Apron Belt Conveyor: Handling Tough Materials
Conveyor systems are integral to the seamless operation of various industrial sectors, facilitating the efficient movement of materials and products across manufacturing and processing facilities. Among the myriad of conveyor types, the apron belt conveyor stands out for its robust design and versatility, making it a critical component in the handling of bulk materials. These conveyors are particularly valued in heavy-duty applications where durability and reliability are paramount. The apron belt conveyor, with its unique construction, combines the efficiency of belt conveyors with the durability of apron feeders, ensuring that even the most challenging materials can be transported safely and effectively. This makes them indispensable in industries such as mining, construction, and heavy manufacturing, where the ability to move large, abrasive, or hot materials is essential to daily operations. Their importance cannot be overstated, as they significantly contribute to the productivity and efficiency of industrial applications worldwide.
What is an Apron Belt Conveyor
An apron belt conveyor is a specialized type of conveyor designed to handle heavy, bulky, or abrasive materials that standard conveyors cannot accommodate efficiently. This conveyor system combines elements of traditional belt conveyors with the robust and durable design of apron feeders, making it uniquely suited for challenging industrial environments.
Definition and Description
- Structure: The apron belt conveyor consists of a series of metal links or pans connected to a chain that moves along a set of rollers. This design provides a sturdy platform to carry materials.
- Capacity: It is designed to transport large volumes of materials, including those with high temperatures or abrasive qualities, which might damage other types of conveyors.
- Versatility: These conveyors can be used in a variety of settings, from mining operations to processing plants, where the movement of heavy or rough materials is required.
- Durability: Built to withstand harsh conditions, apron conveyor belts are made from materials that resist wear and tear, ensuring longevity and reliability.
- Efficient Material Handling: Apron belt conveyors are engineered for efficient handling and transportation of materials, ensuring minimal spillage and optimal flow. Their design allows for the smooth transition of materials onto and off the conveyor, enhancing overall productivity.
- Adjustable Speed: The speed of apron belt conveyors can be adjusted to match the specific requirements of the material being transported and the operational pace of the facility. This flexibility ensures that materials are moved at an appropriate speed for safe handling and efficient processing.
- Low Maintenance: Despite their heavy-duty construction, apron belt conveyors are designed for ease of maintenance. Critical components are easily accessible for inspection and repair, reducing downtime and keeping maintenance costs to a minimum.
Key Features of Apron Belt Conveyors
- Heavy-Duty Construction: Apron belt conveyors are built with durability in mind, featuring metal plates or pans that are linked together and mounted on a chain. This construction allows them to withstand the rigors of transporting heavy or abrasive materials over long distances.
- High Load Capacity: Thanks to their robust design, apron belt conveyors can carry significantly heavier loads compared to traditional belt conveyors. This makes them ideal for industries like mining, construction, and metal processing, where moving large volumes of heavy materials is a daily requirement.
- Versatility in Material Handling: These conveyors are capable of handling a wide range of materials, including hot, abrasive, or sticky substances that would typically pose challenges to other types of conveyors. Their design ensures that materials are securely transported, minimizing spillage and material loss.
- Customizable Design: Apron belt conveyors can be customized to suit specific operational needs. They can be designed with varying pan sizes, chain types, and materials to accommodate different types of loads and operational environments.
- Integrated Skirting Systems: Many apron belt conveyors come equipped with integrated skirting systems along the edges of the conveyor. These systems help to contain the material, reducing spillage and dust emissions. This feature is particularly beneficial in applications where environmental and safety regulations require strict control of particulate matter.
- Impact Resistance: The heavy-duty construction of apron belt conveyors provides exceptional resistance to impact from large, heavy materials dropped onto the conveyor. This capability is crucial in operations such as mining and quarrying, where the conveyor must withstand the sudden impact of rocks and ores.
Comparison with Other Types of Conveyors
When evaluating the various options for material handling within industrial settings, it’s crucial to understand the distinct characteristics and capabilities of different conveyor systems. Among these, the apron belt conveyor stands out for its specialized design, tailored to meet the demands of transporting heavy, abrasive, or high-temperature materials. This comparison aims to shed light on how apron belt conveyors compare with traditional belt conveyors and roller conveyors across several key features, including material type, durability, flexibility, capacity, maintenance requirements, cost, and typical applications. By examining these aspects, we can appreciate the unique advantages that apron conveyor belts offer, particularly in challenging industrial environments where the handling of difficult materials is a routine necessity. The following table provides a concise overview of these comparisons, highlighting the strengths and considerations associated with each conveyor type, and underscoring the specialized role of apron belt conveyors in heavy-duty material handling scenarios.
