Incline And Maximum Angle Belt Conveyor
Angle belt conveyor, a pivotal component in the material handling sector, are designed to transport goods across different elevations efficiently. These conveyors are particularly valuable in industries where space is at a premium or where materials need to be moved from one level to another, such as in mining, agriculture, and manufacturing. The belt conveyor inclination angle plays a crucial role in this process, as it directly influences the conveyor’s capacity to handle various types of materials without compromising on speed or safety. By adjusting the inclination angle, these conveyors can be tailored to meet the specific demands of a wide range of applications, making them a versatile and indispensable tool in the modern industrial landscape.
What Is the Inclination Angle of Angle Belt Conveyor
The inclination angle is a pivotal aspect in the design and functionality of angle belt conveyors, impacting several key areas:
- Material Retention: The inclination angle of angle belt conveyors is critical for ensuring materials stay on the conveyor during transport, especially at steeper angles which may require specific belt features to prevent slippage.
- Conveyor Length Efficiency: A steeper inclination angle can significantly reduce the length required for an angle belt conveyor to achieve a certain vertical lift, which is particularly advantageous in space-constrained environments.
- Load Capacity Impact: The inclination angle directly affects the load capacity of angle belt conveyors. As the angle increases, the gravitational pull on the materials can reduce the effective carrying capacity of the belt.
- Belt Tension Requirements: The required tension in the conveyor belt to prevent material slippage and ensure consistent throughput is influenced by the conveyor’s inclination angle.
- Increased Energy Consumption: Operating angle belt conveyors at higher inclination angles may lead to increased power consumption due to the added resistance of lifting materials.
- Optimal Belt Speed Adjustment: The inclination angle necessitates careful consideration of belt speed to balance efficient material transport and prevent spillage.
- Influence of Material Characteristics: The specific characteristics of the materials being transported, such as bulk density and size, interact with the inclination angle, influencing the choice of conveyor design and belt type.
- Enhanced Safety and Stability: Designing angle belt conveyors with appropriate inclination angles is essential for maintaining system stability and ensuring safe operation, particularly at higher angles.
- Flexibility and Adaptability: The inclination angle contributes to the overall flexibility of the conveyor system, allowing it to accommodate a range of materials and operational demands.
When it comes to tailoring angle belt conveyors for specific applications, the role of conveyor belt angle calculations becomes indispensable:
- Determining the Most Efficient Angle: Calculations are crucial for identifying the optimal inclination angle that balances material transport efficiency and conveyor capacity.
- Customization for Specific Materials: Conveyor belt angle calculations ensure that the conveyor is specifically tailored to the material it will transport, taking into account factors like angle of repose in belt conveyor and material flow characteristics.
- Maximizing Energy Efficiency: Through precise calculations, the inclination angle can be optimized to minimize energy usage while maintaining desired material throughput.
- Incorporating Safety Margins: Calculations include safety margins to prevent material rollback and ensure the conveyor operates within safe inclination parameters.
- Cost-Effectiveness: Optimizing the inclination angle through calculations can lead to cost savings by reducing material loss and lowering energy requirements.
- Seamless Integration: Accurate angle calculations ensure that the angled belt conveyor can be effectively integrated into existing material handling systems without compromising performance.
- Supporting Scalability: Understanding how inclination angles affect conveyor performance aids in designing systems that can be easily adjusted or expanded to meet future needs.
- Ensuring Compliance: Conveyor belt angle calculations help in ensuring that the angle belt conveyor design complies with relevant industry standards and safety regulations, particularly in terms of the inclination angle.
The inclination angle is thus a foundational element in the design and application of angle belt conveyors, influencing everything from material handling efficiency to system safety and adaptability. Precise conveyor belt angle calculations are critical for customizing these conveyors to meet specific industrial requirements, ensuring optimal performance and reliability.
Cost Considerations of Angle Belt Conveyor
When investing in belt conveyor angle, understanding the various factors that contribute to their cost is crucial. These conveyors are designed to transport materials at an incline, which requires specific design considerations to ensure efficiency and safety.
Factors Influencing the Cost of Angled Belt Conveyor
Investing in an angle belt conveyor requires a thorough understanding of the elements that contribute to its overall cost. This understanding ensures that you can make informed decisions tailored to your specific operational needs. Here are the key factors:
- Material Selection: The type and quality of materials used for both the conveyor belt and structure (e.g., rubber, steel, composites) play a significant role in determining the cost. Premium materials that offer durability and resistance to harsh conditions tend to be more expensive.
- Design Intricacy: Complex designs that accommodate steep inclines or incorporate additional features like sidewalls or cleats necessitate more engineering effort, raising the cost.
