Belt Conveyor Head Pulley Design Guide
Belt conveyors are essential in various industries, efficiently transporting materials over long distances. A critical component of these systems is the head pulley, which plays a vital role in the belt conveyor head pulley design. The head pulley is located at the discharge point of the conveyor, driving the belt and ensuring proper material flow. It provides the necessary traction and power transmission to keep the conveyor belt moving smoothly. In essence, the belt conveyor head pulley design significantly impacts the system’s efficiency and longevity, making it a key focus in conveyor engineering. Understanding its role and design principles is crucial for optimizing conveyor performance.
The Belt Conveyor Head Pulley Design and Functionality
Position and Role at the Discharge Point
In belt conveyor systems, the head pulley is strategically positioned at the discharge point, where it plays a crucial role in directing the flow of materials off the belt. This positioning allows the head pulley to control the belt’s movement and ensure smooth material discharge. The head pulley’s primary function is to provide the necessary driving force to move the conveyor belt, which is achieved by its rotation. This movement is essential for the continuous operation of the conveyor system, as it keeps the materials advancing towards the intended destination. By understanding the belt conveyor head pulley design, one can appreciate how this component influences the overall performance and efficiency of the conveyor system.
Power Transmission and Belt Traction
The head pulley is integral to the power transmission mechanism of the conveyor system. It is connected to a motor, which imparts rotational motion to the pulley. This rotation, in turn, drives the conveyor belt. The efficiency of power transmission largely depends on the belt conveyor head pulley design, particularly the pulley’s diameter, surface material, and alignment. Properly designed head pulleys ensure maximum traction, preventing slippage and ensuring that the belt moves consistently and at the correct speed.
Traction is a vital aspect of the head pulley’s function. To enhance traction, head pulleys often feature a lagging material, such as rubber or ceramic, which increases the friction between the pulley and the belt. This friction is crucial in maintaining the belt’s movement, especially under varying loads and environmental conditions. A well-designed head pulley with appropriate lagging can significantly improve the conveyor system’s reliability and efficiency.
Importance of Head Pulley Design in Efficiency and Longevity
The design of the head pulley is paramount in determining the efficiency and longevity of the conveyor system.
- Improved Traction and Reduced Slippage: A head pulley with a well-engineered surface enhances traction, reducing slippage and ensuring smooth operation. For instance, rubber lagging can significantly improve grip, thereby preventing operational disruptions.
- Optimal Diameter for Load Handling: The diameter of the head pulley is designed based on the load requirements and belt specifications. A larger diameter pulley can handle heavier loads more efficiently, reducing stress on the belt and extending its lifespan.
- Enhanced Belt Alignment: Proper belt conveyor head pulley design includes ensuring precise alignment. Misalignment can cause belt wear and tear, leading to frequent maintenance issues. A well-aligned head pulley ensures the belt runs true, reducing maintenance costs and downtime.
- Heat and Wear Resistance: In harsh operating environments, the head pulley’s material selection is critical. For example, ceramic lagging is used in applications where high heat and abrasive materials are present, providing superior resistance and durability compared to rubber lagging.
- Energy Efficiency: A head pulley designed for optimal power transmission can reduce the energy required to drive the belt. Efficient pulleys minimize energy losses, leading to lower operational costs and a more sustainable conveyor system.
The belt conveyor head pulley design is fundamental to the efficient and reliable operation of a conveyor system. By understanding the intricacies of its design and functionality, operators can optimize their systems for better performance and longevity. The head pulley’s role at the discharge point, its contribution to power transmission and traction, and its overall impact on system efficiency are critical factors that underscore its importance in conveyor engineering. By focusing on these design elements, one can ensure that the conveyor system operates smoothly, with minimal disruptions and extended service life.
