Ball Bearing Conveyor Rollers: Maintenance Insights
Ball bearing conveyor rollers play a crucial role in industrial applications, providing smooth and efficient transport of materials across manufacturing facilities. Their precision-engineered design ensures minimal friction, reducing wear and tear on both the rollers and the conveyor systems they support. This blog delves into the various types of ball bearing conveyor rollers available, each tailored to meet specific industry needs. From standard cylindrical rollers to specialized tapered options, we cover the range of configurations that help optimize load distribution, speed, and durability. Whether handling light loads in packaging or heavy-duty materials in steel processing, these rollers offer reliable, long-term performance in diverse environments.
What Are Ball Bearing Conveyor Rollers
Ball bearing conveyor rollers are integral components of modern industrial conveyor systems, designed to enhance efficiency and reliability in material transport. These rollers utilize ball bearings to minimize friction and facilitate smooth movement of the conveyor belt, even under heavy loads. This section will delve deeper into the structure and importance of ball bearing conveyor rollers, detailing their definition, functionality, and their pivotal role in ensuring efficient material handling.
Definition and Function of Ball Bearing Conveyor Rollers
Ball bearing conveyor rollers are designed to support the conveyor belt and the materials being transported. They consist of a tube-like structure that houses ball bearings at each end, enabling the roller to move smoothly with minimal resistance.
- Structural Composition: Each roller is constructed with a strong outer shell, typically made of metal or plastic, and is fitted with ball bearings that reduce surface contact with the belt.
- Friction Management: The primary function of these bearings is to decrease friction, which in turn reduces the wear on the conveyor belt and the roller itself.
- Load Support: These rollers are crucial for distributing the load evenly across the conveyor belt, preventing any single area from bearing too much weight and potentially tearing.
- Operational Speed: They help maintain a consistent belt speed, essential for synchronized operations across various stages of the production line.
- Acoustic Benefits: The reduction in friction not only enhances performance but also significantly cuts down on noise, leading to a more agreeable work environment.
- Energy Savings: Efficient motion translates into lower power requirements, thereby saving energy and operational costs.
- Customization and Adaptability: Ball bearing conveyor rollers are available in various dimensions and materials, adaptable to different environments and operational demands.
Importance in Facilitating Smooth and Efficient Material Handling
The functionality of ball bearing conveyor rollers extends beyond mere movement, playing a critical role in the efficiency and safety of industrial operations. Their design and operation have a direct impact on the productivity and operational costs.
- Streamlined Production: Smooth roller operation ensures that the production line remains uninterrupted, which is crucial for meeting production targets and deadlines.
- Safety Enhancements: Stable and predictable movement reduces the risk of mishaps and injuries, ensuring a safer workplace.
- Longevity of System Components: By minimizing the wear on conveyor components, these rollers extend the usable life of the entire system.
- Handling Accuracy: The stability provided by these rollers enables precise movement and placement of materials, which is particularly important in automated and precision-required processes.
- Economic Efficiency: The reduced need for frequent maintenance and part replacement translates into cost savings and higher return on investment.
- Versatility in Material Handling: They can efficiently transport a wide range of materials, from delicate products to heavy industrial components.
- Reduced Environmental Footprint: Lower energy usage and noise pollution contribute to more environmentally friendly operations.
- Scalable Operations: The ability to integrate these rollers into various parts of the production process allows for easy scalability as business needs evolve.
These detailed insights underscore the critical importance of ball bearing conveyor rollers in industrial conveyor systems, highlighting their role in optimizing operations and facilitating growth.
Types of Ball Bearing Conveyor Rollers
There are various types of ball bearing conveyor rollers available, each designed to meet specific industrial requirements. This section will provide an in-depth analysis of three types: standard ball conveyor rollers, roller ball transfer bearings, and heavy-duty ball transfer bearings. Each type serves a unique purpose in facilitating material handling and improving overall system efficiency.
Standard Ball Conveyor Rollers
Standard ball conveyor rollers are the most commonly used type in conveyor systems, ideal for general-purpose applications. They consist of cylindrical rollers containing ball bearings, designed for efficient transport across a wide range of industries.
- Load Capacity: They offer moderate load capacities, suitable for handling medium-weight materials across diverse industries like packaging and manufacturing.
- Construction Materials: These rollers are often constructed with stainless steel, aluminum, or plastic, chosen based on the specific material being transported.