- Conveyor Size: The physical dimensions, particularly the length and width, directly impact the price due to the increased material and structural requirements.
- Capacity Requirements: Conveyors designed to handle heavier loads need to be built with stronger materials and components, which can elevate the cost.
- Custom Features: Specific customizations to meet unique operational requirements, such as special belt materials or adjustable operational parameters, can add to the overall cost.
- Advanced Controls: Incorporating sophisticated control systems for better operation monitoring and automation can significantly increase the price.
- Installation Demands: The complexity of installing the conveyor, influenced by site-specific conditions and the conveyor’s design, can affect the total cost. Understanding how to install a conveyor belt properly ensures that all factors are considered, from the initial setup to the final adjustments, to minimize complications and additional expenses.
- Maintenance and Longevity: Designs that prioritize ease of maintenance and durability might have higher upfront costs but can offer better value over time by minimizing repair and downtime expenses.
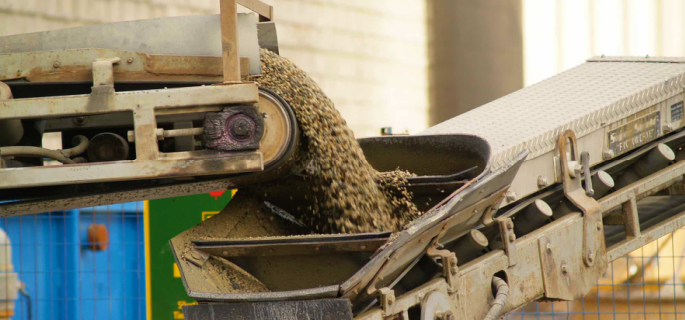
To Maximize Value in Angle Belt Conveyor Investments
To ensure that your investment in an angle belt conveyor yields the best possible return, consider these strategic tips:
- Define Operational Needs: Clearly identify your requirements to avoid overspending on unnecessary features.
- Supplier Comparison: Conduct thorough research and comparisons among suppliers to find the best quality-to-price ratio.
- Total Ownership Cost: Look beyond the initial price to consider ongoing maintenance, energy use, and potential downtime costs.
- Modular Design Preference: Opt for conveyors with modular designs for easier future upgrades or expansions, which can be more cost-effective.
- Quality Over Cost: Investing in higher-quality components can lead to lower long-term costs due to reduced maintenance and replacement needs.
- Strategic Customization: Only invest in custom features that significantly enhance operational efficiency to avoid extraneous expenses.
- Future-Proofing: Choose a design that can adapt to future operational changes without requiring a complete overhaul.
- Maintenance Contract Negotiations: A favorable maintenance contract can help manage long-term costs and ensure the conveyor’s longevity.
- Energy Efficiency: Although energy-efficient designs might cost more upfront, they can lead to substantial operational savings over the conveyor’s lifespan.
By carefully considering these factors and following these tips, you can make a well-informed decision on your angle belt conveyor investment, ensuring it meets your needs effectively without unnecessary expenditure.
Design and Calculations for Angle Belt Conveyor
Designing an belt conveyor inclination angle involves intricate planning and precise calculations to ensure efficiency, safety, and durability. Following the belt conveyor design steps meticulously is crucial, as each step—from selecting the appropriate materials and components to determining the optimal belt tension and alignment—contributes to the overall performance and reliability of the conveyor system. This section delves into the resources and methodologies employed in the design process of angle belt conveyors.
To Understand the Technical Aspects
The design of angle belt conveyors is underpinned by a set of technical considerations and calculations, ensuring the conveyor meets specific operational requirements:
- Load and Capacity Assessment: Determining the maximum load the conveyor needs to transport, factoring in both the weight and volume of materials.
- Belt Selection: Choosing the right belt material and type based on the nature of the materials being conveyed and the conveyor’s inclination angle.
- Inclination Angle Impact: Evaluating how the conveyor’s angle affects material flow, belt tension, and the potential for material slippage.
- Motor and Drive Calculations: Selecting a motor with sufficient power to move the desired load over the conveyor’s length and incline.
- Speed Requirements: Establishing the optimal belt speed to ensure efficient material transport without spillage.
- Structural Integrity: Ensuring the conveyor frame and supports are designed to handle the load and stresses imposed by the inclined operation.
- Safety Features: Incorporating necessary safety features, such as emergency stops, guards, and warning signals, especially critical at higher inclines.
- Energy Efficiency: Analyzing the conveyor’s energy requirements and exploring options for reducing energy consumption.
- Regulatory Compliance: Ensuring the design adheres to industry standards and safety regulations relevant to angle belt conveyor.