The apron belt conveyor distinguishes itself with its ability to transport materials that would typically pose challenges to other conveyor types, combining the efficiency of belt conveyors with the strength and durability of apron feeders. This makes it an invaluable tool in industries where heavy-duty material handling is a daily requirement.
Applications of Apron Belt Conveyor
Apron belt conveyors are versatile and robust systems designed for the efficient transportation of materials in various industrial settings. Their unique construction allows them to handle a wide range of materials, from heavy and abrasive to hot and bulky, making them indispensable in numerous sectors.
Industries and Scenarios
- Mining and Quarrying: Apron belt conveyors are extensively used in the mining industry to transport large chunks of raw materials, such as coal, ore, and aggregates, from the excavation site to processing facilities or directly to the transportation hubs.
- Construction Materials: In the construction industry, these conveyors transport materials like cement, bricks, and tiles, facilitating the continuous supply needed for various construction processes.
- Metal Processing: They are ideal for moving metal parts and scrap in foundries and steel mills, where high temperatures and abrasive materials are common.
- Waste Management and Recycling: Apron belt conveyors handle bulky and abrasive waste materials, including construction debris, metal scraps, and recyclable materials, ensuring efficient waste processing and recycling operations.
- Bulk Material Handling: Industries that deal with bulk materials, such as grain, sugar, and fertilizers, rely on apron belt conveyors for the safe and efficient movement of these products.
- Energy and Power Generation: In power plants, they are used to transport coal and biomass to feed boilers and support energy production processes.
- Food Processing: Although less common, apron conveyor belts can also be tailored for use in the food processing industry, especially for moving large volumes of agricultural products like grains and beans.
Specific Examples of Materials and Products
- Ores and Minerals: Transporting iron, copper, and nickel ores from mining operations to processing plants.
- Coal: Moving coal in power plants and processing facilities for energy production.
- Aggregates: Handling sand, gravel, and crushed stone for construction and infrastructure projects.
- Hot Sinter and Clinker: Conveying hot sinter from sinter plants and clinker from cement kilns, showcasing their ability to withstand high temperatures.
- Heavy Machinery Parts: Transporting large and heavy parts within manufacturing and assembly plants, especially in the automotive and aerospace sectors.
- Wood Chips and Bark: In pulp and paper mills, apron belt conveyors move wood chips and bark as part of the paper production process.
- Recycled Materials: Carrying a variety of recyclable materials, such as metal scraps, glass, and plastics, in recycling facilities to sort and process for reuse.
The apron belt conveyor’s ability to handle these diverse materials and products underscores its versatility and efficiency, making it a critical asset in the operational workflow of various industries. Its robust design ensures reliability and durability, even under the most challenging conditions, further solidifying its role in modern industrial applications.
Components of Apron Belt Conveyor
The apron belt conveyor is a complex system made up of various components, each playing a crucial role in its operation. Understanding these components and their functions is essential for anyone involved in the design, operation, or maintenance of these conveyors.
Key Components and Their Functions
- Apron Plates/Pans: These are the fundamental elements of the apron belt conveyor, designed to carry the material being transported. Made from steel or other durable materials, these plates form a continuous belt that can handle heavy and abrasive materials without significant wear.
- Chain Assembly: The chain assembly includes heavy-duty chains to which the apron plates are attached. This assembly is the driving force of the conveyor, moving the apron plates along the conveyor path. The durability of the chain assembly is crucial for the overall longevity of the conveyor system.
- Drive System: The drive system typically consists of motors and gearboxes that power the chain assembly. The size and power of the drive system are determined by the conveyor’s length and the load it needs to transport, ensuring efficient movement of materials.
- Rollers and Wheels: Rollers and wheels support the chain and apron plates as they move along the conveyor frame. They are strategically placed to reduce friction and wear, contributing to smoother operation and extended equipment life.