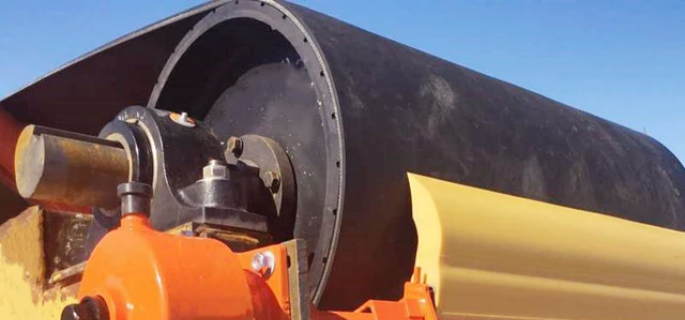
Belt Conveyor Head Pulley Design Factors
Designing a head pulley for a belt conveyor involves considering various factors to ensure efficiency, reliability, and safety. Here are the key design factors to consider:
Pulley Diameter:
- The diameter should be adequate to support the belt and avoid excessive bending. It should also match the speed and tension requirements of the conveyor system.
Belt Tension:
- The head pulley must handle the maximum tension exerted by the belt. This includes understanding the tension in different operating conditions like starting, stopping, and running under full load.
Pulley Material:
- Materials like steel or composite materials are chosen based on the operational environment, load capacity, and durability requirements. The material must be corrosion-resistant if used in harsh environments.
Lagging:
- Lagging (covering the pulley with a material like rubber) enhances grip and reduces belt slippage. The type of lagging depends on the application, such as plain, grooved, or ceramic lagging.
Shaft Design:
- The shaft must be designed to handle the torque and bending stresses. Shaft material and dimensions are selected based on these factors.
Bearing Selection:
- Bearings must support the shaft and allow smooth rotation. They should be chosen based on load ratings, speed, and environmental conditions (e.g., temperature, moisture).
Pulley Balance:
- Proper balancing is crucial to avoid vibrations, which can lead to premature wear and tear. Dynamic balancing is often performed to ensure smooth operation.
Belt Speed:
- The design must consider the operating speed of the conveyor belt. Higher speeds may require different pulley specifications to handle the increased kinetic energy.
Environmental Conditions:
- Factors like temperature, humidity, exposure to chemicals, and abrasive materials influence the choice of materials and protective coatings.
- Maintenance Accessibility:
- Design should facilitate easy maintenance and replacement of parts to minimize downtime.
- Safety Standards:
- Compliance with industry standards and regulations (such as CEMA or ISO) is essential to ensure safety and reliability.
- Pulley Geometry:
- The crown (slight curvature) of the pulley helps in belt tracking. The design must ensure the crown is appropriate for the belt type and application.
- Load Distribution:
- Ensuring uniform load distribution across the pulley surface to prevent localized wear and extend the life of the pulley and belt.
Each of these factors plays a crucial role in the design of a head pulley for a belt conveyor system, ensuring it operates efficiently and reliably under various conditions.
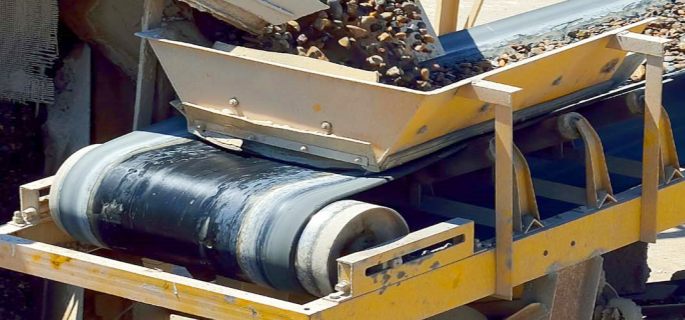
Belt Conveyor Head Pulley Design Formula
Designing a head pulley for a belt conveyor involves several formulas to determine the appropriate dimensions and characteristics. Here are some key formulas and considerations:
1. Pulley Diameter Calculation
The diameter of the pulley can be calculated using the following formula:
D=Tb/(Fs×TaD)
where:
- D = Pulley diameter (mm)
- Tb = Belt tension (N)
- Fs = Safety factor (typically between 1.5 to 2.0)
- Ta = Allowable belt tension (N/mm width)
2. Belt Tension
The belt tension is critical in determining the size and type of pulley. The tension can be calculated as:
T=P/vT
where:
- T = Belt tension (N)
- P = Power transmitted by the belt (W)
- v = Belt speed (m/s)
3. Shaft Diameter
The shaft diameter can be determined using the following formula:
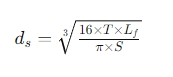
where:
- ds = Shaft diameter (mm)
- T = Torque transmitted (N·m)
- Lf = Load factor (usually between 1.0 to 1.5)
- S = Shear stress of the shaft material (N/mm²)
4. Torque
Torque on the head pulley can be calculated as:
T=P/2πn
where:
- T = Torque (N·m)
- P = Power transmitted by the belt (W)
- n = Rotational speed (rpm)
5. Pulley Face Width
The face width of the pulley should be wider than the belt width to ensure proper tracking and load distribution. A common guideline is:
Wp=B/(2×50 mm)
where:
- Wp = Pulley face width (mm)
- B = Belt width (mm)
6. Pulley Balance
Balancing the pulley is crucial to avoid vibrations. Dynamic balancing is often performed using specialized equipment and procedures.