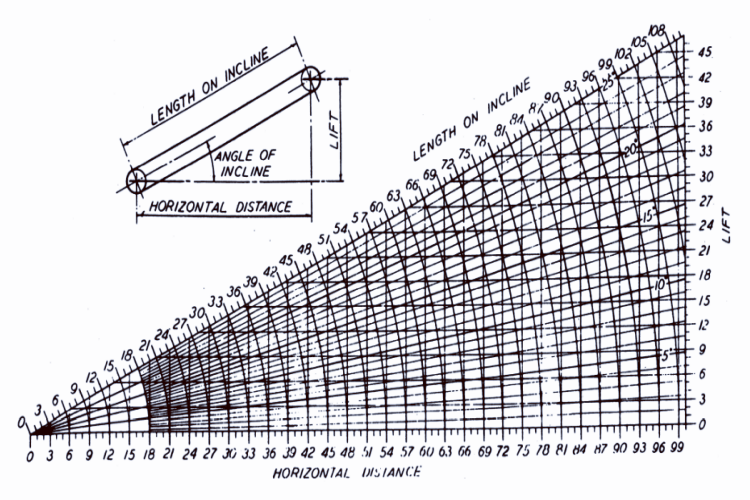
To Performe Basic Conveyor Belt Angle Calculations
A step-by-step guide to basic calculations for designing an angle belt conveyor includes:
- Determine the Conveyor Length: Calculate the horizontal and vertical distances the conveyor will cover, considering the incline angle.
- Calculate the Incline Angle: Use trigonometry or specialized tools to determine the angle based on the conveyor’s vertical lift and horizontal length.
- Assess Material Characteristics: Factor in the material’s bulk density, size, and flowability to ensure the conveyor design can handle the intended load.
- Belt Tension Calculation: Estimate the tension required to move the conveyor belt and the load, considering the weight of the belt and materials.
- Drive Power Calculation: Determine the power required by the drive motor to transport the load over the incline, factoring in friction and belt speed.
- Select Belt Type: Choose a belt type that provides adequate grip and support for the materials at the calculated incline angle.
- Design Pulley System: Design the pulley system to suit the belt type and tension requirements, ensuring efficient power transfer from the motor to the belt.
- Safety Margin Incorporation: Include safety margins in your calculations to account for variations in material characteristics and operational conditions.
By meticulously following these guidelines and performing the necessary calculations, designers can create angle belt conveyors that are efficient, safe, and tailored to specific material handling needs. These steps ensure that the conveyor not only meets the operational requirements but also operates reliably and efficiently over its lifespan.
To perform basic conveyor belt angle calculations, you can use the following steps:
1. Determine the Belt Length:
You need the length of the belt conveyor.
2. Calculate the Elevation Change:
Determine the elevation change (height) from the starting point to the endpoint of the conveyor.
3. Calculate the Horizontal Distance:
Measure the horizontal distance between the starting and ending points of the conveyor.
4. Calculate the Inclination Angle:
Use the trigonometric formula to calculate the inclination angle (θ) of the conveyor.
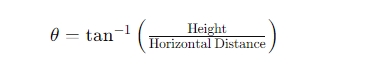
Example Calculation:
Suppose you have a conveyor belt with the following parameters:
- Elevation change (Height, (h)) = 10 meters
- Horizontal distance ((d)) = 50 meters
You can calculate the inclination angle as follows:
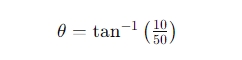
Using a calculator:
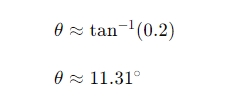
Therefore, the inclination angle of the conveyor belt is approximately (11.31^\circ).
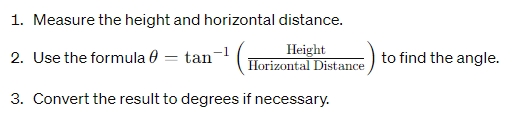
This basic method provides a straightforward way to determine the inclination angle of a conveyor belt.
To Visualize Angle Belt Conveyor: Diagrams and Parts
Delving into the world of angle belt conveyor, it becomes evident that a comprehensive understanding of their design and operational mechanics is crucial. Diagrams play a pivotal role in this context, offering a visual representation that encapsulates the complexity of these systems in a more digestible format.
