Essential Komponen Conveyor for Belt Conveyor Batubara
The belt conveyor batubara system comprises several essential components, each playing a critical role in its operation. These parts include the conveyor belt, which transports the batubara, and pulleys that guide and support the belt. Idlers are used to support the belt and maintain its alignment, while the drive unit provides the necessary power to move the belt. Additionally, the take-up unit ensures proper tension in the belt. Understanding these components and their functions is crucial for the efficient operation and maintenance of a belt conveyor batubara system.
Essential Komponen Conveyor for Belt Conveyor Batubara
Belt conveyor systems are critical in the efficient transportation of bulk materials, and nowhere is this more evident than in the coal industry, particularly with belt conveyor batubara systems. The term belt conveyor batubara refers to conveyor systems specifically designed for the coal industry (batubara means coal in Indonesian), highlighting their importance in this sector. In this detailed analysis, we will explore the essential components of a belt conveyor batubara system, their functions, and their contributions to the overall efficiency of coal handling operations.
Belt conveyor batubara systems are employed extensively in coal mining and processing plants for the efficient transportation of coal from mines to processing units, storage areas, and shipping facilities. These systems are preferred due to their ability to handle large volumes of coal efficiently, reduce operational costs, and minimize environmental impact. The effectiveness of these systems hinges on various critical components, each playing a vital role in ensuring smooth, efficient, and reliable operations.
1. Conveyor Belts
Description
The conveyor belt is the central component of any conveyor system. It is a continuous loop of material that moves around rollers and pulleys to transport materials from one point to another. In belt conveyor batubara systems, these belts are typically made of materials that are resistant to wear and tear, capable of withstanding heavy loads, and designed to operate in harsh environmental conditions.
Importance in Belt Conveyor Batubara
In coal handling, the conveyor belt must be capable of transporting large quantities of coal without significant wear. The belt material often includes a combination of rubber and steel cords to provide the necessary strength and durability. Additionally, the belt surface must be designed to resist the abrasive nature of coal, preventing damage and prolonging the belt’s lifespan.
2. Idlers and Rollers
Description
Idlers and rollers are the components that support the conveyor belt and help reduce friction. Idlers are sets of rollers that are spaced along the length of the conveyor to provide support to the belt and the material being transported.
Importance in Belt Conveyor Batubara
For belt conveyor batubara systems, idlers and rollers must be robust and capable of supporting the heavy loads of coal. They play a crucial role in maintaining the belt’s alignment and ensuring smooth movement, which is essential for preventing spillage and ensuring efficient operation. The idlers and rollers must also be designed to withstand the harsh conditions of coal mining environments, including exposure to dust, moisture, and heavy impacts.
3. Drive Units
Description
The drive unit is the component that powers the conveyor system. It consists of motors, gearboxes, and other mechanical components that work together to move the conveyor belt.
Importance in Belt Conveyor Batubara
In belt conveyor batubara systems, the drive unit must be powerful enough to handle the heavy loads and long distances typical in coal transportation. Reliable and efficient drive units ensure that the conveyor system operates smoothly and continuously, minimizing downtime and operational costs. The drive unit must also be designed for easy maintenance and long-term durability to withstand the challenging conditions of coal handling operations.
4. Pulleys
Description
Pulleys are used to change the direction of the conveyor belt and to tension the belt. There are two main types of pulleys: drive pulleys and tail pulleys. Drive pulleys are connected to the drive unit and provide the driving force for the belt, while tail pulleys are located at the opposite end and help to guide and tension the belt.
Importance in Belt Conveyor Batubara
Pulleys in belt conveyor batubara systems must be robust and designed to handle the high tension and heavy loads associated with coal transportation. They play a critical role in maintaining the proper tension of the belt, preventing slippage, and ensuring efficient power transmission from the drive unit to the belt. The pulleys must also be resistant to wear and corrosion, ensuring long-term reliability and performance.
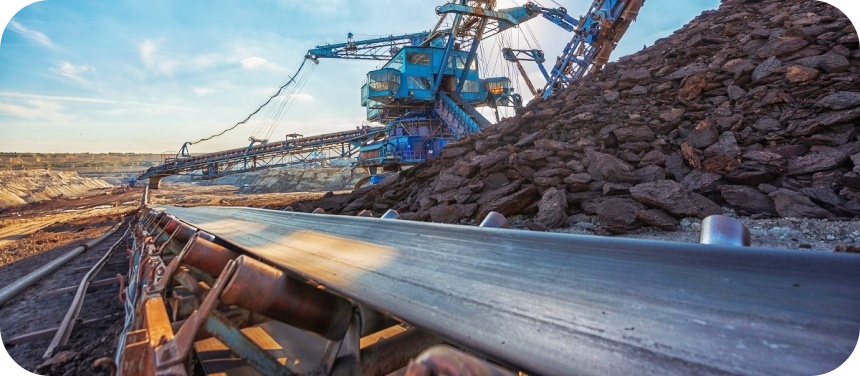
5. Conveyor Structure
Description
The conveyor structure is the framework that supports the entire conveyor system, including the belt, idlers, rollers, and drive units. It is typically made of steel and designed to provide the necessary strength and stability to support the heavy loads of coal.
Importance in Belt Conveyor Batubara
The conveyor structure in belt conveyor batubara systems must be strong and durable to support the significant weight of coal and the associated equipment. It must also be designed to withstand the harsh environmental conditions of coal mining and processing, including exposure to dust, moisture, and high temperatures. A well-designed conveyor structure ensures the stability and reliability of the entire conveyor system, minimizing the risk of structural failures and ensuring efficient coal handling operations.