- Conveyor Frame: The frame provides structural support for the entire conveyor system. It is designed to withstand the weight of the materials being transported, as well as the stress and strain of operation.
- Tensioning System: This system is used to maintain the correct tension in the chain assembly, ensuring efficient operation and preventing slack that could lead to malfunctions or excessive wear.
- Guide Rails: Guide rails are installed along the sides of the conveyor to ensure that the apron plates and materials stay on track, preventing spillage and ensuring that materials are directed to the correct discharge points.
- Discharge Chute: The discharge chute is located at the end of the conveyor path, where the transported materials are offloaded. Its design is critical for directing materials efficiently and minimizing spillage.
- Safety Guards and Covers: Safety components, such as guards and covers, are essential for protecting operators from moving parts and preventing accidents. They are a critical aspect of the conveyor’s design, emphasizing the importance of safety in industrial environments.
- Control System: The control system manages the operation of the apron belt conveyor, including start-up, speed regulation, and shut-down procedures. Advanced control systems can also include features such as load monitoring and automatic tension adjustment.
Each component of the apron belt conveyor plays a specific role in its operation, contributing to the system’s efficiency, durability, and safety. The careful design and maintenance of these components are crucial for the reliable performance of the conveyor system, ensuring that it meets the demanding requirements of industrial applications.
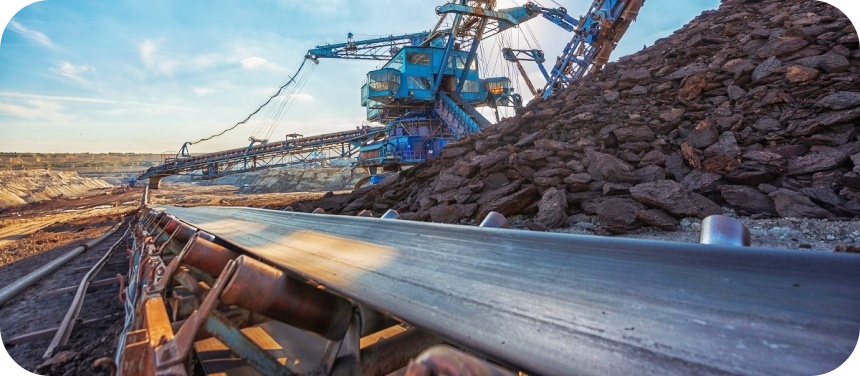
Manufacturers of Apron Belt Conveyor
The apron belt conveyor market is served by a number of key manufacturers, each bringing their own specialties and contributions to the industry. These companies are known for their innovation, quality, and service, ensuring that clients have access to the best solutions for their material handling needs.
Leading Manufacturers
Metso Outotec
- Specializes in providing heavy-duty apron belt conveyors for the mining and aggregates industries.
- Offers custom solutions tailored to specific operational requirements.
- Known for high durability and reliability in harsh conditions.
- Provides comprehensive services, including installation, maintenance, and parts.
- Emphasizes energy efficiency and environmental sustainability in their designs.
- Global presence with extensive support and service network.
FLSmidth
- Focuses on engineering apron belt conveyors for mineral processing and cement industries.
- Expertise in handling abrasive and hot materials.
- Offers a range of sizes and capacities to suit various applications.
- Integrates advanced technology for monitoring and automation.
- Renowned for robust construction and long service life.
- Provides worldwide service and technical support.
Thyssenkrupp Industrial Solutions
- Designs and manufactures apron belt conveyors for bulk material handling in mining, cement, and processing plants.
- Known for innovative solutions and custom designs.
- Offers systems designed for efficiency and cost-effectiveness.
- Emphasizes safety and ease of maintenance in their products.
- Global network of service and support.
- Invests in research and development to push the boundaries of conveyor technology.
TAKRAF
- Specializes in high-capacity apron belt conveyors for large-scale mining and material handling operations.
- Offers conveyors that are designed to withstand extreme conditions and materials.
- Provides a comprehensive range of services, from design through to commissioning.
- Focuses on reliability, durability, and minimizing operational costs.
- Has a strong focus on customer-specific solutions.
- Global presence ensures accessibility and support for clients worldwide.