7. Lagging Thickness
The thickness of the lagging can be calculated based on the application and operational conditions. A typical value for rubber lagging is around 6-12 mm.
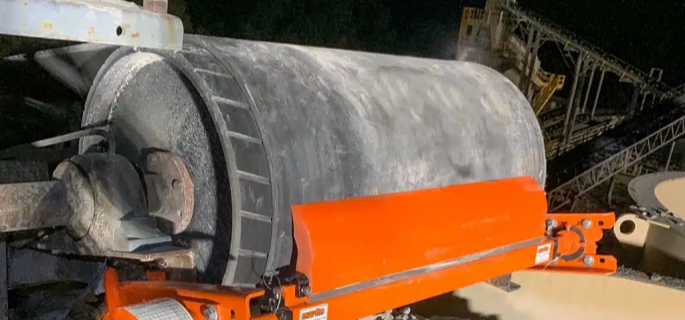
Belt Conveyor Head Pulley Design Effectively
Designing a belt conveyor head pulley effectively involves a combination of theoretical calculations, practical considerations, and adherence to industry standards. Here are detailed steps and factors to consider:
1. Understand the Conveyor System Requirements
- Belt Width and Speed: Determine the belt width and speed based on the material to be transported and the required throughput.
- Load Characteristics: Assess the weight, size, and nature of the material (e.g., granular, abrasive) to ensure the pulley can handle it without undue wear.
2. Select Appropriate Materials
- Pulley Shell Material: Typically made from steel, but can be made from other materials like aluminum or composites for specific applications.
- Shaft Material: Usually high-strength steel to handle bending and torsional stresses.
3. Calculate Pulley Dimensions
- Pulley Diameter: Ensure it fits the belt’s minimum bend radius to prevent undue stress and wear. Use the formula:
D = Tb/{Fs × Ta}
Adjust this formula considering practical constraints and manufacturer recommendations. - Pulley Face Width: The face width should be slightly wider than the belt to ensure proper belt tracking.
Wp = B + (2 × 50 mm)
4. Determine Belt Tension and Torque
- Belt Tension: Calculate using the maximum load conditions, including starting and stopping scenarios.
T = P / v - Torque on the Pulley: Determine based on power and speed.
T = P / 2Πn
5. Design the Shaft
- Shaft Diameter: Use the following formula to ensure it can handle the torque and bending stresses.
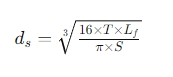
6. Consider Pulley Lagging
- Lagging Material: Choose based on the application, such as rubber for general use, or ceramic for high-abrasion environments.
- Lagging Thickness: Typically between 6-12 mm, depending on the operating conditions.
7. Balance the Pulley
- Static and Dynamic Balancing: Perform balancing to minimize vibrations and ensure smooth operation. Use dynamic balancing machines for precision.
8. Select Appropriate Bearings
- Bearing Type: Choose bearings that can handle the load, speed, and environmental conditions.
- Sealing and Lubrication: Ensure bearings are properly sealed and lubricated to prevent contamination and reduce maintenance.
9. Compliance with Standards
- Industry Standards: Follow standards such as CEMA (Conveyor Equipment Manufacturers Association) or ISO for design and safety guidelines.
10. Consider Environmental Factors
- Temperature and Corrosion: Use materials and coatings that can withstand the operating environment, including extreme temperatures and corrosive conditions.
- Dust and Moisture: Design the pulley and its components to prevent ingress of dust and moisture.