6. Belt Cleaners
Description
Belt cleaners, also known as scrapers, are devices installed at various points along the conveyor belt to remove any material that sticks to the belt. They are essential for preventing material buildup on the belt, which can lead to inefficiencies and maintenance issues.
Importance in Belt Conveyor Batubara
In belt conveyor batubara systems, belt cleaners are crucial for maintaining the cleanliness and efficiency of the conveyor belt. Coal is a sticky and abrasive material that can easily adhere to the belt, causing buildup and potential damage. Belt cleaners help to prevent these issues by removing any residual material from the belt, ensuring smooth operation and reducing the need for frequent maintenance. Effective belt cleaners also help to minimize spillage and dust generation, contributing to a safer and more environmentally friendly operation.
7. Conveyor Controls and Monitoring Systems
Description
Conveyor controls and monitoring systems include the electronic and automated components that manage the operation of the conveyor system. These systems can include sensors, controllers, and software that monitor the performance of the conveyor, detect any issues, and optimize the operation.
Importance in Belt Conveyor Batubara
For belt conveyor batubara systems, effective controls and monitoring systems are essential for ensuring safe and efficient operation. These systems help to detect any potential issues, such as belt misalignment, excessive wear, or mechanical failures, allowing for timely maintenance and repairs. Advanced monitoring systems can also optimize the operation of the conveyor, improving efficiency and reducing energy consumption. By ensuring the reliable and efficient operation of the conveyor system, these controls and monitoring systems help to minimize downtime and operational costs.
8. Safety Devices
Description
Safety devices are critical components that ensure the safe operation of the conveyor system. These can include emergency stop buttons, safety guards, pull cords, and other safety mechanisms designed to protect workers and prevent accidents.
Importance in Belt Conveyor Batubara
Safety is paramount in belt conveyor batubara systems due to the high risks associated with coal handling. Safety devices help to protect workers from potential hazards, such as moving parts, high tension belts, and heavy loads. Emergency stop buttons and pull cords allow for quick shutdown of the conveyor system in case of an emergency, preventing accidents and injuries. Safety guards and other protective mechanisms help to prevent contact with dangerous parts of the conveyor, ensuring a safer working environment. By incorporating robust safety devices, belt conveyor batubara systems can operate more safely and efficiently, reducing the risk of accidents and ensuring compliance with safety regulations.
The essential components of a belt conveyor batubara system play a crucial role in the efficient and reliable transportation of coal. From the conveyor belt itself to the idlers, rollers, drive units, pulleys, and safety devices, each component contributes to the overall performance and efficiency of the system. By understanding the functions and importance of these components, operators can ensure the smooth and efficient operation of their belt conveyor batubara systems, minimizing downtime, reducing operational costs, and enhancing the safety and reliability of coal handling operations.
Conveyor Belt Technology in Belt Conveyor Batubara
In the realm of industrial applications, the belt conveyor batubara system stands out as a pivotal technology for the efficient handling and transportation of coal (batubara). These systems are integral to mining operations, particularly in coal mining, where they streamline the process of moving large quantities of coal from the mining site to the processing plants or loading facilities. The efficiency and reliability of these conveyor systems are crucial for the operational success of mining companies.
Latest Advancements in Belt Conveyor Batubara Systems
The field of belt conveyor batubara has seen significant technological advancements over recent years. These innovations are aimed at enhancing efficiency, safety, and environmental sustainability. Below are some of the latest advancements:
1. Intelligent Conveyor Systems
Modern belt conveyor batubara systems are increasingly incorporating intelligent technologies. These systems utilize advanced sensors, IoT (Internet of Things) devices, and data analytics to monitor and optimize the performance of the conveyor belts. Key benefits include:
- Real-time Monitoring: Sensors can detect various parameters such as belt speed, temperature, and vibration levels, providing real-time data that can be used to prevent breakdowns and ensure smooth operation.
- Predictive Maintenance: By analyzing the data collected from sensors, predictive maintenance can be implemented. This means that potential issues can be identified and addressed before they cause significant downtime.
- Automated Controls: Intelligent conveyor systems can automatically adjust the speed and tension of the belt, optimizing the system’s performance based on the load and operational conditions.
2. High-Durability Materials
The materials used in the construction of belt conveyor batubara systems have also evolved. Modern belts are made from high-durability materials such as reinforced rubber, PVC, and special synthetic compounds. These materials offer several advantages:
- Increased Longevity: Enhanced durability reduces the frequency of belt replacements, thereby lowering maintenance costs and minimizing downtime.
- Resistance to Wear and Tear: Advanced materials are more resistant to the abrasive nature of coal and other harsh materials, ensuring a longer service life.
- Improved Energy Efficiency: Lightweight and high-strength materials contribute to improved energy efficiency, reducing the power consumption of the conveyor system.
3. Energy-Efficient Motors and Drives
Energy efficiency is a critical consideration in the design of modern belt conveyor batubara systems. Innovations in motor and drive technology have led to significant improvements in this area:
- Variable Frequency Drives (VFDs): VFDs allow for precise control of the motor speed, enabling the conveyor to operate at optimal efficiency levels depending on the load and operational requirements.
- High-Efficiency Motors: The use of high-efficiency motors reduces energy consumption and operational costs. These motors are designed to deliver maximum performance with minimal energy input.
- Regenerative Drives: Some advanced conveyor systems incorporate regenerative drives, which can capture and reuse energy that would otherwise be lost during operation, further enhancing energy efficiency.
4. Enhanced Safety Features
Safety is paramount in the operation of belt conveyor batubara systems. Recent advancements have introduced several safety features designed to protect both the equipment and the personnel:
- Emergency Stop Mechanisms: Modern systems are equipped with multiple emergency stop mechanisms that can be activated in case of an anomaly or hazard.