Sandvik
- Offers a wide range of apron belt conveyors with a focus on mining, construction, and demolition debris handling.
- Known for high-quality materials and construction.
- Emphasizes innovation in conveyor technology and material handling efficiency.
- Provides global sales and service network.
- Focuses on safety and environmental sustainability.
- Offers solutions that are tailored to the unique needs of their clients.
Hazemag
- Renowned for their expertise in engineering apron belt conveyors for the cement and aggregates industries.
- Specializes in systems for processing raw materials.
- Known for robust and efficient design.
- Provides tailored solutions that address specific material handling challenges.
- Offers worldwide service and support.
- Continuously innovates to improve conveyor performance and durability.
BEUMER Group
- Specializes in custom apron belt conveyor solutions for various industries, including mining, cement, and power generation.
- Known for implementing advanced technology in their conveyor designs.
- Offers a comprehensive range of material handling solutions.
- Focuses on energy efficiency and sustainability.
- Provides global customer support and maintenance services.
- Emphasizes the reliability and safety of their conveyor systems.
Each of these manufacturers has made significant contributions to the development and advancement of apron belt conveyor technology. Their commitment to quality, innovation, and customer service ensures that industries have access to efficient, reliable, and durable material handling solutions.
Working Principle of Apron Belt Conveyor
The apron belt conveyor is a robust material handling system designed to transport heavy, bulky, or abrasive materials across various industrial settings. Its working principle combines the efficiency of belt conveyors with the durability of apron feeders, making it an ideal solution for challenging operational environments.
How Apron Belt Conveyors Work
- Material Loading: Materials are loaded onto the apron belt conveyor at the feed point. The conveyor consists of a series of metal plates or pans attached to a heavy-duty chain, creating a robust carrying surface.
- Chain Movement: A motor-driven gearbox powers the conveyor’s chain, moving the apron plates in a continuous loop. This movement transports the loaded materials along the conveyor path.
- Support Rollers: Beneath the apron plates, support rollers provide stability and reduce friction, facilitating smooth movement of the conveyor belt and ensuring even distribution of weight.
- Directional Flexibility: Apron belt conveyors can move materials horizontally, at inclines, or vertically, offering versatility in routing and the ability to navigate complex plant layouts.
- Controlled Speed: The conveyor’s speed can be adjusted based on the type of material being transported and the specific requirements of the operation, allowing for precise control over material flow.
- Discharge Mechanism: At the designated discharge point, materials are offloaded from the conveyor for further processing or storage. The design of the discharge area ensures efficient material transfer and minimizes spillage.
- Tensioning System: To maintain optimal performance, a tensioning system keeps the chain assembly tight, preventing sagging and ensuring consistent movement of the apron plates.
Efficiency and Effectiveness in Material Handling
- Handling of Diverse Materials: Apron belt conveyors are exceptionally effective at transporting a wide range of materials, including those that are hot, abrasive, or prone to sticking, which might otherwise damage conventional conveyors.
- Durability and Longevity: The robust construction of apron belt conveyors, including heavy-duty chains and metal plates, ensures they can withstand harsh operational conditions, leading to longer service life and reduced maintenance costs.
- High Capacity Transport: These conveyors are designed to handle large volumes of materials, making them efficient for operations that require the movement of significant quantities of bulk materials.
- Minimized Material Loss: The enclosed design of apron belt conveyors, with overlapping plates, minimizes spillage and material loss during transport, enhancing operational efficiency.
- Operational Flexibility: The ability to adjust the speed and direction of the conveyor allows for operational flexibility, accommodating changes in production needs and material types.
- Safety and Reliability: With built-in safety features and a design that prioritizes durability, apron belt conveyors offer reliable operation with minimal risk of downtime due to mechanical failures.
- Cost-Effectiveness: Despite the higher initial investment, the efficiency, durability, and low maintenance requirements of apron conveyor belts make them a cost-effective solution for heavy-duty material handling over the long term.
The working principle of apron belt conveyors, characterized by their robust design and operational flexibility, makes them an indispensable tool in industries where the efficient, reliable transport of heavy or challenging materials is a daily requirement.
Technical Aspects of Apron Belt Conveyor
The apron belt conveyor is a sophisticated system designed to meet the rigorous demands of heavy-duty industrial applications. Its technical specifications and capabilities are tailored to ensure optimal performance, durability, and reliability in transporting a wide variety of materials.