- Ease of Installation: Their straightforward design allows for quick installation and replacement, minimizing system downtime.
- Sealed Bearings: The use of sealed bearings ensures protection from dust and debris, prolonging the roller’s lifespan.
- Operational Flexibility: Standard rollers are versatile, compatible with various conveyor systems and adaptable to different production lines.
- Friction Reduction: Ball bearings reduce friction, enabling smoother and quieter operation for seamless movement of goods.
- Energy Efficiency: Their efficient design minimizes the required driving force, helping reduce energy costs.
- Customization: They are available in various sizes and finishes, allowing customization to fit specific conveyor systems.
Roller Ball Transfer Bearings
Roller ball transfer bearings differ from standard rollers by featuring a spherical ball that allows for omnidirectional movement, making them ideal for transfer tables and conveyor systems where goods need to change direction frequently.
- 360-Degree Movement: The spherical ball structure enables movement in any direction, simplifying material handling across transfer tables and junctions.
- Low Friction: Ball bearings inside these rollers minimize friction, allowing for effortless directional changes.
- Load Versatility: They can accommodate light to moderate loads, supporting diverse materials across multiple applications.
- Material Compatibility: Available in corrosion-resistant materials like stainless steel, they handle various materials, including fragile and sensitive products.
- Compact Design: Their compact structure allows for integration into tight spaces and existing conveyor systems.
- Improved Handling: These rollers enhance product handling where precise movement and orientation changes are needed.
- Reduced Wear and Tear: The smooth movement provided reduces abrasion on both the product and conveyor surface, ensuring durability.
- Transfer Efficiency: They streamline transitions between conveyor lines or onto workbenches, improving overall productivity.
Heavy Duty Ball Transfer Bearings
Heavy-duty ball transfer bearings are engineered for high-load applications, offering robust performance in industries that require the transport of extremely heavy materials, such as automotive and heavy machinery manufacturing.
- Load Capacity: Designed to withstand significantly high loads, they provide reliable support for transporting heavy machinery and automotive parts.
- Durability: Their rugged construction ensures long-term durability, even under continuous, demanding usage.
- Corrosion Resistance: Often made from corrosion-resistant materials, these bearings withstand harsh environmental conditions.
- Shock Absorption: Their ability to absorb shocks and impacts ensures secure movement of bulky items.
- Omnidirectional Movement: Like roller ball transfer bearings, these allow for omnidirectional movement, which is crucial in positioning large, cumbersome items.
- Low Maintenance: Their durable design requires minimal maintenance, reducing overall operational downtime.
- Specialized Construction: They feature reinforced housing to prevent deformation under pressure, maintaining optimal performance.
- Adaptability: Heavy-duty ball transfer bearings can be customized to fit specific industrial requirements, offering tailored solutions to unique challenges.
Each of these ball bearing conveyor rollers provides unique benefits to conveyor systems, ensuring seamless and efficient handling of materials in diverse applications.
Key Features of Ball Bearing Conveyor Rollers
Ball bearing conveyor rollers are essential components in the effective operation of conveyor systems across various industries. These rollers leverage advanced engineering to maximize efficiency and reliability in handling materials. This section highlights ten critical features of ball bearing conveyor rollers, detailing the materials used, design elements, and performance characteristics that make them indispensable in industrial applications.
- Material Composition: Typically made from robust materials like stainless steel, carbon steel, and durable plastics, these rollers offer excellent resistance to corrosion and wear.
- Design Variations: Available in different shapes such as cylindrical, tapered, and spherical, each design addresses specific operational needs, affecting load distribution and handling efficiency.
- Load Capacity: Ball bearing conveyor rollers are built to support varying weights, making them versatile for use from light packaging to heavy industrial loads.
- Friction Reduction: Internal ball bearings significantly reduce friction, facilitating smoother and more efficient operation, which prolongs the life of both the rollers and the conveyor belt.
- Durability: Designed for durability, these rollers often feature sealed bearings to shield against dust, debris, and other contaminants.
- Corrosion Resistance: With materials chosen for their endurance against corrosive environments, these rollers are suitable for a wide range of industrial conditions.
- Noise Reduction: The reduction in mechanical friction not only extends the operational life of the rollers but also decreases noise levels, enhancing the work environment.