- Fire-Resistant Belts: Given the flammable nature of coal, fire-resistant belts are critical. These belts are designed to withstand high temperatures and prevent the spread of fire.
- Advanced Alarm Systems: Intelligent conveyor systems often include sophisticated alarm systems that can detect potential hazards such as belt misalignment, overloading, and overheating, triggering alarms and automatic shutdowns to prevent accidents.
5. Environmental Considerations
Sustainability is a growing concern in the mining industry, and advancements in belt conveyor batubara technology reflect this trend. Efforts to minimize environmental impact include:
- Dust Suppression Systems: Modern conveyors are equipped with dust suppression systems that reduce the emission of coal dust, improving air quality and reducing health risks for workers.
- Noise Reduction Technologies: Noise pollution is a significant concern in mining operations. Advanced belt conveyor systems incorporate noise reduction technologies to minimize the sound levels generated during operation.
- Eco-Friendly Materials: The use of eco-friendly materials in the construction of conveyor belts and components reduces the environmental footprint of the mining operation.
Implementation Challenges and Solutions
While these advancements bring numerous benefits, the implementation of modern belt conveyor batubara systems also presents several challenges. Overcoming these challenges is essential for maximizing the effectiveness of the technology:
1. Integration with Existing Systems
Integrating new technologies with existing conveyor systems can be complex. Solutions include:
- Modular Upgrades: Implementing modular upgrades allows for the gradual integration of new technologies without disrupting ongoing operations.
- Compatibility Assessments: Conducting thorough compatibility assessments ensures that new components and technologies can be seamlessly integrated with existing systems.
2. Cost Considerations
The initial investment required for advanced conveyor systems can be significant. However, the long-term benefits often justify the cost. Strategies to manage costs include:
- Cost-Benefit Analysis: Performing detailed cost-benefit analyses helps in understanding the long-term savings and efficiency gains.
- Phased Implementation: Implementing the technology in phases can spread out the costs and allow for incremental improvements.
3. Training and Skill Development
The adoption of new technologies necessitates proper training and skill development for the workforce. Approaches to address this include:
- Comprehensive Training Programs: Implementing training programs that cover the operation, maintenance, and troubleshooting of advanced conveyor systems.
- Continuous Learning Opportunities: Providing continuous learning opportunities to keep the workforce updated with the latest technological advancements.
Future Trends in Belt Conveyor Batubara Technology
Looking ahead, several emerging trends are likely to shape the future of belt conveyor batubara systems. These trends include:
1. Integration with Industry 4.0
The integration of Industry 4.0 technologies, such as artificial intelligence (AI), machine learning, and blockchain, will further revolutionize belt conveyor batubara systems. These technologies will enhance predictive maintenance, optimize operational efficiency, and improve supply chain transparency.
2. Wireless and Remote Monitoring
The future of conveyor systems will likely see increased adoption of wireless and remote monitoring technologies. These advancements will enable real-time monitoring and control of conveyor operations from remote locations, enhancing flexibility and responsiveness.
3. Sustainability Initiatives
Sustainability will continue to drive innovations in conveyor belt technology. Future developments will focus on creating even more eco-friendly materials, reducing energy consumption, and minimizing the environmental impact of mining operations.
The advancements in belt conveyor batubara technology represent a significant leap forward in the efficiency, safety, and sustainability of coal transportation systems. From intelligent conveyor systems and high-durability materials to energy-efficient motors and enhanced safety features, these innovations are transforming the mining industry. While challenges in implementation remain, the long-term benefits of adopting these advanced technologies are undeniable. As the industry continues to evolve, the integration of emerging trends such as Industry 4.0 and sustainability initiatives will further enhance the capabilities and impact of belt conveyor batubara systems.
Maintenance Tips for Belt Conveyor Batubara Parts
Maintaining the components of a belt conveyor batubara system is crucial to ensure its longevity, efficiency, and safety. Given the demanding conditions of coal handling operations, regular maintenance can prevent costly downtime, reduce operational costs, and enhance the overall performance of the conveyor system. This section provides practical advice on how to maintain and extend the lifespan of various belt conveyor batubara parts.
1. Conveyor Belts
Regular Inspections
Conduct regular inspections to check for signs of wear and tear, such as fraying edges, cracks, and abnormal stretching. Inspections should be scheduled based on the usage frequency and operating conditions of the conveyor system.
Proper Tensioning
Ensure the conveyor belt is properly tensioned. A belt that is too tight can cause excessive wear on the pulleys and the belt itself, while a belt that is too loose can slip, reducing efficiency and causing misalignment. Regularly check and adjust the tension according to the manufacturer’s specifications.
Alignment
Maintain proper belt alignment to prevent uneven wear and tear. Misaligned belts can lead to material spillage and increased friction, causing premature wear. Use alignment tools and regularly monitor the belt’s tracking to ensure it stays centered on the conveyor.
Cleaning
Keep the conveyor belt clean to prevent material buildup, which can cause the belt to slip or run off track. Use appropriate belt cleaners and scrapers to remove coal dust and other residues. Regular cleaning will also reduce the risk of fire hazards and improve the belt’s lifespan.
2. Idlers and Rollers
Lubrication
Regularly lubricate the bearings of idlers and rollers to reduce friction and wear. Use the recommended type of lubricant and follow the manufacturer’s lubrication schedule. Over-lubrication can attract dust and debris, so apply the correct amount.
Inspection and Replacement
Inspect idlers and rollers for signs of damage, such as worn bearings, cracks, or dents. Replace any damaged components promptly to prevent further damage to the conveyor belt and other parts of the system. Pay particular attention to the return rollers, which are more prone to wear due to their position.