Deciphering Angle Belt Conveyor Diagrams
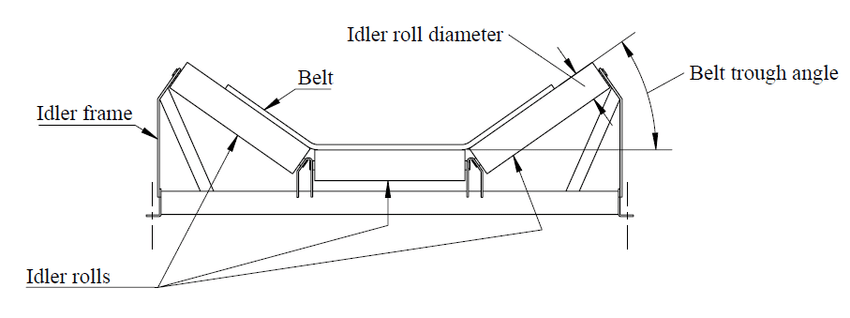
Angle belt conveyor diagrams serve as a blueprint, providing invaluable insights into the conveyor’s architecture:
- Path Illustration: Diagrams delineate the conveyor’s trajectory, clearly marking the ascent from the horizontal to the inclined phase, which is critical for visualizing the flow of materials.
- Material Journey: They trace the route materials take along the conveyor, pinpointing loading zones, transitions, and discharge points, which aids in understanding material handling dynamics.
- Spatial Configuration: By laying out the spatial arrangement of components, diagrams facilitate a deeper comprehension of how each part contributes to the conveyor’s overall functionality.
- Belt Tensioning Insights: The depiction of tensioning mechanisms within diagrams is vital for grasping how belt integrity and optimal tension are maintained, preventing slippage and ensuring smooth operation.
- Drive System Dynamics: The positioning of the drive system within the diagram highlights its role in powering the conveyor, offering clues on how belt movement is initiated and controlled.
- Safety Protocols: Diagrams emphasize safety components, such as emergency stops and protective guards, underscoring their integral role in the conveyor’s safe operation.
- Maintenance Accessibility: Highlighting maintenance access points in diagrams ensures that the design accommodates straightforward servicing, which is essential for long-term efficiency and reliability.
- Power and Control Mapping: The routing of electrical and control systems is illustrated, showing how the conveyor integrates into the larger operational framework, ensuring seamless functionality.
Through these diagrams, the intricate details of conveyor belt inclination angle are unraveled, providing a clear roadmap of their design and operational principles.
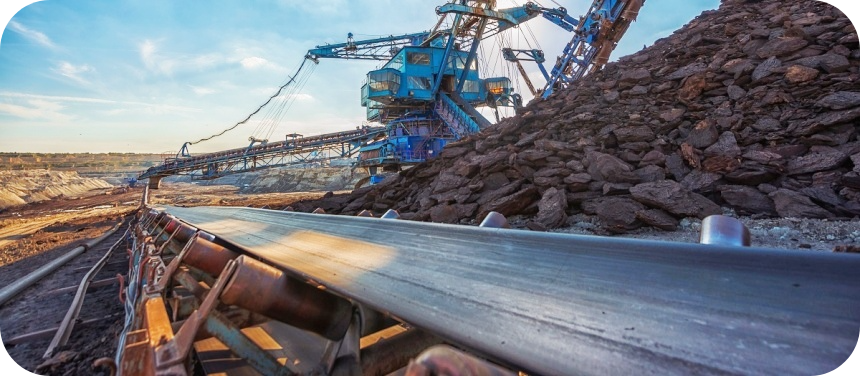
Core Components of Angle Belt Conveyor
The efficacy of angle belt conveyors is contingent upon a symphony of components, each fulfilling a specific role:
- Conveyor Belt: The heart of the conveyor, this component is responsible for the actual transport of materials, adapting to the incline to move items efficiently.
- Drive Pulley: This element propels the conveyor belt, often featuring a textured surface to enhance grip and ensure consistent belt movement.
- Tail Pulley: Positioned at the conveyor’s endpoint, it plays a crucial role in maintaining belt alignment and tension, ensuring smooth operation.
- Idler Rollers: These support the belt along its journey, minimizing friction and wear, which is particularly important in the elongated sections of the conveyor.
- Conveyor Frame: This structural backbone supports the conveyor’s components, providing stability and durability, especially in the demanding conditions of an inclined setup.
- Incline Segment: The angled portion that defines an angle belt conveyor, this segment facilitates the vertical transport of materials, challenging gravity.
- Loading Chute: Engineered to minimize spillage, this entry point ensures materials are smoothly transitioned onto the conveyor, marking the beginning of their ascent.
- Discharge Chute: This component directs materials off the conveyor at designated points, often adjustable to cater to specific unloading requirements.
Understanding these components and their functions is paramount for anyone involved in the design, operation, or maintenance of angle belt conveyors, ensuring they operate at peak efficiency and safety.