Technical Specifications and Capabilities
- Material Composition: Apron belt conveyors are constructed from high-grade, wear-resistant materials, such as steel or other alloys, ensuring they can handle abrasive and heavy loads without significant wear.
- Load Capacity: These conveyors are engineered to support substantial load capacities, often exceeding several hundred tons per hour, making them suitable for large-scale industrial operations.
- Speed Control: Equipped with variable speed drives, apron belt conveyors can adjust their speed according to the material type and processing requirements, enhancing efficiency and reducing energy consumption.
- Temperature Resistance: The design of apron belt conveyors allows them to operate in environments with extreme temperatures, making them ideal for industries like cement manufacturing and metal processing.
- Chain Design: The chains in an apron belt conveyor are specifically designed for high strength and durability, capable of withstanding the operational stresses of heavy-duty use.
- Maintenance Features: Easy access to critical components and modular design elements simplify maintenance and repair tasks, minimizing downtime and operational disruptions.
Customization Options for Specific Industrial Needs
- Apron Plate Design: The size, shape, and material of the apron plates can be customized to match the specific characteristics of the materials being transported, such as their abrasiveness, stickiness, or temperature.
- Conveyor Length and Width: Apron belt conveyors can be custom-built to any length and width to fit the spatial constraints of the facility and the volume of material to be handled.
- Incline and Decline Capabilities: Customization options include the ability to design the conveyor for inclines or declines, accommodating the unique topography of the operation site and the specific material handling requirements.
- Drive System Options: Depending on the application’s needs, the drive system can be tailored for optimal performance, including choices between electric motors, hydraulic drives, or pneumatic systems.
- Integrated Sensors and Controls: Advanced control systems, incorporating sensors for monitoring speed, load, and operational efficiency, can be integrated to automate the conveyor’s operation and optimize material flow.
- Specialized Discharge Mechanisms: Discharge systems can be customized to suit the material handling process, including options for controlled, metered discharge or rapid unloading, ensuring seamless integration into the production line.
The technical specifications and customization options of apron belt conveyors highlight their adaptability and efficiency in meeting the diverse needs of various industries. By tailoring the conveyor to the specific requirements of each application, businesses can achieve optimal material handling performance, enhancing productivity and operational efficiency.
Advantages of Using Apron Belt Conveyor
Apron belt conveyors offer a multitude of benefits that make them a preferred choice for heavy-duty industrial applications. Their design and functionality provide solutions to common material handling challenges, enhancing operational efficiency and productivity.
Key Benefits
- Durability: One of the most significant advantages of an apron belt conveyor is its exceptional durability. Constructed from high-quality, wear-resistant materials, these conveyors are designed to withstand the rigors of transporting heavy, abrasive, and high-temperature materials, ensuring a long service life with minimal maintenance requirements.
- Versatility: The apron belt conveyor’s design allows it to handle a wide range of materials, from fine powders to large, bulky items. This versatility makes it suitable for various industries, including mining, construction, and recycling, where the nature of materials can vary significantly.
- High Load Capacity: With their robust construction, apron belt conveyors are capable of carrying significantly heavier loads compared to traditional belt conveyors. This high load capacity is essential for industries that need to move large volumes of raw materials or finished products efficiently.
- Customization Options: Apron belt conveyors can be customized to meet specific operational needs. From the length and width of the conveyor to the design of the apron plates and the drive system, each aspect can be tailored to optimize performance for specific materials and processing requirements.
- Reduced Material Spillage: The design of apron belt conveyors, with closely fitted plates, minimizes material spillage during transport. This not only reduces waste but also contributes to a cleaner and safer working environment, reducing cleanup costs and minimizing the risk of accidents.
- Operational Efficiency: The ability to adjust the speed of the conveyor and integrate advanced control systems allows for precise control over material flow. This operational efficiency can lead to improved productivity, as materials are moved seamlessly through the production process without unnecessary delays or bottlenecks.
- Safety Features: Apron belt conveyors are equipped with various safety features, including emergency stops, guards, and covers, to protect workers from moving parts and prevent accidents. These safety measures are crucial for maintaining a safe working environment, especially in industries where heavy machinery is in constant operation.