- Energy Efficiency: Lower friction levels translate to reduced energy requirements for the conveyor system, thereby decreasing operational costs.
- Ease of Maintenance: The straightforward design of these rollers allows for easy maintenance and replacement, minimizing downtime and maintaining productivity.
- Customization: Flexibility in customization allows these rollers to be tailored to specific requirements, including size, bearing type, and material, ensuring optimal integration and performance.
Ball bearing conveyor rollers are pivotal in optimizing the performance and efficiency of conveyor systems. Their engineered features address a multitude of industrial demands, enhancing durability, reducing operational costs, and improving overall system reliability. Understanding these features helps in selecting the right rollers for specific applications, ensuring that conveyor systems operate at their best.
Applications of Ball Bearing Conveyor Rollers
Ball bearing conveyor rollers are utilized in various configurations across industrial settings due to their versatility and efficiency. This section explores the key applications where these rollers provide optimal performance, including ball transfer table conveyors, mini ball transfer bearings, and ball transfer conveyor strips.
Ball Transfer Table Conveyor
Ball transfer table conveyors are specialized for managing items that require multidirectional movement or rotation. They consist of a grid of ball bearing conveyor rollers arranged in a table-like layout.
- Material Handling: Ideal for moving boxes, crates, and other containers in logistics and warehousing environments where items need to change direction frequently.
- Inspection Stations: Often used at quality control or inspection points where products are examined from multiple angles.
- Assembly Lines: Useful in assembly operations that require precise positioning and rotation of components before the next stage.
- Loading and Unloading: Perfect for efficiently loading or unloading materials onto conveyor belts or workstations.
- Warehouse Sorting: Streamlines sorting systems by allowing goods to be redirected to different conveyor lines.
- Large Format Printing: Facilitates the handling of printed materials that need to be moved with care to avoid damage.
- Work Benches: Provides the ability to position items conveniently for workers to assemble or process.
- Airport Baggage: Ball transfer tables help in directing baggage to the appropriate conveyor lines.
Mini Ball Transfer Bearings
Mini ball transfer bearings are smaller versions designed for precision and low-weight applications.
- Electronic Assembly: Useful in handling small electronic components that require careful positioning during assembly.
- Optical Equipment Manufacturing: Supports delicate optical instruments that must be handled gently and accurately.
- Pharmaceutical Packaging: Ensures smooth transport of packaged pharmaceutical products without damaging their integrity.
- Jewelry Manufacturing: Ideal for placing and moving tiny jewelry pieces between workstations.
- Laboratory Equipment: Provides reliable handling of small lab equipment requiring careful orientation and minimal contamination.
- Model Making: Assists in the accurate movement of delicate model pieces.
- Robotics: Plays a role in positioning lightweight robotic components on assembly lines.
- Automotive Electronics: Supports the careful placement of automotive electronics during production.
Ball Transfer Conveyor Strips
Ball transfer conveyor strips are modular sections that contain rows of ball bearing conveyor rollers, offering versatility in integrating with existing systems.
- Streamlined Integration: These strips are designed to be incorporated into existing conveyor systems, simplifying upgrades and system expansion.
- Sorting Efficiency: Helps in quickly rerouting products in sorting systems to different lines or processing areas.
- Packaging Lines: Facilitates the smooth movement of goods in packaging operations, where items are often redirected.
- Warehouse Operations: Enhances the flexibility of warehouse operations by offering adaptable layouts for various products.
- Manufacturing Workflow: Assists in optimizing manufacturing workflows by redirecting products efficiently between workstations.
- Maintenance-Friendly: The modular design allows for easy removal or replacement, reducing downtime.
- Custom Layouts: The strips can be arranged in custom layouts to meet unique material-handling requirements.
- Flexible Expansion: Allows for the simple addition of new sections to accommodate changing production needs.
The applications of ball bearing conveyor rollers are diverse and indispensable in modern industrial workflows, significantly enhancing productivity and operational efficiency across different sectors.
Buying Guide: Ball Bearing Conveyor Rollers
When it comes to optimizing your conveyor system, selecting the right ball bearing conveyor rollers is crucial. This buying guide will assist you in navigating the complexities of purchasing these components, comparing the advantages and disadvantages of new versus used rollers, examining the factors that influence pricing, and providing insights on the best places to purchase these essential items.