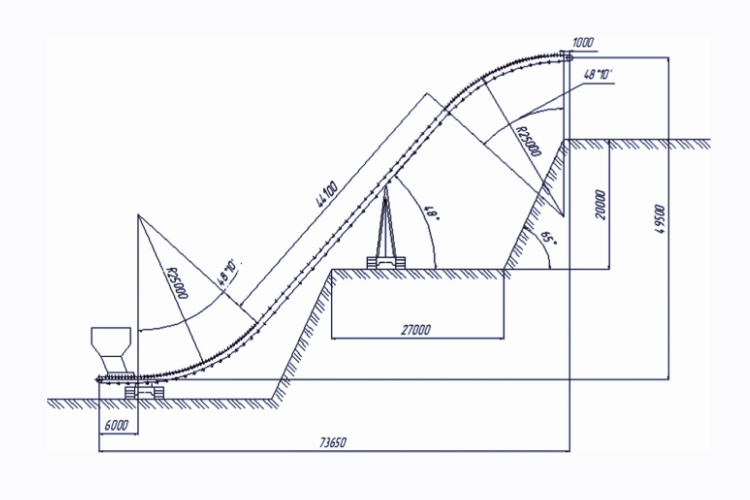
Types and Designs of Angle Belt Conveyor
The realm of belt conveyors is diverse, with various types and designs tailored to meet different industrial needs. Among these, flat belt conveyors and angle belt conveyors stand out for their distinct applications and functionalities. Additionally, the design variations within these categories, such as cleated belt conveyors, further enhance their utility in specific scenarios.
Flat vs. Angle Belt Conveyors
To understand the versatility and adaptability of belt conveyors, it’s essential to compare flat and angle belt conveyors:
Flat belt conveyors are the workhorses of material handling, suitable for a broad range of applications due to their simplicity and efficiency. In contrast, angle belt conveyors are specialized for scenarios where materials need to be moved across different elevations, offering a space-efficient solution for vertical transport.
Exploring Conveyor Belt Types
Diving deeper into the types of conveyor belts reveals the specialized designs catered to handling materials under various conditions:
- Standard Flat Belts: The most common type, used for general material handling and suitable for a wide range of products.
- Modular Plastic Belts: Comprised of interlocking plastic pieces, these belts are durable, easy to clean, and suitable for food processing applications.
- Wire Mesh Belts: Ideal for high-temperature environments, these belts allow for air circulation around the materials, commonly used in baking and drying processes.
- Cleated Belt Conveyors: Featuring raised sections or cleats, these conveyors are specifically designed for angle belt conveyor systems, ensuring materials are securely transported up inclines without rollback.
- Curved Belt Conveyors system: Engineered to navigate corners and bends, these conveyors are used in facilities where space constraints require flexible material flow paths.
- Incline/Decline Belt Conveyors: These are designed to move materials vertically, with specific features like textured surfaces or cleats to prevent slippage and ensure controlled material handling.
Each conveyor type serves a unique purpose, with cleated belt conveyors being particularly crucial in angle belt conveyor systems for their ability to manage inclined material transport efficiently. Understanding the specific applications and advantages of these conveyor types allows for optimized material handling solutions tailored to diverse industrial requirements.
Types of Angle Belt Conveyor
Angle belt conveyors come in various types, each designed to meet specific requirements based on the material being transported, the angle of inclination, and the operational environment. Here are some common types of angle belt conveyors:
1. Standard Incline Belt Conveyor
- Description: These conveyors have a simple design with a flat belt running over a series of rollers or a slider bed.
- Applications: Used for transporting lightweight to medium-weight materials in industries like manufacturing, packaging, and distribution.
- Incline Range: Typically up to 20 degrees.
2. Cleated Belt Conveyor
- Description: Equipped with cleats (protrusions) attached to the belt at regular intervals to prevent material from slipping back.
- Applications: Ideal for transporting bulk materials like grains, powders, and small parts at steeper angles.
- Incline Range: Up to 45 degrees or more.
3. Sidewall Belt Conveyor
- Description: Features corrugated sidewalls and cross cleats to create pockets that contain the material.
- Applications: Used for steep inclines and vertical lifts, often in mining, construction, and recycling industries.
- Incline Range: Up to 90 degrees (vertical).
4. Bucket Belt Conveyor
- Description: Combines a belt with attached buckets to lift materials vertically or at steep inclines.
- Applications: Suitable for handling fine or granular materials like sand, grains, and chemicals.
- Incline Range: Often up to 90 degrees (vertical).
5. Roller Bed Incline Conveyor
- Description: Utilizes rollers along the length of the conveyor to reduce friction and support the belt.
- Applications: Used for heavy-duty applications where low friction and efficient material handling are required.
- Incline Range: Typically up to 30 degrees.
6. Modular Belt Conveyor
- Description: Made of interlocking plastic segments, creating a flexible and durable belt.