11. Ease of Maintenance
- Accessibility: Design the pulley and surrounding structures to allow easy access for maintenance and replacement.
- Modular Components: Use modular components that can be easily replaced without extensive downtime.
By following these steps and using the appropriate formulas, you can design an effective and reliable head pulley for a belt conveyor system.
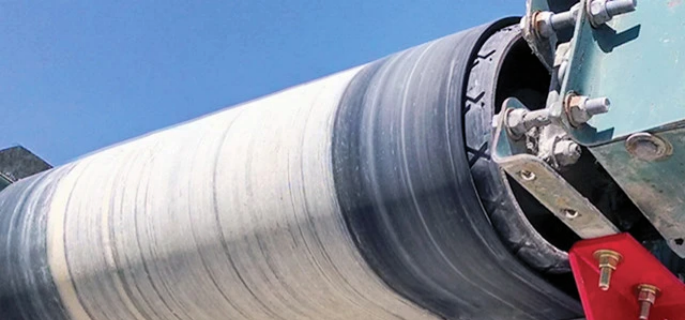
Technical Specifications of Belt Conveyor Head Pulley Design
Overview of Standard Dimensions and How They Are Determined
In the belt conveyor head pulley design, standard dimensions are crucial for ensuring compatibility and optimal performance within a conveyor system. The dimensions of a head pulley include its diameter, face width, and shaft size. These parameters are carefully calculated based on the specific requirements of the conveyor system, including the type of materials being transported, the conveyor belt width, the operational speed, and the load capacity.
The diameter of the head pulley is a fundamental dimension that directly impacts the conveyor system’s efficiency. It is typically chosen based on the belt width and the load requirements. Larger diameters are generally preferred for heavy-duty applications, as they provide better support and reduce belt stress. The face width of the head pulley must be slightly wider than the belt to ensure complete support across the belt’s width, preventing edge wear and maintaining proper alignment.
The conveyor belt shaft size of the head pulley is determined by the torque requirements and the pulley’s overall dimensions. A larger shaft diameter is necessary for higher torque applications to prevent bending and ensure stable operation. Standardized dimensions for head pulleys ensure that they can be easily integrated into various conveyor systems, facilitating maintenance and replacement when necessary.
Insights into Conveyor Head Pulley Diameter Calculation
The diameter of the head pulley in the belt conveyor head pulley design is calculated based on several operational factors, ensuring that the pulley can efficiently drive the belt while withstanding the operational stresses. The following considerations are essential in determining the appropriate head pulley diameter:
- Belt Width and Type: The belt width is a primary factor influencing the head pulley diameter. For wider belts, a larger pulley diameter is required to provide adequate support and prevent belt sagging. Additionally, the type of belt material (e.g., fabric, steel cord) also impacts the required diameter due to different flexibility and load-bearing characteristics.
- Load Capacity: The load capacity of the conveyor system dictates the head pulley diameter. Heavier loads necessitate larger diameters to distribute the load more evenly and reduce the stress on the belt. This prevents premature wear and extends the belt’s lifespan.
- Belt Speed: The operational speed of the conveyor belt influences the head pulley diameter. Higher speeds require larger diameters to ensure smooth operation and reduce the risk of belt slippage. This is particularly important in high-speed applications where consistent traction is critical.
- Material Characteristics: The type of material being transported affects the head pulley diameter. Abrasive or heavy materials require pulleys with greater diameters to withstand the increased wear and tear. Additionally, materials with high moisture content may require special considerations to prevent slippage and ensure efficient material handling.
- Environmental Conditions: The operating environment also plays a role in determining the head pulley diameter. For instance, pulleys used in harsh environments, such as mining or chemical processing, may require larger diameters and special coatings to resist corrosion and abrasion.
To illustrate, consider a conveyor system transporting heavy bulk materials at a high speed. In this scenario, a head pulley with a larger diameter is chosen to ensure that the belt remains taut and does not slip. The larger diameter provides better traction, reducing the likelihood of operational disruptions and extending the system’s overall lifespan.
Another example is a conveyor system used in a food processing plant, where the materials being transported are relatively lightweight but the operational speed is high. In this case, the head pulley diameter is selected to balance the need for smooth operation at high speeds with the requirement to handle the specific belt type used in the plant, ensuring efficient and hygienic material handling.