Cleaning
Keep idlers and rollers clean to ensure smooth operation. Remove any buildup of coal dust, debris, and other materials that can cause blockages or increased friction. Regular cleaning can help identify potential issues early and prevent major failures.
3. Drive Units
Regular Maintenance
Perform regular maintenance on drive units, including motors, gearboxes, and couplings. Check for signs of wear, overheating, or abnormal noises, which can indicate potential issues. Follow the manufacturer’s maintenance schedule and replace any worn or damaged parts promptly.
Lubrication
Ensure all moving parts within the drive unit are properly lubricated. Use the specified lubricants and adhere to the recommended lubrication intervals to prevent excessive wear and reduce the risk of mechanical failures.
Alignment and Tension
Check the alignment of the drive unit and ensure the belt is properly tensioned. Misalignment can cause increased wear on the belt and drive components, reducing efficiency and increasing the risk of breakdowns. Adjust the alignment and tension as needed to maintain optimal performance.
4. Pulleys
Inspection
Regularly inspect pulleys for signs of wear and damage. Look for cracks, grooves, or other deformities that can affect the performance of the conveyor system. Pay special attention to the lagging on the drive pulleys, as it can wear down over time and reduce traction.
Alignment
Ensure pulleys are properly aligned to prevent uneven wear on the conveyor belt and reduce the risk of belt slippage. Use alignment tools and regularly check the pulleys’ position to maintain correct alignment.
Cleaning
Clean pulleys to remove any buildup of coal dust and other materials that can cause slippage and reduce efficiency. Regular cleaning will help maintain proper traction and prolong the life of the pulleys and the belt.
5. Conveyor Structure
Structural Integrity
Regularly inspect the conveyor structure for signs of damage or wear. Check for cracks, rust, and loose bolts that can compromise the stability and safety of the conveyor system. Repair or replace any damaged components promptly to prevent further issues.
Cleaning and Painting
Keep the conveyor structure clean and free from debris. Regularly remove coal dust and other materials that can accumulate and cause corrosion. Apply a protective coating or paint to prevent rust and extend the life of the structure.
Load Management
Ensure the conveyor system is not overloaded, as excessive weight can strain the structure and cause damage. Follow the manufacturer’s load capacity guidelines and regularly monitor the load to prevent overloading.
6. Belt Cleaners
Regular Maintenance
Perform regular maintenance on belt cleaners to ensure they are functioning correctly. Inspect the blades for wear and replace them when necessary. Adjust the tension of the cleaners to maintain optimal contact with the conveyor belt.
Cleaning
Clean the belt cleaners regularly to remove any material buildup that can affect their performance. Ensure the cleaner blades are free from debris and coal dust to maintain efficient operation.
Alignment
Check the alignment of belt cleaners to ensure they are positioned correctly and making proper contact with the belt. Misaligned cleaners can cause uneven wear on the belt and reduce cleaning efficiency.
7. Conveyor Controls and Monitoring Systems
Calibration
Regularly calibrate sensors and monitoring equipment to ensure accurate readings and efficient operation. Incorrect readings can lead to improper adjustments and potential system failures.
Software Updates
Keep the software of monitoring systems up to date to take advantage of the latest features and improvements. Regular updates can enhance the efficiency and reliability of the conveyor system.
Inspection and Testing
Regularly inspect and test the controls and monitoring systems to ensure they are functioning correctly. Identify and address any issues promptly to prevent system failures and downtime.
8. Safety Devices
Regular Testing
Test safety devices regularly to ensure they are working correctly. This includes emergency stop buttons, pull cords, and safety guards. Regular testing can prevent accidents and ensure a safe working environment.
Maintenance
Perform routine maintenance on safety devices to keep them in good working condition. Replace any worn or damaged components to maintain the effectiveness of the safety systems.
Training
Ensure that all personnel are trained in the proper use and maintenance of safety devices. Regular training can prevent accidents and ensure that everyone is aware of the safety procedures.
Effective maintenance of belt conveyor batubara parts is essential for the efficient and safe operation of coal handling systems. By following these practical maintenance tips, operators can extend the lifespan of their conveyor components, reduce operational costs, and minimize downtime. Regular inspections, proper lubrication, alignment, and cleaning are crucial for maintaining the efficiency and reliability of belt conveyor batubara systems. Additionally, maintaining and testing safety devices ensure a safe working environment, preventing accidents and ensuring compliance with safety regulations. Through diligent maintenance practices, the performance and longevity of belt conveyor batubara systems can be significantly enhanced, contributing to the overall success of coal handling operations.
Belt Conveyor Batubara: Innovations in Conveyor Belt Technology for Batubara Handling
Belt conveyor batubara systems have long been the backbone of coal mining operations, providing an efficient and reliable means of transporting coal from mining sites to processing facilities. With the continuous advancement of technology, new innovations are being integrated into these systems, significantly enhancing their performance, safety, and environmental sustainability. This section delves into the cutting-edge technologies designed specifically for batubara handling, highlighting their impact on the industry.
Advanced Materials and Design
The materials used in belt conveyor batubara systems have evolved significantly. Traditional rubber belts are being replaced or supplemented by advanced composite materials that offer greater durability and performance. Some of the key innovations include:
1. Composite Conveyor Belts
Composite materials, such as aramid fibers combined with rubber or PVC, are being used to create conveyor belts that are lighter, stronger, and more durable. These materials provide several advantages:
- Enhanced Durability: Composite belts have a higher resistance to wear and tear, making them ideal for the abrasive nature of coal.