- Applications: Common in food processing, packaging, and pharmaceutical industries for sanitary and corrosion-resistant requirements.
- Incline Range: Up to 45 degrees.
7. Portable Incline Conveyor
- Description: Lightweight, mobile conveyors that can be easily moved and adjusted to different angles.
- Applications: Used in temporary setups, warehouses, and small-scale production lines.
- Incline Range: Up to 30 degrees.
8. Screw Conveyor
- Description: Uses a helical screw blade to move materials along the conveyor.
- Applications: Suitable for moving granular and semi-solid materials like grain, food waste, and sand at various inclines.
- Incline Range: Varies, but typically up to 45 degrees.
Each type of angle belt conveyor is designed to handle specific materials and operational requirements. When selecting a conveyor, it’s important to consider factors such as the type of material, required angle of incline, and environmental conditions to ensure optimal performance and efficiency.
How to Choose The Right Angle Belt Conveyor
Choosing the suit angle belt conveyor involves considering several factors to ensure the conveyor meets the specific requirements of your application. Here’s a step-by-step guide to help you make an informed decision:
1. Understand Material Characteristics
- Type: Determine whether the material is granular, powdered, solid, or liquid.
- Flowability: Assess how easily the material flows. Materials that are free-flowing are easier to transport on inclined conveyors.
- Bulk Density: Know the weight per unit volume of the material.
- Size and Shape: Consider if the material is prone to lumping or bridging.
2. Determine the Inclination Angle
- Maximum Angle: Identify the steepest angle at which your material can be safely transported without slipping back. This is influenced by the material’s properties.
- Application Needs: Balance the desired height and horizontal distance to find the appropriate inclination.
3. Conveyor Length and Height
- Measure the horizontal distance and the vertical height the conveyor needs to cover.
- Ensure the conveyor length and incline match the space and layout constraints of your facility.
4. Capacity Requirements
- Calculate the required conveyor capacity in terms of volume per hour or units per hour.
- Ensure the conveyor can handle peak loads without overloading.
5. Type of Conveyor
- Standard Incline Belt Conveyor: Suitable for light to medium-weight materials at moderate angles.
- Cleated Belt Conveyor: Ideal for steeper inclines and materials prone to slippage.
- Sidewall Belt Conveyor: Best for very steep inclines and vertical lifts.
- Bucket Belt Conveyor: Suitable for vertical lifting of fine or granular materials.
6. Environmental Considerations
- Indoor or Outdoor: Ensure the conveyor material can withstand environmental conditions like moisture, dust, or extreme temperatures.
- Sanitary Requirements: For food processing or pharmaceuticals, choose conveyors with easy-to-clean designs and food-grade materials.
7. Belt Material and Design
- Material: Select the appropriate belt material (rubber, PVC, polyurethane) based on durability, flexibility, and chemical resistance.
- Cleats and Sidewalls: If needed, choose the right cleats and sidewalls to prevent material rollback and spillage.
8. Power and Drive System
- Ensure the motor and drive system can handle the required load and angle.
- Consider variable speed options if you need to adjust the conveyor speed for different operations.
9. Safety and Maintenance
- Choose conveyors with safety features like emergency stops, guards, and sensors.
- Consider ease of maintenance, including accessibility for cleaning and part replacement.
10. Cost and Budget
- Balance the features and specifications with your budget.
- Consider long-term operational costs, including maintenance and energy consumption.
Example Scenario
Suppose you need to transport grain from a ground-level hopper to a storage silo 15 meters above ground level over a horizontal distance of 20 meters. Here’s how you might proceed:
- Material Characteristics: Grain is free-flowing with moderate bulk density.
- Inclination Angle: Determine if the grain can be transported at an angle of around 37 degrees ((θ = tan^{-1}(15/20))).
- Conveyor Type: A cleated belt conveyor would be suitable for this incline and material type.
- Capacity: Calculate the required capacity based on the grain flow rate.
- Environmental Considerations: If the operation is outdoors, ensure the conveyor is weather-resistant.
- Belt Material: Choose a durable belt material like rubber or PVC.
- Power and Drive System: Ensure the motor can handle the load and provide consistent operation at the desired angle.
- Safety and Maintenance: Include features like emergency stops and easy-access points for maintenance.
By following these steps, you can select the right angle belt conveyor that meets your operational needs and ensures efficient and safe material handling.