New vs. Used Ball Bearing Conveyor Rollers
Choosing between new and used ball bearing conveyor rollers involves assessing cost, performance, and operational needs. Below is a detailed comparison to help you make an informed decision:
Factors Affecting Price
The cost of ball bearing conveyor rollers can vary widely based on several key factors. Understanding these can help you budget more effectively:
- Material Quality: Premium materials command higher prices but offer better durability and performance.
- Load Capacity: Enhanced load-bearing capabilities typically increase the cost due to more robust construction.
- Bearings: The type and precision of bearings used directly affect the price, with higher-end bearings costing more.
- Customization: Specific modifications for your conveyor system needs can lead to higher costs.
- Quantity: Purchasing in bulk can often secure you a discount, whereas smaller orders might have a higher per-unit cost.
- Sealing Technology: Advanced sealing against contaminants increases the longevity of rollers but also the price.
- Coating: Special coatings that protect against corrosion or wear are an additional cost.
- Brand Reputation: Established brands with proven reliability may charge more but also offer greater peace of mind.
Where to Buy
Selecting where to buy ball bearing conveyor rollers can significantly affect the quality and cost-effectiveness of your purchase:
- Industrial Equipment Suppliers: These suppliers often have a wide selection, offering both new and used options.
- Manufacturer Direct: Purchasing directly can ensure you get exactly what you need and can include technical support.
- Online Marketplaces: Platforms like Alibaba or Amazon provide extensive listings but require careful vetting of suppliers.
- Surplus Equipment Stores: These can be a goldmine for budget-conscious shoppers looking for used options.
- Specialty Conveyor Companies: Experts in conveyor technology can offer tailored advice and specialized products.
- Auctions: Keep an eye on industrial auctions for potential bargains.
- Refurbished Equipment Sellers: These sellers provide a middle ground between new and used, offering refurbished rollers at reduced prices.
By considering each of these aspects and sources, you can make a well-informed decision that balances cost with operational requirements, ensuring you invest wisely in your conveyor system’s efficiency and longevity.
Maintenance and Care of Ball Bearing Conveyor Rollers
Proper maintenance and effective troubleshooting are key to maximizing the lifespan and efficiency of ball bearing conveyor rollers. This guide details essential maintenance practices and common troubleshooting steps to help ensure your conveyor system operates reliably and efficiently.
Routine Maintenance Tips
Routine maintenance of ball bearing conveyor rollers is critical to prevent premature wear and ensure continuous, efficient operation. Here are several key practices that should be part of your regular maintenance schedule:
- Regular Cleaning: Clean rollers to remove dust and debris that can accumulate and impair functionality. Use appropriate cleaning agents that do not degrade the material of the rollers or bearings.
- Lubrication: Consistent lubrication reduces friction and wear on the bearings. Use lubricants that are suitable for the type of bearings and the operational environment of the conveyor.
- Visual Inspection: Regularly inspect the rollers for signs of wear such as cracks, rust, or misalignment. Early detection of these issues can prevent more serious problems.
- Alignment Checks: Ensure that rollers are properly aligned with the conveyor framework to prevent uneven wear and tear. Misalignment can lead to increased resistance and operational inefficiency.
- Bearing Seals Inspection: Examine the seals on bearings for any signs of deterioration or leakage. Compromised seals can allow contaminants to enter and damage the bearings.
- Load Capacity Monitoring: Continuously monitor the load being placed on the conveyor to avoid overloading, which can stress rollers and lead to failures.
- Tightening Mounting Bolts: Check and tighten any loose mounting bolts and components that secure the rollers to the conveyor frame. This helps maintain stability and alignment.
- Vibration Monitoring: Use vibration detection tools to monitor abnormal vibrations that can indicate issues like bearing failures or alignment problems.
Troubleshooting Common Issues
Even with meticulous maintenance, issues may arise with ball bearings for conveyor rollers. Understanding how to troubleshoot common problems can help quickly restore functionality and minimize downtime.
- Excessive Noise: This can be indicative of poor lubrication or debris caught in the bearings. Re-lubricate and clean the rollers thoroughly. Check for wear and replace bearings if necessary.
- Roller Sticking: Debris accumulation, rust, or insufficient lubrication can cause rollers to stick. Clean the affected area and apply lubricant. Consider replacing the roller if the issue persists.
- Uneven Wear: If rollers wear unevenly, it often points to misalignment or an unevenly distributed load. Adjust the alignment and redistribute the load evenly across the conveyor.
