth and, if necessary, a mild cleaner that won’t damage the aluminum.
- Lubricate Bearings: Ensure the bearings are adequately lubricated according to the manufacturer’s recommendations. Use the correct lubricant type to prevent attracting dirt or causing buildup.
- Check for Misalignment: Misaligned rollers can lead to uneven wear and tear. Realign any rollers that have shifted from their proper position.
- Monitor Load Capacities: Avoid overloading the rollers beyond their designed load capacity, as this can cause premature wear or failure.
- Replace Worn Parts Timely: Don’t wait until a complete failure occurs. Replace worn or damaged parts promptly to maintain optimal performance.
- Avoid Harsh Chemicals: When cleaning, avoid using harsh chemicals that can corrode or damage the aluminum surface.
- Protect from Extreme Conditions: If possible, shield the rollers from extreme environmental conditions such as excessive moisture or direct exposure to chemicals.
- Ensure Proper Installation: Incorrect installation can lead to early failure. Ensure that rollers are installed correctly according to the manufacturer’s guidelines.
- Use Soft Tools for Cleaning: Avoid using abrasive tools that can scratch or damage the surface of the aluminum.
- Regularly Check for Corrosion: Inspect the rollers for signs of corrosion and take appropriate action if any is found, such as cleaning or applying a protective coating.
- Maintain a Maintenance Log: Keep a record of all maintenance activities, including inspections, cleanings, lubrications, and replacements. This log can help identify patterns or recurring issues.
Regular Inspection and Cleaning
Inspection: At least once a month, conduct a thorough inspection of the aluminum guide rollers. Look for signs of wear, such as scratches or dents, and check the integrity of the bearings and alignment. Use a straight edge or laser level for precise alignment checks.
Cleaning: To clean the rollers, first remove any surface dust or debris with a soft brush or cloth. For more thorough cleaning, use a damp cloth with a mild cleaner. Avoid soaking the rollers, as excessive moisture can lead to corrosion, especially in the bearings.
Lubrication: After cleaning, and if the manufacturer recommends, apply lubricant to the bearings. Do not over-lubricate, as excess lubricant can attract dirt that may lead to increased wear.
Alignment Checks: Misalignment can cause uneven wear and reduce efficiency. Use appropriate tools to check the alignment of the rollers and adjust as necessary.
By following these maintenance tips and regularly inspecting and caring for your aluminum guide rollers, you can significantly extend their life and ensure they continue to operate at optimal performance levels.
Have specific aluminum guide roller needs? Fill out the form to get personalized assistance.
FAQs about Aluminum Guide Roller
A guide roller is a specialized component designed to facilitate the smooth and precise movement of materials or objects along a defined path. Typically cylindrical in shape, these rollers are mounted on shafts and strategically positioned within machinery or conveyor systems to guide, support, and manage the flow of materials being processed or transported. Guide rollers are crafted from various materials, including metals like aluminum for its lightweight, durable, and corrosion-resistant properties, making them suitable for a wide range of industrial and commercial applications. The selection of a guide roller depends on several factors such as the load it needs to support, the environmental conditions it will be exposed to, and the speed at which it will operate. Proper maintenance and care of guide rollers, including regular inspections, cleaning, and lubrication, are crucial for ensuring their longevity and optimal performance.
A rolling guide, also known as a linear guide or rail, is an integral component used in precision machinery and equipment to ensure smooth, accurate, and frictionless linear motion. It consists of a guide rail and rolling elements, such as balls or rollers, which move within the rail to facilitate the controlled movement of a component or assembly in a straight line. Rolling guides are designed to bear loads while minimizing motion resistance, allowing for high precision and efficiency in the movement of machine parts or assemblies. These guides are essential in applications requiring precise control over movement, such as in CNC machines, robotic arms, and automated assembly lines. The choice of a rolling guide depends on factors like the required precision, load capacity, and operating environment. Regular maintenance, including cleaning and lubrication, is vital to prevent wear and ensure the rolling guide continues to operate smoothly and efficiently.
Last Updated on August 2, 2024 by Jordan Smith
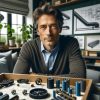
Jordan Smith, a seasoned professional with over 20 years of experience in the conveyor system industry. Jordan’s expertise lies in providing comprehensive solutions for conveyor rollers, belts, and accessories, catering to a wide range of industrial needs. From initial design and configuration to installation and meticulous troubleshooting, Jordan is adept at handling all aspects of conveyor system management. Whether you’re looking to upgrade your production line with efficient conveyor belts, require custom conveyor rollers for specific operations, or need expert advice on selecting the right conveyor accessories for your facility, Jordan is your reliable consultant. For any inquiries or assistance with conveyor system optimization, Jordan is available to share his wealth of knowledge and experience. Feel free to reach out at any time for professional guidance on all matters related to conveyor rollers, belts, and accessories.