The belt conveyor head pulley design is meticulously crafted to fit various operational requirements by considering standard dimensions and calculating the appropriate pulley diameter. This careful design process ensures that the conveyor system operates efficiently, with minimal maintenance and extended service life. By understanding the technical specifications of head pulleys, operators can optimize their conveyor systems for better performance and reliability.
Belt Conveyor Head Pulley Design Features
Lagging Options: Advantages of Rubber Versus Ceramic Lagging
In the belt conveyor head pulley design, lagging is an essential feature that enhances the performance and longevity of the conveyor system. Lagging refers to the application of a coating or covering on the surface of the head pulley to increase friction and improve traction between the pulley and the conveyor belt. There are two primary types of lagging materials used: rubber and ceramic.
Rubber Lagging:
- Increased Traction: Rubber lagging significantly increases the friction between the pulley and the belt, reducing the risk of slippage and ensuring smooth operation. For example, in a quarrying operation, rubber-lagged head pulleys can handle the high traction demands of moving heavy, abrasive materials.
- Noise Reduction: Rubber lagging can help dampen the noise generated by the conveyor system. In food processing plants, where a quieter operation is beneficial, rubber-lagged head pulleys contribute to a more pleasant working environment.
- Cost-Effective: Rubber lagging is generally more affordable than ceramic lagging, making it a cost-effective solution for many industries. For instance, in light manufacturing, rubber-lagged head pulleys provide the necessary traction without a significant increase in cost.
- Easy Installation and Maintenance: Rubber lagging is relatively easy to install and maintain. In packaging facilities, where quick maintenance is crucial, rubber-lagged head pulleys can be easily serviced to minimize downtime.
- Flexibility: Rubber lagging offers flexibility and resilience, which is advantageous in applications where the pulley undergoes frequent start-stop cycles, such as in distribution centers.
Ceramic Lagging:
- Superior Wear Resistance: Ceramic lagging provides exceptional resistance to wear and abrasion, making it ideal for harsh environments. For example, in mining operations, ceramic-lagged head pulleys withstand the abrasive nature of transported minerals, ensuring longer service life.
- Enhanced Heat Resistance: Ceramic lagging performs well in high-temperature conditions. In steel mills, where conveyor systems operate in hot environments, ceramic-lagged head pulleys maintain their performance and durability.
- Increased Lifespan: The durability of ceramic lagging extends the lifespan of the head pulley. For instance, in cement plants, ceramic-lagged head pulleys endure the tough conditions and prolong the operational period before requiring replacement.
- Improved Belt Grip: Ceramic lagging offers excellent grip on the conveyor belt, even under wet or muddy conditions. In aggregate processing, ceramic-lagged head pulleys ensure efficient material transport despite challenging environmental factors.
- High Load Capacity: Ceramic lagging can support higher loads without compromising performance. In bulk material handling, ceramic-lagged head pulleys effectively manage the substantial weight of the materials being transported.
The Significance of Implementing Lagging on the Head Pulley for Enhanced Traction and Belt Alignment
Implementing lagging on the head pulley is a critical aspect of the belt conveyor head pulley design, as it enhances traction and ensures proper belt alignment. Here are five examples illustrating its significance:
- Preventing Belt Slippage: In a logistics center, lagged head pulleys prevent belt slippage during high-speed operations, ensuring that packages are transported efficiently and without interruption.
- Improving Belt Tracking: In agricultural processing facilities, lagged head pulleys help maintain proper belt alignment, reducing the risk of belt misalignment and the associated maintenance issues.
- Enhancing Load Handling: In port facilities, where heavy bulk materials are loaded onto ships, lagged head pulleys improve the belt’s ability to handle substantial loads, ensuring smooth and reliable operation.
- Reducing Maintenance Costs: In manufacturing plants, lagged head pulleys reduce wear and tear on both the pulley and the belt, lowering maintenance costs and extending the life of the conveyor components.
- Ensuring Safety: In recycling plants, where the conveyor system handles various materials, lagged head pulleys provide the necessary grip and alignment, minimizing the risk of accidents caused by belt slippage or misalignment.