The advantages of using an apron belt conveyor in industrial applications are clear. Its durability, versatility, and efficiency make it an invaluable tool for businesses that require reliable and effective material handling solutions. By investing in an apron belt conveyor, companies can improve their operational efficiency, reduce costs, and enhance safety in the workplace.
Maintenance and Safety Considerations for Apron Belt Conveyor
Ensuring the longevity and optimal performance of an apron belt conveyor requires diligent maintenance and adherence to safety protocols. Below are essential tips and best practices for maintaining and safely operating apron belt conveyors.
Maintenance Tips
- Regular Inspections: Conduct routine inspections of the apron belt conveyor to identify wear and tear on the apron plates, chains, and rollers. Early detection of potential issues can prevent costly downtime and repairs.
- Lubrication: Regularly lubricate the chain assembly and moving parts to reduce friction and wear. Use the correct type of lubricant as recommended by the manufacturer to ensure the longevity of the components.
- Cleaning: Keep the conveyor clean from debris and materials that could cause blockages or accumulate on the moving parts, leading to increased wear or potential malfunctions.
- Tension Adjustment: Monitor and adjust the tension of the chains as needed to prevent sagging or excessive tightness, which could lead to premature wear or damage to the conveyor.
- Component Replacement: Replace worn or damaged components promptly. Using genuine parts recommended by the manufacturer ensures compatibility and reliability.
- Monitoring System: Utilize monitoring systems, if available, to track the performance and condition of the conveyor. Advanced systems can alert operators to issues before they become serious problems.
- Training: Ensure that maintenance personnel are properly trained in the specific requirements for servicing apron belt conveyors. Understanding the unique aspects of these conveyors can improve the effectiveness of maintenance activities.
- Maintenance Schedule: Adhere to a regular maintenance schedule as outlined by the manufacturer. Preventative maintenance is key to avoiding unexpected breakdowns and extending the life of the conveyor.
Safety Protocols and Best Practices
- Emergency Stops: Ensure that emergency stop mechanisms are accessible along the length of the conveyor. Regularly test these systems to confirm they are in working order.
- Guarding: Use guards and covers to protect moving parts. This helps prevent accidental contact with chains, rollers, and other components that could cause injury.
- Training: Provide comprehensive training for all operators and maintenance personnel. Understanding how to safely operate and maintain the apron belt conveyor is crucial for preventing accidents.
- Warning Signs: Display warning signs and labels to indicate potential hazards associated with the conveyor. Clearly marking control mechanisms, emergency stops, and other safety features can enhance safety awareness.
- Lockout/Tagout Procedures: Implement lockout/tagout procedures during maintenance and repair activities to ensure that the conveyor cannot be inadvertently activated.
- Personal Protective Equipment (PPE): Require the use of appropriate PPE, such as gloves, safety glasses, and hard hats, when operating or maintaining the conveyor. Protecting against potential hazards is essential for safety.
Adhering to these maintenance and safety considerations for apron belt conveyors can significantly enhance their performance and longevity while ensuring a safe working environment for all personnel involved.
Upgrade your system with our durable conveyor belts.
Future Trends in Apron Belt Conveyor Technology
The apron belt conveyor, a critical component in industrial material handling, is poised for significant technological advancements and innovations. These developments aim to enhance efficiency, sustainability, and adaptability, meeting the evolving demands of industries worldwide.
Technological Advancements and Innovations
- Smart Monitoring Systems: Integration of IoT (Internet of Things) sensors and AI (Artificial Intelligence) analytics for real-time monitoring of conveyor performance, predicting maintenance needs, and optimizing operational efficiency.
- Eco-friendly Materials: Development of apron plates and components using sustainable, recycled, or lighter materials that maintain durability while reducing the environmental footprint.
- Energy Efficiency: Innovations in drive systems to reduce energy consumption, including the use of energy-efficient motors and the incorporation of energy recovery systems in apron belt conveyor operations.
- Advanced Wear Detection: Implementation of sensors capable of detecting wear and tear on apron plates and chains, allowing for predictive maintenance and reducing unexpected downtime.
- Modular and Scalable Designs: Development of modular apron belt conveyors that can be easily expanded or reconfigured to meet changing production needs, enhancing flexibility and scalability.