- Reduced Maintenance Costs: The increased lifespan of composite belts translates to lower maintenance costs and reduced downtime.
- Energy Efficiency: Lighter belts require less energy to move, contributing to overall energy savings in the operation.
2. Self-Cleaning Belts
Self-cleaning conveyor belts are another significant innovation in belt conveyor batubara systems. These belts are designed with special features that prevent the accumulation of coal dust and debris, thereby reducing the need for frequent cleaning and maintenance. Benefits include:
- Improved Efficiency: Self-cleaning belts maintain optimal performance by reducing the build-up of materials that can cause slippage or belt misalignment.
- Enhanced Safety: By minimizing coal dust accumulation, these belts also reduce the risk of fires and explosions, enhancing overall safety.
Smart Conveyor Systems
The integration of smart technology into belt conveyor batubara systems represents a major leap forward in operational efficiency and safety. These systems leverage the Internet of Things (IoT), artificial intelligence (AI), and advanced sensors to create intelligent, automated conveyor solutions.
1. IoT-Enabled Sensors
IoT-enabled sensors play a crucial role in modern conveyor systems by providing real-time data on various operational parameters such as belt speed, tension, and load distribution. Key benefits include:
- Real-Time Monitoring: Operators can monitor the conveyor system in real-time, allowing for immediate detection and resolution of any issues.
- Predictive Maintenance: By analyzing data trends, predictive maintenance can be implemented, identifying potential failures before they occur and reducing unexpected downtime.
- Optimized Performance: IoT sensors help optimize the performance of the conveyor system by adjusting operational parameters based on real-time data.
2. Artificial Intelligence and Machine Learning
AI and machine learning technologies are being used to enhance the decision-making processes in belt conveyor batubara systems. These technologies can analyze vast amounts of data and provide actionable insights to improve efficiency and safety.
- Anomaly Detection: AI algorithms can detect anomalies in the conveyor system’s operation, such as unusual vibrations or temperature changes, which may indicate potential issues.
- Optimized Maintenance Scheduling: Machine learning models can predict the optimal times for maintenance based on historical data, ensuring that maintenance activities are performed only when necessary.
- Operational Efficiency: AI can optimize the conveyor system’s performance by adjusting operational parameters in real-time, leading to improved efficiency and reduced energy consumption.
Enhanced Safety Features
Safety is a paramount concern in the operation of belt conveyor batubara systems. Innovations in safety technology are designed to protect both the equipment and the personnel working in coal handling operations.
1. Fire Detection and Suppression Systems
Given the flammable nature of coal, advanced fire detection and suppression systems are essential. These systems include:
- Infrared and Thermal Cameras: These cameras can detect heat anomalies that may indicate the presence of a fire, allowing for early intervention.
- Automated Suppression Systems: In the event of a fire, automated suppression systems can quickly deploy fire retardants to contain and extinguish the flames, minimizing damage and risk to personnel.
2. Emergency Stop Systems
Modern conveyor systems are equipped with sophisticated emergency stop mechanisms that can halt the conveyor in the event of a hazard. Features include:
- Multiple Stop Points: Emergency stop buttons are strategically placed along the conveyor system, ensuring that personnel can quickly and easily stop the conveyor in an emergency.
- Automated Shutdown Procedures: In the event of a critical failure, the system can automatically initiate a shutdown procedure to prevent further damage and ensure the safety of personnel.
Environmental Innovations
Sustainability is an increasingly important aspect of modern industrial operations. Innovations in belt conveyor batubara technology are aimed at reducing the environmental impact of coal handling and transportation.
1. Dust Control Systems
Coal dust can pose significant environmental and health risks. Advanced dust control systems are designed to minimize dust generation and dispersion.
- Dust Suppression Sprays: These systems use water or chemical sprays to suppress dust at critical points along the conveyor system, such as loading and unloading areas.
- Enclosed Conveyors: Fully enclosed conveyor systems prevent dust from escaping into the environment, reducing air pollution and protecting worker health.
2. Noise Reduction Technologies
Noise pollution is another concern in mining and coal handling operations. Innovations in noise reduction technology help mitigate this issue.
- Acoustic Barriers: Acoustic barriers can be installed around conveyor systems to absorb and deflect noise, reducing the overall noise levels in the surrounding environment.
- Quiet Conveyor Components: The use of quieter motors, bearings, and other components helps reduce the noise generated by the conveyor system, creating a more pleasant working environment.
Future Trends in Belt Conveyor Batubara Technology
Looking to the future, several trends are likely to shape the development of belt conveyor batubara systems, further enhancing their efficiency, safety, and environmental performance.
1. Autonomous Conveyor Systems
Autonomous conveyor systems, capable of self-regulating and self-maintaining, are on the horizon. These systems will leverage advanced AI and robotics to perform routine maintenance tasks, detect and resolve issues autonomously, and optimize operational efficiency without human intervention.
2. Blockchain for Supply Chain Transparency
Blockchain technology has the potential to revolutionize the supply chain management of coal handling operations. By providing a transparent and immutable record of all transactions and movements, blockchain can enhance traceability, reduce fraud, and improve the overall efficiency of the supply chain.
3. Green Technologies
The push for sustainability will drive the adoption of green technologies in belt conveyor batubara systems. Future innovations may include the use of renewable energy sources to power conveyor systems, further reducing their environmental footprint.
The innovations in conveyor belt technology for batubara handling are transforming the coal mining industry, providing more efficient, safer, and environmentally sustainable solutions. From advanced materials and smart technologies to enhanced safety features and environmental innovations, these advancements are setting new standards for belt conveyor batubara systems. As the industry continues to evolve, embracing these cutting-edge technologies will be crucial for maintaining competitive advantage and meeting the growing demands for sustainability and efficiency in coal handling operations. The future of belt conveyor batubara looks promising, with ongoing developments poised to deliver even greater benefits for the industry and the environment.