Illustration Through Conveyor Head Pulley Drawings to Show Design Variations and Installations
Conveyor head pulley drawings are invaluable tools in the belt conveyor head pulley design process, as they illustrate the various design options and installation configurations available. These drawings typically depict the pulley’s dimensions, lagging type, and mounting method, providing a clear visual representation of the design.
For example, a drawing might show a head pulley with rubber lagging designed for a light manufacturing facility, highlighting its cost-effective and noise-reducing properties. Another drawing could illustrate a ceramic-lagged head pulley for a mining operation, emphasizing its superior wear resistance and high load capacity.
Additionally, drawings can depict different installation methods, such as the use of adjustable brackets for easy alignment or the integration of tensioning devices to maintain optimal belt tension. By providing detailed visuals, these drawings help engineers and operators understand the design intricacies and ensure that the head pulley is correctly installed and maintained.
The belt conveyor head pulley design incorporates several critical features that enhance the system’s performance and reliability. By understanding the advantages of different lagging options, the significance of lagging for traction and alignment, and the value of detailed design drawings, operators can optimize their conveyor systems for maximum efficiency and longevity.
Belt Conveyor Head Pulley Design Considerations
Selecting the Right Head Pulley and Tail Pulley for Specific Conveyor Systems
When designing a conveyor system, selecting the appropriate head and tail pulleys is crucial for optimal performance and longevity. The head pulley, located at the discharge end of the conveyor, drives the belt and provides the necessary traction for material transport. The tail pulley, positioned at the opposite end, helps in belt tensioning and direction. The selection process should focus on matching the pulleys to the specific operational requirements and environmental conditions of the conveyor system.
- Application Requirements: Identify the application’s specific needs, such as the type of materials being transported, the required belt speed, and the load capacity. For instance, a conveyor system used in a coal mine will have different requirements compared to one used in a food processing plant.
- Pulley Diameter and Width: Ensure that the pulley diameter and width are compatible with the conveyor belt’s specifications. Larger diameters are better for heavy-duty applications, while smaller diameters can be used for lighter loads. The pulley width should match or slightly exceed the belt width to provide adequate support and prevent edge wear.
- Lagging Material: Choose the appropriate lagging material based on the operational environment. Rubber lagging is suitable for general purposes, providing good traction and noise reduction, while ceramic lagging offers superior wear resistance for harsh environments.
- Shaft and Bearing Selection: The shaft and bearings must be capable of handling the operational loads and conditions. For high-torque applications, larger shafts and heavy-duty bearings are required to prevent bending and ensure stable operation.
- Environmental Conditions: Consider factors such as temperature, humidity, and exposure to chemicals when selecting the head and tail pulleys. For example, stainless steel pulleys may be necessary in corrosive environments to prevent rust and degradation.
Factors Influencing the Design: Load Capacity, Belt Speed, Material Characteristics, and Environmental Conditions
- Load Capacity: The load capacity of the conveyor system directly influences the belt conveyor head pulley design. For heavy loads, larger and more robust pulleys are required to distribute the load evenly and prevent belt stress. In a mining operation, where large quantities of ore are transported, the head pulley must be designed to handle significant weight without deforming.
- Belt Speed: The speed at which the conveyor belt operates affects the design of the head pulley. Higher speeds require larger diameters to ensure smooth operation and reduce slippage. In a high-speed packaging line, a larger head pulley helps maintain consistent belt movement and prevents operational disruptions.
- Material Characteristics: The nature of the materials being transported influences the design. Abrasive materials, like sand and gravel, require head pulleys with durable lagging to withstand wear and tear. In a quarry, ceramic-lagged head pulleys provide the necessary abrasion resistance to handle rough materials.
- Environmental Conditions: The operating environment significantly impacts the design. For instance, in outdoor applications exposed to varying weather conditions, pulleys must be designed to resist corrosion and temperature fluctuations. In a coastal facility, stainless steel head pulleys are essential to prevent rust from saltwater exposure.
- Operational Conditions: Consider factors like operational hours and maintenance schedules. In a continuously operating power plant, the head pulley design must prioritize durability and minimal maintenance to avoid costly downtimes. Heavy-duty materials and robust construction are critical in such scenarios.