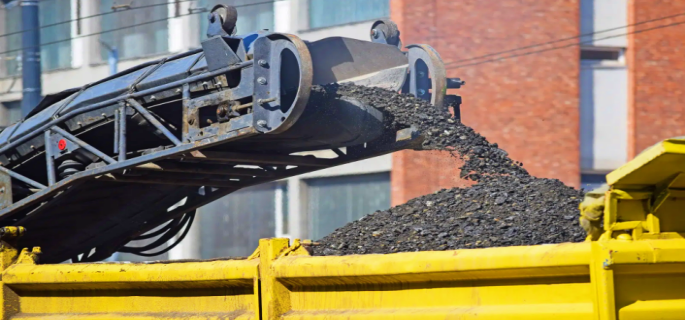
Practical Applications and Case Studies of Angle Belt Conveyor
The adaptability and efficiency of angle belt conveyors have been demonstrated across a wide array of industries, showcasing their ability to meet diverse material handling needs. From mining to food processing, these conveyors have become integral components of various operational workflows, enhancing productivity and operational efficiency. Below are some real-world examples that highlight the effectiveness and versatility of angle belt conveyors in different sectors.
Angle belt conveyors are widely used in various industries to transport materials at inclined angles. Here are some practical applications and case studies highlighting their usage:
Practical Applications
Mining Industry:
- Application: Angle belt conveyors transport bulk materials like ores, coal, and gravel from the mining site to the processing plant.
- Example: In open-pit mining operations, steep angle conveyors are used to move materials from deep pits to the surface, reducing the need for multiple conveyor stages.
Agriculture:
- Application: Inclined belt conveyors move grains, seeds, and fertilizers within storage facilities or from storage to processing areas.
- Example: Grain elevators use angle belt conveyors to elevate grains from ground level to storage bins or silos.
Food Processing:
- Application: These conveyors handle products such as fruits, vegetables, and packaged foods, moving them to different processing or packaging stages.
- Example: In a potato chip factory, inclined belt conveyors transportation potatoes from washing to slicing machines.
Construction:
- Application: Conveyors transport construction materials like sand, gravel, and cement to different levels on construction sites.
- Example: Inclined conveyors move concrete from mixers to pouring sites on multi-story buildings.
Waste Management:
- Application: Angle belt conveyors are used in recycling plants to move sorted materials to different processing areas.
- Example: Conveyors with cleats are used to move sorted plastics, metals, and papers up inclines to baling machines.
Pharmaceuticals:
Pharmaceutical manufacturing plants leverage angle belt conveyors to transport materials and products between different floors, maintaining a seamless flow in highly controlled environments.
Recycling Facilities:
In recycling operations, angle belt conveyors are pivotal in efficiently sorting and conveying recyclable materials to appropriate processing areas, enhancing recycling efficiency.
Case Studies
Case Study: Steep Angle Conveyor in Coal Mining
- Company: A large coal mining company implemented steep angle belt conveyors to transport coal from a depth of 300 meters to the surface.
- Outcome: The system reduced the need for multiple conveyor systems, cutting operational costs by 25% and improving efficiency.
Case Study: Grain Handling Facility
- Company: A grain handling facility installed inclined belt conveyors to transport grain from incoming trucks to storage silos.
- Outcome: The facility increased its grain handling capacity by 40% and reduced the time required for unloading trucks.
Case Study: Food Processing Plant
- Company: A vegetable processing plant used inclined belt conveyors to move washed vegetables to cutting and packaging stations.
- Outcome: The conveyors helped streamline the production process, resulting in a 30% increase in throughput and a reduction in labor costs.
Case Study: Recycling Plant
- Company: A recycling plant implemented cleated belt conveyors to move sorted materials to different processing stages.
- Outcome: The plant improved material handling efficiency by 35% and reduced the incidence of material spillage.
Angle belt conveyors are essential in various industries for their ability to transport materials efficiently over inclined distances. They help improve operational efficiency, reduce costs, and streamline processes in applications ranging from mining and agriculture to food processing and waste management.The application of angle belt conveyors in these industries underscores their capability to address complex material handling challenges, proving their indispensability in modern industrial operations.
Innovative Uses and Impact
The innovation in angle belt conveyor design and application has led to significant advancements in material handling, pushing the boundaries of what is possible in industrial operations. These innovations have not only optimized existing processes but have also introduced new capabilities, as detailed below.
- Space Optimization: By enabling vertical material transport, angle belt conveyors have revolutionized the design of industrial facilities, allowing for more efficient use of space and reducing the need for extensive horizontal conveyor systems.
- Energy Efficiency: Modern angle belt conveyors incorporate advanced drive technologies and control systems, making them more energy-efficient and reducing operational costs.
- Enhanced Safety: The design and operation of angle belt conveyors minimize direct human interaction with materials, leading to safer workplace environments and reducing the risk of accidents.
- Material Integrity: Innovations in conveyor technology now allow for the gentle handling of sensitive materials, ensuring that they are transported without damage, which is especially crucial in industries like food processing and pharmaceuticals.