Troubleshooting Common Issues with Belt Conveyor Batubara Parts
Belt conveyor batubara systems are crucial in coal mining operations, ensuring efficient transportation of coal from extraction sites to processing facilities. However, like any mechanical system, they are prone to various issues that can disrupt operations and reduce efficiency. This section provides a comprehensive guide to identifying and solving common problems associated with belt conveyor batubara parts, ensuring the system operates smoothly and efficiently.
Common Issues with Belt Conveyor Batubara Parts
1. Belt Misalignment
Belt misalignment is a frequent problem in belt conveyor batubara systems, leading to uneven wear, increased energy consumption, and potential damage to the conveyor structure.
- Causes: Misalignment can be caused by improper installation, uneven loading, or worn-out idlers and pulleys.
- Identification: Signs of misalignment include visible belt edge wear, belts running off-center, and unusual noises from the conveyor.
- Solutions:
- Regular Inspections: Conduct routine inspections to ensure that all components are aligned correctly.
- Adjust Tracking: Adjust the tracking of the belt using the appropriate take-up and adjustment mechanisms.
- Replace Worn Parts: Replace worn-out idlers, pulleys, and other components that may cause misalignment.
2. Belt Slippage
Belt slippage occurs when the belt slips on the drive pulley, resulting in reduced efficiency and increased wear.
- Causes: Slippage can be due to insufficient tension, worn drive pulleys, or an overloaded conveyor system.
- Identification: Symptoms of belt slippage include a noticeable drop in belt speed, increased wear on the drive pulley, and burnt rubber smell.
- Solutions:
- Increase Tension: Adjust the tensioning mechanism to ensure the belt has adequate tension.
- Check Pulley Lagging: Ensure that the drive pulley has sufficient lagging to increase friction between the belt and the pulley.
- Avoid Overloading: Do not exceed the conveyor’s capacity, as overloading can lead to slippage.
3. Excessive Wear and Tear
Excessive wear and tear on the belt and other components can lead to frequent breakdowns and high maintenance costs.
- Causes: Continuous exposure to abrasive materials, improper tension, and misalignment are common causes of excessive wear.
- Identification: Signs include visible wear on the belt surface, frequent breakdowns, and increased maintenance requirements.
- Solutions:
- Use Durable Materials: Opt for high-durability materials such as reinforced rubber or synthetic compounds for the belt.
- Proper Maintenance: Implement a regular maintenance schedule to check and replace worn parts.
- Correct Installation: Ensure that the belt is properly installed and aligned to minimize wear.
4. Material Spillage
Material spillage can lead to waste, environmental concerns, and additional cleanup costs.
- Causes: Spillage is often caused by improper loading, excessive belt speed, or misaligned belts.
- Identification: Visible accumulation of material around the conveyor system and reduced material delivery efficiency.
- Solutions:
- Adjust Loading Procedures: Ensure that the material is loaded onto the center of the belt to prevent spillage.
- Control Belt Speed: Adjust the belt speed to match the material flow rate.
- Install Skirts and Seals: Use skirts and seals along the conveyor to contain the material and prevent spillage.
5. Belt Breakage
Belt breakage is a severe issue that can lead to significant downtime and repair costs.
- Causes: Overloading, excessive wear, and improper splicing techniques are common causes of belt breakage.
- Identification: Signs include visible damage or cuts on the belt, sudden stoppages, and unusual noises.
- Solutions:
- Proper Splicing: Use correct splicing techniques and materials to join belt ends.
- Avoid Overloading: Ensure that the conveyor is not overloaded beyond its designed capacity.
- Regular Inspections: Conduct regular inspections to identify and address any signs of wear or damage early.
Advanced Troubleshooting Techniques
To enhance the troubleshooting process for belt conveyor batubara systems, advanced techniques and tools can be employed.
1. Condition Monitoring Systems
Condition monitoring systems use sensors and data analytics to continuously monitor the health of the conveyor system.
- Vibration Analysis: Sensors detect unusual vibrations that may indicate misalignment or worn components.
- Temperature Monitoring: Monitoring the temperature of bearings and drive motors can help detect overheating issues.
- Ultrasonic Testing: Ultrasonic sensors can detect wear and tear on components such as idlers and pulleys.
2. Predictive Maintenance
Predictive maintenance leverages data from condition monitoring systems to predict potential failures before they occur.
- Data Analytics: Analyze data trends to identify patterns that may indicate impending issues.
- Scheduled Maintenance: Plan maintenance activities based on the predicted lifespan of components, reducing unexpected downtime.
3. Automated Troubleshooting Tools
Automated troubleshooting tools can quickly diagnose and resolve issues with minimal human intervention.
- Automated Inspection Drones: Drones equipped with cameras and sensors can inspect conveyor systems in hard-to-reach areas.
- Automated Alignment Systems: These systems use sensors and actuators to automatically align the belt, reducing the need for manual adjustments.
Best Practices for Maintenance and Troubleshooting
Implementing best practices for maintenance and troubleshooting can significantly enhance the reliability and efficiency of belt conveyor batubara systems.
1. Regular Inspections
Conducting regular inspections is crucial to identifying and addressing issues before they escalate.
- Visual Inspections: Regularly check for signs of wear, misalignment, and damage.
- Scheduled Audits: Perform comprehensive audits of the entire conveyor system at scheduled intervals.
2. Comprehensive Training
Ensuring that maintenance personnel are well-trained in troubleshooting techniques and best practices is essential.