- Enhanced Safety Features: Incorporation of more sophisticated safety mechanisms, including automated emergency stops, better guarding, and enhanced safety training modules using virtual reality (VR).
- Improved Material Handling: Innovations in apron plate design to handle a wider variety of materials more efficiently, including designs that minimize spillage and optimize material flow.
- Robotics and Automation: Integration of robotic systems for automated loading and unloading, reducing manual labor requirements and improving precision in material handling.
- Sustainability Focus: Increased emphasis on reducing the carbon footprint of apron belt conveyors through the use of renewable energy sources and the development of more energy-efficient operations.
These future trends in apron belt conveyor technology reflect a broader movement towards smarter, more sustainable, and safer material handling solutions. By embracing these innovations, industries can look forward to improved operational efficiency, reduced environmental impact, and enhanced worker safety in their material handling operations.
FAQs about Apron Belt Conveyor
An apron conveyor is a type of conveyor made to handle bulk materials across various industries, including mining, construction, and heavy manufacturing. It consists of a series of steel or metal plates (aprons) attached to a heavy-duty chain that moves along a track. This design allows the apron conveyor to transport large, heavy, or abrasive materials that might damage other types of conveyors. Its robust construction ensures durability and reliability in harsh operational environments, making it ideal for transporting materials such as rocks, ores, and other bulk goods. The apron conveyor’s design can handle materials with high temperatures, making it suitable for industries like cement manufacturing and metal processing, where materials must be moved through or from high-temperature zones.
The primary difference between belt and apron conveyors lies in their design and material handling capabilities. Belt conveyors consist of a continuous belt made from flexible materials like rubber, PVC, or fabric, running over a series of pulleys. They are suited for transporting light to medium-weight materials over long distances, either horizontally or at slight inclines. Apron conveyors, on the other hand, are constructed with metal plates attached to a chain, designed to transport heavy, abrasive, or hot materials that would damage a belt conveyor. While belt conveyors are versatile and cost-effective for various materials and applications, apron conveyors are specialized for challenging environments where durability and the ability to handle rough materials are paramount.
The three common types of conveyors are belt conveyors, roller conveyors, and chain conveyors. Belt conveyors are used for transporting light to medium-weight materials over long distances and can handle a variety of products with different shapes and sizes. Roller conveyors are ideal for moving items that have a firm bottom surface, relying on gravity or manual power to move goods and are often used in warehousing and package handling. Chain conveyors, which include apron conveyors as a subtype, use chains to move products along the production line and are suitable for heavy or bulky items that require a sturdy conveying solution. Each type of conveyor offers unique advantages and is selected based on the specific needs of the material handling process, including the weight, size, and type of materials to be transported.
A bucket apron conveyor combines the features of an apron conveyor with those of a bucket elevator. This type of conveyor is designed to vertically transport bulk materials, combining the robust, heavy-duty characteristics of apron conveyors with the vertical lifting capabilities of bucket elevators. It consists of a series of buckets attached to a chain or belt, with the added protection and support of apron plates. This design allows for the efficient vertical transport of materials such as grains, coal, minerals, and other bulk goods, especially in situations where space is limited. Bucket apron conveyors are particularly useful in industries where materials need to be lifted from one level to another, such as in silos, storage facilities, and processing plants, offering a durable and efficient solution for vertical material handling challenges.
Last Updated on July 4, 2024 by Jordan Smith
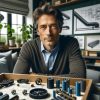
Jordan Smith, a seasoned professional with over 20 years of experience in the conveyor system industry. Jordan’s expertise lies in providing comprehensive solutions for conveyor rollers, belts, and accessories, catering to a wide range of industrial needs. From initial design and configuration to installation and meticulous troubleshooting, Jordan is adept at handling all aspects of conveyor system management. Whether you’re looking to upgrade your production line with efficient conveyor belts, require custom conveyor rollers for specific operations, or need expert advice on selecting the right conveyor accessories for your facility, Jordan is your reliable consultant. For any inquiries or assistance with conveyor system optimization, Jordan is available to share his wealth of knowledge and experience. Feel free to reach out at any time for professional guidance on all matters related to conveyor rollers, belts, and accessories.