Step-by-Step Walkthrough on Calculating Pulley Dimensions and Selecting Appropriate Materials
- Determine Belt Width and Load Requirements: Start by identifying the belt width and the maximum load the conveyor system will handle. This information is essential for calculating the appropriate pulley diameter and width.
- Select Pulley Width: The pulley width should be equal to or slightly greater than the belt width to provide full support. Ensure that the width accommodates the belt and any additional side clearance.
- Choose Lagging Material: Based on the operational environment and material characteristics, select the appropriate lagging material. Rubber lagging is suitable for general applications, while ceramic lagging is ideal for high-abrasion environments.
- Design Shaft and Bearing Assembly: Calculate the required shaft diameter and select bearings that can handle the operational loads. Ensure the assembly can withstand the torque and rotational forces during operation.
- Consider Environmental Factors: Evaluate the environmental conditions and select materials that can resist corrosion, extreme temperatures, and other environmental challenges. Stainless steel or coated pulleys may be necessary for harsh conditions.
By following these design considerations and steps, you can ensure that the belt conveyor head pulley design is optimized for efficiency, durability, and reliable operation in any application.
Innovations in Belt Conveyor Head Pulley Design
Current Trends and Advancements in Head Pulley Designs
The field of belt conveyor head pulley design has seen significant advancements in recent years, with a strong focus on improving efficiency, enhancing safety, and reducing maintenance requirements. These innovations aim to address common challenges faced by industries that rely heavily on conveyor systems.
- Enhanced Lagging Materials: One of the major trends is the development of advanced lagging materials. Modern rubber compounds and ceramic coatings provide superior traction and wear resistance, significantly extending the life of head pulleys. For example, new rubber formulations that incorporate wear-resistant additives can reduce the frequency of maintenance and replacement in mining operations, where abrasion is a constant issue.
- Self-Cleaning Pulleys: Another innovation is the introduction of self-cleaning head pulleys. These designs feature specialized surfaces or attachments that automatically remove debris and buildup from the belt and pulley surface. This is particularly beneficial in environments such as agriculture and food processing, where cleanliness is crucial. Self-cleaning pulleys help maintain consistent performance and reduce downtime for manual cleaning.
- Integrated Condition Monitoring: With the advent of the Industrial Internet of Things (IIoT), condition monitoring has become a vital part of belt conveyor head pulley design. Sensors embedded in the pulleys can continuously monitor parameters such as temperature, vibration, and wear. This real-time data allows for predictive maintenance, preventing unexpected failures and optimizing the lifespan of the equipment. In heavy industries like steel manufacturing, condition monitoring systems can alert operators to potential issues before they lead to costly downtimes.
- Lightweight Composite Materials: The use of lightweight composite materials in pulley construction is another significant advancement. These materials offer high strength-to-weight ratios, reducing the overall weight of the conveyor system and lowering energy consumption. For instance, pulleys made from carbon fiber composites can be used in high-speed packaging lines, where reduced inertia enhances performance and energy efficiency.
- Modular Design: Modular head pulley designs allow for easy replacement of worn components without the need for extensive downtime. This approach is particularly useful in facilities that operate 24/7, such as distribution centers and logistics hubs. Modular designs enable quick swaps of lagging sections or entire pulley assemblies, keeping the conveyor system running smoothly with minimal interruption.
The Role of Computational Analysis in Improving Pulley Design
Computational analysis plays a critical role in modern belt conveyor head pulley design, enabling engineers to create highly optimized and reliable components through precise calculations and simulations.
- Finite Element Analysis (FEA): FEA is widely used to simulate the stresses and strains on head pulleys under various load conditions. By modeling the pulley in a virtual environment, engineers can identify potential failure points and optimize the design to withstand operational demands. For example, FEA can reveal stress concentrations around the pulley shaft, allowing designers to reinforce these areas and extend the pulley’s service life.
- Computational Fluid Dynamics (CFD): In applications where pulleys are exposed to dust or liquids, CFD analysis helps in designing features that minimize the impact of these elements. For instance, in cement manufacturing, CFD can be used to optimize the shape of pulley covers to prevent dust accumulation, thereby maintaining the efficiency of the system.