- Training Programs: Implement training programs to educate staff on common issues and advanced troubleshooting techniques.
- Hands-On Experience: Provide hands-on training to allow personnel to gain practical experience in diagnosing and resolving issues.
3. Maintenance Scheduling
Implementing a structured maintenance schedule helps in maintaining the system’s health and performance.
- Preventive Maintenance: Schedule regular preventive maintenance activities to address potential issues before they cause significant problems.
- Predictive Maintenance: Use predictive maintenance data to plan maintenance activities more efficiently.
4. Documentation and Record-Keeping
Maintaining detailed records of maintenance activities and issues can help in identifying recurring problems and planning future maintenance.
- Maintenance Logs: Keep detailed logs of all maintenance activities, including inspections, repairs, and replacements.
- Issue Tracking: Track recurring issues to identify patterns and address underlying causes.
Effective troubleshooting and maintenance of belt conveyor batubara parts are essential for ensuring the smooth and efficient operation of coal transportation systems. By understanding common issues such as belt misalignment, slippage, excessive wear, material spillage, and belt breakage, and implementing advanced troubleshooting techniques and best practices, mining operations can significantly reduce downtime, enhance safety, and improve overall efficiency. Regular inspections, comprehensive training, structured maintenance scheduling, and detailed documentation are critical components of a robust maintenance strategy. As technology continues to advance, the integration of condition monitoring systems, predictive maintenance, and automated troubleshooting tools will further enhance the capabilities of belt conveyor batubara systems, ensuring they remain a reliable and vital component of coal mining operations.
Critical Komponen Conveyor for Optimal Belt Conveyor Batubara Performance
In the mining and materials handling industries, the efficiency and reliability of conveyor systems are paramount. One of the most critical applications of conveyor systems is the transportation of coal, commonly referred to as belt conveyor batubara. The term belt conveyor batubara not only emphasizes the specific application but also signifies the importance of having a system that can handle the rigorous demands of coal transportation. To ensure optimal performance, several critical components (komponen conveyor) must be meticulously designed, maintained, and synchronized. This section provides an in-depth analysis of these components, their functions, and their impact on the performance of belt conveyor batubara systems.
Conveyor Belts
The conveyor belt itself is the heart of any belt conveyor system. In the context of belt conveyor batubara, the belt must be highly durable and capable of withstanding the abrasive and harsh nature of coal. The materials used in these belts are typically reinforced with multiple layers of fabric or steel to provide additional strength and resistance to tearing and puncturing. Key properties of a high-performance conveyor belt include:
- Tensile Strength: High tensile strength is crucial to withstand the heavy loads of coal.
- Wear Resistance: The belt must resist abrasion from the sharp and coarse coal particles.
- Temperature Resistance: Coal can be transported at high temperatures, necessitating belts that can endure such conditions without degrading.
- Flame Retardancy: Given the combustible nature of coal, the belt should have flame-retardant properties to enhance safety.
Pulleys and Rollers
Pulleys and rollers are essential for supporting and guiding the conveyor belt. They are critical components in ensuring smooth operation and reducing downtime. For belt conveyor batubara systems, these components need to be particularly robust due to the heavy and abrasive nature of coal. Key types of pulleys and rollers include:
- Drive Pulleys: Responsible for moving the conveyor belt, these pulleys must provide sufficient traction and power transmission.
- Idler Rollers: These rollers support the belt and the coal load. They must have low friction bearings to minimize energy consumption and reduce wear on the belt.
- Return Rollers: These rollers guide the empty belt back to the start of the conveyor system. They need to be durable and resistant to the dust and debris associated with coal handling.
Conveyor Motors and Drives
The motors and drives are the powerhouses of the conveyor system. For optimal belt conveyor batubara performance, the motors and drives must be selected and maintained with precision. Factors to consider include:
- Power Rating: The motor must be powerful enough to handle the load of coal and the length of the conveyor.
- Efficiency: High-efficiency motors reduce energy consumption and operating costs.
- Variable Frequency Drives (VFDs): VFDs allow for variable speed control, which is essential for adapting to different operational conditions and optimizing performance.
- Reliability: Given the continuous operation in coal transport, the motors and drives must be highly reliable and capable of withstanding long hours of operation.
Conveyor Structure
The structure of the conveyor, including the frame and supports, must be designed to handle the heavy loads and harsh conditions typical of belt conveyor batubara systems. Critical aspects of the conveyor structure include:
- Stability: The structure must be stable and capable of supporting the dynamic loads of moving coal.
- Corrosion Resistance: Given the outdoor and sometimes wet environments, the structure should be made of materials that resist corrosion.
- Ease of Maintenance: The design should allow easy access for maintenance and repair activities to minimize downtime.
Belt Cleaning Systems
Belt cleaning systems are essential to maintain the efficiency and longevity of the conveyor belt. In belt conveyor batubara systems, these cleaning systems must effectively remove coal dust and residues to prevent buildup and potential damage. Key components include:
- Primary Scrapers: These are installed at the head pulley to remove the bulk of coal residue.
- Secondary Scrapers: These provide additional cleaning to ensure the belt is as clean as possible.
- Brush Cleaners: These use rotating brushes to remove finer particles and ensure a thorough cleaning.
Belt Alignment Systems
Belt misalignment can cause significant operational issues and damage to the conveyor system. For belt conveyor batubara systems, maintaining proper alignment is crucial due to the heavy and abrasive nature of coal. Key alignment components include:
- Tracking Idlers: These idlers help to keep the belt centered and prevent it from drifting off course.
- Sensors and Control Systems: Modern conveyor systems use sensors to monitor belt alignment and automatically adjust idlers to correct any deviations.