- Bearing Failure: Bearings may fail due to overloading, insufficient lubrication, or contamination. Replace damaged bearings immediately to prevent further damage to the roller system.
- Rust or Corrosion: Check for environmental factors contributing to rust, such as moisture or chemicals. Applying corrosion-resistant coatings and improving storage conditions can help mitigate this issue.
- Reduced Speed: If the conveyor slows down, check for friction issues due to inadequate lubrication or mechanical obstructions. Clean and lubricate the affected areas.
- Loosened Fasteners: Regularly inspect and tighten any loosened bolts and fasteners to ensure the stability and proper alignment of the rollers.
By adhering to these maintenance and troubleshooting guidelines, you can effectively maintain and enhance the performance of your ball bearing conveyor rollers, ensuring they remain a reliable component of your industrial operations.
FAQs about Ball Bearing Conveyor Rollers
Roller bearings and ball bearings are two distinct types of bearings that handle load differently. Roller bearings use cylindrical rollers, providing a larger contact area that allows them to handle heavy radial loads and some axial loads. Due to this broader contact, roller bearings can withstand greater forces in demanding applications like heavy machinery. They are less effective, however, for high-speed rotations due to increased friction.
Ball bearings, on the other hand, use spherical balls to reduce friction between moving parts. Their small contact points with races make them better suited for high-speed rotations because they generate less friction and heat. They are more appropriate for applications where speed is crucial but can also handle some axial and radial loads. Ultimately, the choice between roller and ball bearings depends on the specific needs of the machinery, such as load type, speed, and operational environment.
A tapered roller bearing uses conical rollers that are angled, allowing them to accommodate both radial and axial loads efficiently. The design of tapered roller bearings ensures that the rollers maintain contact with both the inner and outer raceways. This configuration makes them suitable for applications where combined loads (both axial and radial) are present, such as in automotive wheel hubs, where the bearing must withstand the axial force when cornering.
Ball bearings, in contrast, consist of spherical balls and are primarily designed for applications where rotational speed is paramount. Their smaller contact points with the bearing races reduce friction and allow for high-speed rotations. However, ball bearings are less capable of handling heavy loads compared to tapered roller bearings, especially in applications where high axial loads are expected.
Ball bearings excel in high-speed applications due to their lower friction and heat generation. They are ideal for applications requiring smooth and rapid motion, like electric motors, hard drives, and high-speed fans. Their ability to handle light to moderate radial loads also makes them suitable for various precision instruments and tools.
Roller bearings are better suited for handling heavy radial loads in slower-speed applications due to their larger contact area with the bearing races. They are typically used in industries involving heavy machinery like mining, construction, and agriculture. Additionally, roller bearings are advantageous in gearboxes, conveyor belts, and mechanical presses, where strength and durability are essential.
Ball bearings are used in wheels due to their ability to reduce friction between the wheel and axle while ensuring smooth and consistent rotation. They have spherical balls that contact both the inner and outer raceways, providing high-speed capabilities essential for rotating wheels. This design allows them to handle the combination of radial and axial forces typically encountered in wheels, such as during acceleration, braking, and cornering.
In addition to their speed and friction-reduction benefits, ball bearings are relatively compact and can fit into smaller wheel assemblies. Their efficiency makes them suitable for bicycles, skateboards, and various motor vehicles where maintaining speed and reducing rolling resistance are crucial for performance. Overall, ball bearings ensure that wheels spin smoothly, enabling a better driving or riding experience.
Last Updated on May 20, 2024 by Jordan Smith
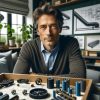
Jordan Smith, a seasoned professional with over 20 years of experience in the conveyor system industry. Jordan’s expertise lies in providing comprehensive solutions for conveyor rollers, belts, and accessories, catering to a wide range of industrial needs. From initial design and configuration to installation and meticulous troubleshooting, Jordan is adept at handling all aspects of conveyor system management. Whether you’re looking to upgrade your production line with efficient conveyor belts, require custom conveyor rollers for specific operations, or need expert advice on selecting the right conveyor accessories for your facility, Jordan is your reliable consultant. For any inquiries or assistance with conveyor system optimization, Jordan is available to share his wealth of knowledge and experience. Feel free to reach out at any time for professional guidance on all matters related to conveyor rollers, belts, and accessories.