- Material Selection Algorithms: Advanced algorithms aid in selecting the best materials for pulley construction based on operational requirements and environmental conditions. These tools consider factors such as tensile strength, abrasion resistance, and thermal properties. In the mining industry, for example, algorithms can recommend materials that offer the best combination of durability and cost-effectiveness for handling abrasive ores.
- Dynamic Simulation: Dynamic simulations model the real-time behavior of conveyor systems, including the interaction between the belt and the pulley. These simulations can predict how changes in load, speed, or belt tension will affect the system’s performance. In a logistics center, dynamic simulation can help optimize pulley design for varying load conditions, ensuring reliable operation under different scenarios.
- Topological Optimization: This advanced design approach uses computational algorithms to optimize the shape and structure of pulleys for maximum performance and minimal material usage. By iteratively refining the design, engineers can create pulleys that are both lightweight and robust. For example, in aerospace applications where weight is a critical factor, topological optimization can produce pulleys that meet stringent weight and strength requirements.
The belt conveyor head pulley design has evolved significantly with the integration of advanced materials, smart technologies, and computational analysis. These innovations not only enhance the efficiency and safety of conveyor systems but also reduce maintenance costs and downtime. By leveraging these advancements, industries can achieve more reliable and efficient material handling operations, ensuring continued productivity and operational excellence.
Real-World Applications of Belt Conveyor Head Pulley Design
Troubleshooting Common Issues with Head Pulleys Based on Real-World Scenarios
Despite the advancements in belt conveyor head pulley design, operational issues can still arise. Below are common problems and troubleshooting strategies based on real-world scenarios:
- Slippage: Slippage occurs when the conveyor belt loses traction on the head pulley. In a metal processing plant, slippage was causing operational delays. The solution involved replacing the existing lagging with a higher-friction rubber lagging and adjusting the belt tension. These changes restored proper traction and eliminated the slippage issue.
- Misalignment: Misalignment of the conveyor belt can lead to uneven wear and system inefficiencies. A manufacturing facility experienced frequent belt misalignments. The troubleshooting involved realigning the head pulley and installing adjustable brackets to maintain proper belt tracking. Regular inspections and adjustments were implemented to prevent future misalignments.
- Excessive Wear: In a quarry, the head pulleys were wearing out rapidly due to the abrasive nature of the transported materials. The solution was to switch to ceramic lagging, which offered greater wear resistance. Additionally, implementing a more frequent maintenance schedule helped in early detection and rectification of wear issues, prolonging the pulley’s life.
- Noise: High noise levels from the conveyor system were a concern in a packaging plant. The head pulley design was modified to include noise-dampening rubber lagging, which significantly reduced operational noise. This improvement enhanced the working environment and complied with noise regulations.
- Belt Tracking Issues: In a paper mill, improper belt tracking was causing frequent shutdowns. The issue was addressed by recalibrating the head pulley alignment and installing automatic belt trackers. These devices ensured the belt remained centered, reducing the need for manual adjustments and improving system reliability.
The belt conveyor head pulley design plays a critical role in the efficiency and reliability of conveyor systems across various industries. Through innovative design solutions and proactive troubleshooting, industries can address common issues and achieve optimal performance. These case studies highlight the importance of tailored pulley designs to meet specific operational requirements, demonstrating the practical application of advanced engineering principles in real-world scenarios.
Last Updated on October 23, 2024 by Jordan Smith
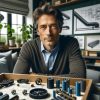
Jordan Smith, a seasoned professional with over 20 years of experience in the conveyor system industry. Jordan’s expertise lies in providing comprehensive solutions for conveyor rollers, belts, and accessories, catering to a wide range of industrial needs. From initial design and configuration to installation and meticulous troubleshooting, Jordan is adept at handling all aspects of conveyor system management. Whether you’re looking to upgrade your production line with efficient conveyor belts, require custom conveyor rollers for specific operations, or need expert advice on selecting the right conveyor accessories for your facility, Jordan is your reliable consultant. For any inquiries or assistance with conveyor system optimization, Jordan is available to share his wealth of knowledge and experience. Feel free to reach out at any time for professional guidance on all matters related to conveyor rollers, belts, and accessories.