- Customization: The ability to customize angle belt conveyors with specific features such as cleats and sidewalls has expanded their utility across various material handling scenarios, making them more adaptable to specific needs.
- Integration with Automation: Angle belt conveyors seamlessly integrate with automated systems, enhancing operational efficiency and reducing the need for manual intervention through precise control and material tracking.
- Reduced Maintenance: Advances in materials and design have led to angle belt conveyors that are more durable and require less maintenance, contributing to higher productivity and reduced downtime.
- Sustainability: By optimizing material flow and reducing reliance on fossil-fuel-powered equipment, angle belt conveyors support more sustainable industrial practices, aligning with global environmental goals.
These innovative uses and impacts highlight the transformative role of angle belt conveyor in modern industry, showcasing their contribution to more efficient, safe, and sustainable operations.
Transform your operations now with our unbeatable, high-performance conveyor belts!
FAQs about Angle Belt Conveyor
The angle of a conveyor belt, often referred to as the incline angle, is the degree to which the conveyor belt or path tilts from the horizontal plane. This angle is crucial in determining the conveyor’s ability to transport materials vertically or along an inclined plane. The specific angle chosen for a conveyor belt system depends on various factors, including the type of material being transported, the desired speed of transportation, and the available space within the facility. Conveyor belts can operate at a wide range of angles, from a slight incline to steep angles exceeding 45 degrees in some high-angle conveyor systems. The design of the conveyor, including the belt’s texture, cleats, and sidewalls, is often tailored to accommodate the specific incline angle, ensuring efficient material handling and minimizing the risk of slippage or spillage.
The angle of wrap on a conveyor belt refers to the extent to which the belt wraps around the drive pulley. This angle is critical for ensuring sufficient friction between the belt and the pulley, which in turn allows for effective power transmission from the pulley to the belt. A larger angle of wrap typically results in better grip and more efficient power transfer, leading to smoother and more reliable conveyor operation. In most conveyor systems, the angle of wrap can range from 180 degrees, where the belt simply passes over the pulley in a semi-circular path, to more than 200 degrees in systems where snub pulleys or other tensioning devices are used to increase the belt’s contact with the drive pulley. The angle of wrap is a key design consideration, especially in systems where high loads or steep inclines challenge the conveyor’s efficiency and require optimal power transmission to maintain consistent belt speed and material flow.
A high angle belt conveyor is a specialized conveyor system designed to transport materials at steep inclines or declines, where traditional flat or slightly inclined conveyors would be ineffective. These conveyors can operate at angles exceeding 45 degrees, with some systems capable of handling inclines up to 90 degrees. High angle belt conveyors utilize specific design features, such as tall cleats and sidewalls, to secure the material on the belt during transport, preventing slippage or spillage even at extreme angles. These systems are particularly beneficial in applications where space is limited, as they allow for vertical transportation of materials, effectively reducing the conveyor’s footprint. High angle belt conveyors find applications in various industries, including mining, construction, and bulk material handling, where they facilitate the efficient transport of materials between different levels or heights within a facility.
Conveyor belts are inclined to facilitate the movement of materials between different levels or heights within a facility, optimizing the material handling process. Inclining a conveyor belt allows for the efficient transport of materials upwards or downwards, eliminating the need for additional equipment such as elevators or hoists. This inclination is particularly useful in industries such as mining, construction, and agriculture, where materials often need to be moved from one elevation to another, whether from the depths of a mine to the surface or from ground level to storage silos. Inclined conveyor belts are designed to overcome the challenges of gravity and material slippage, incorporating features like textured belts, cleats, and sidewalls to ensure the secure and efficient transport of materials. By utilizing inclined conveyor belts, facilities can achieve a more streamlined and cost-effective material handling solution, enhancing productivity and reducing the need for manual labor.
Last Updated on June 6, 2024 by Jordan Smith
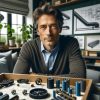
Jordan Smith, a seasoned professional with over 20 years of experience in the conveyor system industry. Jordan’s expertise lies in providing comprehensive solutions for conveyor rollers, belts, and accessories, catering to a wide range of industrial needs. From initial design and configuration to installation and meticulous troubleshooting, Jordan is adept at handling all aspects of conveyor system management. Whether you’re looking to upgrade your production line with efficient conveyor belts, require custom conveyor rollers for specific operations, or need expert advice on selecting the right conveyor accessories for your facility, Jordan is your reliable consultant. For any inquiries or assistance with conveyor system optimization, Jordan is available to share his wealth of knowledge and experience. Feel free to reach out at any time for professional guidance on all matters related to conveyor rollers, belts, and accessories.