Safety Systems
Safety is paramount in any conveyor system, especially in belt conveyor batubara applications where the risks of fire and explosion are higher due to the combustible nature of coal. Critical safety components include:
- Fire Suppression Systems: These systems detect and extinguish fires quickly to prevent spread and damage.
- Emergency Stop Systems: These systems allow operators to stop the conveyor immediately in case of an emergency.
- Guards and Barriers: Physical barriers prevent accidental contact with moving parts, enhancing operator safety.
Dust Control Systems
Dust control is a significant concern in belt conveyor batubara systems due to the fine particles generated during coal handling. Effective dust control systems are essential to maintain air quality and prevent health hazards. Key components include:
- Dust Collectors: These devices capture and remove dust from the air, preventing it from escaping into the environment.
- Enclosures and Covers: Enclosing the conveyor system helps contain dust and prevents it from spreading.
- Spray Systems: Water spray systems can suppress dust by wetting coal particles and preventing them from becoming airborne.
Load Zones and Transfer Points
Load zones and transfer points are critical areas where coal is loaded onto or transferred between conveyor belts. These areas must be designed to handle the impact and reduce spillage and dust generation. Key components include:
- Impact Beds: These beds absorb the impact of coal falling onto the belt, protecting the belt and reducing wear.
- Skirting Systems: Skirting prevents coal from spilling off the sides of the conveyor belt, maintaining a clean and efficient operation.
- Transfer Chutes: These chutes guide coal from one conveyor to another, minimizing the drop height and reducing dust and material degradation.
Monitoring and Control Systems
Modern belt conveyor batubara systems are equipped with advanced monitoring and control systems to optimize performance and ensure safe operation. Key components include:
- Condition Monitoring Systems: These systems monitor the health of critical components such as motors, bearings, and belts, providing early warning of potential failures.
- Automation Systems: Automated control systems manage the operation of the conveyor, adjusting speed and load distribution to optimize performance.
- Data Analytics: Analyzing data from the conveyor system can identify trends and help in predictive maintenance, reducing downtime and improving efficiency.
The performance of belt conveyor batubara systems relies on the seamless integration and optimal functioning of various critical components. From the conveyor belt and pulleys to motors, drives, and safety systems, each component plays a vital role in ensuring the efficient and safe transportation of coal. Regular maintenance, proper selection of materials, and the use of advanced monitoring and control systems are essential to maintain the reliability and performance of these systems. By understanding and addressing the critical components of belt conveyor batubara, operators can enhance productivity, reduce operational costs, and ensure the safe handling of coal.
Looking for conveyor belt options? Fill out the form for details.
FAQs about Belt Conveyor Batubara
The world’s largest conveyor belt is located in the Western Sahara Desert and is known as the Bou Craa conveyor belt. This massive conveyor belt system spans over 60 miles (98 kilometers) and is used to transport phosphate rock from the Bou Craa mine to the port of El Aaiún. The Bou Craa conveyor belt is a remarkable engineering feat, as it traverses through harsh desert conditions, including sandstorms and extreme temperatures. This conveyor belt system plays a critical role in the global phosphate industry, supplying valuable raw materials used in agriculture and various other industries worldwide.
The conveyor belt metaphor is a concept used to describe a process or system that continuously moves items or people through a series of stages or steps. It is often used to illustrate the idea of efficiency, consistency, and predictability in processes such as manufacturing, education, or even life events. For example, in education, the conveyor belt metaphor might describe how students progress through grade levels in a structured, linear fashion. In a broader context, it can highlight the mechanistic nature of certain systems, where each component or participant is treated uniformly and moved along a predefined path.
The most common conveyor belt system is the belt conveyor. Belt conveyors are widely used in various industries, including manufacturing, logistics, mining, and food processing. These systems consist of a continuous belt made of materials like rubber, PVC, or fabric, which is driven by rollers or pulleys. Belt conveyors are popular due to their versatility, cost-effectiveness, and ability to transport a wide range of materials over long distances. They can be customized to handle different loads, speeds, and inclines, making them suitable for diverse applications such as moving boxes in a warehouse, transporting bulk materials in a quarry, or handling delicate products in a food processing plant.
The best angle for a conveyor belt depends on the type of material being transported and the specific application. Generally, for bulk materials like grains, sand, or gravel, the optimal conveyor belt angle ranges from 15 to 20 degrees. For packaged goods or boxes, a steeper angle of up to 30 degrees may be acceptable, provided the items have a secure base and the conveyor is equipped with cleats or sidewalls to prevent slippage. It’s important to consider factors such as the material’s properties, desired transport speed, and space constraints when determining the appropriate angle for a conveyor belt system. Properly setting the angle ensures efficient material flow, minimizes spillage, and reduces wear on the conveyor components.
Last Updated on August 5, 2024 by Jordan Smith
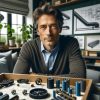
Jordan Smith, a seasoned professional with over 20 years of experience in the conveyor system industry. Jordan’s expertise lies in providing comprehensive solutions for conveyor rollers, belts, and accessories, catering to a wide range of industrial needs. From initial design and configuration to installation and meticulous troubleshooting, Jordan is adept at handling all aspects of conveyor system management. Whether you’re looking to upgrade your production line with efficient conveyor belts, require custom conveyor rollers for specific operations, or need expert advice on selecting the right conveyor accessories for your facility, Jordan is your reliable consultant. For any inquiries or assistance with conveyor system optimization, Jordan is available to share his wealth of knowledge and experience. Feel free to reach out at any time for professional guidance on all matters related to conveyor rollers, belts, and accessories.